电动汽车拆解.docx
《电动汽车拆解.docx》由会员分享,可在线阅读,更多相关《电动汽车拆解.docx(20页珍藏版)》请在冰豆网上搜索。
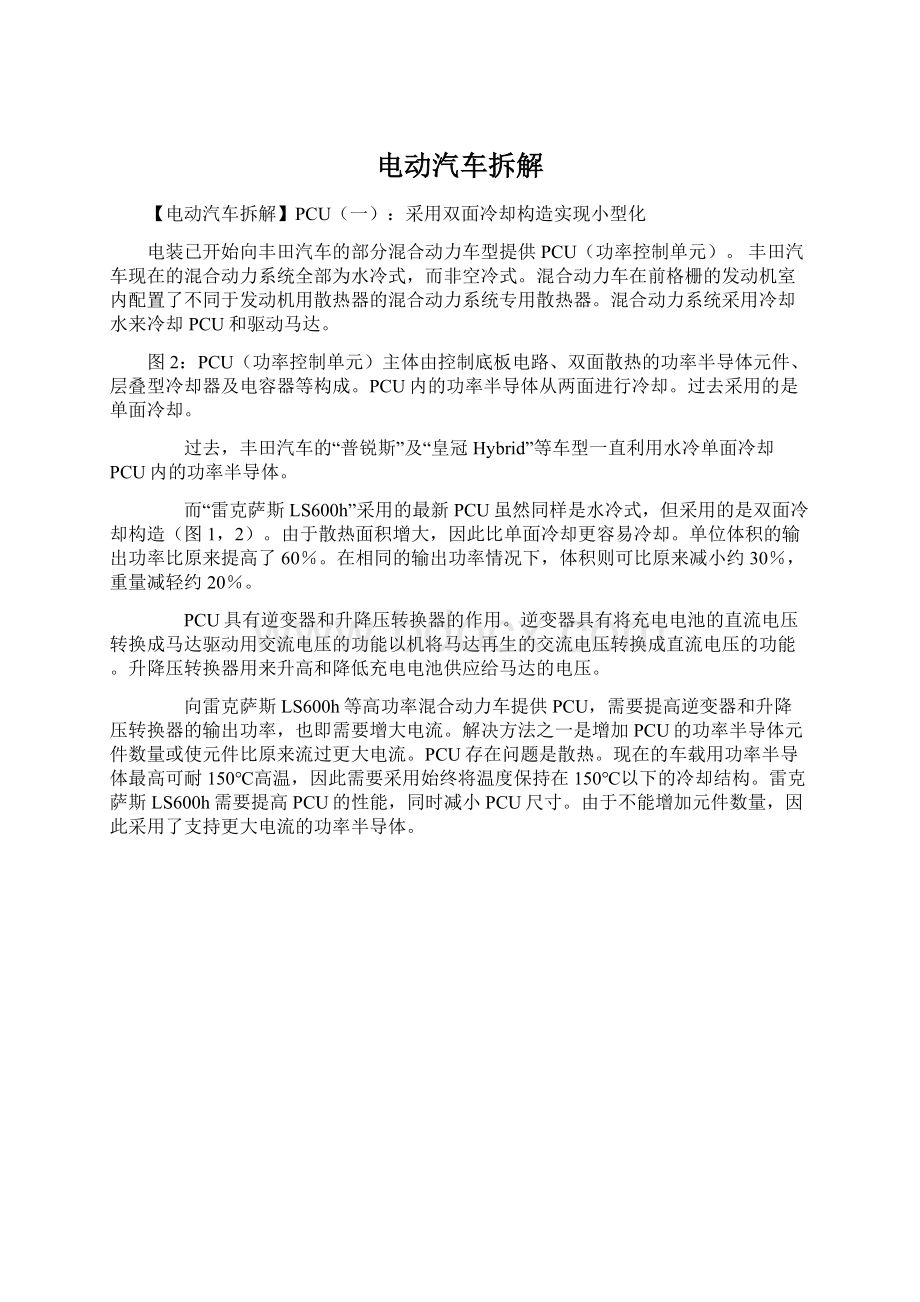
电动汽车拆解
【电动汽车拆解】PCU
(一):
采用双面冷却构造实现小型化
电装已开始向丰田汽车的部分混合动力车型提供PCU(功率控制单元)。
丰田汽车现在的混合动力系统全部为水冷式,而非空冷式。
混合动力车在前格栅的发动机室内配置了不同于发动机用散热器的混合动力系统专用散热器。
混合动力系统采用冷却水来冷却PCU和驱动马达。
图2:
PCU(功率控制单元)主体由控制底板电路、双面散热的功率半导体元件、层叠型冷却器及电容器等构成。
PCU内的功率半导体从两面进行冷却。
过去采用的是单面冷却。
过去,丰田汽车的“普锐斯”及“皇冠Hybrid”等车型一直利用水冷单面冷却PCU内的功率半导体。
而“雷克萨斯LS600h”采用的最新PCU虽然同样是水冷式,但采用的是双面冷却构造(图1,2)。
由于散热面积增大,因此比单面冷却更容易冷却。
单位体积的输出功率比原来提高了60%。
在相同的输出功率情况下,体积则可比原来减小约30%,重量减轻约20%。
PCU具有逆变器和升降压转换器的作用。
逆变器具有将充电电池的直流电压转换成马达驱动用交流电压的功能以机将马达再生的交流电压转换成直流电压的功能。
升降压转换器用来升高和降低充电电池供应给马达的电压。
向雷克萨斯LS600h等高功率混合动力车提供PCU,需要提高逆变器和升降压转换器的输出功率,也即需要增大电流。
解决方法之一是增加PCU的功率半导体元件数量或使元件比原来流过更大电流。
PCU存在问题是散热。
现在的车载用功率半导体最高可耐150℃高温,因此需要采用始终将温度保持在150℃以下的冷却结构。
雷克萨斯LS600h需要提高PCU的性能,同时减小PCU尺寸。
由于不能增加元件数量,因此采用了支持更大电流的功率半导体。
图3:
过去的PCU构成(单面冷却)每个功率半导体元件流过200A,元件散热措施设想采用单面冷却时。
图4:
新型PCU的构成(双面冷却)通过采用高性能功率半导体,每个元件流过300A以上的电流。
采用支持大电流的元件,减少元件数量以实现小型化。
通过双面冷却进行散热。
(
这样,单面冷却就不足以解决大电流功率半导体的散热问题,因此采用了双面冷却结构。
过去,每个元件可流过200A的电流,而雷克萨斯LS600h采用了每个元件可流过300A以上电流的高性能功率元件(图3、4)。
由此逆变器和升降压转换器均减少了功率半导体的数量。
新型功率半导体为富士电机元件科技制造的产品。
(未完待续:
特约撰稿人:
金子高久,电装EHV机器技术部组长)
【电动汽车拆解】PCU
(二):
实现了与铅蓄电池相当的尺寸
雷克萨斯LS600h是在高级轿车“雷克萨斯LS460”基础上追加混合动力系统而成。
如果是混合动力专用车,PCU的尺寸或许会更大一些,而雷克萨斯LS600h最优先强调的就是要减小PCU的尺寸。
LS460将置于车辆前部的铅蓄电池移至车辆后部,PCU的尺寸只能与空出的铅蓄电池容积相当。
原来的功率半导体和冷却器的构造由上往下依次为功率半导体元件、绝缘板、散热板(铜或铜合金)、冷却板(铝合金压铸而成)(图5)。
重叠冷却板制成的是冷却器。
使冷却水在冷却器中循环,通过散热板,冷却半导体元件。
图5:
单面冷却的构成在绝缘板上面配置功率半导体元件。
热量通过绝缘板,传到散热板,由冷却器散热。
而新开发的PCU由散热板、绝缘板和冷却板夹在功率半导体的两侧而成(图6)。
其中,功率半导体和散热板用树脂封装。
功率半导体与信号输入端子之间通过引线键合相连。
另外,为确保引线键合高度方向的空间,在功率半导体的一侧配置了导电垫片。
图6:
新型双面冷却的构成冷却功率半导体的两侧。
为提高热传导,在功率半导体旁边依次配置散热板、绝缘板、冷却器。
为比单面冷却进一步提高热传导率,此次新采用了使功率半导体的热量比起绝缘板,先行向散热板传导的构造。
另外,冷却板跟原来一样,由铝材料制成,不过由压铸件更换成了热传导率高的冲压材料。
为实现双面冷却,制作了交叉重叠功率半导体和冷却板的层叠型(图7)构造。
层叠型的优点在于可以减小PCU的面积。
过去的单面冷却构造在一个封装中集成有多个功率半导体。
通过采用多个封装,提高PCU的性能,不过并不适合细致调整功率半导体数量的设计方案。
图7:
冷却器为层叠型(a)双面冷却的PCU采用的是冷却器的冷却板与半导体交叉层叠的层叠结构。
(b)现在采用该结构的只有雷克萨斯LS600h和RX450h,具有灵活性,可根据车型需要的输出功率改变层叠枚数进行设计。
将来还有望应用于普及车型。
另外,要提高输出功率,需要将封装呈面状横向接合在一起,因此存在面积增大、难以配备于汽车使用的问题。
此次的构造可根据混合动力车的输出功率选择功率半导体元件的数量。
并且,由于是与冷却板交叉重叠功率半导体的层叠型构造,即使功率半导体数量增加,在设计上也能够减小面积。
新型双面冷却构造的采用车型目前只有最高端车型雷克萨斯LS600h和2009年春季上市的“雷克萨斯RX450h”,此外还能应用于输出功率较低的混合动力系统。
(未完待续:
特约撰稿人:
金子高久,电装EHV机器技术部组长)
【电动汽车拆解】PCU(三):
使半导体与冷却板紧密贴合
双面冷却构造的功率半导体需要在制造方法和维持冷却性能方面下工夫。
新型冷却系统采用的交叉层叠功率半导体和冷却板的构造,因此半导体和冷却板需要始终接触在一起。
制造时首先重叠冷却板制成冷却器,然后重叠功率半导体,插入冷却器中(图8)。
图8:
PCU的制造工序在层叠型冷却器中插入功率半导体元件。
通过向冷却器两侧加压,使冷却板与半导体元件紧密贴合。
最后,用板簧对冷却器加压,维持冷却性能。
为便于插入半导体,可增大冷却板与冷却板的间隔。
但是,如果间隔过大,冷却板与半导体之间就会留有缝隙,冷却半导体的性能就会降低。
因此,最初先扩大冷却板的间隔,插入半导体后,通过对冷却器两侧加压,使冷却板与半导体紧密贴合。
对冷却器加压时,为防止冷却器破损,采用了冷却板与冷却板之间产生形变的结构(图9)。
通过使冷却器在冷却水不漏的前提下变形,实现了层叠结构。
图9:
层叠型冷却器在生产时变形层叠型冷却器为使半导体元件与冷却板紧密结合,生产时进行加压。
采用了加压时、为使冷却板与冷却板之间的距离缩短而变形的结构。
作为表示双面冷却性能的数据,有热传导率模拟数据和热阻试验数据。
通过热传导模拟,比较了冷却构造中的最热部分(热阻最高的部分)。
模拟结果表明,双面冷却构造比单面冷却构造的热阻可降低约48%。
通过热阻实验数据,比较了功率半导体每个位置的冷却性能(图10(a)。
该实验将功率半导体耐热性上限150℃下的热阻目标值定为W左右。
实验数据控制在上限以下(图10(b)。
另一组热阻试验的数据测量了改变冷却水流速时的热阻。
将功率半导体每个位置(下降侧的1~12)的热阻做成了图表。
数据显示热阻始终在W以下,满足了散热条件(图10(c)。
图10:
采用双面冷却,冷却性能达到目标值以下(a)对PCU的功率半导体,在冷却水入口按顺序贴上序号1~12。
在冷却水入口侧(上升)和出口侧(下降)比较了功率半导体的冷却性能。
(b)热阻值的比较。
冷却水入口侧和出口侧均控制在功率半导体目标值W以下。
(c)改变冷却水流量时的热阻控制在目标值以下
功率半导体的耐热性是一大课题,不过将来该课题有可能得到彻底解决。
比如,现在使用的是Si(硅)晶圆,而用SiC(碳化硅)材料做的话,耐热性将大幅提高,同时还能够通过更大的电流。
另外,现在设计的是水冷式PCU,今后随着气流改善等,或许还需要研究空冷式PCU。
今后的10年将是决定PCU未来走向的关键时期。
(特约撰稿人:
金子高久,电装EHV机器技术部组长)
【电动汽车拆解】DC-DC转换器(四):
提高电压转换效率
TDK已开始向混合动力车及电动汽车提供“DC-DC转换器”。
电动汽车充电电池的电压高达数百伏。
DC-DC转换器将充电电池的电压降至14V,提供给铅蓄电池。
再把铅蓄电池作为电源驱动发动机的辅机类、雨刷及前照灯等器件。
世界首款量产混合动力车的投入使用已经12年。
包括TDK在内,DC-DC转换器单位体积的功率密度逐年提高,估计今后也是这一趋势。
TDK的DC-DC转换器于1997年实际应用于混合动力车。
本田将在现行的“思域混合动力车”和新款Insight上采用(图1)。
还被部分海外厂商应用于混合动力车。
图1:
本田新款混合动力车“Insight”的后座周围采用小型化PCU(功率控制单元)。
原来配置在后座后面,通过小型化,得以配置在行李舱下面。
后座后面可以当作行李舱空间使用。
Insight之所以采用TDK制造的DC-DC转换器,是因为能够满足小型与轻量化的要求。
本田对Insight减小了包括DC-DC转换器和逆变器在内的PCU(功率控制单元)尺寸及镍氢充电电池的尺寸。
这些器件在思域混合动力车中曾配置在后座后面,而在Insight中,却配置在行李舱下面,以使行李舱的可用空间比以前增大。
DC-DC转换器的小型化有利于扩大行李舱容量,降低成本。
Insight上使用的最新款DC-DC转换器与思域混合动力车上配备的原产品相比,重量减轻45%,容积减小5%(图2)。
重量低于1kg。
转换效率确保在90%以上。
图2:
Insight采用的DC-DC转换器将混合动力车配备的数100V的充电电池电压降至铅蓄电池的14V电压。
Insight采用的方式(空冷式)。
省去交流发电机
混合动力车及电动汽车导入DC-DC转换器之后,可省去交流发电机。
交流发电机利用发动机的旋转发电,发出的电为铅蓄电池充电(图3)。
电动汽车的充电电池容量很大。
因此,以充电电池为电源,能够利用DC-DC转换器为铅蓄电池充电。
从而可以省去原来的交流发电机(图4)。
Insight就未配备交流发电机(图5)。
图3:
汽油发动机车配备交流发电机利用发动机转动交流发电机,为铅蓄电池充电。
图4:
混合动力车和电动汽车不需要交流发电机利用DC-DC转换器降低充电电池的电压,为铅蓄电池充电。
图5:
Insight的动力传动系统未配备交流发电机。
使用充电电池和DC-DC转换器,可以不必考虑发动机的转速而为铅蓄电池充电。
原来的汽油发动机车,当发动机转速低时,如果同时使用空调、立体声及车灯等,有时“电池的电量会用尽”。
即使发动机仍在运行,有些条件下也会出现电力不足现象。
而如果像混合动力车和电动汽车这样使用充电电池和DC-DC转换器,便可不必考虑发动机的转速而使用电力。
(未完待续,特约撰稿人:
近藤朋之,TDK电力系统业务集团EV电源部部长)
【电动汽车拆解】DC-DC转换器(五):
保留铅蓄电池
混合动力车和电动汽车按说也能省去铅蓄电池,但实际上还是保留了铅蓄电池(图6)。
Insight也保留了铅蓄电池。
这样做有两大原因。
一是保留铅蓄电池更能够降低整个车辆的成本。
二是确保电源的冗余度。
图6:
包括DC-DC转换器的混合动力车系统构成现在的DC-DC转换器为单向电流,而今后有可能变成双向。
有些车型还追加DC/AC输出端及升压转换器等转换器部件。
铅蓄电池能在短时间内向空调、雨刷及车灯等释放大电流。
如果省去铅蓄电池而将充电电池的电力用于补机类、空调及雨刷等,DC-DC转换器的尺寸势必就要增大,从而使整体成本增加。
铅蓄电池便宜,因此目前将铅蓄电池置换成充电电池还没有成本上的优势。
二是铅蓄电池还有确保向补机类供电的冗余度的作用。
DC-DC转换器出现故障停止供电时,如果没有铅蓄电池,补机类就会立即停止运行。
夜间车灯不亮,雨天雨刷停止运行等,就会影响驾驶。
如果有铅蓄电池,便能够将汽车就近开到家里或者工厂。
今后DC-DC转换器功能改进的方向之一是双向化。
现在使用的DC-DC转换器只是单向改变电压。
现在也存在要求双向的需求。
当充电电池的电力不足时,便可将铅蓄电池的电力输入充电电池,以备紧急之需。
双向化是今后将继续探讨的课题,这也是确保冗余度的方法。
TDK分代开发了DC-DC转换器基本电路(平台)(图7)。
其中包括2001年开始量产的“GEN3”(第3代)、2005年量产的“GEN4”(第4代)、2008年量产的“GEN4.5”(第代)。
现在正在开发的是“GEN5”(第5代)。
根据基本电路,制成符合各汽车公司要求的产品。
图7:
DC-DC转换器的发展蓝图公布了该公司2001年以来的产品。
DC-DC转换器不断小型·轻量化,效率不断提高。
DC-DC转换器不同的代规定了变压器的种类及DC-DC转换器电路的基本构造。
水冷/空冷、端子位置,主体形状等根据采用车型进行设计。
基本构造以严酷环境下的空冷为前提设计。
按产品来看,转换效率由第2代到第5代一直在提高(图8)。
电流为10A时,转换效率分别为约84%(第2代)、约86%(第4代)、约89%(第代)。
电流为70A时,转换效率由约86%(第2代)提高到约88%(第代)。
预计下一代第5代将超过90%。
(未完待续,特约撰稿人:
近藤朋之,TDK电力系统业务集团EV电源部部长)
图8:
DC-DC转换器的效率效率逐代进化。
最新一代的转换效率为90%左右。
下一代将超过90%。
【电动汽车拆解】DC-DC转换器(六):
DC-DC转换器的性能
DC-DC转换器的主要部件是变压器。
变压器由一次侧(输入侧、充电电池侧)和二次侧(输出侧、铅蓄电池侧)两种线圈构成。
线圈比与电压比成比例。
利用变压器改变电压时,变压器需通过交流电压。
充电电池是直流电压,因此DC-DC转换器通过利用功率半导体ON/OFF来自充电电池的直流电压,将其转换成交流电压。
然后,利用变压器转换交流电压,再利用功率半导体将交流电压转换成14V的直流电压。
利用功率半导体转换交流和直流时,为抑制电压波形的噪声(平滑化),还使用了电容器。
决定DC-DC转换器性能的主要因素是变压器。
变压器的大小、形状及支持的开关频率随着更新换代而进化(图9)。
开关频率由70kHz提高到110kHz,变压器铁芯的重量由215g左右减轻至61g左右。
变压器的线圈通过采用层叠平面线圈的类型,降低了高度。
图9:
变压器铁芯逐代进化(a)产品越新(PC95),温度特性越高。
(b)随着产品更新换代,重量减轻、能量效率提高、进化成易于散热的形状。
通过提高开关频率,可减小变压器和整流电路的尺寸。
因为频率提高,可使功率半导体单位时间的开关次数增加。
不过,为防止接近收音机AM广播的频率,过去一直采用70kHz频帯。
最近由于抑制噪声的技术取得进步,采用了比原来高40kHz的110kHz频帯。
变压器的铁芯材料采用的是最新的铁氧体材料“PC95”。
PC95的原料为Fe(铁)、Mn(锰)、Zn(锌)。
Fe的混合比例等与原产品(“PC44”、“PC45”等)不同。
原产品在有些温度下,会出现铁损增大、效率降低现象。
最新的铁芯可在很大的温度范围内减小铁损。
铁损以磁滞损耗为主,还包括涡流损耗。
与二次侧变压器相连的整流二极管采用了比上代热损耗低的产品。
这样,整流二极管的封装面积比原来减小40%。
混合动力车用DC-DC转换器上使用的变压器铁芯材料采用了铁氧体(表)。
因为变压器中流过100kHz左右的高频电流,与其他材料相比,铁氧体的效率最高。
表DC-DC转换器的变压器铁芯材料铁氧体在铁损和成本方面占优势。
家电中使用的变压器的工作频率为50/60kHz左右,适于采用硅钢。
非晶材料适合于频率高于100kHz的领域。
(全文完,特约撰稿人:
近藤朋之,TDK电力系统业务集团EV电源部部长)
【电动汽车拆解】空调压缩机(七):
不断推进电动化
三电(SANDEN)从1971年开始生产车载空调压缩机。
如今已在欧洲、北美和亚洲拥有生产基地,掌握着全球25%的份额。
受全球环保规定和高燃效技术发展的影响,在汽车行业中,发动机的小型化和HEV(混合动力车)·EV(电动汽车)化的速度正在加快。
关于应对环保规定的办法,除了提高发动机效率、添设增压器来缩小发动机体积外,HEV还可尽量延长电机驱动时间,EV可在轻量化的同时配备高性能电池等。
具体做法因汽车厂商而异。
备有3类压缩机
本公司的空调压缩机大致分为三类。
面向需要提高现有内燃机效率、实现小型化的汽车厂商,供应的是借助传统发动机皮带传动类型的压缩机。
面向以发动机为主体、电机为辅的车辆(Mild-HEV)供应的是皮带传动和电机驱动兼顾的混合式压缩机。
对于以电机为主体(Strong-HEV、EV)的车辆,则供应电动压缩机。
(图1)。
图1:
空调压缩机的类型包括使用发动机驱动的类型,同时使用发动机和电机驱动的混合动力型,单纯使用电机驱动的类型3种。
本公司的电动压缩机开发始于1986年。
开发伊始虽然也经历过摸索阶段,但是在向推进车辆电动化的美国汽车厂商供货的过程中,产品化速度非常之快。
1990年,电动车“EVS-10”在美国投入使用。
当时就是本公司供应的电动压缩机,但产量还非常少,在成本、充电电池、基础设施的限制下未能普及。
当时的电动压缩机需要另配逆变器,成本昂贵,空间利用率也比较低。
之后,本公司在电动压缩机与逆变器的一体化、压缩机构的高效化及小型轻量化等方面推进了开发。
对于2005年上市的本田“思域混合动力”车型,本公司以此前开发的电动压缩机为基础,又开发出了皮带传动与电机驱动兼顾的混合式压缩机(图2)。
这种混合式压缩机能够在车内温度高、车速慢等空调负荷较高的情况下同时使用皮带传动和电机驱动,使制冷能力达到最大(图3)。
图2:
本田2005年9月上市的“思域混合动力”(a)车辆。
(b)混合式压缩机。
同时支持发动机驱动与电机驱动。
图3:
混合式压缩机的驱动分为三种(a)发动机运转带动压缩机工作时。
(b)空调专用电机运转带动压缩机工作时。
(c)发动机用与电机用压缩机同时运转时。
而在空调负荷较低时,则可以区别使用皮带传动和电机驱动,在车辆停止时单独使用电机驱动,以最低限度的制冷性能抑制车内温度的上升。
本公司2009年开始向德国戴姆勒(Daimler)的高级混合动力车“S400”供应电动压缩机(图4)。
S400的要求非常高,面临低电压驱动等众多难题。
但戴姆勒对我们此前的电动压缩机开发进程以及运动型高级车“SL”上使用的皮带传动型压缩机的性能及质量给予了高度评价,因而采用了我们的产品。
图4:
德国戴姆勒2009年6月上市的混合动力车“S400HYBRID”(a)机体,(b)发动机与电机部分。
压缩机中的电机使用钕磁铁,虽然是功率,使用转数范围为700~9000rpm的高功率配置,而额定电压仅为120V(图5)。
图5:
S400采用的电动压缩机(a)机体,(b)截面图。
通常以低电压实现高功率需要大电流,这样就会导致逆变器周围的电子部件成本上升,体积增大。
而此次开发过程中,电机尺寸、成本、噪声均得到了控制,齿槽转矩等特性在设计时也进行了综合考虑。
特别是冷媒压缩部分沿袭了传统的皮带传动型的可靠性,采用了使用低压低温侧冷媒冷却逆变器的方式。
随着车辆电动化的全面展开,空调的电动化正在加速。
本公司在全球最先向车辆供应的涡旋式压缩机虽然具备效率高、静音性高、驱动转矩变化小等车辆厂商要求的高水准,但不适合改变排放容积,进行精密控制的需求。
此次,在对压缩机进行电动化后,压缩机转数无需与发动机转数挂钩,可以使用电机达到所需转数。
从而实现了与排放容积可变型压缩机相同的高效率、静音性能优良等特点,而且能够实施精密控制。
今后的HEV和EV将不再只是汽车厂商的战略车和高级车,还会向中小型的普及车发展。
今后的电动压缩机需要实现更高程度的高效化、小型轻量化及低成本化(图6,7)。
图6:
电动压缩机的发展现行的A型已向S400供应。
B型除支持客户的CAN通信外,还减少了噪声的产生。
新一代型通过实现对高输入电压的支持,缩小了机体体积。
图7:
电动压缩机的发展过程本公司于1986年开始开发电动空调压缩机。
产品于上世纪90年代开始向“EVS-10”供应。
之后,混合式产品于2004年投入量产,并向本田供应。
而且,根据今后的环保规定,未来的HEV必须进一步削减CO2排放量。
这就要缩短发动机驱动时间、延长电机驱动时间。
电机驱动时间的延长必然会缩短内燃机的工作时间,减少车辆产生的热量(排热)。
由于无法再利用排热制暖,因此,对于HEV和EV而言,高效制暖则是重大课题。
比方说,有实验结果显示,如果现在EV的续航距离为160km,那么,在使用加热器制暖的情况下,续航距离将会减半到80km。
也就是说,制冷、制暖会在很大程度上限制EV车辆的商品价值以及用户的使用环境。
这无论对于整车厂商、还是对于空调设备厂商,都是非常紧迫的问题。
要想解决这一问题,电池容量的提升、车辆动力效率的提升、空调效率的提升、新机构的采用必须同时达到较高水平。
对于空调设备厂商而言,包括压缩机、冷凝器、蒸发器、加热器铁芯等热交换器的小型及高效化,降低HVAC空气侧的损耗在内,需要在现有产品基础上进行改进的方面还有很多。
而且,如果不能增加新的机构、手法以及控制方式,从空调系统整体出发结合车辆状态进行控制的话,HEV和EV的商品价值将无以维系。
未来以利用热泵为目标
高效制暖方法有一般家庭使用的热泵。
虽然将其配备在车辆上就可以解决问题,但实施起来却并不简单。
对于住宅与车辆,其外部气体热负荷、负荷变化、振动环境、空间效率等配置要求和使用环境不尽相同,在汽车上安装热泵非常困难。
热泵系统的心脏部件——压缩机也必然置身于恶劣的使用环境中,还需要进一步改进。
除汽车设备业务外,本公司还通过独自的制冷制热技术,为自动售货机、商店、居住环境业务等多个领域开发出了相应的系统。
这些系统中广泛使用了热泵技术,除了与各种使用环境相对应,在简单的空调电路的基础上还采用了二级复合电路,加入了同时调节各个温度区域的技术。
对于汽车,当务之急是对此类技术实施小型轻量化,开发廉价且环境耐受性优良的产品。
(特约撰稿人:
小野时人,三电开发本部全球开发统括室室长)
【电动汽车拆解】制暖(八):
用电加热器代替发动机
电动汽车(EV)的课题之一在于保证车内的制暖性能。
发动机车能够利用发动机产生的热量使车内保持足够温暖。
而EV没有发动机,因此制暖热源须有保证。
三菱重工业为EV开发出了用电发热的加热器。
已由三菱汽车EV“i-MiEV”制暖系统所采用。
三菱汽车2009年7月上市的电动汽车“i-MiEV”采用了三菱重工业生产的电加热器作为空调的制暖热源(图1)。
图1:
三菱汽车的电动汽车“i-MiEV”和制暖系统(a)i-MiEV。
制暖的热源采用了三菱重工为EV全新开发的加热器。
(b)制暖系统。
加热器配置在驾驶席和副驾驶席之间的地板下方。
传统发动机车一直把发动机散热作为制暖热源。
但电动汽车(EV)没有发动机,混合动力车(HEV)在发动机停转时车内也需保暖。
而此次采用的电热式加热器因可用电取暖,是EV和HEV有效的制暖方式。
i-MiEV采用的加热器由可用电发热的PTC(PositiveTemperatureCoefficient)加热器元件、将加热器元件的热量传送至散热剂(冷却水)的散热扇、散热剂流路和控制底板等组成(图2)。
因要求加热器要有较高的制暖性,因此,电源使用的是驱动马达的锂离子充电电池(330V),而非铅充电电池(12V)。
图2:
加热器机身内部有板状加热器元件。
通过在元件两侧通入散热剂(冷却水)提高散热性。
由于要制造的小型单元要使用330V高电压,用少量放热元件产生大量热量,因此,加热器需要丰富的设计和制造技术经验。
用PTC加热器将