金属材料的力学性能.docx
《金属材料的力学性能.docx》由会员分享,可在线阅读,更多相关《金属材料的力学性能.docx(16页珍藏版)》请在冰豆网上搜索。
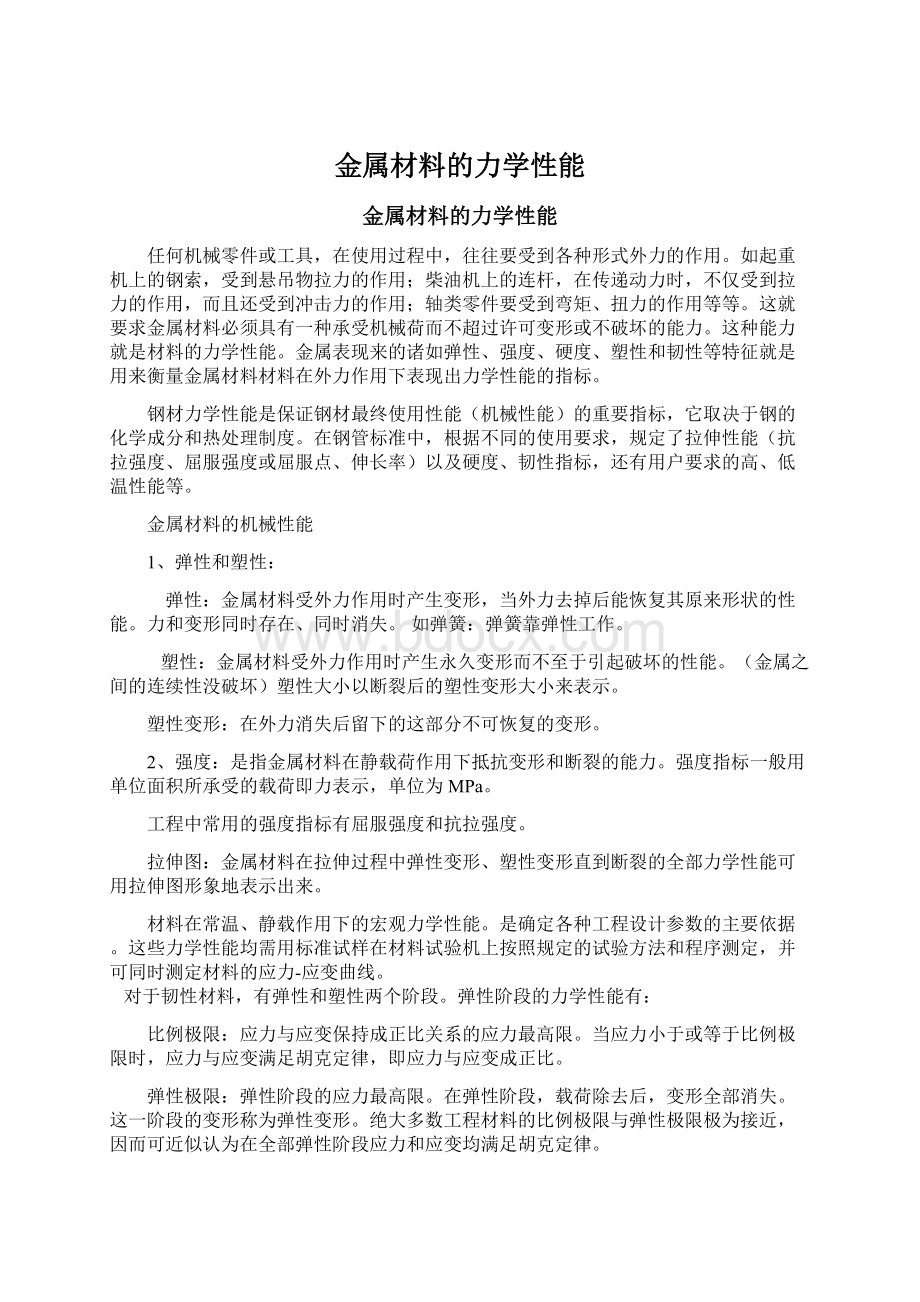
金属材料的力学性能
金属材料的力学性能
任何机械零件或工具,在使用过程中,往往要受到各种形式外力的作用。
如起重机上的钢索,受到悬吊物拉力的作用;柴油机上的连杆,在传递动力时,不仅受到拉力的作用,而且还受到冲击力的作用;轴类零件要受到弯矩、扭力的作用等等。
这就要求金属材料必须具有一种承受机械荷而不超过许可变形或不破坏的能力。
这种能力就是材料的力学性能。
金属表现来的诸如弹性、强度、硬度、塑性和韧性等特征就是用来衡量金属材料材料在外力作用下表现出力学性能的指标。
钢材力学性能是保证钢材最终使用性能(机械性能)的重要指标,它取决于钢的化学成分和热处理制度。
在钢管标准中,根据不同的使用要求,规定了拉伸性能(抗拉强度、屈服强度或屈服点、伸长率)以及硬度、韧性指标,还有用户要求的高、低温性能等。
金属材料的机械性能
1、弹性和塑性:
弹性:
金属材料受外力作用时产生变形,当外力去掉后能恢复其原来形状的性能。
力和变形同时存在、同时消失。
如弹簧:
弹簧靠弹性工作。
塑性:
金属材料受外力作用时产生永久变形而不至于引起破坏的性能。
(金属之间的连续性没破坏)塑性大小以断裂后的塑性变形大小来表示。
塑性变形:
在外力消失后留下的这部分不可恢复的变形。
2、强度:
是指金属材料在静载荷作用下抵抗变形和断裂的能力。
强度指标一般用单位面积所承受的载荷即力表示,单位为MPa。
工程中常用的强度指标有屈服强度和抗拉强度。
拉伸图:
金属材料在拉伸过程中弹性变形、塑性变形直到断裂的全部力学性能可用拉伸图形象地表示出来。
材料在常温、静载作用下的宏观力学性能。
是确定各种工程设计参数的主要依据。
这些力学性能均需用标准试样在材料试验机上按照规定的试验方法和程序测定,并可同时测定材料的应力-应变曲线。
对于韧性材料,有弹性和塑性两个阶段。
弹性阶段的力学性能有:
比例极限:
应力与应变保持成正比关系的应力最高限。
当应力小于或等于比例极限时,应力与应变满足胡克定律,即应力与应变成正比。
弹性极限:
弹性阶段的应力最高限。
在弹性阶段,载荷除去后,变形全部消失。
这一阶段的变形称为弹性变形。
绝大多数工程材料的比例极限与弹性极限极为接近,因而可近似认为在全部弹性阶段应力和应变均满足胡克定律。
塑性阶段的力学性能有:
屈服强度:
材料发生屈服时的应力值。
又称屈服极限。
屈服时应力不增加但应变会继续增加。
屈服点:
具有屈服现象的金属材料,试样在拉伸过程中力不增加(保持恒定)仍能继续伸长时的应力,称屈服点。
若力发生下降时,则应区分上、下屈服点。
屈服点的单位为N/mm2(MPa)。
上屈服点(ReH):
试样发生屈服而力首次下降前的最大应力;
下屈服点(ReL):
当不计初始瞬时效应时,屈服阶段中的最小应力。
条件屈服强度:
某些无明显屈服阶段的材料,规定产生一定塑性应变量(例如0.2%)时的应力值,作为条件屈服强度。
应力超过屈服强度后再卸载,弹性变形将全部消失,但仍残留部分不可消失的变形,称为永久变形或塑性变形。
规定非比例延伸强度(Rp):
非比例延伸率等于规定的引伸计标距百分率时的应力,例如Rp0.2表示规定非比例延伸率为0.2%时的应力。
规定总延伸强度(Rt):
总延伸率等于规定的引伸计标距百分率时的应力。
例如Rt0.5表示规定总延伸率为0.5%时的应力。
强化与强度极限:
应力超过屈服强度后,材料由于塑性变形而产生应变强化,即增加应变需继续增加应力。
这一阶段称为应变强化阶段。
强化阶段的应力最高限,即为强度极限(抗拉强度)。
应力达到强度极限后,试样会产生局部收缩变形,称为颈缩。
抗拉强度(Rm)
试样在拉伸过程中,在拉断时所承受的最大力(Fm),除以试样原横截面积(So)所得的应力(Rm),称为抗拉强度,单位为N/mm2(MPa)。
它表示金属材料在拉力作用下抵抗破坏的最大能力。
计算公式为:
Rm=Fm/So
式中:
Fm--试样拉断时所承受的最大力,N(牛顿);
So--试样原始横截面积,mm2。
工程中常用的塑性指标有伸长率和断面收缩率。
断后伸长率(A)
在拉伸试验中,试样拉断后其标距所增加的长度与原标距长度的百分比,称为伸长率。
以A表示,单位为%。
一般A>5%为塑性材料,A<5%为脆性材料。
断面收缩率(Z)
在拉伸试验中,试样拉断后其缩径处横截面积的最大缩减量与原始横截面积的百分比,称为断面收缩率。
以Z表示,单位为%
伸长率和断面收缩率越大,其塑性越好;反之,塑性越差。
良好的塑性是金属材料进行压力加工的必要条件,也是保证机械零件工作安全,不发生突然脆断的必要条件。
对于脆性材料(A≤5%),没有明显的屈服与塑性变形阶段,试样在变形很小时即被拉断,这时的应力值称为强度极限。
某些脆性材料的应力-应变曲线上也无明显的直线阶段,这时,胡克定律是近似的。
弹性模量由应力-应变曲线的割线的斜率确定。
压缩时,大多数工程韧性材料具有与拉伸时相同的屈服强度与弹性模量,但不存在强度极限。
大多数脆性材料,压缩时的力学性能与拉伸时有较大差异。
例如铸铁压缩时会表现出明显的韧性,试样破坏时有明显的塑性变形,断口沿约45°斜面剪断,而不是沿横截面断裂;强度极限比拉伸时高4~5倍。
拉伸试验:
拉伸试件的加工须按GB/T228-2002的有关要求进行,分为长比例、短比例两种。
如标准圆截面试件有:
长试件:
Lo=10do短试件:
Lo=5do
式中Lo为圆形截面试件的标距长度;do为试样在标距的初始直径,通常为3~25mm,多数情况下取do=10mm。
试件一般有四种形式:
双肩头部试件、单肩头部试件、螺纹头部试件和光面圆柱形头部试件。
下图为光面圆柱形头部试件的简图及加工要求。
为测定低碳钢的断后伸长率A,须用刻线机(或小钢冲)在试样标距围刻划圆周线(或打小冲点),将标距Lo分为等长的10格。
(a)
(b)图1-1拉伸试件
试验原理
拉伸试验是测定材料力学性能最基本的实验之一。
材料的力学性能如屈服点、抗拉强度、断后伸长率和断面收缩率等均是由拉伸试验测定的。
低碳钢
(l)荷载-伸长曲线的绘制。
通过试验机绘图装置可自动绘成以轴向力
为纵坐标、试件伸长量
为横坐标的荷载-伸长曲线(
图),如图1-2(a)所示。
低碳钢的荷载-伸长曲线是一种典型的形式,整个拉伸变形分四个阶段:
弹性变形阶段、屈服阶段、强化阶段和缩颈阶段。
(2)屈服点的测定。
当载荷增加,变形也与载荷成正比增加,
图上为一直线,此即直线弹性阶段。
过了直线弹性阶段,尚有一极小的非直线弹性阶段,因此,弹性阶段包括直线弹性阶段和非直线弹性阶段。
图1-2低碳钢及铸铁拉伸图
当载荷增加到一定程度,测力指针往回偏转,继而缓慢地来回摆动,相应地在
图上画出一段锯齿形曲线,此段即屈服阶段。
经过抛光的试样,在屈服阶段可以观察到与轴线大约成45o的滑移线纹。
曲线在屈服阶段初次瞬时效应之后的最低点所对应的荷载作为下屈服载荷,与其对应的应力称为下屈服强度。
ReL=FPS/So
式中,So为试件标距围的原始横截面面积,单位为mm2,FPS为下屈服载荷,单位为N,ReL为下屈服应力,单位为MPa。
(3)抗拉强度的测定。
过了屈服阶段,随着荷载的增加,试件恢复承载能力,
图的曲线上升,此即强化阶段。
荷载增加到最大值处,测力主动指针回退,试件明显变细变长,
图的曲线下降,试件某一局部截面面积急速减小而出现“颈缩”现象,很快即被拉断,此即缩颈阶段。
试件断裂面的两面各成凹凸状。
由测力度盘上从动指针停留处读取最大荷载值,来计算抗拉强度。
试验出现下列情况之一时,试验结果无效:
1、试样断在标距外或断在机械刻划的标距标记上,而且断后伸长率小于规定最小值时。
2、试验期间设备发生故障,影响了试验结果。
冲击试验
冲击韧性
金属材料抵抗冲击载荷的能力称为冲击韧性,冲击韧性常用一次摆锤冲击弯曲试验测定。
冲击试验原理如图所示。
试验在摆锤式冲击试验机上进行,将标准试样水平放置于试验机支座上,缺口位于冲击相背方向。
冲击时将具有一定质量G的摆锤举至具有一定高度H1的位置。
使其获得一定位能GH1,释放摆锤冲断试样后摆锤的剩余能量为GH2,则摆锤冲断试样失去的位能为GH1-GH2,此即为试样变形和断裂所吸收的功。
具体的试验与方法及操作规可参考GB/T229-1994。
摆锤式冲击试验机主要有机架、摆锤、试样支座、指示装置及摆锤释放、制动和提升机构等组成。
目前常用的国产摆锤式冲击试验机型号很多,500J、300J冲击试验机比较常用。
冲击试验因试验温度不同而分为常温、低温和高温冲击试验三种;若按试样缺口形状又可分为"V"形缺口和"U"形缺口冲击试验两种。
冲击试验:
用一定尺寸和形状(10×10×55mm)的试样(长度方向的中间处有"U"型或"V"型缺口,缺口深度2mm)在规定试验机上受冲击负荷打击下自缺口处折断的试验。
冲击吸收功Akv(u)--具有一定尺寸和形状的金属试样,在冲击负荷作用下折断时所吸收的功。
单位为焦耳(J)。
冲击韧性值akv(u)--冲击吸收功除以试样缺口处底部横截面积所得的商。
单位为焦耳/厘米2(J/cm2)。
常温冲击试验温度为20±2℃;低温冲击试验温度围为<10~-192℃;高温冲击试验温度围为35~1000℃。
冲击试样一般均采用标准试样,即55×10×10mm,当试验材料的厚度在10mm以下而无法制备标准试样时,可采用宽度为7.5mm或5mm的小尺寸试样。
低温冲击试验所用冷却介质一般为无毒、安全、不腐蚀金属和在试验温度下不凝固的液体或气体。
如无水乙醇(酒精)、固态二氧化碳(干冰)或液氮雾化气(液氮)等。
国家标准规定冲击弯曲试验用标准试样分别为夏比(Charpy)U型缺口试样和夏比V型缺口试样,两种试样的形状及尺寸如图所示所测得的冲击吸收功分别记为AkU和AkV。
另外。
测量瓷、铸铁或工具钢等脆性材料的冲击吸收功时,常采用10mm××10mm×55mm的无缺口冲击试样。
冲击试样缺口的作用:
在缺口附近造成应力集中,使塑性变形局限在缺口附近不大的体积围,并保证在缺口处发生断裂,以便正确测定材料承受冲击负荷的能力。
试样应在规定的温度下保持足够的时间,,使用液体介质时,保温时间不少于5分钟,使用气体介质时,保温时间不少于20分钟。
冲击吸收功的表示方法:
V型缺口试样的冲击吸收功,表示为Akv
深度为2mm的U型缺口试样的冲击吸收功,表示为Aku2
冲击试验中几种情况的处理:
1、由于试验机打击能量不足使试样未完全折断时,应在试验数据之前加大于“>”符号,其他情况则应注明“未折断”。
2、试验后试样断口有肉眼可见的裂纹或缺陷时,应在试验报告中注明,
3、试验中如出现误操作,或试样打断时有卡锤现象,,此时得到的结果已不准确,因此试验结果无效,应重新补做试验。
冲击韧性及其工程意义
αkV(αku)是一个综合性的力学性能指标,与材料的强度和塑性有关,单位为J/cm2。
长期以来,人们一直将αkV(αku)视为材料抵抗冲击载荷作用的力学性能指标,用来评定材料的韧脆程度,作为保证机件安全设计的指标。
但αkV(αku)表示单位面积的平均冲击功值,是一个数学平均量。
实际上冲击试样承受弯曲载荷,缺口截面上的应力应变分布是极不均匀的,塑性变形和试样所吸收的功主要集中在缺口附近,故取平均值是毫无物理意
义的,所以这指标目前已不大使用。
目前常用的韧性指标是冲击功Akv,由于它对材料成分、部组织变化十分敏感,而且一次冲击弯曲试验方法简便易行,所以被广泛采用。
一次冲击弯曲试验主要有以下几方面用途:
(1)它能反映出原始材料的冶金质量和热加工产品的质量。
通过测量AKv值和对冲断试样的断口分析,可揭示原材料中的气孔、夹杂、偏析、严重分层和夹杂物超标等冶金缺陷;还可检查过热、过烧、回火脆性等锻造或热处理缺陷。
(2)测定材料的韧脆性转变温度。
根据系列冲击试验(低温冲击试验)可获得Akv与温度的关系曲线,据此确定材料的韧脆转变温度,以供选材参考或抗脆断设计。
(3)对屈服强度大致相同的材料,根据Akv值可以评定材料对大能量冲击破坏的缺口敏感性。
系列冲击实验
系列冲击实验在材料研究与生产实际中应用较广,因为它比其他实验方法更能灵敏地反映出材料力学性能随因和外因变化的差异。
对某些材料,当冲击实验分别在低温、室温和高温下进行时可以得到一系列冲击值Akv,将这些冲击值与所对应的实验温度在直角坐标系中标出,然后用光滑曲线将这些实验数据连接起来,可以得到这种材料冲击韧性与温度的关系曲线,即Akv-t这种不同温度下的冲击试验称为系列冲击试验。
据此可以评定材料的低温脆性、兰脆和重结晶脆性等,而这些脆性是材料使用中力图避免出现的,因此系列冲击试验有一定的实用意义。
系列冲击实验证明,在工程上广泛使用的中、低强度结构钢,在常温下有很好的冲击韧性,当试验温度低于某一温度时,材料由韧性状态变为脆性状态,冲击吸收功明显下降,断裂机理由微孔聚集型变为穿晶解理型,断口特征由纤维状变为结晶状,这就是低温脆性。
转变温度tk称为韧脆转变温度或冷脆转变温度。
弯曲试验
金属弯曲试验是将一定形状和尺寸的试样放置与弯曲装置上,按规定尺寸的弯芯,将试样弯曲至规定的角度后,卸除试验力,检查试样承受变形的能力。
弯曲试验的特点及应用
(1)弯曲加载时受拉的一侧应力状态基本上与静拉伸时相同,且不存在如拉伸时的所谓试样偏斜对试验结果的影响。
因此弯曲试验常用于测定那些由于太硬难于加工成拉伸试样的脆性材料的断裂强度,并能显示出它们的塑性差别。
(2)弯曲试验时,截面上的应力分布也是表面上应力最大,故可灵敏地反映材料的表面缺陷。
因此,常用来比较和评定材料表面处理层的质量。
(3)塑性材料的F-fmax曲线的最后部分可任意延长,表明弯曲试验不能使这些材料断裂。
在这种情况下虽可测定规定非比例和弯曲应力,但实际上很少应用。
对这些材料应采用拉伸试验。
弯曲试样的制备:
试样加工时,应去除由于剪切或火焰切割等形成的热影响区,试样表面不得有划痕和损伤,方形、矩形和多边形横截面试样的棱边应倒圆,倒圆半径不超过试样厚度的1/10,棱边倒圆时不应形成影响试验结果的横向毛刺、伤痕或划痕。
试验弯曲装置:
支辊式弯曲装置、V形模具式弯曲装置、虎钳式弯曲装置、翻板式弯曲装置
钢板或焊缝金属导向弯曲通常是将试样弯曲到180°时,进行结果评定。
试验结果的评定:
弯曲试验结果应按照相关产品标准或技术协议的要求进行评定,如产品标准或技术协议无具体规定时,一般在试验后检查试样弯曲部分外表面,如无肉眼可见裂纹则评定为合格。
落锤撕裂试验
试验装置:
常用落锤试验机主要由道轨、底座、砧座、锤
头及提升机构等部分组成。
落锤试验原理:
将锤头提升到一定高度,把试样放在砧座上,然后迅速释放锤头,使锤头自由落下,将试样快速冲断,检测试样断口剪切面积的百分数。
对落锤试验机的要求:
道轨应与底座垂直,两道轨应平行,以保证锤头能自由下落。
底座应有足够的刚性,有可靠的安全装置。
砧座的支承台应有足够的硬度,锤头应具有在一次冲击下将试样完全冲断的足够的能量。
提升机构应能把锤头提升到不同高度,并能安全迅速地释放锤头。
试验标准:
现在使用的落锤试验国家标准为:
GB/T8363-87;美国标准为:
APIRP5L3-96。
落锤试样缺口形式:
试样通常分为V型缺口和人字型缺口
对韧性较低的管线钢,优先选用压制V型缺口;对韧性较高的管线钢,优先选用人字型缺口,易于冲断。
人字型缺口应采用机加工方法垂直试样边缘加工。
试验:
在低温试验时,试样应完全浸泡在装有适宜液体的浴槽中,浴槽中液体的温度与所要求的试验温度的偏差不应超过1℃,试样的浸泡时间应符合标准的要求。
试样之间以及试样与浴槽边缘、浴槽底部应相互隔开,且至少应有25mm或一个试样厚度的间距,取数据较大者。
应采取措施使浴槽的液体流动以保证浴槽的温度均匀。
试样的评定:
有效试样:
是指整个断裂面呈现延性断裂的试样,或缺口根部呈现解理断裂的试样。
若试样缺口下的断裂为延性断裂接着转化为解理断裂,则试样无效。
试样断口评定时,应通过测定断口表面的剪切面积百分数进行评定。
在美标中,对厚度不大于19mm的试样,评定时,不包括从缺口跟部起一个试样厚度的断裂面以及另一侧一个试样厚度的断裂面。
对厚度大于19mm的试样,略去不计的长度应为19mm。
剪切面积百分数的评定通过区分延性断裂与解理断裂来评定,延性断裂是暗灰色、纤维状的;而解理断裂是有金属光泽、结晶状的,要评定的断口形貌为垂直于断裂试样表面观察到的观察面。
在规定的试验温度下,应对材料做至少2个试样的落锤试验。
硬度试验法
硬度指标
金属材料抵抗硬的物体压入其表面的能力,称为硬度。
根据试验方法和适用围不同,硬度又可分为布氏硬度、洛氏硬度、维氏硬度、肖氏硬度、显微硬度和高温硬度等。
对于管材一般常用的有布氏、洛氏、维氏硬度三种。
1、布氏硬度(HB)
用一定直径的钢球或硬质合金球,以规定的试验力(F)压入式样表面,经规定保持时间后卸除试验力,测量试样表面的压痕直径(d)。
布氏硬度值是以试验力除以压痕球形表面积所得的商。
以HB表示,单位为N/mm2(MPa)。
布氏硬度指标有HBS和HBW,前者所用压头为淬火钢球,故对于较硬的钢不适用,它适用于布氏硬度值低于450的金属材料,如退火钢、正火钢、调质钢及铸铁、有色金属等,因压痕较大,故不宜测试成品件或薄片金属的硬度;后者压头为硬质合金球,适用于布氏硬度值为450~650的金属材料,如淬火钢等。
测定布氏硬度较准确可靠,布氏硬度用途较广,往往以压痕直径d来表示该材料的硬度,既直观,又方便。
举例:
120HBS10/1000/30:
表示用直径10mm钢球在1000Kgf(9.807KN)试验力作用下,保持30s(秒)测得的布氏硬度值为120N/mm2(MPa)。
2、洛氏硬度(HR)
洛氏硬度试验法是用一锥顶角为120°的金刚石圆锥体或直径为1.558mm(1/16英寸)的淬火钢球为压头,以一不定的载荷压入被测试金属材料表面,根据压痕深度可直接在洛氏硬度计的指示盘上读出硬度值。
常用的洛氏硬度指标有HRA、HRB和HRC三种。
洛氏硬度试验同布氏硬度试验一样,都是压痕试验方法。
不同的是,它是测量压痕的深度。
即在初始试验力(Fo)及总试验力(F)的先后作用下,将压头(金钢石圆锥体或钢球)压入试样表面,经规定保持时间后,卸除主试验力,用测量的残余压痕深度增量(e)计算硬度值。
其值是个无名数,以符号HR表示,所用标尺有A、B、C、D、E、F、G、H、K等9个标尺。
其中常用于钢材硬度试验的标尺一般为A、B、C,即HRA、HRB、HRC。
硬度值用下式计算:
当用A和C标尺试验时,HR=100-e
当用B标尺试验时,HR=130-e
式中e--残余压痕深度增量,以规定单位0.002mm表示,即当压头轴向位移一个单位(0.002mm)时,即相当于洛氏硬度变化一个数。
e值愈大,金属的硬度愈低,反之则硬度愈高。
上述三个标尺适用围如下:
采用120金刚石圆锥体为压头,施加压为600N时,用HRA表示。
其测量围为20~85,适于测量合金、表面硬化钢及较薄零件。
采用1.588mm淬火钢球为压头,施加压力为1000N时,用HRB表示,其测量硬度值围为25~100,适于测量有色金属、退火和正火钢及锻铁等。
采用120金刚石圆锥体为压头,施加压力为1500N时,用HRC表示,其测量硬度值围为20~67,适于测量淬火钢、调质钢等。
洛氏硬度测试,操作迅速、简便,且压痕小不损伤工件表面,故适于成品检验。
硬度是材料的重要力学性能指标。
一般材料的硬度越高,其耐磨性越好。
材料的强度越高,塑性变形抗力越大,硬度值也越高。
洛氏硬度试验是目前应用很广的方法,其中HRC在钢管标准中使用仅次于布氏硬度HB。
洛氏硬度可适用于测定由极软到极硬的金属材料,它弥补了布氏法的不足,较布氏法简便,可直接从硬度机的表盘读出硬度值。
但是,由于其压痕小,故硬度值不如布氏法准确。
3、维氏硬度(HV)
维氏硬度试验也是一种压痕试验方法,是将一个相对面夹角为136°的正四棱锥体金刚石压头以选定的试验力(F)压入试验表面,经规定保持时间后卸除试验力,测量压痕两对角线长度。
维氏硬度值是试验力除以压痕表面积所得之商,其计算公式为:
HV=0.1891F/d2
式中:
HV--维氏硬度符号,N/mm2(MPa);
F--试验力,N;
d--压痕两对角线的算术平均值,mm。
维氏硬度采用的试验力F为5(49.03)、10(98.07)、20(196.1)、30(294.2)、50(490.3)、100(980.7)Kgf(N)等六级,可测硬度值围为5~1000HV。
表示方法举例:
640HV30/20表示用30kgf(294.2N)试验力保持20S(秒)测定的维氏硬度值为640N/mm2(MPa)。
维氏硬度法可用于测定很薄的金属材料和表面层硬度。
它具有布氏、洛氏法的主要优点,而克服了它们的基本缺点,但不如洛氏法简便。
维氏法在钢管标准中较常用。
实践证明,金属材料的各种硬度值之间,硬度值与强度值之间具有近似的相应关系。
因为硬度值是由起始塑性变形抗力和继续塑性变形抗力决定的,材料的强度越高,塑性变形抗力越高,硬度值也就越高。
但各种材料的换算关系并不一致。
钢中非金属夹杂物的检验
金相试样的选取:
1、纵向试样:
是指沿着钢材的锻轧方向取样,主要检验非金属夹杂物的变形程度、带状组织、变形后的各种组织形貌、热处理情况等。
2、横向试样:
是指垂直于钢材的锻轧方向取样,主要检验金属材料从表层到中心的显微组织、晶粒度级别、碳化物网、氧化层深度、脱碳层深度等。
夹杂物试样应选取纵向试样,试样可用手锯、砂轮机切割、火焰切割等,但加工时必须去除变形区或热影响区。
试样的磨制:
1、粗磨:
一般在落地砂轮机上进行,磨料粒度的粗细,对试样表面粗糙度和磨削效率有一定影响,粗磨时,还应注意沾蘸水冷却,防止组织变化。
2、细磨:
试样经粗磨后虽已平整,但还存在较深的磨痕及表面加工变形层,需要从粗到细的不同金相纱纸的磨制。
细磨可以用手工磨光、机械磨光和化学磨光三种方法,手工磨光是用不同粗细粒度的金相砂纸由粗到细逐次磨平。
金相砂纸的粗细粒度与编号方法有关,编号若用数字表示的,如280、320、400、600、800等等,则编号越大,则砂粒标准粒度直径越小。
磨光时,将砂纸铺在金属或玻璃板上,左手压住砂纸,右手将试样的磨面放在砂纸上,磨光时用力要均匀,沿着一个方向磨光,不要往返磨制,以免试样表面呈圆弧形,当试样表面的磨痕完全与磨制方向一致时,再更换细粒度的砂纸,每次更换砂纸时,应将试样和手清理干净,玻璃板也要擦净,以免粗号砂纸上的砂粒掉在细号砂纸上,为了容易观察磨痕消除情况,磨试样的方向总是和前一号砂纸上所留下来的磨痕的方向垂直,直到磨痕磨掉为止。
3、抛光:
常用抛光的方法有二种:
(1)机械抛光;
(2)电解抛光。
对于机械抛光,试样磨光后,要仔细地用水将它洗净,以除去砂粒,然后将试样的磨面放在覆盖有呢绒、帆布、绸布等的转动盘上抛光,进行抛光时,要洒上适量的抛光粉的悬浮水溶液,使之均匀地分布在抛光绒布上,然后打开电门,启动转动盘,用手拿稳试样,使试样的磨面与抛