塑料流动性.docx
《塑料流动性.docx》由会员分享,可在线阅读,更多相关《塑料流动性.docx(16页珍藏版)》请在冰豆网上搜索。
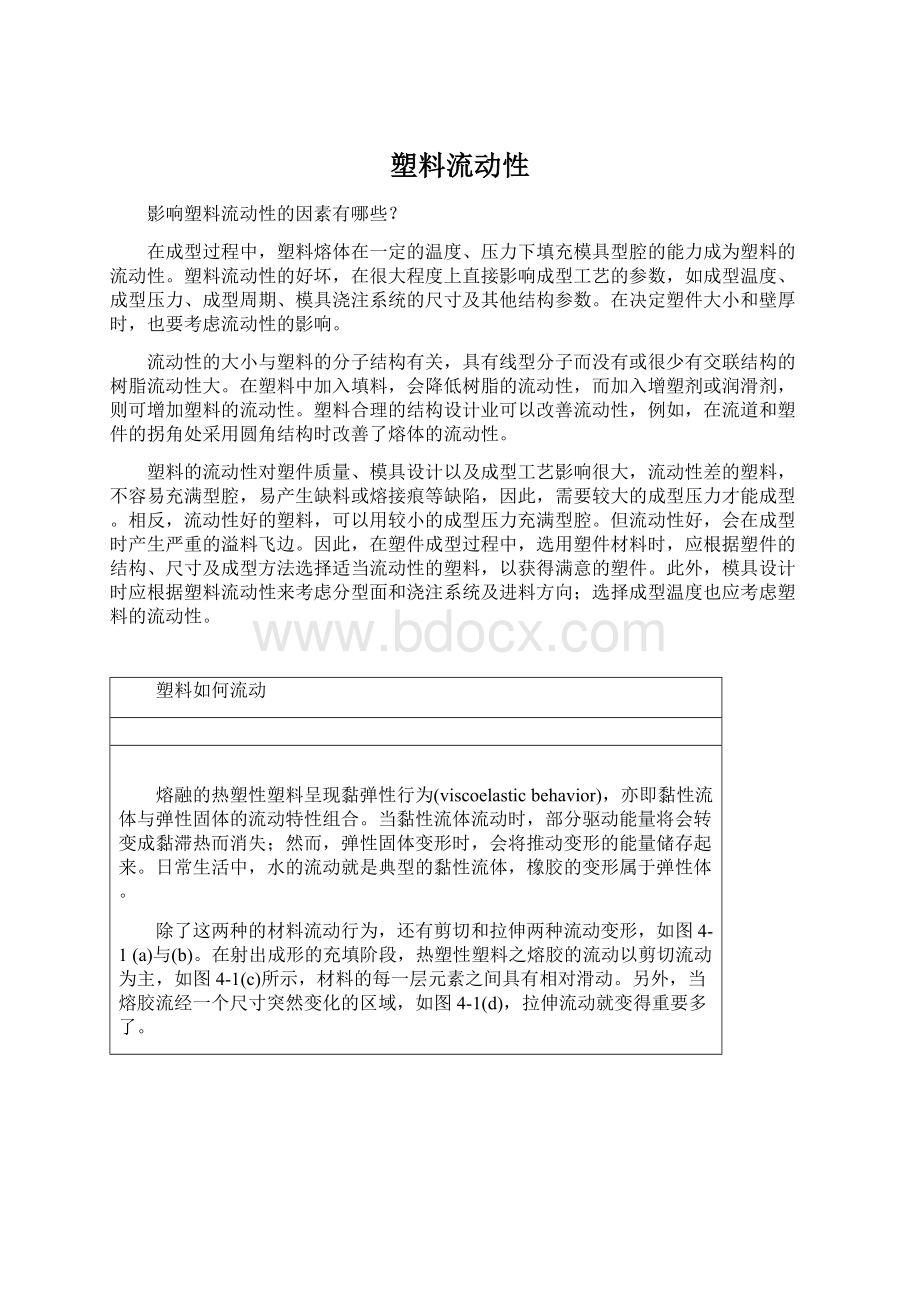
塑料流动性
影响塑料流动性的因素有哪些?
在成型过程中,塑料熔体在一定的温度、压力下填充模具型腔的能力成为塑料的流动性。
塑料流动性的好坏,在很大程度上直接影响成型工艺的参数,如成型温度、成型压力、成型周期、模具浇注系统的尺寸及其他结构参数。
在决定塑件大小和壁厚时,也要考虑流动性的影响。
流动性的大小与塑料的分子结构有关,具有线型分子而没有或很少有交联结构的树脂流动性大。
在塑料中加入填料,会降低树脂的流动性,而加入增塑剂或润滑剂,则可增加塑料的流动性。
塑料合理的结构设计业可以改善流动性,例如,在流道和塑件的拐角处采用圆角结构时改善了熔体的流动性。
塑料的流动性对塑件质量、模具设计以及成型工艺影响很大,流动性差的塑料,不容易充满型腔,易产生缺料或熔接痕等缺陷,因此,需要较大的成型压力才能成型。
相反,流动性好的塑料,可以用较小的成型压力充满型腔。
但流动性好,会在成型时产生严重的溢料飞边。
因此,在塑件成型过程中,选用塑件材料时,应根据塑件的结构、尺寸及成型方法选择适当流动性的塑料,以获得满意的塑件。
此外,模具设计时应根据塑料流动性来考虑分型面和浇注系统及进料方向;选择成型温度也应考虑塑料的流动性。
塑料如何流动
熔融的热塑性塑料呈现黏弹性行为(viscoelasticbehavior),亦即黏性流体与弹性固体的流动特性组合。
当黏性流体流动时,部分驱动能量将会转变成黏滞热而消失;然而,弹性固体变形时,会将推动变形的能量储存起来。
日常生活中,水的流动就是典型的黏性流体,橡胶的变形属于弹性体。
除了这两种的材料流动行为,还有剪切和拉伸两种流动变形,如图4-1(a)与(b)。
在射出成形的充填阶段,热塑性塑料之熔胶的流动以剪切流动为主,如图4-1(c)所示,材料的每一层元素之间具有相对滑动。
另外,当熔胶流经一个尺寸突然变化的区域,如图4-1(d),拉伸流动就变得重要多了。
图4-1(a)剪切流动;(b)拉伸流动;(c)模穴的剪切流动
(d)充填模穴的拉伸流动
热塑性塑料承受应力时会结合理想黏性流体和理想弹性固体之特性,呈现黏弹性行为。
在特定的条件下,熔胶像液体一样受剪应力作用而连续变形;然而,一旦应力解除,熔胶会像弹性固体一样恢复原形,如图4-2(b)与(c)所示。
此黏弹性行为是因为聚合物在熔融状态,分子量呈现杂乱卷曲型态,当受到外力作用时,将允许分子链移动或滑动。
然而,相互纠缠的聚合物分子链使系统于施加外力或解除外力时表现出弹性固体般的行为。
譬如说,在解除应力后,分子链会承受一恢复应力,使分子链回到杂乱卷曲的平衡状态。
因为聚合物系统仍有分子链的交缠,此恢复应力可能不是立即发生作用。
图4-2(a)理想的黏性液体在应力作用下表现出连续的变形;
(b)理想的弹性固体承受外力会立刻变形,于外力解除后完全恢复原形;
(c)热塑性塑料之熔胶就像液体一样,在剪切应力作用下而连续变形。
然而,一旦应力解除,它就像弹性固体一般,部分变形会恢复原形。
4-1熔胶剪切黏度
熔胶剪切黏度(shearviscosity)是塑料抵抗剪切流动的阻力,它是剪切应力与剪变率的比值,参阅图4-3。
。
聚合物熔胶因长分子构而具有高黏度,通常的黏度围介于2~3000Pa(水为10-1Pa,玻璃为1020Pa)。
图4-3以简易之剪切流动说明聚合物熔胶黏度的定义
水是典型的牛顿流体,牛顿流体的黏度与温度有关系,而与剪变率无关。
但是,大多数聚合物熔胶属于非牛顿流体,其黏度不仅与温度有关,也与剪切应变率有关。
聚合物变形时,部份分子不再纠缠,分子链之间可以相互滑动,而且沿著作用力方向配向,结果,使得聚合物的流动阻力随着变形而降低,此称为剪变致稀行为(shearing-thinningbehavior),它表示聚合物承受高剪变率时黏度会降低,也提供了聚合物熔胶加工便利性。
例如,以两倍压力推动开放管线的水,水的流动速率也倍增。
但是,以两倍压力推动开放管线的聚合物熔胶,其流动速率可能根据使用材料而增加2~15倍。
介绍了剪切黏度的观念,再来看看射出成形时模穴的剪变率分布。
一般而言,材料的连接层之间的相对移动愈快,剪变率也愈高,所以,典型的熔胶流动速度曲线如图4-4(a),其在熔胶与模具的界面处具有最高的剪变率;或者,假如有聚合物凝固层,在固体与液体界面处具有最高的剪变率。
另一方面,在塑件中心层因为对称性流动,使得材料之间的相对移动趋近于零,剪变率也接近零,如图4-4(b)所示。
剪变率是一项重要的流动参数,因为它会影响熔胶黏度和剪切热(黏滞热)的大小。
射出成形制程的典型熔胶剪变围在102~1051/s之间。
图4-4(a)相对流动元素间运动之典型速度分布曲线;
(b)射出成形之充填阶段的剪变率分布图。
聚合物分子链的运动能力随着温度升高而提高,如图4-5所示,随着剪变率升高与温度升高,熔胶黏度会降低,而分子链运动能力的提升会促进较规则的分子链排列及降低分子链相互纠缠程度。
此外,熔胶黏度也与压力相关,压力愈大,熔胶愈黏。
材料的流变性质将剪切黏度表示为剪变率、温度与压力的函数。
图4-5聚合物黏度与剪变率、温度、及压力的关系
4-2熔胶流动之驱动--射出压力
射出机的射出压力是克服熔胶流动阻力的驱动力。
射出压力推动熔胶进入模穴以进行充填和保压,熔胶从高压区流向低压区,就如同水从高处往低处流动。
在射出阶段,于喷嘴蓄积高压力以克服聚合物熔胶的流动阻力,压力沿着流动长度向聚合物熔胶波前逐渐降低。
假如模穴有良好的排气,则最终会在熔胶波前处达到大气压力。
压力分布如图4-6所示。
图4-6压力沿着熔胶输送系统和模穴而降低
模穴入口的压力愈高,导致愈高的压力梯度(单位流动长度之压力降)。
熔胶流动长度加长,就必须提高入口压力以产生相同的压力梯度,以维持聚合物熔胶速度,如图4-7所示。
图4-7熔胶速度与压力梯度的关系
根据古典流体力学的简化理论,充填熔胶输送系统(竖浇道、流道和浇口)和模穴所需的射出压力与使用材料、设计、制程参数等有关系。
图4-8显示射出压力与各参数的函数关系。
使用P表示射出压力,n表示材料常数,大多数聚合物的n值介于0.15~0.36之间,0.3是一个适当的近似值,则熔胶流动在竖浇道、流道和圆柱形浇口等圆形管道所需的射出压力为:
熔胶流动在薄壳模穴之带状管道所需的射出压力为:
熔胶的流动速度与流动指数(MeltIndex,MI)有关,流动指数也称为流导flowconductance),流动指数是熔胶流动难易的指标。
实际上,流动指数是塑件几何形状(例如壁厚,表面特征)及熔胶黏度的函数。
流动指数随着肉厚增加而降低,但是随着熔胶黏度增加而降低,参阅图4-9。
射出成形时,在特定的成形条件及塑件肉厚下,熔胶可以流动的长度将根据材料的热卡性质与剪切性质而决定,此性质可以表示为熔胶流动长度,如图4-10所示。
图4-8射出压力与使用材料知黏滞性、流动长度、容积流率和肉厚的函数关系
图4-9 流动指数相对于壁厚与黏度关系
图4-10 熔胶流动长度决定于塑件厚度和温度
将射出成形充填模穴的射出压力相对于充填时间画图,通常可以获得U形曲线,如图4-11,其最低射出压力发生在曲线的中段时间。
要采用更短的充填时间,则需要高熔胶速度和高射出压力来充填模穴。
要采用较长的充填时间,可以提供塑料较长的冷却时间,导致熔胶黏度提高,也需要较高的射出压力来充填模穴。
射出压力相对于充填时间的曲线形状与所使用材料、模穴几何形状和模具设计有很大的关系。
图4-11 射出压力相对于充填时间之U形曲线
最后必须指出,因为熔胶速度(或剪变率)、熔胶黏度与熔胶温度之间交互作用,有时候使得充填模穴的动力学变得非常复杂。
注意,熔胶黏度随着剪变率上升及温度上升而降低。
高熔胶速度造成的高剪变率及高剪切热可能会使黏度降低,结果使流动速度更加快,更提高了剪变率和熔胶温度。
所以对于剪变效应很敏感的材料本质上具有不稳定性。
4-2-1影响射出压力的因素
图4-12针对影响射出压力的设计与成形参数进行比较。
参数
需要高射出压力
可用低射出压力
塑件设计
肉厚
塑件表面
浇口设计
浇口尺寸
流动长度
成形条件
熔胶温度
模壁(冷却剂)温度
螺杆速度
选择材料
熔胶流动指数
图4-12射出压力与设计、成形参数、材料的关系
4-3充填模式
充填模式(FillingPattern)是熔胶在输送系统与模穴,随着时间而变化的流动情形,如图4-13所示。
充填模式对于塑件品质有决定性的影响,理想的充填模式是在整个制程中,熔胶以一固定熔胶波前速度(meltfrontvelocity,MFV)同时到达模穴的每一角落;否则,模穴先填饱的区域会因过度充填而溢料。
以变化之熔胶波前速度充填模穴,将导致分子链或纤维配向性的改变。
图4-13计算机仿真之熔胶充填模式的影像
4-3-1熔胶波前速度与熔胶波前面积
熔胶波前的前进速度简称为MFV,推进熔胶波前的剖面面积简称为MFA,MFA可以取熔胶波前横向长度乘上塑件肉厚而得到,或是取流道剖面面积,或者视情况需要而取两者之和。
在任何时间,
容积流动率=熔胶波前速度(MFV)×熔胶波前面积(MFA)
对于形状复杂的塑件,使用固定的螺杆速率并不能保证有固定的熔胶波前速度。
当模穴剖面面积发生变化,纵使射出机维持了固定的射出速度,变化之熔胶波前速度仍可能先填饱模穴的部份区域。
图4-14显示在镶埋件(insert)周围熔胶波前速度增加,使镶埋件两侧产生高压力和高配向性,造成塑件潜在的不均匀收缩和翘曲。
图4-14熔胶波前速度(MFV)和熔胶波前面积(MFA)。
MFV之差异会
使得塑料分子(以点表示)以不同方式伸展,导致分子与纤维
配向性的差异,造成收缩量差异或翘曲。
在射出成形的充填阶段,塑料材料的分子链或是填充料会依照剪应力之作用而发生配向。
由于模温通常比较低,在表面附近的配向性几乎瞬间即凝固。
分子链和纤维的配向性取决于熔胶之流体动力学和纤维伸展的方向性。
在熔胶波前处,由于剪切流动和拉伸流动的组合,不断强迫熔胶从肉厚中心层流向模壁,造成喷泉流效应(fountainfloweffect),此效应对塑件表层的分子链/纤维配向性的影响甚巨。
请参阅图4-15之说明。
图4-15塑件表层与中心层之纤维配向性
塑件成形之MFV愈高,其表面压力愈高,分子链配向性的程度也愈高。
充填时的MFV差异会使得塑件的配向性差异,导致收缩不同而翘曲,所以充填时应尽量维持固定的MFV,使整个塑件有均匀的分子链配向性。
MFV和MFA是流动平衡的重要设计参数。
不平衡流动的MFA会有突然的变化,当部分的模穴角落已经充饱,部分的熔胶仍在流动。
对于任何复杂的几何形状,应该将模穴的MFA变化最小化,以决定最佳的浇口位置。
流动平衡时,熔胶波前面积有最小的变化,如图4-16所示。
图4-16(a)MFA变化导致的平衡与不平衡流动;及(b)其对应的充填模式。
4-4流变理论
流变学(rheology)是探讨材料受力后变形和流动的加工特性,包括剪变率、剪切黏度、黏弹性、黏滞热、拉伸黏度等等。
熔融塑料大多呈现拟塑性行为,即根据指数律(powerlaw),
,n<1
塑料受剪应力而运动时,其黏度随剪变率增加而降低,此现象称为高分子材料的剪稀性(shearthinning)。
通常厂商比较常提供的塑料特性指标是流动指标MI(Meltindex),一般塑料的MI值大约介于1~25之间,MI值愈大,代表该塑料黏度愈小,分子重量愈小;反之,MI值愈小,代表该塑料黏度愈大,分子重量愈大。
MI值仅仅是塑料剪切黏度曲线上的一点。
(注:
黏度单位1cp=0.001Pa•s,cp=centipoise,Pa=N/m2)
其它影响塑料性质的因素包括分子量的大小及分子量分布、分子配向性、玻璃转移温度和添加物等。
(1)分子量的大小及分子量分布
塑料的特性之一就是分子量很大,分子量分布曲线和其聚合的方法及条件对于所制造出来的成型品有密切影响。
分子量大者璃转移温度Tg较高,机械性质、耐热性、耐冲击强度皆提升,但是黏度亦随分子量增大而提高,造成加工不易。
就分子量分布而言,短分子链影响拉伸及冲击强度,中分子链影响溶液黏度及低剪切熔胶流动,长分子链的量影响熔胶弹性。
(2)玻璃转移温度(glasstransitiontemperature,Tg)
其意思即高分子链开始具有大移动,也就是脱离硬绑绑的玻璃态,开始较具延展性的温度。
而Tg的大小对于塑料性质有很大的影响,所以往往成为判断塑料性质的重要指标,玻璃态时显现出类似玻璃的刚硬性质,但于橡胶态时,又变成较软之橡胶性质。
(3)分子配向性
塑料材料原来的性质会随着外来的因素和作用力而改变,例如聚合物熔胶的黏度(表示材料流动阻力)随分子量增加而增加,但随温度增加而减少。
更进一步,作用于材料的高剪应力所造成的分子配向性也会降低塑料熔胶的黏度。
(4)添加剂、填充材料、及补强材料对于聚合物的影响
包括安定剂、润滑剂、塑化剂、抗燃剂、着色剂、发泡剂、抗静电剂、填充材料、及补强材料等等可以用来改变获改善塑料的物理性质和机械性质。
流动性好尼龙,聚乙烯,聚苯乙烯,聚丙烯,醋酸纤维素,聚(4)甲基戍烯;
流动性中等聚苯乙烯系列树脂(如ABS、AS),有机玻璃,聚甲醛,聚苯醚;
流动性差聚碳酸酯,硬聚氯乙烯,聚苯醚,聚砜,聚芳砜,氟塑料.
塑料熔体的粘度与流动性
(2011-06-1515:
05:
34)
▼
标签:
塑料粘度
杂谈
分类:
塑料行业
塑料熔体的剪切变稀
塑料熔体为非牛顿流体,一个与注射成型密切相关的加工性是塑料熔体的剪切变稀,流体的粘度不随剪切速率变化而变化,这种流体称之为牛顿流体,如水、气体、低分子化合物液体或溶液为典型的牛顿流体,如果流体的粘度依赖于对其的剪切速率,这样的流体为非牛顿流体,大部分塑料熔体表现为非牛顿流体的特性。
非牛顿流体也有多种,塑料在熔融状态下表现出来的特性在图4的坐标中,呈现的是一条切应力先迅速上升而后缓慢上升的曲线,并且不存在屈服应力,这就是塑料熔体剪切变稀的流动特性。
即剪切速率的增加要比切应力的增加来得快,如图4所示。
与之相对应的是剪切变厚的现象。
但是常见的塑料熔体都呈现的是剪切变稀,也就是随着剪切速率的增加,熔体的粘度要降低,粘度降低有助于塑料熔体在模具型腔中的流动和填充。
注塑过程中塑料要通过料筒加热,然后经过注塑机的喷嘴,进入模具的主流道,流道以及模具的浇口,最后进入型腔。
熔体经过各个部分的剪切速率和粘度关系如图5所示,该图表明,塑料熔体在料筒中粘度较高,流动速度也小,到达浇口后,由于浇口的收缩作用,使得熔体流动速度增加,增大了剪切速率,降低了熔体的粘度,有利于熔体的充模。
宽MWD树脂比窄分布树脂剪切变稀程度大。
影响粘度的几个因素
粘度是塑料加工性最重要的基本概念之一,是对流动性的定量表示,影响粘度的因素有熔体温度、压力、剪切速率以及相对分子质量等,下面分别叙述。
(1)温度的影响由前面的分析已经知道,塑料的粘度是剪切速率的函数,但是,塑料的粘度同时也受到温度的影响。
所以,只有剪切速率恒定时,研究温度对粘度的影响才有实际意义。
一般说,塑料熔体粘度的敏感性要比对剪切作用敏感强。
研究表明,随着温度的升高,塑料熔体的粘度呈指数函数方式下降。
这是因为,温度升高,必然使得分子间,分子链间的运动加快,从而使得塑料分子链之间的缠绕降低,分子之间的距离增大,从而导致粘度降低。
易于成型,但制品收缩率大,还会引起分解,温度太低,熔体粘度大,流动困难,成型性差,并且弹性大,也会使制品的形状稳定性差。
但是不同的塑料粘度对于温度的程度不同。
聚甲醛对温度的变化最不敏感,其次是聚乙烯、聚丙烯、聚苯乙烯,最敏感的要数乙酸纤维素,表1中列出了一些常用塑料对于温度的敏感程度。
非常敏感的塑料,温控十分重要,否则粘度较大变化,使操作不稳定,影响产品质量。
表1一些塑料粘度受温度的影响程度
塑料CAPSPPPEPOM
对温度敏感度最高较高高一般差
在实用中,对于温度敏感性好的熔体,可以考虑在成型过程中提高塑料的成型温度来改善塑料的流动性能,如PMMA、PC、CA、PA。
但是对于敏感性差的塑料,提高温度对于改善流动性能并不明显,所以一般不采用提高温度的办法来改进其流动特性。
如POM和PE、PP等非极性塑料,即使温度升幅度很大,粘度却降低很小。
还有,提高温度必须受到一定条件的限制,就是成型温度必须在塑料允许的成型温度围之,否则,塑料就会发生降解。
成型设备损耗大,工作条件恶化,得不偿失。
利用活化能的大小来表达物料的粘度和温度的关系,有定量意义。
表2为一些塑料在低剪切速率下的活化能。
表2一些塑料的活化能kJ/mol
塑料HDPEPPLDPEPSABSPC
活化能26.5~29.437.8~4049.110588.2~109.2109.2~126
(2)压力的影响塑料熔体部的分子之间、分子链之间具有微小的空间,即所谓的自由体积。
因此塑料是可以压缩的。
注射过程中,塑料受到的外部压力最大可以达到几十甚至几百MPa。
在此压力作用下,大分子之间的距离减小,链段活动围减小,分子间距离缩小,分子间的作用力增加,致使链间的错动则更为困难,表现为整体粘度增大。
但是不同塑料在同样的压力下,粘度的增大程度并不相同。
聚苯乙烯(PS)对于压力的敏感程度最高,即增加压力时,粘度增加得很快。
高密度聚乙烯与低密度聚乙烯相比,压力对粘度的影响较小,聚丙烯受压力的影响相当于中等程度的聚乙烯。
增加压力引起粘度增加这一事实表明,单纯通过增加压力去提高塑料熔体的流量是不恰当的。
过高的压力不仅不能明显地改善流体的填充,而且由于粘度的增加,填充性能有时还会有下降的可能,不仅造成过多的功率损耗和过大的设备磨损,还会引起溢料和增加制品应力等弊病。
此外,压力过高,还会出现制品变形等注塑缺陷,导致功率的过度消耗。
但压力过低则会造成缺料。
结合温度对于粘度的影响可以发现,在塑料的正常加工参数围,增加压力对塑料熔体粘度的影响和降低温度对于塑料粘度的影响效果相似。
例如对于很多塑料,当压力增加到100MPa时,其粘度的变化相当于降低温度30~50℃的作用。
几种塑料对于压力的敏感程度如表3所示。
表3压力对塑料熔体粘度的影响
序号名称熔体温度/℃压力变化围/MPa粘度增大倍数
1PS1960~126.6134
2PS18014~175.9100
3PE1490~126.614
4HDPE14~175.84.1
5LDPE14~175.85.6
6MDPE14~175.86.8
7PP14~175.87.3
(3)剪切速率的影响随着剪切速率的加大,塑料的粘度一般降低。
但在剪切速率很低和很高的情况下,粘度几乎不随剪切速率变化而变化。
在温度和压力一定前提下,不同塑料粘度降低程度不相同。
或者说,尽管大多数塑料熔体的粘度是随着剪切速率的增加而下降的,但是不同的塑料对剪切速率(切应力)的敏感程度是不一样的。
几种常用塑料的粘度对于剪切速率的敏感性如表4所示。
表4塑料熔体粘度对剪切速率的敏感度
序号塑料敏感度
1ABS(最敏感)
对剪切的敏感度依次降低
2PC
3PMMA
4PVC
5PA
6PP
7PS
8LDPE(最不敏感)
这一点对使用的启示是:
在一定的剪切速率围,提高剪切速率会显著降低塑料的粘度,改善其流动性能。
尽管如此,宁可选择在熔体粘度对剪切速率不太敏感的围进行工艺调整,否则因为剪切速率的波动,会造成加工不稳定和塑料制品质量上的缺陷。
(4)塑料结构的影响对于塑料,在给定温度下,随着相对平均分子质量的增大,塑料的粘度增大。
相对分子质量越大,分子间作用力越强,于是粘度也高。
塑料的相对分子质量越小,粘度对于剪切速率的依赖程度越小;分子量越大,粘度对于剪切速率的依赖程度越大。
分子量分布宽的树脂和双峯分子量分布树脂熔体粘度低和加工性优良。
因为低分子量链部分有利于提高树脂熔体流动性。
(5)低分子量添加剂的影响低分子可降低大分子链间的作用力,起“润滑”作用因而使熔体粘度减少,同时降低了粘流化温度。
如加入增塑剂和溶剂,使树脂易于充模成型。
表5常用塑料改进流动性能的方法
塑料改进方法塑料改进方法
PE提高螺杆速度PS选非结晶型牌号
PP提高螺杆速度ABS提高温度
PA提高温度PVC提高温度
POM提高螺杆速度PMMA提高温度
PC提高温度
总之,聚合物熔体粘度的大小直接影响注射成型过程的难易。
如控制某塑料成型温度在其分解温度以下,剪切速率为103秒-1时,熔体粘度为50~500帕-秒,注射成型较容易。
但如果粘度过大,就要求有较高的注射压力,制品的大小受到限制,而且制品还容易出现缺陷;如果粘度过小,溢模现象严重,产品质量也不容易保证,在这种情况下要求喷嘴有自锁装置。
熔融指数与热塑性塑料流动性有何关系
熔融指数(M1),是热塑性塑料在一定温度和一定压力下,熔体在10min通过标准毛细管的重量值,以克重/10min表示。
采用熔融指数测定仪测定。
熔融指数越大,塑料在熔融时的流动性越好。
熔融指数越小,塑料在熔融时的流动性越差。
对同一种高聚物,熔融指数大,表示分子量小;常用作高聚物分子量为分类的标志。
在选择树脂时,是否熔融指数越大越好。
流动性故然是在塑料加工时要考虑的一个方面,还要看它开口性,印刷性等指标;国产低密度聚乙烯包装薄膜用树脂,MI一般在2.5左右。
所以我们在选择低密度聚乙烯树脂时,首先要看它是不是薄膜级,最好是轻包装级的,或者是普通包装级的。