中密度纤维板课程设计.docx
《中密度纤维板课程设计.docx》由会员分享,可在线阅读,更多相关《中密度纤维板课程设计.docx(14页珍藏版)》请在冰豆网上搜索。
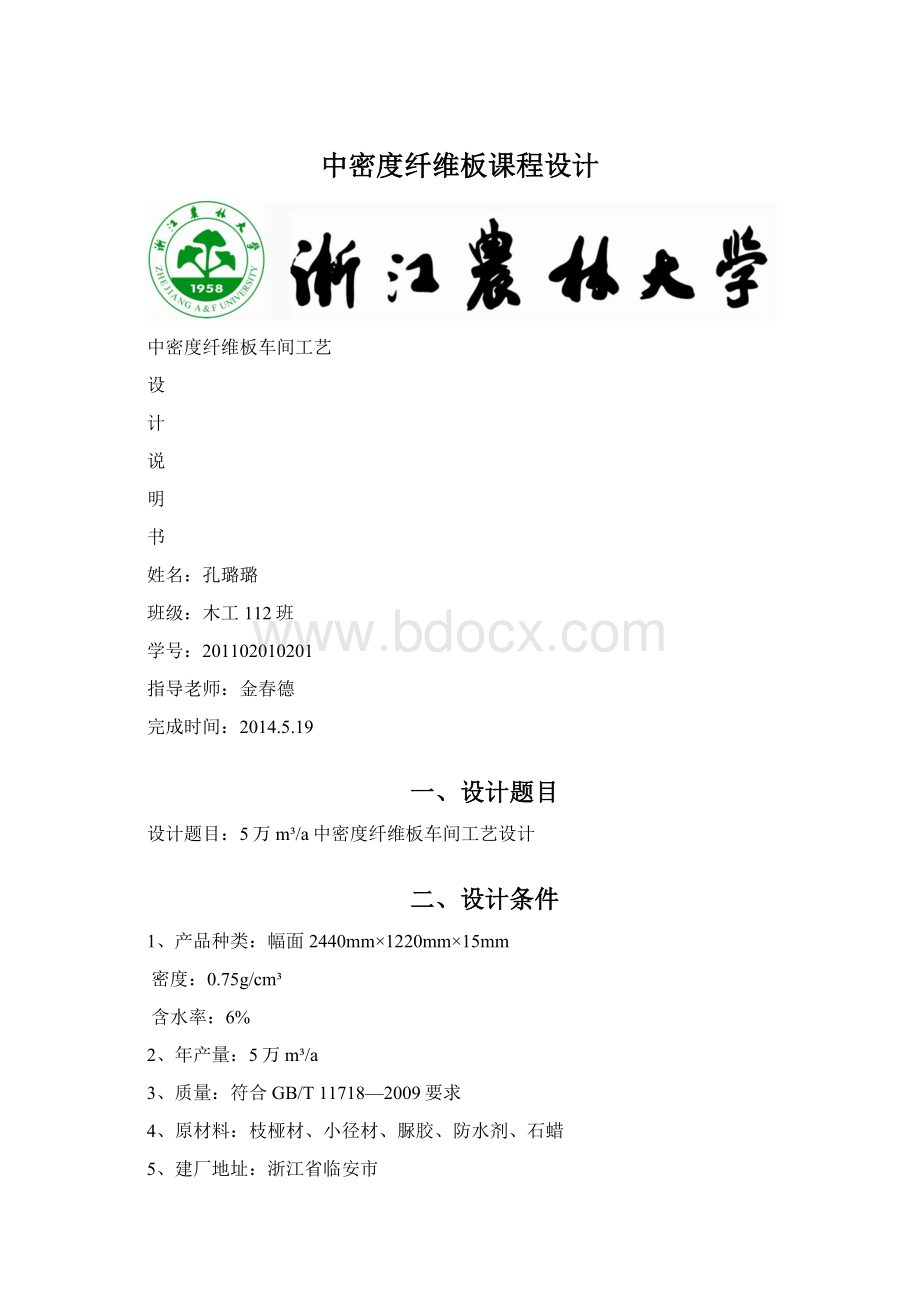
中密度纤维板课程设计
中密度纤维板车间工艺
设
计
说
明
书
姓名:
孔璐璐
班级:
木工112班
学号:
201102010201
指导老师:
金春德
完成时间:
2014.5.19
一、设计题目
设计题目:
5万m³/a中密度纤维板车间工艺设计
二、设计条件
1、产品种类:
幅面2440mm×1220mm×15mm
密度:
0.75g/cm³
含水率:
6%
2、年产量:
5万m³/a
3、质量:
符合GB/T11718—2009要求
4、原材料:
枝桠材、小径材、脲胶、防水剂、石蜡
5、建厂地址:
浙江省临安市
6、工作制度:
年工作日280天、3班(削片2班)
三、设计内容
1、确定实际年产量
(1)确定热压周期
根据工艺要求,15mm厚的MDF成品板,热压周期选为7.5min。
(2)确定压机层数
n=
=
=11.3(层)
式中:
Q——年产量,m³;T——热压周期,min;
L——板净长,取4.88m;a——板净宽,取1.22m;
b——板净厚,取0.015m;k——压机利用系数,取0.98;
d——年工作时,取280d;
k′——压机有效工作时间,取0.94×24(h)
由上式计算结果取整为n=12(层),则年产量为:
Q=
=
=53071.99(m³/a)
考虑工程预留量10%,则年产量为58379.19m³/a,取产品合格率为98%,则实际压机层数为:
n=
=13.47(层)
选用14层幅面为1680mm×5180mm×125mm的多层压机1台(瑞典SUNDS公司Motala压机)。
(3)确定设计年产量
按14层计算,年产量为:
Q=
=61917.32(m³/a)
扣除不合格产品和工程预留量,则设计年产量为Q1=61917.32×(100%-12%)=54487.25(m³/a),则日产量为194.60m³/d,大于设计要求给定的计划产量。
2、工艺流程
根据设计任务书的要求与目前国内常用生产工艺,确定工艺流程。
详见下图。
3、原材料消耗量的计算
1m³板重:
1×0.75=0.75(t)
扣除水分后重:
0.75×(100%-6%)=0.705(t)
1m³板所需消耗的原材料量计算如下:
设1m³板所消耗的绝干纤维量为G
则成板所需辅助材料量为:
胶量=0.6357×10%=0.06357(t)
蜡量=0.6357×0.8%=5.0857(kg)
固化剂=0.6357×10%×1%=0.6357(kg)
4、生产1m³MDF原材料损失量计算
(1)砂光损失量
每张板两面砂去1.5mm
每张板体积:
2.44×1.22×0.015=0.04465(m³)
砂光损失量:
2.44×1.22×0.0015×0.75=0.003349(t)
1m³板损失量:
0.003349/0.04465=0.075(t)
扣除水分后:
(t)
损失率:
0.0705/0.75=0.094
其中:
绝干纤维量:
0.0705/(1+10%+0.8%+10%×1%)=0.06357(t)
胶量:
0.06357×10%=0.006357(t)
蜡量:
0.06357×0.8%=5.0857×
(t)
固化剂量:
0.06357×10%×1%=0.00006357(t)
而砂光前原料量为:
0.0705+0.075×0.94=0.7755(t)
(2)裁边损失量
设板坯的规格为:
(宽×长)1290mm×4980mm
则裁边损失率为:
×100%=7.3%,取8%则:
裁边损失量:
(t/m³)
而
故
=0.06081(t/m³)
胶量:
0.06081×10%=0.006081(t/m³)
蜡量:
0.06081×0.8%=0.00048645(t/m³)
固化剂量:
0.06081×10%×1%=0.00006081(t/m³)
裁边前的原料量为:
0.7755+0.06743=0.84293(t/m³成板)
(3)预压到热压段损失率设为0.5%。
此段主要是横截,其次是预压及热压时气流带走的纤维量极少。
损失量:
(t/m³)
预压前原料总量:
(t/m³)
(4)成型及齐边损失率
成型处的损失在扫平辊及被真空箱吸走的部分,但其量不多设为0.5%。
而齐边齐掉的部分均被回收利用,故不考虑在内。
损失量为:
(t/m³)
成型前的总原料量:
(t/m³)
其中:
绝干纤维量:
0.851423/1.109=0.76774(t/m³)
胶量:
0.851423×10%=0.0851423(t/m³)
蜡量:
0.851423×0.8%=0.0061419(t/m³)
固化剂:
0.851423×10%×1%=0.000851423(t/m³)
本工艺采用管道施胶,设施胶时的平均损失率为0.6%,施蜡及固化剂的损失率为1%。
则原辅材料量:
胶量:
(t/m³)
液蜡量:
(kg/m³)
液固化剂:
(kg/m³)
(5)干燥损失量
设损失率为0.5%
则损失量为:
(t/m³)
干燥前的总量:
(t/m³)
G
=
(t/m³)
(6)热磨损失量(不计)
(7)水洗损失量
设水洗的损失率为5%,则损失量为:
(t/m³)
水洗前的总原料量:
(t/m³)
(8)筛选损失量
设筛选损失率为7%,则损失量为:
(t/m³)
筛选前原料量:
(t/m³)
(9)削片损失量
设损失率为1%,则削片损失量为:
(t/m³)
削片前的原料量:
(t/m³)
5、1m³板所需的原材料量
综合以上计算结果为:
绝干木材量:
0.88216(t/m³)
胶量:
77.24(kg/m³)
固化剂:
0.77549(kg/m³)
蜡量:
6.2039(kg/m³)
6、年需原材料量
绝干木材量:
0.88216×61917.32=54620.98(t/a)
胶量:
0.07724×61917.32=4782.49(t/a)
固化剂:
0.00077549×61917.32=48.02(t/a)
蜡量:
0.0062039×61917.32=384.13(t/a)
7、年需木材的体积
年需绝干木材量为54620.98t。
设软材与硬材的混合比为3:
7,软材的绝干密度为440kg/m³,硬材的绝干密度为650kg/m³,它们的加权平均密度为:
440×0.3+650×0.7=587(kg/m³)
年需木材的体积为54620.98t÷587(kg/m³)=93051.08m³
在木材含水率为40%时,年需木材量为54620.98×(1+40%)=76469.37t。
将以上计算结果汇总成下表,表中按车间小时设计产量为
(m³/h)进行计算。
各工序木材小时用量表
工序
每立方米成品板需绝干纤维用量,kg/m³
绝干木材小时用量,kg/h
含水率
%
该含水率下木材小时用量,kg/h
成品
635.70
5486.09
6
5815.26
砂光前
699.28
6034.79
6
6396.88
裁边前
760.08
6559.50
5
6887.48
预热压前
763.90
6592.46
12
7383.56
成型前
767.74
6625.59
12
9988.36
干燥前
771.60
6658.91
50
5553.65
热磨前
771.60
6658.91
45
9655.42
水洗前
812.21
7009.37
35
9462.65
筛选前
873.34
7536.92
35
10174.85
削片前
882.16
7613.04
40
10658.26
生产1m³板所需原材料平衡图见下图所示。
绝干木材G:
纤维g:
蜡量
1%G9=882.16kgM:
胶量m:
固化剂
削片
7%G8=873.34kg
筛选
5%G7=812.21kg
水洗
损失不计G6=771.60kg
热磨
G5=771.60kgg5=6.1728kg
0.5%M5=77.16kgm5=0.7716kg
干燥
G4=767.74kgg4=6.1419kg
0.5%M4=76.77kgm4=0.7677kg
成型
G3=763.90kgg3=6.1112kg
0.5%M3=76.390kgm3=0.76390kg
预热压
G2=760.08kgg2=6.0806kg
6%M2=76.008kgm2=0.78008kg
裁边
G1=699.28kgg1=5.5942kg
7.9%M1=69.928kgm1=0.69928kg
砂光
G0=635.70kgg0=5.0856kg
M0=63.57kgm0=0.6357kg
成品
原料平衡图
8、主要生产设备的选择与计算
(1)削片机
工作制度2班,工作10h(每班工作5h)
每小时需木材:
(m³/h)
选鼓式削片机BX2113,生产能力36m³/h,则台数
台,取1台,则:
负荷率
(2)木片筛选机
工作制度:
3班,每班7.5h,共22.5h。
每小时筛选:
(m³/h)
选ZMS2型1台,筛选能力85m³/h·台,木材堆积系数为0.35,则需筛选42.2松散m³/h,。
42.2÷85=0.4965,则每台的负荷率为:
(3)热磨机
①热磨机每小时需加工量Q磨的计算:
Q磨=
(kg/h)
771.6kg/m³为生产1m³MDF热磨前所需原材料的重量。
②每班实际可加工量A磨的计算:
瑞典L42热磨机单位时间生产能力7.5t,绝干纤维计为7500kg绝干纤维,即7500kg/h。
③热磨机台数的计算:
C=Q磨/A磨=6673.48/7500=0.8898(台),取C1=1(台)
则热磨机的负荷率为:
η=C/C1×100%=0.8898×100%=88.98%
(4)干燥机选干燥机风机型号为HCMB3-112
①干燥机每小时需加工量Q干的计算:
Q干=
(kg/h)
②干燥机风机的纤维流量为2.57kg/h,则
A干=2.57kg/s×3600=9252kg/h。
③干燥机台数的计算:
C=Q干/A干=6673.48/9252=0.7213(台),取C1=1(台)
设备负荷率的计算:
η=C/C1×100%=0.7213×100%=72.13%
(5)铺装机选潘迪斯特成型头式铺装机
①成型前每小时所需的绝干纤维的重量是:
(kg/h)
②成型头的实际加工量是:
A=5000(kg/h)
③成型头实际台数的计算:
C=Q/A=6640.10/5000=1.33,取C1=2台
成型机负荷率的计算:
η=C/C1×100%=1.33/2×100%=66.4%
(6)热压机选瑞典SUNDS公司Motala压机一台,压板尺寸为1680mm×5180mm,14层。
热压机负荷率为:
13.47/14×100%=96.21%
(7)热压前各工序的设备负荷率分别为
削片机92.30%
筛选机49.65%
热磨机88.98%
干燥机72.13%
成型机66.40%
热压机96.21%
9、车间平面布置图
见附件
四、参考资料
[1]周定国主编.人造板工艺学(第2版).北京:
中国林业出版社,2010
[2]潘淑清、周玉申编著.中密度纤维板工艺设计.广州:
华南工学院出版社,2004
[3]木材工业实用大全编辑委员会编写组编.木材工业实用大全:
纤维板卷.北京:
中国林业出版社,2002
[4]浙江农林大学木材科学与技术学科编著.人造板工艺课程设计指导书(上).浙江:
浙江农林大学出版社,2012
[5]浙江农林大学木材科学与技术学科编著.人造板工艺课程设计指导书(下).浙江:
浙江农林大学出版社,2012
[6]庞庆海主编,《人造板机械设备》.东北林业大学出版社