某型开关盒底座注塑模具设计设计.docx
《某型开关盒底座注塑模具设计设计.docx》由会员分享,可在线阅读,更多相关《某型开关盒底座注塑模具设计设计.docx(49页珍藏版)》请在冰豆网上搜索。
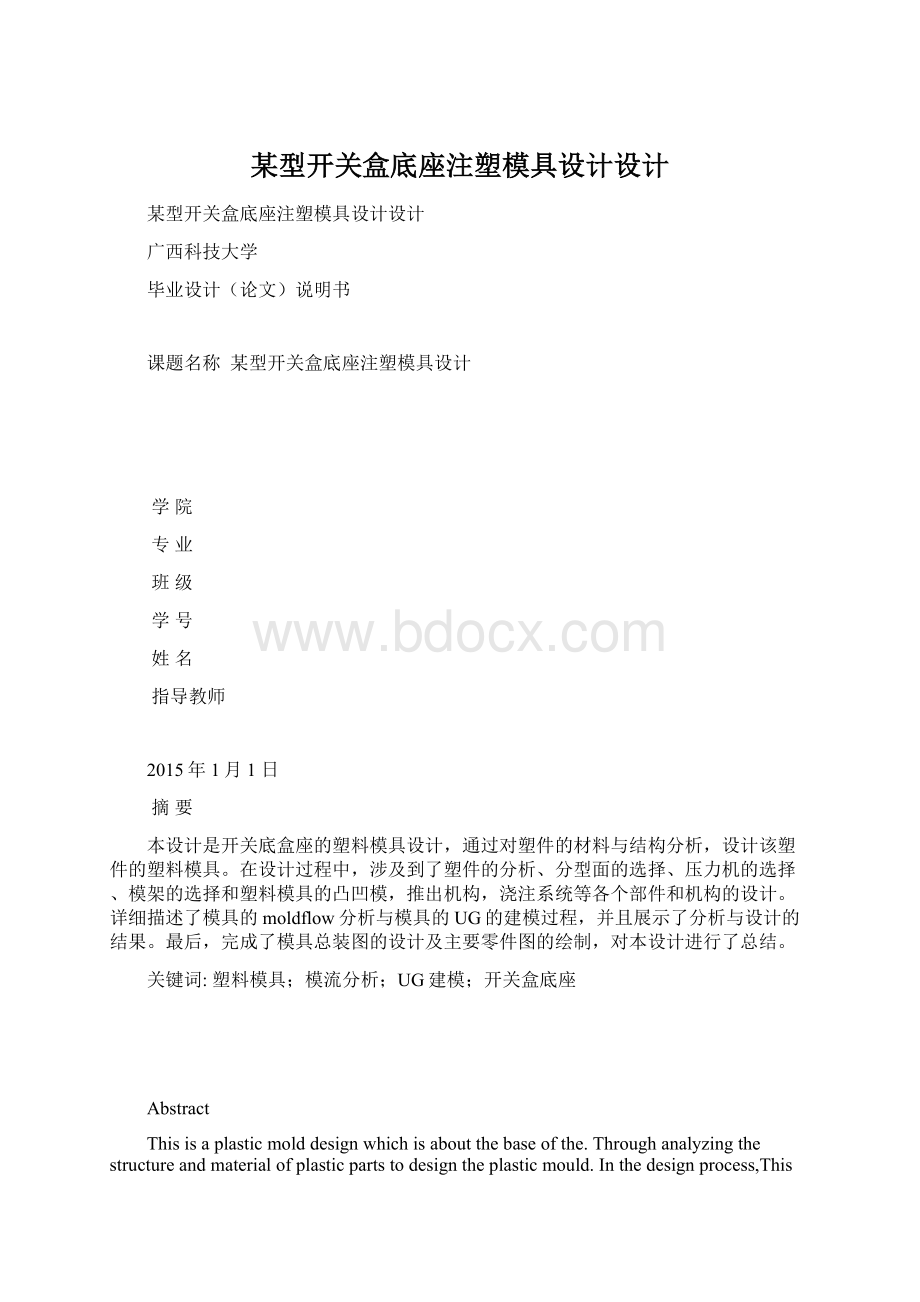
某型开关盒底座注塑模具设计设计
某型开关盒底座注塑模具设计设计
广西科技大学
毕业设计(论文)说明书
课题名称某型开关盒底座注塑模具设计
学院
专业
班级
学号
姓名
指导教师
2015年1月1日
摘要
本设计是开关底盒座的塑料模具设计,通过对塑件的材料与结构分析,设计该塑件的塑料模具。
在设计过程中,涉及到了塑件的分析、分型面的选择、压力机的选择、模架的选择和塑料模具的凸凹模,推出机构,浇注系统等各个部件和机构的设计。
详细描述了模具的moldflow分析与模具的UG的建模过程,并且展示了分析与设计的结果。
最后,完成了模具总装图的设计及主要零件图的绘制,对本设计进行了总结。
关键词:
塑料模具;模流分析;UG建模;开关盒底座
Abstract
Thisisaplasticmolddesignwhichisaboutthebaseofthe.Throughanalyzingthestructureandmaterialofplasticpartstodesigntheplasticmould.Inthedesignprocess,ThisdesignrefertoTheanalysisoftheplastic,theselectionofthepressandthevariousagenciesandcomponentsofPlasticmoldsuchasintensive,Launchinstitutions,gatingsystemetc.this instructionsdetaillydescribesmoldflowanalysisandmouldofUGmodelingprocessofmolddesignandshowstheresultsoftheanalysisanddesign.finally,Completedthedesignofthemoldassemblydiagramandmainpartsgraphdrawingandsummarizedthisdesign.
keywordsDesignofplasticmoldMoldflowanalysisUGmodeling
Switchbase
摘要I
AbstractII
前言1
1毕业设计任务3
2材料以及塑件工艺的分析4
2.1对材料的分析4
2.2塑件结构分析5
2.3成型方法及工艺的选择6
3模具的设计8
3.1模具型腔数的确定8
3.2压力机的选择8
3.3分型面的确定10
4浇注系统11
4.1主浇道的设计11
4.2分流道的设计11
4.3浇口的设计12
5模具成型零件的设计14
5.1凸凹模的设计14
5.2镶件17
5.3抽芯机构18
6模架的选择19
6.1采用的模架形式19
6.2模架参数19
6.3模架校核20
7导向和推出机构21
7.1导向机构21
7.2推出机构21
8复位机构23
8.1复位工作原理23
8.2复位杆与推板23
9排气与冷却系统25
9.1排气25
9.2冷却25
10模具的工作原理26
10.1注射的工艺过程26
10.2模具的工作步骤26
11UG建模27
11moldflow分析31
13校核42
13.1型腔数的校核42
13.2注射机的校核42
13.3推出校核43
参考文献48
前言
在我们的生活中,塑料产品随处可见。
比如我们家里的电视机外壳、水桶、脸盆、吹风机、水果篮子、电线盒、电风扇外壳;我们手中的手机外壳、笔壳、眼镜框;外面看到的塑料水管、灯罩、汽车内的方向盘与手柄等。
这些塑料产品的生产离不开塑料模具。
随着科技的不断发展,各种材料被人们开发。
在满足使用要求的情况下,塑料制品将代替金属制品出现在我们的生活中。
因为塑料产品的物美价廉,美观且有良好的和手感,比金属产品轻,方便使用。
由于人们的日益需求增加,产品的需求量也将非常庞大。
为了满足人满的需求,降低生产成本。
在先进的生产设备、计算机技术的快速发展以及科技的不断进步下,塑料模具的发展速度得到很大的提升。
模具发展的进程。
过去的模具加工是以钳工为核心的,大量依靠人工去技艺制作模具,先在生产水平不断提高,钳工制作为主被以数控机床加工为主代替,钳工将作为一种辅助。
科技的不断发展,从而使模具的生产周期变得越来越短,标准化不断提高,精度也越来越高。
目前,我过模具发展的现状。
模具的产品发展正向着更精密,更大型,更复杂,更经济的方向不断前进。
现代人们生活的高需求,在产品的美观上,质量上都有很高的需求,这也会增加了模具的复杂与精密;汽车防护栏,车内装饰件等大型塑件,不仅能减轻汽车的重量而且具有良好的手感,这也要求我们的模具做的大型与精密。
同时成本低,说明你在市场的竞争力就强,要用最低的成本,生产出质量好的产品。
以无图化、信息化、精细化和自动化的方向去指导生产。
模具的开发是以CAE/CAD/CAM技术来进行的,通过这些技术来设计、模拟与分析模具,预测所设计出来的模具与成产的产品,分析生产过程中的问题和产品的缺陷。
在模具加工之前,通过CAE分析软件moldflow等分析预测熔体的填充、保压、冷却情况,分析制品的翘曲变形与收缩情况,分析气泡产生的位置,浇口的位置。
从而对设计进行优化,能让我们的设计更加完善。
通过UG等CAD软件进行模具的设计与研发,制作好模型之后,编译成数控代码,通过CAM系统控制数控机床进行模具生产。
可以通过计算机技术,实现无图化,信息化,自动化的去生产。
通过快速成型技术RE/RP技术可以让我们快速的制作出产品模型以及模具。
特别是在复杂产品设计时,快速成型技术可以快速的收集产品的数据,转化为计算机语言,避免了对复杂产品的测绘,加快了模具的生产周期。
在以CAE/CAD/CAM技术结合现有的先进设备,使模具的生产周期大大缩短,成产成本大大降低,生产效率不断提高,引领模具行业进入一个新的发展时代。
模具的设计的标准化,通过模架的标准生产,以及标准件的生产,使模具生产得到良好的分工,不再是一套模具的个个两件都要自己成产,我们设计的模具可以自己做出动模与定模,再配合其他厂的标准件就可以制作出一套模具了。
我国模具发展的不足。
我国现在的模具生产与外国相比还是有不小的差距的。
外国有高精密的数控机床,为他们设计模具提供有利条件,有良好的软件支持。
我过模具行业发展不平衡,产品水平较低;设备与工艺落后,相比与外,我们的设备与精度还是有待提高;技术人才相对较少,独立研发与设计,创新与探索的水平要不断加强。
我过还处于发展中国家,中国的强大将落在我们这一代身上,我们要不断的努力,让中国走向强国之列。
我们作为一名大学生,首先最重要的是要把基础打扎实,把我们所学的东西都弄懂并掌握,再者是把所学的东西应用于实际生产中,用理论来指导实际,最后是有一定的水平后能够去创新与探索,学无止境,要不断的去探索与突破,这才是有志青年的特点。
本设计的目的是总结四年所学的知识,加以熟练与巩固,并尝试着去实践与设计,与实际生产接轨。
这是我们四年来知识的浓缩。
我们以图书馆,网上资料,以及课本教学内容为理论基础,通过结合现代软件技术,去设计塑料模具。
去试着分析模具的注射过程。
设计出模具的三维图,画出它的二维图。
本设计具有的意义。
培养我们综合分析和解决问题的能力和独立工作能力、组织管理能力;提高我们的工作态度、事业心和责任感。
同时,做毕业设计能够学习深化、拓宽、综合运用所学知识;总结学习、研究与实践的成果;提高我们的综合素质与工程实践能力。
1毕业设计任务
图1.1塑件实物
(1)对塑件进行分析,材料的选择,对初选模具的结构。
(2)用UG建立3D模型。
(3)选择分型面。
(4)用UG建立分型面,分型出凸凹模。
(5)用moldflow进行分析。
(6)选择压力机并校核。
(7)设计浇注系统。
(8)设计凸凹模模,并校核刚度强度。
(9)选择模架并,校核压力机安装。
(10)设计导向机构。
(11)设计抽芯滑块,并校核推出距离。
(12)设计推出与复位机构,并校核推出力。
(13)设计冷却与排气系统。
(14)总装图,零件图加起来达到3张A0图纸。
(15)写40页以上的说明书。
(16)翻译英文文献,5000个中文以上。
2材料以及塑件工艺的分析
2.1对材料的分析
2.1.1材料的选用
选用的塑料为丙烯腈-丁二烯-苯乙烯塑料(ABS)。
ABS是合成树脂,由丙烯腈、丁二烯、苯乙烯塑料合成。
其英文名为acrylonitrile–butadiene–styrenecopolymer ,简称为ABS。
因为其阻燃性、抗冲击性、耐化学药品性及电气性能优良,还具有易加工、制品尺寸稳定、表面光泽性好等特点我们选择它作为塑件的原料。
2.1.2ABS的性能
丙烯腈具使ABS有良好的耐化学腐蚀性和便面硬度;丁二烯使ABS具有坚韧性;苯乙烯使ABS具有良好的加工性和染色性。
ABS树脂呈浅象牙色,不透明,无毒无味,相对密度约为1.05左右,吸水率0.2%-0.7%。
ABS燃烧缓慢,离火后继续燃烧,火焰呈黄色,有黑烟,燃烧后塑料软化焦化,伴有橡胶燃烧气味,无熔融滴落现象。
[1]
ABS具有突出的抗冲击能力,低温下抗冲击性仍然不变。
没有明显的力学缺陷显示出良好的综合力学能力,具有良好的机械强度,具有一定的耐磨性、耐寒性、耐油性、耐水性。
化学稳定性和电气性能良好。
[1]具有一定的硬度,尺寸稳定,易成型,容易着色。
ABS的耐候性与耐热性差,使用温度在-40度到100度之间,受到紫外线照射易氧化降解。
在ABS中加入炭黑或酚类抗氧化剂可以提高耐候性。
ABS无明显熔点,粘流温度在160℃左右,分解温度达250℃以上,具有良好的成型加工性。
注射成型温度一般在160℃~240℃之间。
ABS的吸水率在3%左右。
在成型加工时常进行干燥处理。
干燥温度在70℃到90℃。
ABS的收缩率为0.4%~0.8%,可以制的精度较高的的制品。
2.1.3ABS的应用
ABS具有良好的成型加工性,使用与注塑、挤出、吹塑等成型方法。
可以制作各种机壳、汽车部件、电气零件、灯具、家具、安全帽等。
ABS有很多类型,有通用型、耐热型、电镀型、阻燃型等。
阻燃型的ABS,通常与难燃的树脂混合制得。
将ABS与PVC混合,所得的材料具有良好的阻燃性能,可以用于各种要求阻燃的部件和制品。
我们选用阻燃型的ABS,因为产品是开关底座,用于电气方面,要求具有良好的阻燃性
2.2塑件结构分析
(1)塑件
如图2.1所示。
图2.1塑件的基本尺寸
(2)塑件的收缩率
由参考资料[1],ABS的收缩率为0.4%~0.8%,我们选择它的收缩率为0.5%。
(3)塑件的尺寸精度和表面粗糙度
塑件的尺寸精度要求较低,满足使用要求即可,表面粗糙度没有太大的要求,底面贴墙要求平整,侧面要求无突出,能够使上盖放入。
(4)斜度
塑件基本上垂直方正的,要求我们为模具设置脱模斜度。
由参考文献【2】,表3.4,ABS的脱模斜度为:
型腔:
35’~1°30’;型芯30’~40’。
根据产品的高度,其高度为6mm,高度较小,我们可以选取在塑件上加一个0.5°的拔模斜度。
(5)壁厚
塑件的壁厚为1.5mm。
厚度刚好合适,不会浪费原料,冷却快,不易产生表面凹陷,内部缩孔等缺陷。
(6)加强筋
产品的壁高6mm,高度较低,不用设置加强筋,而且在使用时,四壁不受很大力,只起到支撑固定作用。
(7)孔的设计
塑件周边4个孔起固定作用,为了加强起强度,在孔处设置一个1mm的凸台。
孔处于四壁相交处,不会影响塑件壁的强度。
2.3成型方法及工艺的选择
(1)加工工艺过程
混料------干燥-----螺杆塑化-----注射充模-----保压-----冷却-----脱模推出塑件-----塑件的后处理。
(2)ABS的干燥处理
以为ABS对水的敏感度较大,具有吸湿性。
在加工前要先做干燥处理。
减少制件由水分造成的表面烟花状泡带,银丝、色斑和云纹等。
而且还有利于塑料的塑化。
干燥时,在80℃
~90℃下干燥两个小时以上。
需要把水分控制在0.1%以下。
可以选用烘干漏斗,且装有热风料斗干燥器。
(3)注射成型时各段温度
ABS的适宜加工温度为200℃到230℃。
料筒后段温度一般取160℃~180℃之间。
料筒中段温度在180℃~200℃之间。
料筒前段温度取200℃~220℃之间。
喷嘴温度一般取170℃~180℃之间。
模具温度一般取60℃~70℃之间。
(4)注射的压力
在注射的过程中,型腔的压力决大小决定了塑件的表面质量和缺陷程度。
压力过小,塑料收缩就变大,塑料与型腔表面脱离,之间表面易雾化。
压力过大,塑料与型腔的表面摩擦及会大,已造成黏模。
由于是一模四腔,需要的注射压力较大,应选在80~120Mpa之间。
保压压力选择在40~50Mpa。
1)注射的速度
注射速度对ABS融体流动性具有一定的影响,若注射速度过快,充模快,但易出现排气不良,表观粗糙度不好的现象;若注射的速度过慢,产品表面可能会出现波纹和熔接不良等现象。
所以采用中等的速度比较好。
2)料量的控制
我们在能满足注射用量的情况下,选着注射剂注射两的50%到70%之间的注射量,以提高塑件的尺寸稳定性。
3)成型时间周期
注射时间:
2-3S。
保压时间:
20-25S。
冷却时间:
15-20S。
成型周期:
40-50s。
4)后处理
模具的尺寸精度较低,没有特殊的要求,满足使用即可,所以不需要做后处理。
因为选用的是侧面浇注,有侧浇口,下零件产品后,需要人工把浇注系统从塑件分离。
3模具的设计
3.1模具型腔数的确定
塑件的精度等级要求较低,结构较为简单,有两个对称的抽芯结构,要求产量较高,工件的尺寸也比较小,在保证质量的前提下,腔数越多经济性越好,我们选择一模四腔。
型腔的排布如图3.1所示。
图3.1塑件在模具中的分布
3.2压力机的选择
(1)塑件的质量与体积的计算
通过UG建模,可以求出塑件的体积与表面积,如图3.2,3.3所示。
单个塑件体积V1=15.24cm2。
单个塑件的投影面积A1=6978mm2。
ABS塑料的密度=1.05g/cm2。
质量m1=ρV1=15.24*1.05=16g,有四个塑件,取塑件凝料为塑件的0.2。
计算注射量:
m=1.2*4*16=76.8gV=m/ρ=76.8/1.05=73.14cm3
图3.2塑件的表面积
图3.3塑件的体积
1)塑件和凝料在分型面上的投影面积与所需的锁模力
取凝料在分型面上的投影面积为塑件的0.2,所以,
A=4A1+0.2A1=4*6978+0.2*6978=29307.6mm2
锁模力F=AP=29307.6*35=1025766N=1025.766KN
其中,由参考资料【3】,表2-2,平均压力P取35Mpa。
2)选取压力机
由参考资料【3】,表13-1,选取型号为XS-ZY-250的压力机。
压力机的参数表3.1所示:
表3.1:
注射机参数
理论注射容积/cm3
250
螺杆直径/mm
50
注射压力/Mpa
130
注射行程/mm
160
注射时间/s
2
塑化能力/(g/s)
18.9
注射方式
螺杆式
合模力/KN
1800
最大成型面积/mm
500
移模行程/mm
500
最大模具厚度/mm
350
最小模具厚度/mm
200
模板尺寸/mm
598*520
拉杆空间/mm
488*370
合模方式
增压式
推出方式
中心及两侧推出
电动机功率./Kw
18.5
喷嘴球半径/mm
18
喷嘴口直径/mm
4
定位孔直径/mm
125
额定注射量250>V=m/ρ=76.8/1.05=73.14cm3
额定锁模力1800>F=AP=29307.6*35=1025766N=1025.766KN
3.3分型面的确定
分型面的设计原则:
(1)分型面应该设在塑件的最大外轮廓处。
(2)分型面的选择应该有利于塑件的脱模。
(3)分型面应该设置在能够保证塑件的尺寸精度与表面质量的地方。
(4)分型面的选择应有利于型腔的加工。
(5)分型面的选择应有利于排气。
根据塑件的结构与方便加工,我们设置在塑件的最大外形处。
并且尽量能够在动模一侧加工。
分型面如图3.4所示.
图3.4模具的分型面
4浇注系统
。
4.1主浇道的设计
我们选择侧浇口的形式进行浇注。
采用单分型面的结构
设计的浇口样式如图4.1所示。
图4.2浇口样式
主流道呈圆锥型,锥角取2°,方便凝料拔出,浇口套上面设有半圆形孔,方便与喷嘴连接,使其半径大于喷嘴圆球半径。
定位环,使安装模具时起到定位作用。
主流道的尺寸如下:
主流道小端的直径=注射机喷嘴直径+(0.5~1)=4+0.5=4.5mm。
主流道的球面半径=注射机喷嘴半径+(1~2)=18+2=20mm。
取球面配合高度=3mm。
主浇道底端孔直径=主流道长度*tan2°+小端口直径=57*tan2°+4.5=6.5mm。
主流到长度=A板的厚度+浇口套的高度-球面高度=40+20-5=55mm。
浇口套总长=A板的厚度+浇口套的高度=60mm。
浇口套采用两个螺钉将其固定在定模板上。
4.2分流道的设计
分流道的设计如图4.3所示。
图4.3分流道
选择对称的方式进行放置。
开设在分型面上,采用半圆形的截面,放置于动模。
方面统一加工和降低动模与定模的配合,不易在塑件上留下痕迹。
流道两端超出,设置冷料穴。
分流道尽量选择较短行程,减少压力与热量损失。
分流道的尺寸:
半圆型截面的直径=7mm。
分支到主浇道的距离=50mm。
冷料穴到分支的长度=5mm。
水平的长流道的长度=7+5+50+50+5=117mm。
四个分支的长度=10+7=17mm。
4.3浇口的设计
浇口如图4.4所示。
浇口为测浇口,我们选着它的截面为长方形。
尺寸如下:
浇口截面长=3mm,高=1mm
分支到塑件,浇口的宽=3mm
图4.4浇口的形状
(1)
浇口位置的选择
通过moldflow分析浇口,结果如图4.5所示。
图4.5moldflow浇口分析
浇口放在塑料中心和四周是最好的,由于底板要装于腔壁上,内部要装部件,要求有一定的平整性,只能选在四周。
我们选择用侧浇的方式,为缩短浇道的距离,浇口选在侧面。
(2)浇口的平衡
由于塑件一模四腔堆成分布,主浇道到塑件的距离是一样的,选择的浇口大小也一致,所以不存在浇注不平衡问题。
5模具成型零件的设计
5.1凸凹模的设计
塑件高度较低,结构较为简单,精度要求不高。
定模版基本上为一个平面,主要加工在凹模部分。
选择整体式的凸凹模结构。
其他细节小部位零件设置小型凸模和固定镶块的模式。
通过UG建模,对凸凹模进行设计,出二维图。
凸凹模的加工,根据数模进行数控加工出来。
(1)通过UG建立零件模型
如图5.1所示。
5.1零件模型图
(2)对塑件进行拔模处理
拔模角度为0.5度,并设置零件的收缩率,起收缩率为0.5%。
如图5.2所示。
(3)抽取分型面与建立毛胚
分型面如图3.4所示。
分型面长为175mm,宽为175mm,塑件边距离坐标轴的距离分别为15mm,20mm。
抽取分型面,补好孔,创建有界毛胚外轮廓,把所有的面缝合去来使它们成一个片体,如图5.3所示。
图5.2斜度分析
图5.3拉伸凸凹模
拉伸凸凹模毛胚,因为塑件是扁平的,凸凹模不用太厚,选择凸凹模的厚度为40mm。
(4)用塑件去切割凹模,形成塑料腔体
如图5.4所示。
图5.4分模
(5)排布组合成凸凹模模板
如图5.5所示。
图5.5左为定模板,右为动模板
两模板的厚度为40mm,长为350mm,宽为350mm
(6)小凸模型芯
塑件上有小槽、小孔,我们选择小型芯来成型。
方便小凸模磨损后更换,也使得定模加工起来方便。
使用台肩固定的形式,用定模固定板来固定和压紧小凸模。
设计如图5.6所示。
图5.6小凸模
一模四腔,每个腔有3个小凸模。
底部凸台为直径为12mm的圆,高5mm。
中间部分为与上部凸模底部尺寸一样的长方体。
5.2镶件
塑件有两个高的小突起,用来支撑按键开关,这两个突起尖齿如果在动模板直接加工,会很麻烦,而且难排气,可能会造成浇注不满的现在。
我们在凸模设置以个镶件,用垫板固定在动模上。
在镶件上面加工出孔,在装到动模上,这样会使得加工起来很方便,而且容易排气。
镶件如图5.7所示。
图5.7镶件
一模四腔,每个塑件有两个镶件。
镶件的尺寸如下:
底部固定部分:
高度为5mm,长为8mm,宽为6mm。
上部:
长8mm,宽3mm。
整个镶件高:
40mm。
5.3抽芯机构
塑件中间有两个需要抽芯的地方,抽芯距离为2mm,塑件总高度为19mm。
我们采用一个内抽芯的方式进行抽芯,使用滑块抽芯机构,不仅具有顶出塑件的作用,而且能够良好的排气。
使滑块滑行平面与竖直方向的夹角为7°,要抽出2mm的距离需要推出16.3mm的距离。
16.3mm<塑件推出距离20mm,满足要求。
抽芯机构设计如图5.8所示。
图5.8型芯滑块
一模四腔,总共有8个抽芯块。
尺寸如下:
上平面的长为70mm,宽为14mm;突出的型芯结构高2mm,宽2mm长70mm;
滑块总高度为77mm。
6模架的选择
6.1采用的模架形式
模架的形式选择如图6.1所示。
图6.1模架
计算选择模架所用数据:
因为是一模四腔,宽方向的距离(塑件的投影宽度):
85+85+30=210得,W3=212mm
长方向的距离:
85+85+40>L2-30-D2,得L2>265mm
其中,W3为推件板宽度;D2为复位杆的直径,取D2=25mm;L2为复位杆之间的距离。
6.2模架参数
根据参考资料[3],表7-4模架尺寸组合,依据数据查表,并选择模架的参数。
如下:
模架代号:
3535
竖直方向:
AB板宽度:
W=350mm
AB板长度:
L=350mm
A板的厚度:
A=40mm
B板的厚度:
B=40mm
C板的厚度:
C=90mm
上模座板与下模座板的厚度:
H1=30mm
BC板之间的固定板厚度:
hH2=25mm
推件板固定板厚度:
H5=20mm
推件板厚度:
H6=25mm
宽方向:
上模座板与下座板宽度:
W1=400mm
C板宽度:
C=63mm
推件板宽度:
W3=220mm
复位杆宽方向之间的距离:
W4=164mm
推件板与推件板固定板固定螺钉宽方向之间的距离:
W5=196mm
导柱宽方向之间的距离:
W6=184mm
下模座板与C板连接螺钉宽方向的距离:
W7=285mm
长方向:
推件板与推件板固定板固定螺钉长方向之间的距离:
L1=326mm