旋钮模具设计.docx
《旋钮模具设计.docx》由会员分享,可在线阅读,更多相关《旋钮模具设计.docx(25页珍藏版)》请在冰豆网上搜索。
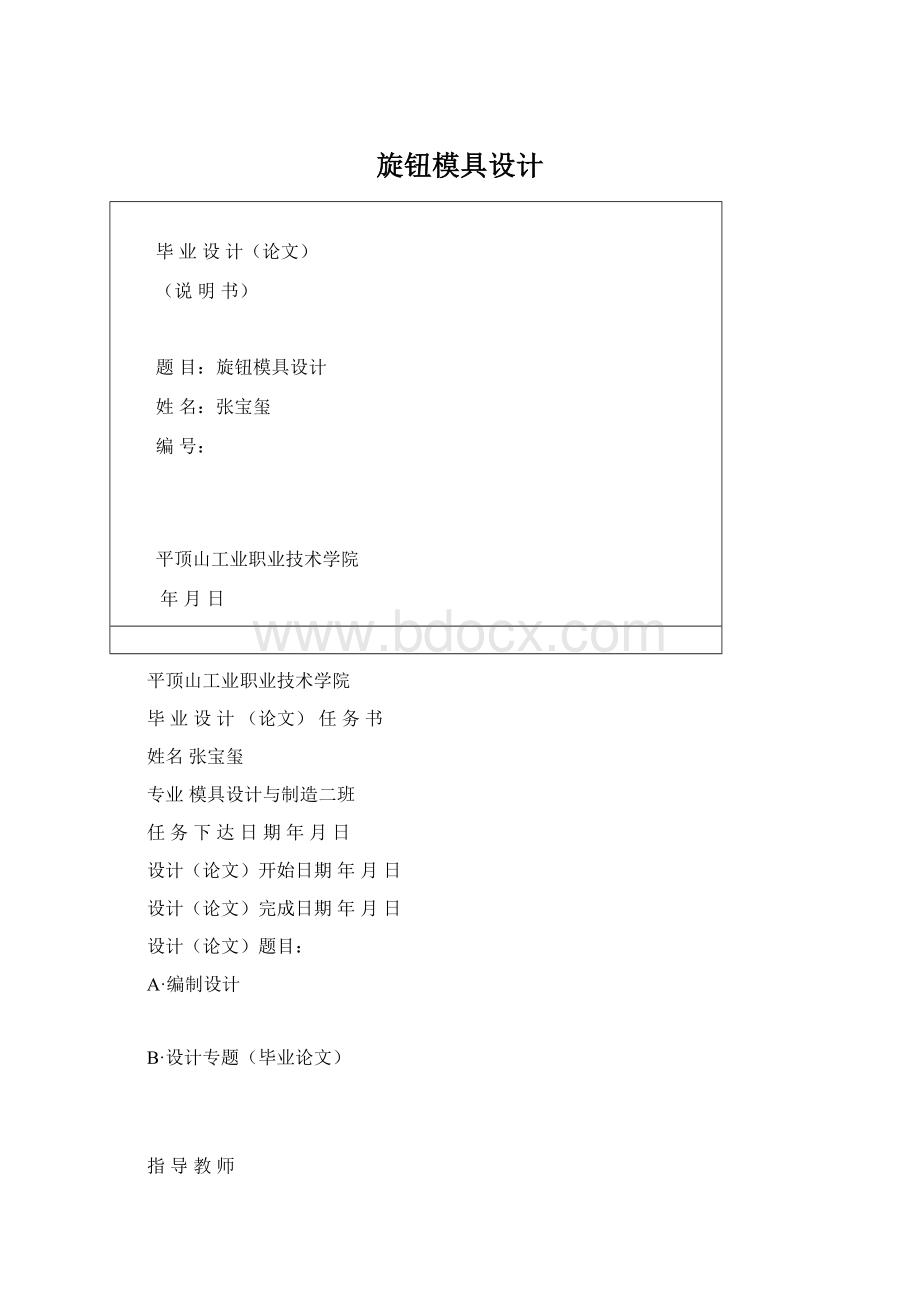
旋钮模具设计
毕业设计(论文)
(说明书)
题目:
旋钮模具设计
姓名:
张宝玺
编号:
平顶山工业职业技术学院
年月日
平顶山工业职业技术学院
毕业设计(论文)任务书
姓名张宝玺
专业模具设计与制造二班
任务下达日期年月日
设计(论文)开始日期年月日
设计(论文)完成日期年月日
设计(论文)题目:
A·编制设计
B·设计专题(毕业论文)
指导教师
系(部)主任
年月日
平顶山工业职业技术学院
毕业设计(论文)答辩委员会记录
机械工程系模具设计与制造专业,学生于年月日
进行了毕业设计(论文)答辩。
设计题目:
旋钮模具设计
专题(论文)题目:
指导老师:
答辩委员会根据学生提交的毕业设计(论文)材料,根据学生答辩情况,经答辩委员会讨论评定,给予学生毕业设计(论文)成绩为。
答辩委员会人,出席人
答辩委员会主任(签字):
答辩委员会副主任(签字):
答辩委员会委员:
,,,
,,,
平顶山工业职业技术学院毕业设计(论文)评语
第页
共页
学生姓名:
张宝玺专业模具设计与制造年级07级
毕业设计(论文)题目:
旋钮模具设计
评阅人:
指导教师:
(签字)年月日
成绩:
系(科)主任:
(签字)年月日
毕业设计(论文)及答辩评语:
摘 要
模具工业是国民经济的基础工业,是国际上公认的关键工业,工业发达国家称之为“工业之母”。
模具成型具有效率高、质量好、节省原材料、降低产品成本等优点,采用模具制造产品零件已成为当今工业生产的重要工艺手段。
模具在机械、电子、轻工、纺织、航空、航天等工业领域里,日益成为使用最广泛的主要工艺装备,它承担了这些工业领域中60%~90%的产品的零件,组件和部件的生产加工。
塑料模是塑料成型的工艺装备。
中国塑料模工业从起步到现在,历经了半个多世纪,有了很大发展,模具水平有了较大提高,约占模具总数的35%,而且有继续上升的趋势。
改革开放以来,我国的模具工业发展十分迅速。
近年来,每年都以15%的增长速度快速发展。
许多模具企业十分重视技术发展。
但长期以来,我国的注塑模设计主要依靠设计者的经验和直觉,通过反复试模、修模修正设计方案,缺乏科学依据,具有较大的盲目性,不仅使模具的生产周期长、成本高,而且质量也难以保证。
随着塑料制品应用的日益广泛,传统的注射模生产方式已不能适应现代社会发展对塑料制品产量、质量和更新换代速度的需求,因此,研究注塑模具对了解塑料产品的生产过程和提高产品质量有很大意义。
本设计是针对旋钮的模具设计,通过对塑料件进行工艺的分析和比较,最终设计出一副注塑模。
该设计从产品结构工艺性,具体模具结构出发,对模具的浇注系统、模具成型部分的结构、顶出结构、冷却系统、注塑机的选择及有关参数的校核、都有详细的设计,同时并简单的编制了模具的加工工艺。
通过整个设计过程表明该模具能够达到此塑件所要求的加工工艺。
根据题目设计的主要任务是旋钮模具的设计。
也就是设计一副注塑模模具来生产旋钮塑件产品,以实现自动化提高产量。
针对具体结构,该模具就是侧浇口交口的注射模具。
其优点在于简化机构,使模具外形缩小,大大降低了模具的制造成本。
通过模具设计表明该模具能达到旋钮的质量和加工工艺要求。
关键词:
旋钮注塑模参数
论文类型:
设计报告
目录
摘 要1
设计题目:
旋钮模具的设计4
第1章塑件的工艺性分析5
1.1塑件的原材料分析5
1.2塑件的结构和尺寸精度及表面质量分析5
1.3塑件的体积重量6
1.4塑件的注射工艺参数的确定7
第2章型腔数的确定及浇注系统的设计8
2.1分型面的选择8
2.2型腔数的确定8
2.3确定型腔的排列方式9
2.4浇注系统的设计9
2.4.1主流道的设计9
2.4.2冷料穴与拉料杆的设计9
2.4.3分流道的设计10
2.4.4浇口的设计11
2.4.5浇口的选用12
2.4.6浇口位置的选择13
第3章排气及冷却系统的设计与计算14
3.1排气系统的设计14
3.2冷却系统的设计与计算14
3.3标准模架的调入及及标准件相关零件结构的生成等等15
第4章模具工作零件的设计与计算18
4.1凹模和型芯结构类型选择18
4.2型腔型芯工作尺寸的计算18
4.3型腔侧壁厚度和底板厚度的计算19
4.3.1型腔侧壁厚度的计算19
4.3.2底板厚度的计算20
第5章脱模机构的设计与计算21
5.1脱模力的计算21
5.2推板的厚度21
5.3顶杆直径的计算22
第6章注射机与模具各参数的校核23
6.1工艺参数的校核23
6.1.1注射量的校核(按体积)23
6.1.2锁模力的校核23
6.1.3最大注射压和的校核23
6.2安装参数的校核24
第7章:
结论25
参考文献26
致谢27
设计题目:
旋钮模具的设计
材料:
聚甲基丙烯酸甲酯
生产批量:
20万件/年
料厚:
1mm
第1章塑件的工艺性分析
1.1塑件的原材料分析
塑件的材料采用聚甲基丙烯酸甲酯,属热塑性塑料,该塑料具有如下的成型特性:
(1)无定形料、吸湿性大、不易分解。
(2)质脆、表面硬度低。
(3)流动性中等,溢边值0.03mm左右,易发生填充不良、缩孔、凹痕、熔接痕等缺陷。
(4)宜取高压注射,在不出现缺陷的条件下宜取高料温、模温,可增加流动性,降低内应力、方向性,改善透明度及强度。
(5)模具浇注系统应对料流阻力小,脱模斜度应大,顶出均匀,表面粗糙度应好,注意排气。
(6)质透明,要注意防止出现气泡、银丝、熔接痕及滞料分解、混入杂质。
1.2塑件的结构和尺寸精度及表面质量分析
图1-1旋钮
(1)塑件的结构分析
该零件的总体形状为圆形,结构比较简单。
(2)塑件尺寸精度的分析
该零件的重要尺寸,如30.9±0.09mm的尺寸精度为3级,次重要尺寸3.75±0.07mm的尺寸精度为4级,其它尺寸均无公差要求,一般可采用8级精度。
由以上的分析可见,该零件的尺寸精度属中等偏上,对应模具相关零件尺寸的加工可保证。
从塑件的壁厚上来看,壁厚最大处为4.5mm,最小处为2.25mm,壁厚差为2.25mm,较为均匀。
(3)表面质量的分析
该零件的表面要求无凹坑等缺陷外,表面无其它特别的要求,故比较容易实现。
综上分析可以看出,注射时在工艺参数控制得较好的情况下,零件的成型要求可以得到保证。
1.3塑件的体积重量
计算塑件的重量是为了选用注射机及确定模具型腔数。
计算得塑件的体积:
V=9132mm3
计算塑件的质量:
公式为W=Vρ
根据设计手册查得聚甲基丙烯酸甲酯的密度为ρ=1.18kg/dm3,故塑件的重量为:
W=Vρ
=9132×1.18×10-3
=10.776g
根据注射所需的压力和塑件的重量以及其它情况,可初步选用的注射机为SZ-60/40型注塑成型机,该注塑机的各参数如表1-1所示:
表1-1SZ-60/40型注塑成型机各参数值
理论注射量/cm3
60
移模行程/mm
180
螺杆直径/mm
30
最大模具厚度/mm
280
注射压力/Mp
150
最小模具厚度/mm
160
锁模力/KN
400
喷嘴球半径/mm
15
拉杆内间距/mm
295×185
喷嘴口孔径/mm
φ3.5
1.4塑件的注射工艺参数的确定
根据情况,聚甲基丙烯酸甲酯的成型工艺参数可作如下选择,在试模时可根据实际情况作适当的调整。
注射温度:
包括料筒温度和喷嘴温度。
料筒温度:
后段温度t1选用180℃
中段温度t2选用200℃
前段温度t3选用220℃
喷嘴温度:
选用220℃
注射压力:
选用100MP
注射时间:
选用20s
保压时间:
选用2s
保压:
80MP
冷却时间:
选用28s
总周期:
50s
第2章型腔数的确定及浇注系统的设计
2.1分型面的选择
该塑件为旋纽,表面质量无特殊要求,端部因与人手指接触因此形成自然圆角,此零件可采用图2-1所示的分型面比较合适。
图2-1分型面
如何确定分型面,需要考虑的因素比较复杂。
由于分型面受到塑件在模具中的成型位置、浇注系统设计、塑件的结构工艺性及精度、嵌件位置形状以及推出方法、模具的制造、排气、操作工艺等多种因素的影响,因此在选择分型面时应综合分析比较,从几种方案中优选出较为合理的方案。
选择分型面时一般应遵循以下几项原则:
1分型面应选在塑件外形最大轮廓处。
2便于塑件顺利脱模,尽量使塑件开模时留在动模一边。
3保证塑件的精度要求。
4满足塑件的外观质量要求。
5便于模具加工制造。
6对成型面积的影响。
7对排气效果的影响。
8对侧向抽芯的影响
2.2型腔数的确定
型腔数的确定有多种方法,本题采用注射机的注射量来确定它的数目。
其公式如下:
n2=(G-C)/V
式中:
G——注射机的公称注射量/cm3
V——单个制品的体积/cm3
C——浇道和浇口的总体积/cm3
生产中每次实际注射量应为公称注射量G的(0.75-0.45)倍,现取0.6G进行计算。
每件制品所需浇注系统的体积为制品体积的(0.2-1)倍,现取C=0.6V进行计算。
n2=0.6G/1.6V=0.375G/V=(0.375×60)/90132=2.46
由以上的计算可知,可采用一模两腔的模具结构。
2.3确定型腔的排列方式
本塑件在注射时采用一模两件,即模具需要两个型腔。
综合考虑浇注系统、模具结构的复杂程度等因素,拟采用图2-2所示的型腔排列方式。
图2-2型腔排列方式
2.4浇注系统的设计
2.4.1主流道的设计
根据设计手册查得SZ-60/40型注射机喷嘴有关尺寸如下:
喷嘴前端孔径:
d0=φ3.5mm
喷嘴前端球面半径:
R0=15mm
为了使凝料能顺利拔出,主流道的小端直径D应稍大于注射喷嘴直径d。
D=d+(0.5-1)mm=φ3.5+1=φ4.5mm
主流道的半锥角α通常为1°-2°过大的锥角会产生湍流或涡流,卷入空气,过小的锥角使凝料脱模困难,还会使充模时熔体的流动阻力过大,此处的锥角选用2°。
经换算得主流道大端直径D=φ8.5mm,为使熔料顺利进入分流道,可在主流道出料端设计半径r=5mm的圆弧过渡。
主流道的长度L一般控制在60mm之内,可取L=55mm。
2.4.2冷料穴与拉料杆的设计
对于依靠推件板脱模的模具常用球头拉料杆,当前锋冷料进入冷料穴后紧包在拉料杆的球头上,开模时,便可将凝料从主流道中拉出。
球头拉料杆固定在动模一侧的型芯固定板上,并不随脱模机构移动,所以当推件板从型芯上脱出制品时,也将主流道凝料从球头拉料杆上硬刮下来。
其结构如右图所示:
冷料穴一般开设在主流道对面的动模板上(也即塑料流动的转向处),其标称直径与主流道大端直径相同或略大一些,深度约为直径的1-1.5倍,最终要保证冷料的体积小于冷料穴的体积,冷料穴有六种形式,常用的是端部为Z字形和拉料杆的形式,具体要根据塑料性能合理选用。
本模具中的冷料穴的具体位置和形状如图(6)中所示。
实际上只要将分流道顺向延长一段距离就行了。
2.4.3分流道的设计
分流道在设计时应考虑尽量减小在流道内的压力损失和尽可能避免熔体温度的降低,同时还要考虑减小流道的容积。
圆形和正方形流道的效率最高,当分型面为平面时一般采用圆形的截面流道,但考虑到加工的方便性,可采用半圆形的流道。
为了便于加工及凝料脱模,分流道大多设置在分型面上,分流道截面形状一般为圆形梯形U形半圆形及矩形等,工程设计中常采用梯形截面加工工艺性好,且塑料熔体的热量散失流动阻力均不大,一般采用下面的经验公式可确定其截面尺寸:
(式1)
(式2)
式中B―梯形大底边的宽度(mm)
m―塑件的重量(g)
L―分流道的长度(mm)
H―梯形的高度(mm)
梯形的侧面斜角a常取50-150,在应用式(式1)时应注意它的适用范围,即塑件厚度在3.2mm以下,重量小于200g,且计算结果在3.2-9.5mm范围内才合理。
梯形小底边宽度取6mm,其侧边与垂直于分型面的方向约成100。
另外由于使用了水口板(即我们所说的定模板和中间板之间再加的一块板),分流道必须做成梯形截面,便于分流道和主流道凝料脱模。
实际加工时实,常用一种截面尺寸的梯形流道
一般分流道直径在3-10mm范围内,分流道的截面尺寸可根据制品所用的塑料品种、重量和壁厚,以及分流道的长度由《中国模具设计大典》第2卷中图9.2-12所示的经验曲线来选定,经查取D’=5.6mm较为合适,分流道长度取L=20mm从图9.2-14中查得修正系数fL=1.02,则分流道直径经修正后为D=D’fL=5.6×1.02=5.712,取D=6mm
图2-3分流道
图2-4U型分流道截面
2.4.4浇口的设计
根据浇口的成型要求及型腔的排列方式,选用侧浇口较为合适。
侧浇口一般开设在模具的分型面上,从制品的边缘进料,故也称之为边缘浇口。
侧浇口的截面形状为矩形,其优点是截面形状简单,易于加工,便于试模后修正。
缺点是在制品的外表面留有浇口痕迹,因为该制件无表面质量的特殊要求,又是中小型制品的一模两腔结构,所以可以采用侧浇口。
在侧浇口的三个尺寸中,以浇口的深度h最为重要。
它控制着浇口内熔体的凝固时间和型腔内熔体的补缩程度。
浇口宽度W的大小对熔体的体积流量的直接的影响,浇口长度L在结构强度允许的条件下以短为好,一般选L=0.5-0.75mm。
确定浇口深度和宽度的经验公式如下:
h=nt①
W=nA1/2/30②
式中:
h——侧浇口深度(mm)中小型制品常用h=0.5-2mm,约为制品最大壁厚的1/3-2/3,取1.5mm;
t——制品的壁厚(mm),3.38mm;
n——塑料材料的系数,查表得0.8;
W——浇口的宽度(mm);
A——型腔的表面积(mm2),计算得2940mm2。
将以上各数据代入公式得:
h=1.5mm,W=1.5mm,L取0.5mm。
计算后所得的侧浇口截面尺寸可用r=6q/(Wh2)≥104s-1作为初步校验。
制品的体积V=9.132cm3,设定充模时间为1s,于是:
q=9.132/1=9132mm3/s
r=6q/Wh2=(6×9132)/(1.5×1.52)=1.6×104>104s-1
所以符合要求。
2.4.5浇口的选用
浇口可分为限制性和非限制性浇口两种。
我们将采用限制性浇口。
限制性浇口一方面通过截面积的突然变化,使分流道输送来的塑料熔体的流速产生加速度,提高剪切速率,使其成为理想的流动状态,迅速面均衡地充满型腔,另一方面改善塑料熔体进入型腔时的流动特性,调节浇口尺寸,可使多型腔同时充满,可控制填充时间、冷却时间及塑件表面质量,同时还起着封闭型腔防止塑料熔体倒流,并便于浇口凝料与塑件分离的作用。
我们采用的是侧浇口。
侧浇口又称边缘浇口,国外称之为标准浇口。
侧浇口一般开设在分型面上,塑料熔体于型腔的侧面充模,其截面形状多为矩形狭缝,调整其截面的厚度和宽度可以调节熔体充模时的剪切速率及浇口封闭时间。
这灯浇口加工容易,修整方便,并且可以根据塑件的形状特征灵活地选择进料位置,因此它是广泛使用的一种浇口形式,普遍使用于中小型塑件的多型腔模具,且对各种塑料的成型适应性均较强;但有浇口痕迹存在,会形成熔接痕、缩孔、气孔等塑件缺陷,且注射压力损失大,对深型腔塑件排气不便。
具体到这套模具,其浇口形式及尺寸如图7所试。
浇口各部分尺寸都是取的经验值。
实际加工中,是先用圆形铣刀铣出直径为Φ4的分流道,再将材料进行热处理,然后做一个铜公(电极)去放电,用电火花打出这个浇口来的。
2.4.6浇口位置的选择
模具设计时,浇口的位置及尺寸要求比较严格,初步试模后还需进一步修改浇口尺寸,无论采用何种浇口,其开设位置对塑件成型性能及质量影响很大,因此合理选择浇口的开设位置是提高质量的重要环节,同时浇口位置的不同还影响模具结构。
总之要使塑件具有良好的性能与外表,一定要认真考虑浇口位置的选择,通常要考虑以下几项原则:
1)尽量缩短流动距离。
2)浇口应开设在塑件壁厚最大处。
3)必须尽量减少熔接痕。
4)应有利于型腔中气体排出。
5)考虑分子定向影响。
6)避免产生喷射和蠕动。
7)浇口处避免弯曲和受冲击载荷。
8)注意对外观质量的影响。
根据本塑件的特征,综合考虑以上几项原则,每个型腔设计1个进浇点,进浇点1的分流道开在行位上,进浇点2的分流道开在后模模仁上。
第3章排气及冷却系统的设计与计算
3.1排气系统的设计
排气槽的截面积可用如下公式进行计算:
F=25m1(273+T1)1/2/tP0 ①
式中:
F——排气槽的截面面积(m2);
m1——模具内气体的质量(kg);
P0——模具内气体的初始压力(Mp),取0.1Mp;
T1——模具内被压缩气体的最终温度(℃);
t——充模时间(s)。
模内气体质量按常压常温20℃的氮气密度ρ0=1.16kg/m3计算,有:
m1=ρ0V0 ②
式中:
V0——模具型腔的体积(m3)。
应用气体状态方程可求得上式中被压缩气体的最终温度(℃):
T1=(273+T0)(P1/P)0.1304-273 ③
式中:
T0——模具内气体的初始温度(℃)。
由V=9132mm3,充模时间t=1s,被压缩气体最终排气压力为P1=20MPa,
由③式得:
T1=(273+20)(20/0.1)0.1304-273=311.7℃
模具内的气体质量由②式得:
m1=V0ρ0=9.132×10-6×1.16kg=1.06×10-5kg
将数据代入①式得所需排气槽的截面面积为:
F=[25×1.06×10-5(273+311.7)1/2]/(1×0.1×106)=0.064mm2
查取排气槽高度h=0.03mm,因此排气槽的总宽度为:
W’’=F/h=0.064/0.03=2.13mm
为了便于加工和有利于排气,运用镶拼式的型芯结构,与整体式型芯相比,镶拼型芯使加工和热处理工艺大为简化。
3.2冷却系统的设计与计算
冷却系统设计的有关公式:
qV=WQ1/ρc1(θ1-θ2)①
式中:
qV——冷却水的体积流量(m3/min);
W——单位时间内注入模具中的塑料重量(kg/min);
Q1——单位重量的塑料制品在凝固时所放出的热量(kJ/kg);
ρ——冷却水的密度(kg/m3):
0.98×103;
c1——冷却水的比热容[kJ/(kg.℃)]:
4.187;
θ1——冷却水的出口温度(℃):
25;
θ2——冷却水的入口温度(℃):
20。
Q1可表示为:
Q1=[c2(θ3-θ4)+u]
式中:
c2——塑料的比热容[kJ/(kg.℃)]:
1.465;
Q3——塑料熔体的初始温度(℃):
200;
θ4——塑料制品在推出时的温度(℃):
60;
u——结晶型塑料的熔化质量焓(kJ/kg)。
Q1=[c2(θ3-θ4)+u]=1.465(200-60)=205.1kJ/kg
将以上各数代入①式得:
qV=(0.013×205.1)/[0.98×103×4.187(25-20)]m3/min
=0.13×10-3m3/min
上述计算的设定条件是:
模具的平均工作温度为40℃,用常温20℃的水作为模具的冷却介质,其出口温度为25℃,产量为0.013kg/min。
由体积流量查表可知所需的冷却水管的直径非常小,体积流量也很小,故可不设冷却系统,依靠空冷的方式即可。
但为满足模具在不同温度条件下的使用,可在适当的位置布置直径d为8mm的管道来调节温度。
3.3标准模架的调入及及标准件相关零件结构的生成等等
模架的设计可以通过自定义方式,也可以通过调入标准模架来建立。
TopSolid建立了丰富的标准模架库:
DME、FUTABA、HASCO、MEUSBURGER、MOLDMAN、PEDROTTIRABOURDIN、HESTRACK_NORMA(2004年底前增加国标模架库)等众多标准模架库,方便设计者与供应商之间的合作设计。
图九为FUTABA_S3550模架,在调入过程中只需鼠标点击定位点,并选择该模架型号便一切就都交给系统了。
模架的调入只是模具结构设计的第一步,为了大量减少后续的设计操作:
1、TopSolid建立了完善的模具设计用的智能标准件库,如导柱/导套系列、浇注系统系列、顶出机构系列、冷却回路系列、侧楔斜导柱系列及常用的紧固件系列等的标准件库。
2、在设计过程中调用标准件时,系统对其相关的零件自动进行布尔操作,即产生与标准件相对应的孔.
图3-2螺钉孔视图
以顶出机构设计为例:
顶杆设计只需确定顶出点,以及顶杆的相应参数(直径等),其他的操作由系统自动完成。
即在调入顶杆的同时,系统将所有与之关联的各模板都进行打孔及确定相应各点顶杆长度等的标准操作。
另又以调用紧固内六角螺钉为例,他的调入只需选择要安装的点、面和要紧固的零件,系统便会智能地为零件进行打孔操作,所打的各个孔均具有不同的
配间隙,所有操作均符合紧固件设计规范。
第4章模具工作零件的设计与计算
4.1凹模和型芯结构类型选择
凹模的结构采用整体嵌入式,这样有利于节省贵重金属材料。
型芯采用镶拼式结构,有利于加工和排气。
(如图4-1所示)
图4-1
4.2型腔型芯工作尺寸的计算
本设计中零件工作尺寸的计算均采用平均尺寸、平均收缩率、平均制造公差和平均磨损量来进行计算,已给出这PMMA的成型收缩率为0.005,模具的制造公差取z=Δ/3。
表4-1型腔型芯工作尺寸的计算
类别
塑件尺寸
计算公式
模具尺寸
型
腔
计
算
型腔板
φ35.250-1.0
Lm=(Ls+Ls.Scp%-3/4Δ)0+δz
φ34.6800.33
R7.5±0.64
R7.0600.21
19.20±0.44
Hm=(Hs+Hs.Scp%-2/3Δ)0+δz
18.7100.15
推件板
φ30.9±0.09
Lm=(Ls+Ls.Scp%-3/4Δ)0+δz
φ30.8800.06
型
芯
计
算
主型芯
φ26.2500.96
Lm=(Ls+Ls.Scp%+3/4Δ)0-δz
27.100-0.32
R2.25±0.24
R2.620-0.16
17.25±0.48
Hm=(Hs+Hs.Scp%+2/3Δ)0-δz
17.980-0.32
小型芯
φ3.75±0.07
Lm=(Ls+Ls.Scp%+3/4Δ)0-δz
φ3.870-0.05
7.5±0.32
Hm=(Hs+Hs.Scp%+2/3Δ)0-δz
8.050-0