现代数控技术集机械制造技术.docx
《现代数控技术集机械制造技术.docx》由会员分享,可在线阅读,更多相关《现代数控技术集机械制造技术.docx(41页珍藏版)》请在冰豆网上搜索。
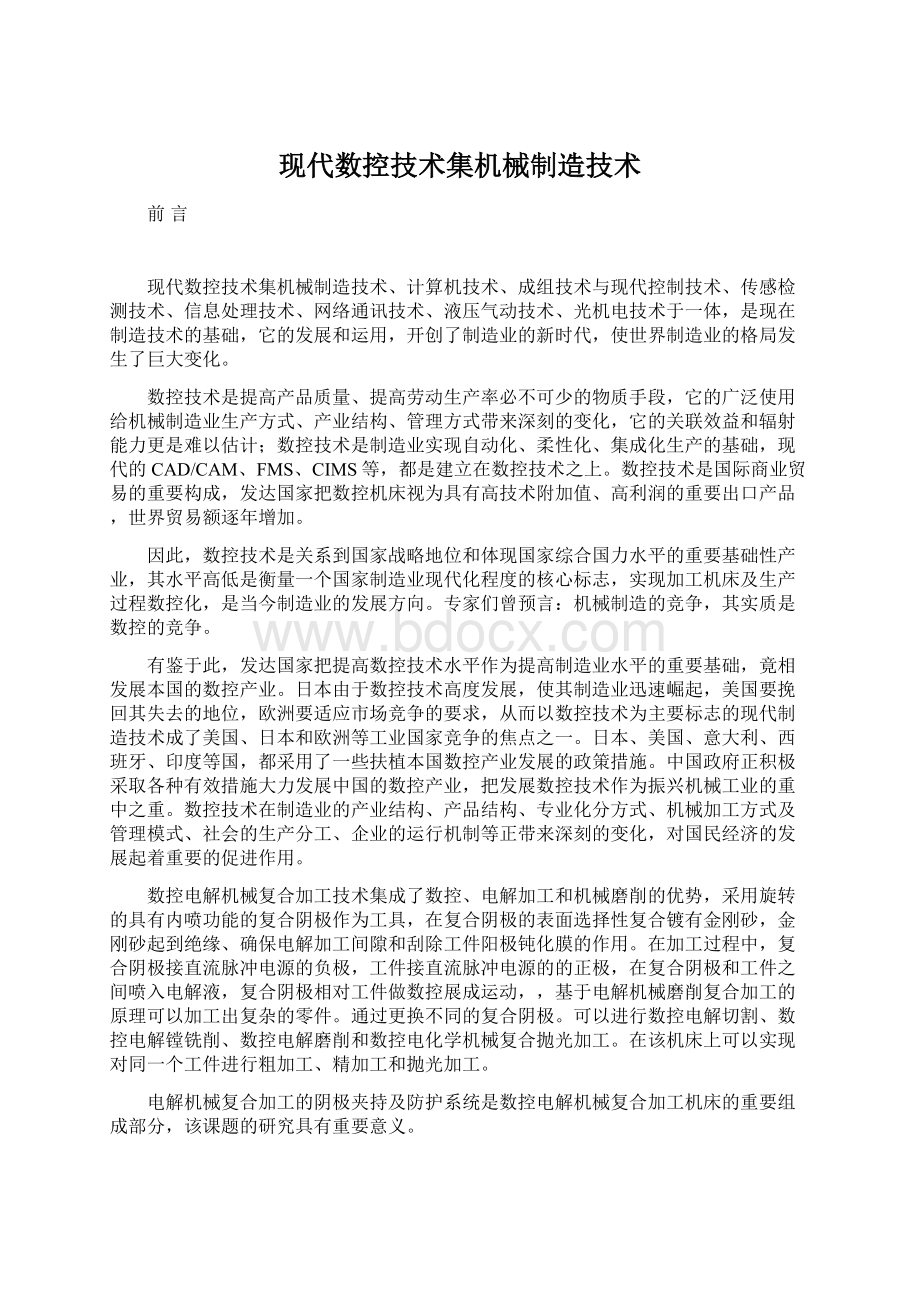
现代数控技术集机械制造技术
前言
现代数控技术集机械制造技术、计算机技术、成组技术与现代控制技术、传感检测技术、信息处理技术、网络通讯技术、液压气动技术、光机电技术于一体,是现在制造技术的基础,它的发展和运用,开创了制造业的新时代,使世界制造业的格局发生了巨大变化。
数控技术是提高产品质量、提高劳动生产率必不可少的物质手段,它的广泛使用给机械制造业生产方式、产业结构、管理方式带来深刻的变化,它的关联效益和辐射能力更是难以估计;数控技术是制造业实现自动化、柔性化、集成化生产的基础,现代的CAD/CAM、FMS、CIMS等,都是建立在数控技术之上。
数控技术是国际商业贸易的重要构成,发达国家把数控机床视为具有高技术附加值、高利润的重要出口产品,世界贸易额逐年增加。
因此,数控技术是关系到国家战略地位和体现国家综合国力水平的重要基础性产业,其水平高低是衡量一个国家制造业现代化程度的核心标志,实现加工机床及生产过程数控化,是当今制造业的发展方向。
专家们曾预言:
机械制造的竞争,其实质是数控的竞争。
有鉴于此,发达国家把提高数控技术水平作为提高制造业水平的重要基础,竟相发展本国的数控产业。
日本由于数控技术高度发展,使其制造业迅速崛起,美国要挽回其失去的地位,欧洲要适应市场竞争的要求,从而以数控技术为主要标志的现代制造技术成了美国、日本和欧洲等工业国家竞争的焦点之一。
日本、美国、意大利、西班牙、印度等国,都采用了一些扶植本国数控产业发展的政策措施。
中国政府正积极采取各种有效措施大力发展中国的数控产业,把发展数控技术作为振兴机械工业的重中之重。
数控技术在制造业的产业结构、产品结构、专业化分方式、机械加工方式及管理模式、社会的生产分工、企业的运行机制等正带来深刻的变化,对国民经济的发展起着重要的促进作用。
数控电解机械复合加工技术集成了数控、电解加工和机械磨削的优势,采用旋转的具有内喷功能的复合阴极作为工具,在复合阴极的表面选择性复合镀有金刚砂,金刚砂起到绝缘、确保电解加工间隙和刮除工件阳极钝化膜的作用。
在加工过程中,复合阴极接直流脉冲电源的负极,工件接直流脉冲电源的的正极,在复合阴极和工件之间喷入电解液,复合阴极相对工件做数控展成运动,,基于电解机械磨削复合加工的原理可以加工出复杂的零件。
通过更换不同的复合阴极。
可以进行数控电解切割、数控电解镗铣削、数控电解磨削和数控电化学机械复合抛光加工。
在该机床上可以实现对同一个工件进行粗加工、精加工和抛光加工。
电解机械复合加工的阴极夹持及防护系统是数控电解机械复合加工机床的重要组成部分,该课题的研究具有重要意义。
在读完大学四年的公共基础课、专业基础课、专业课后,具备了一定的专业理论知识,通过这次综合性的毕业设计,不仅重温了学过的知识,更加锻炼了自我的综合性学习能力、创造性能力、独自设计能力,使自己在数控技术、机床系统设计、数控编程等诸多方面有了更多的理解与提高。
数控技术发展日新月异,由于本人设计水平有限,在整个设计中难免有所错误,恳请老师、同学批评指正提出宝贵意见,以便我在下一次的设计中不断改善。
1、数控电解机械复合加工阴极夹持及防护系统的设计
1.1数控电解机械复合加工机床的设计
1.1.1数控电解机械复合加工机床的特点:
(1)以简单形状的复合阴极就可加工零件的复杂型面。
(2)主要靠电化学阳极溶解的原理去除工件余量,宏观机械切削力小,表面金相组织不发生变化,可加工窄缝、窄槽、薄壁和低刚度零件。
(3)可加工各种高硬度、高韧性和高耐磨性金属难加工材料。
(4)比机械磨削有更高的加工效率,比电解加工有更高的加工精度。
1.1.2数控电解机械复合加工阴极夹持的设计
本实用新型涉及数控电解机床的附件,具体来说就是装夹阴极的刀柄。
其背景技术:
电解加工时利用金属在电解液中产生阳极溶解的原理来去除工件材料的制造技术,能加工高强度、高硬度、高韧性的导电材料,是应用较广泛的加工方法之一。
电解穿孔可以对形状复杂、尺寸较小的型孔进行加工,电解成型可以对工件型腔一次成型,上述电解加工中的阴极由夹具夹持,采取进给方式加工型孔。
电解磨削是一种特殊形式的电解加工,磨削时工件接直流电的正极,电解磨轮接直流电的负极。
电解磨轮直接安装在绝缘主轴上,由主轴带动旋转。
电解液喷嘴独立于电解磨轮外,需由另一套装置支撑。
上述电解磨轮只能加工平面、圆柱表面和直纹展成面,不能加工具有凹凸面的型面。
1.1.3阴极刀柄的特点
(1)新型刀柄本体旋转,由此带动阴极旋转,旋转的阴极配合进给运动能作为加工型腔和型面的工具。
(2)新型刀柄上部设有拉丁和比例为7:
24的锥体,可以方便的配备在钻孔、磨削、铣削和切割等数控电解加工机床中使用。
(3)新型刀柄外部设有能做相对转动的导电体。
导电体起导电和电解液喷嘴作用,实现了电解液内喷。
简化了结构。
(4)新型刀柄上部分和下部分之间设有绝缘体。
可以实现加工部分和机床绝缘,可以通过调整电源的正负可实现阴阳极的调换,能满足特殊加工的要求。
(5)新型刀柄的内壁设有滑动轴承,轴承的上下端均设有耐磨密封圈,两者配套使用能实现高载荷和高转速,能满足电解液内喷对主轴转速的要求。
(6)新型刀柄设置弹簧夹套夹紧阴极,由夹紧螺母固定弹簧夹套,所以可以通过更换通用件弹簧夹套能牢固夹紧不同直径的阴极。
(7)新型刀柄在导电体和夹具体之间设有水银带,外设有密封圈防止泄漏,既不影响导电体与夹具体之间的相对转动,又能保证导电体与夹具体之间良好的电传导性能。
2.1新型刀柄的主要构造
刀柄的本体是采用的标准7/24锥联结,7/24锥联结有很多优点
1、因不能自锁,可实现快速装卸刀具;
2、刀柄的锥体在拉杆轴向拉力的作用下,紧紧的与主轴的内锥面接触,实心的锥体直接在主轴内锥孔内支承刀具,可以减少刀具的悬伸量;
3、这种联结只有一个尺寸即锥角需加工到很高的精度,所以成本很低而且可靠。
1、切割头摆动范围:
0—180°;
2、切割头摆动定位精度:
10秒;
3、主轴转速:
10000转/分;
4、导电装置工作转速达10000转/分。
2.1.5电动机的选择
根据设计要求主轴,选择的电动机为VFG系列铝合金变频电机,额定功率为7.5KW,当基本频率为50HZ时,转速为1500r/min,变频范围为2~150HZ,转速范围为60~4500r/min,带传动主要用于转速较高的机床,具有结构简单、传动平稳,价格低廉、缓冲吸振及过载打滑以保护其他零件等优点。
所以选择通过带传动的主传动这种系统配置方式。
但经过对带传动的设计计算,由于主轴最高转速为10000r/min,变速范围太大,无法满足带轮最小基准直径的要求,所以用齿轮传动,通过齿轮将电动机的运动传给主轴,因为电动机的转速范围大,采用一级齿轮传动。
由于齿轮传动会引起振动与噪声,所以既采用带传动又采用一级齿轮传动。
2.2数控机床切割头摆动轴的设计
2.2.1电动机的选择
根据切割头摆动范围(0—180°)的设计要求,选择永磁式交流伺服电动机,型号为130SM15025,额定功率为3.9KW,静态转矩为15Nm,额定转速为2500r/min,额定电流为22.5A。
2.2.2联轴器的选择
根据此次设计要求选择无弹性元件的挠性联轴器中的滑块联轴器
特点:
结构简单,转动惯量小,具有一定补偿两轴相对偏移、减振和缓冲性能。
型号:
KL6联轴器
JB/ZQ4384-8
2.3数控机床X轴传动系统设计
2.3.1电动机的选择
在选择电动机型号时,首先应考虑电动机与滚珠丝杠的联接方式,才能决定电机型号。
在设计方案中可以看出是直接采用了联轴器传动方式。
数控切割机床进给传动对位置精度、快速响应性能、调速范围等有较高的要求。
实现进给传动的电动机只有三种:
步进电动机、直流伺服电动机和交流伺服电动机。
目前,步进电动机一般用于开环进给系统,可以用于一些普通数控机床;直流伺服电动机多用于对伺服电动机的调速性能要求高的场合,并且存在一些固有缺点,如电刷和换向器易磨损,机构复杂,制造成本高等;交流伺服电动机用于要求较高的场合,根据毕业设计课题要求设计的切割机床的X、Y、Z轴脉冲当量为0.001mm/脉冲,考虑经济性能选择步进电机。
电动机与滚珠丝杠的联接方式主要有三种:
齿轮传动方式、同步带轮传动形式和联轴器传动形式。
由于齿轮在制造过程中不可能达到理想齿面要求,总存在一定的误差,一对齿轮必须有一定的齿侧间隙才能正常工作。
但对于闭环系统来说,齿侧间隙会影响系统的稳定性。
而同步带轮传动形式只能适用于低扭矩特性要求的场合,安装时中心距要求严格,带与带轮制造工艺复杂。
上述两种传动形式都不适合本次所设计的数控切割机床。
因此,在本次设计中选用了联轴器传动联接方式,在电动机轴和滚珠丝杠之间采用联轴器联接,从而使进给传动系统具有较高的传动精度与传动刚度,并且还大大简化了机械结构。
所选择的步进电机,应满足下列条件,并进行负载扭矩计算:
(1)在所有的进给速度范围内(包括快速移动),空载进给力矩应小于电动机额定转矩;
(2)大切削力矩小于电动机额定转矩;
(3)加、减速时间应符合所希望的时间常数;
(4)快速进给频繁度在希望值以内。
负载扭矩计算
负载扭矩是由于驱动系统的摩擦力和切削力所引起,可用下式表示:
2πM=FL(2-1)
式中M—电动机轴转矩;
F—使机械部件沿直线方向移动所需力;
L—电动机转一圈(2πrad)时,机械移动距离。
2πM是电动机以扭矩M转一圈时电动机所做的功,而FL是以力F机械移动L距离时所做的功。
在实际机床上,由于存在传动效率和摩擦系数因素,滚珠丝杠克服外部载荷P做等速运动所需的力矩,应按下式计算:
M1=(KFa0hsp/2π+Phsp/2πη1+MB)z1/z2(2-2)
式中M1—等速运动时的驱动力矩(Nmm);
KFa0hsp/2π—双螺母滚珠丝杠的预紧力矩(Nmm);
Fa0—预紧力(N),通常预紧力取最大轴向工作载荷Fm的1/3,即Fa0=1/3Fmax,当Fmax难于计算时,可采用Fa0=(0.1~0.2)Ca(N);
Ca—滚珠丝杠副的额定载荷,在样品本中可以查到;
hsp—丝杠导程(mm);
K—滚珠丝杠预紧力矩系数,取0.1~0.2;
P—加在丝杠周上的外部载荷(N),P=F+μW;
F—作用于丝杠轴向的切削力(N);
W—法向载荷(N),W=W1+P1;
W1—移动部件重力(N),包括最大承载重力;
P1—有夹板夹持时的夹板夹持力;
μ—导轨摩擦稀疏,粘贴聚四氟乙烯板的滑动导轨副μ=0.09,有润滑条件时,μ=0.03-0.05,直线滚动导轨μ=0.003-0.004;
η1—滚珠丝杠的效率,取0.90-0.95;
ΜB—支承轴承的摩擦力矩,亦叫启动力矩(Nm),可以从滚珠丝杠专用轴承样本中查到,见表2-6(这里要注意,双支承轴承有ΜB之和的问题;
Z1—齿轮1的齿数;
Z2—齿轮2的齿数.
最后按满足下式的条件选步进电动机:
M1≤MS
式中MS—步进电动机的额定转矩。
M1=(0.25+0.005*2500/2π*0.92+0.34)=2.42Nm
所以取MS〉2.42Nm
最后选择了常州新月电机有限公司制造的五相混合式步进电机(Y系列)的110BY5603型步进电机。
其主要参数为:
步距角α=0.3°
M=12Nm
N=2000rpm
2.3.2联轴器的选择
根据此次设计要求选择无弹性元件的挠性联轴器中的滑块联轴器
特点:
结构简单,转动惯量小,具有补偿两轴相对偏移、减振和缓冲性能。
型号:
KL4联轴器
JB/ZQ4384-8
2.3.3滚珠丝杠螺母副的设计
2.3.3.1滚珠丝杠的计算与选择
滚珠丝杠螺母传动装置:
滚珠丝杠螺母传动装置主要分为两种:
外循环插管式,内循环插管式。
外循环插管式可以保证滚珠成切线进入,实现无冲击的均速运动,允许丝杠高速运转且精度高。
内循环反向器式丝杠螺母尺寸较小且易于制造,经济性好,因此,外循环插管式和内循环反向器式都获得了广泛的应用。
滚珠丝杠和滑动丝杠相比具有摩擦小、传动灵敏,不易产生爬行;定位精度高;摩损小、寿命长、精度保持好等优点。
缺点是:
不能自锁,用于升降传动时需另加自锁机构;结构复杂,成本高。
由于丝杠主要承受轴向力,大多采用推力轴承做支承。
在相同尺寸条件,推力球轴承轴向刚度比向心推力球轴承及圆锥滚子轴承的轴向刚度要大一倍以上;推力滚柱轴承刚度又比推力球轴承大一倍左右。
当轴向载荷较小时,可不用推力球轴承而用向心推力球轴承,这样可减少轴承数量。
本次设计中,选择了内循环滚珠丝杠传动装置,采用了“双推—支承”式。
这种方式可避免丝杠因自重引起弯曲,以及高速回转式自由端的晃动。
在机床进给伺服系统设计时,存在着对滚珠丝杠传动进行优化设计和选型的问题。
根据ISO推荐以及各国近年来公认的计算公式,来阐述滚珠丝杠传动装置的设计计算。
1、先详细阐述X轴滚珠丝杠的设计计算过程:
设计计算分析与过程
设计计算结果
(1)、丝杠导程hsp
hsp≤υTmax/nspmax(mm)(2-3)
式中υTmax—工作台最大速度(mm/min);
nspmax—丝杠最大转速(r/min).
hsp≤υTmax/nspmax
hsp≤10*103/2000
hsp≤5mm
丝杠导程hsp和减速机构速比I以及电机最大转速nMmax一起,决定了工作台的最大快进速度,它们之间的关系是:
υTmax=nMmaxhspI(mm/min)(2-4)
丝杠的导程通常是标准值,从经济上考虑,应根据厂家提供的产品样本选取。
(2)、滚珠丝杠螺母副寿命Lh
(2-5)
式中Lh—寿命时间(h),见表2-1;
nm—当量转速(r/min);
Ca—动载荷(N);
fw—载荷系数(见表2-2);
Fm—当量载荷(N)。
hsp≤5mm
取hsp=5mm
Lh
1410
取Lh=1500h
符合要求
设计计算分析与过程
设计计算结果
表2-1滚珠丝杠副预期工作寿命
主机类别
Lh/h
一般机床、组合机床
数控机床、精密机床
工程机械
自动控制系统
测量系统
1000
1500
5000~10000
15000
15000
表2-2载荷系数
`
fw
平稳,无冲击运动
一般运动
伴随着冲击和振动的运动
1.0~1.2
1.2~1.5
1.5~2.0
(3)、额定动载荷校核
额定动载荷系指一批规格相同的滚珠丝杠副,在相同条件下运转100万转,其中90%不产生疲劳损伤时所能承受的最大轴向载荷。
在知道受力情况和确定丝杠寿命以后,可计算出丝杠的动载荷Ca/,可得到:
Ca/=(60nmLh)1/3Fmfw*10-2(N)(2-6)
Ca/=(60*1100*1500)1/3*1.2*2594*10-2
=14105(N)
在丝杠产品样本中,可查得丝杠的额定载荷Ca,应保证
Ca≥Ca/
14122≥14105
Ca/=14105N
14122≥14105
符合要求
设计计算分析与过程
设计计算结果
(4)、额定静载荷校核
额定静载荷系指滚珠丝杠副在静止或低速(v<=10r/min)下,滚珠与滚道型面在接触点上产生塑性变形之和为滚珠直径万分之一的轴向载荷。
丝杠的静载荷刻有下式计算:
C0a/=fdFmax(N)(2-7)
式中Fmax—最大轴向力(N);
fd—静态安全系数,见表2-3。
C0a/=fdFmax=1.5*3820
C0a/=5730(N)
表2-3静态安全系数
使用条件
fd的下限值
一般运动
伴随有冲击与振动的运动
1~2
2~3
在丝杠产品样本中可查得丝杠的额定静载荷C0a,应保证
C0a≥C0a/
50113≥5730
(5)、临界转速nc
nc=fdsp*107/L2(r/min)(2-8)
式中dsp—丝杠底径(mm);
L—丝杠支承间距(mm);
f—与支承方法有关的临界转速系数,见表2-4
nc=fdsp*107/L2
nc=15.1*49*107/9172
nc=8799(r/min)
(6)、最大转速nmax
丝杠最大转速nmax按下式计算:
d0nmax≤A(2-9)
式中d0—丝杠名义直径(mm);
nmax—丝杠最大转速
通常取A=50000~70000。
50nmax≤60000
nmax≤1200(r/min)
设计计算分析与过程
C0a/=4730N
50113≥5730
符合要求
nc=8799r/min
nmax≤1200r/min
设计计算结果
在机床工作台加速与切削加工过程中,在进给轴向方向会产生力,必须保证这个力小于允许的压弯临界载荷Fa,否则可能导致进给丝杠弯曲。
压弯临界载荷Fa可用下式计算:
(2-10)
式中dsp—丝杠底径(mm);
L—丝杠支承间距(mm);
m—与丝杠支承方法有关的临界载荷系数,见表2-4
表2-4系数f和m
支承方法
f
m
双推—双推
双推—支承
单推—单推
双推—自由
21.9
15.1
9.7
3.4
20.3
10.2
5.1
1.3
(7)、轴向拉压刚度Ks
确定进给丝杠尺寸的最重要设计准则,是考虑它的抗张和抗压刚度。
其计算公式如下:
(2-11)
式中dsp—丝杠底径(mm);
E—弹性模量(钢为2*1011Pa);
L—丝杠的总自由长度(mm)。
对于直径小的丝杠,由轴向力引起的丝杠扭转变形转化为工作台的轴向位移,可能影响丝杠的抗扭刚度。
进给丝杠的抗扭刚度是
(2-12)
式中G—切变模量(钢为8*1010Pa);
dsp—丝杠底径(mm);
L—丝杠的总自由长度(mm)。
(8)、传动效率
滚珠丝杠的传动效率一般都在0.8~0.9之间。
本设计中所选择的滚珠丝杠的传动效率要求η不低于0.85。
Fa=6992719N
Ks=330374Nm
KTsp=39661Nm
η≥0.85
(9)、预紧力
订购滚珠丝杠副时,需根据丝杠受力情况通知厂家所需预紧力的大小,以便厂家按给定的预紧力预紧。
实践证明:
预紧力Fpr选的合理,可以使滚珠丝杠副工作在最佳状态,它的优点才能充分发挥。
预紧力增加,钢珠和滚道之间的接触刚度也增加,传动精度也会提高。
但是,过大的预紧力将导致钢珠和滚道之间接触应力增大,从而降低工作寿命和传动效率。
滚珠丝杠预紧力的大小应使得滚珠丝杠副在承受最大轴向工作载荷时,丝杠螺母副不出现轴向间隙为最好(参照表2-5)。
表2-5不同工作条件下的预紧力
工作条件
Fpr
应用举例
工作
速度
方向
间隙
定位
精度
接触
刚度
中速
无
高
高
Fpr=(0.1~0.13)Ca
加工中心
精密NC机床
中速
无
较高
较高
Fpr=1/3Fmax
经济型NC机床
NC机床,普通机床
高速
无
一般
底
Fpr<<1/3Fmax
工业机器人
工程机械
而本次设计的是精密型数控机床,所以选择Fpr=(0.1-0.13)Fmax。
(10)、滚珠丝杠副精度
根据JB3162.2-82标准,我国滚珠丝杠付根据使用范围和要求分为六个精度等级,即C、D、E、F、G、H级。
C级精度最高,依次逐级降低,而JB3162.2-91分为1、2、3、4、5、7、10共七个等级,1级最高,依次递减。
据使用范围,又可分为定位P类和传动T类。
选择滚珠丝杠副精度的原则是:
(1)要满足主机定位精度的要求滚珠丝杠副的综合行程误差大约为主机定位误差的30%~40%。
(2)要合理选择滚珠丝杠副的精度盲目提高精度等级是不经济的,相同尺寸规格的精度滚珠丝杠副,每提高一个精度等级,成本增加30%以上。
而且由于制造周期相应加长,延长了交货期。
(3)对于精密机床,在选择相应等级时,还要考虑包括滚珠丝杠副在内的整个进给伺服系统的热变形对滚珠丝杠副导程精度的影响。
通常对滚珠丝杠副施加适当的预拉力,使其拉伸量接近丝杠的热变形量。
这样在工作过程中,轴向热变形量正好与丝杠弹性恢复量抵消,从而达到预期的定位精度。
2、计算Z轴滚珠丝杠的刚度
设计计算分析与过程
设计计算结果
(1)、临界转速nc
nc=fdsp*107/L2(r/min)(2-8)
式中dsp—丝杠底径(mm);
L—丝杠支承间距(mm);
f—与支承方法有关的临界转速系数,见表2-4
nc=fdsp*107/L2
nc=15.1*159*107/11032
nc=19734(r/min)
(2)、最大转速nmax
丝杠最大转速nmax按下式计算:
d0nmax≤A(2-9)
式中d0—丝杠名义直径(mm);
nmax—丝杠最大转速
通常取A=50000~70000。
160nmax≤70000
nmax≤437.5(r/min)
在机床工作台加速与切削加工过程中,在进给轴向方向会产生力,必须保证这个力小于允许的压弯临界载荷Fa,否则可能导致进给丝杠弯曲,这对于Z轴至关重要。
压弯临界载荷Fa可用下式计算:
(2-10)
式中dsp—丝杠底径(mm);
L—丝杠支承间距(mm);
m—与丝杠支承方法有关的临界载荷系数,见表2-4
nc=19734r/min
nmax≤437.5
(r/min)
Fa=53584310N
设计计算分析与过程
设计计算结果
(3)、轴向拉压刚度Ks
确定进给丝杠尺寸的最重要设计准则,是考虑它的抗张和抗压刚度。
其计算公式如下:
(2-11)
式中dsp—丝杠底径(mm);
E—弹性模量(钢为2*1011Pa);
L—丝杠的总自由长度(mm)。
对于直径小的丝杠,有轴向力引起的丝杠扭转变形转化为工作台的轴向位移,可能影响丝杠的抗扭刚度。
进给丝杠的抗扭刚度是:
(2-12)
式中G—切变模量(钢为8*1010Pa);
dsp—丝杠底径(mm);
L—丝杠的总自由长度(mm)。
Ks=2579023Nm
KTsp=3260015Nm
经以上设计计算和设计要求,X、Z轴滚珠丝杠可参考(汉江机床厂)(汉江滚珠丝杠厂)的精密滚珠丝杠可得到如下系列符合设计要求,其参数代号如下所示:
X轴滚珠丝杠:
系列代号:
5005-3
表2-6滚珠丝杠尺寸
中径
50
外径
49
导程
5
螺旋角
3°39′
滚珠直径
3.175
列数×圆数
3×(3+3)
表2-7螺母安装尺寸
D
71
D1
110
D2
90
B
15
E
6
M
4
L
FN.FN(Z)50
FYND85
FFND105
Q
M6
ψ1
9
ψ2
15
h
9
额定载荷:
动载荷14122N
静载荷5