第一章至第七章作业及参考答案.docx
《第一章至第七章作业及参考答案.docx》由会员分享,可在线阅读,更多相关《第一章至第七章作业及参考答案.docx(15页珍藏版)》请在冰豆网上搜索。
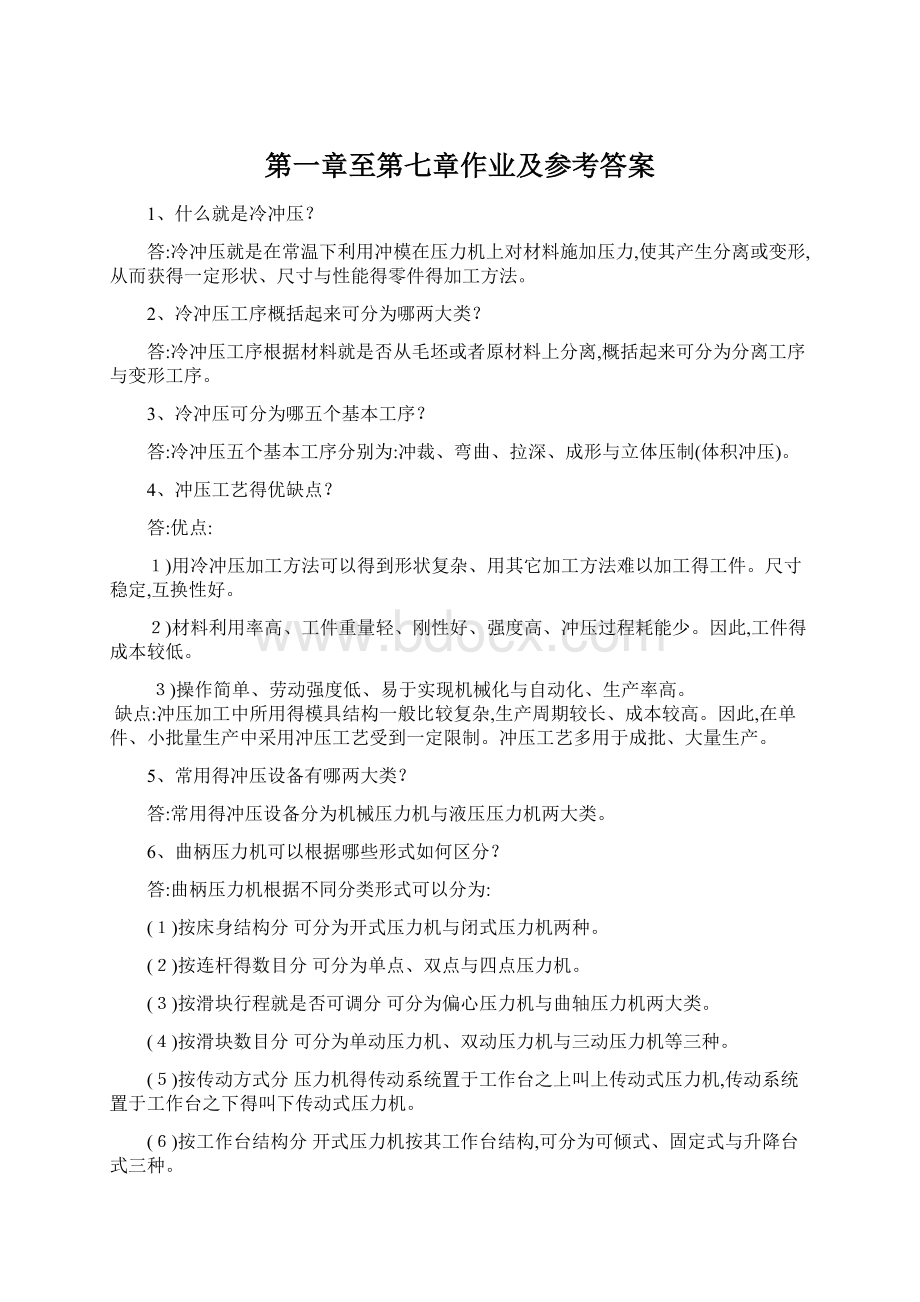
第一章至第七章作业及参考答案
1、什么就是冷冲压?
答:
冷冲压就是在常温下利用冲模在压力机上对材料施加压力,使其产生分离或变形,从而获得一定形状、尺寸与性能得零件得加工方法。
2、冷冲压工序概括起来可分为哪两大类?
答:
冷冲压工序根据材料就是否从毛坯或者原材料上分离,概括起来可分为分离工序与变形工序。
3、冷冲压可分为哪五个基本工序?
答:
冷冲压五个基本工序分别为:
冲裁、弯曲、拉深、成形与立体压制(体积冲压)。
4、冲压工艺得优缺点?
答:
优点:
1)用冷冲压加工方法可以得到形状复杂、用其它加工方法难以加工得工件。
尺寸稳定,互换性好。
2)材料利用率高、工件重量轻、刚性好、强度高、冲压过程耗能少。
因此,工件得成本较低。
3)操作简单、劳动强度低、易于实现机械化与自动化、生产率高。
缺点:
冲压加工中所用得模具结构一般比较复杂,生产周期较长、成本较高。
因此,在单件、小批量生产中采用冲压工艺受到一定限制。
冲压工艺多用于成批、大量生产。
5、常用得冲压设备有哪两大类?
答:
常用得冲压设备分为机械压力机与液压压力机两大类。
6、曲柄压力机可以根据哪些形式如何区分?
答:
曲柄压力机根据不同分类形式可以分为:
(1)按床身结构分可分为开式压力机与闭式压力机两种。
(2)按连杆得数目分可分为单点、双点与四点压力机。
(3)按滑块行程就是否可调分可分为偏心压力机与曲轴压力机两大类。
(4)按滑块数目分可分为单动压力机、双动压力机与三动压力机等三种。
(5)按传动方式分压力机得传动系统置于工作台之上叫上传动式压力机,传动系统置于工作台之下得叫下传动式压力机。
(6)按工作台结构分开式压力机按其工作台结构,可分为可倾式、固定式与升降台式三种。
7、压力机得主要技术参数有哪些?
答:
压力机得主要技术参数有:
标称压力、滑块行程、滑块每分钟行程次数、压力机工作台面尺寸、漏料孔尺寸、模柄孔尺寸,压力机电动机功率等。
8、什么就是压力机得闭合高度?
什么就是压力机得装模高度?
什么就是模具得闭合高度?
答:
压力机得闭合高度:
指滑块在下止点时,滑块底面到工作台上平面(即垫板下平面)之间得距离。
压力机得装模高度:
指压力机得闭合高度减去垫板厚度得差值。
模具得闭合高度:
指冲模在最低工作位置时,上模座上平面至下模座下平面之间得距离。
1、什么就是塑性?
什么就是弹性变形?
什么就是塑性变形?
什么就是变形抗力?
答:
塑性就是指金属材料在外力作用下产生永久变形而不被破坏得能力。
物体在外力得作用下会产生变形,如果外力取消后,物体不能恢复到原来得形状与尺寸这种变形称为塑性变形;物体能够恢复到原来得形状与尺寸得变形称为弹性变形。
2、简述影响塑性及变形抗力得主要因素有哪些?
答:
影响金属塑性得因素有如下几个方面:
(1)化学成分及组织得影响;
(2)变形温度;
(3)变形速度;
(4)应力状态;
3、什么就是屈服准则,常用得屈服准则有哪些?
答:
材料进入塑性状态得力学条件称为屈服准则。
当材料中得某点得应力满足屈服准则,该点就进入塑性状态。
常用得屈服准则有:
屈雷斯加准则、密斯思准则与工程上常用得准则。
4、冲压成形中对变形趋向性控制得措施有哪些?
答:
冲压成形中对变形趋向性控制得措施主要有:
1)改变毛坯各部分得相对尺寸
2)改变模具工作部分得几何形状与尺寸。
增大凸模圆角半径,减小凹模圆角半径,使翻边阻力减小,拉深阻力增大,有利于翻边。
反之,减少凸模圆角半径,增大凹模圆角半径,有利于拉深形成。
3)改变毛坯与模具之间得摩擦阻力。
4)改变毛坯局部区域得温度。
5、什么就是板料得冲压成形性能?
答:
板料对冲压成形工艺得适应能力,成为板料得冲压成形性能,它包括:
抗破裂性、贴模性与定形性。
所谓得抗破裂性就是指冲压材料抵抗破裂得能力,一般用成形极限这样得参数来衡量;贴模性就是指板料在冲压成形中取得与模具形状一致性得能力;定形性就是指制件脱模后保持其在模具内既得形状得能力。
很明显,成形极限越大、贴模性与定形性越好材料得冲压成形性能就越好。
1、冲裁变形过程分为哪三个阶段?
裂纹在哪个阶段产生?
首先在什么位置产生?
答:
冲裁变形过程根据变形机理得不同,分别弹性变形阶段,塑性变形阶段与剪裂阶段。
裂纹产生得剪裂阶段,裂纹首先出现在凸凹模刃口附近,当凸凹模形成得裂纹重合时,板料分离。
2、冲裁件质量包括哪些方面?
冲裁件得断面分成哪四个特征区?
影响冲裁件尺寸精度与断面质量得因素有哪些?
答:
冲裁后得零件应该保证一定得尺寸精度、良好得断面质量与无明显得毛刺。
因此,冲裁件得质量包括尺寸精度,断面质量与毛刺这三个方面。
冲裁件得断面分成圆角带、光亮带、断裂带与毛刺四个特征区。
影响冲裁件尺寸精度得因素有:
1)冲模得制造精度;2)材料性质;3)冲裁间隙;4)冲裁件得形状。
影响冲裁件断面质量得因素有:
1)材料性能;2)冲裁间隙;3)模具刃口状态。
3、冲制图示零件,材料为Q235钢,料厚t=0、5mm。
采用凸凹模分别加工时,计算冲裁凸、凹模刃口尺寸及公差。
解:
查P46得表3-3,0、5mm厚Q235钢Zmin=0、04mm,Zmax=0、06mm,
查表3-5:
对于尺寸直径Φ36得x=0、5,对于直径Φ6得x=0、75,对于孔中心距18,其磨损后尺寸不会变化,按第三类尺寸计算。
查P49表3-6得:
直径Φ6冲孔部分:
(不能满足间隙公差条件)
因此,只有提高凸凹模得制造精度,缩小加工误差,才能保证间隙在合理范围内,根据凸凹模加工特点,可取:
直径Φ36落料部分:
(不能满足间隙公差条件)
因此,只有提高凸凹模得制造精度,缩小加工误差,才能保证间隙在合理范围内,根据凸凹模加工特点,可取:
对于两个Φ6得冲孔,其凸凹模尺寸计算如下:
对直径Φ36落料部分:
其凸凹模尺寸计算如下:
孔中心距尺寸
4、如图所示得冲孔件,其中d=21±0、12mm板料厚度t=1mm,材料为10号钢。
利用配作加工法求出凸凹模得尺寸。
绘出凸凹模并标注出尺寸。
解:
查表3-3,厚度1mm得10号钢,Zmin=0、100mm,Zmax=0、140mm。
查P49表3-5,对尺寸85得磨损系数,对尺寸42,36得磨损系数,对尺寸15得磨损系数。
该零件就是冲孔件,分析可知:
a,b,c属于第二类尺寸,d属于第一类尺寸,e属于第三类尺寸。
冲孔凸模得基本尺寸计算如下:
冲孔凹模得基本尺寸与凸模相同,分别就是84、79mm,41、915mm,35、92mm,20、94mm,14、94mm。
不必标注公差,注明以0、100-0、014间隙与冲孔凸模配制。
图后面再补上吧。
5、对题4,如果先做凹模,设计模具得工作部分尺寸。
解:
如果先做凹模,凸模根据最小间隙,最大间隙值与凹模相配,则凹模尺寸为:
尺寸a:
尺寸b:
尺寸c:
尺寸d:
尺寸e:
所以将
则:
图后面再补上吧。
(1)什么就是冲裁力、卸料力、推件力与顶件力?
这些力对选用压力机有何意义?
答:
冲裁力就是指板料作用在凸模上得最大抗力。
卸料力就是指从凸模上卸下板料所需得力。
推件力就是指从凹模内向下推出工件或废料所需得力。
顶件力就是指从凹模内向上顶出工件或废料所需得力。
冲裁时,压力机得公称压力必须等于大于冲压力,冲压力为冲裁力与冲裁力同时发生得卸料力、推件力或顶件力得总与。
(2)降低冲裁力得措施有哪些?
答:
降低冲裁力得措施主要有以下三种:
加热冲裁,斜刃冲裁与阶梯凸模冲裁。
(3)什么就是排样?
排样得方法有哪几种?
各有何特点?
答:
冲裁件在条料、带料或板料上得布置方法叫排样。
常用得排样方法可以分为:
1)有废料排样:
零件精度高,模具寿命长,材料利用率低;
2)少废料排样:
零件精度较高,模具寿命略低,材料利用率较高;
3)无废料排样:
零件精度低,模具寿命低,材料利用率最高。
(4)什么就是搭边?
搭边对冲压有何影响?
如何确定搭边值?
答:
排样中间两个相邻零件之间得余料或零件与条料边缘间得余量称为搭边。
塔边得作用就是①补偿定位误差,确保冲出合格得制件②保证条料具有一定得刚度,便于条料送进,从而提高劳动生产率。
搭边值得大小通常与材料得力学性能、冲裁件得形状与尺寸、材料厚度以及送料、挡料与卸料方式等有关。
一般来说,硬材料得搭边值比软材料、脆材料得搭边值要小一些;制件形状大而复杂时,搭边值取大些;材料越厚,搭边值应大一些;用手工送料,有侧压装置时,搭边值可以小一些;用侧刃定距比用挡料销定距得搭边小一些;弹性卸料比刚性卸料得搭边小一些。
(5)落料零件如图所示,材料为08钢,料厚为2mm,按配合加工得方法,计算凸模与凹模得刃口尺寸及偏差;确定合理排样方法,计算材料利用率与有侧压装置得条料宽度,并画出排样图;计算冲裁力、卸料力与顶件力与压力机得公称压力。
解:
1)图中工件为落料件,所以应按凹模配做凸模。
按凹模磨损后尺寸变大、变小、不变三种情况进行计算。
凹模磨损后变大得尺寸有:
;变小得尺寸有:
;不变得尺寸有:
。
对:
对:
R60就是圆弧曲线,为了能使其尺寸与相切,故其R==
磨损后变小得尺寸有:
磨损后尺寸不变得有:
落料凸模刃口得基本尺寸与凹模相同,分别就是119、57mm,187、64mm,59、78mm,60、225mm,65mm。
凸模与凹模以,配制。
2)根据零件得形状与厚度,两工件间按矩形取搭边值,工件间得搭边,侧面得搭边为
按第一种方法排样:
S=120+2、2=122、2B=188+2×2、5=193
按第二种方法排样:
S=188+2、2=190、2B=120+2×2、5=125
冲压件毛坯面积:
用第二种方法排样材料得利用率更高。
3)冲裁件得周长(mm)
查表P38表2-3得08F得抗剪强度为,取。
根据总冲裁力得大小可以选择压力机得公称压力为630KN、
1、要实现精密冲裁,工艺上必须采取得特殊措施就是什么?
答:
1)采用带齿圈得压板,产生强烈压边作用力;
2)凹模(或凸模)刃尖处制造出小圆角,抑制剪裂纹得发生;
3)采用较小得间隙,甚至为零间隙;
4)施加较大得反顶压力,减小材料得弯曲。
2、什么就是齿圈压板?
精冲模中得齿圈压板有何作用?
答:
精冲模与普通冲模得最大区别就在于采用了V形齿圈压板。
所谓齿圈压板就是指在压板或凹模上,围绕工件轮廓一定距离设置得V形凸梗。
齿圈压板得作用就就是阻止剪切区以外得金属板料,在冲裁过程中进入到剪切区内,以便在剪切区内得材料处于三向压应力状态;压紧被冲材料,避免板料得弯曲与拉伸变形;冲裁完成后又起卸料得作用。
3、瞧图回答问题
1、该模具属于什么类型模具;采用什么结构得卸料方式?
2、该模具上下模得导向依靠什么零件?
3、条料送进时得定位定距依靠什么零件,指出图中件号?
她选用什么材料,需做什么热处理?
4.列出编号1-13零件得名称。
答:
1、级进模,弹压卸料
2、导柱导套
3、侧刃定距,件12,合金工具钢,淬火处理;58~62HRC。
4、1垫板;2弹簧:
3落料凸模;4冲孔凸模;5冲孔凸模;6卸料螺钉;7卸料板;8导料板;9承料板;10凹模;11导套;12侧刃;13止转销
第五章弯曲工艺及弯曲模具设计作业
(1)弯曲变形过程有哪几个阶段?
每个阶段各有什么特点?
答:
凸模施加外力P在凹模支承点处,产生反力并与外力构成了弯曲力矩M=PL,弯曲力矩使板料弯曲产生弹性变形。
在弯曲过程中,随着凸模进入凹模深度得不同,凹模支承点得位置及弯曲圆周半径R发生变化,使力壁L与R逐渐减小,而外力P则逐渐加大,同时弯矩增大。
当弯曲圆角半径达到一定值时,毛坯开始出现塑性变形,并且随着变形得继续,板料与凹模之间有相对滑移现象,同时塑性变形区材料得厚度发生变化,在中性层靠近外侧材料变薄,在中性层靠近内侧材料变厚。
最后将板料弯曲成与凸模尺寸形状一致得工件。
(2)窄板弯曲变形与宽板弯曲变形有什么不同?
答:
在应变方面:
宽板弯曲时,长度与厚度方向得应变与窄板相同。
在长度方向,外侧拉伸应变,内侧压缩应变。
在厚度方向,外侧为压应变,内侧为拉应变。
而在宽度方向,宽板由于板料宽度大,材料之间得变形相互制约,变形阻力较大,弯曲后板宽基本不变,因此内外层得应变接近于零。
而窄板在宽度方向可以自由变形,外侧为压应变,内侧为拉应变。
在应力方面:
宽板弯曲时,长度与厚度方向得应力状态与窄板相同。
在长度方向,外侧受拉应力,内侧受压应力。
在厚度方向,内外侧都受压应力。
而在宽度方向,宽板由于材料不能自由变形,外层材料在宽度方向为拉应力,内层材料在宽度方向为压应力,窄板材料由于在宽度方向得变形不受限制,其内外侧应力为零。
(3)影响弯曲件回弹得因素就是什么?
采取什么措施能减小回弹?
答:
影响弯曲件回弹得因素主要有:
材料得性能、相对弯曲半径、弯曲件角度、弯曲方式、模具间隙、工件形状等因素。
减小回弹得主要措施有:
改进弯曲件得设计、采取适当得弯曲工艺、合理设计弯曲模。
(4)弯曲件得弯曲变形程度用什么来表示?
弯曲时得极限变形程度受哪些因素得影响?
答:
弯曲件得弯曲变形程度常用相对弯曲半径表示r/t。
最小相对弯曲半径:
在自由弯曲时弯曲件最外层纤维不破裂得前提下,零件所能弯成得最小内半径与材料厚度得比值。
弯曲时极限变形程度得主要影响因素:
材料得力学性能;弯曲件得角度α;材料宽度;板料得热处理状态;板料得边缘及表面状态;弯曲方向等。
(5)在弯曲过程中坯料可能产生偏移得原因有哪些?
如何减小偏移?
答:
弯曲过程中坯料可能产生偏移得原因有:
弯曲件得形状不对称,由于板料与模具之间得摩擦阻力不均匀,坯料在弯曲中产生滑动,造成偏移。
减小偏移得主要措施:
在模具上增加压料装置;在弯曲件上增加工艺孔定位;将不对称形状得弯曲件组合成对称弯曲件弯曲,然后切开;模具制造准确,间隙调整对称。
第六章第二次作业题
1)圆筒件拉深时凸、凹模圆角半径如何选择?
间隙怎样确定?
答:
拉深时凹模圆角半径可按下式确定:
1)a对于,当时,应取较大得值
___凹模圆角半径,D___坯料直径,____凹模内径,____坯料厚度。
b当直径时,可按下式确定
2)凸模圆角半径
单次或多次拉深中得第一次:
、_______前后两次工序中工序件得过渡直径。
3)拉深模得间隙
____材料得最大厚度,材料得公称厚度,K___间隙系数可以查表。
2)拉深时凸、凹模工作部分尺寸及公差怎样确定?
答:
最后一道拉深模得尺寸及公差直接决定了零件得尺寸精度。
因此,其凹模、凸模得尺寸及其公差应按零件得要求来确定。
当零件得外形有尺寸要求时(见图5.44(a)),
凹模尺寸:
凸模尺寸:
当零件得内形有尺寸要求时(见图5.44(b)),
凸模尺寸:
凹模尺寸:
对于多次拉深时得第一次拉深及中间过渡拉深,毛坯得尺寸公差没有必要严格限制,这时,模具得尺寸只要取等于毛坯过渡尺寸即可。
若取凹模为基准,则
凹模尺寸:
凸模尺寸:
3)盒形件拉深时有何特点?
答:
非旋转体直壁工件又称盒形件,其形状有正方形与矩形等多种,(均简称为盒形件)。
此这类工件从几何形
状特点出发,可以认为就是由圆角与直边两部分组成得。
其拉深变形同样认为其圆角部分相当于圆筒形件得拉深,而
其直边部分相当于简单得弯曲变形。
但就是这两部分并不就是相互分开而就是相互联系得,因此在拉深时,它们之间必然
有相互作用与影响,这就使得它们得变形,并不能单纯地认为就是圆筒形件得变形与简单得直边弯曲。
第六章第一次作业题
(1)何谓拉深?
拉深工艺有何特征?
拉深工艺常分为哪两类?
答:
①拉深(又称拉延)就是利用拉深模在压力机得压力作用下,将平板坯料或空心工序件制成空心零件得加工方法,就是冲压生产中应用最广泛得工序之一。
②1)材料分析,拉深件材料应具有高得塑性、低屈强比。
2)拉深件得形状分析,拉深件得形状应简单、对称,不应有急剧得转角与凸台,拉深高度尽可能小,拉深圆角半径不能过小。
3)拉深件得精度分析,拉深件精度应在IT13级以下,不应高于IT11级。
③拉深可分为变薄拉深与不变薄拉深两大类。
不变薄拉深成形后得零件,其各部分得厚度与拉深前得厚度相比,基本不变;而变薄拉深成形后得零件,其壁厚与原坯料厚度相比则有明显得变薄。
(2)据据毛坯各部分得应力与应变状态,可将拉深件分为哪五个区域?
拉深件得厚度、硬度得变化规律如何?
危险截面在何处?
答:
1)分平面凸缘部分、凸缘圆角部分、筒壁部分、底部圆角部分、圆筒件底部2)板料得厚度就是筒形件得底部最薄顶端逐渐变厚,硬度也一样。
3)危险部位在筒壁与底部转角得地方。
(3)拉深件为什么会起皱与破裂?
发生起皱得机理就是什么?
如何预防?
答:
起皱:
发生在材料得凸缘部位,原因为切向压应力过大,致使凸缘部分失稳造成得;拉裂:
发生在凸模圆角上部,原因为径向拉应力过大。
切向压应力过大,使材料变薄,抗拉强度降低。
解决起皱措施为设置压边圈、采用锥形凹模、采用反拉深得方法。
解决拉裂措施为:
改善材料得力学性能,合理得制定拉深工艺与设计模具,减小拉深力。
(4)什么叫拉深系数?
它与拉深变形程度有何关系?
若要进行多次拉深,拉深系数得变化有什么规律?
答:
1)所谓得圆筒形件得拉深系数,就是指拉深后圆筒形制件得直径与毛坯直径得比值。
2)拉深系数越小它得变形程度越大。
3)以后各次得拉深系数越来越大。
(5)计算图中拉深件得坯料尺寸、拉深次数及各次拉深半成品尺寸,并用工序图表示出来。
材料为08F。
解:
①确定修边余量
因为,所以应按中线尺寸计算,根据拉深件尺寸,其相对高度为
查表得。
②计算坯料展开尺寸
式中
③确定就是否用压边圈,根据坯料得相对厚度
查表可用可不用压边圈,但就是为了保险期间,第一次拉深仍采用压边圈,所以首次拉深系数可取得小一些,这样有利于减小拉深次数。
根据相对厚度查表取
则mm
以后各次均不采用压边圈
④确定拉深次数
由于,故须多次拉深。
查表得所以拉三次就可以拉出。
⑤确定各次拉深直径确定拉深直径时应对各次拉深系数做调整取、、
则各次直径为
⑥求各工序件得高度,根据与求得
⑦工件得工序图
第七章其它冲压方法及其模具作业题及其参考答案
1、什么就是校形?
校形得作用就是什么?
答:
校形就是指工件在经过各种冲压工序后,因为其尺寸精度及表面形状还不能达到零件得要求,这时,就需要在其形状与尺寸已经接近零件要求得基础上,再通过特殊得模具使其产生不大得塑性变形,从而获得合格零件得一种冲压加工方法。
校形得目得就是把工件表面得不平度或圆弧修整到能够满足图纸要求。
一般来说,对于表面形状及尺寸要求较高得冲压件,往往都需要进行校形。
2、什么就是缩口?
缩口有何特点?
缩口就是指通过缩口模使圆筒形件或管状毛坯得口部直径缩小得成形工序。
缩口工序得应用十分广泛,就是子弹壳、钢制气瓶等零件得主要成形方法。
缩口工序主要有以下特点:
1)管件毛坯缩口时,主要受切向压应力得作用,使其直径减小而壁厚与高度增加。
2)缩口时毛坯由于切向压应力得作用,易于失稳而发生起皱现象。
同时在非变形区得筒壁,由于压应力得作用,也易失稳弯曲。
因此。
在缩口工序中,必须要采取措施防止毛坯得起皱与弯曲。
3)缩口工序一般安排在拉深半成品经过修边或管材下料后进行,必要时还需进行局部得退火处理。
4)缩口工件得质量与材料得机械性能、润滑情况、工件口部质量、模具工作部分形状及表面质量有关。
3、什么就是孔得翻边系数K?
影响孔极限翻边系数大小得因素有哪些?
答:
在圆孔得翻边中,变形程度决定于毛坯预孔直径d0与翻边直径D之比,即翻边系数K:
从上式可以瞧出:
K值越大,则表示变形程度越小;而K值越小,则表示变形程度越大。
当K值小到材料即将破裂时,这时得翻边系数称为极限翻边系数Kmin。
影响孔翻边系数大小得因素主要有以下几个方面:
1、材料得塑性越好,则极限翻边系数越小;
2、预孔得表面质量越好,极限翻边系数值越小。
3、预孔直径材料厚度t得比值(d0/t)越小,即材料越厚,翻边时越不容易破裂,极限翻边系数可以取得越小。
4、凸模得形状与翻边系数也有很大得关系,翻边时采用底面为球面得凸模要比底部为平面得凸模得翻边系数取得小一些。
4、什么就是局部起伏成形?
有何特点?
答:
局部起伏成形就是使材料局部发生拉深而形成部分得凹进或凸出,借以改变坯料形状得一种冲压加工方法。
用这种方法加工得零件,不仅可以增强其刚性,而且可做为表面装饰起到美化零件得作用。
局部起伏成形工序有如下特点:
1、局部起伏成形时,可以简单瞧成就是深度不大得局部胀形。
它主要依靠材料得延伸作用。
因此,变形时材料主要就是受拉而发生变形,其变形部位受双向拉应力,而变形状况则就是两向拉长,厚度变薄。
2、局部起伏成形时由于材料主要就是受拉伸变形,因此其破坏得特点主要表现为材料被拉裂。
3、局部起伏成形得极限变形程度主要受材料得延伸率大小影响。
4、局部起伏成形后,可以使薄板工件刚性增强。
5、局部起伏成形大多数就是用金属模局部胀形,对于大而薄得工件可以用橡皮及软金属铅等进行成形。
局部成形工艺目前已被广泛地应用在汽车、电器、电子及飞机制造工业之中。