阿莫西林生产工艺规程.docx
《阿莫西林生产工艺规程.docx》由会员分享,可在线阅读,更多相关《阿莫西林生产工艺规程.docx(29页珍藏版)》请在冰豆网上搜索。
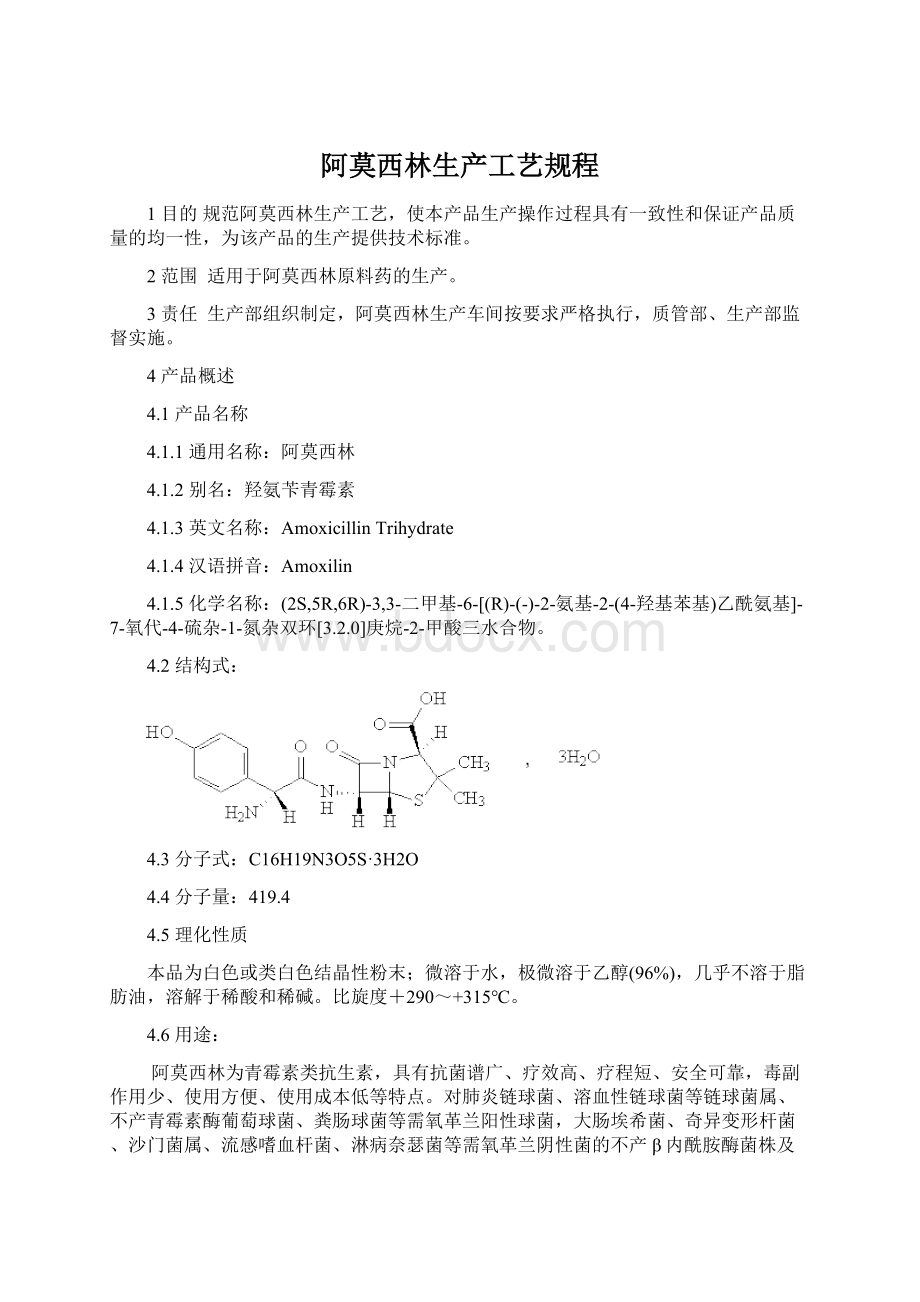
阿莫西林生产工艺规程
1目的规范阿莫西林生产工艺,使本产品生产操作过程具有一致性和保证产品质量的均一性,为该产品的生产提供技术标准。
2范围适用于阿莫西林原料药的生产。
3责任生产部组织制定,阿莫西林生产车间按要求严格执行,质管部、生产部监督实施。
4产品概述
4.1产品名称
4.1.1通用名称:
阿莫西林
4.1.2别名:
羟氨苄青霉素
4.1.3英文名称:
AmoxicillinTrihydrate
4.1.4汉语拼音:
Amoxilin
4.1.5化学名称:
(2S,5R,6R)-3,3-二甲基-6-[(R)-(-)-2-氨基-2-(4-羟基苯基)乙酰氨基]-7-氧代-4-硫杂-1-氮杂双环[3.2.0]庚烷-2-甲酸三水合物。
4.2结构式:
4.3分子式:
C16H19N3O5S·3H2O
4.4分子量:
419.4
4.5理化性质
本品为白色或类白色结晶性粉末;微溶于水,极微溶于乙醇(96%),几乎不溶于脂肪油,溶解于稀酸和稀碱。
比旋度+290~+315℃。
4.6用途:
阿莫西林为青霉素类抗生素,具有抗菌谱广、疗效高、疗程短、安全可靠,毒副作用少、使用方便、使用成本低等特点。
对肺炎链球菌、溶血性链球菌等链球菌属、不产青霉素酶葡萄球菌、粪肠球菌等需氧革兰阳性球菌,大肠埃希菌、奇异变形杆菌、沙门菌属、流感嗜血杆菌、淋病奈瑟菌等需氧革兰阴性菌的不产β内酰胺酶菌株及幽门螺杆菌具有良好的抗菌活性。
阿莫西林通过抑制细菌细胞壁合成而发挥杀菌作用,可使细菌迅速成为球状体而溶解、破裂。
4.7产品编号:
C02
4.8包装规格:
25Kg/桶。
4.9批量:
900-1120kg
4.10贮藏:
密封保存。
4.11有效期:
暂定2年
5化学反应式及生产工艺流程图
5.1化学反应式:
+
+CH3OH
5.2生产工艺流程图
氨水、工艺用饮用水
D-对羟基苯甘氨酸甲酯盐酸盐溶液、青霉素G酰基转移酶、氨水
盐酸、EDTA-2Na
氨水
纯化水、丙酮
物料
工序
检验项目
控制参数注:
带*的为中间体质量标准,其他的为中间控制质量标准,带★号的为关键工序。
D级区
6生产过程、工艺条件、注意事项及常见偏差
6.1生产前准备
岗位操作人员进入生产现场按岗位操作程序进行生产前检查,并检查洁净区温湿度是否符合工艺条件,同时做好记录。
如不符合要求,按相关SOP重新处理并经车间质管员或授权人员确认后才可进行下一步操作。
6.2原辅料领取、发放、验收
6.2.1车间领料员依据生产需求从仓库领取原辅料。
检查品名、批号、规格、外包装有无异常,无异常后才可领用。
6.2.2注意事项
6.2.2.1物料应经检验合格并由质量管理部门批准放行后,方可使用,原辅料生产商变更后应通过小样试验,必要时需通过验证。
6.2.2.2物料应做到帐、卡、物一致。
6.2.2.3传递物料过程中,传递窗两侧严禁对开。
6.2.3常见偏差及处理办法
在检查原辅料的过程中如发现原辅料的外观形状、数量异常,应立即将异常的原辅料单独定置存放,并挂上“待处理”标示牌,明确物料状态。
并及时报告车间质管员,由车间质管员按偏差处理程序进行处理。
6.36-APA溶解工序
6.3.1工艺原理
6-APA在碱性条件下可以全部溶解在水相中。
6.3.23M氨水的配制
名称
体积比
氨水:
工艺用饮用水
1:
3
6.3.3备料
名称
投料量
6-APA
300kg或350kg
工艺用饮用水
2200L或2600L
6.3.4操作过程
在不锈钢溶解罐加入工艺用饮用水2200L或2600L,加入300kg或350kg6-APA。
开启搅拌,于12.0-22.0℃下,加入3M氨水至pH为7.00-8.00并保持,至6-APA全部溶解至澄清,停止搅拌,关闭所有阀门,将6-APA溶解液交缩合工序,最后加200-300L工艺用饮用水冲洗溶解罐,并将洗罐水交缩合工序。
6.3.5工艺控制点
工艺参数项目
参数值
温度
12.0-22.0℃
pH
7.00-8.00
6.3.6中间控制质量标准
名称
编号
项目
标准
6-APA溶解液
Z0203
外观
澄清液体
6.3.7注意事项
6.3.7.1投料前,应再次核对所投物料的品名、批号、数量。
6.3.7.26-APA包装袋统一集中收集进行灭活操作。
6.3.8常见偏差及处理
6.3.8.1搅拌出现异常或晃动应立即停止搅拌,检查螺丝是否有松动。
6.3.8.2溶解过程中温度、pH偏离指标要求,检测温度计和pH计显示是否准确,应调整使符合要求,并及时上报,由车间质管员会同相关人员查明原因后按偏差处理程序处理。
6.3.8.3物料投料量在±10%波动范围内不视为偏差。
6.4缩合工序
6.4.1工艺原理
在青霉素G酰基转移酶的作用下,6-APA和D-对羟基苯甘氨酸甲酯盐酸盐在酸性条件下,在水中合成阿莫西林。
6.4.2备料
名称
投料量
青霉素G酰基转移酶
800kg
D-对羟基苯甘氨酸甲酯盐酸盐溶液
1000L(约含D-对羟基苯甘氨酸甲酯盐酸盐450Kg)
1200L(约含D-对羟基苯甘氨酸甲酯盐酸盐525Kg)
6.4.3操作过程
将6-APA和D-对羟基苯甘氨酸甲酯盐酸盐的溶解液打入缩合罐,加入3M氨水,控制反应液pH值5.80-6.50,于15.0-25.0℃下反应2-8h(反应终点控制:
6-APA残留≤5mg/ml)。
然后将阿莫西林缩合液放入抽滤罐中,最后用200-300L工艺用饮用水冲洗,将冲洗水一并放入抽滤罐中。
6.4.4酶使用操作过程
青霉素G酰基转移酶在生产过程中重复使用,由于机械搅拌的外力原因造成破碎而损失,外界环境的影响造成活力降低,导致反应时间延长。
为了保证阿莫西林的质量和收率,需在每使用20批进行酶活的检测。
当酶活<40u/g或每批反应时间超过8h时更换新酶。
6.4.5关键工艺控制点
工艺参数项目
参数值
反应温度
15.0-25.0℃
反应时间
2-8h
pH
5.80-6.50
6.4.6中间控制质量标准
名称
编号
项目
标准
阿莫西林缩合液
Z0204
外观
白色或类白色混悬液
6-APA残留
≤5mg/ml
使用过程青霉素G酰基转移酶
Z0210
活力
≥40u/g
6.4.8注意事项
6.4.8.1缩合反应、待料过程中,注意青霉素G酰基转移酶的保存。
6.4.8.2软管使用完毕后,需清洁沥干存放。
6.4.8.3当酶活<40u/g或每批反应时间超过8h时更换新酶。
6.4.9常见偏差及处理
6.4.9.1搅拌出现异常或晃动应立即停止搅拌,检查螺丝是否有松动
6.4.9.2反应过程中温度、pH偏离指标要求,检测温度计和pH计显示是否准确,应调整使符合要求,并及时上报,由车间质管员会同相关人员查明原因后按偏差处理程序。
处理。
6.4.9.3如中间产品质量偏离指标要求,应立即报告车间质管员,由车间质管员会同相关人员查明原因后按偏差处理程序进行处理。
6.4.9.4物料投料量在±10%波动范围内不视为偏差。
6.5过滤工序
6.5.1备料
名称
投料量
纯化水
5000L或5800L
6.5.2操作过程
将反应好的缩合液放至抽滤罐中,控制真空度≤-0.06Mpa,抽滤至液位下降至抽滤罐锥体界线时,向抽滤罐中加纯化水5000L或5800L。
6.5.3工艺控制点
工艺参数项目
参数值
真空度
≤-0.06Mpa
6.5.4注意事项
操作人员在设备运行过程中应关注真空度的情况,如发现异常及时通知车间负责人,由车间质管员会同设备员及岗位人员排除异常情况后,方可继续生产。
6.5.5常见偏差及处理
6.5.5.1抽滤罐在使用过程中如果出现抽料速度变慢,首先检查真空度是否降低,如果真空度降低检查是否真空泵没有水或水温过高,若是,加水或降低水温;若不是,应及时报告车间负责人,车间负责人通知设备员进行检修,检查真空泵是否发生腐蚀或气蚀等。
检修过程中应挂“正在检修”标识牌,明确机器状态。
检修完毕,由车间质管员会同相关人员进行分析、评估,确认对产品质量无影响,方可继续生产。
6.5.5.2物料投料量在±10%波动范围内不视为偏差。
6.6粗品溶解工序
6.6.1工艺原理
阿莫西林在酸性条件下能够完全溶解在水相中。
6.6.2盐酸(1:
1)的配制
名称
体积比
盐酸:
纯化水
1:
1
6.6.3操作过程
将抽滤罐中的料液约6500L或7300L放至搪瓷溶解罐内。
于16.0-22.0℃温度下加盐酸(1:
1)调节pH0.80-1.50。
调毕,加入EDTA-2Na3.0-4.0Kg,保持pH0.80-1.50,搅拌反应5-10分钟,至阿莫西林完全溶解。
将阿莫西林溶解液交结晶岗位,最后加200-300L纯化水冲洗阿莫西林溶解罐,将洗罐水一并交结晶岗位。
6.6.4工艺控制点
工艺参数项目
参数值
温度
16.0-22.0℃
pH
0.80-1.50
6.6.5中间控制质量标准
名称
编号
项目
标准
阿莫西林溶解液
Z0206
外观
澄清液体
6.6.6注意事项
物料使用前,应再次核对所投物料的品名、批号、数量。
6.6.7常见偏差及处理
6.6.7.1搅拌出现异常或晃动应立即停止搅拌,检查螺丝是否有松动
6.6.7.2反应过程中温度、pH偏离指标要求,检测温度计和pH计显示是否准确,应调整使符合要求,并及时上报,由车间质管员会同相关人员查明原因后按偏差处理程序处理。
6.7结晶工序
6.7.1工艺原理
阿莫西林在水相中采用等电点结晶的方法从水中析出晶体。
在等电点时,阿莫西林在水中的溶解度最小,并且阿莫西林在水中随温度的升高溶解度升高。
6.7.26M氨水的配制
名称
体积比
氨水:
纯化水
1:
1
6.7.3操作过程
与溶解岗位进行溶解液的交接,记录溶解液的体积,打开搅拌,缓慢加入6M氨水调pH值5.00-6.20,同时把结晶液降温至1.0-3.0℃,养晶1.0-1.5小时。
将结晶液交过滤洗涤岗位,最后加200-300L纯化水冲洗结晶罐,将洗罐水一并交过滤洗涤岗位。
6.7.4关键工艺控制点
工艺参数项目
参数值
养晶温度
1.0-3.0℃
养晶时间
1.0-1.5h
pH
5.00-6.20
6.7.5注意事项
6.7.5.1按要求检查洁净区温湿度、压差是否符合工艺条件。
6.7.5.2检查冷盐水压力、温度、流量是否符合生产要求。
6.7.6常见偏差及处理
6.7.6.1搅拌出现异常或晃动应立即停止搅拌,检查螺丝是否有松动
6.7.6.2反应过程中温度、pH偏离指标要求,检测温度计和pH计显示是否准确,应调整使符合要求,并及时上报,由车间质管员会同相关人员查明原因后按偏差处理程序处理。
6.8过滤洗涤工序
6.8.1工艺原理
阿莫西林经过过滤,纯化水、丙酮洗涤后,利于提纯和干燥。
6.8.2操作过程
打开通往离心机轴心的氮气阀门让少量氮气不断通入,加料前核对结晶罐和体积,将料液分别均匀加入离心机中。
启动离心机,离心机加料时接收母液,在加料期间使流量匀速。
当加料完成后,先关结晶罐底阀,再关离心机进料阀。
调节离心机的速度为洗涤速度13-18分钟。
开始洗滤饼,洗涤前核对纯化水计量罐(纯化水温度控制在0-10℃)的液位,用150±10L/次·台,连续洗涤两次;然后核对丙酮计量罐液位,用150±10L/次·台丙酮洗涤,连续洗涤两次。
洗涤结束后,调节离心机速度为甩干速度甩干20-30分钟。
甩干结束后减速到卸料速度。
同时完全打开氮气阀,通氮气3-6分钟,后关闭氮气阀门,卸料,将每台刮刀离心机的滤饼经过摇摆式颗粒机粉碎后,连同卸下的物料一起取样检验阿莫西林湿粉外观、水分,并将湿粉交干燥岗位。
6.8.3工艺控制点
工艺参数项目
参数值
甩干时间
20-30分
6.8.4注意事项
6.8.4.1按要求检查洁净区温湿度、压差是否符合工艺条件。
6.8.4.2产尘量大的房间呈相对负压。
6.8.4.3生产过程中产生的污粉统一收集进行灭活操作。
6.8.4.4为了防止微生物滋生,每罐贮存期限不得超过24小时,每月对纯化水计量罐进行一次巴氏消毒。
6.8.5常见偏差及处理
6.8.5.1洗涤过程中若离心机出现声音异常,如噪音变大,应该检查产生噪音的地方,检查螺丝是否松动。
6.8.5.2离心机震动异常,检查进料是否均匀及滤布是否损坏。
6.8.5.3洗涤用纯化水若温度降不下来,应立即检查冷盐水进回阀门是否开启,若冷盐水温度及流量均正常,应及时上报车间负责人,由车间相关人员进行调查并处理。
6.8.5.4洗涤用纯化水、丙酮使用量偏离指标要求,应及时上报车间负责人,由车间质管员会同相关人员查明原因后按偏差处理程序处理。
6.9干燥工序
6.9.1工艺原理:
真空空抽,使阿莫西林的水分合格。
6.9.2操作过程
将阿莫西林湿粉加入双锥干燥机中,开启双锥转动按钮,打开双锥真空阀,真空度≤-0.07Mpa,不通热水的情况下,转动0.5-1h,然后通热水,继续转动,使热水温度保持50-65℃下真空干燥4±0.5小时,取样,检验,水分合格(水分控制:
12.0~14.0%),取样,检验,水分合格后出料,得到阿莫西林轻粉。
与真空输送器连接好,准备吸粉。
6.9.3关键工艺控制点
工艺参数项目
参数值
真空度
≤-0.07Mpa
干燥温度
50-65℃
干燥时间
4±0.5小时
6.9.4注意事项
6.9.4.1按要求检查洁净区温湿度、压差是否符合工艺条件。
6.9.4.2产尘量大的房间呈相对负压。
6.9.4.3生产过程中产生的污粉统一收集进行灭活操作。
6.9.5常见偏差及处理
6.9.5.1干燥过程中如双锥出现异常声音或震动,应立即停止转动双锥,检查螺丝是否松动及传动轴是否损坏。
6.9.5.2干燥过程中若真空度达不到要求,如果真空度降低检查是否真空泵没有水或水温过高,若是,加水或降低水温;若不是,应及时报告车间负责人,车间负责人通知设备员进行检修,检查真空泵是否发生腐蚀或气蚀等。
检修过程中应挂“正在检修”标识牌,明确机器状态。
检修完毕,由车间质管员会同相关人员进行分析、评估,确认对产品质量无影响,方可继续生产。
6.9.5.3干燥过程中若热水温度达不到要求,应立即检查热水罐温度是否偏低。
6.9.5.4如收率、中间产品质量偏离指标要求,应立即报告车间质管员,由车间质管员会同相关人员查明原因后按偏差处理程序处理。
6.10造粒工序
6.10.1工艺操作过程
用物料管路将双锥与物料储罐连接,将阿莫西林轻粉转入物料储罐待用。
阿莫西林轻粉经真空上料系统转入压实机储料仓中,压实机料仓中物料到2/3以上时,启动压实机(压实机压辊油压10±5Mpa,压辊电机转速≥500转/分,送料电机转速≥300转/分)和颗粒机的电源开始造粒,同时打开振荡筛。
物料经压片后,成片的物料经颗粒机粉碎成颗粒,真空上料系统将颗粒抽入振荡筛整粒,粒度不够的物料经真空上料系统返回压实机再次重压,合格的颗粒经真空上料系统送入双锥混合器混合5-10分钟,混合结束后,取样检测重粉的松密度、叩实密度合格后进行分装。
6.10.2工艺控制点
工艺参数项目
参数值
压辊油压
10±5Mpa
压辊电机转速
≥500转/分
送料电机转速
≥300转/分
混合时间
5-10分钟
6.10.3中间控制质量标准
名称
编号
项目
标准
混合颗粒
Z0209
松密度
0.45g/ml-0.70g/ml
叩实密度
≥0.65g/ml
6.10.4注意事项
6.10.4.1按要求检查洁净区温湿度、压差是否符合工艺条件。
6.10.4.2产尘量大的房间呈相对负压。
6.10.4.3生产过程中产生的污粉统一收集进行灭活操作。
6.10.5常见偏差及处理
6.10.5.1造粒过程中如造粒机出现异常声音或震动,应立即停止造粒,检查螺丝是否有松动及压辊轴是否损坏。
6.10.5.2造粒过程中如果造粒速度变慢,检查真空度是否偏低及物料供应是否不足。
6.10.5.3如收率偏离指标要求,应立即报告车间质管员,由车间质管员会同相关人员查明原因后按偏差处理程序处理。
6.11包装工序
6.11.1操作过程
连接真空输送器进料口与双锥出料口,启动真空输送器,输送器内部形成负压状态。
双锥中的物料在负压气流的作用下,输送到输送器料仓中。
吸料循环结束,落料阀打开,物料落入储料仓。
如此往复循环,直到物料到达指定料位。
物料由储料桶落至计量桶中,计量出粉子重量。
称量时每袋的净重为25Kg,允许偏差±0.05Kg。
通知QC取样后立即开始封口,将内层的无色PE袋里的空气排尽,从下向上,将PE袋按顺时针方向拧成麻花状,用扎带将口袋扎紧,然后将外层的黑色PE袋里的空气排尽,从下向上,将PE袋按顺时针方向拧成麻花状,用扎带将口袋扎紧。
将扎好袋的成品传递到外包间。
装入纸板桶内,封口,入库待验。
6.11.2注意事项
6.11.2.1领取包装材料时,应检查品名、规格、批号、外观,确认符合标准。
6.11.2.2称量时必须双人复核,计量准确。
6.11.2.3注意扎带的数量,不要误入粉中。
6.11.2.4认真核对打印批号是否正确。
6.11.2.5标签应由专人保管、发放。
6.11.3常见偏差及处理
6.11.3.1出现不符合要求的包材,应立即更换,并及时报告车间质管员,由车间质管员按偏差处理程序进行处理,
6.11.3.2如出现标签损坏,应按照车间标签管理规程进行处理。
6.12工艺条件
6.12.1生产车间为青霉素药物专用车间,设备、容器具均为青霉素类药专用。
6.12.2结晶、洗涤、干燥生产过程在洁净级别为D级的区域下进行。
6.12.3具有符合工艺的设备和度量、衡器具,设备、管线、工具布局合理,以防止产品污染,便于清洗维修。
6.12.4控制一定的温湿度:
温度18~26℃,湿度45~65%
6.12.5生产所需空压要求0.6~0.8MPa,真空度要求(-0.08~-0.02)MPa。
压差要求:
不同洁净级别压差﹥10Pa,洁净区内产尘量大的房间应呈相对负压。
6.12.6具有专业技术人员和操作工和设备维修工,生产人员均需技术培训后培训合格后方可上岗操作,主要岗位技术人员应保持相对稳定。
6.12.7所有岗位生产前均应做岗位清洁及清场检查,并有上一批已清洁清场合格证。
6.12.8生产用物料,需经检验合格才能使用,生产用水为工艺用饮用水和纯化水。
6.12.9具有符合要求的防污染设施和劳动保护器具。
6.13注意事项
6.13.1在生产操作过程中工艺或设备的控制参数有偏差,应报告车间质管员,对偏差进行分析、评估或者通过检测,认为偏差不影响该工序的产品质量,可进入下工序生产,在记录中注明发生的偏差及处理方法。
6.13.2生产过程中产生的废粉和废料由各岗位统一收集后按青霉素产品污粉灭活操作程序进行处理。
6.13.3生产过程中接触青霉素类废弃物由各岗位统一收集后按接触青霉素类废弃物灭活操作程序进行处理。
6.14偏差及处理
6.14.1生产过程中公共系统(如电、压缩空气、纯化水、蒸汽等)出现故障各岗位应立即停止生产,并将发生故障时生产的产品挂“待验”标示牌,明确产品状态,需要检验的产品由车间送检,车间质管员会同相关人员进行评估,确认有无质量问题,待公共系统恢复正常后,方可继续开机生产。
6.14.2生产过程中如机器发生故障,操作人员应立即报告车间负责人、车间质管员、设备员,并将发生故障时生产的产品挂“待验”标识牌,明确产品状态,需要检验的产品由车间送检,车间质管员会同相关人员进行评估,确认有无质量问题。
待机器恢复正常后,方或继续生产。
7工艺卫生
参考物品进入洁净区清洁程序及车间各岗位清场清洁规程。
8技术安全及劳动保护
8.1技术安全
8.1.1所有员工接受安全知识和原料药生产特殊知识的培训,经考核合格后上岗。
8.1.2企业制定了各种安全管理制度。
8.1.3厂房设置技术夹层,所有管线暗装。
8.1.4生产车间内暴露的各种管道均有明显标识,并标明流向。
蒸汽管道、风管、热水及冷盐水等管道均做保温处理。
8.1.5车间设有紧急出口标志,洁净区设有安全门。
8.2安全防火与防爆
8.2.1车间设有专职安全员,负责本车间的安全工作。
8.2.2非生产人员未经许可不得进入车间和仓库。
8.2.3车间内设有防火门、烟雾探头以及灭火栓等防火装置,重点防火区所用开关、灯、电机等均为防爆产品。
8.2.4车间用火必须由安全部下发动火证。
8.2.5车间和仓库周围一律不准堆放易燃易爆危险品,严禁吸烟或携带火具进入车间和库区,在重点防火区域严禁携带手机或手机处于关机状态。
8.2.6溶媒库设有静电触摸装置,出入人员触摸消除静电。
8.2.7经常检查电器线路及仓库物资发现问题及时解决
8.2.8车间和仓库配备的专用消防工具,应定期检查完好情况,要妥善保管,及时更换灭火器。
8.3劳动保护
8.3.1产尘大的岗位安置排风或局部除尘设施。
8.3.2员工定期体检,对不适应本岗工作的员工及时调整。
8.3.3有关车间配备通风及空调设备,以改善操作人员的劳动条件。
8.3.4一般区域生产操作人员上岗时穿戴规定的工作服,安全帽,工作鞋防护眼镜。
噪音大的区域需佩戴耳塞。
8.3.5洁净区的操作人员工作时穿戴洁净服。
9主要设备一览表
序号
设备编号
设备名称
性能参数/
规格型号
材质
容积(m3)
数量(台)
1
R17205A-C
溶解罐
V-DN2600×4725
ocr18Ni9
20
3
2
R17102A-F
缩合罐
DN2600
SS
15
6
3
R17103A-H
缩合罐
DN2600
SS
15
8
4
R17120A-F
缩合罐
DN2600
SS
15
6
5
V17125A-R
抽滤罐
V=9001L
0cr18Ni9
10
18
6
R17206A-C
溶解罐
DN3183*4760
搪瓷
20
3
7
R17201A-L
结晶罐
V6119DN2600×4325
SS
20
12
8
X17301A(1