第三篇锅炉本体1分析.docx
《第三篇锅炉本体1分析.docx》由会员分享,可在线阅读,更多相关《第三篇锅炉本体1分析.docx(51页珍藏版)》请在冰豆网上搜索。
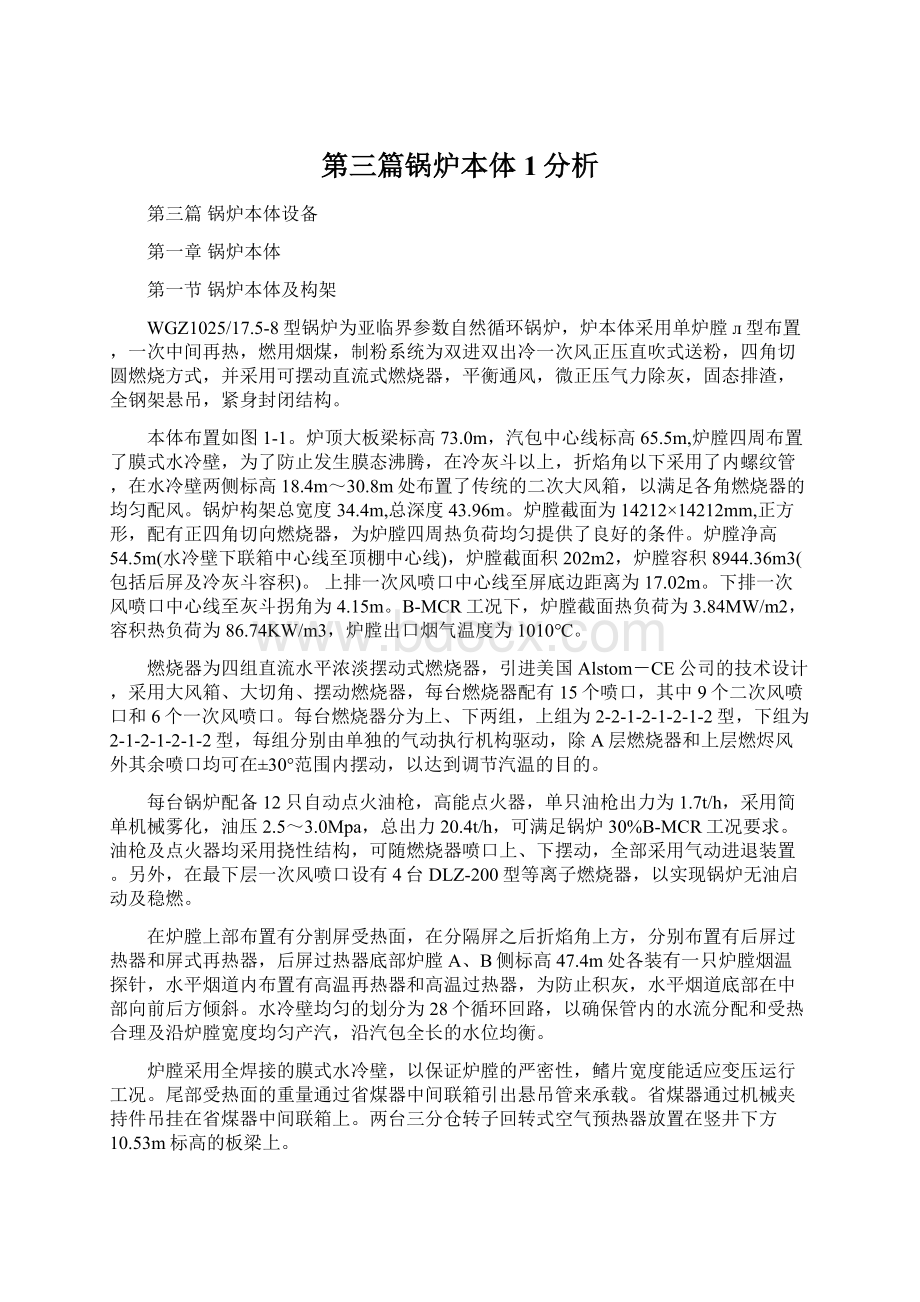
第三篇锅炉本体1分析
第三篇锅炉本体设备
第一章锅炉本体
第一节锅炉本体及构架
WGZ1025/17.5-8型锅炉为亚临界参数自然循环锅炉,炉本体采用单炉膛л型布置,一次中间再热,燃用烟煤,制粉系统为双进双出冷一次风正压直吹式送粉,四角切圆燃烧方式,并采用可摆动直流式燃烧器,平衡通风,微正压气力除灰,固态排渣,全钢架悬吊,紧身封闭结构。
本体布置如图1-1。
炉顶大板梁标高73.0m,汽包中心线标高65.5m,炉膛四周布置了膜式水冷壁,为了防止发生膜态沸腾,在冷灰斗以上,折焰角以下采用了内螺纹管,在水冷壁两侧标高18.4m~30.8m处布置了传统的二次大风箱,以满足各角燃烧器的均匀配风。
锅炉构架总宽度34.4m,总深度43.96m。
炉膛截面为14212×14212mm,正方形,配有正四角切向燃烧器,为炉膛四周热负荷均匀提供了良好的条件。
炉膛净高54.5m(水冷壁下联箱中心线至顶棚中心线),炉膛截面积202m2,炉膛容积8944.36m3(包括后屏及冷灰斗容积)。
上排一次风喷口中心线至屏底边距离为17.02m。
下排一次风喷口中心线至灰斗拐角为4.15m。
B-MCR工况下,炉膛截面热负荷为3.84MW/m2,容积热负荷为86.74KW/m3,炉膛出口烟气温度为1010℃。
燃烧器为四组直流水平浓淡摆动式燃烧器,引进美国Alstom-CE公司的技术设计,采用大风箱、大切角、摆动燃烧器,每台燃烧器配有15个喷口,其中9个二次风喷口和6个一次风喷口。
每台燃烧器分为上、下两组,上组为2-2-1-2-1-2-1-2型,下组为2-1-2-1-2-1-2型,每组分别由单独的气动执行机构驱动,除A层燃烧器和上层燃烬风外其余喷口均可在±30°范围内摆动,以达到调节汽温的目的。
每台锅炉配备12只自动点火油枪,高能点火器,单只油枪出力为1.7t/h,采用简单机械雾化,油压2.5~3.0Mpa,总出力20.4t/h,可满足锅炉30%B-MCR工况要求。
油枪及点火器均采用挠性结构,可随燃烧器喷口上、下摆动,全部采用气动进退装置。
另外,在最下层一次风喷口设有4台DLZ-200型等离子燃烧器,以实现锅炉无油启动及稳燃。
在炉膛上部布置有分割屏受热面,在分隔屏之后折焰角上方,分别布置有后屏过热器和屏式再热器,后屏过热器底部炉膛A、B侧标高47.4m处各装有一只炉膛烟温探针,水平烟道内布置有高温再热器和高温过热器,为防止积灰,水平烟道底部在中部向前后方倾斜。
水冷壁均匀的划分为28个循环回路,以确保管内的水流分配和受热合理及沿炉膛宽度均匀产汽,沿汽包全长的水位均衡。
炉膛采用全焊接的膜式水冷壁,以保证炉膛的严密性,鳍片宽度能适应变压运行工况。
尾部受热面的重量通过省煤器中间联箱引出悬吊管来承载。
省煤器通过机械夹持件吊挂在省煤器中间联箱上。
两台三分仓转子回转式空气预热器放置在竖井下方10.53m标高的板梁上。
锅炉尾部烟道由竖井前墙、侧墙、后墙及顶棚管组成。
尾部竖井标高48.904m以上布置了立式低温过热器,在标高48.47m以下,40.3m以上布置了三级卧式低温过热器。
两级省煤器布置在竖井标高35.6m至39.1m之间,省煤器入口联箱在尾部竖井标高32.26m处,在炉外与给水管道连接。
尾部竖井烟道下集箱在标高32.86m处。
水冷壁下集箱中心线标高6.5m,在炉膛冷灰斗下方装有一台刮板式捞渣机。
锅炉受热面主要包括水冷壁,分割屏过热器,后屏过热器,高温过热器,低温过热器,壁式再热器,屏式再热器,高温再热器,省煤器,空气预热器和暖风器等。
从传热学的角度可以把上述受热面分为辐射式受热面,半辐射式受热面和对流受热面三种,其中水冷壁、分割屏过热器为辐射式受热面;后屏过热器,壁式再热器,属半辐射式受热面,其余均属对流
二、水冷壁结构
式受热面。
锅炉构架为桁架体系,各杆件之间用高强度螺栓连接,连接形式采用铰接。
整个构架借助垂直支撑,水平支撑保证。
除捞渣机和空气预热器外,锅炉本体通过不同的吊杆悬吊在炉顶大板梁上。
锅炉设有膨胀中心,其膨胀零点设置在炉膛深度和宽度中心线上,通过装在炉前、炉后、两侧的导向装置来实现。
垂直方向的零点设在炉顶大罩壳上,所有受压吊杆均与膨胀零点有关,对位移量大的吊杆均留有予进量,以减少锅炉运行时的吊杆应力。
膨胀可由深500mm的水封槽来吸收。
锅炉炉顶采用包覆框架密封形成炉顶小室,炉底则由水封槽,刮板捞渣机及其冷却水,液压关断门形成密封。
第二节水冷壁
一、水冷壁的作用
水冷壁的作用是由自身结构组成锅炉燃烧室,同时吸收炉膛辐射热,建立自然循环,将炉水加热成饱和蒸汽。
二、水冷壁结构
水冷壁是辐射蒸发受热面,热负荷很高,一般为233~350KW/m2,可以减小锅炉受热面,达到节省金属的目的。
水冷壁根据类型可以分为光管式和膜式两种,水冷壁采用那种型式因锅炉类型和参数而异,对于亚临界参数锅炉,一般采用膜式水冷壁。
我厂锅炉水冷壁采用模式水冷壁。
(一)膜式水冷壁的优点
1、由于膜式水冷壁具有很好的严密性,可以显著降低炉膛的漏风系数,改善炉内燃烧工况。
2、有效增加了炉内辐射受热面,节约了钢耗。
3、采用膜式水冷壁后,只需保温材料而不需耐火材料,大大减轻了炉墙重量和金属耗量,同时亦可减少炉墙蓄热量,缩短了锅炉启停时间。
4、增加了炉墙刚性,若发生异常时,膜式水冷壁可以承受冲击压力,不致引起破坏。
5、隔绝了高温烟气对炉墙紧固件冲刷,腐蚀和烧坏,延长紧固件的使用寿命。
6、可以在制造厂成片制造,大大减少了安装工作量。
(二)膜式水冷壁结构
水冷壁的结构主要有两种类型图1-2所示:
1、由光管加焊扁钢制成。
2、由轧制的肋片管拼焊制成。
我厂采用的水冷壁为光管加焊扁钢制成,水冷壁由外经为φ63.5mm的管子制成,节距
为26.2mm,管子中间的空隙以扁钢焊接,如图1-3所示。
炉膛延伸侧墙由外径为φ76mm管子按152mm节距用连接鳍片焊成。
炉膛上部顶棚管由外径φ60mm的管子按152mm节距用分段鳍片焊接而成。
选择水冷壁管径和节距,既要考虑节省金属降低钢耗,又要保证有足够的水冷壁受热面,尽快建立水循环,还要保证在同样的热负荷下,水冷壁不致被烧坏,根据有关资料表明,管间距s/d通常在1.2-1.4范围。
(三)水冷壁布置
WGZ1025/17.5-8型锅炉炉膛宽度14212mm,深度14212mm,水冷壁根据受热情况和几何特性,分成28个循环回路,其中前后墙各6个回路,两侧墙各8个回路,如图1-4所示。
汽水循环系统包括汽包、集中下降管、引入管、水冷壁管和引出管。
来自省煤器的水进入汽包内给水分配管中,分4路分别进入4根Φ588.8×60mm集中下降管内,给水直接在下降管中与炉水混和,以避免给水与汽包壁接触,减少锅炉启、停时汽包内外、上下壁温差,在4根下降管的下端各接有一Φ610×95mm分配集箱,68根Φ159×18mm与18根Φ133×4mm的引入管相接,引入管将欠焓水送入水冷壁的四周下集箱Φ324×50mm。
炉膛水冷壁采用膜式结构,由Φ60×7.5mm,材质为SA210C光管和内螺纹管与6mm扁钢相焊而成,节距S=76mm,折焰角处由Φ70×10mm的内螺纹管组成。
在炉膛四周处的水冷壁管子形成燃烧器的水冷套以保护喷口烧坏。
工质在水冷壁中受热后,汽水混合物沿着水冷壁向上流动,经98根Φ159×18mm与12根Φ133×4mm的SA106B引入管引入汽包内,通过切向旋风式分离器和水平百叶窗进行汽水分离,分离后的炉水流入汽包下部空间,干蒸汽由18根Φ159×18mm的引出管接入顶棚过热器入口集箱Φ273×50mm。
水冷壁下集箱内装有蒸汽加热装置,锅炉在点火前采用蒸汽对28只水冷壁下集箱提前加热,以缩短启动时间。
前后水冷壁在标高16.20m处折成冷灰斗,以550落角向炉膛中心处倾斜形成开口1400mm×1600mm的排渣口,排渣口浸在标高6.5m的炉底水封槽中。
后水冷壁至标高40.83m处形成深3200mm,倾角为向上550的折焰角,在标高46.2m处水冷壁以300水平倾角向后上方沿升,在后水冷壁中心管处,其中31根φ76×13的管子垂直向上形成后水冷壁悬吊管,延伸至烟道的152根φ76×9的水冷壁管中,左右各有22根管子外折形成水冷壁延伸侧墙,其余108根则延伸至距后水冷壁3.378m处垂直向上形成水平烟道对流排管。
(四)水冷壁折焰角
我们把后墙水冷壁在炉膛上部突出的部分称作折焰角。
折焰角具有以下作用:
1、增加烟气行程,延长燃料在炉内的停留时间,有利于燃料的燃烬;
2、改善火焰在炉内的充满度,使烟气能更好地充满炉膛的上部,增加了前墙和侧水冷壁的吸热量;
3、使烟气在炉膛出口处沿高度方向均匀进入过热器,改善过热器的传热。
4、增加了水平烟道的长度,便于布置受热面。
如图1-5所示为我厂锅炉折焰角尺寸。
(五)水冷壁联箱
水冷壁进出口均设有联箱,联箱具有以下作用:
1、将管径不等,用途不同的管子汇集在一起,如水冷壁下联箱将大直径下降管的分散管与φ76.2mm的小直径水冷壁管连接起来。
2、减少与汽包相连的管子,不但有效地减少了汽包上的开孔,而且便与布置。
3、混合工质,改善工质的受热不均。
(六)水冷壁角部突出。
如图1-6,水冷壁前后墙两侧各有21根管子向炉内突出,使炉膛呈不明显的八角形状,通常把四个角相接处的管子称为角隅管。
角隅管距离炉膛中心最远,在锅炉传热中炉膛辐射传热比例高达95%,并且辐射传热是直接传播的,但一部分热辐射受到角隅管附近管子的折挡,使角隅管的吸热量明显低于其它管子,使得这部分管子进入汽包水空间时容易产生水循环倒流,进入汽包汽空间时易产生自由水位,无论出现哪种情况,都会危及这些管子的安全。
为了使同一循环回路中的各根水冷壁吸热量差别减小,我厂锅炉设计及制造中将每面墙上的水冷壁分成6-8个回路,尽管如此,但角隅管的吸热量仍明显低于其它管子,因此为了增加角隅管吸热量,通常将这些管子向炉内突出。
三、亚临界压力自然循环特性
自然循环的形成是由于上升管中的汽水混合物与下降管中的水有密度差,从而产生了循环推动力,迫使工质在上升管中作向上流动和在下降管中作向下流动,从而产生了工质循环流动.其循环回路的动压头(即为循环回路的推动力)Syd如下式:
Syd=(ρ´-ρ")ψg(H-Hrs)(式1-1)
式中:
ρ´,ρ"——饱和水、汽的密度;
ψ——截面含汽率,ψ=A"/A;
A"——管子中汽占据截面积;
A——管子截面积;
g——重力加速度;
H——循环回路高度(汽包水位面到下联箱中心线);
Hrs——循环回路热水段高度。
从式1-1中可知,增加循环回路高度H,能使运动压头增加,但回路高度提高受炉内水冷壁及炉膛燃烧、锅炉布置的限制。
对于亚临界压力自然循环锅炉,随着压力的增大,(ρ´-ρ")的数值是下降的,为保证循环回路的推动力Syd,势必增大循环回路中的截面含汽率ψ,从而使循环回路的质量含汽率X值增大,当X值大于该循环回路界限含汽率Xjx时,就会产生第二类传热恶化,使水冷壁管子的安全受到威胁。
循环回路中的循环流速往往随着负荷的不同而异,上升管受热增强时,其产生的蒸汽量就多,截面含汽率ψ增加,反之,上升管受热弱时,循环流速就减小。
这种在一定的循环倍率范围内,自然循环回路上升管吸热量增加时,循环流量随之相应增加已进行补偿的特性,称之自然循环的自补偿特性。
自补偿特性对水冷壁安全有利,也是自然循环的一大优点。
动压头能够造成多大的循环流速,还取决于循环回路的阻力特性。
当上升管的蒸汽含量增加时(质量含汽率X增加,循环倍率K减少),一方面运动压头增加,循环流量增加,而另一方面循环回路的阻力也随之增加。
在一定的循环倍率范围内,热负荷增加,质量含汽率增加,循环回路循环倍率K下降,此时循环回路流量随K下降而上升,即循环工作在自补偿范围内。
但当循环倍率K低至某一值以下时,则会出现运动压头增