铸铁件的针孔缺陷.docx
《铸铁件的针孔缺陷.docx》由会员分享,可在线阅读,更多相关《铸铁件的针孔缺陷.docx(9页珍藏版)》请在冰豆网上搜索。
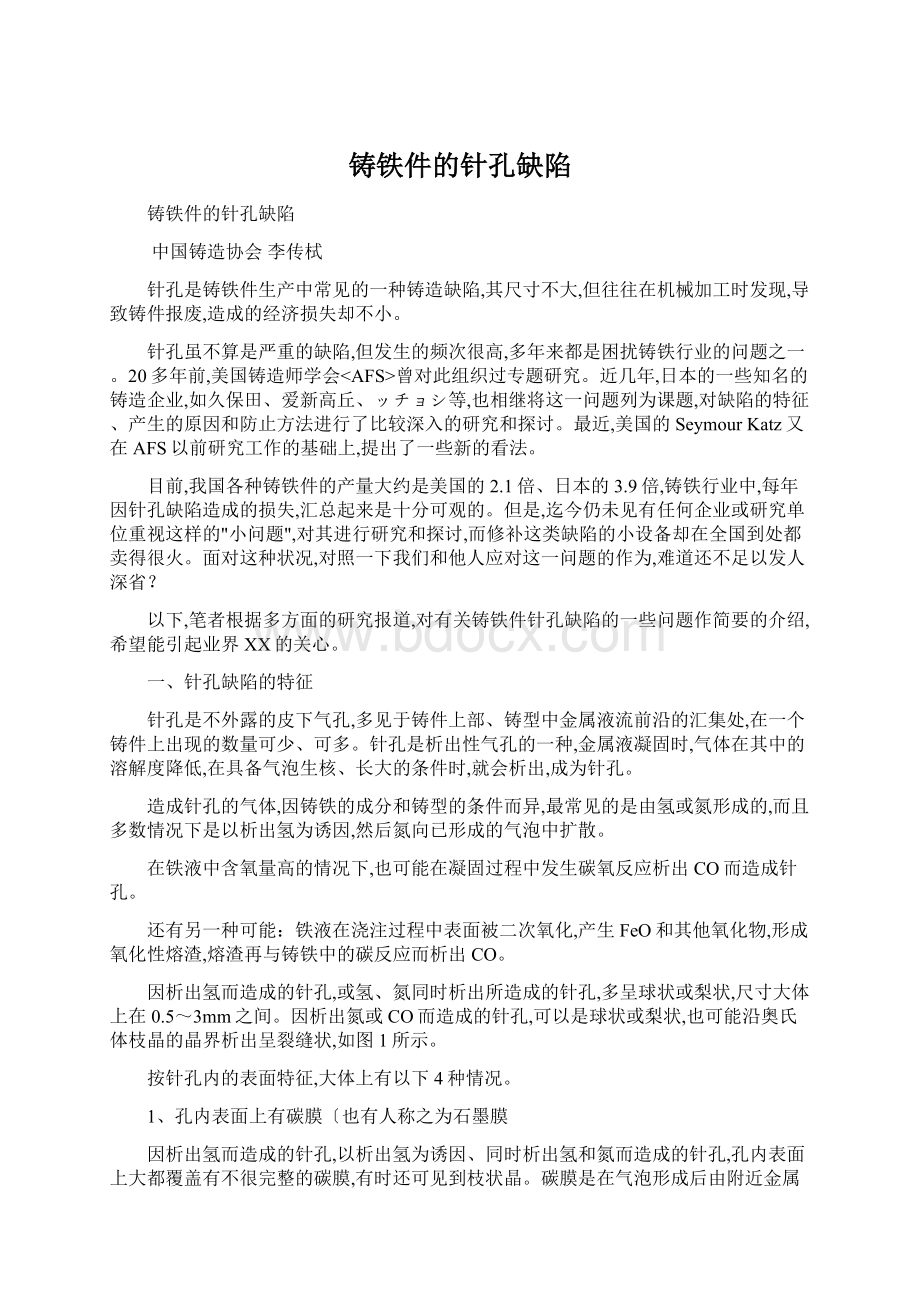
铸铁件的针孔缺陷
铸铁件的针孔缺陷
中国铸造协会李传栻
针孔是铸铁件生产中常见的一种铸造缺陷,其尺寸不大,但往往在机械加工时发现,导致铸件报废,造成的经济损失却不小。
针孔虽不算是严重的缺陷,但发生的频次很高,多年来都是困扰铸铁行业的问题之一。
20多年前,美国铸造师学会曾对此组织过专题研究。
近几年,日本的一些知名的铸造企业,如久保田、爱新高丘、ッチョシ等,也相继将这一问题列为课题,对缺陷的特征、产生的原因和防止方法进行了比较深入的研究和探讨。
最近,美国的SeymourKatz又在AFS以前研究工作的基础上,提出了一些新的看法。
目前,我国各种铸铁件的产量大约是美国的2.1倍、日本的3.9倍,铸铁行业中,每年因针孔缺陷造成的损失,汇总起来是十分可观的。
但是,迄今仍未见有任何企业或研究单位重视这样的"小问题",对其进行研究和探讨,而修补这类缺陷的小设备却在全国到处都卖得很火。
面对这种状况,对照一下我们和他人应对这一问题的作为,难道还不足以发人深省?
以下,笔者根据多方面的研究报道,对有关铸铁件针孔缺陷的一些问题作简要的介绍,希望能引起业界XX的关心。
一、针孔缺陷的特征
针孔是不外露的皮下气孔,多见于铸件上部、铸型中金属液流前沿的汇集处,在一个铸件上出现的数量可少、可多。
针孔是析出性气孔的一种,金属液凝固时,气体在其中的溶解度降低,在具备气泡生核、长大的条件时,就会析出,成为针孔。
造成针孔的气体,因铸铁的成分和铸型的条件而异,最常见的是由氢或氮形成的,而且多数情况下是以析出氢为诱因,然后氮向已形成的气泡中扩散。
在铁液中含氧量高的情况下,也可能在凝固过程中发生碳氧反应析出CO而造成针孔。
还有另一种可能:
铁液在浇注过程中表面被二次氧化,产生FeO和其他氧化物,形成氧化性熔渣,熔渣再与铸铁中的碳反应而析出CO。
因析出氢而造成的针孔,或氢、氮同时析出所造成的针孔,多呈球状或梨状,尺寸大体上在0.5~3mm之间。
因析出氮或CO而造成的针孔,可以是球状或梨状,也可能沿奥氏体枝晶的晶界析出呈裂缝状,如图1所示。
按针孔内的表面特征,大体上有以下4种情况。
1、孔内表面上有碳膜〔也有人称之为石墨膜
因析出氢而造成的针孔,以析出氢为诱因、同时析出氢和氮而造成的针孔,孔内表面上大都覆盖有不很完整的碳膜,有时还可见到枝状晶。
碳膜是在气泡形成后由附近金属中所含的碳向其中扩散而形成的,因此,针孔内有碳膜时,针孔周围的金属组织中往往没有石墨。
2、氧化型针孔
铁液中氧含量较高,或铁液在浇注、充型过程中二次氧化程度较高,或铁液与铸型中的水分反应生成了较多的FeO时,由于FeO和铁液中所含的碳反应而析出CO,也可以造成针孔。
这种针孔的内表面基本上见不到碳膜,有时可见到氧化膜。
如果是因金属-铸型界面处FeO含量增多而造成的针孔,则缺陷位于表皮以下,呈球状或梨状。
如果亚共晶铸铁析出奥氏体枝晶时,枝晶附近铁液中的FeO浓度高,与碳反应产生CO,则生成的气孔可能沿晶界析出,形状类似于图1所示的裂缝状。
3、内表面有熔渣
有时,针孔內表面上有熔渣模样的夹杂物,这类夹杂物是由氧化物、硫化物和硅酸盐等构成的。
针孔往往是由夹杂物中的氧化物与铁液中的碳反应生成CO,并在夹杂物处生核而形成的。
这类针孔也是氧化型针孔。
4、针孔内有铁粒
浇注过程中,金属液在浇注系统中发生紊流、飞溅而产生的铁粒,往往会被裹在液流中。
铸件凝固时,铁粒表面的氧化膜可能与铁液中的碳反应而造成针孔,铁粒附近金属液中的气体也易于依附铁粒生核、长大。
但也可能有这样的情况:
气孔中的"铁粒"并非在浇注系统中形成的,而是在气孔形成后,由奥氏体枝晶间的低熔点偏析物渗入气孔中形成的。
这种情况下,观察针孔附近铸件的显微组织时,可能见到晶粒边界处有偏析物流向针孔后留下的空隙。
二、影响针孔形成的一些因素
铸铁件针孔缺陷的形成取决于多种因素,如铸铁的化学成分、铸型的特点、浇注温度、浇注系统和排气孔的设置等,虽然在这方面已经进行过大量的研究工作,但是,迄今为止,对于形成针孔的机制,仍在探求之中。
在生产经验和研究工作的基础上,对影响针孔形成的一些主要因素,可作如下的分析。
1、铁液中的气体含量
氢、氮、氧是可以存在于铁液中的三种气体元素。
铁液的凝固过程中,先析出的固相中含有的气体量很少,使残留的液相中气体的浓度不断增高。
当液相中气体含量超过其溶解度后,就可能以气泡的形式析出。
气体在铁液中的溶解度的上限,决定于铸铁的成分、温度和环境中相应气体的分压。
〔1氢
在正常的熔炼条件下,铁液中的氢含量〔质量分数一般不超过2×10-4%。
在这种情况下,不会以气泡的形态析出。
如果铸型中含有水分,在高温下,液态铸铁中的Fe、Al、Mg、Mn等元素使水还原而释放氢,铁液中的氢含量就可能大幅度提高,具备析出气体的条件。
〔2氮
在正常的熔炼条件下,铁液中的氮含量〔质量分数一般不超过100×10-4%,不会以气泡的形态析出。
氮含量超过120×10-4%后,就可能出现针孔。
氮含量超过150×10-4%,就可能出现裂缝状针孔。
如果用尿烷树脂冷芯盒工艺制芯,或用酚醛树脂覆膜砂制芯,都有可能因芯子释放氮而使液态铸铁中的氮含量提高,从而造成针孔缺陷。
冷芯盒工艺制芯所用的尿烷树脂,第一组分中不含氮,第二组分〔聚异氰酸酯中含氮。
配制芯砂时,树脂的第一组分与第二组分用量之比一般应为50:
50。
有时,铸造厂为提高芯子的强度,以便于芯子硬化后将其自芯盒中取出,将第二组分的用量增加,使二者之比为40:
60,甚至到35:
65,这样,就很容易使铸铁中氮含量过高而造成针孔。
采用覆膜砂制芯时,由于硬化剂〔六亚甲基四胺中含氮,如覆膜砂中树脂用量太高,浇注过程中铸铁中的氮含量也可能增高,从而导致产生针孔。
用树脂自硬砂造型时,采用尿烷树脂或含氮量较高的呋喃树脂作粘结剂,也是可能是导致铁液中氮含量增高的因素。
〔3氧
铁液中溶解的氧的质量分数应保持在20×10-4%~30×10-4%,以保证为石墨生核提供条件,增强孕育处理的效果。
如果熔炼过程控制不当,铁液中的氧含量过高,也可能导致针孔缺陷。
此外,在铁液浇注、充型的过程中,液流表面会发生二次氧化,其中所含的Fe、Si、Mn等元素被氧化,形成含FeO、SiO2、MnO等氧化物的熔渣,这类氧化物的共晶成分的熔点很低。
低熔点的熔渣极易成为携带FeO的载体,在具备气泡在液相中生核的条件时,其中的FeO就与铁液中的碳反应,生成CO,造成氧化型针孔。
2、液态铸铁中产生气泡的外部条件
在均匀的液相中产生另一新相〔气泡是非常困难的,需要相当大的能量,使系统的自由能增加。
液相中产生气泡时,总是先由几个原子或分子聚集而生核,起初体积非常微小。
这种微小的气泡,比表面积〔即单位体积的表面面积极大,要在液相中产生新的界面,就要获得能量,使新产生的气泡具有必要的界面能,其值等于其表面面积与液-气界面上表面张力的乘积。
即使新相〔气泡已经生核,其长大也需要能量,而且只有在尺寸超过某一临界值后才能继续长大。
尺寸小于临界值的气泡不可能长大,只会自行消失。
新相在非均匀相中生核,情况就大不相同了。
例如:
在固相-液相界面处产生气泡所需的界面能就少于在均匀的液相中产生气泡所需的能量;如果固相以尖端插入液相,则在尖端处产生气泡所需的界面能更少;如果固相是由液相凝固而形成的,可能因凝固过程中的体积收缩而在固相-液相界面处产生微小的缩孔,在这种情况下,气体可直接向缩孔中扩散而析出,使微小的缩孔扩大为针孔,不需要产生新相所需的界面能。
〔1铸型-金属界面处形成一层硬皮后最有利于形成针孔
铁液开始凝固时,先在铸型-金属界面处结晶,形成一层硬皮,晶粒的析出使固-液相界面处液相中的气体含量增高,同时还有自铸型吸收的气体。
这是有利于在此处产生针孔的内部条件。
同时,硬皮朝液相的一侧是固-液相界面,又有奥氏体枝状晶的尖端插入液相。
有些情况下,还可能有微小的缩孔。
这是有利于产生针孔的外部条件。
因此,针孔都产生于硬皮与液相的界面处,成为不外露的皮下气孔。
〔2铸型中金属液流前沿汇集处有利于形成针孔
在铁液浇注、充型的过程中,液流的前沿不断与新的铸型表面接触,这部分铁液与铸型接触的时间也最长,有利于吸收铸型受热后释放的气体。
液流前沿的金属与大气接触的时间最长,易于氧化,其中含有的FeO量很高。
因此,在铸型中金属液流前沿汇集处,各种气体的含量都高,是最易于产生针孔的部位。
〔3使铁液表面张力降低的因素都可以促进针孔的形成
前面已经提到,液相中产生气相需要增加的界面能,等于其表面面积与界面上的表面张力的乘积。
因此,所有能使铁液表面张力降低的因素,无论是化学的或物理的,都有助于气泡的生核和长大,使产生针孔的可能性增大。
3、不同品种的铸铁对针孔缺陷的敏感程度不同
因为球墨铸铁中含有活性很强的镁,球墨铸铁件比灰铸铁件更易于出现针孔缺陷。
在采用粘土干型浇注的条件下,球墨铸铁件与灰铸铁件出现针孔的概率基本相近。
如采用壳型、含氮的树脂砂型或粘土湿砂型,则球墨铸铁件对针孔缺陷的敏感程度就比灰铸铁件大得多,生产中应特别注意采取防止产生针孔的措施。
4、浇注温度和铸件壁厚的影响
铁液的浇注温度对针孔的形成有多方面的影响,很难笼统地说浇注温度高些好,还是浇注温度低些好,要根据具体条件认真分析。
液态金属浇注到砂型中后,型砂受到高温的作用,产生大量气体,很快就会在型内形成一个压力峰值,型内的压力对针孔的形成影响很大。
浇注温度较高,铁液在铸型中吸收气体较多,这是有利于产生针孔的因素。
但是,浇注温度高,则铸件凝固比较缓慢,凝固可能发生在型内气压峰值消减之后,这又是有利于气体自铸型逸出、从而可避免针孔产生的因素。
浇注温度低,虽然金属吸气较少,但其凝固较快,而且凝固往往发生在铸型内处于压力峰值的附近,铁液中卷入的气体和析出的气体不易排出,导致产生针孔缺陷的可能性增大。
因此,判断浇注温度的影响,要综合考虑铸件壁厚、凝固速率、铸型条件以及一些其他因素。
一般的规律是:
用粘土湿砂型时,提高浇注温度易导致铸件产生针孔;用含氮的树脂砂型时,提高浇注温度则有利于减少针孔缺陷。
用含氮的树脂砂型时,一般说来,在1280~1400℃之间采用较高的浇注温度可减少针孔的形成。
但是,生产薄壁铸件时,降低浇注温度,则针孔缺陷减少;生产厚壁铸件时,降低浇注温度,则针孔缺陷增多。
无论是灰铸铁件或球墨铸铁件,薄壁铸件产生针孔缺陷的概率都低于壁较厚的铸件。
除薄壁铸件凝固较快、金属吸气较少外,组织中碳化物较多也是导致针孔缺陷较少的原因。
有研究报道称:
铸铁组织中的石墨比碳化物更易于促进针孔的形成。
不同壁厚的铸件产生针孔缺陷的倾向大致是:
●壁厚在6mm以下的铸件,凝固快,吸气少,即使有气泡生核,也很难长大,因而产生针孔的概率较小;
●壁厚在6~25mm之间的铸件,最易于产生针孔缺陷;
●壁厚在25mm以上的铸件,凝固缓慢,有利于气体的扩散、逸出,也不易产生针孔缺陷。
5、铸铁中硅、碳含量的影响
铁液中所含的硅,能使其表面张力稍稍降低,但是硅又能使铁液中的FeO含量减少、抑制CO的析出量。
总体而言,灰铸铁中的硅含量在1.6~2.3%之间、球墨铸铁中的硅含量在2.2~3.0%之间,提高硅含量可使铸件产生针孔缺陷的倾向略有降低,但影响并不明显。
在正常含量范围内,碳对形成针孔缺陷也没有明显的影响。
6、铸铁中所含的铝在形成针孔方面的作用
20世纪60年代初,英国铸铁研究协会的J.V.Dawson就发现:
铁液中所含的铝,对铸件是否产生针孔缺陷有重要的影响。
浇注前往铁液中加入少量的铝,会导致铸件上产生针孔。
要特别说明的是:
浇注前往铁液中加入的铝,其作用与铁液经熔炼过程后其中残留的铝有很大的差别,因为残留铝含量的测定值中包括一些铝的氧化物,其活性要低得多。
70年代,美国铸造师学会曾对铸铁件的针孔缺陷组织专题研究,由CaseWesternReserve大学的J.F.Wallace等具体实施。
为研究浇注前往铁液中加铝的影响,在保持其他参数不变的条件下,浇注前往铁液中加入不同数量的铝,然后浇注不同厚度的试件,分析产生针孔缺陷的情况。
结果表明:
铝加入量在0.015%以下,试件上基本上不产生针孔;加入量在0.20%以上,对针孔缺陷也不敏感;加入量在0.015~0.20%之间,最容易出现针孔。
为了探求铝的这种作用的机制,Wallace等对不同条件的液态铸铁进行了表面张力的测定。
大量的测定数据表明:
铁液中所含的铝量对其表面张力有不可忽视的影响,而且表面张力的改变与铸件上产生针孔的概率有对应关系。
铁液中所加的铝量很少时,表面张力高,出现针孔的概率很小;加铝量在0.015~0.20%之间,铁液的表面张力降低,铸件上易于产生针孔;加铝量在0.20%以上,表面张力再次提高,又可以抑制针孔的产生。
在用粘土湿砂造型的条件下,铁液中所含的铝可以与铸型中的水分反应,生成Al2O3和氢气,所释放氢气部分被液态铸铁所吸收。
铁液凝固时,氢的溶解度大幅度降低,就具有析出氢、形成气泡的内部条件。
但是,产生气泡还必须具备在固-液相界面形成气泡所需的外部条件。
如果没有产生新相的外部条件,氢将以过饱和状态存在于铸铁中,不可能析出形成针孔。
液态铸铁中含0.015~0.20%的铝,其表面张力降低,正好为气泡的形成准备了外部条件。
为了确认由上述试验得到的结论,Wallace等还进行了脱除铁液中的铝的试验。
在含有铝、凝固时易产生针孔的铁液中,加入细粒铁矿石或其他氧化物,使其中所含的铝氧化。
将铝脱除以后,浇注的铸件就很少见到针孔。
一旦形成了氢气泡,对于铁液中溶有的氮气而言,该气泡就是真空,氮很易于向其中扩散,增强针孔的形成。
7、氮化铝〔AlN的作用
最近,美国的S.Katz提出:
促使铸铁件中形成针孔的并不是铝,而是AlN。
铁液凝固过程中,其中溶有的氮与溶有的铝结合,形成可溶性的AlN。
AlN在铁液中的溶解度随温度的降低而下降,在一定的条件下,可以在铁液凝固过程中析出。
析出的AlN与铸型中的水分反应,就会释放氢和氮;与铁液或熔渣中的FeO反应就会释放氮,从而形成针孔。
以含碳3.5%、硅2.5%的铸铁为例,根据热力学分析得到的数据,在不同的铝含量和不同的温度下,液态铸铁中溶有的氮量见图2。
铁液中铝含量很低〔0.003%以下时,在浇注温度〔1400℃和共晶温度〔1150℃下,其中溶有的氮量都不因铝含量的变化而改变,如图2中Ⅰ区内的两条直线所示,即在两种温度下都没有AlN析出。
铝含量在0.003~0.07%之间,在浇注温度下,铁液中溶有的氮量也不因铝含量的变化而改变,如图2中Ⅱ区内的直线所示,也没有AlN析出;在共晶温度〔1150℃下,铁液中溶有的氮量随铝含量的增加而减少,如图2中Ⅱ区内的斜线所示,说明有一部分氮已经以AlN的形态析出。
形成的AlN的量因铝含量的增加而增多。
铝含量超过0.07%以后,在浇注温度下和共晶温度下都有AlN形成,如图2中Ⅲ区内的两条斜线所示。
浇注温度下有AlN形成,会使铁液中溶有的氮量减少,结果,凝固过程中产生的AlN也就较少。
铝含量不同的铁液,在共晶温度下以AlN形态析出的氮量可按图2算出,计算的结果见图3。
图3中,细线与粗线所包含的范围内虽然也产生AlN,但因铝含量低,不足以与铸铁中所含的氮充分反应,因而不会产生针孔缺陷。
铝含量高的右端,在浇注温度下即产生AlN,此时产生的AlN,可能上浮到液面被熔渣所吸收,也可能被大气中的氧所氧化,结果,凝固过程中析出的AlN减少,也不至于导致针孔缺陷。
图3中点线所示的范围是易产生针孔的范围,这与多年来由经验确认的对针孔缺陷敏感的铝含量范围基本上是一致的。
三、防止产生针孔缺陷的措施
导致铸铁件产生针孔缺陷可以有多种原因。
虽然目前我们对缺陷产生的机制还没有确切的认识,但是,如果能根据生产经验和他人的研究成果,对实际生产中的各种参数作认真的分析,就有可能拟定一些有效的防范措施。
如有可能,根据企业的具体条件进行必要的试验、检测和研究,还可以提出针对性更强、效果更好的措施。
1、铁液中铝含量的控制
无论采用何种铸型,都应控制向铁液中加入的铝量,力求避免其在使铁液表面张力最低的范围〔0.015~0.20%内。
铸铁中铝的来源有二:
一是孕育剂带入;二是炉料中混有的铝或含铝材料。
孕育处理是铸铁件生产工艺中最重要的环节,是保证铸铁的显微组织和各项性能符合要求的所不可缺少的工序。
目前,应用最广的孕育剂是75硅铁,而各种牌号的硅铁中都含有少量的铝和钙。
除硅铁以外,可供选用的孕育剂品种还有很多,其中大部分也都含有少量的铝和钙。
孕育剂中所含铝和钙对孕育处理的效果有重要的作用,是不可或缺的。
在正常生产条件下,一般不会因孕育剂带入的铝造成针孔缺陷,但工艺人员必须对投入生产的每批孕育剂中的铝含量都做到心中有数,一旦出现问题,就可以及时作出正确的判断。
炉料中夹杂的铝或其他元素往往是影响铸铁冶金质量的原因,生产中应对炉料进行严格的管理和控制。
但是,近年来铸铁行业中有一项值得注意的新举措,即:
在冲天炉炉料中配加少量的铝,以提高铁液的温度并减少合金元素的烧损。
在此种情况下,所加的铝绝大部分都会被氧化掉,但也会有少量活性铝残留在铁液中,有时,其浓度足以导致产生针孔缺陷。
因铁液中含铝而产生针孔缺陷时,可在浇注前再向铁液中补加0.2%左右的铝,这样,既可提高铁液的表面张力,而且较多的铝还有固定氮的作用。
2、必须使铸型排气通畅
铁液浇注到铸型以后,铸型和芯子中的水分、粘结剂及其他附加材料因受热而产生大量气体,使型内压力瞬时增高,阻碍铁液中析出的气体和反应形成的气体排出,这也是导致铸件产生针孔缺陷的重要原因之一。
据日本爱新高丘公司近期进行的研究,用粘土湿砂造型生产线制造中、小型铸铁件时,加强铸型的排气,使浇注后型内的压力峰值降低、保持压力峰值的时间缩短,可以有效地降低针孔缺陷的发生率。
所采取的主要措施有:
●上型内设置足够数量的外通式排气孔;
●上型完成后刮平其上表面时,避免余砂堵塞排气孔;
●在压铁与上型的接触面上开通气槽,避免压铁堵塞排气孔。
在铸型的上方、浇注时液流前沿的会集处,设置尺寸略大的排气冒口,也是使铸型的排气通畅的有效措施。
此处的排气冒口,除排气外,还有收集液流前沿过冷铁液的作用,如设置得当,不仅能避免该处产生针孔缺陷,而且可以改善铸件的显微组织。
3、用粘土湿砂型铸造时可采用的措施
用粘土湿砂造型时,铁液中所含的铝、镁等元素与铸型中的水反应而生成氢气,是导致铸件产生针孔的主要原因。
如果铸铁中氮含量较高,或芯子采用含氮量较高的粘结剂时,氢气析出后,氮也会向气泡中析出,使缺陷更为严重。
因此,严格控制型砂中的水分至关重要。
虽然煤粉受热后会析出大量低分子量烃类气体,使铁液吸氢的可能性增加。
但是,无论生产灰铸铁件或球墨铸铁件,粘土湿砂中加入3~5%的煤粉都有防止产生针孔缺陷的作用,这已是各国同行的共识。
其原因可能是:
煤粉热解产生的气体在铸型-金属界面处造成强还原性气氛,阻碍铁液中所含的活性元素与铸型中的水发生反应。
也有研究报道称:
粘土湿型砂中加入2%左右的Fe2O3粉可以防止针孔缺陷,其原因是Fe2O3能与硅砂作用生成铁橄榄石,在铸型-金属界面处形成屏障,阻碍铁液与铸型间发生的反应。
目前,对此仍有不同的看法,在生产中采用以前,必须通过试验确认。
4、用含氮粘结剂制芯时可采用的措施
采用尿烷树脂冷芯盒工艺制芯,或用覆膜砂制芯,每一铸型中芯子用量又很多时,因铁液吸收氮而致铸件产生针孔的情况是经常发生的。
在这种情况下,除加强铸型的排气外,还应尽可能地降低芯砂的发气量。
一般情况下,改善原砂砂粒表面的清洁程度,采用圆形砂,都可在保持芯子强度相同的条件下降低树脂用量,从而降低芯子的发气量。
一些制造难度很高的芯子,如汽缸盖的水套芯,一方面,由于形状复杂、截面很薄,又要求具有很高的强度,难以将芯砂中的树脂用量降低;另一方面,芯子与铁液接触的面积很大,受热的情况特别严酷,会因树脂热解产生大量气体,而芯子的截面面积又小、排气特别困难。
对于这种芯子,采用人造陶粒砂,是前景十分看好的选择。
日本久保田公司的恩加岛铸造厂,原来用硅砂配制覆膜砂,制造汽缸盖的水套芯,树脂用量很难降到3%以下,铸件上经常出现气孔缺陷。
后改用人造顽辉石圆粒砂配制覆膜砂,树脂用量降到2%,发气量减少了38%,而芯砂的抗弯强度却提高了约50%。
无论是壳芯、还是冷芯盒芯,芯子制成后再予以短时间的低温烘烤,也是防止针孔缺陷的有效措施。
加热时,可使已硬化的树脂中含有的一些游离烃挥发,芯子的发气量可明显降低。
采用尿烷树脂冷芯盒工艺制芯,芯子再次烘烤时,树脂第二组分中的氮还可能进一步发生反应,生成更为稳定的化合物。
据报道:
美国有铸造厂将冷芯盒工艺制成的芯子于250℃左右烘烤2小时〔称为CorePostBaking,显著减少了铸件的针孔缺陷。
日本有一铸造厂发现:
制造壳芯时芯子的加热不充分,是导致针孔缺陷增加的原因之一。
将制成的壳芯于250~300℃再次烘烤0.5小时,可使其发气量降低15%左右,对于防止针孔缺陷也有很好的效果。
5、浇注前往铁液中添加固定氮的合金元素
在芯子或铸型采用含氮树脂作粘结剂的情况下,如铸件频繁出现针孔缺陷,也可考虑往铁液中添加固氮元素。
常用的固氮元素主要有铝、钛和锆,可根据具体条件选用。
用于防止针孔时,都应在浇注前加入铁液中。
加铝时,可采用由铝线切成的细粒或加工的铝屑,随铁流加入,用量一般为铁液的0.2%。
钛的固氮作用很强,铁液中加入0.03%左右的钛,能有效地减少铸件上的针孔缺陷,但钛不能用于球墨铸铁,因为少量的钛就可能导致石墨形态发生畸变。
浇注前加钛,不宜采用钛铁,因为钛铁在浇注温度下不易溶于铁液,钛的收得率不稳定。
需要加钛时,最好用含钛的硅铁,同时完成瞬时孕育和加钛两项任务,采用这种工艺,钛的加入量只需0.025%。
锆在铸铁中形成的氮化物比氮化钛更为稳定,也能有效地防止铸件产生针孔,但锆的原子量〔91.22是钛原子量〔47.88的1.9倍,其加入量应略多于钛,宜为0.05%左右。
可采用含锆的硅铁,在浇注前加入铁液中。