01004动力工艺规程.docx
《01004动力工艺规程.docx》由会员分享,可在线阅读,更多相关《01004动力工艺规程.docx(19页珍藏版)》请在冰豆网上搜索。
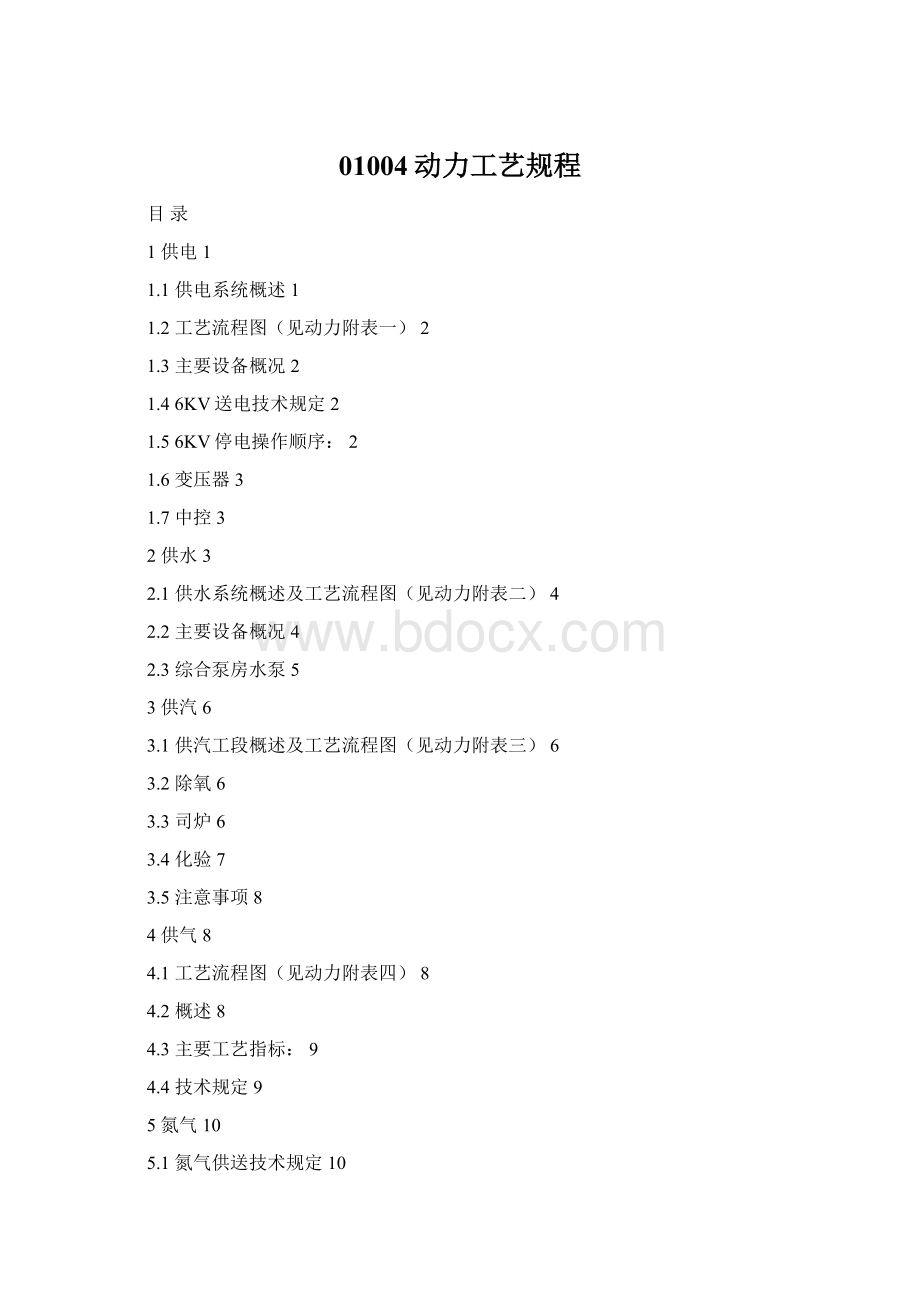
01004动力工艺规程
目录
1供电1
1.1供电系统概述1
1.2工艺流程图(见动力附表一)2
1.3主要设备概况2
1.46KV送电技术规定2
1.56KV停电操作顺序:
2
1.6变压器3
1.7中控3
2供水3
2.1供水系统概述及工艺流程图(见动力附表二)4
2.2主要设备概况4
2.3综合泵房水泵5
3供汽6
3.1供汽工段概述及工艺流程图(见动力附表三)6
3.2除氧6
3.3司炉6
3.4化验7
3.5注意事项8
4供气8
4.1工艺流程图(见动力附表四)8
4.2概述8
4.3主要工艺指标:
9
4.4技术规定9
5氮气10
5.1氮气供送技术规定10
5.2氮气停送技术规定10
5.3氮气切换压缩空气的技术规定10
5.4压缩空气切换氮气的技术规定11
5.5注意事项11
6污水处理11
首钢长治钢铁有限公司瑞达公司作业文件
动力工艺技术规程
ZY.24.01.004—2012
1供电
1.1供电系统概述
本厂供电系统由长钢1#总变电站(距本厂0.8km)提供双回路6KV供电电源到201、202变电所。
201变电所为供水系统及化产区供电。
负责新鲜水、循环水、复用水系统、生化处理、冷鼓电捕、制冷站、脱硫、硫铵、洗脱苯、锅炉房、空压站及加压站等的高低压设备工号供电,并负责中心化验室办公楼的供电。
202变电所负责炼焦、熄焦、备煤和筛焦等工号的高低压用电设备的供电。
并负责炼焦车间办公楼、仓库、二建和全厂照明等工号的供电。
201、202变电所均采用微机监控保护系统。
全厂总装机容量:
11987.58kW,其中6kV负荷装机容量3600kW。
常用容量:
8964.76kW,其中6kV负荷容量2200kW;需要容量:
4792.04kW,其中6kV负荷需要容量1548.8kW。
201变电所380V负荷装机容量为4159.89kW;常用容量为2915.79kW;需要容量为2175.44kW,变压器选用两台1250kVA变压器和两台1600kVA变压器,负荷率54.39%,6kV负荷装机容量为2100kW;常用容量为1190kW,需要容量为952kW。
202变电所380V负荷装机容量为3813.69kW;常用容量为3394.97kW;需要容量为1241.11kW,变压器选用两台1600kVA变压器,负荷率38.78%,6kV负荷装机容量为1460kW;常用容量为1010kW;需要容量为808kW。
电容无功补偿采用低压集中补偿方式,使6kV进线侧功率因数达到0.95以上。
所有工艺生产装置及管线,按工艺及管道要求做防静电接地。
接地点一般不少于两点。
建(构)筑物防雷按第二类防雷建(构)筑物设计,部分按第三类防雷建(构)筑物设计。
1.2工艺流程图(见动力附表一)
1.3主要设备概况
设备名称
规格型号
台(套)数
主要技术参数
备注
变压器
S9-1600kVA/6.3kV/0.4kVD,yn11
4
阻抗电压4.42%
变压器
S9-1250kVA/6.3kV/0.4kVD.Yn11
2
阻抗电压4.42%
高压开关柜
KYN28-12
36
低压开关柜
MNS
61
1.46KV送电技术规定
1.4.1合上要送电回路的控制开关。
1.4.2将接地刀开关置于断开位置。
1.4.3检查手车的位置,在试验位置上进行试验分、合操作,正常后,将断路器置于断开位置。
1.4.4摇断路器置于工作位置。
合上储能开关使操作机构处于储能状态。
1.4.5确信以上步骤无误后,合上断路器。
1.4.6检查各指示灯和指示仪表正常后,操作完毕。
1.56KV停电操作顺序:
1.5.1核对要停电的线路。
1.5.2断开真空断路器。
1.5.3将手车从工作位置摇至试验位置。
1.5.4将接地刀开关合上。
1.5.5断开控制电源开关。
1.6变压器
1.6.1变压器投运和停运工艺技术规定
1.6.2在投运变压器之前,值班人员应仔细检查,确认变压器及其保护装置在良好状态,具备带电运行条件。
并注意外部有无异物,临时接地线是否已拆除,分接开关位置是否正确,各阀门开闭是否正确。
变压器在低温投运时,应防止呼吸器因结冰被堵。
1.6.3运用中的备用变压器应随时可以投入运行。
长期停运者应定期充电,同时投入冷却装置。
1.6.4大修、事故检修或换油后的变压器,在施加电压前静止时间不应少于以下规定:
6KV等级为24小时。
1.7中控
1.7.1配电中控室工艺系统概述:
配电中控室为动力车间工艺总监控点,一台电脑分别监视锅炉房、水泵房、空压站的工艺运行工况即初冷器温度、制冷循环水温度、化产循环水温度、生产消防水压力、工艺用气压力、仪表用气压力、除氧器温度、蒸汽分缸压力、工艺用汽流量和供暖用汽流量;另一台电脑监视201、202高压系统的运行及后台保护。
1.7.2配电工负责对各种工艺参数进行记录、判断、汇总,并根据公司工艺考核指标报告相关人员进行协调、调整,使水、电、汽、风的运行在规定范围之内。
2供水
2.1供水系统概述及工艺流程图(见动力附表二)
本厂供水系统分为生产、消防给水系统、生活给水系统;循环水给系统(包括化产循环水系统和制冷循环水系统);复用水系统和冷冻水系统共计十三种管线。
2.1.1水源:
生产及生活用水均由公司现有生产供水管网及生活供水管网供水,节点位于厂区南侧围墙1.0m处,节点压力生产水0.1MPa,生活水0.4MPa。
2.1.2生产、消防水系统
生产、消防给水系统为一个给水系统,(7J管线);在厂区内为环状布置,设室外消火栓28座;生产最大用水量为:
127.15m3/h;消防用水量60L/s,其中:
室内消火栓25L/s,消防水带10L/s,室外25L/s,给水压力0.4MPa。
2.1.3生活给水系统
由生活用水管网直接供给,最大用水量13.78m3/h。
(5J管线)
2.1.4循环水系统(1X、2X;1X′、2X′)
2.1.4.1化产循环水:
循环水量3060m3/h,供水压力:
0.4MPa,回水压力:
0.2MPa。
2.1.4.2制冷循环水:
循环水量1500m3/h,供水压力:
0.4MPa,回水压力:
0.2MPa。
2.2主要设备概况
设备名称
规格型号
台(套)数
主要技术参数
备注
化产循环泵
KQSN350-M9/433-F
4
扬程57m;流量1100m3/h
单级双吸
制冷循环泵
TYPe300S-58A
3
扬程50m;流量735m3/h
单级双吸
冷冻水泵
TYPe250S65
3
扬程65m;流量485m3/h
单级双吸
消防泵
KQL150/400-4.5
2
扬程48m;流量220m3/h
立式单级
生产泵
ISG100-200
3
扬程50m;流量100m3/h
立式单级
2.3综合泵房水泵
2.3.1综合泵房工艺说明:
综合泵房由两大部分组成:
其一是向化产车间区域及制冷站提供符合水量、水温、水压、水质等要求的循环冷却水、制冷水,并能循环使用。
其二是用泵输送生活、消防用水。
本岗位循环水工艺流程为零排放,是向化产系统送去,然后循环水直接上冷却塔降温后流入循环水池。
生活水由动力厂提供。
生产、消防水的工艺流程主要是通过生活、消防水泵向全公司生产、消防水。
当循环水池水量不足时,也通过生产消防来水抽泵向循环水池补充一部分新鲜水。
2.3.2启动水泵技术规定
a.按下启动按钮,泵投入运行。
b.检查泵出口压力,将泵出口阀门缓慢开至正常。
c.循环泵出口压力保持在0.4Mpa以上。
d.生产泵出口压力保持在0.4Mpa以上。
e.在运行中出现不正常现象应立即停止。
2.3.3停泵技术规定
a.须停泵时,先关闭出水阀门。
b.按动停车按钮,直到停运。
2.3.4水量调整
司泵工应根据工艺要求,调节生产水与循环水水量。
并根据化产循环水和制冷循环水的温度调节补水量,使化产循环水出水温维持在25℃~32℃。
制冷循环水出水温度维持在15℃~18℃
3供汽
3.1供汽工段概述及工艺流程图(见动力附表三)
动力车间供汽工段包括锅炉房、软化水、换热站等。
锅炉房装设一台WNS15-1.25-Q.Y,15t/h燃油、燃气锅炉,一台WNS15-1.25-Q,15t/h燃气锅炉,供应全厂的生产、生活用汽。
软化水系统供应两台锅炉的用水。
3.2除氧
3.2.1启动软水泵,软化水由水箱进入除氧器,打开水位调节阀,关闭旁路阀门。
3.2.2打开顶部排气阀、蒸汽压力调节阀,供气加热。
3.2.3除氧器水位(水位表指示到1/2外),水温达104℃左右可启动给水泵,打开出水阀供锅炉用水。
3.2.4除氧器正常运行时,上部排气阀开度约1/4圈。
3.2.5每隔一小时化验进水、出水的含氧量,记录各种监督仪表的数值。
3.3司炉
3.3.1运行操作顺序:
司炉人员合上控制柜或操作盘电源,电源指示灯亮。
按下启动按钮,锅炉自动进入程序点火启动,其中自动点火是锅炉启动的重要环节之一。
如果锅炉点火失败,或者燃烧过程中发生熄火,都会发出灯光示警,并自动转入停炉程序。
注意,此时必须将程序控制器的红色复位按钮按下,复位才能再次进入启动状态。
燃烧器启动后,进入程序运行。
3.3.2工艺技术规定
3.3.2.1经常检查人孔及手孔是否漏洞,同时检查排污阀是否严密无漏,附属配件、阀门仪表有无漏水漏气等情况如有泄漏现象,应在停炉或系统压力小于2个大气压下拧紧入孔及手孔盖螺栓,当锅炉水压逐渐升高时,应注意锅炉内各部件有无特别响声,如有应立即检查,必要时,应立即停炉检查,解除故障后方可继续运行。
3.3.2.2停炉
按动控制箱停炉按钮,锅炉可按程序停炉,停炉后根据系统安排可以关闭主汽阀。
设定的超压自动停炉也属正常停炉,无需进行操作待恢复后可自动启动,也可人工干预启动。
3.3.3注意事项
3.3.3.1经常煤气管道的泄露情况,避免煤气中毒。
3.3.3.2锅炉水温度达194℃,防止烧伤。
3.4化验
3.4.1软化水处技术规定
3.4.1.1开机前的准备工作:
检查过滤器、钠离子交换器、软水箱等所有水处理设备上的阀门、压力表、水位计、电子线路、流量控制器、时间再生控制器等附件的完好泄露情况以及盐罐里氯化钠的饱和状态。
3.4.1.2正常运行:
原水经过滤器、钠离子交换器后进入软水箱,运行时压力保持在0.25MPa左右,水流速度控制在10—15米/时。
3.4.1.3顺流再生:
该套自动软器属于两罐单流量计互锁状态,一主一副,同时供水,交替再生,当钠离子交换树脂失效后,流量控制再生器直接启动时间再生器进行再生。
a反洗(14分钟):
硬水进入控制阀——经中心升降管向下——进入底部分流器——经过交换剂层向上——最后进入控制阀排水口排出。
b再生(50分钟)硬水进入控制阀后,向上进入注水器,经过射流过程中将盐罐中的还原剂吸入,带还原剂的水向下经过交换剂层进入分流器和升降管,再经过控制阀排水口排出。
c清洗(16分钟)硬水经控制阀进入树脂罐,经过交换后进入分流器沿升降管向上,最后通过控制阀排水口排出。
d注水(20分钟)硬水进入控制阀,在向树脂罐供水的同时,经注水器向盐罐内注水。
盐罐内在任何时间内必须保持补充水,随时满足下一个再生过程的需要。
3.4.2化验标准:
执行《低压锅炉水质标准》GB1576—1996
项目
指标
悬浮物
≤5mg/l
给水硬度
≤0.003mmol/l
炉水碱度
6~24mmol/l
炉水PH值
10~12
Cl-
≤300mg/l左右
3.5注意事项
3.5.1强酸强碱要加强管理,按说明使用。
3.5.2化学药品要分类保存,有毒要注明。
3.5.3取锅炉水样时,要待冷却后,以防烧伤。
4供气
4.1工艺流程图(见动力附表四)
4.2概述
4.2.1空压机是向再生塔、煤塔等需要压缩空气的部位输送压缩空气的设备。
并且通过无油再生干燥器向仪表系统输送干燥无油的压缩空气。
4.2.2我公司使用的是MM160和MM75回转式螺杆空气压缩机。
该设备由进气过滤系统、压缩机和电机总成、冷却油系统、分离系统、气量控制系统、电机起动控制系统、仪器仪表系统、安全防护系统、后冷却器、水分离器和排放系统及智能控制系统组成。
4.2.3设备概况
(a)型号:
(一)、MM160
(二)、MM75
(b)排气量:
26m3/min12.2m3/min
(c)额定排气压力:
0.85MPa
(d)进气温度:
常温
(e)出口温度:
≤40℃(环境温度8℃)
(f)冷却方式:
水冷风冷
(g)进水温度最高允许46℃
(h)冷却水量13.6t/h(在最高进水温度时)(无)
(i)主电机:
额定功率160kW/台75kW/台
(j)冷却风扇电机功率(无)4kW
(k)冷却油量:
87.4升
4.3主要工艺指标:
工艺用气压力:
≥0.6MPa;仪表用气压力≥0.6MPa;
4.4技术规定
4.4.1启动:
按“START”(启动)按钮,空压机启动,自动加载产生足够的气量,气压逐步升高。
4.4.2停车:
4.4.2.1按“UNLOADEDSTOP”(卸载停机)按钮,空压机立即卸载并继续卸载运行约7秒钟,然后停机。
如果按“UNLOADEDSTOP”(卸载停机)按钮时,空压机已在卸载运行,则空压机会立即停机。
5氮气
5.1氮气供送技术规定
5.1.1氮气系统概述:
氮气由集团公司动力厂通过氮气管网线输送到瑞达公司动力车间工艺和仪表储气罐。
通过储气罐后,工艺用气送至再生塔、煤塔等需要氮气的部位;仪表用气送至全厂各仪表用氮气点。
5.1.2主要工艺指标:
工艺用气压力≥0.6MPa;仪表用气压力≥0.6MPa
5.2氮气停送技术规定
5.2.1送气:
5.2.1.1送氮气前要检查确认空压机是否已停机,由空压机向储气罐送压缩空气的阀门是否关闭;压力表是否完好。
5.2.1.2缓慢打开向储气罐供送氮气的阀门,并逐渐调节供送氮气压力在0.6-0.65MPa。
5.2.1.3禁止快速打开氮气阀门,快速向储气罐及用气管网送气,确保管网管道及用气设备安全。
5.2.2停气:
5.2.2.1先关储气罐氮气进气阀门。
5.2.2.2再关储气罐出气阀门。
5.3氮气切换压缩空气的技术规定
5.3.1当氮气压力不足0.4MPa时,向调度报告,得到批准后,可启用空压机,空压机启动前先关闭氮气向储气罐进气阀门。
5.3.2打开空压机向储气罐进气的主管道阀门和空压机阀门。
5.3.3给空压机送电。
5.3.4启动空压机。
(空压机操作执行空压机操作规程)
5.4压缩空气切换氮气的技术规定
5.4.1当氮气压力达到0.6MPa以上时,及时向调度报告,得到批准使用氮气后,先停止空压机的运行,然后关闭空压机向储气罐送气的主管道阀门和空压机阀门。
5.4.2按氮气停送操作规程的送气操作规定送氮气。
5.5注意事项
5.5.1工作前操作工要穿戴好防护用品,衣边袖口要扎紧,不准围围巾,女工要戴好防护帽。
5.5.2严格按工艺技术操作规程进行操作。
5.5.3加强巡回检查,及时发现和排除设备管线的泄漏情况。
严防事故的发生。
5.5.4在操作时,应仔细检查阀门、仪表的完好和显示准确与否,不要正对阀门开关。
5.5.5要时刻看氮气压力波动情况,如果不符合工艺要求要随时调整,必要时可启动空压机。
6污水处理
6.1工艺流程概述及工艺流程图(附污水处理工艺流程图)
无压污水经格栅间及提升泵房进入隔油池,有压蒸氨废水也直接进入隔油池。
污水经隔油池除油后自流入调节池,经调节池均衡水质、水量后由提升泵提升进入加药混合反应装置及溶气气浮机,以进一步降低污水中S2-、悬浮物及油的含量,保证生化处理系统的效果。
经气浮装置处理后的出水自流入SDN池,同时稀释水、回流污泥及混合液在SDN池前的混合井混合后由泵送至SDN池。
SDN池的出水经二沉池泥水分离后,进入混凝反应池及混凝沉淀池进行深度处理,出水回用或达标外排。
二沉池及混凝沉淀池出泥进入集泥池,经泵提升进入污泥浓缩池,浓缩后的污泥用泵送入综合工房内的带压机脱水,脱水后的泥饼定时外运,反冲洗水和滤液由站区排水系统收集至格栅间及污水提升泵房进行再处理。
6.2处理量及技术指标
长钢瑞达焦化污水处理站设计水量为1800m3/d,其中生产工艺废水75m3/h,在生化阶段加入75m3/h的自来水作为稀释水。
主体采用SDN工艺,是对全厂蒸氨废水、炼焦废水、硫铵及洗脱苯废水、生活和化验废水进行处理,废水经过预处理、A/O2生物处理和深度处理后,出水水质达到《钢铁工业水污染物排放标准》(GB13456-92)中的一级标准。
主要污染物指标如下即:
CODcr≤100mg/LBOD5≤20mg/L
NH3-N≤15mg/L挥发酚≤0.5mg/L
油类≤8mg/LS2-≤1.0mg/L
氰化物≤0.5mg/LSS≤70mg/L
pH6~9
6.3格栅间及污水提升泵房
6.3.1无压污水通过格栅去除废水中带有的大量漂浮物,格栅间的最大处理水量Q=30m3/h。
6.3.2格栅机:
格栅运行方式为间歇运行,每三小时开启一次,每次运行10分钟。
6.3.3提升泵房设2台污水提升泵(1用1备)。
将经格栅后的废水提升至隔油沉淀池。
现场控制泵的启、停,中控室显示泵的运行状态。
正常液位启动一台泵;超高液位时两台泵启动,两台互为备用,每天轮换一次;超过高液位及低液位,高、低液位报警。
6.4隔油沉淀池及油水分离器
6.4.1无压污水经过格栅间后进入隔油沉淀池,有压污水直接进入隔油沉淀池,分离污水中带有的大量焦油,以降低生化处理阶段进水中的焦油含量。
隔油沉淀池内设有导流筒和蒸汽加热系统。
隔油沉淀池的正下方设有旋流泵,用于将池底的焦油抽送至油水分离设备。
油水分离器内设有蒸汽加热盘管。
油水分离器内定期分离出来的焦油外运至焦化总厂的相关车间进行回收利用。
6.4.2定期检查焦油排放管,防止焦油堵塞,必要时进行反冲;焦油排放时泵前加热蒸汽一定要及时打开;油定期外运。
6.5调节池、事故池
6.5.1事故池的主要功能是接受其他水处理设施的事故性排放(如生产水量大、辅助设备抢修等),以保证水处理设施的平稳安全运行。
6.5.2调节池内设潜水搅拌机对来水进行混合均衡水质水量,通过池内高、中、低三个液位计控制立式提升泵的运行,现场及中控电脑都可进行泵启动及停止操作。
6.5.3调节池提升泵,正常液位与中液位时,两台泵运行;液位超高或者低液位都会报警
6.5.4池内水力停留时间24小时,有效水深5.0米。
6.6气浮装置
6.6.1在正常运行下,将溶气水的出口压力调节到大于4.5bar(巴),进口侧的真空度为-0.02Mpa左右(不得大于-0.04Mpa)即控制溶气泵的进水量为处理水量的30%,进气量控制在泵的流量的10-12%。
6.6.2正常运转时气浮机的启动与调节池提升泵互为连锁,提升泵启动则气浮机启动,提升泵停止则气浮机停止。
6.6.3在气浮阶段投加FeSO4和PAM水处理药剂,除去废水中颗粒悬浮物等污染指标。
6.7A/O2池
6.7.1工艺控制参数
6.7.1.1适宜的进水条件为COD≤2000、NH3-N≤150mg/L,因此需将废水稀释后处理。
6.7.1.2污泥负荷0.1-0.20kgCOD/kgMLSS.d。
6.7.1.3溶解氧(DO)2.0-4.0mg/L
6.7.1.4MLSS2-4g/L
6.7.1.5SV20-50%
6.7.1.6SRT15-20d
6.7.1.7进水温度控制在30℃,PH值7.0-8.2
6.7.1.8水力条件控制:
本工艺为连续曝气操作,因此在控制上应保证水量的连续性,即系统连续地进水和出水。
6.7.1.9污泥浓度控制:
MLSS一般应控制在2000-4000mg/L之间,超过此范围致使出水水质恶化时,可通过改变剩余污泥的排放量来调整。
6.7.1.10污泥龄:
通常大于15-20d。
6.8二沉池
6.8.1技术指标:
表面负荷(1.0~1.5/㎡·h);停留时间(1.5~2.5h);污泥含水率(99.2~99.6%)。
6.8.2根据池组设置、进水量的变化,应调节各池进水量,使之均匀配水。
6.8.3二次沉淀池的污泥必须连续排放。
保证排泥平衡。
6.8.4二次沉淀池刮吸泥机的排泥闸阀,应经常检查和调整,保持吸泥管路畅通,使池内污泥面不得超过设计泥面1m;刮吸泥机集泥槽内的污物应每周清除一次。
6.9混合反应池、混凝沉淀
6.9.1处理水量为150m3/h,反应池1座,反映时间36min。
6.9.2混凝沉淀池1座,采用中心进水辅流式沉淀池,直径12m,池边水深3m,混凝沉淀池表面负荷0.7/m2·h,沉淀时间2.0h。
6.9.3混合反应池加药系统的工艺控制
6.9.4M180(固体)8小时配药一次,每天配3次,配制浓度10%,计量泵加药量为400L/h。
6.9.5定期测定COD、BOD、SS、NH3-N的指标,并作好记录,以便观察出水水质是否满足回用水标准。
6.10污泥脱水系统
6.10.1污泥脱水系统采用带式压滤机。
脱水机房及加药间合建,分两层,尺寸为28.0×12.6×9.1m,一楼为加药间及储药室,二楼为脱水机房。
脱水机房内设置1台带式压滤机有效带宽B=1500mm,N=1.5+0.37KW。
6.10.2PAM投加量应根据污泥的性质、消化程度、固体浓度等因素,通过试验确定投加量。
6.10.3药剂量的配制应符合脱水工艺的要求0.1~0.3%。
6.10.4污泥脱水完毕,应立即将设备和滤布冲洗干净。
6.10.5污泥脱水机在运行中,随污泥变化应及时调整控制泥量、药剂量等;
6.10.6在污泥脱水机械带负荷运行前,打开反冲洗泵,应空车运转数10分钟;
6.10.7技术指标:
进泥含水率(95~97%);泥饼含水率小于(80%);PAM的投加0.1~0.3%/m3脱水干泥;150~350kg干泥/㎡·h。
6.11污水处理化验工艺规定
6.11.17.9.1化验执行标准与采样点:
化验执行《钢铁工业水污染物排放标准》(GB13456-92)中的一级标准。
主要污染物指标如下即:
6.11.2CODcr≤100mg/LBOD5≤20mg/L
6.11.3NH3-N≤15mg/L挥发酚≤0.5mg/L
6.11.4