轴承封盖成形工艺及相关模具的研究冲压设计.docx
《轴承封盖成形工艺及相关模具的研究冲压设计.docx》由会员分享,可在线阅读,更多相关《轴承封盖成形工艺及相关模具的研究冲压设计.docx(23页珍藏版)》请在冰豆网上搜索。
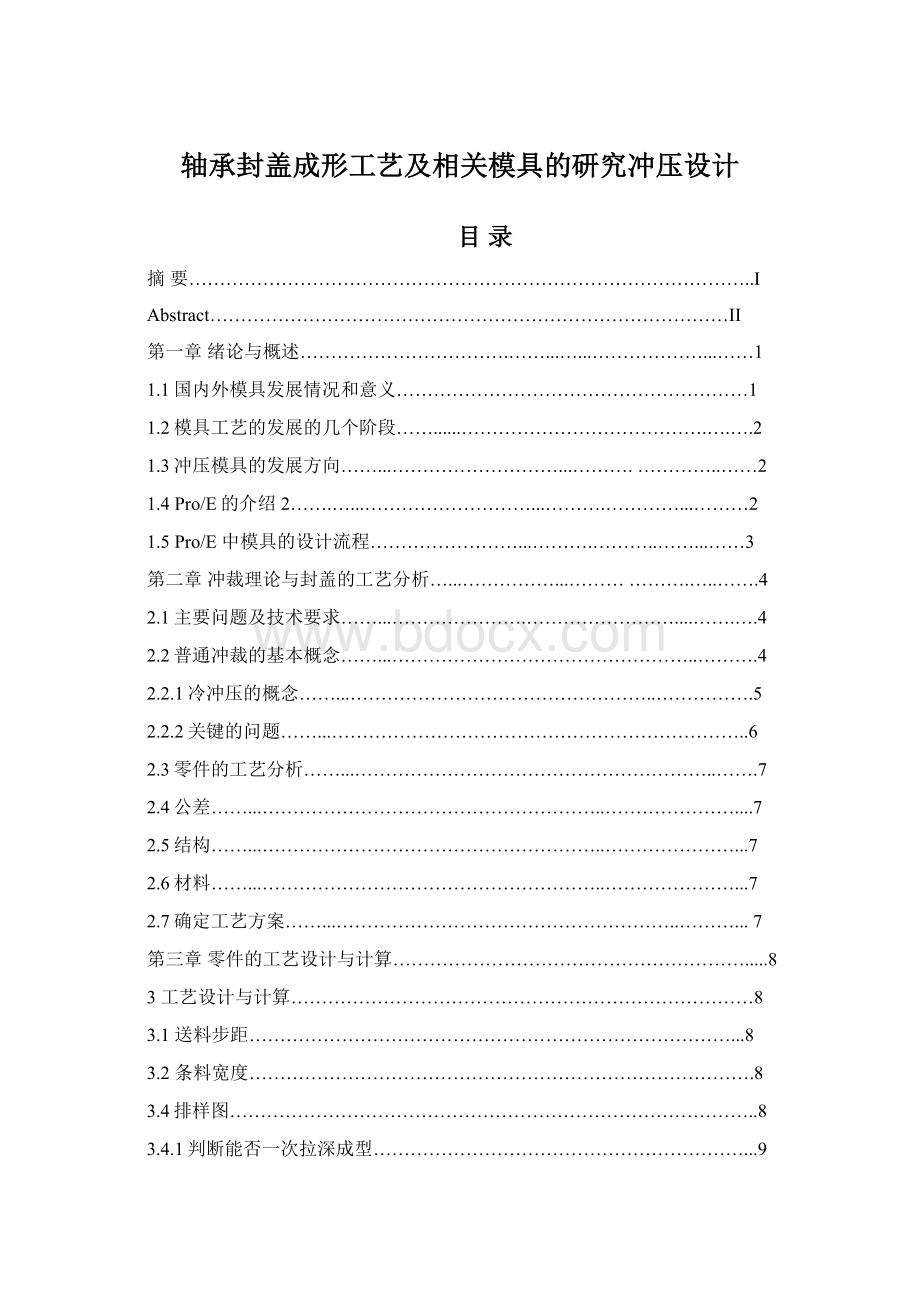
轴承封盖成形工艺及相关模具的研究冲压设计
目录
摘要………………………………………………………………………………..I
Abstract…………………………………………………………………………II
第一章绪论与概述…………………………….……...…...………………...……1
1.1国内外模具发展情况和意义…………………………………………………1
1.2模具工艺的发展的几个阶段……......………………………………….….….2
1.3冲压模具的发展方向……...………………………...……….…………..……2
1.4Pro/E的介绍2…….…...………………………...……….…………...………2
1.5Pro/E中模具的设计流程……………………...……….………..……...……3
第二章冲裁理论与封盖的工艺分析…...……………...……………….…..…….4
2.1主要问题及技术要求……...………………….……………………....…….….4
2.2普通冲裁的基本概念……...…………………………………………..……….4
2.2.1冷冲压的概念……...…………………………………………..…………….5
2.2.2关键的问题……...…………………………………………………………..6
2.3零件的工艺分析……...…………………………………………………..…….7
2.4公差……...………………………………………………..…………………....7
2.5结构……...………………………………………………..…………………...7
2.6材料……...………………………………………………..…………………...7
2.7确定工艺方案……...………………………………………………..………...7
第三章零件的工艺设计与计算………………………………………………….....8
3工艺设计与计算…………………………………………………………………8
3.1送料步距……………………………………………………………………...8
3.2条料宽度……………………………………………………………………….8
3.4排样图…………………………………………………………………………..8
3.4.1判断能否一次拉深成型……………………………………………………...9
3.4.2确定各次拉伸直径………………………………………………………...9
3.4.3选取各次半成品底部的圆角半径…………………………………………9
3.4.4计算各次拉伸高度………………………………………………………...9
3.5凸、凹模刃口尺寸、冲裁力的计算及结构的设计………………………10
3.5.1落料……………………………………………………………………...10
3.5.2刃口………………………………………………………………………10
3.5.3拉深力的计算……………………………………………………………11
第四章模具的选择……………………………..…………………………………13
4.1模具总压力的确定…………………………………………………………..13
4.2模具压力中心的确定………………………………………………………...13
4.3计算各主要零件的尺寸……………………………………………………...13
4.3.1凹模厚度……………………………………………………………………...13
4.3.2凸模尺寸…………………………………………………………………….13
4.4模具总体设计………………………………………………………………….14
第五章Pro/e的造型…………………………………..………………….………15
选定设备…………………………………………………………….…………….20
参考文献………………………………………………………………...……….…21
小结………………………………………………………………….……………...22
致谢……………………………………………………………….………………23
摘要
本设计着重对模具结构的设计,因为冲模结构是冲模设计的灵魂,它不仅决定了模具的功能,同时也决定了模具开发的成本和制造周期及操作的安全性。
本模具凹模采用拼块和镶块相结合的结构,便于制造和维护:
模具的冲孔和落料凸模分别用不同的固定板固定,便于调整间隙;冲孔凹模和落料凹模则采用整体固定板固定。
落料凸模内装有导正销,保证了工件上孔和外形的相对位置准确,提高了加工精度。
如此设计出的结构可确保模具工作运行可靠和冲压产品大批量生产的要求。
关键词:
拉伸,落料
Abstract
Thisdesignemphaticallytomoldstructuredesign,becausediesthestructureisdiesthedesignsoul,ithadnotonlydecidedmold'sfunction,simultaneouslyalsohasdecidedthemolddevelopmentcostandthemanufacturingcycleandtheoperationsecurity.
Thismoldlowerdieusesputstogethertheblockandinlaysthestructurewhichtheblockunifies,isadvantageousforthemanufactureandthemaintenance:
Mold'spunchholesandfallthematerialplungertousethedifferentdeadplatetobefixedseparately,areadvantageousforthecontrolgap;Thepunchholeslowerdieandfallsthemateriallowerdietousetheoveralldeadplatetobefixed.Fellinthematerialplungertobeloadedwithleadsisselling,hasguaranteedontheworkpiecetheholeandthecontourrelativepositionisaccurate,increasedtheworkingaccuracy.Sodesignsthestructuremayguaranteethatthemoldworkmovementisreliableandrammingproductproductioninenormousquantitiesrequest.
Keyword:
Thestretch,fallsthematerial
第一章绪论与概述
1.1模具国内外发展现状及意义
改革开放以来,随着国民经济的高速发展,市场对模具的需求量不断增长。
近年来,模具工业一直以15%左右的增长速度快速发展,模具工业企业的所有制成分也发生了巨大变化,除了国有专业模具厂外,集体、合资、独资和私营也得到了快速发展。
浙江宁波和黄岩地区的“模具之乡”;广东一些大集团公司和迅速崛起的乡镇企业,科龙、美的、康佳等集团纷纷建立了自己的模具制造中心;中外合资和外商独资的模具企业现已有几千家。
一些国内模具企业已普及了二维CAD,并陆续开始使用UG、Pro/Engineer、I-DEAS、Euclid-IS等国际通用软件,个别厂家还引进了Moldflow、C-Flow、DYNAFORM、Optris和MAGMASOFT等CAE软件,并成功应用于冲压模的设计中。
艺手段、冲压件质量及模具性能方面,均以达到或接近国际先进水平。
多工位连续模和多功能模具是我国重点发展的精密、高效模具品种。
目前,国内以可制造具有自动冲切、叠压、铆合、计数、分组、转子铁心扭斜和安全保护等功能的铁心精密自动叠模具厂、第一汽车厂模具中心等都能制造。
他们在CAD/CAM/CAE的运用、加工工压多功在冷冲模具方面,代表当代模具技术水平的汽车覆盖件模具,我国东风汽车公司能模具。
生产电动机定、转子双回转叠片的硬质合金连续模的步距精度可大2μm,寿命达到1亿次以上。
用于生产集成电路引线匡架的20-30工位生产电子枪零件的硬质合金连续模和生产空调器散热片的连续模也已达到较高的水平。
1.2模具工业发展的几个阶段
模具工业是随着改革开放,在快速发展的经济浪潮推动下得以发展壮大的。
20世纪80年代初至今,模具工业整整走过了20个年头。
在这期间模具工业的发展大体可以分为三个阶段。
1、从20世纪的年代初期到中期,北京模具工业处于封闭或半封闭状态模具生产力比较低,技术水平也比较落后。
2、从20世纪80年代中期到90年代中期,模具工业处于改革开放机制转变的大好时期,随着改革开放不断深人,模具工业也发生了巨大变化。
3、从20世纪90年代中期到2003年,企业进人调整、重组、改制阶段。
1.3冲压模具的发展方向
模具技术的发展应该为适应模具产品“交货期短”、“精度高”、“质量好”、“价格低”的要求服务。
达到这一要求急需发展如下几项:
(1)全面推广CAD/CAM/CAE技术
(2)高速铣削加工
(3)模具扫描及数字化系统
(4)电火花铣削加工
(5)提高模具标准化程度
(6)优质材料及先进表面处理技术
(7)模具研磨抛光将自动化、智能化
(8)模具自动加工系统的发展
在模具新材料及热、表处理方面必须提高使用性能,改善加工性能,提高寿命。
模具CAD/CAM的技术方面,必须采用二、三维相结合的数字化设计技术与数字化制造技术,模具行业是最早应用CAD/CAM技术的行业之一。
快速经济制模技术,加快模具的制造速度,降低模具生产成本,适应小批量试制。
提高先进的管理模式,并行工程思想、标准化、专业化生产。
综上所述,模具技术是先进制造技术的重要代表,模具工业是高新技术产业的一个重要组成部分,模具工业又是高新技术产业化的重要领域。
1.4Pro/E的介绍
Pro/E(Pro/Engineer操作软件)是,美国参数技术公司(ParametricTechnologyCorporation,简称PTC)的重要产品。
在目前的三维造型软件领域中占有着重要地位,并作为当今世界机械CAD/CAE/CAM领域的新标准而得到业界的认可和推广,是现今最成功的CAD/CAM软件之一。
域的新标准而得到业界的认可和推广,是现今最成功的CAD/CAM软件之一。
Pro/E第一个提出了参数化设计的概念,并且采用了单一数据库来解决牲的相关性问题。
另外,它采用模块化方式,用户可以根据自身的需要进行选择,而不必安装所有模块。
Pro/E的基于特征方式,能够将设计至生产全过程集成到一起,实现并行工程设计。
它不但可以应用于工作站,,而且也可以应用到单机上。
Pro/E采用了模块方式,可以分别进行草图绘制、零件制作、装配设计、钣金设计、加工处理等,保证用户可以按照自己的需要进行选择使用。
1.5Pro/E的设计流程
1进入P的模具设计(MOLDDESING)模块,创建参照模型。
可以装配参照模型和工件,或直接创建参照模型和工件,或检索模具型腔。
2创建模具型腔的收缩。
可以为某些或所有的尺寸创建各项同性的比列收缩或收缩系数。
可将按尺寸收缩应用到设计模型上,使设计模型保持不变,以便在其他应用程序中使用。
3定义体积块或分型面以将其分割成单独的元件。
4拾取模具体积块。
抽取完毕后,模具元件成为功能完全的Pro/E零件。
他可以在零件模式中调出,在绘图中使用,以及应用Pro/NC进行加工等。
5增加浇口,绕道和流水线作为模具特征。
6定义模具开模步骤。
对每一步进行是否与静态零件向干涉的检查,有必要时,应该修改模具元件。
第二章冲裁理论与加强板零件的工艺分析
2.1主要问题及技术要求
1、基本内容是利用垂直复合冲裁模冲裁技术完成定子冲片成型,保证图中所示的尺寸正确。
完成此零件的相关配件的设计和各个配件的绘图任务,最后完成该零件的模具的设计。
分析冲裁件的结构形状,尺寸精度,材料是否符合,冲压力工艺要求,从而确定冲裁的可能性。
2、确定冲裁工艺方案及模具结构形式
工序数目,工序性质,工序顺序,工序组合及模具结构形式。
3、冲压模具的设计计算。
排样
冲压力
压力中心
模具刃口尺寸计算
确定各主要零件的外形尺寸
计算模具的闭合高度
确定所用冲床
4、绘制冲模总装图
5、从冷冲模标准中选取标准件,将标准编号写入详细表。
6、绘制非标准零件图
技术要求:
该零件材料为Q235,材料厚度为2mm,本次研究的类容落料胀行一次性完成任务,其中所以未注公差都按照IT15来要求。
任务书中未提及其他技术要求。
凹、凸模的制造,技术要求也相对比较简单材料将会选用Crl2MoV,热处理大概在58~62HRC之间。
2.2普通冲裁的基本概述
2.2.1冷冲压的概念:
冷冲压是在常温下利用冲模在压力机上对材料施加压力,使其产生分离或变形,从而获得一定形状、尺寸和性能的零件的加工方法,是机械制造中先进的加工方法之一。
冲裁工艺的种类很多,常用的有切断、落料、冲孔、切边、切口、剖切等。
所以冲裁是分离工序的总称,其中尤以落料、冲孔应用最多。
根据冲裁变形机理的不同,冲裁工艺可以分为普通冲裁和精密冲裁两大类。
所谓普通冲裁是有凹、凸模刃口之间产生剪裂缝的形式实现板料分离。
而精密冲裁则是以变形的形式实现板料的分离。
本次设计,所涉及到的是精密复合冲裁模,相对比较复杂,精度较高。
2.2.2关键问题:
(1)、冲压工序:
对零件进行落料拉伸;
(2)、材料:
Q235,具有良好的冲压性能,适合冲裁;
(3)、零件要多次拉伸
(5)、冲压工艺方案的分析
用复合模具冲出的工件精度高于连续模,而连续模又高于单工序模。
这是因为用单工序模冲压多工序的冲裁件时,要经过多次定位和变形,产生积累误差大,冲裁件精度较低。
复合模是在同一位置一次冲出,不存在定位误差。
因此,对于精度较高的冲裁件宜用复合工序进行冲裁。
综上所述初步选定模具结构为复合模具。
(6)、压力中心的确定及相关计算
因为此零件非规则零件,因此压力中心需要自己通过公式计算。
2.3零件的工艺分析
工件图如图2.1所示。
图2.1工件图
经分析本制件属有孔的拉深件,经初步分析,用复合模经过落料、拉深、冲孔等工序来完成。
2.4公差
制件上未注尺寸公差按IT14级计算,所有工序需保证尺寸精度都为IT14级。
工件的这种精度一般的冲裁都能保证。
经分析,此工件的加工工序的基本步骤为落料、拉深、冲孔等工序来完成。
2.5结构
本制件属于拉深落料件,经分析落料拉深可用一套模具,且可保证零件工艺精度。
因此选用复合模。
2.6材料
Q235,已退火,此材料抗剪强度τ=320-380Mpa,抗拉强度σb=410-470Mpa,伸长率ξ=21%。
2.7确定工艺方案
该制件工艺复杂程度一般,考虑采用单工序模具,复合模和级进模三种方案;由于该制件为大批量生产,用单工序模冲压多工序的冲裁件时,要经过多次定位和变形,产生积累误差大,冲裁件精度较低,因为要经过多道工序,所以使用单工序模又会影响到工作效率,所以否放弃单工序模方案。
试想采用级进模生产方案,由于该工件尺寸很大,这样就增加了级进模的长度,使设计和加工难度加大,所以虽然级进模方案符合大批量生产要求,但由于设计加工难度大而屏弃。
而复合模可以解决单工序模的精度差的缺点。
在零件尺寸稍大的情况下,复合模只需要稍微加大尺寸,来配合零件的尺寸就行。
相对单工序模和级进模的弊端而采用级进模设计思想,采用复合模可解决以上两种方案的弊端。
第三章工艺设计与计算
3.1送料步距
A=D+a=126+2=128mm
式中D—平行于送料方向工件宽度
a—冲件间搭边值
3.2条料宽度
B=D+2(a+δ)+c
=130mm
3.3材料利用率
n=F/F0x100%
式中F—一个步距内零件的实际面积
F0—个步距内毛胚面积
N=F/F0x100%
=127/130x100%
=75.5%
所以该方案的有效利用率是75.5%,经综合分析,虽然略有浪费,但是生产效率比较高,精度易保证,所以方案可行。
3.4排样图
材料的排样图如图3.1所示
图3.1排样图
3.4.1判断能否一次拉深成形
由《中国模具设计大典》19.4-8查得各次拉伸的极限拉伸系数为
=0.45,
=0.72,
>1,
,此件为圆筒形件。
,
0.45,
<
,不能一次拉深成形。
=0.314小于
,因此2次拉伸可以完成。
可采用阶梯拉伸。
3.4.2确定各次拉伸直径
计算各次拉伸直径,各次拉伸直径为
=0.52×36=18.72mm
=0.72×18.72=13.48mm<14mm(制件直径),说明允许的变形过程未用足,应对各次拉伸系数做适当调整,使均大于相应的极限拉伸系数。
经调整后,实际选取
=0.53、
=0.72,各次拉伸直径为
=0.53×36=19mm
=0.72×18.72=14mm
3.4.3选取各次半成品底部的圆角半径
先选取第一次拉的凹模圆角半径
,查表19.4-35,当D-
=(36-19)mm=17mm,t=0.5mm时,取
=3mm,然后根据
=(0.6—0.9)
,分别选取工序制件的圆角半径;
=3mm、
=1mm;
=3mm、
=1mm。
3.4.4计算各次拉伸高度
=0.25(D
-
)+0.43
(
+0.32
)
=0.25(
)mm+0.43
mm
=11mm
3.5凸、凹模刃口尺寸、冲裁力的计算及结构的设计
3.5.1落料
(1)刃口尺寸的计算
φ126料按公差九级查得φ126+0.1
查表得2cmin=0.1262cmax=0.180
则2cmax-2cmin=0.25-0.21=0.04
未注公差按IT14级计算取X=0.75
凸凹模分别按IT6和IT7级加工制造则
φ126
Dd=(Dmax-x△)0+δd=(126-0.75*0.1)+0.0250=125.12+0.0250
Dp
=(Dp+2cmin)-δp0=(126-0.126)0+0.04=125.25-0.040
校核
0.025+0.004<0.054
满足间隙条件;
3.5.2刃口
(1)刃口尺寸的计算
凹凸模的基本尺寸计算如下:
Dd1=(Dmax-x△)0+δd=(105-0.75x1)0+0.14x0.25=4.930+0.22mm
Dp1=(Dd-2Cmin)0-δp=(8-1x0.075)-0.140=101.85-0.140mm
Dp2=(Dmin+X△)-δp0=(91+0.4x0.87)-0.220=91.35-0.220mm
Dd2=(Dp2+2Cmin)0+δd=(91+0.4x0.74+2x1.2)0+0.14=55.060+0.14mm
Dp3=(Dmin+X△)-δp0=(64+0.4x0.74)-0.120=64.3-0.120mm
孔dp=(dmin+X△)-δp0=(40+0.5x0.62)-0.160=40.13-0.160mm
dp=(dp+2Cmin)0+δd=(40.13+0.126)0+0.25=55.060+0.25mm
(2)冲裁力的计算
Fp=KptLτ
=1.3x1.2x395.64x340
=210kN
式中K—系数,一般取1.3
L—冲裁周边长度(mm)
τ—材料的抗剪强度(Mpa)
t—材料厚度(mm)
3.5.3拉深力的计算
F拉=k
dt
b
式中k—系数0.4
d—拉深件直径
t—材料厚度
b—材料抗拉强度
F拉=0.4x3.14x105x1.2x450
=71215N
第四章模具的设计
4.1模具总压力的确定
FpΣ总1=F卸料+F落料+F拉深
=8.4+210+71215
=71433.4KN
≈71434KN
4..2模具压力中心的确定
本模具采用解析法计算压力中心,建立坐标系,因为左右对称,所以XG=0,只需要求YG。
根据合力矩定理有:
YG=(Y1L1+Y2L2+Y3L3+Y4L4+Y5L5)/(L1+L1+L1+L1+L1)
={-240.75x2x(43.5+3.5)-26.75x2x2x(40+3.5)-158.75x2x(55.25+3.5)}/(240.75+158.75+26.75)
=(-22630.5-4654.5-18653.1)/426.25
=-107.8mm
4.3计算各主要零件的尺寸
4.3.1凹模厚度
查得
H凹=kb
式中k=0.22b为最大外形尺寸
冲孔、切槽凹模厚度H凹=kb=0.22*126=28mm取H凹=50mm
冲孔、切槽凹模壁厚C=1.5H=1.5*50=75mm考虑到实际强度和厚度限制取C=80mm。
凹模板零件图如图4.1所示。
图4.1凹模
4.3.2凸凹模尺寸
由零件尺寸可算出凸模的尺寸,凸模为冲孔模,直径为45.由此推算出凸凹模尺寸
凸凹模的零件图如图4.2所示
图4.2凸凹模
4.4模具总体设计
根据以上计算所得数据及确定的工艺方案,对模具进行总体设计,绘结构草图。
如图3.3所示:
从结构草图初算闭合高度H=265mm
根据凹模外形尺寸,确定下模板的外形尺寸为310mm*310mm
考虑到制件较大,为了送料取件方便,采用后角导柱模架。
第五章.PRO/E的造型
5.1卸料板的造型
第一步:
打开【Pro/E】点击【文件】,在【新建】选择【零件】,在【名称】里输入:
卸料板,最后点击【确定】。
弹出一个窗口。
第二步:
创建草绘平面,点击【旋转】,在点击【创建截面】,选择一个基准面,最后点击【草绘】
第三步:
在草绘平面里画出要旋转的形状,最后点击确定
得到的图如下图4.1所示:
图5.1卸料板
5.2凸凹模的造型
第一步:
打开【Pro/E】点击【文件】,在【新建】选择【零件】,在【名称】里输入:
凸凹模,最后点击【确定】。
弹出一个窗口。
第二步:
创建草绘平面,点击【旋转】,在点击【创建截面】,选择一个基准面,最后点击【草绘】
第三步:
在草绘平面里画出要旋转的形状,最后点击确定。
得到如图4.2所示
图5.2凸凹模
5.3凹模的造型
第一步:
打开【Pro/E】点击【文件】,在【新建】选择【零件】,在【名称】里输入:
凹模,最后点击【确定】。
弹出一个窗口。
第二步:
创建草绘平面,点击【拉深】,在点击【创建截面】,选择一个基准面,最后点击【草绘】
第三步:
在草