环锭细纱机加捻卷绕技术结构现状与创新.docx
《环锭细纱机加捻卷绕技术结构现状与创新.docx》由会员分享,可在线阅读,更多相关《环锭细纱机加捻卷绕技术结构现状与创新.docx(50页珍藏版)》请在冰豆网上搜索。
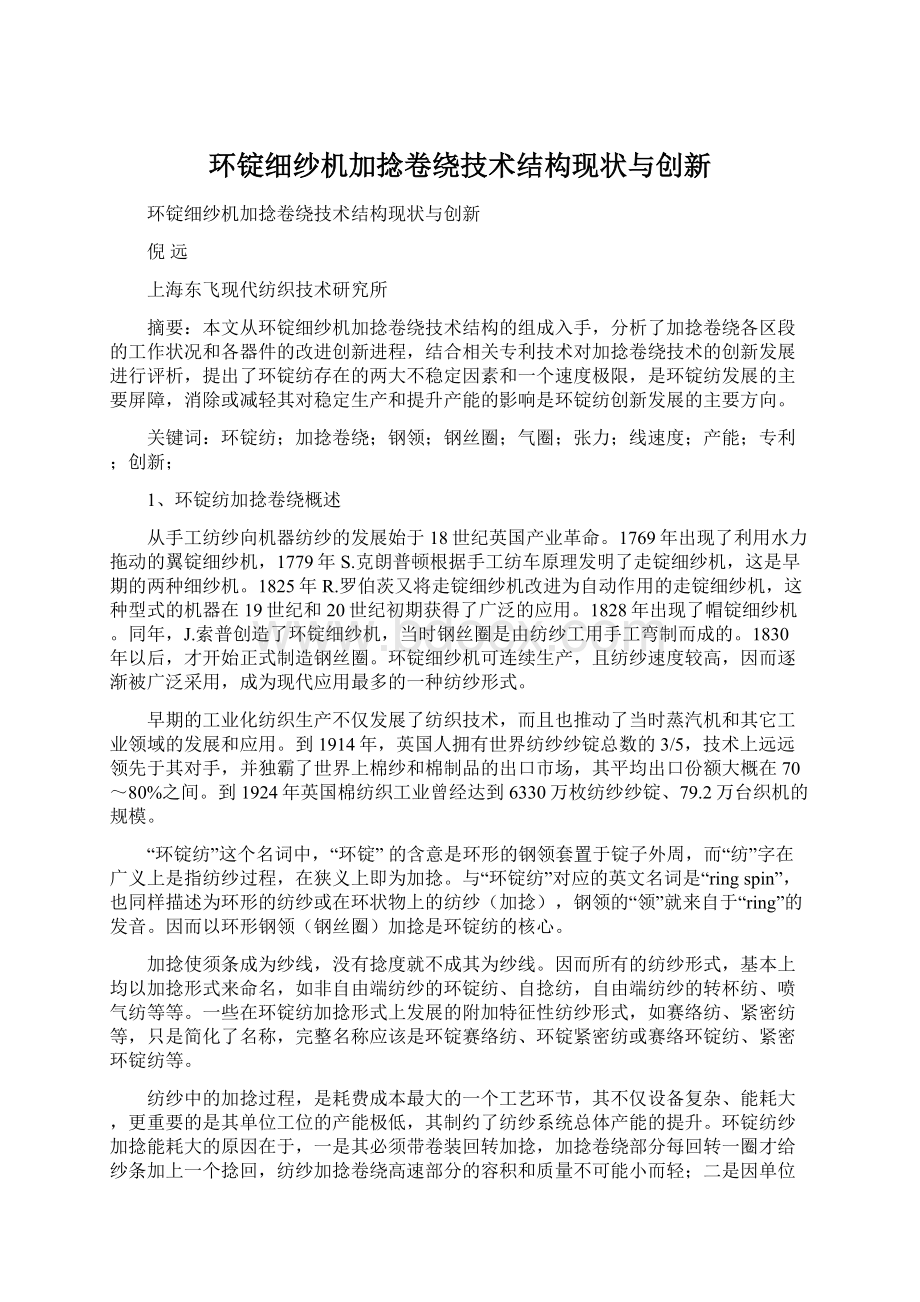
环锭细纱机加捻卷绕技术结构现状与创新
环锭细纱机加捻卷绕技术结构现状与创新
倪远
上海东飞现代纺织技术研究所
摘要:
本文从环锭细纱机加捻卷绕技术结构的组成入手,分析了加捻卷绕各区段的工作状况和各器件的改进创新进程,结合相关专利技术对加捻卷绕技术的创新发展进行评析,提出了环锭纺存在的两大不稳定因素和一个速度极限,是环锭纺发展的主要屏障,消除或减轻其对稳定生产和提升产能的影响是环锭纺创新发展的主要方向。
关键词:
环锭纺;加捻卷绕;钢领;钢丝圈;气圈;张力;线速度;产能;专利;创新;
1、环锭纺加捻卷绕概述
从手工纺纱向机器纺纱的发展始于18世纪英国产业革命。
1769年出现了利用水力拖动的翼锭细纱机,1779年S.克朗普顿根据手工纺车原理发明了走锭细纱机,这是早期的两种细纱机。
1825年R.罗伯茨又将走锭细纱机改进为自动作用的走锭细纱机,这种型式的机器在19世纪和20世纪初期获得了广泛的应用。
1828年出现了帽锭细纱机。
同年,J.索普创造了环锭细纱机,当时钢丝圈是由纺纱工用手工弯制而成的。
1830年以后,才开始正式制造钢丝圈。
环锭细纱机可连续生产,且纺纱速度较高,因而逐渐被广泛采用,成为现代应用最多的一种纺纱形式。
早期的工业化纺织生产不仅发展了纺织技术,而且也推动了当时蒸汽机和其它工业领域的发展和应用。
到1914年,英国人拥有世界纺纱纱锭总数的3/5,技术上远远领先于其对手,并独霸了世界上棉纱和棉制品的出口市场,其平均出口份额大概在70~80%之间。
到1924年英国棉纺织工业曾经达到6330万枚纺纱纱锭、79.2万台织机的规模。
“环锭纺”这个名词中,“环锭”的含意是环形的钢领套置于锭子外周,而“纺”字在广义上是指纺纱过程,在狭义上即为加捻。
与“环锭纺”对应的英文名词是“ringspin”,也同样描述为环形的纺纱或在环状物上的纺纱(加捻),钢领的“领”就来自于“ring”的发音。
因而以环形钢领(钢丝圈)加捻是环锭纺的核心。
加捻使须条成为纱线,没有捻度就不成其为纱线。
因而所有的纺纱形式,基本上均以加捻形式来命名,如非自由端纺纱的环锭纺、自捻纺,自由端纺纱的转杯纺、喷气纺等等。
一些在环锭纺加捻形式上发展的附加特征性纺纱形式,如赛络纺、紧密纺等,只是简化了名称,完整名称应该是环锭赛络纺、环锭紧密纺或赛络环锭纺、紧密环锭纺等。
纺纱中的加捻过程,是耗费成本最大的一个工艺环节,其不仅设备复杂、能耗大,更重要的是其单位工位的产能极低,其制约了纺纱系统总体产能的提升。
环锭纺纱加捻能耗大的原因在于,一是其必须带卷装回转加捻,加捻卷绕部分每回转一圈才给纱条加上一个捻回,纺纱加捻卷绕高速部分的容积和质量不可能小而轻;二是因单位工位产能低,且只能通过提高锭速来成比例地增加产能,而高速元件的能耗与速度的平方成正比,因此速度越高,单位长度或质量的纱线能耗成本越大。
可见纺纱设备的利用率与纺纱能耗之间存在着不可调和的矛盾。
表1是一带四锭加捻卷绕传动式环锭细纱机纺纱功耗的实测数据。
(表1的纺纱条件是:
二个方案同机台,420枚纱锭细纱机,采用17KW三相异步电机,变频控制;工艺:
纺制JC/T45英支,C60/T40-CVC品种,捻度1020/米,粗纱定量8克/10米,重量牵伸约61倍,平面牵伸弹簧摇架后区双压力棒,高效工艺牵伸配置;用PG1/2-4254钢令,OSS5/0钢丝圈。
纺纱长度4000米(管纱中纱),空纱管中部直径19毫米,管纱中部直径39毫米。
)
表1:
方案
锭速RPM
主机有功功率KW
1
16000
9.92
2
12000
5.44
2比1
-4000
-4.52
-25%
-45.6%
从表1数据可见,正常纺纱时,锭速12000rpm较16000rpm时功耗小45.6%,剔除产量因素以单位产量纺纱用电成本计,较低的纺纱速度比较高的纺纱速度整机功耗节电,该品种锭速12000rpm比16000rpm可节电(5.44/12000-9.92/16000)/(9.92/16000)=27%;同时其基本上符合纺纱功耗正比于纺纱速度之平方,即9.92/5.44≈(16000/12000)2。
使环锭纺发展成为主流的纺纱形式,其重要因素在于钢领钢丝圈加捻卷绕形式结构的简单和巧妙。
说钢领钢丝圈加捻卷绕结构为所有加捻卷绕形式中最简单和巧妙的结构并不为过。
一个环形轨道的“钢领”加上一个不成圈的“钢丝圈”,构成了最简洁有效的加捻卷绕主要结构。
在纺纱过程中,钢丝圈为完成输出纱线的卷绕而滞后于锭速,其自调速运动非常巧妙地适应于卷装上大小直径的卷绕,而不必机械地伺服于卷绕直径的变化。
气圈也是环锭纺加捻另一个巧妙的“结构”构成,虽然其没有应用附加构件。
说环锭纺为环锭回转加捻,其确切的描述应该是钢丝圈引导并和气圈纱条一起在环绕锭子的钢领上作回转加捻。
可见,气圈是空间无刚性约束的柔性体:
既是加捻结构的构成又是纱线输送的路径、钢丝圈是速度无刚性控制的周向运动自由体:
既是加捻的引导者又是卷绕的引导者。
这就是钢领钢丝圈加捻卷绕形式的简单和巧妙之所在。
环锭纺产能的制约,从根本上说也是源自于这种纺纱加捻卷绕形式的简单和巧妙,简单和巧妙的结构赋予了其成为主流纺纱加捻卷绕形式的重要元素,但其独有的纺纱气圈形态、张力波动状况和钢丝圈运行姿态、线速度极限等纺纱稳定性影响因素,都会在一个运转参数上体现出来――纺纱断头率,细纱机高效纺纱――产能进一步提升的梦想,也被纺纱断头所粉碎。
断头的主要因素除了纱线强力弱环小于张力峰值外,还包括钢丝圈过热、软化和烧毁飞圈及钢丝圈磨损割断头等钢丝圈运行意外状况造成的断头,这些是钢丝圈线速度或寿命超限的表征。
环锭纺被长期和大范围应用的另外两个因素是:
与其它纺纱形式相比,其适纺品种最广和纱线断裂强度最高。
环锭纺几乎可以纺制所有品种的纤维和所有线密度的纱线;环锭纱线也是所有纱线中对纤维强度利用率最高的纺纱形式。
这两大因素也与钢领钢丝圈和气圈加捻形式直接相关。
在环锭纺纱用电成本和用工成本占纺纱总成本比例不断增大的情况下,高速纺纱带来的单位用电功耗增加和因断头率增加而用工增加的矛盾日益凸显,在环锭纺纺纱加捻卷绕结构没有重大突破之前,进行加捻卷绕结构部件的改良和探寻综合经济性良好的纺纱工艺参数是近阶段业界可以作为的事。
2、纺纱分段与导纱角
2.1纺纱段
将前罗拉钳口到导纱钩之间的区域称为纺纱段,只是一种习惯的称呼。
前已所述,广义的“纺纱”是指整个纺纱过程,而细纱机上狭义的“纺纱”应该是指整个加捻卷绕过程。
2.1.1加捻三角区
按须条的行进方向看,加捻区始于加捻三角区。
从牵伸部分最后一个握持钳口输出的扁平须条被传来的捻回所包卷。
从捻度传递的路径看,三角区是加捻的末端。
握持钳口处扁平须条横向宽度的存在阻止了捻回向钳口的传递,形成了一个弱捻环节。
导纱钩与前钳口的相对位置关系,决定了在一落纱过程中,与卷绕升降相关的导纱钩升降和级升使纺纱段中三角区纱条与上下罗拉包围弧的动态变化状况。
纱条与上下罗拉的包围弧具有阻止捻度向三角区传递的不良效应。
同时导纱钩所处水平面与纺纱段纱条之间的夹角,即导纱角,决定了纱条在导纱钩上接触包围弧的长度,且由于导纱钩的升降和级升运动使其动态变化,气圈段纱条的回转加捻运动在纱条与导纱钩的接触中被阻止捻回向纺纱段传递的程度也在动态变化。
这种捻回逆纱线运动方向传递并受阻于接触点的现象称为捻陷。
因此纺纱段的捻度总是小于气圈段的捻度,也是整个加捻卷绕部分捻度最弱的一段,而在三角区,则是捻度最难以传递到的地方。
三角区一方面是动态纱条捻度和强度最弱的环节,另一方面也是须条的边纤维难以被包卷入纱体而产生毛羽的关键部位。
无论是牵伸区中的集聚,还是通过附加阻捻钳口设置附加集聚区,并在附加集聚区中进行集聚,都是为了缩小须条进入加捻区的横向尺寸,即缩小三角区的横向尺寸。
二十世纪末期兴起的紧密纺纱技术正是源自于这样的设计思路,采用负压气流式的同步凝聚也好,或者机械式的喇叭口、改变纱路矢量也好,都是为了减轻或消除三角区的不良影响,其对纱线产生了两个方面超乎想象的良性效应:
纱线毛羽大幅度减少、断裂强度明显提升。
可见小小三角区对纺纱外观和内在品质的影响。
由于纱线因与毛羽相关疵点的降低和强伸特性的改善,环锭紧密纺纱线成为所有纱线中纱体最紧密、断裂强度最高(单纤维强力利用率最高)的纱线。
2.1.2导纱角
导纱钩所处水平面与纺纱段纱条之间的夹角,称为导纱角。
导纱钩一方面阻止了捻度的传递,同时也使气圈段张力及其波动向纺纱段的传送被阻碍,对纺纱过程中卷绕段和气圈段动态张力的传送起到了缓冲效应。
因此,导纱角作为细纱机断面形态的一个重要参数,对其利弊平衡是细纱机设计的关键要素之一。
传统的细纱机导纱角设计取值,是在一个较小的范围内选择,细纱机集体落纱技术的应用,对包括导纱角、纺纱段长度、导纱钩与前罗拉钳口上下和进出位置、纱条与前上下罗拉包围弧等细纱机断面设计相关尺寸提出了新的要求。
集体落纱的细纱机断面尺寸中,为了适于垂直拔管的需要,导纱角和纺纱段长度均有增大的趋势。
这些参数的增大减弱了导纱钩对张力波动传递的缓冲效应,同时由于增加了气圈控制技术和纺纱张力――锭速控制技术,即气圈控制环和锭速的大中小纱分段变频调速技术(纺纱输出长度锭速控制)甚至复合卷绕直径变频调速技术(纺纱输出长度复合卷绕直径的锭速控制)的应用(详见本文3.5.4),缩小了纺纱张力的波动范围,从而也可以减少对通过纱条与导纱钩捻陷效应来抑制卷绕段和气圈段动态张力对纺纱段影响的依赖。
2.2气圈段
气圈段位于导纱钩与钢丝圈之间。
纺纱气圈是环锭纺所特具的产品工作形态,气圈段既是加捻卷绕的导纱路径,又是加捻结构的必要构成。
由于高速状态下纱条质点受离心力的作用,纱条呈外凸封闭的立体纺锤形体,在气圈上各点角速度相等的情况下,所处的直径越大,受到的离心力也越大,同时较大的回转半径使线速度成比例增大,纱条与空气的摩擦加剧,不但影响纱条外观品质,同时气圈回转所需的驱动功率和驱动力增加。
离心力和驱动力的增大意味着卷绕段和气圈段的动态张力增大,相应的断头概率增大。
因此控制气圈形态一向是细纱机设计和纺纱生产的重要任务,高速纺纱中控制气圈形态显得尤为重要。
现代细纱机设计中广泛采用导纱钩独立随动升降和气圈控制环技术。
导纱钩的独立随动升降功能,对小纱和大纱阶段的纺纱性能都有良性效应。
在小纱阶段,导纱钩的随动下移可以有效降低小纱特别是管底成形时的气圈高度,从而缩小气圈最大处直径,相应降低气圈段纺纱张力;在大纱阶段,导纱钩的随动上移可以有效增加气圈高度,因为过小的气圈高度使气圈对纺纱张力的柔性缓冲作用降低,从而导纱钩的随动上移可以有效降低断头概率。
采用气圈环控制气圈形态的方法,是将一个大气圈分隔成两个小气圈,气圈环便是两个小气圈结合处的颈部,其可以非常直观和有效地控制气圈最大直径,从而也控制了气圈段因气圈直径增大而产生的动态张力峰值。
因而,在高速(锭速大于18000RPM)纺纱中,气圈环的应用已是一个基本和必需的选项。
气圈形态对于纱线动态张力来说,是一个具有柔性缓冲调控作用的加捻结构,其可以在纱线动态强力允许的范围内,自动平衡由于钢领钢丝圈滑动摩擦副配合不协调而产生运行稳定性降低所导致的张力变化,使纺纱过程顺利进行。
随着卷绕升降、卷绕直径、气圈形态的动态变化,钢丝圈运行姿态也在不断改变,而钢丝圈运行姿态是其与钢领运动配合不协调、运行稳定性降低和纱线张力突变的主要原因。
日常生产中的气圈直径控制主要是钢丝圈重量的调整。
在钢丝圈型号不变的情况下,增加钢丝圈重量可以在一定范围内控制气圈直径,当然这也同时改变了纺纱张力。
较重的钢丝圈重量使卷绕段张力增大,气圈直径减小。
2.3卷绕段
卷绕段位于钢丝圈与卷装纱管之间,这是加捻卷绕三个分段中纱条路径最短的一段。
卷绕段是纱线加捻卷绕运行驱动力之源。
锭子与筒管通过卷绕段张力将驱动功率传递到钢丝圈与气圈,使之作高速回转运动并完成纱条的卷绕输送。
在一个卷绕升降动程中,卷绕直径的最大(一般为钢领直径减去三毫米)和最小(筒管直径)之比通常为两倍左右(钢领标称直径42毫米时),在最大直径时,纱条与钢丝圈所处点钢领的法线成最大卷绕角;在最小直径时,纱条与钢丝圈所处点钢领的法线成最小卷绕角。
因此,卷绕段的纺纱张力与卷绕直径的大小直接相关。
表2为纺纱实际有功功率分项测试和计算。
表2:
方案
整机有功功率
KW
平均每锭有功功率W
测试状态或计算说明
1
9.07
21.60
测试计算升降动程大直径段卷捻功率(剔除牵伸升降)
2
8.77
20.88
测试计算升降动程小直径段卷捻功率(剔除牵伸升降)
3
8.92
21.24
测试计算卷捻部分平均功率
4
6.68
15.90
测试计算断纱卷捻部分平均功率
5=1-4
2.39
5.69
计算大直径段的卷绕功率
6=2-4
2.09
4.98
计算小直径段的卷绕功率
7=5-6
0.3
0.71
计算大小直径段卷绕功率之差
8=3-4
2.24
5.34
计算平均卷绕功率
9=5比6
114.35%
计算大直径段与小直径段的卷绕功率之比
10=8比3
25.1%
计算卷绕功率占卷捻功率的比例
表2的纺纱条件同表1。
表中的卷捻功率是指传动加捻卷绕部分的有功功率,卷绕功率是指通过卷绕段纱条传递的有功功率。
在表2的纺纱有功功率实际测试和计算中获知:
一个升降动程中大直径时纺纱卷绕功率比小直径时大14.35%;实际消耗于纱线加捻卷绕的有功功率仅占卷捻部分有功功率的25.1%,即在加捻部分的有功功耗中,卷绕功耗仅占整个加捻卷绕部分有功功耗的四分之一左右,其余的四分之三均耗费在加捻传动部件和卷装驱动上。
这些耗能部件包括:
主电机传动皮带-主轴-滚盘-锭带-张力盘-锭子等传动链系统,其中主要可以分为二大部分,即在张力、重力、应力和润滑剂粘滞力等综合作用下的支承摩擦损耗及高线速度运行元件的空气阻尼损耗。
通过表2数据还可以计算卷绕段宏观平均张力,每锭卷绕段平均张力=每锭卷绕功率/卷绕线速度。
由于在短动程上下部存在卷绕直径的差异,即上部卷绕直径为19毫米,下部卷绕直径为39毫米,在锭速为16000rpm时,短动程大直径段每锭平均卷绕段张力=(5.69)/(16000×0.039×3.14/60)=0.174牛顿=17.4CN,短动程小直径段每锭平均卷绕段张力=(4.98)/(16000×0.019×3.14/1000/60)=0.313牛顿=31.3CN,短动程小直径比大直径卷绕段张力大(31.3-17.4)/17.4=79.9%。
通过上述测试和计算可知,同样纺纱阶段的小直径纺纱张力较大,这便是小直径纺纱时拎头偏重、断头偏多的主要原因。
同时该品种成纱的单纱强力为213.9CN,测试最低强力为167.9CN,中纱时短动程上部小直径纺纱的宏观平均卷绕段张力占成纱最低强力的比例=31.3/167.9=18.6%,纱线强力有较大余量(当然这是与计算宏观平均卷绕段张力而非动态瞬时纺纱张力比),纺纱处于正常状态,断头较少。
3、加捻卷绕形式与元件的创新
加捻卷绕形式与元件的创新伴随着环锭纺的技术进步。
以下以可资检索的专利信息为主要技术背景进行概要讨论。
3.1导纱钩
导纱钩的改良基本上围绕以下几个方面进行:
减小捻陷效应、降低张力波动对纺纱段的影响、降低毛羽、提高引纱操作的便利性、延长使用寿命。
表3是近十多年来有关导纱钩改良的典型专利申请。
表3:
专利名称
申请号
申请人
地域
主要特征
主要性能
附图
导纱钩
952159775
河北
板式导纱器
缩短接头时间提高工作效率
图1
一种细纱机导纱钩
972126260
河北
螺旋顺时针
向下
缩短接头时间提高工作效率
图2
导纱装置
012186430
台北
铝质导纱轮
降低毛羽50%
图3
细纱机
导纱钩
02234909x
天津
镶嵌式
组合结构
减少断头降低毛羽纱条运行平稳操作方便寿命长
图4
环锭细纱机导纱钩
032787340
江苏
特硬材质
抗磨性能好寿命长
图5
导纱钩
2004201223795
安徽
V形圆弧槽
集聚
降低毛羽15%
图6
导纱钩
2007200408834
江苏
NiCr材质,2.2mm孔径
抗磨性能好寿命长
图7
低毛羽率刚玉导纱钩
2008200282135
陕西
刚玉材质双迎纱与引纱曲面
减少断头降低毛羽50%纱条运行平稳操作方便寿命长
图8
其中,申请号为012186430(图3)和2008200282135(图8)的专利申请声称可以降低成纱毛羽达50%,如果商品化应用中也具有相近效果的话,则在没有其它附加成本的情况下,对成纱品质的改善是难能可贵的。
导纱钩上的导纱孔引导纱线以与锭子和钢令同心的方式进入气圈段,导纱孔是气圈段的起点。
对于导纱孔直径和导纱钩体直径的改良是适当缩小,较小的导纱孔直径可以减小气圈旋转时纱条在导纱孔中跳动的幅度,从而降低纺纱张力波动;较小的导纱钩体直径可以减小纱条与导纱钩的包围弧,从而减轻捻陷效应。
在纺纱角角度较小时,这样的改良效果较有效。
导纱钩上擒纱器(钩)的原始设计有两大功能:
断头擒纱和清纱擒纱。
断头擒纱即在气圈段或卷绕段发生断头时,纱条头端被离心力甩到擒纱钩上,曲绕在擒纱钩头端的刻槽处;清纱擒纱是纱条因特大粗节或结杂质量超重而使气圈膨大时擒纱钩切断并擒住。
第二个功能是早期的设计思路,随着络筒工序电子清纱和电脑在线监控技术的完善,笔者认为已无必要刻意设置导纱钩的清纱擒纱功能,因为主动切断头会影响劳动生产率。
应该适当上翘擒纱钩头端,保证纺纱纱路畅通,尽量降低断头率,特别是人为断头。
图1图2图3图4
图5图6图7图8
3.2气圈控制环
气圈控制环的应用已是一项成熟技术。
气圈控制环把一个大气圈分成两个小气圈后,每个气圈的高度减小了,纺纱张力也有所下降,并且有效避免了气圈波节的产生。
适应高速纺纱的细纱机在设计上就已考虑了除钢领板、导纱钩外的第三套气圈环专用独立随动升降结构,其可以在卷装升降的情况下,始终保持气圈环位于气圈直径最大处,从而更加合理有效地控制气圈形态。
而在普通细纱机上加装气圈环则只能在钢领板上通过安装支架加装。
3.3钢领附加环形导轨
钢领附加环形导轨(笔者简称)是奥地利申请人为改善钢丝圈运行状态而提出的技术方案,其有两项申请:
申请号为92104563.8专利名称为钢领旋转装置及申请号为93105612.8专利名称为环锭纺纱设备,该方案通过在钢领上部加装与钢领同心或接近同心的附加环形导轨,改变进入钢丝圈纱线与水平面之间的夹角α,使其成为一个锐角,从而使纱线对钢丝圈的作用合力抵消部分离心力,以便减轻钢领钢丝圈的磨损。
并以纱线与环形导轨的摩擦阻力替代部分钢丝圈与钢领的摩擦阻力,获得纺纱所需的张力。
同时纱线进入钢丝圈角度的改变也使钢丝圈的运行姿态得以改变,有利于改善钢丝圈运行稳定性。
实际应用时,由于环形导轨的内径小于钢领内径,因此只要α角大于管纱成形半角r/2的补角(管纱肩部表面斜面与水平面的夹角),就可以完成正常纺纱卷绕,但接头的拔管无法进行,除非纺制直径小于环形导轨内径的管纱或设置环形导轨移除的结构。
图9图10
3.4钢领钢丝圈
无论对于设计、应用或改良,钢领与钢丝圈都是成对配套进行的。
目前用于生产实践的主要为平面钢领和锥面钢领两种形式,平面钢领占绝对多数。
锥面钢领诞生于二十世纪七十年代。
作为实现高速、大卷装的主要措施之一,锥面钢领的主要特点是钢领内跑道的几何形状为近似双曲线的直线部分,配套的钢丝圈几何形状为非对称形,内脚长,与钢领内跑道近似直线接触,接触面积大、压强小,可减少磨损与增大散热面积,钢丝圈运行平稳,有利于降低细纱断头。
钢领钢丝圈的改良主要围绕适于高速、降低断头、延长寿命和改善品质影响进行,改良的内容主要为两个方面:
一是形态结构;二是材质和表面处理。
3.4.1钢领钢丝圈形态结构
钢领钢丝圈形态结构改良的着力点在于优化跑道形态、增大钢领钢丝圈间的接触面积,改善运行平稳性、抗楔性和散热性能。
表4摘录二十多年来钢领钢丝圈形态结构相关技术的专利申请。
表4:
专利名称
申请号
申请人
地域
主要特征
主要性能
附图
耐用节电钢领钢丝圈
85205004
上海
内跑道多曲面支承弧面
节电3%,钢领延寿2倍,钢丝圈延寿1倍
图11
托力轨道平面钢领
90102935.1
上海
外凸缘颈壁设有托力轨道面
线速度达每秒42-50米,断头率低,寿命长,品质好
图12
下支承多点接触钢领和钢丝圈
92102070.8
辽宁
包括有辅助支承面直线和上支承面直线的主跑道曲线
断头率降低25-35%,抗锲性好,钢领寿命长2-4倍,钢丝圈寿命长1-3倍,运行稳定,挂花率低50%
图13
新型钢领
95205840.5
湖北
上沿轨道向外倾斜32-38度
改善质量,减少磨损,延长寿命长1倍
图14
分别制造跑道及底座且将二者合为一体的钢领
03134348.1
陕西
跑道用硬质合金粉末冶金注射成形制造
成本低,寿命长
图15
通道隔离式钢丝圈
200720193727.1
山东
内脚设有隔离式纱线通道
纱线与钢丝圈摩擦阻力小,毛羽少,寿命长
图16
平面钢领用钢丝圈
200520023668.4
河北
内外脚相对于主体以相反方向折弯一个相等角度
纱线通畅,减小摩擦阻力,运行稳定,重心低,寿命长
图17
环锭纺纱机(锥面钢领)
9510074.8
瑞士
内跑道带有弧面的锥面钢领
改善质量,降低断头,钢领钢丝圈磨损小寿命长
图18
带有倾斜平面钢领的环锭纺纱机
95106457.6
瑞士
较小纱线通道GDL=0.1-0.3的钢领钢丝圈
利用纱条毛羽产生润滑膜改善润滑性,
特别适于紧密纺
图19
顶边锥面钢领和钢丝圈
01280134.8
山西
顶边平直的平台,外边设有上支承跑道,钢丝圈设有弓形纱线通道
接触面大,受力均匀,运转平稳,磨损少,寿命长
图20
新型钢领
03239741.0
天津
钢领上部锥形,双曲率支撑面,瓦楞型钢丝圈
张力稳定,断头率低,加捻效率高,毛羽少,强力高
图21
锥面钢领
200320120492.5
江苏
内跑道设有圆弧过渡磨损面
使用寿命长,开机断头少
图22
在国内外钢领钢丝圈形态结构的改良方面,锥面钢领结构或类锥面结构的专利案例所占比例较大,说明较多的改良取向是针对增大钢领钢丝圈接触面积、降低运动副接触压强。
但锥面钢领的实际应用不多,没有形成发展趋势。
图11图12图13图14
图15图16图17图18
图19图20图21图22
3.4.2钢领钢丝圈的材质和表面处理技术
钢领钢丝圈的材质和表面处理技术主要改善运动副接触摩擦性能为主,如耐磨性、润滑性、抗疲劳性等,其中表面处理技术主要包括表面改性技术、涂镀技术和薄膜技术。
以下摘录二十多年来钢领钢丝圈材质和表面处理相关技术的专利申请:
湖北申请人申请号为86201962 名称为镀铬钢领的专利申请公开了一种早期的钢领镀层方案:
钢领表面经特殊处理和探索铬原子生核规律、改变镀硬铬工艺,选择合理的电流密度等参数,获得晶粒细小光洁、结合牢度好的镀铬钢领。
上海申请人申请号为87105949.5名称为纺纱粉冶钢领材料及制造方法的专利申请公开了一种用于制造纺纱粉冶钢领的Fe-Mn-Mo-C四元合金及制造方法。
由于合