再加热炉的设计.docx
《再加热炉的设计.docx》由会员分享,可在线阅读,更多相关《再加热炉的设计.docx(17页珍藏版)》请在冰豆网上搜索。
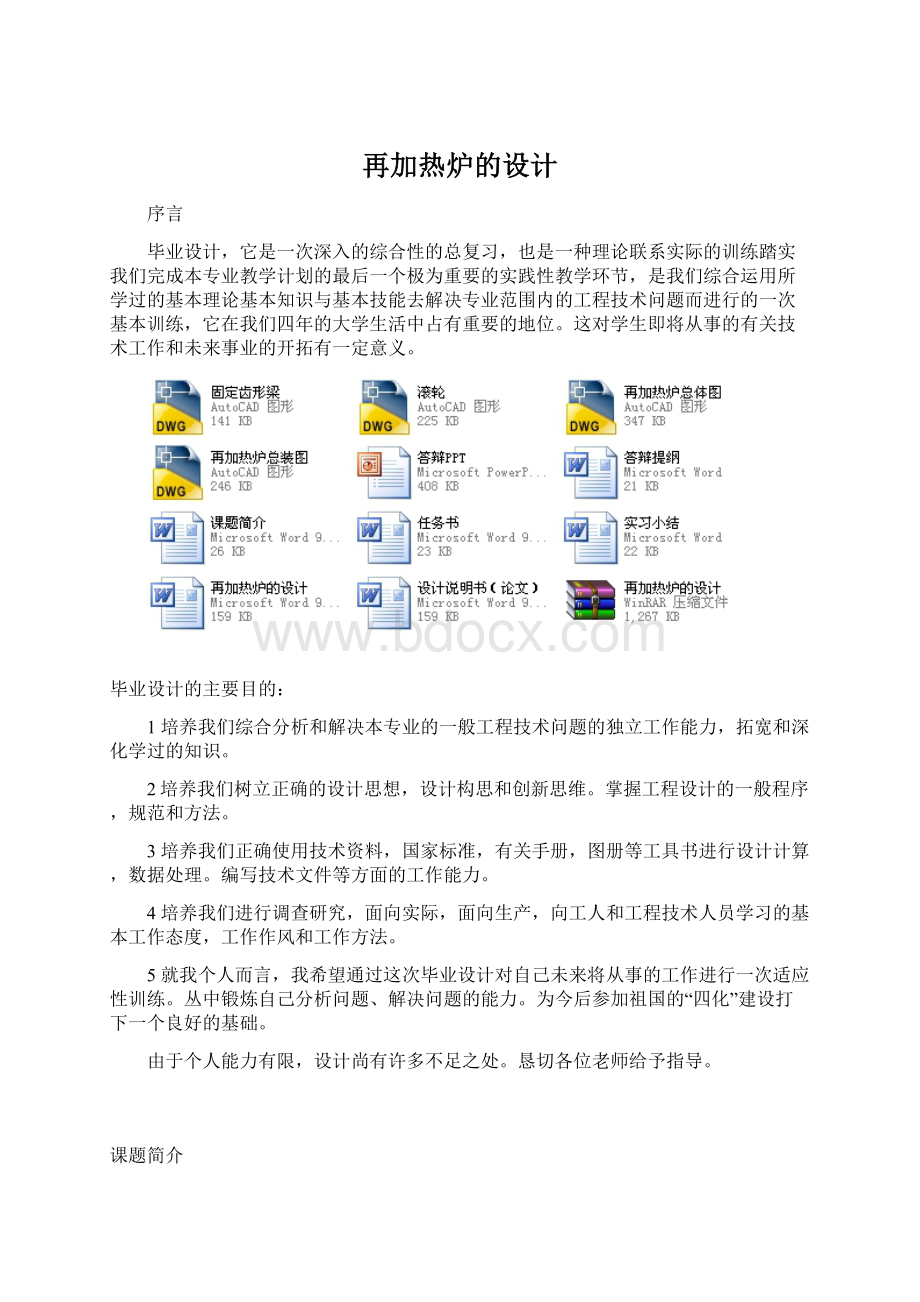
再加热炉的设计
序言
毕业设计,它是一次深入的综合性的总复习,也是一种理论联系实际的训练踏实我们完成本专业教学计划的最后一个极为重要的实践性教学环节,是我们综合运用所学过的基本理论基本知识与基本技能去解决专业范围内的工程技术问题而进行的一次基本训练,它在我们四年的大学生活中占有重要的地位。
这对学生即将从事的有关技术工作和未来事业的开拓有一定意义。
毕业设计的主要目的:
1培养我们综合分析和解决本专业的一般工程技术问题的独立工作能力,拓宽和深化学过的知识。
2培养我们树立正确的设计思想,设计构思和创新思维。
掌握工程设计的一般程序,规范和方法。
3培养我们正确使用技术资料,国家标准,有关手册,图册等工具书进行设计计算,数据处理。
编写技术文件等方面的工作能力。
4培养我们进行调查研究,面向实际,面向生产,向工人和工程技术人员学习的基本工作态度,工作作风和工作方法。
5就我个人而言,我希望通过这次毕业设计对自己未来将从事的工作进行一次适应性训练。
丛中锻炼自己分析问题、解决问题的能力。
为今后参加祖国的“四化”建设打下一个良好的基础。
由于个人能力有限,设计尚有许多不足之处。
恳切各位老师给予指导。
课题简介
摘要:
步进梁式再加热炉是为连轧生产线提供钢管再加热在线常化(一种热处理方式)所用。
它是依靠专用的步进机械使工件在炉内移动的一种机械化炉。
步进炉底的结构和传动方式要根据出料的频率和炉子的生产能力决定,它不仅要考虑炉内的温度、还要考虑被加工工件的尺寸参数和工地方面的实用性。
所以必须严格计算其内部参数,保证炉子的生产和安全。
炉底机械采用双轮斜轨式机构。
步进梁的升降和平移动作采用液压缸驱动。
步进梁支柱穿炉底的孔洞采用干式“拖板”密封。
装出料端设有拨料机,固定梁最末一个料位检测有料后,出料拨料机上升将钢管拖起后,出料拨杆立即下降将钢管拨送到出料悬臂轨道上,使钢管能够马上出炉,出料周期最快20s,可以满足125根/h的操作频率。
关键词:
步进梁式再加热炉步进梁双轮斜轨式机构有效炉底长度
梁距齿距
在生产中,利用燃料产生的热量,或者将电能转化成热量对工件或物料进行加热的设备,称为工业炉。
锅炉也是工业炉的一种,机械工业应用的工业炉有多种类型,在铸造车间有熔炼金属的平炉、冲天炉、感应炉、电阻炉、真空炉等;在锻压车间有对钢锭或钢坯进行煅前加热的各种加热炉和消除应力的热处理炉;在热处理车间,有改善工件力学性能的各种退火、正火、淬火和回火的热处理炉;在焊接车间有压制前的钢板加热炉和焊后热处理炉;在粉末冶金车间还有烧结金属的加热炉等。
步进梁式再加热炉是为连轧生产线提供钢管再加热在线常化(一种热处理方式)所用。
它是依靠专用的步进机械使工件在炉内移动的一种机械化炉。
参数:
1、再加热炉加热钢管规格及产量:
外径:
148mm、164mm、256mm、281mm
壁厚:
4.5——25/32mm
长度:
8000——32000mm
产量:
125t/h
1.2最高炉温:
1050℃
1.21钢管入炉温度:
720℃——870℃
1.22钢管出炉温度:
900℃——950℃
1.3炉型和炉子的基本尺寸
炉型:
步进梁式炉
装出料轨道中心距:
16000mm
炉子内长:
15300mm
炉子内宽:
34000mm
有效炉底面积:
约542m
固定梁顶面标高:
+6644
1.4炉型概述
炉子从装料至出料沿炉长方向分为炉子预热段,加热段和均热段。
装料端炉顶压底,以防止入炉钢管骤然受到强大热冲击产生变形。
提高加热传热效率和保证钢管加热的均匀是炉子结构与烧嘴选型合理配
置的前提。
设计以天然气为燃料,步进梁式再加热炉加热段和均热段的供热全部采用端部亚高速烧嘴,其优点是传热效率高,温度分布均匀:
同时加热段和均热段沿炉宽方向,分别分为4个温度控制段,以保证钢管长度方向的温度均匀性。
钢管再加热是用耐热铸刚梁支托钢管的步进梁式炉。
活动梁和固定梁的顶面是带弧型的齿型,使钢管在炉内等间距放置。
在每一次步进时钢管都能转动一个角度,从而保证钢管的加热温度更加均匀并防止钢管在炉内弯曲变形。
步进梁用支柱支撑高出炉底,使炉气能围绕钢管形成良好循环,均匀加热。
钢管再加热炉采用炉内悬臂辊道侧进料和侧出料;炉内悬臂辊道由交流变频电机驱动和调速,并与炉外辊道速度相匹配。
路底机械采用双轮斜轨式机构。
步进梁的升降和平移动作采用液压缸驱动。
步进梁支柱穿炉底的孔洞采用干式“拖板”密封。
装出料端社、设有拨料机,固定梁最末一个料位检测有料后,出料拨料机上升将钢管拖起后,出料拨杆立即下降将钢管拨送到出料悬臂轨道上,使钢管能够马上出炉,出料周期最快20s,可以满足125根/h的操作频率。
所有炉子的机械运动均采用PLC自动控制,装出料端都设有工业电视,用于监视炉内钢管装,出料的操作。
炉区的主要设备有:
炉内装料悬臂轨道、装料拨料机、炉内缓冲挡板、步进梁式加热炉本体、炉内出料悬臂辊道、出料拨料机、以及煤气管道和助燃空气管道系统、冷却水系统、排烟系统以及炉区操作平台等。
再加热路分八段温度与燃烧控制,即:
均热段一、均热段二、均热段三、均热段四、热段一、加热段二、加热段三、加热段四。
每个温度控制段均配备8支亚高速天然气烧嘴进行供热。
二、再加热炉机械设备设计
2.1再加热炉技术性能
序号
项目
单位
规格
1
炉型
步进梁式
2
用途
钢管再加热
3
钢管规格
外径
壁厚
长度
mm
ø148ø164ø256281
4.5——25/32
8000——32000
4
加热钢种
低合金钢
合金钢
5
钢管入炉温度
℃
720℃——870℃
6
钢管出炉温度
℃
900℃——950℃
7
钢管加热后温差
℃
5
8
炉子能力
产量
出料频率
t/h
根/h
最大125
最大180
9
燃料种类
天然气
10
燃料发热值
KJ/Nm
34694
11
天然气耗量(最大)
Nm³/h
2530
12
空气耗量(最大)
Nm³/h
34000
13
空气预热温度
℃
~450
14
冷却水耗量
T/h
~100
15
压缩空气耗量
m³/h
180(最大)
16
电器设备安装功率
KW
17
炉底机械传动方式
液压
18
步进行程
升降
平移
mm
180
310
19
步进周期
秒
最快20
20
烟囱高度
出口内径
m
25
1.52
2.1步进梁式加热炉底方案设计:
步进式炉是依靠专用的步进机械使工件在炉内移动的一种机械化炉。
该炉内机械传动有多种方式,如:
齿条式、链条牵引式——因为炉子下方粉尘较大,影响传动因数,不宜使用。
摩擦推杆式——摩擦系数较大,使用寿命相比之下较低。
机械杠杆托升机构——受力较大,所需要支撑力也较大,比较琐烦。
四杆机构升降式——由于该步进机构处于梁式再加热炉的下方,所用空间有限,而机械能控制的四杆机构需较大的空间,而且当需要对其进行维护和修复时较为困难。
但考虑到功率损耗和设备的使用周期,故:
步进炉的步进机械传动方式采用液压传动和双轮斜轨机构,该机构应设有两层框架(升降框架和水平框架),升降和水平运动都要设有定心装置,用以保证使炉底步进机械沿炉子中心线正常运行,减少钢管在炉内的跑偏,使钢管被顺利的输送到出料端据资料显示它的运行的可靠性高,安装调试方便,利于设备维修。
升降定心装置应安装于升降框架和炉基础上,水平定心装置安装于升降框架和水平框架上。
2.2炉子主要尺寸计算
有效炉底长度
有效炉底长度是指炉子总长度中工件在炉内受热的一段长度。
装料端用悬臂辊由炉侧装入,以辊道中心线为起点。
出料端用悬臂辊由炉侧出料,以辊道中心线为终点。
计入工件间隔后,有效炉底长度为:
L=
=
=15998.5mm
式中K——修正系数;修正系数K包括炉型系数C1,钢种系数C2,形状系数C3,燃料系数C4。
根据《工业炉设计手册》得:
C1=1.0,C2=0.7,C3=1.0,C4=1.0。
G——要求达到的炉子生产能力
s——工件直径
b——工件宽度
e——工件间隔
L——工件长度
f——工件截面积
n——装料列数
7.85——合金钢的密度
1.10——安全系数
最终有效炉底长度还要取决于节能的观点和装出料机的操作节奏以及步进机械的输送能力协调,根据该炉设计要求根据设计要求,出料滚道中心距即为有效炉底长度。
有效炉长L=16000mm
炉底宽度根据炉底长度L和工件在炉内的列数N决定,工件两端之间和工件端头与侧墙之间的距离取0.2~0.5mm,当炉底特别长时,考虑到工件在运行中的跑偏量炉宽应适应放大。
确定炉宽时应计入步进炉底和固定炉底之间的间隙,间隙过小,会产生堵塞现象,过大时容易损失炉内热量和使炉底金属件产生弯曲变形。
梁距和齿距的确定:
步进炉底的数量和宽度、固定炉底的宽度、工件的悬臂长度、厚度及其加工温度有关。
悬臂过长或支点距离过大,工件下垂到超过炉底升降行程时就会碰到炉底而发生故障。
查《工业炉设计手册》得:
工件允许的悬臂长度是一个经验数据,250mm×250mm的合金钢悬臂长度取1800mm,然而当加热温度超过1000℃时,结果因下垂过多而无法生产,当悬臂长度为1200mm时可以正常生产。
实践证明:
不同的被加工材料在炉子中所处的梁距是不相同的,低合金钢与合金钢在炉中被加热时,梁距(活动梁与活动梁之间的距离或固定梁与固定梁之间的跨距),根据«工业炉设计手册»得:
跨距B的计算公式为:
B=(1.5~1.76)l
=1.5×1200
=1800mm
式中l——为悬臂长度,
步进梁安装在炉底下部的整体框架上,由步进机构使之运动。
固定梁则被固定在炉底钢结构上,梁的顶面是根据加热圆钢的规格]装炉量做出齿形凸槽,
梁数:
N=34000/1800=18.9(排)
通过实践和理论方面验证,考虑到工地的实际情况和炉子的设计宽度,
将炉内梁数设为十九排较为合适。
在此取梁距1720mm,根据工地的实际大小,和炉子的具体尺寸。
齿距通常是工件外径的1.3~2.0倍,步距则比齿距小20~50mm。
行程约为200mm,周期时间为15~30s,只有这样才可保证与炉子装料机构相匹配以保证炉子的生产能力。
查《工业炉设计手册》,通过对此炉子的设计要求:
因此,取被加工圆钢的最大直径为:
281mm,由于被加工件时普通钢材,取1.3为参数。
故齿距为:
281×1.3=265.3mm
因为钢材为普通钢材,钢材在被加工过程中会会剥落外部杂质,导致圆钢外径减小,加之圆整,所以:
齿距取350mm为宜
可以保证炉子正常工作。
步距则比齿距小20~50mm,这样设计是由于能让圆钢更好的全面地受热,保证再加热炉的生产质量。
因此根据参考资料和工地实际情况取步距为310mm,查手册,再加热炉的步距即本加热炉的活动梁的平移距离.
故此该加热炉的水平行程为310mm,其差值40mmm,为钢管在齿形槽内转动的距离。
活动梁支柱穿过炉底的孔洞应采用双层“托板”密封,这样第一保证了炉内温度不会有较大量的外泄损失,其二,可以保证炉内被加工圆钢所脱落的杂质能顺利的完全的被清除出炉外。
下层托板用1Cr18Ni9钢板衬以耐火隔热浇注料制成,炉内托板用耐热铸钢制作。
在加热过程中,步进机构的每一步运动都是由步进梁的升降(或平移)运动来带动的。
步进梁的运动可以有多种机械或液压机构带动或控制它,机械方面可以由机械能带动四杆机构对其的运动方式进行控制,但由于该步进机构处于梁式再加热炉的下方,所用空间有限,而机械能控制的四杆机构需较大的空间,而且当需要对其进行维护和修复时较为困难,在加热炉炉底难免会有粉尘和氧化物,对于裸露在外的四杆机构影响较大,所以无论是经济性、实用性,还是对于操作人员的安全性都有甚多不合理之处,所以不能采用,应打消此方案。
所以考虑第二方案:
采取液压传动的方式来控制步进梁的升降(或平移)运动,之所以选择液压系统其原因如下:
液压传动能方便的实现无级变速,调速范围大。
在相同功率情况下,液压传动能量转换元件的体积较小,重量较轻。
工作比较平稳,换向冲击比较小,便于实现频繁换向。
便于实现过载保护,便于实现自动化。
特别适合电气控制联合使用时,易于实现复杂的自动工作循环。
通过上述的比较分析,决定在带动炉子的步进工作循环中,采用液压系统来控制较为合适。
采用液压系统来控制整个炉子的进出料装置和步进梁的升降运动,它们均是通过液压缸将液压能转换成机械能,进出料装置是通过两对液压缸来实现运动的;步进梁的升降运动是通过四个升降液压缸来实现的。
升降液压缸推动带上下轮组的升降框架,下轮组在斜轨上面作上下运动,通过上下轮组带动水平框架作升降运动。
在此过程中,水平运动液压缸被锁定。
步进梁的进、退运动(即平移运动)是通过2个液压缸来实现的。
它直接作用于平移框架上,使之在升降框架的上轮组上作平移运动。
在此过程中,升降运动的液压缸被锁定。
升降和平移框架的定心倒像是借助于安装在框架中心线升降定心导向轮和水平导向轮来实现的。
步进梁运动循环图:
在斜轨座轨道下端部设安全止当。
升降缸的设计是超行程的,在检修时可使框架降低到斜轨座的止挡上,从而使液压缸处于无负荷状态,易于拆装检修。
炉底有关设备的轴承和部件必须定期加注润滑油脂(包括轨道表面也要涂以黄油进行润滑。
综上所述:
该炉底步进机械主要由以下几部分构成:
斜轨装置、滚轮组、升降框架、水平框架、步进梁、上定心装置、下定心装置、水平缸、升降缸等机构的配合动作方能完成规定的工作步骤。
2.5炉区附属机械设备设计:
2.3天然气烧嘴:
烧嘴
在炉子不同部位,依据不同的加热制度要求,配置了二种不同型式的天然气烧嘴。
2.4炉两侧设备
在炉体两侧安装有装,出料炉门、采用气动升降机械、与装、出料辊道进行连锁、完成钢管的入炉,出炉。
同时,还设有4个侧开炉门,用于日常观察和操作。
在加热段的两侧各设有两个检修炉门,供检修时出入炉子和运送材料。
2.5.装料系统设备:
2.5.1.炉门升降机械
炉门升降机械性能:
炉门最大行程500mm
炉门最大重量400kg
工作压力0.6Μpa
炉门最大重量400kg
炉门数量:
1(装料炉门)+2(出料炉门)
装料炉门的升降必须与炉子上料辊道连锁,即必须先升起炉门到位后才能允许上料辊道运转钢或倒料退钢。
该炉门既可单独手动操作也可以完全自动控制。
出料炉门也必须与出料悬臂辊道运动连锁,当出钢时,该炉门必须先升到位后才能允许出料辊道运转出钢,并且两炉门能手动控制升,降,停。
2.5.1.1炉内悬臂辊道
作用:
通过电动机带动悬臂辊道旋转,以此将工件传输到位.
炉内悬臂辊道辊道性能:
辊形及传动方式:
V型的悬臂辊,电机传动
辊轴冷却方式:
水冷却
悬臂辊个数:
装料辊道19个,出料辊道20个
2.5.1.3装出料机
装料机
出料机
装料机二组,出料机二组,便于炉内进行单排料或双排料。
2.5.1.4炉内缓冲挡板
弹性挡板
为防止入炉坯料因失控而撞坏炉墙,在装料炉门对面侧墙内设有弹性挡板。
炉内缓冲挡板技术参数设计:
主弹簧直径:
ø30mm
冷却方式:
轴心水冷。
2.6液压系统设备:
2.6.1液压系统的功能
根据对步进梁式再加热炉中升降液压系统的设计任务和工况分析,该步进梁式再加热炉是由多缸控制的工作回路,因此多缸工作控制是该加热炉要解决的主要问题,速度、压力的调节、换向、平衡、顺序动作是该加热炉液压系统设计的核心。
2.6.2液压系统的性能
工作压力25MPa
工作油泵P=31.5MPaQ=207.2L/min
工作油泵电动机110KW1480r/minAC:
380
循环冷却过滤油泵Pmax=1MPaQ=415L/min
循环冷却油泵电动机5.5KW1440r/minAC:
380
油箱容积8000L
电加热器4KWAC:
380
冷却液冷却面积50㎡P=1.5MPa水消耗量45m3/h
工作介质L-HM46液压油
工作油温30℃-50℃
过滤器Q=1000L/min20u
2.7.3液压泵的最高工作压力:
工作压力:
Pp≧p1+Σ△p1
式中Pp——系统的最大工作压力
p1——工作压力
Σ△p1——压力损失
由于该系统元件较多,所以压力损失也比较多。
查«液压系统设计手册»,取△p1=1.5Mpa.
所以:
Pp≧p1+Σ△p1
=25Mpa+1.5Mpa
=26.5Mpa
又因为该系统的应用场合所须的压力较大,从安全角度出发,取系统的最大压力为31.5Mpa.
安全压力:
综上所述,液压系统得安全工作压力取31.5Mpa.
在液压系统控制下,升降液压缸和平移液压缸均有动作,步进梁的升降运动是通过四个升降液压缸来实现的。
升降液压缸推动带上下轮组的升降框架,下轮组在斜轨上面作上下运动,通过上下轮组带动水平框架作升降运动。
在此过程中,水平运动液压缸被锁定。
步进梁的进、退运动(即平移运动)是通过2个液压缸来实现的。
它直接作用于平移框架上,使之在升降框架的上轮组上作平移运动。
在此过程中,升降运动的液压缸被锁定。
升降和平移框架的定心倒像是借助于安装在框架中心线升降定心导向轮和水平导向轮来实现的。
2.7.4干油润滑系统:
所有轴承润滑都采用1号极压锂基润滑脂。
使用干油集中润滑装、出料辊道及炉底机械。
此系统使用1套电动终端式干油集中润滑系统。
三、加热炉区域内工艺流程简述
3.1装料控制:
当炉内装料辊道上无料,并且上料区提供了坯料待装信号及其坯料长度数据时,开启1#装料炉门至上位。
而后向上料区发出装料启动信号。
当坯料前端遮蔽装料炉门外的光电开关至尾端开止,通过编码器的计数实现动态测长,同时向上料区发出装料结束信号。
根据坯料长度及对中布料的要求,计算出所装坯料还需运行的距离。
待坯料运行距目标为1.5mm时,炉内装料辊道由高速减至低速,继续运行到目标位停止。
同时关闭1#装料炉门至下位。
当需要倒料时,先向上料区发出倒料启动信号。
并将1#装料炉门打开到上限位,同时炉内装料辊道与炉外上料辊道同步反向慢速运转至到了结束信号(当坯料尾端离开光电开关时)发出停止信号。
3.2步进移钢过程:
装料机将悬臂辊道上钢管拖上固定梁后,步进梁由原点进行一次正循环运动(升、进、降、退)。
将钢管向前移送一个齿距,直至出料位等待出料。
3.3出料控制:
当炉内最后料位有料时,向轧线区发出等待出刚信号。
当轧线区发出要钢信号时,出料机由原位上升,出料机上升到位后延时0.5s(可调)下降到位,出料辊道加速启动至高速正向运转出料,并且随时根据轧线区要求出料速度变化的具体数据,进行炉内除料辊道速度随动控制至轧线区出钢结束信号(坯料尾端通过处料炉门外金属检测器)发出信号为止。
而炉内除料辊道恢复低速空转。
当事故倒料时,轧线区发出事故倒料信号。
炉区解除连锁约束后,反馈允许信号,同时炉内出料辊道与出料炉门外辊道同步反向慢运转至手动操作停止。
3.4坯料直通控制:
当轧线区发出坯料直通等待信号,且炉内出料辊道上无料时,开启2#装料炉门及出料炉门至上位。
炉内出料辊道由低速空转加速启动至高速正向运转出料,并且随时根据轧线区要求出料速度变化的具体数据,进行炉内出料辊道速度随动控制至轧线区出钢结束信号(坯料尾端通过出料炉门外热金属检测器)发出停止信号。
同时关闭出料炉门至下位,而炉内出料辊道恢复低速空转。
3.5炉区等待:
当轧线区因客观情况暂时无法要料时,炉区可进行原地踏步操作,步进梁由原位点(后下位)开始逆循环(水平40mm),直至下一个出钢动作开始回位。
四、炉区机械设备控制操作
根据生产和维修(或调试)的不同需要有下列不同的操作方式:
——自动:
由PLC按照预定的程序和时序执行,进行自动生产。
——半自动:
由人工按照生产的要求,用操作台上的开关,按照设备功能分区或通过PLC按照预定的程序和时序,进行生产。
——手动:
由人工按照生产的要求,用操作台上的开关,通过PLC对炉区单体设备进行操作生产。
——机旁检修手动:
人工在设备旁或设备附近的操作点,用操作开关进行检修操作。
]
炉区机械设有主操作台,若干机旁操作箱:
4.2步进梁机旁操作箱
步进梁机旁手动操作箱的操作和显示-步进梁升、进、降退四个按钮及点动/单动转换开关(点动-按钮压下及以低速运行至按钮松开时停止。
单动-按钮按下一次即完成一次工艺运行。
);正常/调试转换开关(正常-系统接受PLC动作指令,封闭手动操作;调试-仅客站外机旁手动操作箱操作,封闭其他处操作。
)允许机旁操作显示灯;升、进、降、腿按钮相互连锁。
(五)炉区机械设备的检查验收和试车
炉区装料悬臂辊道、炉子步进机械及其液压系统、炉内出料悬臂辊道、拨料机、割炉门升降装置,各种限位开关等检测与控制元件,工业电视监视系统等,必须按照国家有关规定或设计文件提出的技术要求,逐项进行检查验收合格签字确认后,方可进行单机试车和联动试车。
5.1试车前的检测项目
所有炉子的机械运动均采用PLC自动控制,装出料端都设有工业电视,用于监视炉内钢管装,出料的操作。
试车的质量直接影响控制系统的准确性,应给于注重。
检查项目如下:
(1)检查并确认步进梁立柱与炉底开孔之间有无杂物。
(2)检查步进框架(包括框架或步进梁立柱)即步进机械活动部分是否与周围固定的不间有相碰撞的可能。
(3)检查炉内悬臂辊道和炉内缓冲挡板的滚轴与炉墙开孔之间有无杂物,并将杂物清除干净。
轴滚与炉墙开孔之间密封良好,检查确认合格。
(4)检查步进框架下面的平轨道是否干净,并将清理干净后,涂上黄油。
(5)检查液压管道和液压缸的连接是否正确,密封状况合格。
将轮子的轮缘表面清理干净。
(6)检查润滑油管与各润滑点的连接是否正确,各润滑点是否已住满干油,确认润滑站已经可正常投入使用。
(7)检查确认液压站各设备安装完毕合格。
(8)检查和维护炉子热工仪表,保证仪表能长期稳定运转
5.2机械设备的单机试车
炉区机械设备包括油炉内装料悬臂辊道]、步进机械、炉内出料悬臂辊道、拨料机和炉门升降装置等,应对逐个设备的应具有的功能,应达到的技术参数,按设计要求和有关的规范规定进行单机试运转,逐项检查验收。
单机试车采用手动点动方式,可将运行的全过程,分成几个环节进行,然后再连续运转,以步进机械为例说明如下:
(1)将步进机械的水平液压港点动一个往返行程要检查运行的平稳性和最大行程是否达到要求,然后再进行数次往返运动。
(2)将升降缸点动一个往返行程要检查运行的平稳性和最大行程是否达到要求,然后再进行数次往返运动。
(3)拨料机手动数次,调整后确认送钢行程正常。
(4)启动炉内装、出悬臂辊道,做正传、反转、升速、降速、停止操作,确认转动灵活,工作可靠为止。
(5)上述试车合格后,在进行半自动试车,作数次步进陆炉底的正循环和逆循环动作,达到运行平稳。
(6)联动试车
联动试车是将上料系统,炉子步进机械、出料系统共同配合进行的连续动作操作,其目的是检查各部分运转是否正常,连锁关系是否正常,并且在联动试车后期应采用冷态有负荷方式进行。
联动试车后应调整各个设备的运行速度和运行时间,直到相互协调满足设计要求为止。
九、谢词
四年的大学学习,让我对机械设计与制造方面的知识有了一个系统而又