橡胶行业申报技师论文.docx
《橡胶行业申报技师论文.docx》由会员分享,可在线阅读,更多相关《橡胶行业申报技师论文.docx(15页珍藏版)》请在冰豆网上搜索。
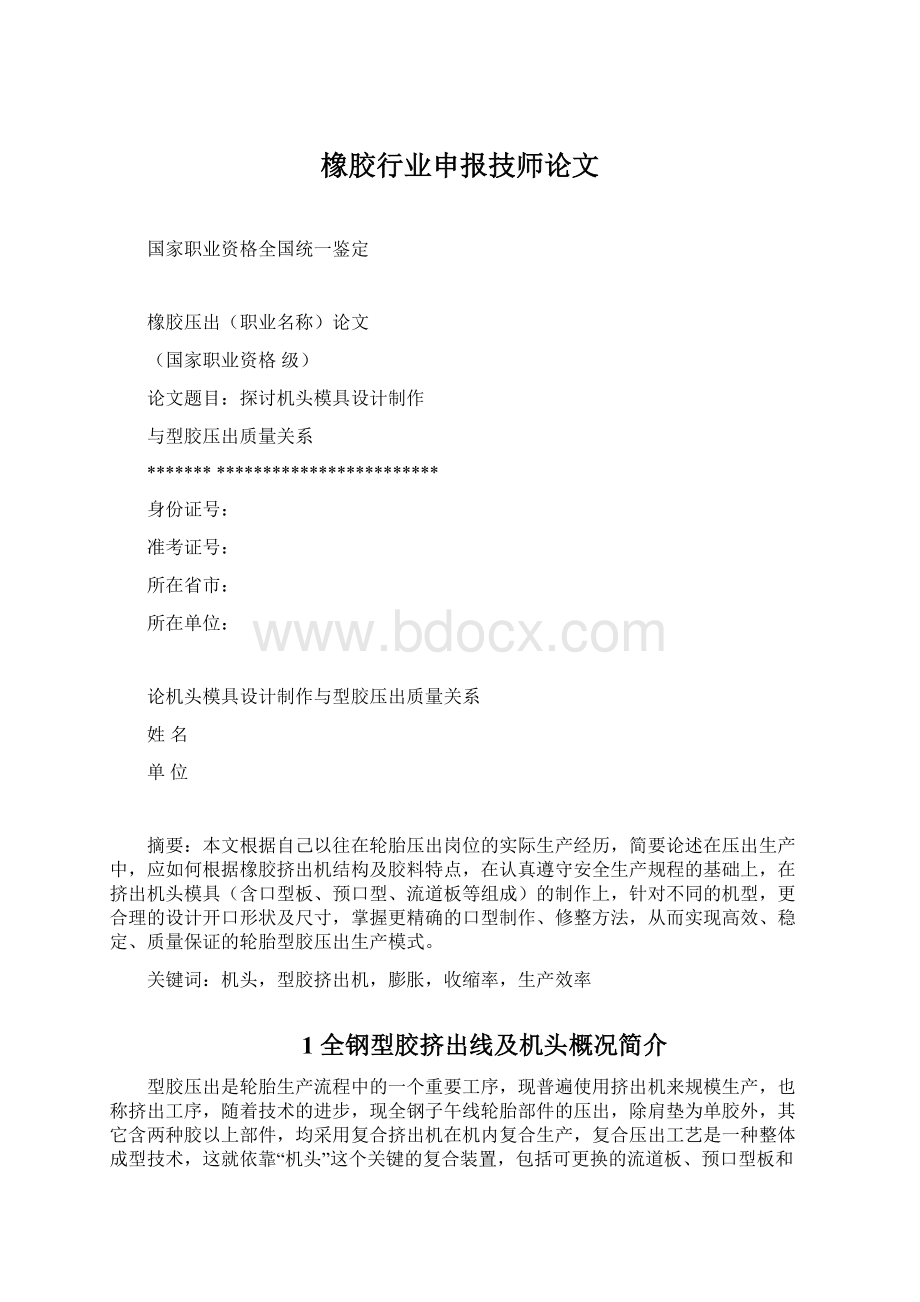
橡胶行业申报技师论文
国家职业资格全国统一鉴定
橡胶压出(职业名称)论文
(国家职业资格级)
论文题目:
探讨机头模具设计制作
与型胶压出质量关系
*******************************
身份证号:
准考证号:
所在省市:
所在单位:
论机头模具设计制作与型胶压出质量关系
姓名
单位
摘要:
本文根据自己以往在轮胎压出岗位的实际生产经历,简要论述在压出生产中,应如何根据橡胶挤出机结构及胶料特点,在认真遵守安全生产规程的基础上,在挤出机头模具(含口型板、预口型、流道板等组成)的制作上,针对不同的机型,更合理的设计开口形状及尺寸,掌握更精确的口型制作、修整方法,从而实现高效、稳定、质量保证的轮胎型胶压出生产模式。
关键词:
机头,型胶挤出机,膨胀,收缩率,生产效率
1全钢型胶挤出线及机头概况简介
型胶压出是轮胎生产流程中的一个重要工序,现普遍使用挤出机来规模生产,也称挤出工序,随着技术的进步,现全钢子午线轮胎部件的压出,除肩垫为单胶外,其它含两种胶以上部件,均采用复合挤出机在机内复合生产,复合压出工艺是一种整体成型技术,这就依靠“机头”这个关键的复合装置,包括可更换的流道板、预口型板和口型板等组成,几种不同配方的胶料经过各自的螺杆被压出到流道板上,在预口型内复合并经口型板一起压出机外,不需粘接或贴合,形成一体的型胶半成品,具有优良的黏合质量,各种胶料分布定位准确、断面清楚,对比机外复合具有无法比拟的优点[1];我们现场所采用挤出机主要有一热一冷双复合和三冷三复合两种形式,如图1为双复合挤出机,图2为三复合挤出机。
图1双复合挤出机
图2三复合挤出机
以上两种机型每台挤出机都主要包括螺杆、机筒、机头、喂料、供料、传动、温控、液压、润滑等系统,只是压出机个数不同,能同时复合生产胶料的品种不同,适应各类复合型胶半成品的生产;整个压出联动线同时包括附助生产线(图3),由接取、收缩、称量、贴胶、打印、输送、冷却、吹干、切割、分离、称量、分选、卷取等装置组成,压出机组及联动生产线在电脑控制下按不同的工艺要求实现全自动化生产,整条生产线大约有80-100米长。
图3德国克虏伯公司的一热一冷喂料双复合压出联动线
目前我公司全钢子午线轮胎型胶挤出生产线增加到6条,设备生产厂家分别为德国克虏勃公司,天津赛象科技股份有限公司、桂林橡胶工业设计院等,主要生产胎面、胎侧,胶芯、肩垫四种全钢半成品部件,目前在产全钢胎各种规格花纹有110多种,而每条轮胎均需有以上四种半成品部件组合,型胶半成品产量累计达到43000条/日,同台挤出机生产不同的半成品,主要是靠频繁更换机头内不同的流道板、预口型板和口型板来实现。
胶料在压出过程中,因压出膨胀和收缩而造成型胶变形,不符合施工要求标准,另外停放变形一直是个重要的问题,极大降低了型胶压出一次合格率,在停放后型胶如继续无规则收缩,会造成二次返回,影响到压出工序质量与生产效率。
2型胶变形的主要表现
型胶变形主要表现为膨胀和收缩,以胎面为例(图4),压出膨胀是指胶料从口型压出后胎面的断面尺寸较口型断面尺寸增大的现象。
压出收缩是指压出后半成品在停放过程中发生的长度缩短、宽度和厚度增大的现象。
压出膨胀和收缩的实质是一样的,都是由于具有粘弹性的胶料在加工过程中不仅发生不可逆的塑性形变,而且还发生可逆的弹性形变。
一部分弹性形变在半成品离开口型后恢复,从而产生压出膨胀,而另一部分弹性形变由于受到分子链的粘滞或滞后作用,需要经过一段时间才能恢复,即在停放过程中恢复,从而导致收缩。
压出膨胀和收缩发生在胎面压出生产中,它在整个橡胶和塑料压出生产中都备受关注。
图4某规格胎面标准尺寸
3口型(含口型板、预口型、流道板)等整个机头组成在压出联动线中的作用
3.1机头
机头是胶料压出过程中将胶料由螺旋运动变为直线运动的关键部件,可节制螺杆的塑化功能的强弱,同时直接影响制品的几何尺寸和表面质量,下面对组成机头的流道板、预口型分别论述。
3.2流道板
流道板是将直接连接螺杆通道,将双螺纹螺杆两股胶由圆柱体改变为压力平均分布的扁平体,要解决流道中间压力相对边部高,而出现中间厚两边薄问题,同时要防止两侧压力不均而左右不对称现象,其形状的精确与否对压出型胶的精确度有极大的影响,特别是对同时双条挤出半成品是否一致有决定性作用,为解决以上问题现普遍采用设置中心岛来分解胶料走向,中心岛的高度、角度设计是主要的技术数据,我们现用流道板形状图来说明(图5-1,图5-2)。
图5-1机头上流道板
图5-2拆卸下流道板
复合压出机各胶料的进口角度和流道的布置都要尽量避免流道改变方向,使压力损失减至最小。
这样设计的好处是既可降低胶料的温度,又可提高产量。
同时适当加大机头流道的长度,使机头的阻力提高,使压出系统的压力提高,从而使压出胶料得到更充分的剪切和混合。
塑化好了的胶料,经过较长流道与口型后,能获得充分的应力松弛过程,降低了压出物的记忆效应[2],这对半成品的几何尺寸和表面光洁度都是有利的,特别是对压出后停放待用型胶的稳定性有很大影响。
但过长的机头流道,也会导致半成品压出温度升高;为了使半成品表面更平滑光洁,对设备厂家我们要求机头流道板在调正后都应镀铬抛光,我们在设备开始设计及调试期间,对各挤出机流道就进行了严格的带胶测试、修正,各机头出胶量、出胶走向均匀,流道内腔压力分布合理,作为胶料基本流向分布,在后期新规格开发投产时,一般重新制作新口型、预口型,而对应所用流道板不会随意改动。
已修正定型流道板如图6所示。
图6已修正定型的流道板尺寸
3.3预口型板
预口型板的主要作用是将分别从各流道来的胶料按照设计要求形状尺寸、多少输送至口型前,经口型压出后得到断面尺寸各种胶料分布符合工艺要求的半成品,实际生产中使用的预口型如图7所示。
图7实际生产中使用的预口型
在此必须要注意冷热压出机对胶料热炼后胶料的膨胀系数,我们现场均采用的是销钉式冷喂料压出机,如图8所示。
图8销钉式冷喂料挤出机
采取在机筒的一定部位上安装数排销钉,每排沿圆周方向又分布有数个,相对应的螺旋部位开有环形槽,销钉直接插入这些环形槽中,胶料在这些销钉的作用下作横向运动、分流运动、旋转运动。
胶料便会受到一排多个销钉的分割和剪切,强化了捏炼,获得高质量的混合、捏炼和塑化的胶料。
经测量分析,按我们目前使用的胶料,冷喂料压出机压出的膨胀率比热喂料低17%,因此在预口型开口面积上冷喂料胶料对比热喂料按实用比例进行增加。
图9已定型的预口型加工图纸
3.4口型板
口型板是最终决定半成品形状模型,它的开口大小、形状及各部位角度都直接影响半成品的质量,决定着型胶外观尺寸是否达到工艺标准要求以及型胶半成品定型后的稳定性,同时口型板是根据生产各规格尺寸不同轮胎而需用数量最多,改变最大的,需根据各半成品形状不同要考虑胶料流经较厚部位与较薄部位时,有整体平稳的速度分布,以胎面为例对此重点进行研究,如图10所示。
图10实际生产在用口型板
挤出膨胀和收缩的产生机理都可以归纳为以下两点:
(1)入口效应。
胶料从大直径的机筒被压入小直径的口型时,受到强烈的挤压和剪切作用,于口型入口处产生收敛流动,沿流动方向产生速度梯度,使分子链部分拉直(构象变化),在体积基本不变(除将其中的空气部分排出外)的情况下,产生可恢复的弹性形变。
(2)剪切流动。
在口型里稳定流动时,由于切向应力差会使分子链构象产生变化,导致弹性形变,它在挤出后也会恢复。
在计算胶料挤出膨胀比或收缩率时,由于口型不同,侧重点也不同,在口型较厚情况下(大于30mm),入口收敛流动产生的弹性形变大部分在口型中得到了恢复,而剪切流动产生的弹性形变则是主要的弹性形变,而在胎面实际挤出生产中,入口收敛流动产生的拉伸弹性形变则是主要的弹性形变,胶料流动状态(如图11),这种情况是在挤出辅线速度保证与胶料出口型速度一致时,胶料会产生这种膨胀变化。
图11胶料流动示意图
对于挤出口型尺寸,包括口型长径比和口型入口角等等,根据挤出膨胀率入口效应产生的弹性,前人都进行了各种复杂的测量与演算,也推举了大量公式,均有数据支持,这里并不一一列举,但在实际生产中影响型胶半成品稳定因素还有很多,这里主要谈讨口型板开口大小与生产效率的直接关系,也与型胶停放后对收缩率的影响;
经常听机台操作主机反映,不同规格的胎面生产速度并不是完全按大小排列,有个别较大型、用胶较多胎面生产速度反而对比小胎面要快,生产效率高,唯一的不足是长度难掌握,建议口型均按照此方式设计,经测量这种现象是口型板开口尺寸过大而引起的。
为论证此方式对生产效率及质量的影响,进行试验测量,某规格轮胎胎面厚宽216mm,总宽300mm,同时开两块口型,一块按标准216mm宽度开,一块按110%口型上肩宽开口到238mm,总宽开口330mm。
(1)先试验生产加宽口型,依我公司现有胶料数据,挤出后约有2.8%的膨胀率,胶料经过口型后肩宽实际达到238mm+238*2.8%=245mm,总宽同样加宽,此时为达到尺寸合格,主机加快辅线牵引速度,速度达15.8m/min,在挤出线收缩辊道前,测量肩宽218-220mm,在经过冷却线后胎面收缩,宽度合格,在216mm±2mm间,裁断长度现场测量合格,装车待测量。
表1部分试验时机台数据
挤出机的设定与显示
类别
250挤出机
200挤出机
单位
螺杆转速设定
30..4
27.5
RPM
螺杆实际转速
30.65
27.71
RPM
压力
4.37
7.35
MPa
电流
229.1
210.3
A
温度控制
螺杆℃
塑化段℃
挤出段℃
机头℃
250挤出机
设定
50
40
50
下
中
上
实际
41.2
39.9
42.1
83.7
70
60
200挤出机
设定
50
50
50
85.8
85.2
60.7
实际
50.2
50.2
76.1
供胶设备
冷却水温度℃
辊转速m/min
胶条宽度mm
胶条厚度
跑胶温度℃
进
出
粗炼机
前辊
实际
17
19
82
后辊
实际
17
17
细炼机
前辊
实际
16
17
90
后辊
实际
17
18
供胶机
前辊
实际
18
22
26
105
84
后辊
实际
17
20
挤出机
胎面
基部
挤出温度
标准
≤125℃
≤120℃
实际
118
111
挤出机的设定与显示
类别
250挤出机
200挤出机
单位
螺杆转速标准
RPM
螺杆转速设定
30.4
27.5
RPM
螺杆实际转速
30.65
27.71
RPM
压力
4.37
7.35
MPa
电流
229.1
210.3
A
挤出联动生产线
设定
实际
一线速度m/min
15.6
15.8
二线速度m/min
45
45
宽度mm
218
每米重量kg
4.8
4.66/4.78
长度mm
3350/3355
3310/3320
单条重量kg
16.19
16.2
(2)试验依标准数据肩宽216mm开口口型板,同样以上设备参数,转速不变,由于开口量减少,胶料经口型后膨胀扩为219-221mm,主机将牵引速度设为14.6m/min,收缩辊道后测量厚宽为217-218mm,在经过冷却线后胎面收缩,宽度合格,在216mm±2mm间,裁断长度现场测量合格,装车待测量。
同时在两次挤出时进行了在线伸缩率测试,方法为:
在出口型后1.5m固定一处,在胎面上两次试验同样划定1m长两点,在冷却线后车未裁断前对两点测量,结果第1块口型板试验原1m距离两点收缩为85mm,收缩率为15%,第二块口型板测量为91mm,收缩率为9%,相差较大。
实际生产效率计算:
第一块:
15.8m/min-15.8*15%=13.43m/min
第二块:
14.6m/min-14.6*9%=13.29m/min
对比两种口型实际生产效率相差并不多,但挤出质量方面,第一块开口较大口型其挤出压力对比第二块小0.3-0.6mpa,断面明显上气孔明显较多(图12),而第二块较密实.
图12胎面断面对比图
对两块口型挤出停放胎面进行定长测量,数据如下:
表2胎面试验定长数据测量
胎面试验定长数据测量
口型
停放时间min
15
30
60
90
120
180
原定长mm
3310
3310
3310
3310
3310
3310
第一块
胎面1实际长度mm
3290
3270
3255
3240
3220
3215
胎面1伸缩率
0.60%
1.21%
1.66%
2.11%
2.72%
2.87%
第二块
胎面2实际长度mm
3295
3285
3280
3275
3270
3270
胎面2伸缩率
0.45%
0.76%
0.91%
1.06%
1.21%
1.21%
表2中的数据绘制成测量图如下所示。
图13胎面实验定长测量图
试验证明,口型开口较大的实际中并不能提高生产效率,并且由于过度拉伸,长度不断处于变化中,长度变化同样造成了厚度的变化,这种不稳定给产品带来极大隐患,相反低拉伸型尺寸口型能够有效的保证胎面各方面尺寸稳定,胎面合理的在线的收缩率应在10%-6%之间。
4简单汇总型胶压出其它常见问题形成原因及解决方法
表3型胶压出其它常见问题形成原因及解决方法
常见问题
原因
解决办法
焦烧:
胶料配方不当,焦烧时问太短
调整配方
流道板或预口型中有积胶或死角引起
改正口型锥角,定期清除积胶
流胶口太小,压力过高
加开流胶口
机头温度太高
降低机头温度
螺杆冷却不足
检查冷却系统,加强螺杆冷却
喂料中断形成空车滞料
防止供料脱节
气泡和海绵
转速太快
调慢车速
原料中水分、挥发物多
加强原材料检测
热炼时夹入空气
改进热炼操作,采取收剑式螺纹
机头温度过高
冷却
型胶两侧厚薄不均,或出现沟痕
畸形产品,各部位应力不一致
改进口型设计
热炼不足
延长热炼时间
条痕裂口
杂质引起松开口型,让杂质排出
撕边
口型预热到位
5结论
综上所述.机头模具在轮胎型胶挤出过程中作用是关键的,同时这些模具在实际设计制作时要充分考虑到本挤出机设备特点,并根据所使用胶料不同、膨胀率收缩率不同,逐步建立一个完整的数据库,依照数据库来归纳出本设备流道、预口型、口型板最佳形状、尺寸,逐步杜绝手工设计、修正口型传统作法,而采取EDM机来进行精细一次性加工,不断地改进型胶压出工艺,提高型胶质量,为制作优质成品轮胎提供良好基础。
参考文献
[1]《子午线轮胎结构设计与制造生产新技术新工艺及产品质量检测手册》中国橡胶工业协会编
[2]卢巍等,《胎面挤出膨胀与收缩的研究》轮胎工业,2003