推动架说明书.docx
《推动架说明书.docx》由会员分享,可在线阅读,更多相关《推动架说明书.docx(55页珍藏版)》请在冰豆网上搜索。
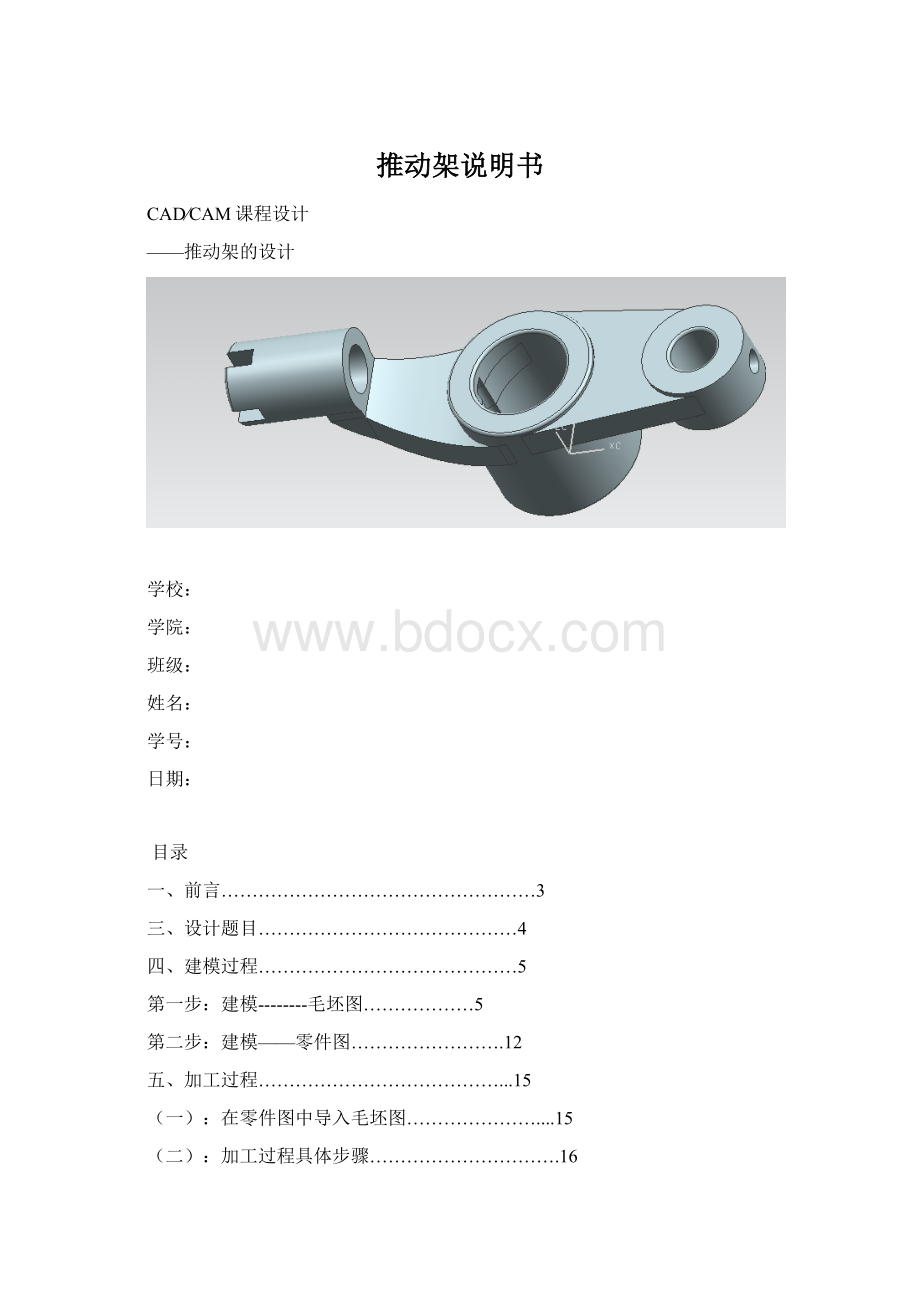
推动架说明书
CAD∕CAM课程设计
——推动架的设计
学校:
学院:
班级:
姓名:
学号:
日期:
目录
一、前言……………………………………………3
三、设计题目……………………………………4
四、建模过程……………………………………5
第一步:
建模--------毛坯图………………5
第二步:
建模——零件图…………………….12
五、加工过程…………………………………...15
(一):
在零件图中导入毛坯图…………………....15
(二):
加工过程具体步骤………………………….16
第一节:
直径为50的圆上表面和直径为32孔的加工….16
第二节、直径为35的圆上表面和直径为16孔的加工….37
第三节、在直径为27的圆中直径为16孔的加工………40
第四节、直径为27的圆中直径为10孔的加工…………42
第五节、直径为50的圆下表面……………………….44
第六节、直径为35的圆下表面………………………...46
第七节、直径为8的孔……………………………………..47
第八节、直径为6的孔……………………………………..49
六、生成车间工艺文档…………………….51
七、生成数控加工程序…………………….52
八、心得与体会……………………………….52
九、参考文献…………………………………...53
一、前言
本次的课程设计是开放性的设计。
首先创建或设计具有曲面的三维零件,然后,利用现代的CAD/CAM技术进行零件三维实体建模,分析此零件的加工工艺,并用CAD/CAM技术模拟仿真零件的加工过程。
同时进一步学习前沿的机械CAD/CAM技术,感受现代CAD/CAM技术的先进性,提高对CAD/CAM技术的综合运用能力和现场动手操作能力,是一次理论联系实际,理论转化成实际的质的飞跃.
通过本次设计,系统地了解和掌握CAD/CAM技术的基本内容和基本知识,了解数控技术的发展趋势;并能灵活使用目前使用比较普遍的CAD/CAM软件对较复杂零件进行编程,为以后的工作打下坚实的基础。
同时培养创新意识、工程意识和动手能力。
三、设计题目
四、建模过程
第一步:
建模——零件图
(一),进入UG建模模式建立如下模型:
图1
(二):
零件图的具体建模过程如下:
2.1、进入草图——绘制直径为32的圆——退出草图——拉伸该曲线——拉伸距离为45并进行与直径为50的圆求差如图2-1所示——点击确定即可得出如图2-2所示的图形。
图2-1图2-2
2.2、进入草图绘制区域——绘出直径为16的圆——退出草图——拉伸该曲线——拉伸的曲线与直径为35的圆进行求差且拉伸距离为20如图2-3所示——点击确定即可得出图2-4图形。
图2-3图2-4
2.3、进入草图绘制区域——绘出直径为16的圆——退出草图——拉伸该曲线——拉伸的曲线与直径为27的圆进行求差且拉伸距离为26如图2-5所示——点击确定即可得出图2-6图形。
图2-5图2-6
2.4、进入草图绘制区域——绘出直径为10的圆——退出草图——拉伸该曲线如图2-7所示——拉伸的曲线与直径为27的圆进行求差且拉伸距离为6----点击确定
图2-7图2-8
2.5、创建基准平面——进入草图绘制区域——绘出直径为8的圆——退出草图——拉伸该曲线——拉伸的曲线与直径为35的圆进行求差且拉伸距离为20如图2-9所示——点击确定即可得出图2-10图形。
图2-9图2-10
2.6、创建基准平面——进入草图绘制区域——绘出直径为6的圆——退出草图——拉伸该曲线——拉伸距离为25并且再与直径为50的圆求差——点击确定;然后在对曲线进行倒斜角如图2-11所示——倒斜角的距离为2——点击确定即可得出图2-12图形。
图2-11图2-12
图2-13图2-14
2.7、对图形中所需边倒圆的部分进行边倒圆:
单击边倒圆图标显示如图2-13所示——选择边(把所需边倒圆的部分全选)——对图形边1个的倒圆——完成之后如图2-14所示
2.8、进入草图——绘制出直径为6的圆——然后在编辑图形绘出所需图形如图2-22图中的小半圆曲线——然后对其拉伸且拉伸距离为45还要和直径为50的圆进行求差——完成后还要对其曲线在两端进行拉伸,这时一端拉伸距离为4——完成后点击确定——再对其这段圆弧曲线的里面那段曲线进行边倒圆且边1个的倒圆
2.9、求和:
对直径为50的圆和2.8节里绘制的两段圆弧图形进行求和——求和结果如图2-15所示
图2-15
2.10、通过以上步骤的操作完成就可得出所需要的零件图,最后绘制出来的图形如图1所示。
第二步:
建模--------毛坯图
(一),进入UG建模模式建立如下模型:
图2
(二):
毛坯图的具体建模过程如下:
1.1、进入草图页面——绘制直径为50的圆——完成草图——拉伸直径为50的圆、拉伸距离为45——点击确定
1.2、进入草图——绘制直径为35的圆——完成草图——拉伸直径为35的圆、拉伸距离为20——点击确定
1.3、创建基准平面——进入草图——绘制的图形——完成草图——拉伸曲线,拉伸距离为10——点击确定就会出现
1.4、创建基准平面——进入草图——绘制直径为27的图形——完成草图——拉伸曲线,拉伸距离为41——确定就会出现所需的图形。
1.5、创建基准平面——进入草图——绘制图形——完成草图——拉伸曲线,拉伸距离为(-25—25)——点击确
1.6、创建基准平面——进入草图——绘制中的曲线——完成草图——对图形进行拉伸——拉伸的曲线与圆弧板进行求差运算如图1-1所示——求差后点击确定就会出现如图1-2所示的图形——这就得出了所需要的图形。
图1-1图1-2
1.7、进入草图——绘制一个直径为20的圆——拉伸这个草图——拉伸距离为45——与直径为50的圆进行求差——点击确定得出图形——即可得出所需图形。
1.8、进入草图——绘制一个直径为8的圆——拉伸这个草图——拉伸距离为20——与直径为35的圆进行求差——点击确定得出如图1-3所示的图形——即可得出所需图形。
图1-3
1.9、进入草图——绘制一个直径为8的圆——拉伸这个草图——拉伸距离为26——与直径为27的圆进行求差——点击确定得出如图1-4所示的图形——即可得出所需图形。
图1-4
1.10、在图1-19的基础上对图进行编辑:
选中直径为50的圆单击鼠标右键——选中编辑参数对直径为50的圆进行编辑——在此基础上对直径为50的圆再拉伸4个的毛坯量;选中直径为35的圆单击鼠标右键——选中编辑参数对直径为35的圆进行编辑——在此基础上对直径为35的圆再拉伸4个的毛坯量;选中平面肋板进行下移2个的距离。
这样就可得出零件的毛坯如图2所示。
五、加工过程
(一):
在零件图中导入毛坯图
图3
如图3-1、3-2、3-3所示
图3-1图3-2
图3-3
(二):
加工过程具体步骤
第一节:
直径为50的圆上表面和直径为32孔的加工
(1):
加工环境
1、进入加工模块单击“起始”图标,选择“加工”命令,进入加工模块,弹出“加工环境”对话框如图3-4所示
图3-4
2、选择加工环境在表框中选择模块文件“mill-planar”(平面铣)进入加工环境
(2):
创建父节点组
1、创建程序父节点组创建名称为YECHUN1的程序父节点组,
2、创建刀具父节点组
2.1、创建第一把刀具:
圆角刀,单击“加工创建”工具栏中的“创建刀具”,在“创建刀具”对话框中,选择类型为:
mill-planar;选择子类型“平底刀”;输入名称为T1D16R1;点击确定,刀具直径:
16;刀具下半经:
1;刀具号:
1,如图3-5所示,
图3-5
2.2、创建第二把刀具:
中心钻,单击“加工创建”工具栏中的“创建刀具”,在“创建刀具”对话框中,选择类型为:
drill;选择子类型“中心钻”;输入名称为T2D3;点击确定,如图3-6所示,在“钻刀”对话框中完成以下的参数。
刀具直径:
3
刀具号:
2
其它参数保持默认值;
设置完参数后,单击“确定”按钮,完成第二把刀具的创建。
图3-6
2.3、创建第三把刀具:
麻花钻,单击“加工创建”工具栏中的“创建刀具”,在“创建刀具”对话框中,选择类型为:
drill;选择子类型“麻花钻”;输入名称为T3D31.8;点击确定,在“钻刀”对话框中完成以下的参数。
刀具直径:
31.8
刀具号:
3
其它参数保持默认值;
设置完参数后,单击“确定”按钮,完成第三把刀具的创建。
2.4、创建第四把刀具:
铰刀,单击“加工创建”工具栏中的“创建刀具”,在“创建刀具”对话框中,选择类型为:
drill;选择子类型“铰刀”;输入名称为T4D32如图3-11所示;点击确定,在“钻刀”对话框中完成以下的参数。
刀具直径:
32
刀具号:
4
其它参数保持默认值;
设置完参数后,单击“确定”按钮,完成第四把刀
2.5、创建完刀具的机床视图见图3-7
图3-7
3、创建几何体父节点组
3.1、单击“操作导航器”工具栏中的“几何视图”图标,切换操作导航器至几何视图。
3.2、定义加工坐标系:
双击几何视图中的“MCS-MILL”节点,弹出“MILL-ORIENT”对话框,如图3-8所示,所选坐标系是在零件图的直径为50的圆的上表面。
图3-8图3-9
3.3、设置安全平面:
在安全设置选项中选择“平面”,指定平面会出现图3-9所示,在“平面构造器”的对话框中,所选平面是在零件图的直径为50的圆的上表面,“偏置”值为50。
完成后如图3-10所示。
图3-10图3-11
3.4、选择零件几何:
在几何视图中,单击“MCS-MILL”节点前的“+”号,在双击“WORKPIECE”节点,弹出一个对话框,在对话框中单击“零件几何”图标,弹出一个对话框如图3-11所示,在“工件几何体”对话框中,绘制零件图中直径为50的圆作为几何体,单击“确定”按钮,完成零件几何的选择。
3.5、定义毛坯几何:
在对话框中选择“毛坯几何”图标,单击“选择”按钮,弹出“毛坯几何”对话框,如图3-12所示,在该对话框中选择“几何体”单击按钮,所选的“几何体”为毛坯图。
单击“确定”按钮,即可回到对话框中,如图3-14所示,单击“确定”按钮。
图3-12图3-13
图3-14
4、设置加工方法父节点组
4.1、单击“操作导航器”工具栏中的“加工方法视图”图标,切换操作导航器至加工方法视图。
4.2、设置粗加工方法:
双击加工方法视图中的“MILL-ROUGH”节点,弹出“MILL-METHOD”对话框,在该对话框中设置如下粗加工参数:
部件余量:
0.2;
内公差:
0.03;
外公差:
0.03;
单击“确定”按钮,完成粗加工方法的设置,如图3-15所示。
图3-15图3-16
4.3、设置精加工方法:
双击加工方法视图中的“MILL-FINISH”节点,弹出“MILL-METHOD”对话框,在该对话框中设置如下精加工参数:
部件余量:
0;
内公差:
0.01;
外公差:
0.01;
单击“确定”按钮,完成精加工方法的设置,如图3-16所示。
(3)、创建平面加工操作
1、创建平面铣操作
1.1、单击“加工创建”工具栏中的“创建操作”图标,弹出“创建操作”对话框。
1.2、在弹出“创建操作”对话框中,选择类型为:
mill-pianar;选择子类型:
平面铣,设置如下各父节点组:
程序:
YECHUN
使用几何体:
WORKPIECE;
使用道具:
T1D16R1;
使用方法:
MILL-ROUGH;
输入名称为:
1。
1.3、单击“确定”按钮,弹出“PLANAR-MILL”对话框。
2、定义部件边界
2.1、在“PLANAR-MILL”对话框中选择“部件”图标,单击“选择”按钮,弹出“边界几何体”对话框
2.2、在“边界几何体”对话框中默认选择模式为“面”、材料侧为“内部”,此时,选择的面为零件图直径为50的圆上表面。
2.3、然后单击“确定”按钮,返回到“PLANAR-MILL”对话框。
2.4、单击“显示”按钮,在图形中显示出已定义的部件边界。
3、定义底平面
3.1、在“PLANAR-MILL”对话框中选择“底面”图标,单击“选择”按钮,弹出“平面构造器”对话框,如图3-16所示。
3.2、这时选择零件图直径为50的圆的底面,单击“确定”按钮。
图3-16
4、设置切削方式选择切削方式为:
跟随周边。
5、设置切削参数
5.1、单击“切削”按钮,弹出“切削参数”对话框。
5.2、选择“策略”选项卡,设置切削顺序:
层优先;切削方向为:
顺铣切削;进给方向为:
向外。
5.3、选择“毛坯”选项卡,设置最终底面余量为:
0.1;
6、设置切削深度
6.1、单击“切削深度”按钮,弹出“切削深度参数”对话框。
6.2、在“切削深度参数”对话框中,设置切削参数类型为:
用户定义;最大值:
2。
如图3-17所示。
图3-17
7、设置进给率
7.1、单击“进给率”按钮,弹出“进给和速度”对话框。
7.2、选择“速度”选项卡,设置主轴速度为:
1000rpm。
如图3-18所示。
7.3、选择“进给”选项卡,设置进刀速度:
150mmpm;设置剪切速度:
350mmpm;如图3-18所示。
8、所有参数设置完后就会出现图3-19和图3-20所示。
图3-20
9、生成刀具轨迹
单击“生成”图标如图3-20所示,单击“确定”按钮,就会出现3-21图形。
图3-18图3-19
图3-21
10、仿真刀具轨迹
单击“确认”图标,选择“2D动态”选项卡,如图3-22所示。
图3-22
(4)、创建定位孔加工操作
1、创建中心钻操作
1.1、单击“加工创建”工具栏中的“创建操作”图标,弹出“创建操作”对话框。
1.2、如图4-1所示,在弹出“创建操作”对话框中,选择类型为:
drill;选择子类型:
中心钻,设置如下各父节点组:
程序:
YECHUN;
使用几何体:
WORKPIECE;
使用道具:
T2D3;
使用方法:
DRILL-METHOD;
输入名称为:
2。
图4-1
2.1、选择“孔”图标,单击“选择”按钮。
2.2、单击“面上所有孔”按钮,选择的面为直径为50的圆的上表面。
2.3、单击“确定”按钮——“选择结束”按钮——单击“确定”按钮——单击“显示”按钮。
3、定义部件表面
3.1、单击“确定”按钮,弹出“部件表面”对话框,如图4-2所示。
3.2、在“部件表面”对话框中,选择类型:
面,这时的面是毛坯图的直径为50的圆上表面。
3.3、单击“确定”按钮——单击“显示”按钮。
图4-2图4-3
4、设置循环参数
4.1、默认循环类型为:
标准钻,单击“编辑参数”,如图4-3所示。
4.2、默认循环参数组:
1——单击“确定”按钮——在“Cycle深度”中单击“刀尖深度”——深度值:
3——单击“确定”按钮。
5、设置最小安全距离最小安全距离为:
5。
6、设置进给率
6.1、单击“进给率”按钮,弹出“进给和速度”对话框。
6.2、选择“速度”选项卡,设置主轴速度为:
1000rpm。
6.3、选择“进给”选项卡,设置剪切速度:
60mmpm;
7、生成刀具轨迹
单击“生成”图标,单击“确定”按钮,就会出现4-4图形。
图4-4
8、仿真刀具轨迹
单击“确认”图标,选择“2D动态”选项卡。
(5)、创建预钻孔加工操作
1、创建啄钻操作
1.1、单击“加工创建”工具栏中的“创建操作”图标,弹出“创建操作”对话框。
1.2、在弹出“创建操作”对话框中,选择类型为:
drill;选择子类型:
啄钻,设置如下各父节点组:
程序:
YECHUN;
使用几何体:
WORKPIECE;
使用道具:
T3D31.8;
使用方法:
DRILL-METHOD;
输入名称为:
3。
2、定义加工孔位置
2.1、选择“孔”图标,单击“选择”按钮,弹出如图4-2所示。
2.2、单击“面上所有孔”按钮,选择的面为直径为50的圆的上表面。
2.3、单击“确定”按钮——“选择结束”按钮——单击“确定”按钮——单击“显示”按钮。
3、定义部件表面
3.1、单击“确定”按钮,弹出“部件表面”对话框,如图4-3所示。
3.2、在“部件表面”对话框中,选择类型:
面,这时的面是毛坯图的直径为50的圆上表面。
3.3、单击“确定”按钮——单击“显示”按钮。
4、定义底面
4.1、选择“底面”图标,单击“选择”按钮,弹出“底面”对话框,这时选择的底面为为直径为50的圆的下表面。
4.2、单击“确定”按钮——单击“显示”按钮。
5、设置循环参数
5.1、默认循环类型为:
标准钻-深度,单击“编辑参数”
图4-5
5.2、默认循环参数组:
1——单击“确定”按钮——在“Cycle深度”中单击“穿过底面”——设置Step1:
5——单击“确定”按钮。
6、设置最小安全距离最小安全距离为:
5。
7、设置进给率
7.1、单击“进给率”按钮,弹出“进给和速度”对话框。
7.2、选择“速度”选项卡,设置主轴速度为:
550rpm。
如图4-6所示。
7.3、选择“进给”选项卡,设置剪切速度:
40mmpm;如图4-6所示完成后如图4-7所示。
8、生成刀具轨迹
单击“生成”图标,单击“确定”按钮,就会出现4-8图形。
图4-6图4-7
图4-8
9、仿真刀具轨迹
单击“确认”图标,选择“2D动态”选项卡。
(6)、创建铰孔加工操作
1、创建铰孔操作
1.1、单击“加工创建”工具栏中的“创建操作”图标,弹出“创建操作”对话框。
1.2、如图4-9所示,在弹出“创建操作”对话框中,选择类型为:
drill;选择子类型:
铰孔,设置如下各父节点组:
程序:
YECHUN
使用几何体:
WORKPIECE;
使用道具:
T4D32;
使用方法:
DRILL-METHOD;
输入名称为:
4。
2、定义加工孔位置
2.1、选择“孔”图标,单击“选择”按钮,弹出如图4-2所示。
2.2、单击“面上所有孔”按钮,选择的面为直径为50的圆的上表面。
2.3、单击“确定”按钮——“选择结束”按钮——单击“确定”按钮——单击“显示”按钮。
3、定义部件表面
3.1、单击“确定”按钮,弹出“部件表面”对话框,如图4-3所示。
3.2、在“部件表面”对话框中,选择类型:
面,这时的面是毛坯图的直径为50的圆上表面。
3.3、单击“确定”按钮——单击“显示”按钮。
4、定义底面
4.1、选择“底面”图标,单击“选择”按钮,弹出“底面”对话框,这时选择的底面为为直径为50的圆的下表面。
4.2、单击“确定”按钮——单击“显示”按钮。
5、设置循环参数
5.1、默认循环类型为:
标准镗,单击“编辑参数”·
5.2、默认循环参数组:
1——单击“确定”按钮——在“Cycle深度”中单击“穿过底面”——单击“确定”按钮。
6、设置最小安全距离最小安全距离为:
5。
7、设置进给率
7.1、单击“进给率”按钮,弹出“进给和速度”对话框。
7.2、选择“速度”选项卡,设置主轴速度为:
300rpm。
如图4-10所示。
7.3、选择“进给”选项卡,设置剪切速度:
30mmpm;如图4-10所示完成后如图4-11所示。
8、生成刀具轨迹
单击“生成”图标,单击“确定”按钮,就会出现4-12图形。
9、仿真刀具轨迹
单击“确认”图标,选择“2D动态”选项卡。
图4-10图4-11
图4-12
第二节、直径为35的圆上表面和直径为16孔的加工
(1):
创建父节点组
1、创建程序父节点组
2、创建刀具父节点组
2.1、创建第一把刀具:
平底刀,输入名称为T1D16。
2.2、创建第二把刀具:
中心钻,输入名称为T2D3。
2.3、创建第三把刀具:
麻花钻,输入名称为T3D15.8。
2.4、创建第四把刀具:
铰刀,输入名称为T4D16。
具体过程同第一节创建刀具父节点组类似。
3、创建几何体父节点组
3.1、单击“操作导航器”工具栏中的“几何视图”图标,切换操作导航器至几何视图。
3.2、定义加工坐标系:
双击几何视图中的“MCS-MILL”节点,弹出“MILL-ORIENT”对话框,所选坐标系是在零件图的直径为35的圆的上表面。
3.3、设置安全平面:
在安全设置选项中选择“平面”,指定平面,在“平面构造器”的对话框中,所选平面是在零件图的直径为35的圆的上表面,“偏置”值为50。
3.4、选择零件几何
3.5、定义毛坯几何
具体过程同第一节创建几何体父节点组类似
5、设置加工方法父节点组
具体过程同第一节加工方法父节点组类似
(2)、创建平面加工操作
具体过程同第一节平面加工操作类似,结果如图5-1所示。
图5-1
(3)、创建定位孔加工操作
具体过程同第一节定位孔加工操作类似,结果如图5-2所示。
图5-2
(4)、创建预钻孔加工操作
具体过程同第一节预钻孔加工操作类似,结果如图5-3所示。
图5-3
(5)、创建铰孔加工操作
具体过程同第一节铰孔加工操作类似,结果如图5-4所示。
图5-4
第三节、在直径为27的圆中直径为16孔的加工
(1):
创建父节点组
1、创建程序父节点组
2、创建刀具父节点组
2.1、创建第一把刀具:
中心钻,输入名称为T1D3。
2.2、创建第二把刀具:
麻花钻,输入名称为T2D15.8。
2.3、创建第三把刀具:
铰刀,输入名称为T3D16。
具体过程同第一节创建刀具父节点组类似。
3、创建几何体父节点组
3.1、单击“操作导航器”工具栏中的“几何视图”图标,切换操作导航器至几何视图。
3.2、定义加工坐标系:
双击几何视图中的“MCS-MILL”节点,弹出“MILL-ORIENT”对话框,所选坐标系是在零件图的直径为27的圆的上表面。
3.3、设置安全平面:
在安全设置选项中选择“平面”,指定平面,在“平面构造器”的对话框中,所选平面是在零件图的直径为27的圆的上表面,“偏置”值为50。
3.4、选择零件几何
3.5、定义毛坯几何
具体过程同第一节创建几何体父节点组类似
6、设置加工方法父节点组
具体过程同第一节加工方法父节点组类似
(2)、创建定位孔加工操作
具体过程同第一节定位孔加工操作类似,结果如图6-1所示。
图6-1
(3)、创建预钻孔加工操作
具体过程同第一节预钻孔加工操作类似,结果如图6-2所示。
图6-2
(4)、创建铰孔加工操作
具体过程同第一节铰孔加工操作类似,结果如图6-3所示。
图6-3
第四节、直径为27的圆中直径为10孔的加工
(1):
创建父节点组
1、创建程序父节点组
2、创建刀具父节点组
2.1、创建第一把刀具:
中心钻,输入名称为T1D3。
2.2、创建第二把刀具:
麻花钻,输入名称为T2D9.8。
2.3、创建第三把刀具:
铰刀,输入名称为T3D10。
具体过程同第一节创建刀具父节点组类似。
3、创建几何体父节点组
3.1、单击“操作导航器”工具栏中的“几何视图”图标,切换操作导航器至几何视图。
3.2、定义加工坐标系:
双击几何视图中的“MCS-MILL”节点,弹