机床主轴的振动的有限元模态分析.docx
《机床主轴的振动的有限元模态分析.docx》由会员分享,可在线阅读,更多相关《机床主轴的振动的有限元模态分析.docx(35页珍藏版)》请在冰豆网上搜索。
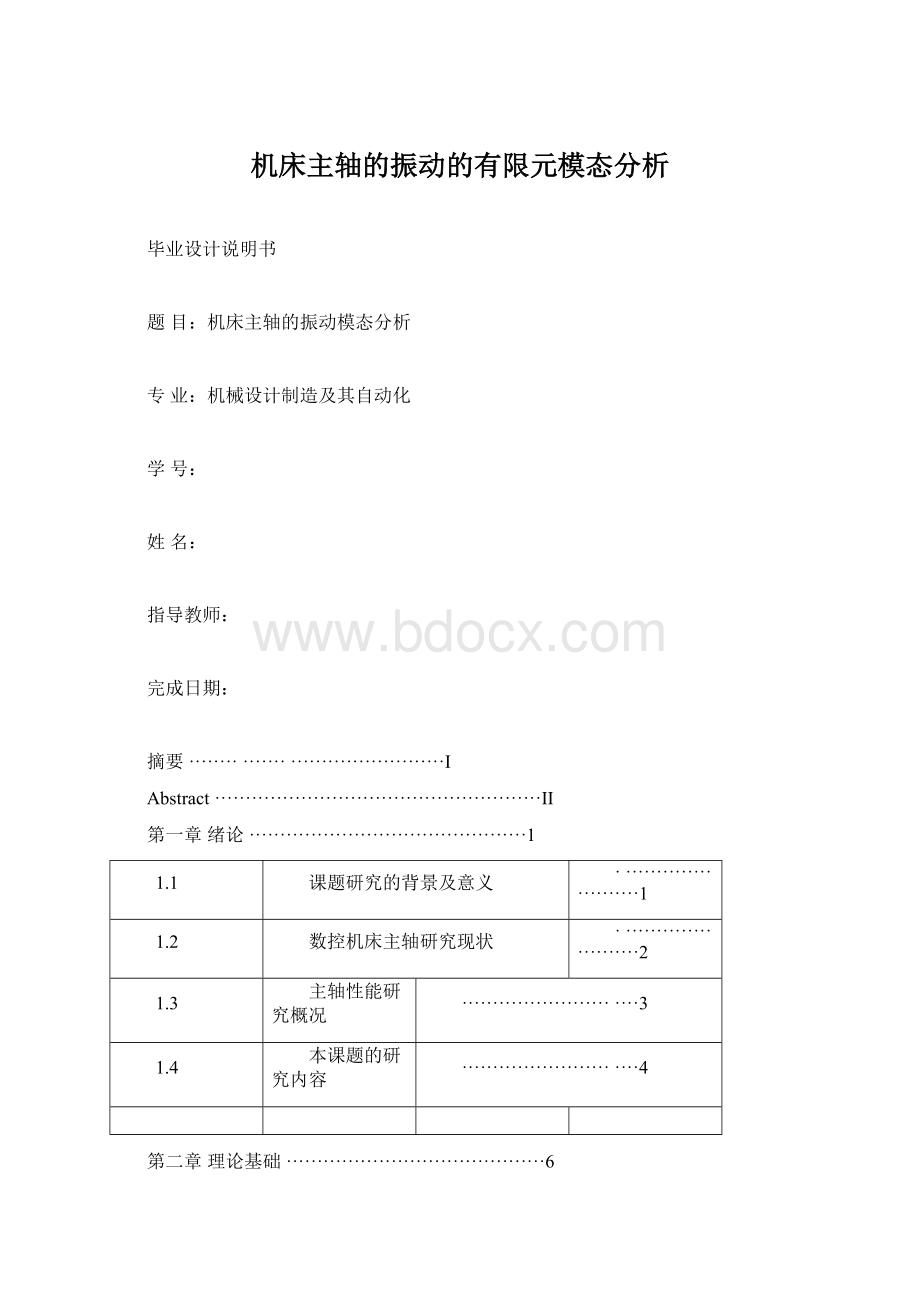
机床主轴的振动的有限元模态分析
毕业设计说明书
题目:
机床主轴的振动模态分析
专业:
机械设计制造及其自动化
学号:
姓名:
指导教师:
完成日期:
摘要········································I
Abstract·····················································II
第一章绪论·············································1
1.1
课题研究的背景及意义
·························1
1.2
数控机床主轴研究现状
·························2
1.3
主轴性能研究概况
····························3
1.4
本课题的研究内容
····························4
第二章理论基础··········································6
2.1模态分析理论·································6
2.2本章小节································10
第三章机床主轴的有限元分析······························11
3.1有限元简介及ANSYS软件应用·····················11
3.1.2ANSYS软件应用························12
3.1.2.1ANSYS的线性静力分析·················12
3.1.2.2分析步骤··························12
3.2机床主轴有限元分析模型·······················12
3.2.1构建几何模型··························12
3.2.2有限元模型建立··························13
3.2.3单元类型选择和网格划分·····················14
3.3机床主轴振动模态分析························16
3.3.1ANSYS动力分析························16
3.3.2模态分析·······························17
3.4本章小结··············································21
结论·······································22
参考文献···································23
致谢·······································24
附录一英文文献翻译
附录二英文文献原件
机床主轴振动的有限元模态分析
摘要:
机床发展日益朝向高速度和高精度的方向发展,这对机床的设计提出了更高的要求,需要
采用更加先进和合理的设计方法来完成机床设计。
作为一种先进的设计手段,动态设计方法已经成
为企业提高竞争力的重要方面。
要进行动态设计,前提是对机床的动态性能作出正确的分析。
主轴
是数控机床的重要组成部分,其动态特性的好坏对机床的性能有着重要的影响。
因此,对主轴部件
进行动态特性分析十分必要。
为了提高机床的设计水平,将现代化的设计方法应用于机床的设计,
主要是对现有数控机床CKS6125主轴振动进行模态分析,为进一步进行动态设计打基础。
本文态参数,识别原理;
(1)简要论述了有限元方法和动力学分析的基本求解过程,建立机床主轴有限元模型,合理的
确定了载荷、轴承支承刚度和约束条件,选定了单元类型。
采用Lanczos法对其进行自由模的具体
研究内容;
(2)总结了机床、动态设计方法研究和机床主轴动静态研究的发展状况和发展趋势,在总结前人
研究成果的基础上,结合当前的技术发展趋势,采用有限元方法来进行开展研究;
(3)简要论述了模态分析,得到主轴的固有频率和振型,找出工作时容易发生共振的频率域
为进一步提高精度和转速提供理论依据。
关键词:
有限元分析;模态分析;机床主轴;振动
Spindlevibrationmodalanalysis
byfiniteelementmethod
ABSTRACT
High-speedandhigh-accuracyarethetrendsindevelopmentofmachinetool,weneedtouseadvancedandappropriatemethodtodesignmachinetool.Asawaytoimproveenterprise'scompetitivepower,thedynamicdesignmethodhasbeenplayedanimportantrole.Theanalysisofdynamicperformanceisthepremiseofdynamicdesign.SpindleisakeypartofCNCmachine;itsperformancewillaffectthemachine'sperformanceandqualityofworkpiecemostly.Itsdynamiccharacteristicisanimportantinfluenceforthefunctionofthetoolmachine.ToimprovedesignlevelanduseadvanceddesignchoseMachineToolsCKS6125todostudyondynamicperformanceandapplication.ThepaperisbasedonthestudyandthemainlyworkisstudyondynamicperformanceofMachineTool'sSpindlewhichcanprovideafoundationfordynamicdesign.
Thecontentsare:
(1)Inthepaper,thedevelopmenttrendsofmachinetoolanddynamicdesignaresummarized.AndtheFEAmethodsaretakentouse.
(2)Thebasicresolvingprocessesaboutthemodalparametersidentifiertheory.
(3)Thebasicresolvingprocessesaboutstaticanalysisandkineticanalysis.Thesolidmodelofspindleisestablished.Duringthebuildingofthemodel,theloadonthespindle,thesupportingstiffnessofbearing,theboundaryandelementsareanalyzedcorrectly.ThemodalfrequencyandmodalshapecharacteristicsareobtainedbyFEMmodalanalysiswiththeLanczosmethod.Andthefrequencyregionoftheresonanceinworkisobtained.Itprovidestheoreticalbasisforpromotingtheprecisionandrotationalspeedofthespindleparts.
Keywords:
FiniteElementMethod;ModalAnalysis;Spindle;vibration
II
第一章绪论
1.1课题研究的背景及意义
制造业是体现一个国家综合实力的重要方面,是国家财富的主要创造者世界上凡是发达国家都拥有高水平的制造业。
而装备制造业作为整个国家工业部门的装备提供者,
其水平的高低决定了我国制造业的国际竞争力,特别是我国加入到WTO以后,行业竞争更加激烈,已经关系到我们国家现代化的进程和民族的复兴,因此提高我国装备制造业的整体技术水平具有重大的理论和现实意义。
在当前的振兴过程中,我们应该清醒的认
识到我国装备制造业和发达国家的差距,不能只看到眼前的一时繁荣。
特别是机床行业,在设计水平上与发达国家有着比较大的差距,缺少创新和突破,掌握核心技术较少,特
别在高端的产品领域,竞争力还不够强大。
同时由于工业、农业、国防与科学技术的发展,对机械设备提出了越来越高的要求,同时现代产品的更新速度比较快,为了提高产品的市场竞争力,就要缩短产品生产设计周期,提高产品设计的水平。
为了实现这个要求,要求产品设计人员在产品物理样机设
计完成后,在产品的物理样机制造出来之前,能够对产品的各项性能进行评价,了解和掌握产品的静动态性能,从而可以在产品投产之前对设计进行修改和结构优化,提高设计的成功率和产品质量。
动态设计就是机械结构和机器系统的动态性能在图纸设计阶段就得到预测和优化,整个设计过程实质上是运用动态分析技术,借助计算机辅助设计和计算机辅助分析的方法来实现的。
长期以来,国内的机床设计多为经验模拟设计,结构设计计算沿用传统的计算方法,如材料力学、结构力学以及弹性力学的一些公式进行计算。
这些公式的推导多以强度方面的理论为主,辅以实验和测试方法得出,具有一定的可靠性。
但由于机床结构的复杂,计算过程中的数学模型对结构进行了许多简化,导致了计算的精度差异较大。
同时凭借简单的计算工具,计算繁冗,时间很长,有些项目无法计算。
因此,利用传统的模拟设计方法进行机床设计虽然可以对机床或某些组成的零部件进行综合或者
部分的技术性能实验,但是受实验手段和方法的限制,还不能够进行深入的研究,从而根本上也谈不上优化设计以及动态设计,多为“设计——制造——修改设计——制造”周期循环,有些甚至经过几代才可能形成比较好的产品,费时费力,效率低下。
动态设计的原则:
目标是保证机械满足其功能前提要求的条件下具有较高的动刚度,使其经济合理、运转平稳、可靠。
要从总体上把握机械结构的固有频率、振型和阻尼比。
具体为:
避开共振,避开率应在15%-20%;降低机器运行过程中的振动幅度;结构各阶模态刚度最大且尽量相等;结构的各阶模态阻尼比要尽量高;避免结构疲劳破坏;提高振动稳定性。
设计步骤:
1
(1)建立机械结构或机械系统的动力学模型,根据设计图纸建立力学模型,也可以应用试验模态分析技术建立结构的试验模型;
(2)利用数学模型求解自由振动方程得到结构振动的固有特性,引入外部激励可以进行动力响应分析;
(3)动态性能评定;
(4)结构修改和优化设计[1]。
1.2数控机床主轴研究现状
我国数控技术的开发始于1958年,几乎与国外同时起步。
但由于自身技术的落后,研制进展十分缓慢。
但“九五”以来,我国机床在关键技术的突破上主要表现在以下方面:
(1)数控系统网络化、集成化。
应用PC机开发出了8轴联动,可控48轴的分布式数控系统,以及可靠性达到15000小时的高分辨率数控系统。
(2)实现了高速主轴、快速进给、高速换刀机构的“三高”技术的突破。
国产加工中心的主轴转速可以达到1万~1.2万rpm,快速进给一般都能达到30~40m/min。
(3)静压技术、精密传动技术的突破,有效地提高了重型机床的主轴精度和定位精度。
如武汉重型机床厂和齐齐哈尔第一机床厂开发的精密双齿轮条传动系统,大大消除了齿轮传动间隙,提高了传动精度。
在机床主轴转速方面,我国取得了长足的进步,
但与国外的差距还是很大。
在80年代之前,我国机床主轴转速一般都不到2000rpm。
进入90年代,机床厂商和各高校都加紧了新产品的研制。
国内有些厂家也生产出转速
上5000rpm。
如:
上海明精机床公司生产的2HM-007/25T型高速数控车床,主轴最高转速7500rpm;南京机床厂生产的CK1416/12、1425/34型高速数控车床,主轴最高转速
6000rpm;上海肯信精密机器制造有限公司生产的KSJM6130C/6132C型高速精密数控车
床最高转速也是5000rpm。
在国际上,数控机床高速化发展也经历了几个过程,其如表1-1所示。
表1-1数控机床高速化发展过程
时间
60年代
70年代
80年代
90年代
21世纪初
主轴转速(rpm)
1000-2000
2000-4000
2000-6000
4000-10000
10000-15000
主轴是数控机床的关键部件,在其前部安装工件、刀具,直接参与切削加工,对机床的加工精度,工件表面质量和生产效率有很大的影响,其性能的好坏将对机床的最终性能和加工工件的质量有非常重要的影响。
据研究表明中型车床在不同频率的动载荷作用下,各个部件反映在刀具与工件切削处的综合位移中主轴部件所占比例最大,未处于共振状态下占30%-40%,共振状态下占60%-80%[2]。
2
对于数控机床的主轴部件常用的结构主要有以下几种形式:
(1)对于高速高精度机床,为了实现高的主轴转速,采用主轴电机结构;
(2)对于中等要求的数控机床,采用主轴电机,驱动经过减速机构驱动(采用齿轮传动和同步带传动)的专用主轴生产厂生产的主轴;
(3)对于一般的数控机床(经济型数控机床),采用交流电机经过皮带传动,再经过
主轴变速箱体(其结构与普通机床的主轴箱有很大的不同)实现主轴的变速[3]。
数控机床的主传动无论采用上面那种结构,设计人员都应该非常重视主轴部件的设
计和机床主轴部件的动态性能。
采用传统的设计方法,在机床的物理样机制造出来之前,
人们不能准确知道机床及其主轴部件的动态性能,需要制造出物理样机通过试验来确
定,一旦设计达不到要求性能,一切需要重来。
近年随着计算机及其相关软硬件技术的发展促进了虚拟样机技术的快速发展,同时
成熟的CAE建模和分析软件技术使产品动态设计成为可能。
1.3主轴性能研究概况
机床主轴的动静态特性主要就是固有频率、受力变形、临界转速、动态响应等,由
于其重要性,国内外的才昆多单位和研究机构很早就开始了机床动态设计的相关研究工
作,也获得一系列的成果。
在60年代以前,一般采用经验模拟法设计,方法繁琐,精度低。
60年代以后由于
计算机技术和计算方法的进步,出现了有限差分法、结构分析法、有限元法、结构修正法,模态法等大量方法。
在国外,1964年,Bollinger将轴承模拟为一个简单的径向弹簧和阻尼器,采用有限差分模型分析了车床主轴的特性[4]1985年Red即和Sharan应用有限元模型研究车床主轴的动态特性及其设计[5]。
1988年Sadeghipor将动柔度分析引人对主轴系统的动力特性和动态设计的研究之中[6]。
1992年,Spur.G等利用结构修正法分析了切削机床的主轴一
轴承的静态和动态性能,但只是考虑轴承径向一个自由度,并且忽略了轴向、力矩方向
的自由度,更忽略了轴承刚度的非线性[7]。
1997年,美国普渡大学的Bert.R.Jorgensen
和、ixng.C.Shin推出了一个包括热变形的轴承载荷一变形模型,并与离散的主轴动态模
型结合在一起,这一模型可以得到主轴固有频率、轴承刚度和热变形较好的计算值[8]。
同年,Tsutsumi等人研究了滚动轴承的动态性能对主轴振动特性的影响。
Yhland建立了
仅受球轴承几何缺陷激励的无阻尼主轴——轴承系统的线性分析模型,该模型在主轴的中、低速有效[9]。
而国内从事这一领域研究的也很多,特别是早期对普通主轴动特性的研究。
1992年,江苏工学院的付华应用试验模态分析与有限元计算相结合的方法,对传统主轴部件进行
3
了动力特性分析,并对主轴进行了动力修改[10]。
1994年,大连理工大学的肖曙红用有
限元结合迭代的分析方法,编制了主轴组件静、动特性分析软件SAAS[11]。
1999年,北
京工业大学的费仁元等采用实验方法对复杂的主轴部件进行了动态特性分析[12]。
2000
年,沈阳工业学院的史安娜等对主轴部件建立了空间梁单元模型,并在此基础上对其静
动态特性进行了分析[13]。
同年,北京理工大学的刘素华利用有限元分析软件
ALGORFEAS对电主轴的动静态特性进行了分析[14]。
2001年,杨曼云等利用MSC.
Nastran软件对TH6350卧式加工中心的主轴系统进行了静、动态特性分析[15]。
武汉理
工大学的杨光等利用传递矩阵法对电主轴系统进行了动力学特性分析[16]。
2003年,无
锡机床股份有限公司的蔡英等基于Riccatti传递矩阵法,对MK2120A型内圆磨床的高速主轴系统进行了动力学特性分析[17]。
从国内外研究的情况看,对高速主轴的一些基本特性都被人们所认识,高速主轴的静刚度,热特性,高速轴承特性等都逐渐被人们所掌握。
但是,数控机床的高速化不是
简单分析零件就能行的。
提升主轴的转速是要综合分析主轴部件,特别是要掌握主轴与主轴箱的固有特性,即二者的振动频率,阻尼比等参数。
只有系统的对主轴和主轴箱的静、动态特性分析,才能全面掌握影响主轴部件转速的因素。
本课题就是要研究机床主轴的动静态特性,由上述各文献所总结的经验可知,其主要任务是计算轴承的刚度、建立合理有效的模型,特别是轴承部分的简化,再对模型进行静变形、模态及响应等各方面的分析,得到固有频率、振型等参数。
其中轴承刚度的计算较复杂,静刚度可用经验公式计算得出;而动刚度的计算部分则要考虑主轴高速运
转条件下对轴承的影响,目前在国内还未见到简便有效的计算方法,本文做了初步讨论。
1.4本课题的研究内容
本课题采用ANSYS有限元软件来分析主轴的动静态特性。
ANSYS软件是一个应用
广泛的工程有限元分析软件,主要是利用有限元法将所探讨的工程系统转化成一个有限
元系统,该有限元系统由节点及元素所组合而成,以取代原有的工程系统,有限元系统
可以转化成一个数学模式,并根据该数学模式得到该有限元系统的解答,且可以通过节
点、元素把结果表现出来。
完整的有限元模型除了节点、元素外,还包含工程系统本身
所具有的边界条件,如约束条件、外力的负载等。
利用ANSYS有限元软件对主轴进行静、动态特性分析,确定合理的边界条件,改
善主轴部件的静动态特性,并采用合理的数学建模方法进行对比分析,最后以沈阳机床
一厂生产的CKS6125型数控车床为研究对象,检验前面进行的理论分析,从而得出合
理的设计方法,为实现产品的动态设计打下基础。
具体工作分为以下几个部分:
4
(1)总结了机床、动态设计方法研究和机床主轴动静态研究的发展状况和发展趋势,
在总结前人研究成果的基础上,结合当前的技术发展趋势,采用有限元方法来进行开展
研究;
(2)阐述学习理论基础,即振动理论(模态分析理论),简要论述了模态参数,识别原理;
(3)简要论述了有限元方法和动力学分析的基本求解过程,建立机床主轴有限元模
型,合理的确定了载荷、轴承支承刚度和约束条件,选定了单元类型。
采用Lanczos法
对其进行自由模态分析,得到主轴的固有频率和振型,找出工作时容易发生共振的频率域,为进一步提高精度和转速提供理论依据。
5
第二章理论基础
在对运动系统的结构动力学特性研究中,模态分析是近年来被广泛采用的一种研究手段。
它的主要方法是将耦合的运动方程组解耦成为相互独立的方程,通过求解每个独
立的方程得到各模态的特性参数,进而就可以用所求得的模态参数来预测和分析该系统的运动特性等[18]。
由于首先通过线性坐标变换的方法解耦运动方程,所以对于求解多自由度系统的运动方程,模态分析具有其他计算方法所不能替代的优势。
数控机床主轴是
形状不规则的多自由度系统,本文采用模态分析的方法研究它们的结构动力学特性。
模态分析的具体研究方法根据其手段的不同主要分为两种:
基于有限元法的计算模态分析和基于测试技术的实验模态分析。
2.1模态分析理论
模态分析的理论是在机械阻抗与导纳的概念上发展起来的。
近十余年来,模态分析理论吸取了振动理论、信号分析、数据处理、数理统计以及自动控制理论的知识,形成
了一套独特的理论,它已经成为近年来应用于结构动力学研究的重要方法[19]。
模态分析的基本原理是:
将线性定常系统振动微分方程组中的物理坐标变换为模态坐标,使方程组解耦,成为一组以模态坐标及模态参数描述的独立方程,以便求出系统的模态参数。
坐标的变换矩阵为模态矩阵,其每一列为模态振型。
由振动理论,系统任一点的响应均
可表示为各阶模态响应的线性组合。
因而,通过求出的各阶模态参数就可以得到任意激
励下任意位置处的系统响应。
模态分析的最终目标是识别出系统的模态参数,为结构系
统的振动特性分析、振动故障诊断和预报以及结构动力学特性的优化设计提供依据。
工
程中较复杂的振动问题多为象机床主轴箱这样的多自由度系统。
对于多自由度系统利用
矩阵分析方法,N自由度线性定常系统的运动微分方程为:
...
MXCXKXF
(2-1)
其中,M,C,K分别表示系统的质量、阻尼和刚度矩阵
(均为N×N阶矩阵),X,F表示
系统各点位置上的位移响应和激励力向量。
x1
f1
X
x2
F
f2
(2-2)
xnfn
...
方程(2-1)中是用各坐标点的位移、速度和加速度(X,X,X)描述的运动方程组,其中每一个方程中均包含了系统的各个物理坐标点的影响,所以是耦合的运动方程。
对
6
于耦合的运动方程,当系统的自由度数比较大时,要对其求解是非常困难的。
模态分析
的基本思想就是对这样耦合的运动方程进行解耦,使其变成为非耦合的、独立的运动微
分方程组。
对(2-1)式两边进行拉氏变换,得到
(s2MsCK)X()s(F)s
(2-3)
式中的拉氏因子:
s
j