易拉罐知识.docx
《易拉罐知识.docx》由会员分享,可在线阅读,更多相关《易拉罐知识.docx(12页珍藏版)》请在冰豆网上搜索。
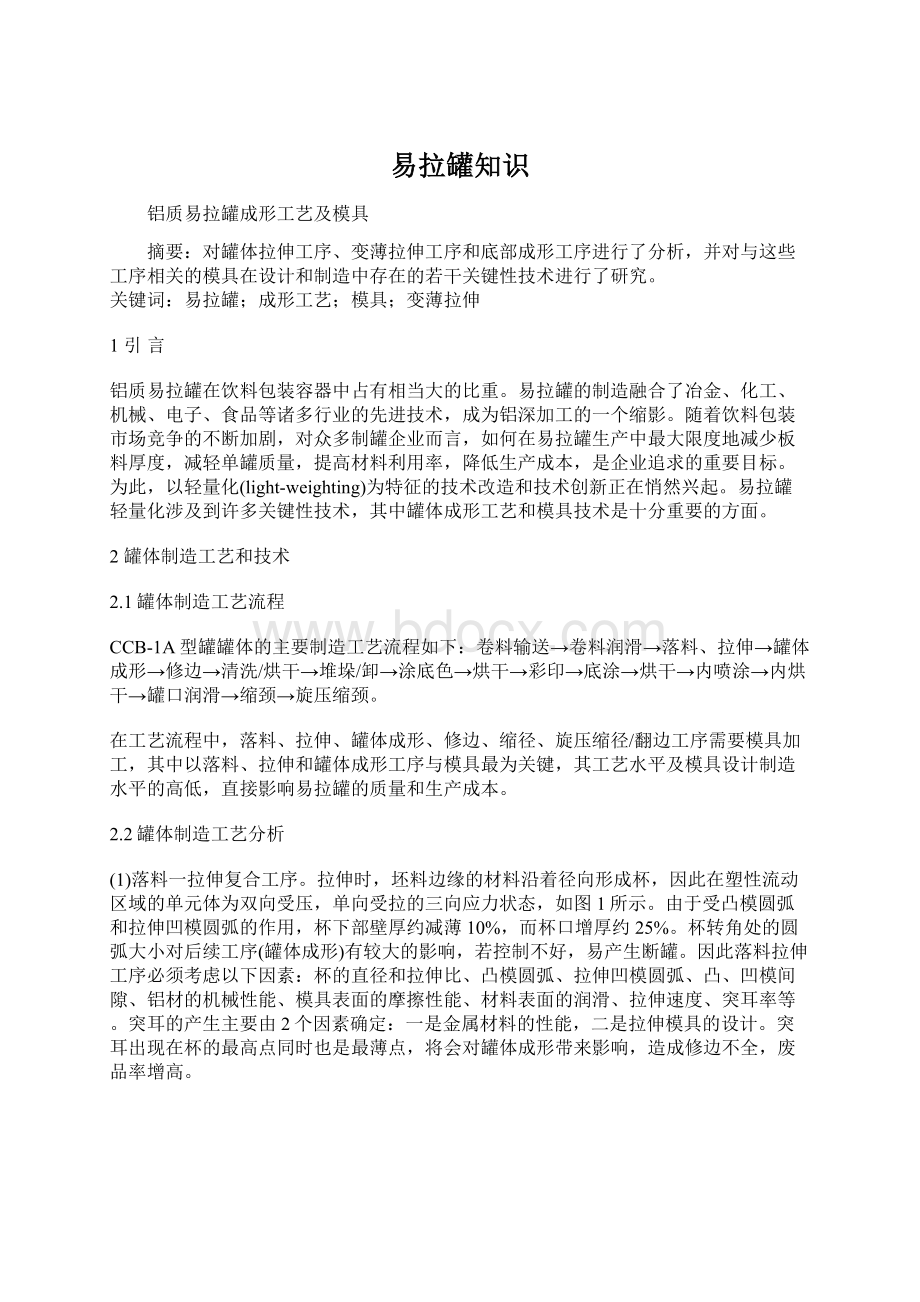
易拉罐知识
铝质易拉罐成形工艺及模具
摘要:
对罐体拉伸工序、变薄拉伸工序和底部成形工序进行了分析,并对与这些工序相关的模具在设计和制造中存在的若干关键性技术进行了研究。
关键词:
易拉罐;成形工艺;模具;变薄拉伸
1引言
铝质易拉罐在饮料包装容器中占有相当大的比重。
易拉罐的制造融合了冶金、化工、机械、电子、食品等诸多行业的先进技术,成为铝深加工的一个缩影。
随着饮料包装市场竞争的不断加剧,对众多制罐企业而言,如何在易拉罐生产中最大限度地减少板料厚度,减轻单罐质量,提高材料利用率,降低生产成本,是企业追求的重要目标。
为此,以轻量化(light-weighting)为特征的技术改造和技术创新正在悄然兴起。
易拉罐轻量化涉及到许多关键性技术,其中罐体成形工艺和模具技术是十分重要的方面。
2罐体制造工艺和技术
2.1罐体制造工艺流程
CCB-1A型罐罐体的主要制造工艺流程如下:
卷料输送→卷料润滑→落料、拉伸→罐体成形→修边→清洗/烘干→堆垛/卸→涂底色→烘干→彩印→底涂→烘干→内喷涂→内烘干→罐口润滑→缩颈→旋压缩颈。
在工艺流程中,落料、拉伸、罐体成形、修边、缩径、旋压缩径/翻边工序需要模具加工,其中以落料、拉伸和罐体成形工序与模具最为关键,其工艺水平及模具设计制造水平的高低,直接影响易拉罐的质量和生产成本。
2.2罐体制造工艺分析
(1)落料一拉伸复合工序。
拉伸时,坯料边缘的材料沿着径向形成杯,因此在塑性流动区域的单元体为双向受压,单向受拉的三向应力状态,如图1所示。
由于受凸模圆弧和拉伸凹模圆弧的作用,杯下部壁厚约减薄10%,而杯口增厚约25%。
杯转角处的圆弧大小对后续工序(罐体成形)有较大的影响,若控制不好,易产生断罐。
因此落料拉伸工序必须考虑以下因素:
杯的直径和拉伸比、凸模圆弧、拉伸凹模圆弧、凸、凹模间隙、铝材的机械性能、模具表面的摩擦性能、材料表面的润滑、拉伸速度、突耳率等。
突耳的产生主要由2个因素确定:
一是金属材料的性能,二是拉伸模具的设计。
突耳出现在杯的最高点同时也是最薄点,将会对罐体成形带来影响,造成修边不全,废品率增高。
基于以上分析,确定拉伸工序选择的拉伸比m=36.55%,坯料直径Dp=140.20±0.0lmm,杯直径Dc=88.95mm。
(2)罐体成形工序。
变薄拉伸工艺分析。
典型的铝罐拉伸、变薄拉伸过程如图2所示,变薄拉伸过程中受力状况如图3所示。
在拉伸过程中,集中在凹模口内锥形部分的金属是变形区,而传力区则为通过凹模后的筒壁及壳体底部。
在变形区,材料处于轴向受拉、切向受压、径向受压的三向应力状态,金属在三向应力的作用下,晶粒细化,强度增加,伴有加工硬化的产生。
在传力区,各部分材料受力状况是不相同的,其中位于凸模圆角区域的金属受力情况最为恶劣,其在轴向、切向两向受拉,径向受压,因而材料的减薄趋势严重,金属易从此处发生断裂,从而导致拉伸失败。
比较变形区和传力区金属的应力状态可知:
变薄拉伸工艺能否顺利进行主要取决于拉伸凸模圆角部位的金属所受拉应力的大小,当拉应力超过材料强度极限时就会引起断裂,否则拉伸工艺可以顺利进行。
因此,减小拉伸过程中的拉应力成为保证拉伸顺利进行的关键。
变薄拉伸拉伸比的选择为:
再拉伸:
25.7%,第1次变薄拉伸:
20%~25%,第2次变薄拉伸:
23%~28%,第3次变薄拉伸:
35%~40%。
在成形过程中,影响金属内部所受拉应力大小的因素很多,其中凹模锥角。
的取值直接关系到变形区金属的流动特性,进而影响拉伸所需成形力的大小,所以,其数值合理与否对工艺的实施有着重要影响。
当α较小时,变形区的范围比较大,金属易于流动,网格的畸变小。
随着α的增大,变形区的范围减小,金属的变形集中,流动阻力增大,网格歧变严重。
而且,随着凹模锥角的增大,变形区材料的应变相应增加,这说明凹模锥角较大时,不仅金属的变形范围集中,而且变形量迅速上升,因而使得变形区金属的加工硬化现象加剧,导致金属内部的应力上升,从而对拉伸产生不利影响。
另一方面,在α过于大或过小时都会引起拉伸力的增加,其原因在于:
当α过大时,金属流动急剧,材料的加工硬化效应显著,并且随着锥角的增大,凹模锥面部分产生的阻碍金属流动的分力加大,因而所需拉伸力增加;当。
过小时,虽然金属流动的转折小,但由于变形区金属与凹面的接触锥面长,锥面上总摩擦阻力大,因此网格畸变虽小,总拉伸力却增大。
由此可见,凹模锥角的合理确定应同时考虑变形区材料的变形特点以及模具与工件间的摩擦状况,凹模锥角合理范围的确定对拉伸工艺有着直接的影响。
工艺试验表明,对于CCB-1A型罐用铝材3104H19,其凹模锥角合理取值在α=5°-8°为宜。
底部成形工艺分析。
罐底部成形发生在凸模行程的终点,采用的是反向再拉伸工艺。
图4为罐底成形受力状况示意图,底部成形力主要取决于摩擦力的性质以及压边力的大小。
通常,材料的厚度和强度是一对矛盾,材料愈薄,强度愈低,因此轻量化技术要求减少罐底直径及设计特殊的罐底形状。
工艺试验表明,罐底沟外壁夹角若α1大于40°,将大大减小罐底耐压。
考虑到金属的成形性,凸模圆弧R不能小于3倍的料厚。
但R太大,将会减小强度。
球面和罐底沟内壁圆弧R1,至少为3倍料厚,通常R1取4~5倍料厚。
减小罐底沟内壁夹角α2,将增加强度,生产中大多数采用10°以下。
罐底部有两处失效点:
一为底部球面;二为连接球面和侧壁的罐底部圆弧R。
罐底球面的强度取决于以下几个因素:
材料的弹性模量、底部直径、材料的强度、球面半径以及在底部成形时金属的变薄程度。
罐底球面半径常用公式R球=d1/0.77确定,实际取R球=45.72mm
3模具设计与制造
3.1罐体拉伸模
罐体拉伸过程实际上是筒形件的拉伸过程,拉伸过程中,其材料的凸缘部分在压应力作用下易失稳,导致起皱,因此必须考虑设置防止起皱的压边装置。
当材料通过凹模时,凹模圆角部分是一个过渡区,其变形较复杂,除了径向拉伸与切向压缩外,还受弯曲作用,因此凹模圆角选择尤为重要。
材料通过凹模圆角后,处于拉伸状态,由于拉伸力来自凸模压力,是经过凸模圆角处传递的,凸模圆角处的材料变薄最严重,此处成为最易破裂的危险断面。
落料一拉伸组合模结构如图5所示。
(1)模具材料:
凸、凹模均选择镶硬质合金的材料。
(2)变形量:
在易拉罐行业内,一般采用拉伸比δ表示变形量,δn=(dn-1-dn)/dn-1×100%,按此公式,计算如下:
首次拉伸取δ1=(d0-d1)/d0×100%=(140.2001-88.951)/140.2004×100%=36.6%。
再拉伸取δ2=(d1-d2)/d1×100%=(88.951-66.015)/88.951×100%=25.8%。
一般要求2次总拉伸比δ≤64%,δ1≥δ2≥……≥δn,δ1≤40%。
(3)压边装置:
采用波形压边圈,0.2-0.3MPa压缩空气作为动力源。
(4)拉伸模工作部参数:
圆角半径:
拉伸凹模圆角半径rA取3.556mm,再拉伸凹模圆角半径rA取1.78mm。
拉伸凸模圆角半径rB取2.921mm,再拉伸凸模圆角半径取rB2.286mm。
间隙:
拉伸模凸、凹模单边间隙Z/2大,则摩擦小,能减少拉伸力,但间隙大,精度不易控制;拉伸模凸、凹模单边间隙Z/2小,则摩擦大,增加拉伸力。
单边间隙Z/2可按以下公式计算:
Z/2=tmax+Kt
式中tmax--最大料厚,取0.285+0.005mm
t--公称料厚,取0.285mm
K--系数,当t<0.4mm时,取0.08
则Z/2=0.290+0.08×0.285=0.313mm。
3.2变薄拉伸模易拉罐罐体成形实际上是将再拉伸和3道变薄拉伸组合在一起的组合工序。
现将变薄拉伸模的设计介绍如下:
(1)模具材料。
凸模:
基体材料为合金工具钢,凸模材料为M2,热处理硬度60~62HRC,镀TiN。
凹模(变薄拉伸环):
基体材料为合金工具钢,模口材料为硬质合金(牌号为VALENITEVCID-H.L.D或KE-84KENNAMETAL)。
(2)变形量。
变薄拉伸比方的计算公式为:
δ=(tn-tn-1)/tn×100%,其中tn、tn-1分别为n次及n-1次变薄拉伸后的零件侧面壁厚,计算得:
δ1=(0.285-0.225)/0.285×100%=21.05%;δ2=(0.225-0.170)/0.225×100%=24.44%;δ3=(0.170-0.106)/0.170×100%=37.65%。
制罐工厂常常根据给定的材料厚度、罐体厚、薄壁要求、拉伸环和凸模尺寸、拉伸机精度等条件,编制拉伸环和凸模的匹配表供技术人员、模具维修人员和操作人员选配凸模和拉环。
(3)模具的工作部分参数。
凸模:
凸模圆弧R1.016±0.025mm,再拉伸凸模圆弧R2.286mm,罐底沟外侧壁圆弧R10.478±0.013mm。
变薄拉伸环:
凹模锥角α=5°,工作带宽度h=0.38+0.25mm。
3.3罐底成形模
罐底成形模结构如图6所示。
罐底凸模材料选用合金工具钢Crl2MoV,热处理硬度60~64HRC,其轮廓形状应与罐型设计一致。
底压边模材料选用合金工具钢Cr5MoV,热处理硬度58~60HRC,其轮廓形状应与凸模相匹配。
4结束语
(1)拉伸工序考虑的重要因素有:
拉伸比、凸、凹模圆弧半径、凸、凹模间隙、铝材机械性能、润滑、作业参数。
(2)变薄拉伸工序中凹模锥角。
的大小关系到变形区金属的流动性质、应力大小以及模具的受力情况,合理的取值范围为α=5°-8°。
(3)合适的罐型设计是轻量化技术能否实施的关键。
研究表明,对于CCB-1A型罐,设计参数选择:
底沟外壁夹角α1=32°,罐底沟内壁夹角α2=5°,凸模圆弧R=1.016mm,球面和罐底沟内壁圆弧R1=1.524mm,罐底球面半径R球=45.72mm,可以大大增加罐体强度。
易拉罐是由三种不同成分的铝合金组成,罐体、罐盖、拉环。
铝质是制罐的关键,罐体不成形、罐盖口拉不开都是铝质的问题。
在国内开模具没有问题。
下面是制造工艺,希望对你有所帮助。
罐体制造工艺和技术:
罐体制造工艺流程
CCB-1A型罐罐体的主要制造工艺流程如下:
卷料输送→卷料润滑→落料、拉伸→罐体成形→修边→清洗/烘干→堆垛/卸→涂底色→烘干→彩印→底涂→烘干→内喷涂→内烘干→罐口润滑→缩颈→旋压缩颈。
在工艺流程中,落料、拉伸、罐体成形、修边、缩径、旋压缩径/翻边工序需要模具加工,其中以落料、拉伸和罐体成形工序与模具最为关键,其工艺水平及模具设计制造水平的高低,直接影响易拉罐的质量和生产成本。
罐体制造工艺分析
(1)落料一拉伸复合工序。
拉伸时,坯料边缘的材料沿着径向形成杯,因此在塑性流动区域的单元体为双向受压,单向受拉的三向应力状态,如图1所示。
由于受凸模圆弧和拉伸凹模圆弧的作用,杯下部壁厚约减薄10%,而杯口增厚约25%。
杯转角处的圆弧大小对后续工序(罐体成形)有较大的影响,若控制不好,易产生断罐。
因此落料拉伸工序必须考虑以下因素:
杯的直径和拉伸比、凸模圆弧、拉伸凹模圆弧、凸、凹模间隙、铝材的机械性能、模具表面的摩擦性能、材料表面的润滑、拉伸速度、突耳率等。
突耳的产生主要由2个因素确定:
一是金属材料的性能,二是拉伸模具的设计。
突耳出现在杯的最高点同时也是最薄点,将会对罐体成形带来影响,造成修边不全,废品率增高。
基于以上分析,确定拉伸工序选择的拉伸比m=36.55%,坯料直径Dp=140.20±0.0lmm,杯直径Dc=88.95mm。
(2)罐体成形工序。
变薄拉伸工艺分析。
典型的铝罐拉伸、变薄拉伸过程如图2所示,变薄拉伸过程中受力状况如图3所示。
在拉伸过程中,集中在凹模口内锥形部分的金属是变形区,而传力区则为通过凹模后的筒壁及壳体底部。
在变形区,材料处于轴向受拉、切向受压、径向受压的三向应力状态,金属在三向应力的作用下,晶粒细化,强度增加,伴有加工硬化的产生。
在传力区,各部分材料受力状况是不相同的,其中位于凸模圆角区域的金属受力情况最为恶劣,其在轴向、切向两向受拉,径向受压,因而材料的减薄趋势严重,金属易从此处发生断裂,从而导致拉伸失败。
比较变形区和传力区金属的应力状态可知:
变薄拉伸工艺能否顺利进行主要取决于拉伸凸模圆角部位的金属所受拉应力的大小,当拉应力超过材料强度极限时就会引起断裂,否则拉伸工艺可以顺利进行。
因此,减小拉伸过程中的拉应力成为保证拉伸顺利进行的关键。
变薄拉伸拉伸比的选择为:
再拉伸:
25.7%,第1次变薄拉伸:
20%~25%,第2次变薄拉伸:
23%~28%,第3次变薄拉伸:
35%~40%。
在成形过程中,影响金属内部所受拉应力大小的因素很多,其中凹模锥角。
的取值直接关系到变形区金属的流动特性,进而影响拉伸所需成形力的大小,所以,其数值合理与否对工艺的实施有着重要影响。
当α较小时,变形区的范围比较大,金属易于流动,网格的畸变小。
随着α的增大,变形区的范围减小,金属的变形集中,流动阻力增大,网格歧变严重。
而且,随着凹模锥角的增大,变形区材料的应变相应增加,这说明凹模锥角较大时,不仅金属的变形范围集中,而且变形量迅速上升,因而使得变形区金属的加工硬化现象加剧,导致金属内部的应力上升,从而对拉伸产生不利影响。
另一方面,在α过于大或过小时都会引起拉伸力的增加,其原因在于:
当α过大时,金属流动急剧,材料的加工硬化效应显著,并且随着锥角的增大,凹模锥面部分产生的阻碍金属流动的分力加大,因而所需拉伸力增加;当。
过小时,虽然金属流动的转折小,但由于变形区金属与凹面的接触锥面长,锥面上总摩擦阻力大,因此网格畸变虽小,总拉伸力却增大。
由此可见,凹模锥角的合理确定应同时考虑变形区材料的变形特点以及模具与工件间的摩擦状况,凹模锥角合理范围的确定对拉伸工艺有着直接的影响。
工艺试验表明,对于CCB-1A型罐用铝材3104H19,其凹模锥角合理取值在α=5°-8°为宜。
底部成形工艺分析。
罐底部成形发生在凸模行程的终点,采用的是反向再拉伸工艺。
图4为罐底成形受力状况示意图,底部成形力主要取决于摩擦力的性质以及压边力的大小。
通常,材料的厚度和强度是一对矛盾,材料愈薄,强度愈低,因此轻量化技术要求减少罐底直径及设计特殊的罐底形状。
工艺试验表明,罐底沟外壁夹角若α1大于40°,将大大减小罐底耐压。
考虑到金属的成形性,凸模圆弧R不能小于3倍的料厚。
但R太大,将会减小强度。
球面和罐底沟内壁圆弧R1,至少为3倍料厚,通常R1取4~5倍料厚。
减小罐底沟内壁夹角α2,将增加强度,生产中大多数采用10°以下。
罐底部有两处失效点:
一为底部球面;二为连接球面和侧壁的罐底部圆弧R。
罐底球面的强度取决于以下几个因素:
材料的弹性模量、底部直径、材料的强度、球面半径以及在底部成形时金属的变薄程度。
罐底球面半径常用公式R球=d1/0.77确定,实际取R球=45.72mm
模具设计与制造
罐体拉伸模
罐体拉伸过程实际上是筒形件的拉伸过程,拉伸过程中,其材料的凸缘部分在压应力作用下易失稳,导致起皱,因此必须考虑设置防止起皱的压边装置。
当材料通过凹模时,凹模圆角部分是一个过渡区,其变形较复杂,除了径向拉伸与切向压缩外,还受弯曲作用,因此凹模圆角选择尤为重要。
材料通过凹模圆角后,处于拉伸状态,由于拉伸力来自凸模压力,是经过凸模圆角处传递的,凸模圆角处的材料变薄最严重,此处成为最易破裂的危险断面。
落料一拉伸组合模结构如图5所示。
(1)模具材料:
凸、凹模均选择镶硬质合金的材料。
(2)变形量:
在易拉罐行业内,一般采用拉伸比δ表示变形量,δn=(dn-1-dn)/dn-1×100%,按此公式,计算如下:
首次拉伸取δ1=(d0-d1)/d0×100%=(140.2001-88.951)/140.2004×100%=36.6%。
再拉伸取δ2=(d1-d2)/d1×100%=(88.951-66.015)/88.951×100%=25.8%。
一般要求2次总拉伸比δ≤64%,δ1≥δ2≥……≥δn,δ1≤40%。
(3)压边装置:
采用波形压边圈,0.2-0.3MPa压缩空气作为动力源。
(4)拉伸模工作部参数:
圆角半径:
拉伸凹模圆角半径rA取3.556mm,再拉伸凹模圆角半径rA取1.78mm。
拉伸凸模圆角半径rB取2.921mm,再拉伸凸模圆角半径取rB2.286mm。
间隙:
拉伸模凸、凹模单边间隙Z/2大,则摩擦小,能减少拉伸力,但间隙大,精度不易控制;拉伸模凸、凹模单边间隙Z/2小,则摩擦大,增加拉伸力。
单边间隙Z/2可按以下公式计算:
Z/2=tmax+Kt
式中tmax--最大料厚,取0.285+0.005mm
t--公称料厚,取0.285mm
K--系数,当t<0.4mm时,取0.08
则Z/2=0.290+0.08×0.285=0.313mm。
变薄拉伸模易拉罐罐体成形实际上是将再拉伸和3道变薄拉伸组合在一起的组合工序。
现将变薄拉伸模的设计介绍如下:
(1)模具材料。
凸模:
基体材料为合金工具钢,凸模材料为M2,热处理硬度60~62HRC,镀TiN。
凹模(变薄拉伸环):
基体材料为合金工具钢,模口材料为硬质合金(牌号为VALENITEVCID-H.L.D或KE-84KENNAMETAL)。
(2)变形量。
变薄拉伸比方的计算公式为:
δ=(tn-tn-1)/tn×100%,其中tn、tn-1分别为n次及n-1次变薄拉伸后的零件侧面壁厚,计算得:
δ1=(0.285-0.225)/0.285×100%=21.05%;δ2=(0.225-0.170)/0.225×100%=24.44%;δ3=(0.170-0.106)/0.170×100%=37.65%。
制罐工厂常常根据给定的材料厚度、罐体厚、薄壁要求、拉伸环和凸模尺寸、拉伸机精度等条件,编制拉伸环和凸模的匹配表供技术人员、模具维修人员和操作人员选配凸模和拉环。
(3)模具的工作部分参数。
凸模:
凸模圆弧R1.016±0.025mm,再拉伸凸模圆弧R2.286mm,罐底沟外侧壁圆弧R10.478±0.013mm。
变薄拉伸环:
凹模锥角α=5°,工作带宽度h=0.38+0.25mm。
罐底成形模
罐底凸模材料选用合金工具钢Crl2MoV,热处理硬度60~64HRC,其轮廓形状应与罐型设计一致。
底压边模材料选用合金工具钢Cr5MoV,热处理硬度58~60HRC,其轮廓形状应与凸模相匹配。
(1)拉伸工序考虑的重要因素有:
拉伸比、凸、凹模圆弧半径、凸、凹模间隙、铝材机械性能、润滑、作业参数。
(2)变薄拉伸工序中凹模锥角。
的大小关系到变形区金属的流动性质、应力大小以及模具的受力情况,合理的取值范围为α=5°-8°。
(3)合适的罐型设计是轻量化技术能否实施的关键。
研究表明,对于CCB-1A型罐,设计参数选择:
底沟外壁夹角α1=32°,罐底沟内壁夹角α2=5°,凸模圆弧R=1.016mm,球面和罐底沟内壁圆弧R1=1.524mm,罐底球面半径R球=45.72mm,可以大大增加罐体强度。
1.89101372.5真空易拉罐
2.92103613.2生产金属盖易拉罐塑料罐体的方法和设备
3.92111362.5金属盖易拉罐塑料罐体及成型方法
4.92113239.5装有吸管的易拉罐
5.93110688.5纯铝易拉罐及其挤压成型工艺与专用模具
6.94103679.0防污染易拉罐及其制做方法和加工装置
7.94111071.0一种纯铝易拉罐拉伸工艺及专用设备
8.95100798.X防污染易拉罐及其制作方法和加工装置
9.96199682.X保留撕开拉片的易拉罐端盖
10.97102424.3易拉罐盖
11.97103865.1纸的压铸工艺及由此制得的纸易拉罐
12.97109528.0易拉罐
13.98122862.3顶盖容易清洁的易拉罐
14.99113365.X用PET聚酯生产易拉罐的方法
15.99117742.8平衡全营养素饮料与一分二易拉罐
16.00126595.4卫生易拉罐
17.03115293.7全塑带吸管的易拉罐
18.200410019744.4卫生型易拉罐
19.200410075069.7纸浆模塑制造纸质易拉罐工艺
20.200510009715.4纸浆模塑易拉罐罐体的制作方法
21.200510010537.7能够实现大量生产的内含饮液吸管的易拉罐
22.200510025116.1对单个易拉罐的顶盖及罐身的包装
23.200510035069.9发热易拉罐
24.200510061688.5一种带饮嘴的易拉罐
25.200510071586.1带吸管的易拉罐
26.200510135383.4易拉罐饮口部位防菌方法及易拉罐防菌衣
27.200580018595.2易拉罐卫生盖
28.200610025408.X对单个易拉罐的顶盖及罐身的包装
29.200610155110.0用于便携易拉罐的提带
30.200710031046.X一种制作塑料易拉罐罐体的工艺方法
31.200710190567.X内置导流件的易拉罐
32.200710200330.5纸塑复合材料易拉罐的制造方法及制造设备
一、项目概况铝制易拉罐等包装容器生产项目总投资7500万美元,折人民币50000万元,新建16000平方米生产车间、24350平方米办公楼、380平方米食堂、9000平方米仓库及配套建筑物等共计52460平方米,配套建设水、电、气等公用设施,新购买易拉罐成套生产线、彩印机和空压机等生产设备33台(套),项目建设完成后,易拉罐生产能力达到2000罐/分钟,年产铝质易拉罐8亿只。
二、项目主要生产工艺、主要污染物排放及环保措施
(一)生产工艺流程开卷、冲杯→拉伸→切割、修边→清洗→烘干→外表面印刷、烘干→内喷涂→缩颈、翻边→光检→码垛、包装
(二)污染物排放、环保措施和环境影响1、废气
(1)酸雾清洗工序添加含有硫酸及氢氟酸的清洗剂。
微量氟化氢、硫酸雾废气经16.5m高的排气筒排放。
(2)燃气炉尾气清洗、印刷、喷涂烘干热源由燃气炉提供。
天然气燃烧废气污染物年排放量分别为烟尘、SO2、NOx,通过16.5m高排气筒排放。
(3)非甲烷总烃印刷烘干、内喷涂烘干产生的微量非甲烷总烃通过16.5m高排气筒排放。
(4)内喷涂废气项目内喷涂工序有少量废气以无组织形式排放。
(5)油烟废气项目配套建有中型食堂,食堂油烟经净化效率达90%的设施处理后。
上述废气污染物排放量较少,不会对周边区域环境空气产生明显影响。
项目无需设置大气环境防护距离。
2、废水项目排放的废水有清洗工艺废水、反冲洗废水以及生活污水。
清洗工艺废水、反冲洗废水经项目自设的污水处理站,出水水质能够满足CJ343-2010《污水排入城镇下水道水质标准》中表1的B级标准。
生活污水与处理达标后的生产废水一起经市政污水管网进入上马污水处理厂处理。
3、噪声项目主要噪声源为生产线设备、空压机、泵等,噪声源强在65~95dB(A)之间。
项目选用低噪声设备,经车间隔声和距离衰减后,厂界噪声可满足GB12348-2008《工业企业厂界环境噪声排放标准》3类标准要