UG设计端盖.docx
《UG设计端盖.docx》由会员分享,可在线阅读,更多相关《UG设计端盖.docx(121页珍藏版)》请在冰豆网上搜索。
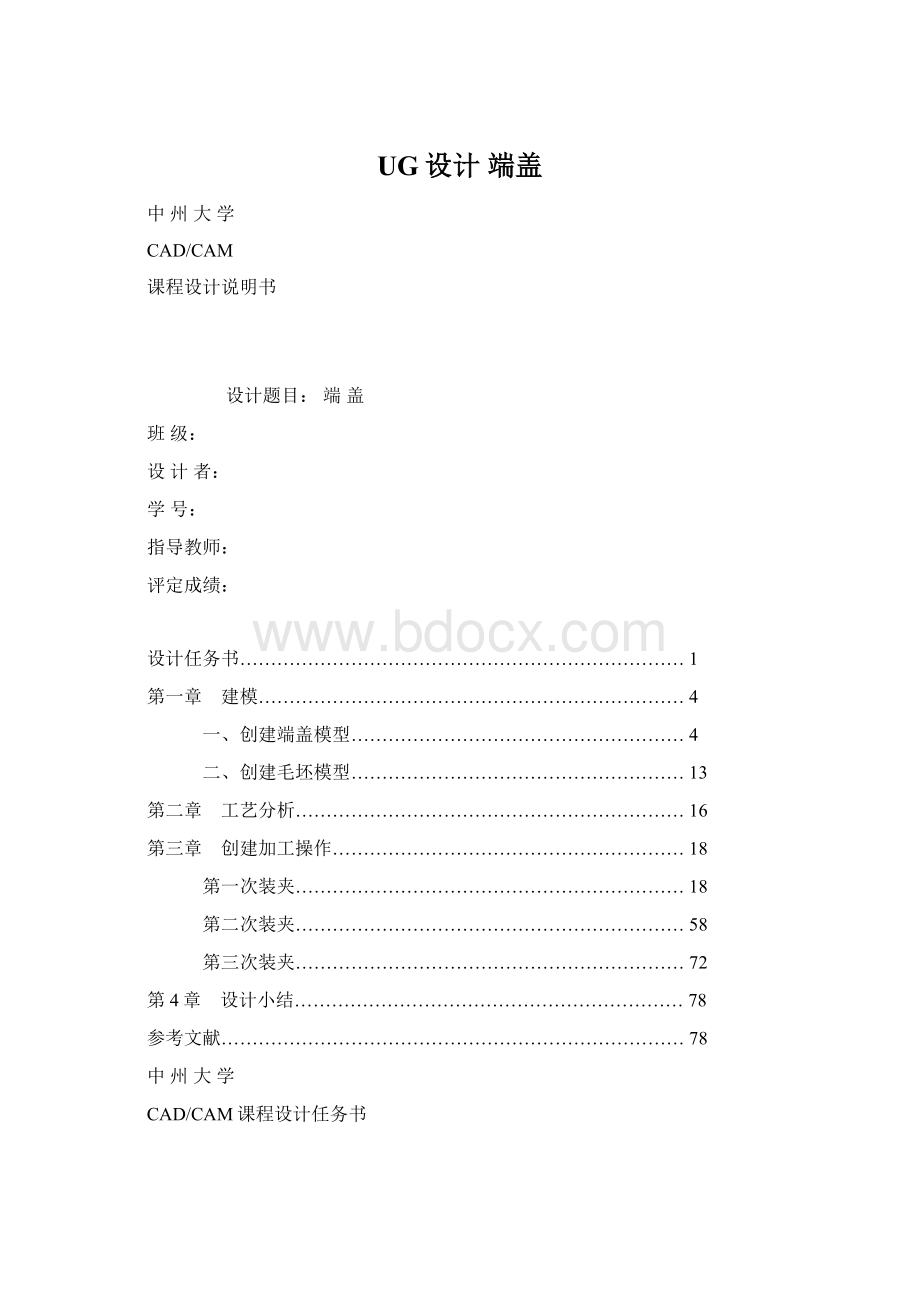
UG设计端盖
中州大学
CAD/CAM
课程设计说明书
设计题目:
端盖
班级:
设计者:
学号:
指导教师:
评定成绩:
设计任务书………………………………………………………………1
第一章 建模……………………………………………………………4
一、创建端盖模型………………………………………………4
二、创建毛坯模型………………………………………………13
第二章 工艺分析………………………………………………………16
第三章 创建加工操作…………………………………………………18
第一次装夹………………………………………………………18
第二次装夹………………………………………………………58
第三次装夹………………………………………………………72
第4章 设计小结………………………………………………………78
参考文献…………………………………………………………………78
中州大学
CAD/CAM课程设计任务书
设计题目:
端盖
设计要求
1、总体介绍:
设计包括CAD与CAM两大模块,重点在于CAM。
2、具体要求:
根据平面图建模,并对该零件上所有能够铣、钻的表面进行加工。
完成指定题目的设计后,要求每人编写说明书一份(包括封面、目录、设计任务书、正文、设计心得与体会、参考资料等七部分,可以打印,请上交前自己检查是否缺项)。
同时上交电子稿与相应prt文件。
正文应包括:
零件的建模过程、毛坯的建模过程、零件工艺分析与编制的工艺过程、具体加工过程(每个操作的创建详细过程,要求说明各个参数是如何配置的、每个操作生成的刀轨)、车间工艺文档
特别提醒:
不接收未经同意擅自更改题目的设计,不接收完全相同的设计。
3、时间要求:
2011年11月15日前交上
第1章 建模
一、创建端盖模型
1.新建部件文件新建一个名称为duangai200925090215的部件文件。
1)启动UG6.0,选择“文件/新建”命令,弹出“新建”对话框。
2)如图1-1所示,在“新建”对话框选择存放新建部件文件的路径,输入文件名为:
duangai200925090215;选择单位为:
毫米。
2.进入建模模块 单击“开始”
图标,选择“建模”命令,进入建模模块。
图1-1
3.创建圆柱体
1)选择“圆柱”命令,弹出“圆柱”对话框。
2)如图1-2所示,在“圆柱”对话框中设置如下参数:
直径:
90;
高度:
20;
3)设置完参数后,单击“确定”按钮,完成圆柱的创建,生成圆柱见图1-3
4.创建圆台1
1)选择“凸台”命令,弹出“凸台”对话框。
2)选择圆柱的上表面作为圆台的放置平面
3)如图1-4所示,在“圆台”对话框设置如下参数:
直径:
52;
高度:
12;
锥角:
0。
4)单击 “凸台”对话框的“确定”按钮,弹出“定位”对话框。
5)单击定位对话框的
(点到点)图标,弹出“点到点”对话框,提示选择目标边。
6)选择圆柱上表面的圆周作为目标边,如图1-5所示。
7)此时弹出“设置圆弧的位置”对话框,单击“选择圆弧中心”按钮,完成圆台的创建,生成圆台如图1-6所示。
图1-2 图1-3
图1-4 图1-5
图1-6 图1-7
5.创建圆台2
1)选择“凸台”命令,弹出“凸台”对话框。
2)选择圆柱的下表面作为圆台的放置平面
3)如图1-4所示,在“凸台”对话框设置如下参数:
直径:
55;
高度:
5;
锥角:
0。
4)单击 “凸台”对话框的“确定”按钮,弹出“定位”对话框。
5)单击定位对话框的
(点到点)图标,弹出“点到点”对话框,提示选择目标边。
6)选择圆柱下表面的圆周作为目标边。
7)此时弹出“设置圆弧的位置”对话框,单击“选择圆弧中心”按钮,完成圆台的创建,生成圆台如图1-7所示。
6.创建埋头孔1
1)选择“孔”命令,弹出“孔”对话框。
2)在“孔”对话框中,选择孔类型为:
常规孔;选择形状和尺寸为:
埋头孔;埋头孔直径为:
32;埋头孔角度为:
90;直径为:
29;深度限制为:
值;深度为:
10;尖角为:
0,其他参数保持默认值;如图1-8所示。
此时提示选择孔的放置平面。
3)选择圆台1的上表面作为孔的放置平面。
4)弹出“创建草图”对话框,单击“确定”按钮。
5)进入绘制草图界面,弹出“点”对话框。
6)在“点”对话框中,选择类型为:
圆弧中心/椭圆中心/球心;此时提示选择点位置。
7)选择圆台1的上表面的圆心,单击“点”对话框“确定”按钮。
8)单击“完成草图”按钮,退出草图任务环境。
9)单击“孔”对话框的“确定”按钮,完成埋头孔1的创建,生成的埋头孔如图1-9所示。
7.创建简单孔2
1)选择“孔”命令,弹出“孔”对话框。
2)在“孔”对话框中,选择孔类型为:
常规孔;选择形状和尺寸为:
简单孔;直径为:
35;深度限制为:
值;深度为:
5;尖角为:
0,其他参数保持默认值;如图1-10所示。
此时提示选择孔的放置平面。
3)选择圆台2的下表面作为孔的放置平面。
4)弹出“创建草图”对话框,单击“确定”按钮。
5)进入绘制草图界面,弹出“点”对话框。
6)在“点”对话框中,选择类型为:
圆弧中心/椭圆中心/球心;此时提示选择点位置。
7)选择圆台2的下表面的圆心,单击“点”对话框“确定”按钮。
图1-8 图1-9
图1-10 图1-11
8)单击“完成草图”按钮,退出草图任务环境。
9)单击“孔”对话框的“确定”按钮,完成简单孔2的创建,生成的简单孔如图1-11所示。
8.创建沉头孔3
1)选择“孔”命令,弹出“孔”对话框。
2)在“孔”对话框中,选择孔类型为:
常规孔;选择形状和尺寸为:
沉头孔;沉头孔直径为:
11;沉头孔深度为:
5;直径为:
7;深度限制为:
贯通体,其他参数保持默认值;如图1-12所示。
此时提示选择孔的放置平面。
3)选择圆柱的上表面作为孔的放置平面。
4)弹出“创建草图”对话框,单击“确定”按钮。
5)进入绘制草图界面,弹出“点”对话框。
6)在“点”对话框中,选择类型为:
自动判断的点;在坐标选项中选择为:
相对于WCS;XC为:
35;YC为:
0;ZC为:
0;单击“点”对话框“确定”按钮,如图1-13所示。
7)单击“完成草图”按钮,退出草图任务环境。
8)单击“孔”对话框的“确定”按钮,完成沉头孔3的创建,生成的沉头孔如图1-14所示。
9.创建螺纹孔4
1)选择“孔”命令,弹出“孔”对话框。
2)在“孔”对话框中,选择孔类型为:
螺纹孔;空方向为:
沿矢量;选择形状和尺寸为:
Ssize:
M5×0.8;螺纹深度为:
10;尺寸栏中深度限制为:
值;深度为:
12,其他参数保持默认值;如图1-15所示。
此时提示选择孔的放置平面。
3)选择圆台1的上表面作为孔的放置平面。
4)弹出“创建草图”对话框,单击“确定”按钮。
5)进入绘制草图界面,弹出“点”对话框。
6)在“点”对话框中,选择类型为:
自动判断的点;在坐标选项中选择为:
相对于WCS;XC为:
0;YC为:
-21;ZC为:
0;单击“点”对话框“确定”按钮,如图1-16所示。
7)单击“完成草图”按钮,退出草图任务环境。
8)单击“孔”对话框的“确定”按钮,完成螺纹孔4的创建,生成的螺纹孔如图1-17所示。
图1-12 图1-13
图1-14 图1-15
图 1-16 图1-17
10.创建螺纹孔5
1)选择“孔”命令,弹出“孔”对话框。
2)在“孔”对话框中,选择孔类型为:
螺纹孔;空方向为:
沿矢量;选择形状和尺寸为:
Sice:
M12×1.75;螺纹深度为:
12;尺寸栏中深度限制为:
值;深度为:
31,其他参数保持默认值。
此时提示选择孔的放置平面。
3)单击位置栏中图标
。
4)弹出“创建草图”对话框,单击“确定”按钮。
5)进入绘制草图界面,弹出“点”对话框。
6)在“点”对话框中,选择类型为:
自动判断的点;在坐标选项中选择为:
相对于WCS;XC为:
0;YC为:
45;ZC为:
10;单击“点”对话框“确定”按钮。
7)单击“完成草图”按钮,退出草图任务环境。
8)单击“孔”对话框的“确定”按钮,完成螺纹孔4的创建,生成的螺纹孔如图1-18所示。
图1-18 图1-19 图1-20
11.创建简单孔6
1)选择“孔”命令,弹出“孔”对话框。
2)在“孔”对话框中,选择孔类型为:
常规孔;选择形状和尺寸为:
简单孔;直径为:
16;深度限制为:
值;深度为:
30;尖角为:
0,其他参数保持默认值。
此时提示选择孔的放置平面。
3)选择沉头孔1的底面作为孔的放置平面。
4)弹出“创建草图”对话框,单击“确定”按钮。
5)进入绘制草图界面,弹出“点”对话框。
6)在“点”对话框中,选择类型为:
圆弧中心/椭圆中心/球心;此时提示选择点位置。
7)选择沉头孔1的底面的圆心,单击“点”对话框“确定”按钮。
8)单击“完成草图”按钮,退出草图任务环境。
9)单击“孔”对话框的“确定”按钮,完成简单孔6的创建,生成的简单孔如图1-19所示。
12.创建简单孔7
1)选择“孔”命令,弹出“孔”对话框。
2)在“孔”对话框中,选择孔类型为:
常规孔;选择形状和尺寸为:
简单孔;直径为:
10;深度限制为:
值;深度为:
10;尖角为:
90,其他参数保持默认值。
此时提示选择孔的放置平面。
3)选择圆台2的下表面作为孔的放置平面。
4)弹出“创建草图”对话框,单击“确定”按钮。
5)进入绘制草图界面,弹出“点”对话框。
6)在“点”对话框中,选择类型为:
自动判断的点;在坐标选项中选择为:
绝对;X为:
0;Y为:
20;Z为:
-5;单击“点”对话框“确定”按钮。
7)单击“完成草图”按钮,退出草图任务环境。
8)单击“孔”对话框的“确定”按钮,完成简单孔7的创建,生成的简单孔如图1-20所示。
13.创建沉头孔3的圆形阵列
1)选择“插入/关联复制/实利特征”命令,弹出如图1-21所示的“实例”对话框。
2)单击“实例”对话框中的“圆形阵列”按钮,弹出如图1-22所示的“实例”对话框。
3)选择沉头孔3的特征,如图1-23所示。
4)单击“实例”对话框中的“确定”按钮,弹出新的“实例”对话框。
5)在新的“实例”对话框中选择方法为:
相同;数字为:
6;角度为:
60,如图1-24所示,单击“确定”按钮,弹出新的“实例”对话框。
6)在新的“实例”对话框中单击“基准轴”按钮,弹出“选择一个基准轴”对话框,如图1-25所示,提示选择基准轴,在所创建的模型中选择Z轴,单击“确定”按钮。
弹出“创建实例”对话框。
7)在“创建实例”对话框中单击“确定”按钮,完成沉头孔3的圆形阵列的创建,生成的沉头孔3圆形阵列如图1-26所示。
图1-21
图1-22 图1-23
图1-24 图1-25
图1-26 图1-27 图1-28
14.创建螺纹孔4的圆形阵列
1)选择“插入/关联复制/实利特征”命令,弹出如图1-21所示的“实例”对话框。
2)单击“实例”对话框中的“圆形阵列”按钮,弹出如图1-22所示的“实例”对话框。
3)选择螺纹孔4的特征。
4)单击“实例”对话框中的“确定”按钮,弹出新的“实例”对话框。
5)在新的“实例”对话框中选择方法为:
相同;数字为:
3;角度为:
120,单击“确定”按钮,弹出新的“实例”对话框。
6)在新的“实例”对话框中单击“基准轴”按钮,弹出“选择一个基准轴”对话框,如图1-25所示,提示选择基准轴,在所创建的模型中选择Z轴,单击“确定”按钮。
弹出“创建实例”对话框。
7)在“创建实例”对话框中单击“确定”按钮,完成简单孔4的圆形阵列的创建,生成的螺纹孔4圆形阵列如图1-27所示。
15.边倒圆
1)选择“插入/细节特征/边倒圆”命令,弹出“边倒圆”对话框。
2)在“边倒圆”对话框中,设置Rradius1为:
2,选中的边为简单孔2的底面圆周。
3)单击“边倒圆”对话框中的“确定”按钮。
完成简单孔2边倒圆的创建。
生成的倒圆如图1-28所示。
至此,完成了整个端盖的创建。
单击“保存”按钮
,将文件“duangai200925090215.prt”单独保存一份以备后续使用。
二、创建毛坯模型
1.新建部件文件新建一个名称为duangaimaopi1的部件文件。
1)选择“文件/新建”命令,弹出“新建”对话框。
2)在“新建”对话框选择存放新建部件文件的路径,输入文件名为:
duangaimaopi1;选择单位为:
毫米。
2.进入建模模块 单击“开始”
图标,选择“建模”命令,进入建模模块。
3.创建圆柱体
1)选择“圆柱”命令,弹出“圆柱”对话框。
2)所示,在“圆柱”对话框中设置如下参数:
直径:
94;
高度:
24;
3)设置完参数后,单击“确定”按钮,完成圆柱的创建,生成圆柱。
图2-1 图2-2
4.创建圆台1
1)选择“凸台”命令,弹出“凸台”对话框。
2)选择圆柱的上表面作为圆台的放置平面
3)如图3所示,在“圆台”对话框设置如下参数:
直径:
56;
高度:
12;
锥角:
0。
4)单击 “凸台”对话框的“确定”按钮,弹出“定位”对话框。
5)单击定位对话框的
(点到点)图标,弹出“点到点”对话框,提示选择目标边。
6)选择圆柱上表面的圆周作为目标边。
7)此时弹出“设置圆弧的位置”对话框,单击“选择圆弧中心”按钮,完成圆台的创建,生成圆台如图2-1所示。
5.创建圆台2
1)选择“凸台”命令,弹出“凸台”对话框。
2)选择圆柱的下表面作为圆台的放置平面
3)在“凸台”对话框设置如下参数:
直径:
59;
高度:
5;
锥角:
0。
4)单击 “凸台”对话框的“确定”按钮,弹出“定位”对话框。
5)单击定位对话框的
(点到点)图标,弹出“点到点”对话框,提示选择目标边。
6)选择圆柱下表面的圆周作为目标边。
7)此时弹出“设置圆弧的位置”对话框,单击“选择圆弧中心”按钮,完成圆台的创建,生成圆台如图2-2所示。
6.创建简单孔1
1)选择“孔”命令,弹出“孔”对话框。
2)在“孔”对话框中,选择孔类型为:
常规孔;选择形状和尺寸为:
简单孔;直径为:
28;深度限制为:
值;深度为:
8;尖角为:
0,其他参数保持默认值。
此时提示选择孔的放置平面。
3)选择圆台1的上表面作为孔的放置平面。
4)弹出“创建草图”对话框,单击“确定”按钮。
5)进入绘制草图界面,弹出“点”对话框。
6)在“点”对话框中,选择类型为:
圆弧中心/椭圆中心/球心;此时提示选择点位置。
7)选择圆台1的上表面的圆心,单击“点”对话框“确定”按钮。
8)单击“完成草图”按钮,退出草图任务环境。
9)单击“孔”对话框的“确定”按钮,完成简单孔1的创建,生成的简单孔如图2-3所示。
7.创建简单孔2
1)选择“孔”命令,弹出“孔”对话框。
2)在“孔”对话框中,选择孔类型为:
常规孔;选择形状和尺寸为:
简单孔;直径为:
12;深度限制为:
贯通体,其他参数保持默认值。
此时提示选择孔的放置平面。
3)选择简单孔1的底面作为孔的放置平面。
4)弹出“创建草图”对话框,单击“确定”按钮。
5)进入绘制草图界面,弹出“点”对话框。
6)在“点”对话框中,选择类型为:
圆弧中心/椭圆中心/球心;此时提示选择点位置。
图2-3 图2-4
7)选择简单孔1的底面的圆心,单击“点”对话框“确定”按钮。
8)单击“完成草图”按钮,退出草图任务环境。
9)单击“孔”对话框的“确定”按钮,完成简单孔2的创建,生成的简单孔如图2-4所示。
8.创建边倒圆
1)选择“边倒圆”命令,弹出“边倒圆”对话框
2)在“边倒圆”对话框中,在Radius1输入1.5
3)在绘图区选中端盖毛坯的所有棱
4)单击“边倒圆”对话框的“确定”按钮,完成边倒圆的创建,如图2-5所示。
图2-5
至此,完成了整个端盖毛坯的创建。
单击“保存”按钮
,将文件“duangaimaopi1.prt”单独保存一份以备后续使用。
第二章 工艺分析
1.确定装夹方式由于毛坯的各侧面及底面均不符合零件的要求需要加工,根据零件形状可确定需分三次装夹。
第一次装夹加工φ90圆柱的上表面,φ52的侧面及端面,φ32的埋头孔,φ16的通孔,φ7的沉头孔,M5的螺纹孔;第一次装夹采用三爪卡盘装夹方式。
第二次装夹加工φ90的侧面及下表面,φ55的侧面及端面,φ35的孔;第二次装夹采用三爪卡盘装夹方式。
第三次装夹加工φ90圆柱侧面的螺纹孔;第三次装夹采用三爪卡盘装夹方式。
2.确定加工坐标系原点为了便于加工时对刀,第一次装夹,加工坐标系原点设置在零件顶面的中心;第二次装夹,加工坐标系原点设置在零件底面的中心;第三次装夹,加工坐标系原点设置在零件的几何中心。
3.确定工步
第一次装夹:
分析图可得,可用φ16的平底铣刀对φ90圆柱的上表面,φ52的侧面及端面,φ32的埋头孔进行粗加工和精加工。
对C1的倒角用φ40的90°锪刀加工至要求尺寸。
对φ16的通孔,用φ15.5和φ16镗刀镗孔至要求尺寸。
对φ7的通孔,为了保证加工精度,先用φ3的中心钻打定位孔,然后用φ6.8的麻花钻预钻孔,最后用φ7的机用铰刀铰孔至要求尺寸。
对φ11的沉头孔,用φ11的平底镗孔刀加工。
对M5的螺纹孔,为了保证加工精度,先用φ3的中心钻打定位孔,然后用φ4麻花钻预钻孔,最后用M5的螺纹刀加工至要求尺寸。
具体工步安排见表2-1。
表2-1
序号
加工工步
加工方式
刀具
加工余量
主轴速度
进给速度
1
端盖外表面粗加工
PLANAR_MILL
Φ16平底刀
0.2mm
1000rpm
350mmpm
2
Φ32腔体粗加工
PLANAR_MILL
Φ16平底刀
0.2mm
1000rpm
350mmpm
3
端盖外表面粗精加工
FINISH_WALLS
Φ16平底刀
0
1000rpm
150mmpm
4
Φ32腔体侧面精加工
FINISH_WALLS
Φ16平底刀
0
1000rpm
150mmpm
5
Φ32腔体底面精加工
FINISH_WALLS
Φ16平底刀
0
1000rpm
150mmpm
6
φ7的定位孔加工
DRILLING
φ3中心钻
1200rpm
60mmpm
7
φ7的预钻孔加工
DRILLING
φ6.8麻花钻
550rpm
40mmpm
8
φ7的铰孔加工
DRILLING
φ7机用铰刀
300rpm
30mmpm
9
φ11沉头孔扩孔加工
DRILLING
Φ11平底镗孔刀
300rpm
30mmpm
10
Φ16孔镗孔粗加工
DRILLING
Φ15.5粗镗刀
300rpm
40mmpm
11
Φ16孔镗孔精加工
DRILLING
Φ16精镗刀
400rpm
40mmpm
12
M5的定位孔加工
DRILLING
φ3中心钻
1200rpm
60mmpm
13
M5的预钻孔加工
DRILLING
φ4的麻花钻
550rpm
40mmpm
14
M5的攻丝加工
DRILLING
M5螺纹刀
500rpm
200mmpm
15
倒角1×45°的加工
DRILLING
Φ40锪刀
200rpm
18mmpm
第二次装夹:
分析图可得,可用φ16的平底铣刀对φ90圆柱的上表面级侧面和φ52的侧面及端面进行加工,φ35的圆形型腔可用一把φ16R2的圆角刀进行加工。
对φ10的孔,为了保证加工精度,先用φ3的中心钻打定位孔,然后用φ9.8的麻花钻预钻孔,最后用φ10的机用铰刀铰孔至要求尺寸。
具体工步安排见表2-2。
表2-2
序号
加工工步
加工方式
刀具
加工余量
主轴速度
进给速度
1
端盖外表面粗加工
PLANAR_MILL
Φ16平底刀
0.2mm
1000rpm
350mmpm
2
Φ35腔体粗加工
PLANAR_MILL
Φ16圆角刀
0.2mm
1000rpm
350mmpm
3
Φ90侧壁粗加工
PLANAR_MILL
Φ16平底刀
0.2mm
1000rpm
150mmpm
4
端盖外表面粗精加工
FINISH_WALLS
Φ16平底刀
0
1000rpm
150mmpm
5
Φ90侧壁精加工
FINISH_WALLS
Φ16平底刀
0
1000rpm
150mmpm
6
Φ32腔体侧面精加工
FINISH_WALLS
Φ16圆角刀
0
1000rpm
150mmpm
7
Φ32腔体底面精加工
FINISH_WALLS
Φ16圆角刀
0
1000rpm
150mmpm
8
Φ10的定位孔加工
DRILLING
φ3中心钻
1200rpm
60mmpm
9
φ10的预钻孔加工
DRILLING
Φ9.8麻花钻
550rpm
40mmpm
10
φ10的铰孔加工
DRILLING
Φ10机用铰刀
300rpm
30mmpm
第三次装夹:
分析图可得,对M12的螺纹孔,为了保证加工精度,先用φ3的中心钻打定位孔,然后用φ10.5麻花钻预钻孔,最后用M12的螺纹刀加工至要求尺寸。
具体工步安排见表2-3。
表2-3
1
M5的定位孔加工
DRILLING
φ3中心钻
1200rpm
60mmpm
2
M5的预钻孔加工
DRILLING
Φ10.5麻花钻
550rpm
40mmpm
3
M5的攻丝加工
DRILLING
M12螺纹刀
500rpm
200mmpm
第三章 第一次装夹
打开第一章中创建的部件“duangai200925090215”
一、选择加工环境
1.进入加工模块 单击“开始”图标,选择“加工”命令,进入自动加工模块,弹出“加工环境”对话框。
2.选择加工环境
1)在“加工环境”对话框的“要创建的CAM设置”列表框中选择模板文件“mill_planar”(平面铣)。
如图3-1所示。
2)单击“确定”按钮,进入加工环境。
图3-1
二、创建父节点组
1.