轧钢厂生产准备技术操作规程.docx
《轧钢厂生产准备技术操作规程.docx》由会员分享,可在线阅读,更多相关《轧钢厂生产准备技术操作规程.docx(12页珍藏版)》请在冰豆网上搜索。
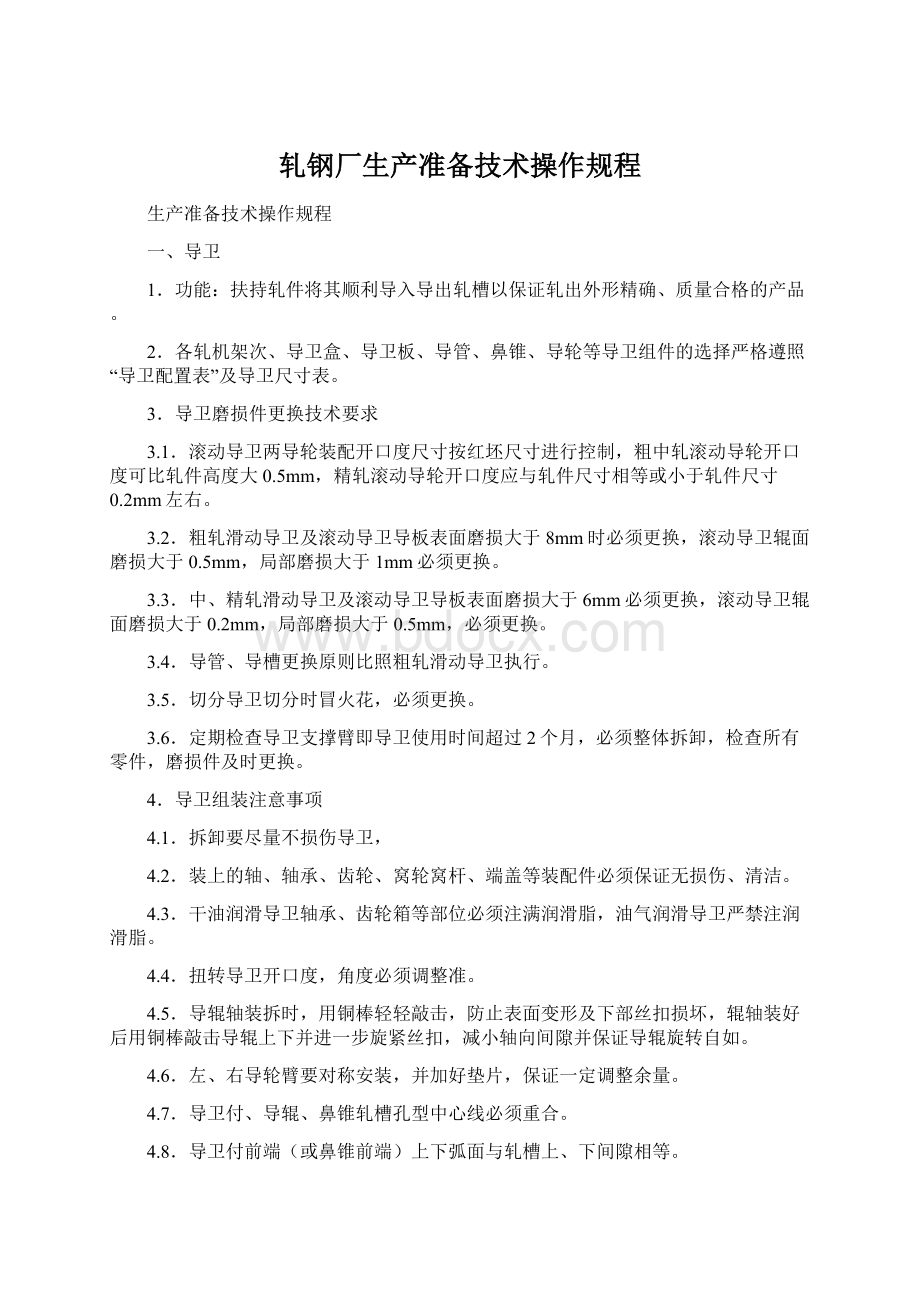
轧钢厂生产准备技术操作规程
生产准备技术操作规程
一、导卫
1.功能:
扶持轧件将其顺利导入导出轧槽以保证轧出外形精确、质量合格的产品。
2.各轧机架次、导卫盒、导卫板、导管、鼻锥、导轮等导卫组件的选择严格遵照“导卫配置表”及导卫尺寸表。
3.导卫磨损件更换技术要求
3.1.滚动导卫两导轮装配开口度尺寸按红坯尺寸进行控制,粗中轧滚动导轮开口度可比轧件高度大0.5mm,精轧滚动导轮开口度应与轧件尺寸相等或小于轧件尺寸0.2mm左右。
3.2.粗轧滑动导卫及滚动导卫导板表面磨损大于8mm时必须更换,滚动导卫辊面磨损大于0.5mm,局部磨损大于1mm必须更换。
3.3.中、精轧滑动导卫及滚动导卫导板表面磨损大于6mm必须更换,滚动导卫辊面磨损大于0.2mm,局部磨损大于0.5mm,必须更换。
3.4.导管、导槽更换原则比照粗轧滑动导卫执行。
3.5.切分导卫切分时冒火花,必须更换。
3.6.定期检查导卫支撑臂即导卫使用时间超过2个月,必须整体拆卸,检查所有零件,磨损件及时更换。
4.导卫组装注意事项
4.1.拆卸要尽量不损伤导卫,
4.2.装上的轴、轴承、齿轮、窝轮窝杆、端盖等装配件必须保证无损伤、清洁。
4.3.干油润滑导卫轴承、齿轮箱等部位必须注满润滑脂,油气润滑导卫严禁注润滑脂。
4.4.扭转导卫开口度,角度必须调整准。
4.5.导辊轴装拆时,用铜棒轻轻敲击,防止表面变形及下部丝扣损坏,辊轴装好后用铜棒敲击导辊上下并进一步旋紧丝扣,减小轴向间隙并保证导辊旋转自如。
4.6.左、右导轮臂要对称安装,并加好垫片,保证一定调整余量。
4.7.导卫付、导辊、鼻锥轧槽孔型中心线必须重合。
4.8.导卫付前端(或鼻锥前端)上下弧面与轧槽上、下间隙相等。
4.9.入口导卫付,内膛宽度必须保证轧件按孔型设计要求准确导入轧槽。
4.10.出口导管安装必须保证轧机顺利脱槽,并走向正直。
导管前端(或鼻锥前端)与轧槽吻合。
4.11.导卫组装完毕后,应将导卫型号、架次、品种规格标于导卫上或挂标牌。
4.12.粗轧导卫安装时,距离轧辊5mm;中轧导卫安装时,距离轧辊4mm;精轧导卫安装时,距离轧辊3mm。
4.13.导卫组装完成后,必须用压缩空气检查油路和水路。
4.14.导卫间隙与样棒尺寸相比较应小于或等于0.1mm,这样能够保证导卫与料型形成一定的夹持力。
4.15.切分导卫15、16架进口在装配时一定要注意蜗轮蜗杆的调整,在上线前必须认真检查调试,做到能够调整导卫夹持力。
即在调整导卫时,左右两排导轮能够同时向内外移动,形成均匀的夹持力。
5.导卫摆放原则
5.1.滚动导卫
a.滚动导卫总成按机架(大类)、成品规格(小类)的优先等级堆放。
b.导轮、插入件按导卫型号(大类)、孔型(小类)的优先等级来堆放。
c.滚动导卫盒按导卫型号堆放。
5.2.滑动导卫按机架(大类)、规格范围(小类)的优先等级来堆放。
5.3.鼻锥、导板、导管按类型、规格的优先等级来堆放。
二、车床
1.功能:
轧辊车床用于车削轧槽,铣床用于铣螺纹筋
2.车床操作
2.1.必须掌握并灵活运用轧辊车削技术及数控铣床的操作技术。
2.2.熟悉车床上手柄、按钮的作用,并能准确操作。
2.3.掌握各附件、工具、量具、样板等的使用性能及精度,准确使用。
2.4.吊装或拆装轧辊时应小心,以免碰坏卡盘及顶针。
2.5.工作前对轧辊各部尺寸对照图纸认真检查合格后方可加工。
2.6.根据工件形状、材质、技术要求、机床负荷能力,合理选择装卡方法、切削量、加工步骤。
2.7.精密量具、工具、样板、使用前要校准,复核其尺寸,测量要准确,禁止用精密量具测量粗糙表面。
2.8.严格按车床技术操作规程进行操作。
2.9.为提高产品质量及生产效率,操作者有权及责任提出合理化建议。
2.10.对质量、设备事故,要认真分析研究,共同吸取教训。
三、轧机装配
1.设备名称:
闭口轧机、短应力轧机
型号:
粗轧机组1H—4V:
φ550闭口轧机
粗轧机组5H、6V中轧机组7H—10V:
φ450闭口轧机
中轧11#、12#、精轧机组:
φ350短应力轧机
2.设备技术参数
轧机型号
φ550闭口轧机
φ450闭口轧机
φ350短应力轧机
最大轧辊工作中心距(mm)
640
495
380
最小轧辊工作中心距(mm)
520
420
330
辊颈尺寸(mm)
340
280
200
辊身长度(mm)
800
700
650
最大轧制压力(KN)
2730
1356
1300
轴向调整量(mm)
±5
±5
±3
轴向调整螺母
每转一圈调整量(mm)
0.341
压下机构旋转一小格
辊缝调整量(mm)
0.255
3.组装轧机前的准备工作
3.1.轧辊的检验
检验孔型:
用孔型样板严格测量孔型,确认是当前所准备的规格;不合格的轧槽涂红漆。
另附轧辊检验标准。
3.2.迷宫圈的安装
安装前擦净辊颈,将迷宫圈放在轴承感应加热器上加热,温度为120℃(可以用加热时间来恒定),当温度加热到120℃即可往辊颈上装配,安装时可以用铜棒轻打迷宫圈的外圆端面,装上后顶住迷宫圈的外圆端面,防止冷却收缩时轴向回松。
3.3.轴承内圈的安装
加热前用卫生纸擦净内圈表面上的油污,然后放在轴承加热器上加热。
加热温度为T夏=70℃,T冬=85℃,当温度达到要求后装到辊颈上,安装过程中可以用铜棒轻轻敲打,保证装配到位。
4.φ350轧机的组装程序
4.1.确认孔型无误后,把装有迷宫圈及轴承内圈的一对轧辊吊到拆辊装置的轧辊小车(即中间小车)上并注意轧辊辊身在小车左右横梁上的对称性,同时锁紧轧辊,防止轧辊在水平方向滚动。
再次确认轧辊孔型无误。
4.2.从轧机支座上松开导卫横梁固定螺栓,吊走导卫横梁。
4.3.脱开机架支座上与机芯平衡缸、液压马达、油气润滑管快速接头;松开支座联结螺栓,吊出机芯到拆辊装置横向小车上,在手动阀台上操作横向小车到轧辊小车附近,保证两轧辊垂直中心线和左右轴承座中心线重合。
4.4.调节轧辊中心线在水平方向标高(通过偏心轴的转动)直到上下辊水平方向中心线和上下轴承座对应中心线重合,测出标准辊缝试块高度待以后使用,还有定好两辊中心线后,锁定偏心轴,以后再装时可以不用转动。
辊颈及轴承内加润滑油。
4.5.慢慢点动轴承座小车,直到两小车全部前进到位(即横向两小车到位)不得有卡阻。
辊颈进入轴承座过程中应为自由状态。
4.6.装上止推轴承压盖定位销,旋紧辊头螺栓,并对好防松内六角、旋紧。
4.7.松开轧辊锁紧装置,抽掉插板。
调辊缝,用塞尺测量,
4.8.将装配好的机架吊到机架底座上,拧紧拉杆螺栓。
4.9.由“F”形扳手来卡住传动端,将每只轧辊转动数圈,使轧辊扁头定位在要求的位置,转动中不得有卞阻。
4.10.接上液压马达,平衡缸及油气润滑管快速接头。
4.11.将与该架轧机孔型对应的导卫横梁固定好,确保横梁装正,将导卫固定在横梁上,调整导卫,接上导卫水冷管和油气润滑管,装好轧槽冷却水管。
4.12.在轧机上标明架次、规格。
4.13.另附轧机检验标准。
5.注意事项
5.1.待装轧辊的辊颈尺寸及内圈尺寸严格测量,防止过盈量太小,而导致内圈游动。
5.2.所装轧辊孔型必须确认以防装错。
5.3.迷宫圈及内圈的加热温度应控制在要求的温度。
5.4.组装轧机时辊颈及轴承中必须加入少量润滑油。
5.5.凡需在换辊机器人上调节辊缝时,应同时连上液压马达软管和平衡缸软管,只要两侧轴承座中心标高相同,原则上不脱开马达接手来单侧手动调整辊缝。
5.6.轧机装配时避免轴错。
5.7.轧辊咬入不良时,做轧辊表面粗糙处理。
5.8.检查配管,确保配管完好,否则及时更换。
5.9.轧槽冷却水管与所用轧槽对正。
四、拆辊装置操作说明
1.说明
1.1本说明适用于ZJD-350×650-Ⅲ型高刚度轧机。
1.2拆辊装置用于轧机本体的拆装辊。
1.3450、550拆辊装置参照本说明。
2.注意事项
2.1在拆装辊时,必须将轧辊中心距调至A=430mm。
并且要用专用垫块放置在机架支脚和轴承座之间。
2.2吊运轧机本体时必须使用专用吊具,保证轧机吊运时的平衡。
3.技术性能和操作
3.1技术性能
(1)设备图号:
DC12709
(2)轧辊辊身长:
650mm
(3)更换轧辊中心距:
430mm
(4)中心小车移动液压缸:
Ø80/Ø56×1200
(5)中心小车移动最大距离:
1200mm
(6)分离小车移动液压缸:
Ø80/Ø56×710
(7)分离小车移动最大距离:
710mm
(8)移动速度max0.07m/s
3.2拆辊装置说明
该装置由一个纵横底板,一个中心小车,两个分离小车组成。
底板:
底板由钢板焊接而成,利用地脚螺栓固定在基础上,上下表面通过高精度机加工来满足表面的精度,横纵中心的垂直度。
上表面有V型定位导轨和平导轨支撑小车运行。
中心小车:
中心小车有4个滚动轮,内有滚动轴承,其中二个轮子为V型槽,满足V型轨道,另外二个为平滚轮,以确保小车直线运行。
小车上有两对支持新旧轧辊的支架,一个支架放置两根新轧辊(或重车辊),另一个放置待更换轧辊的轧机本体,两个下辊由四个带楔块的垫杆支撑并定位。
每个垫杆的一端由固定销固定,保证轧辊放置的正确位置。
垫杆的另一端有一调节轧辊轴承位置的调节螺纹装置支撑,供调节轧辊放置中心不平时调整用。
在轧辊从轴承座的插入,抽出时,用调节螺纹装置可对不同轧辊重量与轴承座之间间隙进行调整。
轧辊与轴承座的精确位置通过手动调节螺纹装置来完成。
两个上轧辊由4个手动垫杆来支撑,其精确定位由手动调节螺纹来完成。
垫杆的一端由固定销支撑,另一端由螺纹带动凸轮装置支撑,原理与下杆相似。
导卫板的开启便于机架插入和抽出。
以上操作均由手动操作。
分离小车:
两分离小车各自独立工作,每个小车由液压缸驱动。
每个小车均有四个轮子,两个平滚轮,两个V型滚轮,确保小车的直线运行。
小车的上部有两个支持轧辊的支架,其中一个支架,放有两个新轧辊(或重车轧辊)准备更换,另一个放置待更换轧辊的新机架,两个下轧辊由四个带楔块的垫杆定位。
两个上辊由垫杆支撑,垫杆的一侧由固定销支撑,以保证正确定位,垫杆的另一侧带有螺纹调整装置,在轧辊由轴承座插入及抽出时,用该调整装置可对不同重量轧辊与轴承座间隙进行调整。
两个上辊由两个垫杆支撑,其结构和作用与上轧辊相似,导卫板的开启便于机架的插入和抽出。
以上操作均由手工完成。
分离小车:
两个分离小车各自独立工作,每个小车的行程由液压缸行程决定。
每个小车有四个轮子,两个平滚轮,两个V型滚轮,确保小车的直线运行。
小车上部用来固定轧机本体,上有支撑轧机本体的支撑块和固定用吊环螺栓。
供拆装辊时与轧机本体固定一体。
拆辊装置配有专用液压站及控制阀架(由用户配置),供分离小车及中心小车运动,在控制阀架上有联接轧机本体上的液压管路的快换接头。
接头的数量由轧机的配置形式决定。
4.使用说明
4.1设备使用前的检查
1)检查液压回路中有无气泡,若有用放气螺栓放气。
2)中间小车及横向小车的联锁灵活。
3)检查地面站上小车运动的警示灯是否完好。
4)检查机器人的位置正确与否。
5)检查手动润滑点的润滑情况。
6)检查液压回路中的油量。
7)检查液压缸及管线有无泄漏。
8)看小车运动时有无震动及杂音。
4.2换辊的准备:
1)将已装好迷宫环和支撑内套的新辊放到中心小车上,对靠近分离小车的“O”“P”表面涂好润滑油脂。
必须确保轴承内套的安装与拆卸时的加热温度不超过100℃
2)靠近分离小车,装上上支撑垫杆“A”。
3)用连杆“B”在靠近分离小车处打开定位板“C”。
4)检查中心小车“G”是否在其行程的极限位置。
5)启动液压缸将分离小车“E”和“F”移动到其行程的极限。
6)将调整块“D”放在固定支脚与两个轴承座之间。
7)移开导卫和所带的导卫梁。
8)拆走所有与轧机本体连接的软管。
9)松开固定支脚到机架支座的吊环螺栓。
10)将软管的快速接头接通液压马达和轧辊平衡(带平衡装置的轧机)将轧辊中心距调至430mm后拆下。
4.3轧辊的更换
1)用吊车和特殊的平衡梁提起机架并将其放在拆辊装置上,尽量用手帮助定位,直到机架支脚距离分离小车上支撑表面约5mm时,但不允许接触该表面。
2)插入上垫杆“A”
3)将机架放到分离小车上,用吊环螺栓H紧固支脚。
4)用连杆“B”锁紧定位“C”。
5)拆下压下调整机构“Q”的联轴器,移走轧辊轴向锁紧使用的螺栓“R”“S”,将机架放在分离小车上。
6)缓慢开动分离小车,检查行进中是否有阻碍,注意不能有阻力,直到轧辊脱离轴承座,此后可加速移动分离小车直至到其行程的极限。
7)检查径向轴承是否仍然完好,有无氧化铁皮等杂物。
如果情况良好,迷宫环外表面足够清洁(小心不要将脏物带进轴承中)。
如果径向轴承目视有磨损必须更换它们。
也用同样的方法检查推力轴承。
如果在径向轴承的滚柱中存在过量的杂质和碎片,需将推力、径向轴承都拆下来,用油清洗干净。
8)启动液压缸使中心小车横移,以便使新轧辊就位。
9)首先移动分离小车靠近,轴承内套距迷宫环约20mm处停止。
10)检查轴承内圈和迷宫环引入位置是否正确。
11)其次缓慢移动分离小车,确认轧辊与轴承座插入时无阻碍后,再将分离小车移动到其极限位置。
12)连接压下调整机构的联轴器“G”并锁紧螺栓,然后在锁紧轴向调整螺栓“S”,并用螺帽“R”再次紧固它们。
13)松开紧固机架支脚和分离小车的吊环螺栓“H”,并拆下。
14)使用吊车和特殊平衡梁,将机架吊起约5mm,并移走上垫杆“A”。
15)从拆辊装置中吊起机架放到轧机本体的支座上,用特殊的吊环螺栓紧固。
4.4轧机的生产准备:
4.4.1用手动干油泵给径向和轴向轴承填充润滑油脂,直到可以看到油脂从迷宫密封中流出,并给迷宫密封本身注油脂。
4.4.2连接支架与支撑座间所有的软管,装上导卫梁、导卫和冷却水管。
4.4.3将机架内轧辊的扁头正确定位,以便于伸缩接轴顺利插入。
4.5.设备使用过程紧急情况的处理规定
4.5.1.移动横向小车时,若有卡阻现象,应立即操作,查明原因。
4.52.出现软管及其连接处油漏,立即停止操作。
4.5.3.横向小车前进时,若轧辊磕撞轴承,应立即停止。
摆正轧辊后再缓慢移动小车。
4.6.交接使用的规定
4.6.1.机器人使用完毕后,清理杂物及油污。
4.6.2.小车位于液压缸完全关闭的位置。
4.6.2.机器人使用完毕后应关闭电源。
5.液压系统技术说明
油品N46抗磨液压油
泵能力26升/分
压力12Mpa
6.维修及保养
6.1如果拆辊装置各种功能正常,车轮表面应必须经常保持清洁。
因此,每次换辊后应进行清扫。
因为表面的污物将被车轮碾压,容易使车轮本身产生变形,使小车的行进时不是直线运动,使小车运动时产生颠簸。
6.2调整螺纹内的衬套每月也应人工加油润滑。
6.3每年对导卫板的凸轮座二次,每年要检查二次液压缸是否有渗漏现象。
每个液压缸至少要备有一套密封圈。
6.4中心小车和分离小车
6.4.1每换辊十次至少要进行一次检修。
6.4.2每年都要对小车车轮轴承和偏心情况进行检查。
6.5吊至机器人的轧机应清洗并吹干。
6.6每周清洗机器一次。
6.7所有油管及管道的磨损情况每周检查一次。
6.8.小车轮子应经常保持干净。
6.9每日检查一次轴承及辊支撑部位的磨损。
6.10每周检查一次小车滑动装置的间隙。
6.11时常检查轮子处的轴承及边缘部位。
6.12小车润滑部位的润滑油每月检查一次。
五、轧辊加工与管理
1.轧辊的验收(光辊)
粗轧机轧辊、中轧机轧辊、精轧机轧辊分别按图纸上的尺寸精度进行验收。
特别注意扁头、轧辊轴肩外用样板测量,轴头螺栓孔的尺寸是否符合要求,不符合要求的新辊退货。
2.轧辊辊径的使用范围
机组
机架号
轧辊直径mm
最大辊径
最小辊径
粗轧机组
1#——4#
610
520
5#、6#
495
420
中轧机组
7#——10#
495
420
11#、12#
495
420
精轧机组
13#——18#
380
330
3.轧辊开槽
3.1.新轧辊开槽,必须严格按图纸要求车削。
轧槽加工精度见下表:
孔型分类
粗轧机
中轧机
精轧机及切分孔
成品孔
轧槽允许误差
±0.35mm
±0.25mm
±0.1mm
±0.05mm
带肋钢筋成品光圆孔允许偏差(内径):
±0.1;
3.2.旧轧辊重车修复,开槽标准如下表:
机架
轧辊最大直径(mm)
轧辊最小直径(mm)
上/下辊径差(mm)
辊身椭圆度
辊身与辊颈同轴度
重车量(mm)
1#~4#
610
520
≤1
≤0.3
≤0.15
≤10
5#~10#
495
420
≤0.5
≤0.1
≤0.08
≤8
11#~18#
380
330
≤0.2
≤0.1
≤0.05
≤8,螺纹钢成品孔光刀无裂纹
预切分
380
330
≤0.1
≤0.1
≤0.05
≤8
切分孔
380
330
≤0.1
≤0.1
≤0.05
≤8
4.带肋钢筋月牙槽加工:
加工要求按国家标准及公司、分厂有关要求执行。
注:
加工的孔型若不合格涂红漆。
5.轧辊验收标准
5.5.1.样板检验标准
1)样板加工后必须除去毛刺,注明孔型代号;
2)样板孔型部分粗糙度小于6.3;
3)样板与孔型的车削间隙:
成品孔≤0.05mm;粗轧孔型≤0.15mm;其它孔≤0.1mm;
4)对于不符合规定的样板及时修复,孔型修改后应及时做新样板;
5)样板严格按照样板图加工制作。
5.5.2.辊的验收
用样板测量加工过的每个轧槽,孔型与样板尺寸相符合;带肋钢筋月牙槽加工检验重点检查横肋数和横肋高。
6.轧辊的存放
5.6.1.所有辊按孔型代号成对放置到辊架上;
5.6.2.加工后的轧辊按轧辊验收标准验收合格后及时放到相应位置;
5.6.3.报废辊、断辊待拆下迷宫圈及内套送回收站。
5.6.4.对每月的生产计划品种规格做到心中有数,为生产备足相应轧辊。
5.6.5.对轧辊在加工及使用中出现的问题及时掌握,解决问题。
7.轧辊备用情况
1#~4#轧辊用1备4套;成品轧辊用1备5套;预切分孔、切分孔轧辊用1备4~6套;其它架次轧辊备4套。