深圆筒底孔冲压工艺和模具设计.docx
《深圆筒底孔冲压工艺和模具设计.docx》由会员分享,可在线阅读,更多相关《深圆筒底孔冲压工艺和模具设计.docx(16页珍藏版)》请在冰豆网上搜索。
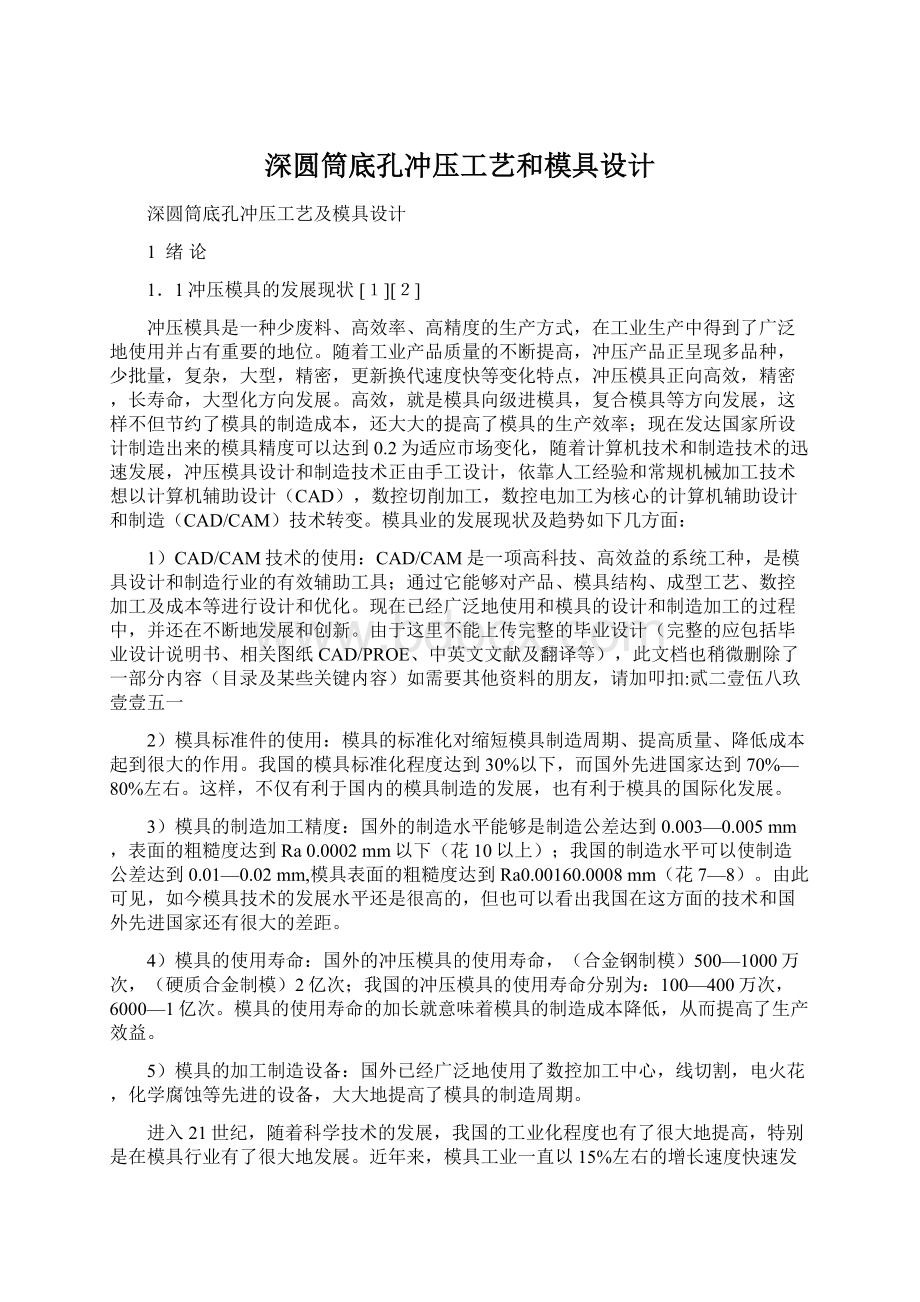
深圆筒底孔冲压工艺和模具设计
深圆筒底孔冲压工艺及模具设计
1绪论
1.1冲压模具的发展现状[1][2]
冲压模具是一种少废料、高效率、高精度的生产方式,在工业生产中得到了广泛地使用并占有重要的地位。
随着工业产品质量的不断提高,冲压产品正呈现多品种,少批量,复杂,大型,精密,更新换代速度快等变化特点,冲压模具正向高效,精密,长寿命,大型化方向发展。
高效,就是模具向级进模具,复合模具等方向发展,这样不但节约了模具的制造成本,还大大的提高了模具的生产效率;现在发达国家所设计制造出来的模具精度可以达到0.2为适应市场变化,随着计算机技术和制造技术的迅速发展,冲压模具设计和制造技术正由手工设计,依靠人工经验和常规机械加工技术想以计算机辅助设计(CAD),数控切削加工,数控电加工为核心的计算机辅助设计和制造(CAD/CAM)技术转变。
模具业的发展现状及趋势如下几方面:
1)CAD/CAM技术的使用:
CAD/CAM是一项高科技、高效益的系统工种,是模具设计和制造行业的有效辅助工具;通过它能够对产品、模具结构、成型工艺、数控加工及成本等进行设计和优化。
现在已经广泛地使用和模具的设计和制造加工的过程中,并还在不断地发展和创新。
由于这里不能上传完整的毕业设计(完整的应包括毕业设计说明书、相关图纸CAD/PROE、中英文文献及翻译等),此文档也稍微删除了一部分内容(目录及某些关键内容)如需要其他资料的朋友,请加叩扣:
贰二壹伍八玖壹壹五一
2)模具标准件的使用:
模具的标准化对缩短模具制造周期、提高质量、降低成本起到很大的作用。
我国的模具标准化程度达到30%以下,而国外先进国家达到70%—80%左右。
这样,不仅有利于国内的模具制造的发展,也有利于模具的国际化发展。
3)模具的制造加工精度:
国外的制造水平能够是制造公差达到0.003—0.005mm,表面的粗糙度达到Ra0.0002mm以下(花10以上);我国的制造水平可以使制造公差达到0.01—0.02mm,模具表面的粗糙度达到Ra0.00160.0008mm(花7—8)。
由此可见,如今模具技术的发展水平还是很高的,但也可以看出我国在这方面的技术和国外先进国家还有很大的差距。
4)模具的使用寿命:
国外的冲压模具的使用寿命,(合金钢制模)500—1000万次,(硬质合金制模)2亿次;我国的冲压模具的使用寿命分别为:
100—400万次,6000—1亿次。
模具的使用寿命的加长就意味着模具的制造成本降低,从而提高了生产效益。
5)模具的加工制造设备:
国外已经广泛地使用了数控加工中心,线切割,电火花,化学腐蚀等先进的设备,大大地提高了模具的制造周期。
进入21世纪,随着科学技术的发展,我国的工业化程度也有了很大地提高,特别是在模具行业有了很大地发展。
近年来,模具工业一直以15%左右的增长速度快速发展,模具工业企业的所有制成分也发生了巨大变化,除了国有专业模具厂外,集体、合资、独资和私营也得到了快速发展。
如:
在模具设计和制造上,不但自己可以制造一些大型,精密,复杂,高效,长寿命的模具,并且能够出口到国外,打开国外的市场。
但是,目前我国的冲压技术和工业发达国家相比还存在一定的差距,主要原因是我国在冲压基础理论及成型工艺,模具标准化,模具设计,模具制造工艺及设备等方面和工业发达国家尚有相当大的差距,导致我国的模具在寿命,效率,加工精度,生产周期等方面和工业发达国家的模具相比差距相当大。
因此这就需要我们努力去研究,推动我国模具业的不断发展,早日赶上先进国家制造水平。
1.2本课题拟解决的问题
1)通过对制件的结构工艺性分析来选择确定冲压工艺方案。
2)通过分析计算来确定来确定模具主要工作零件的尺寸、精度、工作间隙。
3)通过综合分析和研究来选择模具的基本类型。
4)通过分析来选择确定模具主要零件的结构类型。
5)对模具进行装配和调试。
2深圆筒底孔的冲压工艺分析及工艺方案的确定
2.1对工件进行的结构工艺性分析
从图纸上制件的整体看,该制件是经过前面的拉深成型为深圆筒型件,现又要求用一种合理的冲压工艺来完成该深圆筒件底部孔的冲压工序。
现在,从该制件的结构形状、材料、尺寸、精度要求等方面进行分析:
[1][2]
1)从制件的结构形状上看,该制件的整体结构比较大,属于较深的深圆筒型件,其最大深度为350mm;直径为220mm;但是其整体结构比较简单对称;
2)从材料上看,本制件使用的是q235,查询有关钢材特性手册可知,该材料具有良好的冲压性能,比较适合冲裁;
3)从制件的尺寸上看,该制件的冲压工艺要求在深圆筒型件的底部中间位置冲出一个直径为20mm的孔,冲压工艺比较简单;从制件的壁厚上看,整个制件的壁厚较均匀为3mm,相对于较大的整体尺寸壁厚有点薄,可能会在冲压工作中造成一些不便之处。
4)从制件的精度要求上看,在制件的图纸上并没有对制件的尺寸精度有特殊标注,可以认为制件的全部尺寸为自由公差,可选择公差为it14级,尺寸的精度要求不高。
综合以上几方面的考虑,该制件底部冲孔采用普通的冲压工艺就能够满足要求。
2.2冲压工艺方案的分析及确定
2.2.1对制件的冲压工艺方案进行分析
通过以上对制件的结构工艺性分析可知,该制件是在经过拉深成型后,又要求对其底部进行冲孔,而冲孔工序比较简单,因此可以利用单工序模具就能完成。
下面就针对单工序模具的冲孔的工艺方案进行分析:
[3][5]
1)深圆筒形件的开口方向向上;
2)深圆筒形件的开口方向向下;
3)深圆筒形件的开口方向为横向;
2.2.2冲压工艺方案的确定
对以下各种冲压工艺方案进行多方面的对比比较,并确定一种最为合理的方案:
方案一:
制件的开口向上,符合一般的冲压工艺要求,但是存在许多的缺点:
[3]
1)若按照此方案,所设计的凸模的尺寸比较大,重量比较大,所以在一定的程度上就会增加模具的制造成本
2)由于凸模的尺寸,重量较大,致使模具在维修和安装的过程中造成许多不便
3)由于制件本身尺寸较大不容易定位。
方案二:
制件的开口向下时:
1)所设计的模具的冲孔凸模的尺寸较小重量也小,从一定程度上就降低了模具的制造成本,也节约了模具钢材。
2)所设计的模具,在冲压工作中,只需将制件套在凹模上就能够对制件起到很好的定位效果,并通过弹性卸料装置很好地保证制件的变形程度很小。
3)由于凸模的设计尺寸较小,重量也小,所以在模具的安装、修时也比较方便。
方案三:
制件的开口为横向:
[1][2]
1)按照此种方案所设计的模具的高度有所减小,但是又增大了模具的横向尺寸,对模具的材料利用和重量上基本没有太大变化。
2)这种方案所设计的模具的结构比较复杂,需要利用斜滑块,所以在模具的安装和调试时间会带来许多不便。
3)模具在工作过程中的定位不能很好的保证。
综合对以上三种冲压工艺方案的对比分析,因此选用方案三较为合理。
3深圆筒底孔的冲压模具设计
3.1主要的设计计算
在深圆筒形件底孔的冲压模具设计的过程中,必须进行一些必要的设计计算来确定模具的基本尺寸结构和大小,并通过设计计算来选择压力机的型号。
3.1.1冲压力的计算:
该模具采用单工序冲孔模具,拟选择弹性卸料。
冲压力的相关计算如下所示:
根据计算结果,冲压设备拟选择:
3.1.1.1冲裁力F的计算[3]
根据计算公式:
F=KLtтb
=1.3×62.8×3×300
=73476N
式中:
L:
冲裁周边长度L=2пr=2×3.14×10=62.8mm
K:
系数
t:
材料的厚度
Tb:
材料的抗剪强度
3.1.1.2卸料力的计算Fx[2][3]
根据计算公式:
Fx=KxF=0.04×73476
=2940N
查表2.6.1得到,Kx=0.04
3.1.1.3推件力的计算Ft[2][3]
根据计算公式:
Ft=nKtF=5×0.45×73476=165321N
式中:
n=h/t=15/3=5
3.1.1.4冲压工艺总力的计算Fz[2][3]
根据计算公式:
Fz=F+Fx+Ft
=73476+2940+165321
=241737N
3.1.2压力中心的确定及相关的计算[3]
计算压力中心时,先画出凹模型口图,如图2所示:
图一压力中心
在图中将xoy坐标系建立在图示的对称中心线上。
由于该工件为规则的深圆筒形件,且底部的孔要求位置在正中位置,所以将压力中心和其重合,即设在坐标原点o处,这样不但满足操作要求,还便于模具的加工和装配。
3.1.3工作零件的刃口尺寸计算
在确定工作零件尺寸计算之前,首先要考虑工作零件的加工方法及模具的装配方法。
结合该模具的特点,工作零件的形状相对比较简单,凹模和凸模均为圆柱体结构,分开制造方便快捷,又能保证尺寸精度。
所以,工作零件刃口尺寸就按照分开加工的方法来计算:
该工件只需要一次冲孔工序,根据计算原则:
冲孔时以凸模为设计基准,首先确定凸模的尺寸,使凸模的尺寸接近或等于工件的最大极限尺寸,将凸模尺寸增大最小合理间隙值即得凹模尺寸。
根据计算公式:
[3][4][6]
Dt=(dmin+x△)
Da=(dt+zmin)=(dmin+x△+zmin)
式中:
dt/da:
冲孔凸凹模的尺寸;
Dmin:
冲孔件孔的最小极限尺寸;
△:
工件的制造公差;
Zmin:
最小合理间隙;
X:
磨损系数;
δt/δa:
凸凹模的制造公差;
由于工件的图纸上没有标注尺寸公差,可以按照IT14级精度进行计算,查《公差和配合检测技术》表2.4得:
孔的公差为+0.52mm;取x为0.5mm。
[6]
查《冲压模具设计和制造》表2.4.1得:
凸凹模的制造公差分别为:
δt=0.020mm;δa=0.025mm;
校核:
|δt|+|δa|≤|Zmin-Zmax|
查《冲压模具设计和制造》表2.3.3得:
冲裁双面间隙Z为:
Zmin=0.460mm;Zmax=0.640mm;
∴|0.020+0.025|≤|0.460-0.640|
∵0.045≤0.180
∴以上数据满足要求。
∴dt=
da=
3.1.4卸料橡胶的计算
弹性元件—卸料橡胶在选用的过程中选用的4块橡胶板的厚度务必一样,不然会造成受力不均匀,运动产生歪斜,影响模具的正常工作。
各个橡胶的尺寸大小可以根据标准选择使用。
[2][3]
3.2模具的总体设计
通过以上的设计计算对模具的主要工作尺寸和所需要的工作压力的大小有了比较详细的了解,下面就对所要设计的模具的类型、定位方式、卸料方式、导向方式等方面进行分析。
3.2.1模具类型的选择
1)首先通过对制件的结构形状、材料、尺寸、精度要求等各个方面进行分析,可用普通的单工序冲孔模具便能完成深圆筒形件底部孔的冲压工序;
2)经过多种冲压工艺方案的对比分析,综合考虑,可以选择在冲孔工作中使制件的开口向下的模具结构形式。
[1][2]
3.2.2定位方式的选择
1)如果采用一般的模具结构形式进行设计,采用定位板或定位圈等装置对制件进行定位,由于该制件的整体尺寸比较大,特别是深度较大,所以在上料时,对制件进行定位就比较困难,并且这种定位方式也变得不太可靠,在冲压过程中制件还可能会产生变形。
[3][5]
2)如果采用直接将制件套装在凹模上进行定位冲孔,这样就会使上料比较容易,定位也比较可靠(由于制件和凹模的结仇面积比较大),并且在一定的程度上也可以减少制件在冲压过程中所产生的变形。
还有就是,模具在设计过程中不需要另外设计定位装置,从而减少模具的制造成本,同时也简化了模具的结构。
3.2.3卸料方式的选择[2][3]
该制件的整体尺寸比较大,尤其是其深度较大,这就给冲压工作带来了许多的不便,但是该制件的壁厚比较薄,所以在冲孔过程中,制件卡在冲孔凸模上的几率不大。
但是为了避免这种现状的产生出现,可以在模具上设计一套弹性卸料装置——卸料板,它不仅可以防止制件在冲压过程中卡在冲孔凸模上,还可以在冲压过程中起到压料的作用,以保证冲孔的质量。
3.2.4导向方式的选择
在模具的设计当中,采用中间导柱导向方式,从受力方面讲,在冲压工作过程中,压力机所施加的压力通过中间导柱导向而均匀地分散在整个模具上,使模具受力均匀,保证模具各个部件的正常工作,特别是冲孔凸模的行程的正确性,从而保证制件的冲孔质量。
另外,采用中间导柱导向方式的模具在按扎、调试、维修时也比较[1][2]
3.3主要零部件的设计
在模具的设计当中,最为重要的一步就是模具的主要零部件的结构尺寸的设计,因为这是直接影响冲压模具能否正常工作的主要因素。
3.3.1工作零件的结构设计
3.3.1.1冲孔凸模的结构设计
根据标准选择台阶式的凸模,因为台阶式凸模刚度好,装配修磨方便。
其中其最大直径部分的作用是形成台肩,以固定凸模,保证工作时凸模不被拉出;其配合形式为过渡配合H7/m6或H7/n6。
其结构如图3所示:
[2][3]
图.3凸模结构图
凸模的长度计算:
根据凸模的结构形式和计算公式计算,[2][3]
L=h固+h卸+t+h
=30+40+3+30+3
=96mm
3.3.1.2冲孔凹模的结构设计
凹模采用整体式结构,这样可以保证凹模的,便于安装和维修。
其结构如图4所示:
[2][3]
凹模的尺寸计算:
凹模的厚度:
H=kb=0.50×20=10mm
凹模的壁厚:
c=(1.5—2)H=20mm
取凹模的厚度H=385mm;
凹模的直径:
D=220+90×2=250mm;
凹模的轮廓尺寸为:
250×385
图.4凹模结构图
凹模在本套模具中作用较大,首先它是冲孔的主要工作零件,同时也是制件的定位装置。
冲孔时将制件套在凹模上进行定位,能够很好地保证孔的位置精度。
3.3.2卸料零部件的设计
卸料板的边界尺寸和固定板的边界尺寸保持一致,厚度为20毫米.[5]
3.3.3模架及其他零部件的设计
该模具采用中间导柱模架,这种模架的导柱在模具的中间位置,冲压时可以防止由于偏心力矩而引起的模具歪斜。
根据凹模的工作过程所需强度要求和凹模周界尺寸为依据,来选择模架的规格。
导柱d/mm×L/mm分别为35×430,导套d/mm×L/mm×D/mm分别为50×40×55。
上模座厚度H上模取50mm,上模垫板厚度H垫取10mm;固定板厚度H固取30mm;下模座厚度H下模取55mm。
综上,模具的闭合高度H闭合为:
[3]
H闭合=H上模+H垫+L+H+H下模-h2
=50+10+96+385+55-3
=593mm
式中:
L—凸模长度,L=96mm;
H—凹模厚度,H=385mm;
H2—凸模冲裁后进入凹模的深度,h2=3mm。
可见该模具闭合高度小于所选压力机为闭式双点压力机公称压力为1600KN的最大装模高度600mm,所以可以采用。
[3]
3.4模具总装图
通过以上设计,可以得到如图.6所示的模具总装简图。
模具的上模部分主要由模柄、上模板、垫板、凸模、凸模固定板、卸料板等组成。
卸料方式采用的是弹性卸料,以橡胶为弹性元件。
下模部分由下模座、凹模板、定位板等组成。
在冲压过程中,由于制件的尺寸太大,所以在装制件的时候比较困难,需要导柱和导套完全脱离,然后将制件套在凹模上进行定位,上模下行对制件进行冲孔,此时弹性卸料板紧压制件,对制件起到压料作用,冲孔动作完成,废料从凹模孔中落下,而制件可能会紧裹在凸模上,这时上模回程,在弹性卸料板的作用下将制件从凸模上卸下。
接着进行第二次冲压工序。
图.6模具总装简图
3.5冲压设备的选定
通过各项指标的校核,压力机可以选择闭式双点压力机能够满足使用要求,其主要技术参数如下:
[1][2]
公称压力:
1600KN
滑块行程:
400mm
最大闭合高度:
600mm
最大装模高度:
850mm
连杆调节长度:
250mm
工作台尺寸(前后×左右):
1120×1900mm
模柄孔尺寸:
50mm
最大倾斜角度:
30度
3.6模具零件的加工工艺
本副冲压模具,模具的主要零部件加工工艺过程如下:
冲压凸模的加工工艺过程见附录表格1;
冲压凹模的加工工艺过程见附录表格2;
冲压凸模固定板的加工工艺过程见附录表格3;
4模具的安装和调整
4.1模具的装配
模具装配是最后实现冲压模具设计和冲压工艺的意图的过程,也是模具制造过程中的关键工序。
模具装配的质量直接影响制件的冲压质量、模具的使用和模具寿命。
模具的装配一般都有两个装配过程:
首先是主要零部件的装配,最后再进行总装配。
4.1.1主要零部件的装配[3][4]
4.1.1.1模柄的装配
在安装凸模固定板和垫板之前先安装模柄,按照H7/m6的配合条件,在压力机上将其压入上模座,并把模柄端面突出部分锉平或磨平。
安装完成后用角尺检查模柄和上模座上平面的垂直度。
4.1.1.2凸模的装配
按照H7/m6的配合,在压力机上将凸模压入固定板内,检查凸模的垂直度,然后将固定板的上平面和凸模尾部一齐磨平,为了保持刃口锋利,还可以将凸模的端面磨平。
4.1.1.3弹性卸料板的装配
弹性卸料板起卸料又起压料的作用,在装配时应保证它和凸模之间具有适当的间隙,具体的装配方法是,将弹压卸料板套在已装入固定板的凸模内,在固定板和卸料板之间垫上平行垫块,并用平行夹板将它们夹紧,然后,在固定板上钻螺纹孔和销钉孔。
4.1.2模具的总体装配
根据凹模在下模的导柱模具的安装要点,先选择凹模作为装配基准件,先装下模,再装上模,并调整间隙,进行试冲,修磨,试冲……。
其详细过程如表.4所示:
4.2 模具的调试
模具装配以后,必须在生产条件下进行试冲.冲出的工件按冲压零件产品图或试样进行检查验收.在检查验收过程中,如发现各种缺陷,必须经过仔细分析,找出原因,并对模具进行适当的调整和修理,然后再试冲,直到模具正常并得到合理的冲件为止.冲压过程中的缺陷及模具的调整详细过程见附录表格5.
5总结
经过近段的努力,在老师和同学们的指导和帮助下,我顺利地完成了这次的毕业设计任务。
经过这次的设计任务,使我对模具设计,特别是冲压模具的设计过程有了进一步地了解;对冲压模具的基本结构、组装、调试、加工制造等方面有了深刻理解。
在设计的过程中,通过对制件的分析和对模具的设计的研究时,能够较好地将课本上的理论知识使用和设计当中,并且能够从整体,宏观上去研究、分析、考虑设计问题。
同时,在这次的设计过程中,还很大地程度上锻炼了自己的动手能力,如:
亲自去收集和查找有关资料,并从中又学会了一门新的课程《如何查找资料和文献》;其次,通过搜寻大量的资料,还大大地锻炼了自己的画图、看图、排版等方面的能力。
最重要的是,经过这次毕业设计,使我真正地感受到了集体的力量和学习方法。
在设计过程中,难免会遇到技术或其他方面的难题,但是通过老师的指导和和同学们的交流和虚心地请教都得到了解决,使我最终顺利地完成设计。
由于本人的水平有限,经验不足,在设计当中如有不妥之处,还恳请各位老师指导更正。
致谢
经过一段时间的紧张工作,至今日终于顺利完成毕业设计。
在这里,我要忠心地感谢一些在我的设计工作中给予我很大的帮助。
首先:
我要感谢我的指导老师程老师,特别感谢程老师的近段设计期间对我的指导和帮助,特别是在离校期间的关心。
其次:
我要感谢的是我的同学们,在设计过程中遇到技术问题,通过和他们的商讨和帮助,查阅资料,一一攻破难关,助我顺利地完成设计。
最后:
我还要深深地感谢在工厂里的师傅们,在进行毕业设计期间,他们给予我以模具制造和设计方面上的经验指导。
参考文献
[1]精密面具制造技术 胡石玉主编 北京 东南大学出版社
[2]冲压模具设计国家十五电子出版北京机械工业出版社
[3]冲压模具设计和制造刘建超主编北京高等教育出版社
[4]模具制造技术翟德梅主编河南河南机电高等专科学校
[5]冲压模具图册杨占尧主编北京高等教育出版社
[6]公差配合和技术测量薛彦成主编北京机械工业出版社
[7]金属工艺学邓文英主编北京高等教育出版社
[8]模具材料高为国主编北京机械工业出版社
[9]模具设计和制造 骆志斌主编北京化学工业出版社
[10]模具设计大典李志刚主编 北京中国机械工程学会
[11]TolerancefittingandtechnologyofmeasuringTracyMcGradyPublishinghouseofthemechanicalindustry
附 录
表.1凸模的加工工艺过程:
工序号
工序名称
工序内容
机械设备名称
1
备料
圆钢
锯床
2
锻造
锻造
空气锤
3
热处理
退火
电炉
4
磨平面
磨削上下两端面
锉刀
5
粗车
粗车并留有余量
车床
6
精车
精车并留有少许余量
车床
7
热处理
淬火+回火达到58—62HRC
电炉
8
磨削
磨外缘和端面留有少量余量
外缘磨+平面磨
9
钳工精修
按照图纸精修,达到尺寸精度要求
砂纸+锉刀
10
检验
检验是否合格
千分尺
表.2凹模的加工工艺过程:
工序号
工序名称
工序内容
机械设备名称
1
备料
圆钢
锯床
2
锻造
锻造
空气锤
3
热处理
退火
电炉
4
磨平面
磨上下两端面
平面磨床
5
钳工划线
划出各孔的位置线和轮廓
划针+钢尺
6
磨平面
精磨上下两平面
磨床
7
线切割
按照图线切割,轮廓达到图纸要求
线切割
8
钳工精修
按照图纸精修至图纸要求尺寸精度
砂纸+锉刀
9
检验
检验是否合格
千分尺
表.3固定板的加工工艺过程:
工序号
工序名称
工序内容
机械设备名称
1
备料
圆钢
锯床
2
锻造
锻造
空气锤
3
热处理
退火
电炉
4
磨平面
磨上下两端面
平面磨床
5
车削
车外缘至图纸要求
车床
6
镗孔
镗定位孔并留有加工余量
镗床
7
铰孔
精铰定位孔留有精修余量
铰刀
8
钳工精修
按照图纸精修至图纸要求尺寸精度
砂纸+锉刀
9
检验
检验是否合格
千分尺
表.4总装配过程:
序号
工序
工艺说明
1
凸、凹模预配
①装配前仔细检查各凸模形状及尺寸以及凹模形孔,是否符合图纸要求尺寸精度、形状。
②将凸模和凹模孔相配,检查其间隙是否加工均匀(可以通过切纸法检验)。
不合适者应重新修磨或更换。
2
凸模装配
以凹模孔定位,将凸模压入凸模固定板的形孔中,并磨平端面。
3
装配下模
①在下模座上划中心线,按中心预装凹模。
②在下模座上用已经加工好的凹模分别确定其螺钉孔的位置,并分别钻孔、攻丝。
③将下模座、凹模装在一起,并用螺钉紧固,打入销钉。
4
装配上模
①在已经装好的下模上放等高垫铁,再在凹模中放入薄纸片,然后将凸模和固定板组合装入凹模;
②预装上模座,划出和凸模固定板相应螺孔、销钉孔位置并钻铰螺钉孔和销钉孔。
③用螺钉将固定板组合、垫板、上模座连接在一起,但不拧紧;
④将卸料板套装在已