薄壁管数控绕弯塑性成形中摩擦作用机理的模拟研究.docx
《薄壁管数控绕弯塑性成形中摩擦作用机理的模拟研究.docx》由会员分享,可在线阅读,更多相关《薄壁管数控绕弯塑性成形中摩擦作用机理的模拟研究.docx(16页珍藏版)》请在冰豆网上搜索。
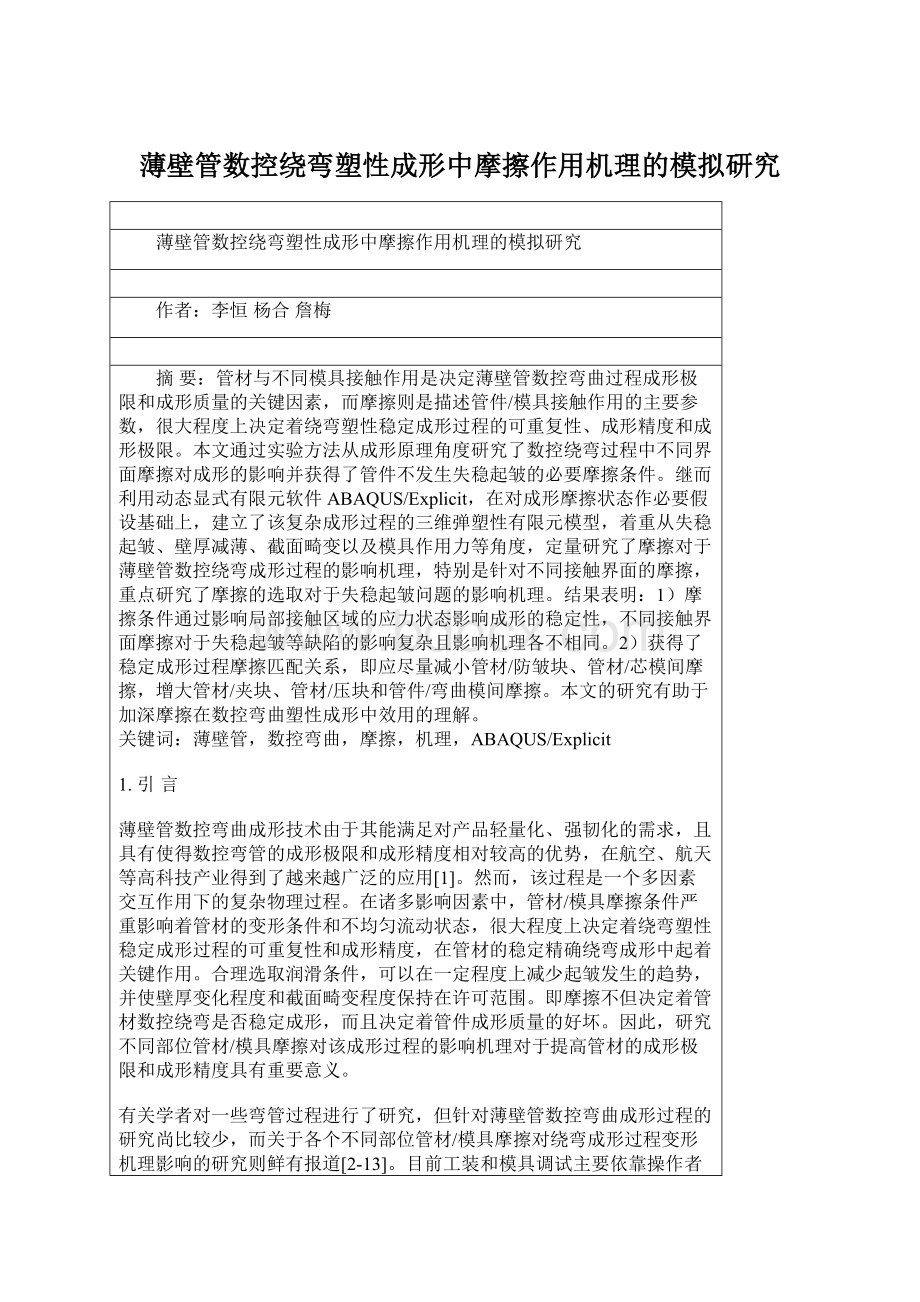
薄壁管数控绕弯塑性成形中摩擦作用机理的模拟研究
薄壁管数控绕弯塑性成形中摩擦作用机理的模拟研究
作者:
李恒杨合詹梅
摘要:
管材与不同模具接触作用是决定薄壁管数控弯曲过程成形极限和成形质量的关键因素,而摩擦则是描述管件/模具接触作用的主要参数,很大程度上决定着绕弯塑性稳定成形过程的可重复性、成形精度和成形极限。
本文通过实验方法从成形原理角度研究了数控绕弯过程中不同界面摩擦对成形的影响并获得了管件不发生失稳起皱的必要摩擦条件。
继而利用动态显式有限元软件ABAQUS/Explicit,在对成形摩擦状态作必要假设基础上,建立了该复杂成形过程的三维弹塑性有限元模型,着重从失稳起皱、壁厚减薄、截面畸变以及模具作用力等角度,定量研究了摩擦对于薄壁管数控绕弯成形过程的影响机理,特别是针对不同接触界面的摩擦,重点研究了摩擦的选取对于失稳起皱问题的影响机理。
结果表明:
1)摩擦条件通过影响局部接触区域的应力状态影响成形的稳定性,不同接触界面摩擦对于失稳起皱等缺陷的影响复杂且影响机理各不相同。
2)获得了稳定成形过程摩擦匹配关系,即应尽量减小管材/防皱块、管材/芯模间摩擦,增大管材/夹块、管材/压块和管件/弯曲模间摩擦。
本文的研究有助于加深摩擦在数控弯曲塑性成形中效用的理解。
关键词:
薄壁管,数控弯曲,摩擦,机理,ABAQUS/Explicit
1.引言
薄壁管数控弯曲成形技术由于其能满足对产品轻量化、强韧化的需求,且具有使得数控弯管的成形极限和成形精度相对较高的优势,在航空、航天等高科技产业得到了越来越广泛的应用[1]。
然而,该过程是一个多因素交互作用下的复杂物理过程。
在诸多影响因素中,管材/模具摩擦条件严重影响着管材的变形条件和不均匀流动状态,很大程度上决定着绕弯塑性稳定成形过程的可重复性和成形精度,在管材的稳定精确绕弯成形中起着关键作用。
合理选取润滑条件,可以在一定程度上减少起皱发生的趋势,并使壁厚变化程度和截面畸变程度保持在许可范围。
即摩擦不但决定着管材数控绕弯是否稳定成形,而且决定着管件成形质量的好坏。
因此,研究不同部位管材/模具摩擦对该成形过程的影响机理对于提高管材的成形极限和成形精度具有重要意义。
有关学者对一些弯管过程进行了研究,但针对薄壁管数控弯曲成形过程的研究尚比较少,而关于各个不同部位管材/模具摩擦对绕弯成形过程变形机理影响的研究则鲜有报道[2-13]。
目前工装和模具调试主要依靠操作者的经验和通过生产现场“errorandtrial”的方式进行,周期长、成本高且耗时费力,所得经验结果往往不具备普适性,而其中不同接触界面摩擦的选取是调模成功的关键和难点之一。
主要原因在于缺乏摩擦对于塑性成形的影响机理。
利用实验方法可以直接观察物理现象,并能验证有限元模拟结果的可靠性。
但由于数控绕弯过程的动态接触条件过于复杂,且大口径薄壁管材小弯曲半径的难成形条件使管件的不均匀塑性变形程度加剧,使得仅用理论解析或实验方法难以对成形过程进行深入系统的研究。
随着计算机和有限元模拟技术的深入发展,数值模拟技术,与理论及实验研究相结合,已成为解决复杂物理过程的强有力工具。
文献[14]利用实验方法研究了不同种类润滑剂对不锈钢管数控弯曲成形过程中过程参数、管件壁厚和表面质量的影响,但仅获得特定条件下某种润滑剂的宏观响应,而关于摩擦对于绕弯成形的影响机理并没有涉及,特别是没有考虑摩擦对失稳起皱等缺陷的全面的影响机理。
因此,本文首先实验研究了数控绕弯成形中的摩擦效应,得到了保证绕弯过程稳定完成所满足的摩擦必要条件,然后建立了该成形过程的三维弹塑性有限元模型,研究了管材/防皱块等不同接触界面间摩擦对薄壁管数控弯曲塑性成形过程的影响规律,着重讨论了摩擦对于失稳起皱、壁厚减薄和截面畸变等缺陷的影响机理。
2.摩擦对数控绕弯影响实验研究
薄壁管如图1所示,在数控绕弯成形过程中,管材内外壁受到多种模具的严格配合,如弯曲模、夹块、压块(带助推作用)、防皱块、芯模(带多个芯头)和顶推装置等。
弯曲时管件被弯管模和夹块带动并缠绕在弯曲模圆槽内转动,过弯曲切点转动到预设弯曲角度,管件与弯曲模的贴合使得管件达到所需要的弯曲半径;压块不但使管材与防皱块接触,同时通过摩擦对管件外侧施加一定的轴力。
在弯管成形中,管材/模具的接触界面分别有管材/防皱块、管材/芯模间隙、管材/压块、管材/弯曲模以及管材/夹块等。
图1数控弯曲成形工作原理
由此可以看出,绕弯成形本质上是依靠管材与各个不同模具之间的接触摩擦作用而完成的,管材/模具摩擦交互边界条件改变着变形材料局部甚至全局变形域的应力应变状态,从而对塑性弯曲过程,特别是失稳起皱、壁厚变化和截面畸变等缺陷的发生产生重要影响。
从成形原理角度来看,夹块对管件的夹持作用依靠夹块与管件的摩擦实现,因此管件/夹块间摩擦必须足够大,不允许管件与夹块间产生相对滑动,该摩擦类型为静摩擦;压块的助推作用同样依靠其与管件表面的摩擦来施加,管件/压块间摩擦情况直接影响着助推的效果,该摩擦一般为动摩擦;管件/防皱块间摩擦、管件/芯模间摩擦以及管件/弯曲模间摩擦同样影响着管件各部分的塑性变形,继而影响到整个变形情况。
在实际弯曲中,为了保证成形的稳定精确成形,应针对不同的摩擦界面采取不同的润滑状态。
本文通过实验研究讨论了保证管材稳定成形所需的摩擦必要条件。
图2微电脑控制液压弯管机
实验设备为自行设计定制的微电脑PLC控制液压弯管机W27YPC-63NC(图2所示)。
材料为1Cr18Ni9Ti不锈钢和LF2M铝合金,外径D为38mm、壁厚t为1mm,弯曲半径R为57mm,弯曲角α约为90°。
弯曲模转速为0.15rad/s,压块助推速度同弯曲模中心线切向线速度一致,未加顶推装置。
选用不锈钢专用拉伸油S980B为润滑剂,并对各接触表面进行不同层次的润滑。
模具参数如表1所示,其中模具尺寸和芯模参数的选取见文献[15]。
本文设计了几组实验来获得保证管材稳定成形所必需满足的摩擦条件。
表1模具参数
1)实验1:
夹持端在保持干摩擦、内槽垫硬质砂纸两种条件下,前者在弯曲过程中管件与夹块发生了相对滑动,两种材料管件弯曲前端均发生了失稳起皱现象,但在后一种加载条件下,可以保证管件与夹块不发生相对滑动,实现了稳定成形。
2)实验2:
管材/压块之间在干摩擦和加润滑剂两种成形条件下,后者情况下管材的壁厚和畸变较前者严重,有时还会导致管件与夹块发生相对滑动。
3)实验3:
增大管件/芯模和管件/防皱块间摩擦会加剧防皱块和芯模的磨损,大大减少使用寿命,并会导致管件表面划痕,同时增大对管件的拖动而使管件/夹块发生滑移,造成严重截面扁化和内侧凹坑的出现。
4)实验4:
在一组稳定成形条件下,利用了表面经过抛光的不锈钢管时,管材后端出现较明显的起皱。
但在管件/防皱块间保持为干摩擦时,后段管材堆积而发生失稳起皱。
基于实验研究,可以看到管材不同部位与不同功能模块之间的功能不同,所需润滑条件也各不相同;摩擦对于绕弯塑性弯曲成形的稳定成形发挥着重要作用,决定着这一先进成形过程能否实现精确稳定成形。
然而,由于该过程本身的复杂性及其摩擦机理研究的不足,实验研究不足以高效和深入地研究摩擦因素对塑性成形的影响机理。
因此,在实验的基础上,本文通过所建立的有限元模型进一步分析了摩擦对该成形过程的作用机理。
3.有限元模型建立及摩擦条件处理
薄壁管数控弯曲成形技术由于其能满足对产品轻量化、强韧化的需求,且具有使得数控弯管的成形极限和成形精度相对较高的优本文在前期研究的基础上[9-13],按照实际的弯曲工艺,利用动态显式有限元软件ABAQUS/Explicit,研究建立了薄壁管数控弯曲成形过程的三维弹塑性有限元模型(图3所示)。
由于在数控弯曲成形过程中,材料和边界条件平面对称,本文建立了平面对称模型。
图3三维动态显示弹塑性有限元模型
材料参数选用铝合金管材(LF2M),外径D为38mm、壁厚t为1mm,长度L为600mm。
弯曲半径R为57mm,R/D为1.5。
通过单向拉伸实验获得了铝合金管材的力学性能,如表2。
采用幂指数型应力应变关系描述材料的弹塑性加工硬化行为:
采用四节点双曲率壳单元S4R来描述薄壁管材,该单元具有沙漏控制和缩减积分功能;单元厚度方向选择5个积分点以反映面外弯曲功能。
对于弯曲模、压块(侧推)、防皱块、夹块、芯棒和芯头等刚性模具则采用离散刚体单元R3D4来描述模具对管材施加力的几何曲面。
表2管材的力学性能参数
通过选取合理的接触算法及施加方法,使模具的运动方式同实际弯曲过程相同。
接触界面分别有管材/压块(T-P)、管材/芯模(T-M)(包括管材/芯头T-B)、管材/防皱块(T-W)、管材/弯曲模(T-B)和弯曲/夹块(T-C)。
根据实际过程,将管件/夹块间运动属性设为“小滑动模式”外,其余接触界面则均采用“有限滑动模式”。
接触界面间均采用面-面接触方式;除了管材/芯模间接触采用罚函数法作为接触约束算法之外,其余界面均采用动态约束。
边界约束和载荷施加通过位移/转动和速度/角速度两种方式实现。
其中,弯曲模和夹块采用一致的自由度,只开放绕弯曲模中心的转动自由度;压块只开放X方向的平动自由度,且平动速度与弯曲模转动线速度保持一致;防皱块的自由度在弯曲过程中全部被约束。
芯模在管材弯曲过程中X方向的位移为零,但在到达弯曲角度时回撤。
芯轴和柔性芯头以及芯头之间的相对运动较为复杂,芯头可随管材的弯曲而发生转动。
本文利用运动属性为“铰接”的连接单元对芯棒和芯头以及芯头之间的接触状态进行了建模[16]。
图4库仑摩擦模型
在以上建模基础上,选取合理的摩擦属性来描述加载过程中管材与模具表面传递法向压力和切向剪应力的行为。
对于冷成形过程,一般选用经典库仑摩擦模型来描述工件与模具之间的摩擦接触状态(如图4所示),认为摩擦力与接触面上的正压力成正比,数学表达式为[16]
τ=μp
其中,τ为摩擦力,μ为摩擦系数,p为接触面上的正压应力。
摩擦系数μ通常根据实验来确定。
本文假设成形过程中各摩擦接触状态摩擦系数为常值,与滑动速率、接触面压力、环境温度和其它场变量无关,同时假设摩擦系数在不同方向上是各向同性的。
如图所示,若摩擦剪应力大于μp,则管材/模具间处于粘着状态;当摩擦应力小于μp,管材/模具之间产生相对滑动。
由于摩擦切应力达到材料的剪切屈服强度时,成形金属的接触表面要产生塑性流动,因此在应用中,摩擦系数的极限值为0.5~0.577。
但在实际工艺中,要采取特殊夹持手段来保证两个接触界面如管材/夹块之间不发生相对滑动,此时在库仑摩擦模型的基础上,将摩擦系数μ设为较大的值来满足该夹持要求。
ABAQUS建立了“Rough”模型保证两个接触表明一旦发生接触,将不再发生相对滑动,在“Rough”模型中μ取值为∞。
本文依据实验结果,设置了模拟中各接触界面间的摩擦系数取值范围。
表3所示为各个接触界面不同的摩擦状况。
其中括号中的摩擦系数为模拟时选用的各界面的稳定成形摩擦系数,这些值的选取通过实验研究获得。
管材/夹块间摩擦系数可以大于0.6,必要时选用“Rough”模型,以满足在弯曲加载过程中管件与夹块接触后不允许发生相对滑动的条件。
表3接触边界摩擦条件
4.结果与讨论
本文在前期研究衡量管件质量好坏的指标为失稳起皱、截面变化和壁厚变化。
对于壁厚变化,通过弯曲后的壁厚变化来衡量。
而由于绕弯过程特殊接触边界条件,使得管件截面变化呈现出主要在截面纵向发生变形的特点,因此本文定义管材截面纵向伸长量变化率L来衡量截面畸变程度。
由于在管材绕弯过程中中性层内移越严重,则内侧压缩变形越大,从而材料发生失稳起皱的趋势也越明显,而由力矩守恒原理,材料内移越严重则外侧所受拉应力和内侧轴向压应力差值也大。
因此本文以内外侧轴向压应力的差值f这一无量纲化指标的大小作为发生失稳起皱的指标。
f越大,则起皱趋势越明显。
由文献[14]知,失稳起皱只发生在初始变形时刻,因此一般考虑选取弯曲角度30度左右以内的f值作为判断标准。
4.1管材/防皱块摩擦的影响
管材/防皱块摩擦系数分别为0、0.1、0.2、0.3、0.4和0.5,其它接触界面摩擦系数根据实验和建模分析理论结果选取。
在建模时使防皱块同弯曲模凹槽100%的接触,防皱块与X方向的倾角为0。
其余参数均与实验中采用的参数保持一致。
结果表明,在这几种摩擦条件下,管材均没有发生失稳起皱现象。
但文献[15]理论研究表明,增大这一界面间摩擦系数有助于抵抗受压失稳,为了进一步证实这一观点,本文考察了不同润滑条件下的f值。
模拟表明,尽管在不同摩擦条件下管材达到稳定变形后的应力应变保持不变,但其历史曲线却有所不同。
图5所示为不同摩擦系数对应的f值。
结果表明,随着管材/防皱块摩擦减小,f值有所增大,即起皱趋势较明显。
但整体上对于失稳起皱的影响显著性较小。
这与理论预测结果相近。
图5管材/防皱块不同摩擦系数对应的f值图6管材/防皱块不同摩擦对应的截面畸变情况
本文考察了在不同管材/防皱块摩擦下的截面畸变率和壁厚变化情况。
图6和7分别为弯曲后不同管材/防皱块摩擦条件下的截面畸变和壁厚变化曲线。
图6表明,随着管材/防皱块摩擦系数的增大,管材截面畸变越来越严重。
图7则表明,管材/防皱块间的摩擦对外侧壁厚减薄的影响较小,但内侧壁厚则随摩擦系数的增大而减少。
另外,图8所示为不同管材/防皱块摩擦下弯曲模上作用力历史曲线。
可见,随着管材/防皱块摩擦的增大,弯曲模所受作用力增大。
考察了弯曲成形后不同摩擦条件下处于弯曲切点位置处的节点流动情况。
研究发现,摩擦系数越大,过弯曲切点的单元越少。
μ为0.5情况下要比μ为0时要少进入弯曲变形区2个单元。
图7不同管材/防皱块摩擦对应的内外侧壁厚变化图8不同管材/防皱块摩擦对应的弯曲模作用力
由上可知,管材与防皱块之间的摩擦通过影响局部接触区域的应力状态,影响着管材的成形质量。
但除了对管件截面畸变的影响较大之外,对于失稳起皱和壁厚变化的影响则较小;同时,在实际生产中,防皱块与管材处于较剧烈的摩擦接触状态,管材对防皱块施加的法向压力和摩擦力对刃口很薄(约为0.127)的防皱块磨损很大。
因此,为了避免防皱块易损件的破坏,常在管材/防皱块间加一定的润滑油。
4.2管材/芯模摩擦的影响
管材/防在模拟中,管材/芯模之间的摩擦系数取值分别为0~0.5。
其余参数均与实验中采用的参数保持一致。
结果表明,摩擦系数为0时管材不发生失稳起皱,而摩擦系数分别为0.3和0.5时管材发生了起皱,且后者的起皱程度大于前者。
图9所示分别为两种情况下管材开始发生起皱的时刻变形云图。
这一结果似乎同文献[15]的理论结果不一致。
文献[15]通过数值-解析方法对数控绕弯成形起皱进行了研究,认为管材/芯模之间的摩擦对失稳起皱的影响可以忽略不计。
究其原因,是由于两种方法采取的加载条件不一致引起的。
在理论预测中,假设管材和夹块间处于理想夹持条件,即夹块上的压力管件与夹块永远不会发生相对滑动。
而在模拟结果中,管材/夹块摩擦系数取为0.6,因此若管材/芯模摩擦过大,则会对管材产生大的拖动力,导致管材/夹块间摩擦由静摩擦转化为动摩擦,发生相对滑动,导致过多的材料堆积在压缩变形区,从而导致管材在弯曲前段发生失稳。
实验验证了这一模拟结果。
图9管材/芯模间不同摩擦系数失稳起皱时刻
本文研究了稳定变形时刻前f值的历史变化曲线,如图10所示。
可以看到,随着管材/芯模摩擦的增大,f值反而有所减小。
这主要是由于此时所发生的起皱失稳缺陷机理不同于正常弯曲变形情况下受压失稳导致的。
在摩擦系数分别为0.3和0.5时,管材/夹块间均发生了相对滑动,且0.5条件下的滑动距离大于0.3条件对应的滑动距离。
分析认为,管材/夹块间相对滑动导致成形加载条件失效,夹持端材料流入弯曲段的末端,减弱了这部分材料的传力作用,弯曲切点后的材料的滑动速度大大降低,材料不能被有效地拉伸过弯曲切点并弯曲成形,由弯曲变形所产生的内侧压应力减小,同时过多的材料流入弯曲变形区又大大减小了这部分材料的轴向压应力,因而表现为随着管材/芯模摩擦的增大,内侧轴向压应力越来越小,f值有所减小。
模拟结果显示,相比μ为0摩擦条件,管材/芯模摩擦系数为0.3时少进入弯曲变形区10个单元左右。
图10管材/芯模不同摩擦系数对应的f值图11不同管材/芯模摩擦系数对应壁厚变化
为了进一步验证以上理论分析,本文在管材/芯模摩擦系数为0.5情况下,将对应的管材/夹块摩擦分别取为0.8和“Rough”两种特殊情况。
模拟结果表明,管材/夹块摩擦系数即使在0.8情况下管材/夹块间仍然有滑动,这说明管材/芯模件摩擦的增大将大大增加芯模与管材之间的拖动阻力,导致成形失败;当管材/夹块间摩擦按照“Rough”模型通过有限元模型计算后,管材/夹块没有发生相对滑动,但此时在夹块附近,管材截面发生了肉眼可见的明显的塌陷。
另外,本文在管材/夹块间摩擦模型为“Rough”条件下,比较了不同管材/芯模间摩擦系数对应的f值历史曲线,结果表明,在保证管材/夹块间不发生相对滑动的加载条件下,管材/芯模间摩擦条件对管材失稳起皱的影响不大,从而进一步验证了文献[15]理论分析的正确性。
由于管材/芯模间摩擦在0.3和0.5情况下,管材发生了严重的起皱变形,本文没有对此种情况下的截面畸变进行比较,只比较了壁厚和弯曲模所受作用力。
图11和12分别为不同管材/芯模摩擦条件下管材的壁厚变化和弯曲模作用力历史曲线。
研究表明,管材/芯模间摩擦系数越大,管材外侧壁厚减薄程度越大,但内侧壁厚增厚程度不大。
同时,管材/芯模间摩擦系数越小,弯曲模所受的作用力也越小。
图表明,管材/芯模摩擦为0.5时模具作用力在1.2时刻左右发生了突变,由峰顶快速下降,而管材/芯模摩擦为0.3时这一现象同样存在,但幅度要要得多。
通过观察两种情况下材料的变形网格图,失稳起皱时刻同图中的突变发生时刻相同,从而进一步说明了管材/芯模摩擦对失稳起皱的影响的理论解释。
图12不同管材/芯模摩擦对应弯曲模作用力图13管材/夹块摩擦为0时起皱时刻变形云图
4.3管材/夹块摩擦的影响
管材/防在在模拟中,管材/夹块间的摩擦系数取值分别为0~0.5。
其余参数均与实验中采用的参数保持一致。
模拟结果表明,摩擦系数为0时管件发生了严重的失稳起皱(图13所示),在0.3和0.5时管件能够实现无皱弯曲成形。
图14为不同管材/夹块摩擦系数条件下f值历史曲线。
可以看到,管材/夹块摩擦系数对f值的影响同管材/芯模类似,f值较大时管材发生没有发生失稳起皱,反而在较小时发生了失稳。
这是由于减小管材/夹块摩擦和增大管材/芯模情况下,失稳起皱的机理相同导致的。
图14不同管材/夹块摩擦系数对应f值图15不同管材/夹块摩擦系数对应的壁厚变化
本文比较了不发生失稳起皱情况下管材的壁厚变化和截面畸变情况。
图15和16表明,管材/夹块摩擦条件对管材壁厚变化的影响很小,但增大这一界面的摩擦将有利于控制管材的截面畸变程度。
图16不同管材/夹块摩擦系数对应的截面畸变图17不同管材/压块摩擦系数对应的f值
4.4管材/压块摩擦的影响
模拟中,管材/夹块间的摩擦系数取值分别为0~0.5。
其余参数均与实验中采用的参数保持一致。
研究表明,在这几种情况下,管材均没有发生失稳起皱。
这说明管材/压块摩擦条件对失稳起皱的影响比较小。
但进一步考察不同条件下对应的f值历史曲线(图17所示),本文发现,减小管材/压块摩擦,整体上有助于减小起皱发生的趋势,但在摩擦系数较大情况下再增大摩擦,其对失稳起皱的影响已不明显。
本文比较了不同管材/压块摩擦条件下管材的壁厚变化和截面畸变情况。
由图18可知,管材/压块间摩擦越大,管材截面畸变程度控制得越好;管材/压块摩擦的减小加剧了管材截面畸变程度。
同时图19表明,增大管材/压块间摩擦有助于控制外侧壁厚的减薄程度。
这是由于,增大管材/压块摩擦能够更好地发挥压块的侧推作用,即更有效地将材料向弯曲区域推进,从而同时控制截面畸变程度和壁厚减薄。
图18不同管材/压块摩擦系数对应截面畸变图19不同管材/压块摩擦系数对应壁厚变化
对弯曲模作用力历史变化的观察表明(图20所示),管材/压块间摩擦系数越小,弯曲模所受的作用力越大。
但在大于一定程度后再增加摩擦对模具作用力的影响不再显著增大。
因此,在实际生产中,应将管材/压块的摩擦增大,从而保证管件的截面畸变程度和壁厚减薄程度,但也不应如管材/夹块一样过分增大,不但不能显著提高壁厚减薄和截面畸变程度,而且容易造成管材外表面产生划伤。
图20不同管材/压块摩擦系数对应弯曲模作用力图21不同管材/弯曲模摩擦系数对应的f值
4.5管材/弯曲模摩擦的影响
在模拟中,管材/弯曲模间的摩擦系数取值分别为0~0.5。
其余参数均与实验中采用的参数保持一致。
在所有摩擦条件下,管材均没有发生失稳起皱。
图21所示为不同管材/弯曲模摩擦条件下f值的历史变化曲线。
可以知道,随着管材/弯曲模间摩擦系数的增大,管材失稳起皱的趋势越明显,这同文献[15]中的理论预测结果一致。
这是由数控绕弯塑性成形过程的塑性变形特点决定的,即材料被夹持过弯曲切点以后便与弯曲模内槽贴模,并产生压缩变形。
此时若这一界面间的摩擦力增大,则阻碍了临界失稳区坯料的稳定压缩变形而发生起皱缺陷。
本文考察了不同管材/弯曲模摩擦条件下管材截面畸变、壁厚变薄情况。
图22表明,管材/弯曲模间的摩擦情况对管材外侧壁厚的变化没有显著影响,但显然在摩擦较大的情况下,管材内侧壁厚增厚程度较小。
同时图23表明,增大管材/弯曲模间摩擦可以一定程度上控制管材的截面畸变程度。
图22不同管材/弯曲模摩擦系数对应的截面畸变图23不同管材/弯曲模摩擦系数对应的壁厚变化
图24所示为不同管材/弯曲模条件下弯曲模作用力的历史曲线。
研究表明,管件/弯曲模摩擦越大,弯曲模作用力越小。
因此,综合以上分析,在实际生产中,应将管材/弯曲模的摩擦增大,从而进一步减轻截面畸变程度,又不会对失稳起皱和壁厚变化产生太大的影响。
图24不同管材/弯曲模摩擦系数对应弯曲模作用力
5.结论与展望
在模拟中,不同管材/模具摩擦影响着管材局部或整体的受力和流动情况,对薄壁管数控绕弯成形过程的影响复杂,同时各自的摩擦响应机理各不相同。
本文的研究结论如下:
1)增大管材/防皱块摩擦有助于减少起皱趋势。
同时实验研究表明增大管材/防皱块间隙将加剧防皱块的磨损。
鉴于其对失稳起皱的影响显著程度并不特别高,因此应尽量减小管材/防皱块间摩擦。
在理想夹持条件下,管材/芯模摩擦对失稳起皱的影响不大;但在一般条件下,管材/芯模摩擦增大会对管材产生大的拖动力,导致管材/夹块产生相对滑动,从而使管材弯曲前端易发生失稳起皱。
管材/芯模间摩擦系数越大,管材外侧壁厚减薄程度越大,但内侧壁厚增厚程度不大;同时,管材/芯模间摩擦系数越小,弯曲模所受的作用力也越小。
2)减小管材/夹块摩擦同增大管材/芯模的失稳起皱的机理相同。
管材/夹块摩擦条件对管材壁厚变化的影响很小,但增大这一界面的摩擦将有利于控制管材的截面畸变程度。
减小管材/压块摩擦,整体上有助于减小起皱发生的趋势,但在摩擦系数较大情况下再增大摩擦,其对失稳起皱的影响已不明显。
增大管材/压块间摩擦有助于控制截面畸变程度和外侧壁厚的减薄程度。
管材/压块间摩擦系数越小,弯曲模所受的作用力越大。
实验中采用干摩擦就可以满足要求而不划伤管件外表面