四工位自动旋转刀架设计说明书.docx
《四工位自动旋转刀架设计说明书.docx》由会员分享,可在线阅读,更多相关《四工位自动旋转刀架设计说明书.docx(15页珍藏版)》请在冰豆网上搜索。
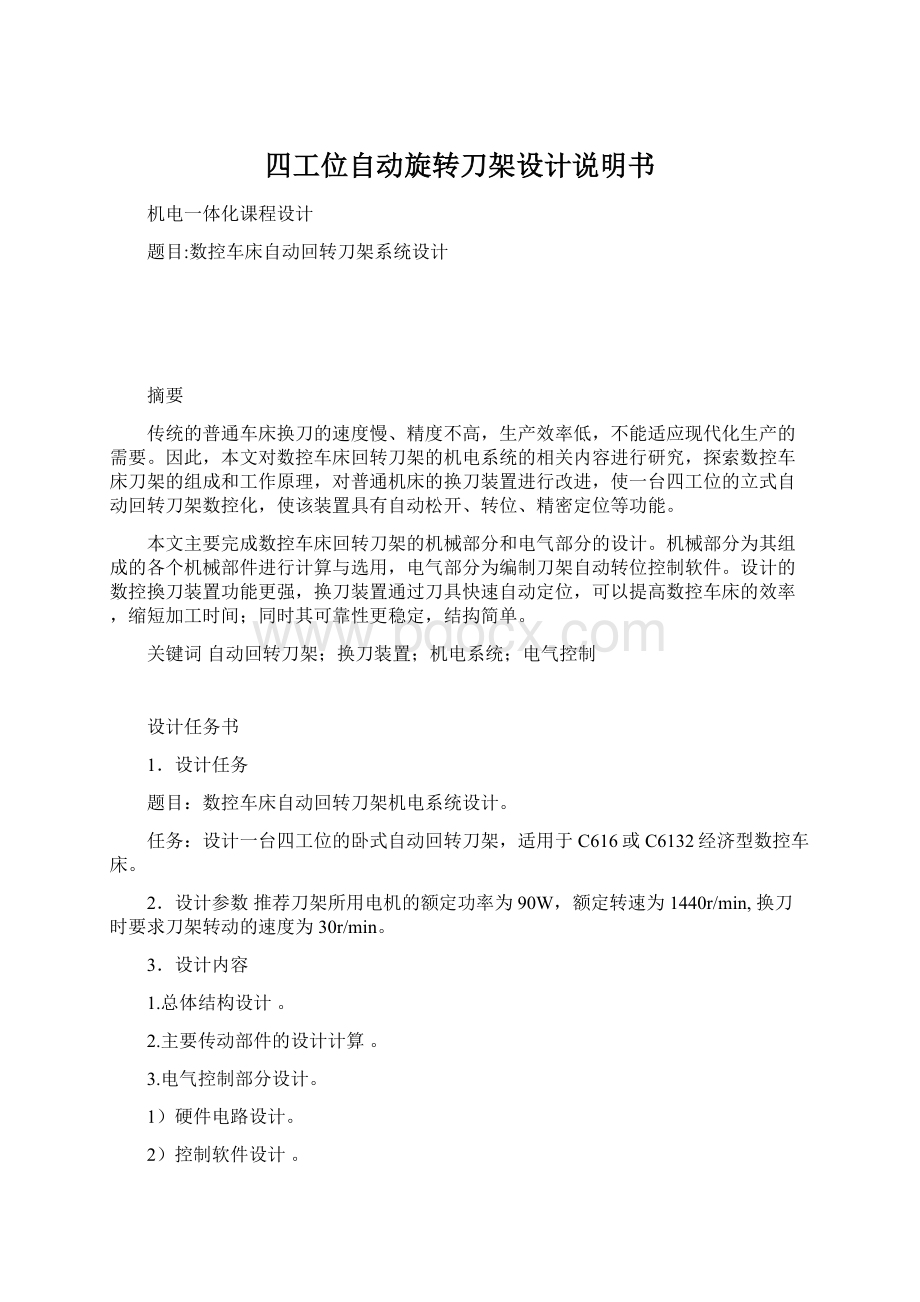
四工位自动旋转刀架设计说明书
机电一体化课程设计
题目:
数控车床自动回转刀架系统设计
摘要
传统的普通车床换刀的速度慢、精度不高,生产效率低,不能适应现代化生产的需要。
因此,本文对数控车床回转刀架的机电系统的相关内容进行研究,探索数控车床刀架的组成和工作原理,对普通机床的换刀装置进行改进,使一台四工位的立式自动回转刀架数控化,使该装置具有自动松开、转位、精密定位等功能。
本文主要完成数控车床回转刀架的机械部分和电气部分的设计。
机械部分为其组成的各个机械部件进行计算与选用,电气部分为编制刀架自动转位控制软件。
设计的数控換刀装置功能更强,换刀装置通过刀具快速自动定位,可以提高数控车床的效率,缩短加工时间;同时其可靠性更稳定,结抅简单。
关键词自动回转刀架;换刀装置;机电系统;电气控制
设计任务书
1.设计任务
题目:
数控车床自动回转刀架机电系统设计。
任务:
设计一台四工位的卧式自动回转刀架,适用于C616或C6132经济型数控车床。
2.设计参数推荐刀架所用电机的额定功率为90W,额定转速为1440r/min,换刀时要求刀架转动的速度为30r/min。
3.设计内容
1.总体结构设计。
2.主要传动部件的设计计算。
3.电气控制部分设计。
1)硬件电路设计。
2)控制软件设计。
4.编写设计说明书。
四.设计任务
1.模拟整体设计方案
2.机械结构装配图一张(A0图)
3.控制系统设计
要求完成一张A1图纸的硬件电路设计工作,设计控制系统的主要软件流程,对RAM和I/O接口芯片进行详细编程。
4.设计说明书
要求清楚地叙述整个设计过程和详细的设计内容,包括总体方案的分析,比较和确定机械系统的结构设计,主要零部件的计算与选型,控制系统的电路原理分析,软件设计的流程图以及相关程序等。
撰写的内容不少于7000字符,要求内容丰富,条理清晰图文并茂,符合国标。
一绪论
题目的背景和意义
数控技术自20世纪中叶出现以来,数控机床给机械制造业带来了革命性的变化。
数控加工的加工柔性好,加工精度高,生产率高,能减轻操作者劳动强度、改善劳动条件,有利于生产管理的现代化以及经济效益的提高。
数控机床是一种典型的机电一体化产品,适用于加工多品种小批量、结构较复杂、精度要求较高、价格昂贵不允许报废的关键零件。
而刀架是数控机床的主要附件之一,它的性能直接影响着数控机床的精度和效率,所以随着数控机床的发展必然会提高其对刀架的要求,不言而喻,研究自动刀架系统是非常有意义的。
国内外研究现状
自动刀架系统应用了自动控制、微电子、精密测量等方面的最新成就,是典型的机电一体化产品。
它的发展和运用,改变了制造业的生产方式、产业结构、管理方式,为普通机床演变为数控机床创造了条件,使世界制造业的格局发生了巨大的变化。
数控水平的高低已经成为衡量一个国家制造业水平高低的标志。
随着数控机床的发展,以前的刀架,能装的刀具太少,定位精度不高,效率低,精度差,已不能满足要求,于是便出现了许多精度更高、刀架更大、自动化程度更高的刀架。
目前我国的数控机床和加工中心使用的自动换刀装置主要有转塔式自动换刀和刀库式自动换刀两种。
转塔式换刀一般为顺序换刀,其换刀时间短,结构简单、紧凑,但刚性较差,能容纳刀具较少;刀库式换刀一般刀库只有选刀动作而另需机械手进行换刀动作,其刀库容量大,但其成本高,结构相对复杂。
存在的问题和发展趋势
机床工具行业的发展,依赖于行业技术水平和创新能力的提高,依赖于机床的数控化和产品快速的升级换代,依赖于制造业从刚性自动化向柔性自动化方向转变这一社会需求,由于我国机床附件厂资金紧张,造成技术创新和技术改造的力度不大,使附件水平的发展严重滞后,成为制约民族机床工业发展的瓶颈。
国产配套件在产品质量、性能、结构创新、品牌信誉、外观造型、精度稳定性等方面与发达国家相比都存在一定的差距。
二自动回转刀架的工作原理
图(b)
图(d)
图(c)
1—上盖圆盘2—圆柱销3—弹簧4—上刀体5—圆柱销6—反靠销7—反靠圆盘
当刀架处于锁紧状态时,两销的情况如图a所示,此时反靠销6落在反靠圆盘7的十字槽内,上刀体4的端面齿和下刀的端面齿处于啮合状态(上下端面齿在图a中未画出)。
需要换刀时,控制系统发出刀架的转位信号,三相异步电动机正向旋转,通过蜗杆副带动螺杆正向转动,与螺杆配合的上刀体4逐渐抬起,上刀体4与下刀体之间的端面齿慢慢脱开;与此同时,上盖圆盘1也随着螺杆正向转动(上盖圆盘1通过圆柱销与螺杆联接),当转过约150度时,上盖圆盘1直槽的另一端转到圆柱销2的正上方,由于弹簧3的作用,圆柱销2落入直槽内,于是上盖圆盘1就通过圆柱销2使得上刀体4转动起来(此时端面齿已完全脱开),如图b所示。
上盖圆盘1、圆柱销2以及上刀体4在正转的过程中,反靠销6能够从反靠圆盘7中十字槽的左侧斜坡滑出,而不影响上刀体4寻找刀位时的正向转动,如图c所示。
上刀体4带动磁铁转到需要的刀位时,发信盘上对应的霍尔元件输出低电平信号,控制系统收到后,立即控制刀架电动机反转,上盖圆盘1通过圆柱销2带动上刀体4开始反转,反靠销6马上就会落入反靠圆盘7的十字槽内,至此,完成粗定位,如图d所示。
此时反靠销6从反靠圆盘7的十字槽内爬不上来,于是上刀体4停止转动,开始下降,而上盖圆盘1继续反转,其直槽的左侧斜坡将圆柱销2的头部压入上刀体4的销孔内,之后,上盖圆盘1的下表面开始与圆柱销2的头部滑动。
在些期间,上、下刀本的端面齿逐渐啮合,实现定位,经过设定的延时时间后,刀架电动机停转,整个换刀过和结束。
由于蜗杆副具有自锁功能,所以刀架可稳定的工作。
三总体结构设计
减速机构的设计
电动机的选择
电动机选择三步异相电动机,额定功率为90W,额定转速为1440r/min,而刀架转速设定30r/min,由于转速较高不能直接驱动刀架,因此必须经过适当的减速。
采用蜗杆副减速,蜗杆副传动可以改变运动的方向,获得较大的传动比,以保证传动精度和平稳性并能自锁,可以减少整个装置的空间,比较精简。
上刀体锁紧与精定位机构的设计
上刀架锁紧与精定位将直接影响工件的加工精度,因为刀具直接安装在上刀体上,所以刀体要承受全部的切削力,因此对它的选择很重要,在设计中选择端面将上刀体与下刀体的配合加工成梯形的端面齿。
采用梯形的端面齿,刀架处于锁紧时,下端面齿相互啮合,这时上刀体不能绕刀架的中心轴转动;换刀时电动机正转,抬起机构使上刀体抬起,等上下端面齿脱开后,上刀体才可以绕刀架中心轴转动,完成转位工作。
刀架抬起机构的设计
在上述过程中欲使上下刀体的两个端面齿脱离。
就必须设计分离机构,在此选择螺杆—螺母副,并在上刀体内部加工出内螺纹,当电动机通过蜗杆—蜗轮带动螺杆绕中心轴转动时,而将上刀体看做螺母,要么转动,要么上下移动。
两种情况,当刀架处于锁紧状态时,上刀体与下刀体的端面齿相互啮合,因为这时上刀体不能与螺杆一起转动,转动会使上刀体向上移动。
当端面齿脱离啮合时,上刀体就和螺杆一同转动,在设计螺杆时要注意螺距的选择,而螺距的选择是否合理非常重要,选择适当以便当螺杆转动一定角度时,使上刀体与下刀体的端面齿能够完全脱离啮合状态。
自动回转刀架的传动机构示意图
1—发信盘2—推力轴承3—螺杆螺母机构4—端面齿盘5—发靠圆盘6—三相异步电动机7—联轴器8—蜗杆副9—反靠销10—圆柱销11—上盖圆盘12—上刀体
四主要传动部件的设计计算
蜗杆副的设计计算
自动回转刀架的动力源是三相异步电动机,其中蜗杆与电动机直联,刀架转位时蜗杆与上刀体直联。
已知电动机额定功率P1=90W,额定转速n1=1440r/min,上刀体设计转速n2=30r/min,则蜗杆副的传动比i=1440/30=48。
刀架从转位到锁紧时,需要蜗杆反向,工作载荷不均匀,起动时冲击较大,今要求蜗杆的使用寿命Lh=10000h,因此对蜗杆的型号材料的选择以及齿面接触疲劳强度计算相当重要。
蜗杆的选型
本设计采用阿基米德型圆柱蜗杆,因为阿基米德蜗杆虽然精度不高,但是具有加工简便的优点,目前在机械应用中最为广泛,因此选用阿基米德蜗杆(ZA蜗杆)。
蜗杆的材料
刀架中的蜗杆副传递的功率不大,但蜗杆转速较高,因此,蜗杆的材料选用45钢,其螺旋齿面要求淬火,硬度为45~50HRC。
而蜗轮需要提高其表面耐磨性,而锡青铜的耐磨性最好,因此选用铸造锡青铜,采用金属模铸造。
按涡轮齿面接触疲劳强度进行设计
刀架中的蜗杆副采用闭式传动,多因齿面脱离危险合或点蚀而失效。
因此,在进行承载能力计算时,先按齿面接触疲劳强度进行校核。
按蜗轮接触疲劳强度条件设计计算的公式为:
——蜗杆副的传动中心距,单位为mm;
KA——使用系数,KA=~,当冲击载荷,环境温度高,速度较高时,取大值.
——材料综合弹性系数,钢与铸锡青铜配合时,ZE=150.
——接触系数,用d1/a表示,一般取~
因为i=48,查表8-2得取z1=1。
由z1=1查表8-9得估计η=,z2=iz1=48。
因为P1=90w可得蜗轮传递功率P2=.又因为n2=30r/min,所以作用在蜗轮上的转矩
T2=n2=η/n2=·mm
因为工作载荷不均匀,启动时冲击较大,取KA=,取d1/a=,则
=()。
蜗轮材料是锡青铜,且是金属型铸造,且蜗杆齿面硬度大于45HRC,所以取
=220Mpa。
计算中心距:
=
=
蜗杆和蜗轮的主要参数与几何尺寸
蜗杆分度圆直径d1≈×=
模数:
m≈(~)×a/z2=~。
查表8-1取m=,d1=20mm,q=,d2=。
所以a=×Tm(q+z2)=。
圆整取a=50mm。
接触强度满足要求。
导程角:
tanγ=z1/q,所以γ=º
校核蜗轮齿根弯曲强度
蜗轮齿形系数,当量齿数zv=Z2/cos3γ=
查表7-10,取YFa2=,查表8-6,许用弯曲应力
=70Mpa。
所以蜗轮齿根弯曲应力
=×KA×YFa2×T2/(d1×d2×m×cosγ)=38<70Mpa
所以弯曲强度足够。
蜗杆轴的设计
蜗杆轴的材料选择,确定许用应力
考虑轴主要传递蜗轮的转矩,为普通用途中小功率减速传动装置。
选用45号钢,正火处理,查表16-1,因为直径小于100mm,所以取
。
按扭转强度初步估算轴的最小直径
因为是传动轴,所以取M=0,扭转切应力是脉动循环变应力,所以取
。
查表8-3得
dmin=
确定各轴段的直径和长度
同一轴上的轴承选用同一型号,以便于轴承座孔镗制和减少轴承类型。
因为考虑
轴上有一个键槽,故槽径增大5%。
圆整
。
选用轴承类型是深沟球轴承,型号为6202,
,
。
起固定作用,d2相对于
是一个轴肩作用,所以查手册取定位载荷高度可在h=(~)
范围内。
所以
=
+2h=~18mm。
所以取
=18mm。
为蜗杆与蜗轮啮合部分,取齿顶高系数为1,径向间隙系数为。
所以齿顶圆直径为,齿根圆直径为。
所以取
=24mm。
因为
和
的作用是一致的,都是用于固定,所以
以便于加工和安装。
各轴段长度:
与轴承配合的轴段,查轴承宽度为11mm,端盖的宽度为
=10mm,所以取L1=21mm。
尺寸长度与刀架体的设计有关,蜗杆端面到刀架端面距离为65mm,故L2=44mm。
为蜗杆部分长度,L3=b1,查表8-7可得b1
(11+×48)×=
,圆整取
=30mm。
取45mm,
在刀架体部分长度为(12+8)mm,伸出刀架部分通过联轴器与电动机相连长度为30mm,故
。
螺杆的设计及上盖圆盘旋转角度的计算
螺杆螺纹类型的选择
螺纹有矩形、梯形与锯齿形,常用的是梯形螺纹。
梯形螺纹牙型为等腰梯形,牙形角α=30º,梯形螺纹的内外螺纹以锥面贴紧不易松动。
故选梯形螺纹。
在此自动回转刀架中,根据结构,查表取螺纹类型为:
螺距P=5,头数N=2,则导程为S=10mm.
选取螺杆材料
螺杆材料常用Q235、Q275、40、45、55等。
本刀架选45钢。
螺杆的计算
根据国家规定
=~,取
=(梯形螺纹);螺纹牙的工作高度h=;查教材表2-4-9,[p]取21Mpa
故,d2≥
=
=
查机械制图附表2-3,
,P=5mm
螺纹牙的工作高度
根据教材(2-4-36)的校核式
,满足条件
螺杆自锁验算
自锁条件是
v,式中:
为螺纹升角;v为螺旋副当量摩擦角,v=arctan
,当螺旋副材料为钢对青铜时取
=(为保证自锁,螺纹升角至少要比当量摩擦角小1°~°)
=arctan(nP/d2)=arctan(1
5/
)
°
v=
故,
=°上盖圆盘旋转角度的计算
综上所述,螺杆的导程为10mm,上下齿盘齿形高为4mm,当两齿盘脱离啮合时,螺杆上升4mm,此时,螺杆旋转
即旋转
.由于螺杆与上盖圆盘通过销连接,另外,上盖圆盘旋转的同时,上刀体也在旋转,脱离啮合时约旋转4°,故上盖圆盘旋转大约140时,上刀体内的定位销进入上盖圆盘中.
五其他部件的说明
深沟球轴承:
基本额定动载荷比:
1;极限转速比:
高;轴向承载能力:
少量;轴向限位能力:
I;性能和特点:
主要承受径向载荷,也可同时承受小的轴向载荷,当量摩擦系数最小,在高转速时,可用来承受纯轴向载荷,工作中允许内、外圈轴线偏斜量小于等于8分到16分,大量生产,价格最低。
电机法兰盘:
法兰,是flange的中文翻译。
法兰一般是盘状物,且上面带至少一个连接用的光孔或者螺孔,是用来与其它部件进行连接的。
电机上的法兰主要有2类,一个是“大法兰”,一般指电机的端盖,是用来支撑电机的转子、安放轴承、有时也起对电机密封〔保护〕的作用。
另一个是“小法兰”,一般是指轴承盖,用来固定和防护轴承的。
霍尔元件:
按照霍尔开关的感应方式可将它们分为:
单极性霍尔开关、双极性霍尔开关、全极性霍尔开关。
单极性霍尔开关的感应方式:
磁场的一个磁极靠近它,输出低电位电压(低电平)或关的信号,磁场磁极离开它输出高电位电压(高电平)或开的信号,但要注意的是,单极性霍尔开关它会指定某磁极感应才有效,一般是正面感应磁场S极,反面感应N极。
双极性霍尔开关的感应方式:
因为磁场有两个磁极N、S(正磁或负磁),所以两个磁极分别控制双极性霍尔开关的开和关(高低电平),它一般具有锁定的作用,也就是说当磁极离开后,霍尔输出信号不发生改变,直到另一个磁极感应。
另外,双极性霍尔开关的初始状态是随机输出,有可能是高电平,也有可能是低电平。
全极性霍尔开关的感应方式:
全极性霍尔开关的感应方式与单极性霍尔开关的感应方式相似,区别在于,单极性霍尔开关会指定磁极,而全极性霍尔开关不会指定磁极,任何磁极靠近输出低电平信号,离开输出高电平信号。
发信盘:
RC滤波电路由电阻和电容组成。
在电动刀架发信盘的所有信号输出端串联本实用新型的保护电路后,可以防止直流电源倒相和操作过电压、高次谐波电压及瞬间过电流的冲击破坏,电源输入端串联本实用新型的保护电路后,可以保证发信盘霍尔元件工作点稳定。
轴承盖是轴承端面的盖子,其作用是:
1:
阻止灰尘等异物侵入滚动体的滚道;
2:
保证润滑剂(润滑脂)仅对滚动体和滚道起作用而不溢出。
3:
一定程度上防止滚动体保持架等易损件受外力作用而损坏。
刚性联轴器,顾名思义,实际上是一种扭转刚性的联轴器,即使承受负载时也无任何回转间隙,即便是有偏差产生负荷时,刚性联轴器还是刚性传递扭矩。
单片机控制系统属于弱电控制部分,说它是干扰源是因为它的主电路部分属于强电控制部分,因此,为了保证系统工作稳定,在弱电和强电之间采用一定的隔离措施是非常必要的。
六电气控制部分设计
自动回转刀架的电气控制部分主要包括收信电路和发信电路两大块
收信电路
图a中发信盘上的4只霍尔开关(型号为UGN3120U),都有3个引脚,第1脚接+12V电源,第2脚接+12V地线,第3脚为输出。
转位时刀台带动磁铁旋转,当磁铁对准某一个霍尔开关时,其输出端第3脚输出低电平;当磁铁离开时,第3脚输出高电平。
4只霍尔开关输出的4个刀位信号T1~T4分别送到4只光耦合器进行处理,经过光电隔离的信号再送给I/O接口芯片8255的PC4~PC7。
发信号电路
刀架电动机正反转控制电路,I/O接口芯片8255的PA6与PA7分别控制刀架电动机的功率只有90W,所以刀架电动机与380V交流电源的接通可以选用大功率直流继电器,而不必采用继电器-接触器控制电路,以节省成本,降低故障率。
正转继电器的线圈KA1与反转继电器的一组常闭触点串联,而反转继电器的线圈KA2又与正转继电器的一组常闭触点串联,这样就构成了正转与反转的互锁电路,以防控制系统失控时导致短路现象。
当KA1或KA2的触点接通380V电压时,会产生较强的火花,并通过电网影响控制系统的正常工作,为此,布置了3对R-C阻容用来灭弧,以抑制火花的产生。
控制软件的设计
在清楚了自动回转刀架的机械结构和电气控制电路后,就可以着手编制刀架自动回转转位的控制软件了。
对于四工位自动回转刀架来说,它最多装4把刀具,设计控制软件的任务,就是选中任意一把刀具,让其转到工作位置。
设控制系统的CPU为AT89C51单片机,扩展8255芯片作为自动回转刀架的收信与发信控制,已知8255芯片的控制口地址为2FFH。
1#刀转到工作位置的程序流程,2#~4#刀的转位流程与1#刀相似。
T01:
MOVDPTR,#2FFEH;指向8255的PC口地址
MOVXA,@DPTR;读取PC口的内容
JNB,TEND;测试PC4=0若是,则说明1#已在工作位置,程序转到TEND
MOVDPTR,#2FFCH;指向8255的PA口地址
MOVXA,@DPTR;读取PA口锁存器的内容
CLR;令PA6=0,刀架电动机正转有效
SETB;令PA7=1,刀架电动机反转无效
MOVX@DPTR,A;刀架电动机开始正转
CALLDE20MS;延时20ms
YT01:
MOVXDPTR,#2FFEH;指向8255的PC口地址
MOVXA,@DPTR;第二次读取PC口内容
JB,YT01;PC4=0若是,则往下执行;若否,则程序转到YT01
CALLDE20MS;延时20ms
MOVDPTR,#2FFCH;指向8255PA口地址
MOVXA,@DPTR;读取PA口锁存器内容
SETB;令PA6=1,刀架电动机正转无效
SETB;令PA7=1,刀架电动机反转无效
MOVX@DPTR,A;刀架电动机停转
CALLDE150MS;延时150ms
CLR;令PA7=0,刀架电动机反转无效
SETB;令PA6=1,刀架电动机正转无效
MOVX@DPTR,A;刀架电动机开始反转
CALLDELAY;延时设定的反转锁紧时间
SETB;令PA6=1,刀架电动机正转无效
SETB;令PA7=1,刀架电动机反转无效
MOVX@DPTR,A;刀架电动机停转
TEND:
RET;换1#刀结束
结论
为了能在工件的一次装夹中完成多个工序加工,缩短加工辅助时间,减少多次安装所引起的加工误差,充分发挥数控机床的效率,采用“工序集中”的原则,采用自动回转刀架。
通过对四工位刀架的设计,分别对其组成部分即机械总体结构、工作原理、主传动部件以及电气控制部分进行研究、改善。
文中减速机构选用三相异步电机和蜗杆副,能获的大的传动比,保证传动精度平稳,能实现整个装置的小型化;考虑所受载荷和加工精度选取端面齿盘,在刀架抬起机构中釆用丝杆螺母机构。
主传动部件设计中蜗杆采用阿基米德型圆柱蜗杆,材料采用45钢,涡轮用耐磨性大的铸锡磷青铜ZCuSn10P1,并通过假定参数对其疲劳强度进行设计,并依次算出蜗杆蜗轮的主要参数和尺寸,再通过查表计算确定了中心轴、齿盘、轴承等其他部件的型号、选材及其主要参数和尺寸。
电气部分分别对硬件和软件进行设计。
硬件电路设计中发信采用芯片8255的PA6、PA7控制正反转,接收端采用霍尔元件控制其转位,软件设计CPU中釆用AT89C51单片机,扩展8255芯片控制刀架的收信与发信,并编辑汇编程序控制刀架转位。
设计从经济适用出发在材料选择和参数选择都做到优化选择。
参考文献
[1]尹志强.机电一体化系统设计课程设计指导书[M].北京:
机械工业出版社,2007:
54-99
[2]王润孝.机床数控原理与系统[M].甘肃:
西北工业大学出版社,2004:
64-75
[3]冯辛安.机械制造装备[M].北京:
机械工业出版社,2005:
23-56
[4]刘红文.材料力学[M].北京:
高等教育出版社,1998:
61-111
[5]余仲裕.数控机床维修[M].北京:
机械工业出版社,2002:
52-81
[6]郑文伟.机械原理[M].北京:
高等教育出版社,1997:
45-68
[7]张至丰.金属工艺学[M].北京:
机械工业出版社,2004:
52-69
[8]张发玉.PLC可编程序控制器[M].陕西:
西安电子科技大学出版社,2006:
58-78
[9]于骏一.机械制造技术基础[M].北京:
机械工业出版社,2004:
58-69
[10]成大先.机械设计手册单行本机械传动[M].北京:
化学工业出版社,2004:
76-98
[11]殷际英.光机电一体化应用技术[M].北京:
机械工业出版社,2003:
46-73