配送中心布局优化仿真设计.docx
《配送中心布局优化仿真设计.docx》由会员分享,可在线阅读,更多相关《配送中心布局优化仿真设计.docx(13页珍藏版)》请在冰豆网上搜索。
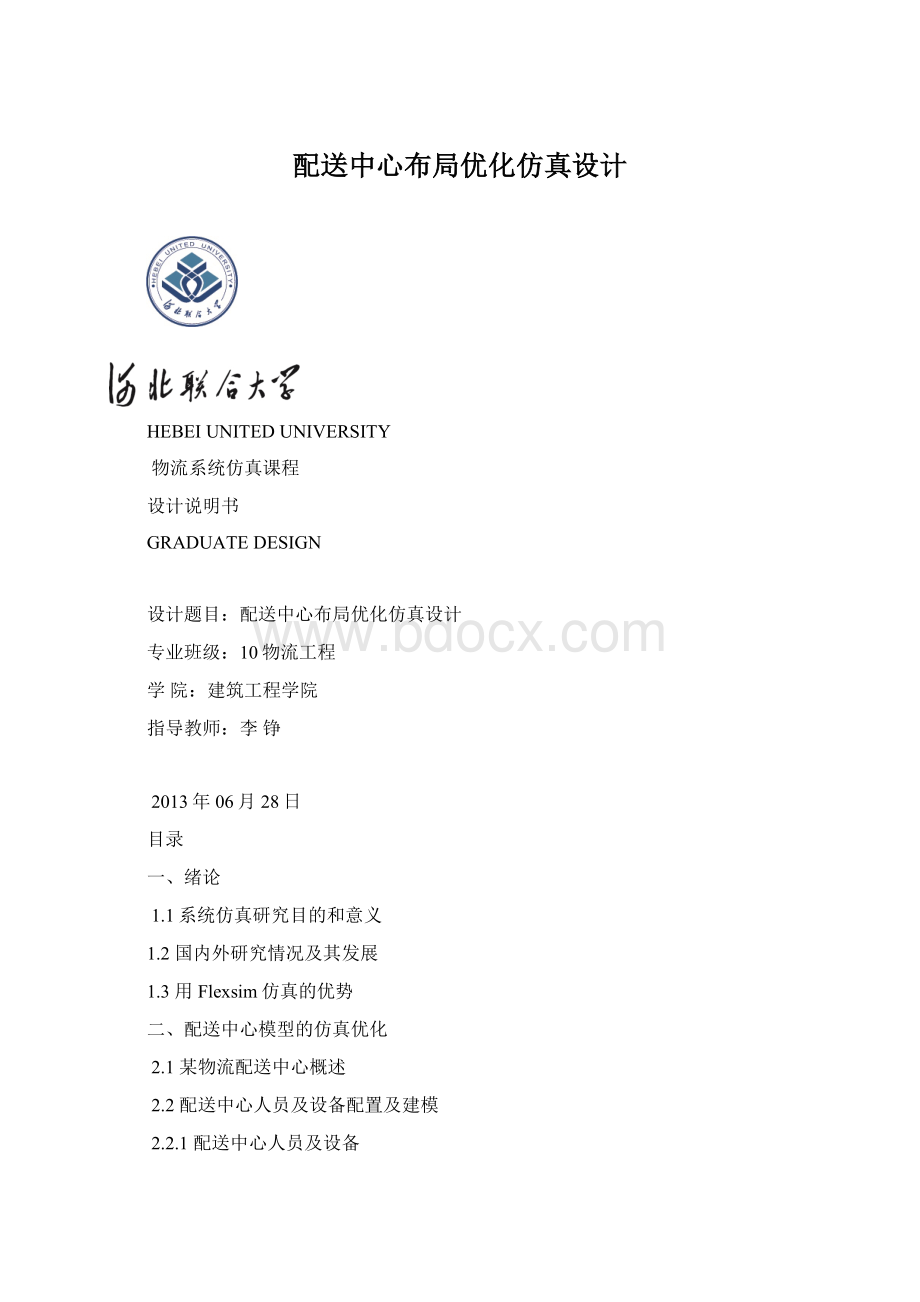
配送中心布局优化仿真设计
HEBEIUNITEDUNIVERSITY
物流系统仿真课程
设计说明书
GRADUATEDESIGN
设计题目:
配送中心布局优化仿真设计
专业班级:
10物流工程
学院:
建筑工程学院
指导教师:
李铮
2013年06月28日
目录
一、绪论
1.1系统仿真研究目的和意义
1.2国内外研究情况及其发展
1.3用Flexsim仿真的优势
二、配送中心模型的仿真优化
2.1某物流配送中心概述
2.2配送中心人员及设备配置及建模
2.2.1配送中心人员及设备
2.2.2人员设备建模
2.3配送中心流程及建模
2.3.1配送中心流程
2.3.2配送中心流程建模
三、仿真结果与数据分析
3.1仿真数据收集
3.2仿真优化
3.2.1优化目的
3.2.2效率分析和系统优化
3.2.3优化结果
四、课程设计小结
五、参考文献
一、绪论
1.1系统仿真研究目的和意义
在许多发达国家,物流己在实践中得到了广泛的发展,并己成为一国经济发展的重要支柱。
在我国,随着市场经济发展的深入,降低社会物流总成本是中国经济发展模式转变的重要标志之一,也是提高国民经济运行质量的综合性指标之一,发展物流产业,降低流通总成本,无疑将成为我国新的经济增长点。
对于企业,面对日益激烈的竞争,如何降低物流的成本已成为一个重要课题。
配送作为物流链上最具增值特性的环节之一,倍受投资者的重视。
配送中心正是顺应这一潮流而发展起来。
配送中心是从事物流活动的场所或组织,是为了有效地保证货物流通而建立的物流综合管理、控制与配送的机构或设施,它具有集货中心、分货中心等综合功能,是产销企业之间的中介。
如何调整配送中心的系统结构、优化配送流程、提高配送效率、降低配送成本,越来越具有理论意义和实践意义。
配送中心是典型的现代机械电子相结合的系统,由半自动化、自动化以致具有一定智能的物流设备和计算机管理和控制系统组成。
它的规划设计要综合考虑的因素很多,各子系统功能部分相互交叉、互为因果,需要进行严密的分析。
为了避免在配送中心的优化构建上浪费大量的人力、物力和时间,系统仿真是必然的选择。
通过仿真,操作者可以在屏幕上观察不同的场景,通过不同的资源配置对各种物流方案进行评价,并可以假设一些条件,比如一个子系统暂时停止工作后,观察可能发生的情况。
系统仿真还可以让人们直观系统模型动态运行的效果,找出瓶颈,多次修改参数,反复仿真,以达到系统优化。
配送中心系统仿真的意义更在于在我们在配送中心的规划设计阶段就希望评价方案的优劣,显然无法在真实系统上进行,利用模型来研究系统不仅是必要的,更是唯一可行的方法。
本论文的研究目的是运用系统建模方法,使用Flexsim仿真软件建立配送中心流通加工作业系统及其与之相关的运输、搬运作业系统仿真模型,在仿真模拟的基础上,进行统计分析,得出配送中心物流作业系统运行的较优策略,为提高配送中心的运作效率提供依据。
1.2国内外研究情况及其发展
在国外,物流系统仿真建模研究创新步伐较快。
如:
配送中心选址的经典模型是HarveyN.Shucom和RichardB.Maffei在1960年提出的,为亨氏公司开发,后来用于雀巢公司的配送问题。
该仿真模型为基本的配送中心选址问题提供了答案,且可以涉及多达4000个客户、40个配送中心,10-15个工厂。
L.vandenBruggen,R.Gruson,M.Salomon在1995年为一家大型石油公司设计了一套物流仿真系统,来处理石油加油站的选址和分配到每个站点的顾客量的问题,通过仿真表示优化后的结构每年能节省费用5%-6%;德国亚探工业大学为德国某集团公司的物流配送网络系统的设计及优化开发了一套仿真软件;IBM公司为自己复杂的多级售后服务网络开发了一套零配件库存管理系统等。
可以看出这些方法虽然都实现了对物流中心定量化分析的目标,但是都是针对物流中心的静态建模研究,建模过程中没有考虑物流中心大多数影响因素动态随机的特点,不能很逼真的反映物流中心运营过程中出现的许多问题。
因此国内外许多学者开始将系统仿真的思想引入物流中心仿真建模中并根据物流中心离散事件系统的特征采用计算机方法实现其仿真建模研究,这成为实现物流中心仿真建模的新手段和发展趋势。
国外对物流中心采取离散事件系统仿真思想仿真建模。
我国也有一些学者进行了相应研究,陕西科技大学的张志刚、曹西京等人将OpenGL技术应用十自动化立体仓库的建前规划,分析了其中的关键技术,开发了二维仿真动画程序;西南交通大学的李涛采用离散事件数字仿真原理,利用数据库和计算机图形技术,建立二维可视化仿真系统,对集装箱货场物流系统运行效率和实现物流系统适时的作业运行进行动态显示。
但是随着计算机仿真技术的快速发展,人们逐渐发现依此进行系统仿真造价大,且可能造成重复性劳动,所以国内外研究领域开始致力十开发相应的物流仿真软件并将其应用在物流系统仿真建模上。
国外在这方面的研究步伐较快,英国Lanne公司推出的Witness,美国BrooksAutomation公司开发的Automod,美国Rockwell公司开发的Arena及Flexsim,SoftwareProducts公司开的Flexsim等都是一些功能完善、广泛应用于物流系统仿真建模的先进软件。
1.3用Flexsim仿真的优势
Flexsim是一款相对较新的仿真软件,由于其研发较晚,所基于的技术与前一代软件相比有所不同,具有开放式的柔性仿真平台,更贴近现代的建模思想和用户需求,在高校、科研和企业领域内具有较好的应用前景,它保留了好多对外的接口,可以方便地与外界系统进行信息的交换它基于C++平台,高级开发用户可以直接使用C语言来创建和修改对象以及控制对象的行为活动,还可以使用C++语一言实现动态布局,提供自动化建模的可能性。
Flexsim还支持用户二次开发,可以使用封装的OpenGL来实现设备的可视化造型,也可以直接导入3DS文件进行设备造型,以开发满足各个领域、各个企业的特殊设备对象仿真模型。
随着计算机软件和硬件技术的发展,仿真系统将应用于人类生产实践的全过程,这样可以避免决策失误,可以预测可能发生的问题,达到避免故障、安全控制的目的。
有关专家预言,在21世纪,仿真技术的发展必将对经济、社会以及人们的观念产生巨大影响。
由此可见,本文研究的将基于Flexsim仿真软件的仿真方法和物流配送中心的优化相结合,具有较大的实际意义。
物流仿真的优势在于不管实际物流系统是否存在,均可通过建立系统研究模型,将实物数据输入仿真系统,通过数据运算和图形模拟,产生贴近实际物流系统的信息输出。
仿真试验具有良好的可控性、无破坏性和可重复性。
仿真过程经济安全,不受气象条件和场地环境的限制。
仿真的实时性,使实时系统的仿真应用成为可能,为仿真应用奠定了良好的基础。
物流仿真给评估对象系统(配送中心、仓库存储系统、拣货系统、运输系统等)的整体能力提供一种评价方法物流仿真技术在复杂物流系统的分析和决策中的巨大价值在欧美己成为不争的事实,每年创造着数以千亿美元的经济效益。
二、配送中心模型的仿真优化
2.1某物流配送中心概述
配送中心仿真不仅可以为即将建立的配送中心提供方案评估及论证依据,而且也可以对已建成配送中心的经济效益及人员、设备配置的合理性进行科学评价,从而避免资金、人力和物力的浪费,提高配送中心的综合效益,为消除配送中心运行瓶颈、挖掘配送中心发展潜力提供科学、合理的理论依据和决策支持。
本文所研究的配送中心接收上游3个供应商提供的3种不同类型的产品,由产品入库区、产品储存区、产品分拣区、产品出库区四个主要功能区组成。
配送中心功能区分布如下图所示。
2.2配送中心人员及设备配置及建模
2.2.1配送中心人员及设备
(1)入库区:
由2个产品入库口,2个入库加工台,2个组盘器,1个托盘入库口,组成。
配送中心共有200个托盘,入库区中每个托盘可以装载8个单位产品。
(2)储存区:
由2个货架和1台自动堆垛机组成,堆垛机负责相应货架的出入库作业。
3个货架均设置成10行10列,每个货格只允许存放一个托盘货物,即每个货架存储托盘的最大量为100。
考虑到存储成本和安全库存量,结合各类货物的以往销售数据设置货架,当存储量大于80时自动关闭输入端口,当存储量小于20时自动开启输入端口。
(3)分拣区:
由1个拆盘器,1个托盘暂存区,1个产品暂存区,2个产品传送带组成。
其中,2个拆盘器负责从储存区进入的对应托盘产品的拆盘作业,把拆卸下来的空托盘放入托盘暂存区,并把产品放入对应的产品暂存区。
当订单来临时,拣选操作人员负责按照订单要求的数量将所需产品送至打包台进行打包作业,订单为固定的,由全局表查看分拣。
为了更好地控制整个配送中心的作业流程,分拣区内的产品暂存区的最大容量均设置为100。
(4)出库区:
由1个组盘器,2个传送带,1个产品接收器组成。
出库区主要功能是把按订单打包好的产品按预先设定好的配送路线进行分类整理,并放置到对应的产品暂存区。
2.2.2配送中心人员及设备建模
上节所列配送中心需要用到的实体设备均可在Flexsim仿真软件的实体库里找到对应的仿真对象,不需导入使用AutoCAD等绘图工具制作的三维文件。
配送中心实体设备与Flexsim仿真软件实体库仿真对象的对应关系如i
表1所示。
表1配送中心实体设备与Flexsim实体库对象对应
实体设备
Flexsim仿真软件实体对象
产品
发生器(2个)
托盘
发生器(1个)
入库加工台
处理器
组盘台、打包台
合成器
堆垛机
堆垛机
高架库
货架
产品分拣
分解器
暂存区
暂存区
订单配备
合成器
客户
吸收器
2.3配送中心系统流程及仿真
2.3.1配送中心系统流程介绍
该配送中心的系统流程分为以下两个主要环节:
入库储存和出库分拣,其运作流程分别如图2(a)和(b)所示。
2.3.2配送中心流程仿真
在对配送中心人员、设备进行分析、配置的基础上,构建其整体仿真模型。
(1)入库区实体及参数设置
入库区由3个生成器,2个处理器,2个合成器组成。
入库区参数设置如下表2:
表2入库区实体及参数设置
实体名称
对象说明
参数设置
产品发生器1,2
发生器
1,2到达时间间隔分别服从均匀分布(7,11,1);(6,10,1)
托盘发生器
发生器
固定到达时间间隔为6分钟
入库加工区1,2
处理器
固定加工时间为2分钟
打包器1,2
合成器
加工时间为10分钟,每个托盘上放8件产品
(2)储存区实体及参数设置
储存区由2个货架和1个堆垛机组成,储存区实体参数设置如表3所示:
表3储存区实体及参数设置
实体名称
对象说明
参数设置
高架库1,2
货架
货架设置成10行10列,最大容量为100,每个货格存放一个托盘产品,当货架的存储量达到80个时,系统将关闭货架的输入端口;当存储量减少到20个时,系统将自动打开货架的输入端口继续补货。
堆垛机20
堆垛机
每次运送数量设为1,最大工作速度为2分钟
(3)分拣区实体及参数设置
分拣区由1个拆盘器,1个托盘暂存区,1个产品暂存区,2个产品传送带组成。
分拣区实体参数设置如表4所示。
表4分拣区的实体及参数设置
实体名称
对象说明
参数设置
拆盘器
分解器
参数保持默认设置
产品、托盘暂存区
暂存区
产品暂存区的最大容量为100
传送带4,5
传送带
传送速度为0.5
(4)出库区实体及参数设置
出库区由1个组盘器,2个传送带,1个产品接收器组成。
出库区实体参数设置如表5所示:
表5出库区实体及参数设置
实体名称
对象说明
参数设置
组盘器
合成器
加工时间为20分钟
传送带6
传送带
参数设置保持默认
产品接收器
接收器
参数设置保持默认
三、仿真结果与数据分析
3.1仿真数据收集
表6仿真运行数据表
FlexsimStateReport
Time:
86400
Object
Class
idle
processing
blocked
产品发生器1
Source
0.00%
0.00%
95.07%
入库加工区1
Processor
0.01%
65.79%
34.20%
高架库1
Rack
100.00%
0.00%
0.00%
堆垛机20
ASRSvehicle
92.21%
0.00%
0.00%
拆盘器
Separator
98.70%
1.30%
0.00%
入库加工区2
Processor
0.01%
65.51%
34.48%
打包器1
Combiner
0.25%
40.97%
0.00%
产品发生器2
Source
0.00%
0.00%
95.61%
托盘发生器
Source
0.00%
0.00%
27.40%
托盘暂存区
Queue
0.00%
0.00%
0.00%
打包器2
Combiner
0.55%
40.28%
0.00%
高架库2
Rack
100.00%
0.00%
0.00%
产品暂存区
Queue
0.00%
0.00%
0.00%
传送带4
Conveyor
0.00%
0.00%
92.90%
传送带5
Conveyor
0.00%
0.00%
93.30%
组盘器
Combiner
17.05%
76.89%
0.00%
传送带6
Conveyor
0.00%
0.00%
0.00%
吸收器
Sink
0.00%
0.00%
0.00%
3.2仿真优化
3.2.1优化目的
在物流配送中心规模的确定过程中进行深层次的量化及细化,在预定的区域内合理的布置好物流中心各功能块的相对位置时物流配送中心规划的重点。
配送中心优化的目的可以概括为
(1)有效利用空间、设备、人员和能源;
(2)最大限度的减少物料搬运;
(3)简化作业流程;
(4)缩短生产周期;
(5)力求投资最低;
(6)为职工提供方便、舒适、安全、卫生的工作和休息环境。
3.2.2效率分析及系统优化
各个功能区参数设置好后运行仿真模型,观察仿真数据,可以看出一些参数设置得不够合理。
比如,货架1,2的最大存货量为3箱,平均存货量仅为0.17箱,也就是说货架上基本没有存货,托盘经过组盘合成器进入储存区后很快又被运出至分拣区,仓库利用率很低,造成这种现象的主要原因是产品入库加工和组盘的速度赶不上分拣的速度,以至于产品停留在储存区的时间很短。
除此之外,组盘器的收集订单所占时间比率太大,说明分拣效率太低,常常需要等待;打包器的等待运输时间过长,堆垛机的空闲率太高,说明相对应的堆垛机的运行效率设置得不合理;反映出组盘时间过长和分拣效率太低,经常造成设备和人员的闲置。
对以上仿真数据进行分析,可以看出,配送中心的综合效率和重要性能指标跟入库区的工作效率、储存区的存货策略以及分拣区人员、设备是否协调运作都有直接的关系。
下面分别从补货策略、人员、设备数量及设备工作效率等方面对模型进行优化分析。
1.改变储存区安全库存
原来模型中设置当货架存量大于80时,关闭货架的输入端口,停止补货;当货架存量小于20时打开货架的输入端口,继续补货,这样造成货架的利用率较低。
为了提高货架的利用率和平均存货量,可以设置当货架存量大于90时停止补货,当货架存量小于50时继续补货。
2.提高人员、设备效率
在原模型中,打包器的收集时间和等待时间均较长,原因是产品到达速度较慢和堆垛机效率较低,为了使这一作业能更好的衔接,可以加快产品入库速度,同时提高堆垛机的工作效率。
3.2.3优化结果
表7仿真优化结果表
FlexsimStateReport
Time:
86400
Object
Class
idle
processing
blocked
产品发生器1
Source
0.00%
0.00%
93.30%
入库加工区1
Processor
0.01%
89.03%
10.96%
高架库1
Rack
30.00%
0.00%
0.00%
堆垛机20
ASRSvehicle
89.38%
0.00%
0.00%
拆盘器
Separator
42.83%
57.17%
0.00%
入库加工区2
Processor
0.01%
88.16%
11.84%
打包器1
Combiner
15.71%
0.00%
0.00%
产品发生器2
Source
0.00%
0.00%
94.12%
托盘发生器
Source
0.00%
0.00%
16.84%
托盘暂存区
Queue
0.00%
0.00%
0.00%
打包器2
Combiner
16.26%
0.00%
0.00%
高架库2
Rack
30.00%
0.00%
0.00%
产品暂存区
Queue
0.00%
0.00%
0.00%
传送带4
Conveyor
0.00%
0.00%
55.71%
传送带5
Conveyor
0.00%
0.00%
55.31%
组盘器
Combiner
1.20%
54.81%
0.00%
传送带6
Conveyor
0.00%
0.00%
0.00%
吸收器
Sink
0.00%
0.00%
0.00%
1、通过与仿真优化之前对比,高架库,拆盘器等的空闲率明显下降,提高了设备的利用率,工作效率有所提升。
2、设备高度集成,外形统一协调,与分拣效率相同的设备相比占地面积小。
整个分拣系统内的作业流程清晰明了。
四、课程设计小结
本次课程设计中,我们小组五个人首先确定了设计方案,制定了具体的计划,明确了设计的时间安排和分工情况,使设计变得有章可循,井井有条。
我认为,这是我们设计的良好开端,对于设计的成功进行具有重要意义。
设计过程中,我们发现,计划赶不上变化,设计中,遇到了好多的问题,这是我们之前并没有料到的,比如设计软件服务器故障,只能添加20个以内的控件;软件经常出现意想不到的问题等。
这些意料之外的问题给设计加大了难度,也给我们增加了挑战。
我们通过查找资料,团结协作,客服重重阻碍,终于完成了设计。
设计增加了我们对于Flexsim软件的了解,对配送中心的工作流程和布局认识也更为深刻。
同时,设计中锻炼了毅力,增强了友谊,收益颇丰。
设计中一定还有很多的不完美,希望老师能够批评指教,让我们的设计成果更实用,更完美。
五、参考文献
1.王红卫、谢勇、王小红等《物流系统仿真》北京清华大学出版社2009
2.彭阳、吴承建《物流系统建模与仿真》杭州浙江大学出版社2009
3.张晓平、王玉坤《系统仿真软件Flexsim3.0实用教程》北京
清华大学出版社2006
4.刘志强、丁鹏等《物流配送系统设计》北京清华大学出版社2004