毕业设计机床主轴的振动的有限元模态分析.docx
《毕业设计机床主轴的振动的有限元模态分析.docx》由会员分享,可在线阅读,更多相关《毕业设计机床主轴的振动的有限元模态分析.docx(23页珍藏版)》请在冰豆网上搜索。
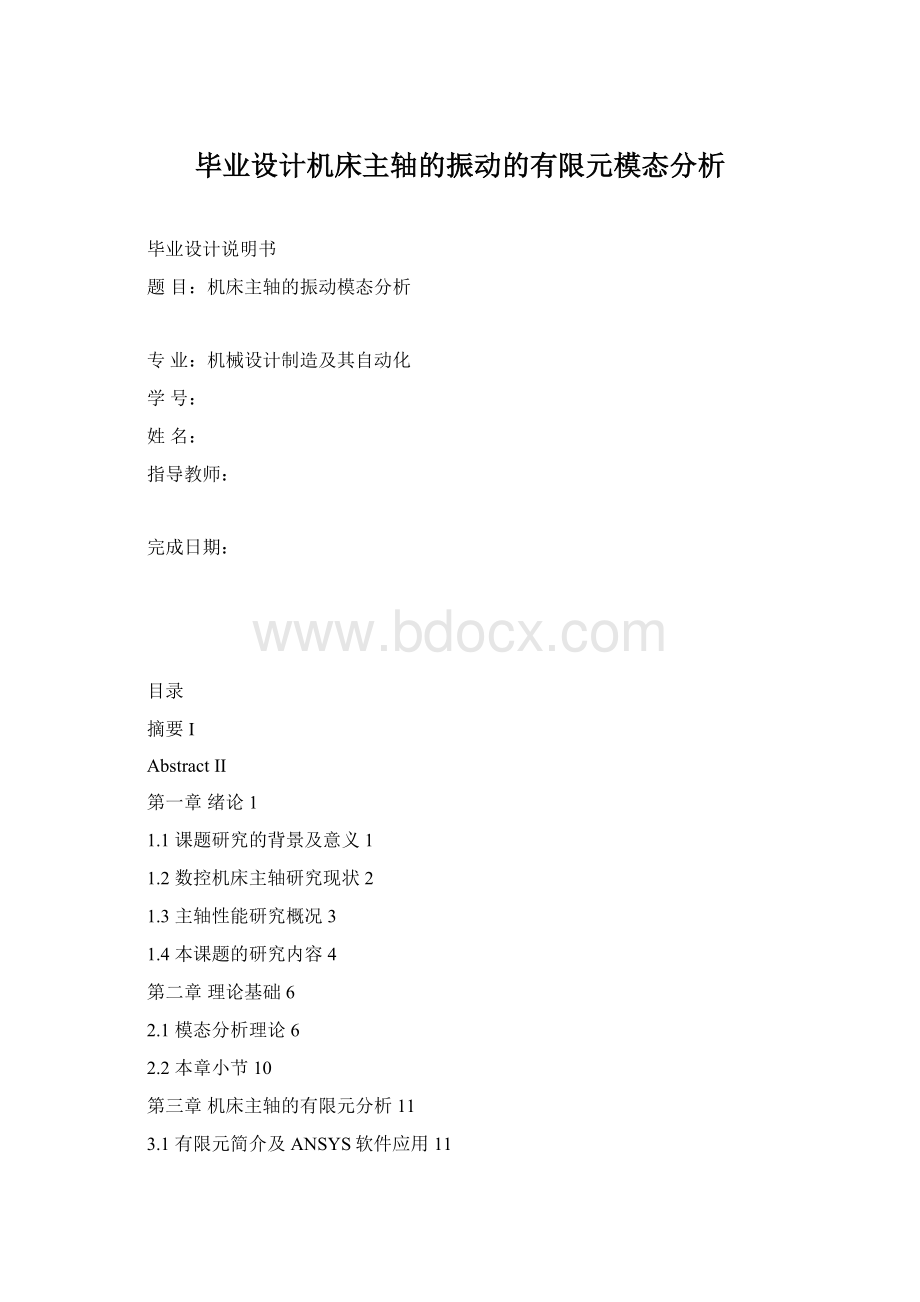
毕业设计机床主轴的振动的有限元模态分析
毕业设计说明书
题目:
机床主轴的振动模态分析
专业:
机械设计制造及其自动化
学号:
姓名:
指导教师:
完成日期:
目录
摘要I
AbstractII
第一章绪论1
1.1课题研究的背景及意义1
1.2数控机床主轴研究现状2
1.3主轴性能研究概况3
1.4本课题的研究内容4
第二章理论基础6
2.1模态分析理论6
2.2本章小节10
第三章机床主轴的有限元分析11
3.1有限元简介及ANSYS软件应用11
3.1.2ANSYS软件应用12
3.1.2.1ANSYS的线性静力分析12
3.1.2.2分析步骤12
3.2机床主轴有限元分析模型12
3.2.1构建几何模型12
3.2.2有限元模型建立13
3.2.3单元类型选择和网格划分14
3.3机床主轴振动模态分析16
3.3.1ANSYS动力分析16
3.3.2模态分析17
3.4本章小结21
结论22
参考文献23
致谢24
附录一英文文献翻译
附录二英文文献原件
机床主轴振动的有限元模态分析
摘要:
机床发展日益朝向高速度和高精度的方向发展,这对机床的设计提出了更高的要求,需要采用更加先进和合理的设计方法来完成机床设计。
作为一种先进的设计手段,动态设计方法已经成为企业提高竞争力的重要方面。
要进行动态设计,前提是对机床的动态性能作出正确的分析。
主轴是数控机床的重要组成部分,其动态特性的好坏对机床的性能有着重要的影响。
因此,对主轴部件进行动态特性分析十分必要。
为了提高机床的设计水平,将现代化的设计方法应用于机床的设计,主要是对现有数控机床CKS6125主轴振动进行模态分析,为进一步进行动态设计打基础。
本文态参数,识别原理;
(1)简要论述了有限元方法和动力学分析的基本求解过程,建立机床主轴有限元模型,合理的确定了载荷、轴承支承刚度和约束条件,选定了单元类型。
采用Lanczos法对其进行自由模的具体研究内容;
(2)总结了机床、动态设计方法研究和机床主轴动静态研究的发展状况和发展趋势,在总结前人研究成果的基础上,结合当前的技术发展趋势,采用有限元方法来进行开展研究;
(3)简要论述了模态分析,得到主轴的固有频率和振型,找出工作时容易发生共振的频率域,为进一步提高精度和转速提供理论依据。
关键词:
有限元分析;模态分析;机床主轴;振动
Spindlevibrationmodalanalysis
byfiniteelementmethod
ABSTRACT
High-speedandhigh-accuracyarethetrendsindevelopmentofmachinetool,weneedtouseadvancedandappropriatemethodtodesignmachinetool.Asawaytoimproveenterprise'scompetitivepower,thedynamicdesignmethodhasbeenplayedanimportantrole.Theanalysisofdynamicperformanceisthepremiseofdynamicdesign.SpindleisakeypartofCNCmachine;itsperformancewillaffectthemachine'sperformanceandqualityofworkpiecemostly.Itsdynamiccharacteristicisanimportantinfluenceforthefunctionofthetoolmachine.ToimprovedesignlevelanduseadvanceddesignchoseMachineToolsCKS6125todostudyondynamicperformanceandapplication.ThepaperisbasedonthestudyandthemainlyworkisstudyondynamicperformanceofMachineTool'sSpindlewhichcanprovideafoundationfordynamicdesign.
Thecontentsare:
(1)Inthepaper,thedevelopmenttrendsofmachinetoolanddynamicdesignaresummarized.AndtheFEAmethodsaretakentouse.
(2)Thebasicresolvingprocessesaboutthemodalparametersidentifiertheory.
(3)Thebasicresolvingprocessesaboutstaticanalysisandkineticanalysis.Thesolidmodelofspindleisestablished.Duringthebuildingofthemodel,theloadonthespindle,thesupportingstiffnessofbearing,theboundaryandelementsareanalyzedcorrectly.ThemodalfrequencyandmodalshapecharacteristicsareobtainedbyFEMmodalanalysiswiththeLanczosmethod.Andthefrequencyregionoftheresonanceinworkisobtained.Itprovidestheoreticalbasisforpromotingtheprecisionandrotationalspeedofthespindleparts.
Keywords:
FiniteElementMethod;ModalAnalysis;Spindle;vibration
第一章绪论
1.1课题研究的背景及意义
制造业是体现一个国家综合实力的重要方面,是国家财富的主要创造者世界上凡是发达国家都拥有高水平的制造业。
而装备制造业作为整个国家工业部门的装备提供者,其水平的高低决定了我国制造业的国际竞争力,特别是我国加入到WTO以后,行业竞争更加激烈,已经关系到我们国家现代化的进程和民族的复兴,因此提高我国装备制造业的整体技术水平具有重大的理论和现实意义。
在当前的振兴过程中,我们应该清醒的认识到我国装备制造业和发达国家的差距,不能只看到眼前的一时繁荣。
特别是机床行业,在设计水平上与发达国家有着比较大的差距,缺少创新和突破,掌握核心技术较少,特别在高端的产品领域,竞争力还不够强大。
同时由于工业、农业、国防与科学技术的发展,对机械设备提出了越来越高的要求,同时现代产品的更新速度比较快,为了提高产品的市场竞争力,就要缩短产品生产设计周期,提高产品设计的水平。
为了实现这个要求,要求产品设计人员在产品物理样机设
计完成后,在产品的物理样机制造出来之前,能够对产品的各项性能进行评价,了解和掌握产品的静动态性能,从而可以在产品投产之前对设计进行修改和结构优化,提高设计的成功率和产品质量。
动态设计就是机械结构和机器系统的动态性能在图纸设计阶段就得到预测和优化,整个设计过程实质上是运用动态分析技术,借助计算机辅助设计和计算机辅助分析的方法来实现的。
长期以来,国内的机床设计多为经验模拟设计,结构设计计算沿用传统的计算方法,如材料力学、结构力学以及弹性力学的一些公式进行计算。
这些公式的推导多以强度方面的理论为主,辅以实验和测试方法得出,具有一定的可靠性。
但由于机床结构的复杂,计算过程中的数学模型对结构进行了许多简化,导致了计算的精度差异较大。
同时凭借简单的计算工具,计算繁冗,时间很长,有些项目无法计算。
因此,利用传统的模拟设计方法进行机床设计虽然可以对机床或某些组成的零部件进行综合或者部分的技术性能实验,但是受实验手段和方法的限制,还不能够进行深入的研究,从而根本上也谈不上优化设计以及动态设计,多为“设计——制造——修改设计——制造”周期循环,有些甚至经过几代才可能形成比较好的产品,费时费力,效率低下。
动态设计的原则:
目标是保证机械满足其功能前提要求的条件下具有较高的动刚度,使其经济合理、运转平稳、可靠。
要从总体上把握机械结构的固有频率、振型和阻尼比。
具体为:
避开共振,避开率应在15%-20%;降低机器运行过程中的振动幅度;结构各阶模态刚度最大且尽量相等;结构的各阶模态阻尼比要尽量高;避免结构疲劳破坏;提高振动稳定性。
设计步骤:
(1)建立机械结构或机械系统的动力学模型,根据设计图纸建立力学模型,也可以应用试验模态分析技术建立结构的试验模型;
(2)利用数学模型求解自由振动方程得到结构振动的固有特性,引入外部激励可以进行动力响应分析;
(3)动态性能评定;
(4)结构修改和优化设计[1]。
1.2数控机床主轴研究现状
我国数控技术的开发始于1958年,几乎与国外同时起步。
但由于自身技术的落后,研制进展十分缓慢。
但“九五”以来,我国机床在关键技术的突破上主要表现在以下方面:
(1)数控系统网络化、集成化。
应用PC机开发出了8轴联动,可控48轴的分布式数控系统,以及可靠性达到15000小时的高分辨率数控系统。
(2)实现了高速主轴、快速进给、高速换刀机构的“三高”技术的突破。
国产加工中心的主轴转速可以达到1万~1.2万rpm,快速进给一般都能达到30~40m/min。
(3)静压技术、精密传动技术的突破,有效地提高了重型机床的主轴精度和定位精度。
如武汉重型机床厂和齐齐哈尔第一机床厂开发的精密双齿轮条传动系统,大大消除了齿轮传动间隙,提高了传动精度。
在机床主轴转速方面,我国取得了长足的进步,但与国外的差距还是很大。
在80年代之前,我国机床主轴转速一般都不到2000rpm。
进入90年代,机床厂商和各高校都加紧了新产品的研制。
国内有些厂家也生产出转速上5000rpm。
如:
上海明精机床公司生产的2HM-007/25T型高速数控车床,主轴最高转速7500rpm;南京机床厂生产的CK1416/12、1425/34型高速数控车床,主轴最高转速6000rpm;上海肯信精密机器制造有限公司生产的KSJM6130C/6132C型高速精密数控车床最高转速也是5000rpm。
在国际上,数控机床高速化发展也经历了几个过程,其如表1-1所示。
表1-1数控机床高速化发展过程
时间
60年代
70年代
80年代
90年代
21世纪初
主轴转速(rpm)
1000-2000
2000-4000
2000-6000
4000-10000
10000-15000
主轴是数控机床的关键部件,在其前部安装工件、刀具,直接参与切削加工,对机床的加工精度,工件表面质量和生产效率有很大的影响,其性能的好坏将对机床的最终性能和加工工件的质量有非常重要的影响。
据研究表明中型车床在不同频率的动载荷作用下,各个部件反映在刀具与工件