初冷.docx
《初冷.docx》由会员分享,可在线阅读,更多相关《初冷.docx(42页珍藏版)》请在冰豆网上搜索。
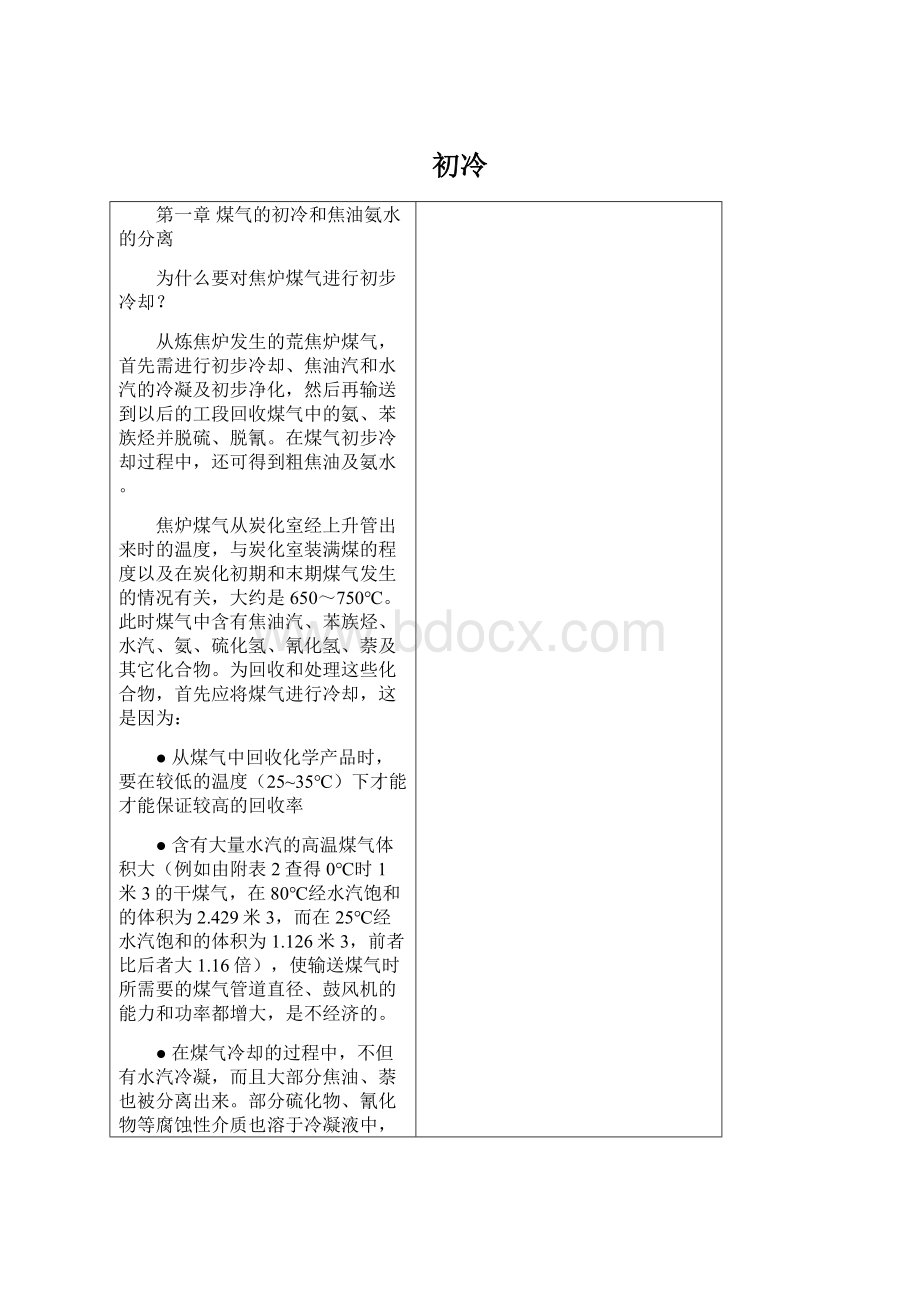
初冷
第一章煤气的初冷和焦油氨水的分离
为什么要对焦炉煤气进行初步冷却?
从炼焦炉发生的荒焦炉煤气,首先需进行初步冷却、焦油汽和水汽的冷凝及初步净化,然后再输送到以后的工段回收煤气中的氨、苯族烃并脱硫、脱氰。
在煤气初步冷却过程中,还可得到粗焦油及氨水。
焦炉煤气从炭化室经上升管出来时的温度,与炭化室装满煤的程度以及在炭化初期和末期煤气发生的情况有关,大约是650~750℃。
此时煤气中含有焦油汽、苯族烃、水汽、氨、硫化氢、氰化氢、萘及其它化合物。
为回收和处理这些化合物,首先应将煤气进行冷却,这是因为:
●从煤气中回收化学产品时,要在较低的温度(25~35℃)下才能才能保证较高的回收率
●含有大量水汽的高温煤气体积大(例如由附表2查得0℃时1米3的干煤气,在80℃经水汽饱和的体积为2.429米3,而在25℃经水汽饱和的体积为1.126米3,前者比后者大1.16倍),使输送煤气时所需要的煤气管道直径、鼓风机的能力和功率都增大,是不经济的。
●在煤气冷却的过程中,不但有水汽冷凝,而且大部分焦油、萘也被分离出来。
部分硫化物、氰化物等腐蚀性介质也溶于冷凝液中,从而可减少对回收设备及管道的堵塞和腐蚀。
●此外在回收氮和苯族烃以前,对煤气进行初步净化还有利于氨的回收、改善硫铵质量和减少对循环洗油质量的影响。
近年来,在煤气的初冷过程中,也为此目的采取了一定的措施。
煤气的初步冷却分两步进行:
第一步是在集气管及桥管中用大量的循环氨水喷洒,使煤气冷却到82~86℃;第二步再在煤气初冷器中冷却到25~35℃(生产硫铵系统)或低于25℃(生产浓氨水系统)
第一节煤气在集气管内的冷却
一、煤气在集气管内冷却的机理
1.冷却的传热、传质机理
煤气在桥管和集气管内的冷却,是用表压为1.5~2.0公斤/厘米3的循环氨水通过喷头强烈喷洒。
当细雾状的氨水与煤气充分接触时,由于煤气温度很高而湿度又很低,所以煤气放出大量显热,氨水大量蒸发,快速进行着传热和传质过程。
传热过程取决于煤气与氨水的温度差。
因煤气的温度高于循环氨水的温度,所以热量就从煤气传给氨水,从而使煤气冷却。
传质过程的推动力是循环氨水液面上的水汽分压与煤气重水汽分压之差。
因为循环氨水液面上的水汽分压大于煤气中的水汽分压,所以氨水就部分蒸发,同时煤气温度急剧降低,以供给氨水蒸发所需的潜热。
,
煤气在集气管中冷却时所放出的大部分热量用于蒸发氨水(约占75~80%),其余的其余的热量消耗于使氨水升温(约占10~15%)和集气管的散热损失(约占10%左右)。
通过上述冷却过程,煤气温度由650~700℃降至82~86℃,同时有60%左右的焦油汽冷凝下来。
在实际生产上,煤气温度可冷却至高于其最后达到的露点温度1~3℃。
2.冷却的影响因素
煤气的冷却及所达到的露点温度同下列因素有关:
煤料的水分、进集气管前煤气的温度、循环氨水量和进口温度、氨水喷洒效果等。
其中以煤料水分的影响最大。
如一生产条件下,煤料水分每降低l%,露点温度可降低0.6~0.7℃。
显然,降低煤料水分对煤气在集气管和初冷器中的冷却都很重要。
由于煤气的冷却主要是靠氨水的蒸发,所以氨水喷洒的雾化程度较高,循环氨水的温度较高,氨水蒸发量较大,就能使煤气冷却的较好;反之则差。
3.集气管的操作指标
集气管技术操作的主要数据如下:
集气管前的煤气温度,℃650~700
离开集气管的煤气温度,℃82~86
循环氨水温度,℃72~78
离开集气管氨水温度,℃74~80
煤气露点,℃80~83
循环氨水量,米3/吨干煤5~6
蒸发的氨水量,%(占循环氨水量)2~3
冷凝焦油量,%(占煤气中焦油量)~60
由上述数据可见,煤气虽然已显著地冷却,但离开集气管的煤气仍未被水汽所饱和。
4.冷却介质的选择
集气管在正常操作过程中不用冷水喷洒,因冷水不易蒸发,冷却效果不好,且带入的矿物杂质会增加沥青的灰分。
此外由于水温很低,使集气管底部剧烈冷却,冷凝的焦油粘度增大,易使集气管堵塞。
进入集气管前的煤气露点温度同装入煤的水分含量有关,当装入煤总水分为8~11%肘,露点温度约为65~70℃。
为保证氨水蒸发的推动力,进口水温应高于煤气露点温度5~10℃。
所以采用72~78℃的循环氨水喷洒煤气。
这样能克服用冷水喷洒的缺点,并且由于氨水是碱性的,能中和焦油酸,保护煤气管道。
氨水又有润滑性,便于焦油流动,可以防止焦油因积聚而堵塞煤气管道。
5.循环氨水量
不同型式的炼焦炉所需的循环氨水量也有所不同,按经验确定的定额数值为:
对单集气管的焦炉,每吨干煤需5米3循环氨水;对双集气管的焦炉,需6米3循环氨水。
循环氨水量可通过对集气管进行物料平衡和热量恒算求得。
近年来,有些焦化厂采用高压循环氨水代替蒸汽喷射进行无烟装煤。
有些厂在采用预热煤炼焦时,设置了独立的氨水循环系统,用于专设的装炉集气管的喷洒,则它们的循环氨水量又各有不同。
第二节煤气的初冷
炼焦煤气由集气管沿吸煤气主管流向煤气初步冷却器。
吸煤气主管除将煤气由焦炉引向化产回收车间外,还起着空气冷却器的作用,但散失的热量不大,煤气温度仅降低1~3℃。
煤气在进人冷却器前的温度还相当高,且含有大量焦油汽和水汽,须在初步冷却器中进一步冷却到25~35℃,并将大部分焦油汽和水汽冷凝下来。
目前国内外广泛采用的煤气初步冷却方式有:
间接冷却、直接冷却和间冷直冷相结合三种。
上述三种方式各有优缺点,可因生产规模、工艺要求以及其他条件选择采用。
一、煤气的间接初冷
1.煤气间接初冷工艺流程
煤气间接初冷工艺流程如图所示。
该流程在我国得到广泛采用。
荒煤气与喷洒氨水冷凝焦油等沿吸煤气主管首先进入气液分离器,煤气与焦油、氨水、焦油渣等于此处分离。
分离下来的焦油、氨水和焦油渣一起进入焦油氨水澄清槽,经过澄清分成三层:
上层为氨水;中层为焦油;下层为焦油渣。
沉淀下来的焦油渣由刮板输送机连续刮送至漏斗处排出槽外。
焦油则通过液面调节器流至焦油中间槽,由此用泵送至焦油贮槽,经初步脱水后,再用泵送往焦油车间。
氨水由澄清槽的上部满流到氨水中间槽,再用循环氨水泵送回焦炉集气管喷洒以冷却荒煤气。
这部分氨水称为循环氨水。
经气液分离后的煤气进入数台并联的立管式间接初冷器内用水间接冷却。
煤气走管间,冷却水走管内。
从并联操作的各台初冷器出来的煤气温度是有差别的,汇集在一起后的煤气温度称为集合温度。
这个温度依生产工艺的不同而有不同的要求:
在生产硫铵系统中,要求集合温度低于35℃;在生产浓氨水系统中,则要求集合温度低于25℃。
随着煤气的初步冷却,煤气中的绝大部分焦油汽、大部分水汽和萘在初冷器中被冷凝下来,萘溶解于焦油中。
煤气中一定数量的氨、二氧化碳、硫化氢、氰化氢和其他组分则溶解于冷凝水中,形成冷凝氨水。
焦油和冷凝氨水的混合液称为冷凝液。
冷凝氨水中含有较多的挥发氨盐[
、
、
等],固定氨盐[
、
、(
、
等)含量较少。
循环氨水中则主要含有固定氨盐,在其单独循环时,固定氨盐含量可高达30~40克/升。
为了降低循环氨水中固定氨盐的含量,以减轻对焦油蒸馏设备的腐蚀和改善焦油的脱水和脱盐操作,目前多采用两种氨水混合的流程。
混合氨水的固定氨盐的含量可降至1.3~3.5克/升。
如图所示,冷凝液自流入中间槽,再用泵送入机械化氨水澄清槽,与循环氨水混合澄清分离。
分离后所得的剩余氨水送去脱酚和蒸氨。
由管式初冷器出来的煤气还含有1.5~2克/标米3的雾状焦油,被鼓风机抽送至电捕焦油器将其中绝大部分焦油雾除去后,再送至下一工序。
当冷却煤气用的冷却水为直流水时,冷却器后的热水直接排放。
如为循环水时。
则将温度约为45℃的热水送往凉水架冷却至25℃左右,再用初冷水泵送回初冷器循环使用。
上述煤气间接初冷流程适用于生产硫铵的工艺系统,当生产浓氨水时,为使初冷器后煤气的集合温度低于20℃,以减少煤气中焦油雾和萘的含量,宜采用两段初步冷却。
2.冷凝氨水和焦油的特点和用途
冷凝氨水的组成随煤气初步冷却的形式、冷却温度及氨水的产量不同而波动,在间接冷却时,冷凝液的平均组成(克/升)为:
全氨量:
8~12
挥发氨:
4~6
固定铵:
4~8
二氧化碳:
2~4
硫化氢:
1~3
酚:
1.2~2.5
吡啶盐基:
0.2~0.5
萘和轻油:
少量
目前,我国焦化厂均采用混合氨水系统,挥发氨含量为0.1~0.2%(1~2克/升),一般为1.3~1.5克/升。
在常压下,氨水略带淡黄色,有强烈的刺激气味,略呈碱性。
氨水中氨易挥发,加热时蒸发带走大量的潜热。
氨水主要作焦炉的循环氨水,在上升管和集气管处冷却煤气,将剩余氨水送去蒸馏,产生氨气。
氨气在饱和器经硫酸吸收后生产硫铵,并回收吡啶;送去脱酚可生产酚盐,也可以经蒸氨后生产浓氨水。
粗焦油颜色为黑色,密度为1.12~1.22克/厘米3之间(20~4℃)50℃时的比粘度约9~10°(恩式粘度),闪点为96~105℃,一般含氨水2~5%。
焦油本身用途并不大,一般仅作碳黑原料油、燃料油、涂料和防腐剂。
但若将焦油加工,可得轻油、酚油、萘油、洗油、一蒽油、二蒽油和沥青等窄馏分,再进一步加工精制,可获得众多的化学工业产品,可作医药、染料、塑料、合成纤维及国防工业等原料。
3.剩余氨水量的影响因素
在炼焦配煤中含8~10%的外在水分,另外在炼焦过程中,煤中所含的氧在高温下与氢化合生成约占干煤重量2~4%的化合水。
这两部分水分在炼焦过程中变成水蒸气随荒煤气一起逸出,经冷凝后,除补充氨水少量损失外,其余部分则为剩余氨水。
显然,剩余氨水量取决于配煤水分和化合水的数量以及煤气初冷后的集合温度(决定初冷后煤气的水气含量)。
4.集合温度的影响
如果集合温度偏高,可能带来的问题有:
●煤气中水汽含量增多,体积变大,造成鼓风机能力不够,影响煤气的正常输送。
●焦油汽的冷凝率降低,初冷器后煤气中焦油含量增多,如捕焦油器效率不高,将使氨的回收、洗苯、脱硫均受到影响。
●在初冷器内,煤气中的萘蒸汽在遇冷时,有相当部分呈细小薄片晶体析出,很难从高速的煤气中沉降下来,结果随煤气带走,所以煤气中的实际合萘量比在同温下萘汽的饱和含量要高1~2倍。
当集合温度偏高时,煤气中含萘量将更显著增大,这是因为:
①煤气中纯萘的蒸汽压随煤气温度的升高而有很大的增长。
②初冷器冷端得到的冷凝焦油中含萘量可达21~26%(当初冷器后煤气温度为31℃时),而全焦油量仅约8~10%。
由此可见,如冷却器后煤气温度偏高,则由于焦油冷凝率及萘在焦油中溶解度的降低,溶解于焦油中的萘量减少,随煤气带走的萘量就相应地增多了。
煤气含萘量高,将使煤气管道和设备堵塞,增加以后洗萘系统的负荷。
给洗氨洗苯带来困难。
由上述可见,在煤气初冷操作中,必须保证初冷器后集合温度不高于规定值,并尽可能地脱除煤气中的萘。
二、煤气的直接初冷
1,间接初冷的流程
煤气的直接初冷,是在直接冷却塔内,由煤气和冷却水直接接触传热而完成的。
我国一些小型焦化厂多采用直接初冷流程,如图所示。
由吸气主管来的82℃左右的荒煤气,经气液分离器进入并联的直接式木格填料初冷塔,用氨水喷洒冷却到28℃,然后由鼓风机送至捕焦油器捕除焦油雾后,再送至下一工序。
从气液分离器分离出来的循环氨水、焦油和焦油渣,经焦油盒分出焦油渣后,流入焦油氨水澄清池。
从澄清池出来的循环氨水,用泵送回集气管喷洒冷却煤气。
澄清池底部的焦油流入焦油池,然后用泵抽送到焦油槽,再送往焦油车间加工处理。
焦油盒底部的焦油渣由人工捞出。
初冷塔底部流出的喷洒氨水和冷凝液经水封槽进入初冷循环氨水澄清池,与洗氨塔来的氨水混合并进行焦油分离。
分离出来的焦油与上述焦油混合。
澄清后的氨水用泵送入喷淋式冷却器经冷却后,送至初冷塔循环使用。
剩余氨水即富氧水则送去蒸氨。
从初冷塔流出的氨水管路上引出支管至焦炉循环氨水澄清池,以补充焦炉循环氨水的蒸发损失。
国外有些大型焦化厂也采用煤气直接初冷流程。
在空喷塔内用经过冷却的氨水和澄清槽分离出来的焦油分段喷洒。
或用经过冷却的氨水焦油混合液喷洒。
这样在冷却煤气的同时,还可将煤气中所夹带的部分萘除去。
由初冷塔流出的氨水和焦油进入专用的焦油氨水澄清槽进行分离,澄清后的氨水供循环使用,并将多余部分送去加工。
2.直接初冷流程的优缺点
煤气直接初冷,不但冷却了煤气,而且具有净化煤气的良好效果。
生产实测数据表明,在直接初冷塔内,可以洗去进塔煤气中90%以上的焦油,80%左右的氨,60%以上的萘,以及约50%的硫化氢和氰化氢。
这对后面洗氨、洗苯过程及减少设备腐蚀,都是有好处的。
同煤气间接初冷相比,直接初冷还具有冷却效率较高、煤气压力损失较小、不易堵塞、以及建设投资和钢材耗用量较少等优点。
但也具有工艺流程较复杂、动力消耗较大、循环氨水冷却器易堵等缺点。
所以,目前在大型焦化厂已很少单独采用煤气直接初冷流程。
三、间冷直冷相结合的煤气初冷
1.、间冷直冷相结合的初冷流程
自集气管来的温度为82℃左右的荒煤气几乎是为水汽所饱和的。
水蒸汽热焓约占煤气总热焓的4%,故煤气在高温阶段冷却所放出的热量绝大部分为水汽冷凝热,冷却效率较高。
同时在温度较高时(高于52℃),萘不会凝结造成设备堵塞。
所以,煤气高温阶段宜采用间接冷却。
而在低温冷却阶段,由于煤气中水汽含量已大为减少,煤气层将限制水汽一煤气混合物的冷却,同时萘的凝结也易于造成堵塞。
所以,此阶段直采用冷却效率较高、不易堵塞,且能净化煤气的直接冷却。
因而,目前在国内外新建的大型焦化厂,趋向于采用间冷直冷相结合的煤气初冷流程。
如图所示,由集气管来的82℃左右的荒煤气经气液分离器分离出焦油、氨水后,进入横管式间接冷却器被冷却到50~55℃,再进入直冷空喷塔冷却到25~35℃。
在直冷空喷塔内,煤气由下向上流动,与分两段喷淋下来的氨水、焦油混合液密切接触而得到冷却。
聚集在塔底的喷洒液及冷凝液经沉淀析出其中的固体杂质后,用于循环喷洒的混合液经依封槽用泵送入螺旋换热器冷却到25℃左右,再压送至直冷空喷塔上、中两段喷洒。
相当于塔内生成的冷凝液量的部分混合液,由塔底导入机械化氨水澄清槽,与气液分离器下来的氨水、焦油及横管冷却器下来的冷凝液等一起混合进行分离。
澄清的氨水进入氨水槽后,用循环氨水泵送往焦炉喷洒。
剩余氨水经氨水贮槽送往脱酚与蒸氨装置。
初步澄清的焦油送至焦油分离槽除去焦油中的焦油渣及进一步脱除水分,然后经焦油中间槽转送入贮槽。
在采用两种氨水混合系统时,循环氨水中挥发氨的浓度相对增加,而循环氨水的温度又很高,因而氨的挥发损失将增大。
为了防止氨的挥发损失和减少污染,可采用封闭式的澄清槽,并设置洗涤塔以净化由槽内排出的气体。
直冷塔内喷洒用的洗涤液在冷却煤气的同时,还会吸收氨、硫化氢及萘等,并逐渐被萘饱和。
因此在洗涤液闭路循环系统中,采用螺旋板式冷却器来冷却循环洗涤液,可以减轻由于萘的沉积而造成的堵塞。
但洗涤液一经冷却,水对萘的溶解度即随之下降,一部分萘便呈固态析出,并和焦油一起沉积于换热面上,因而冷却器仍需经常清扫。
四、初冷过程中在操作方面应注意的事项
1)循环氨水泵的出口压力应保持在1.96×105Pa(2公斤/厘米2),氨水的温度应保持在72~78℃的范围,这样才能使氨水达到足够的雾化程度和焦炉煤气达到降温的效果。
2)在氨水郊游澄清槽内应注意氨水、焦油和焦油渣的分层情况,应做到分离出的氨水中不夹带焦油和少带浮油,分离出的焦油应不带焦油渣和少带氨水。
为此,氨水在澄清槽内的停留时间应不少于20分钟,液面不得忽高忽低,有条件时应连续压油。
3)为了使煤气初冷器正常工作,应经常注意循环氨水的质量和循环氨水泵的压力,力求入煤气初冷器的煤气温度较低。
与此同时,应保证入初冷器的冷却水有较稳定的水量和较低的温度,一般要求进水温度为25℃。
为此,应经常检查凉水架的和通风情况。
在夏天时,可补充一部分低温水,以保证进水温度的要求。
为了保证出初冷器的煤气达到25~35℃,除了使入口煤气和进水温度较低外,还应定期检查清扫冷却管的外壁,保持冷却管的传热效果,或改善冷却水的水质,防止在管内壁上结水垢。
第三节煤气冷却设备
一、传热原理及设备简介
1.传热的概念
传热,就是热的传递,是自然界和工程技术领域中极普遍的一种传递过程,化工生产中用的极为广泛,焦化厂中应用的也相当广泛。
例如:
焦炉蓄热室中空气和烟气的换热,煤气的初冷、粗苯工段中为达到工艺要求所设置的换热器,如:
贫油冷却器、贫富油换热器、分缩器等都是依据的传热的原理。
传热有三种基本方式:
热传导、热对流、热辐射,通常是两种或三种传热方式的综合使用。
2.两种流体热交换的基本方式
两种流体实现热交换的方式有三种:
1)直接接触式传热
直接接触式传热的特点是冷、热两流体在传热器中以直接混合的方式进行热量交换,故也称混合式换热。
这种换热方式对于在工艺上允许两种流体相互混合的情况是比较方便和有效的,其所用的设备结构也比较简单,常用于气体的冷却或水蒸气的冷凝。
直接接触换热机理比较复杂,在此过程中在进行传热的同时往往伴随传质过程。
2)蓄热式换热
蓄热式换热器是由热容量较大的蓄热室构成。
室中充填耐火砖作为填料,当冷、热流体交替的通过同一室时,就可以通过蓄热室的填料将热流体的热量传递给冷流体,达到两流体换热的目的,蓄热式换热器通常由两个蓄热室交替使用,这类换热器结构简单,能耐高温,常用于高温气体换热。
其缺点是设备体积大,而且两种流体在蓄热室内交替时难免有一定程度的混合。
例如焦炉的蓄热室。
3)间壁式换热
间壁式换热的特点是冷、热流体被一固体隔开,分别在壁的两侧流动,不相混合,通过固体壁进行热量传递。
其传热过程可分为三步:
热流体将热量传给固体壁面(对流传热),热量从壁的热侧传到冷侧(热传导),热量从壁的冷侧面传给冷流体(对流传热),壁的面积称为传热面,是间壁式换热器的基本尺寸。
化工生产中最常遇到的换热过程是间壁式换热。
3.典型的间壁式换热器及其传热过程
换热器是实现换热过程的基本设备,简单介绍典型的换热器。
1)套管式换热器
套管式换热器是由两种直径大小不同的直管组成的同心管,一种流体在内管中流动,另一种流体在内、外两壁间的环隙中流动,通过内管管壁进行热量交换。
因此,内管壁的表面积即为传热面积。
2)列管式换热器
列管式换热器由壳体、管束、管板和封头等部件组成。
一种流体由封头的进口管进入器内,流经封头与管板的空间分配至各管内(称为管程)。
通过管束后,从另一端封头的出口流出换热器。
另一种流体则由壳体的接管流入,在壳体与管束间的空隙流过(称为壳程),从壳体的另一端接管流出。
壳体内往往安装若干块与管束相垂直的折流挡板。
换热器中流体在管束内只通过一次,称为单程列管式换热器。
若在换热器封头内设置隔板,将管束的全部管子平均分隔成若干组,流体每次只通过一组管子,然后折回进入另一组管子,如此往复多次,最后从封头接管流出换热器。
这种换热器称为多管程列管式换热器。
列管式换热器的换热面积为管束管壁的全部表面积。
4.传热速率
在换热器中传热的快慢是用传热速率来表示的。
传热速率(又称为热流量)Q是指单位时间内通过传热面的热量,单位为w,热通量(又称为热流密度或传热速度)q,是指单位传热面积的传热速率。
单位为w/m2
传热速率与热通量的关系为:
和其它传递过程相似,
传热温差以
表示,热阻通常以R或r表示,
5.间壁式换热器传热速率的计算
间壁式换热器的传热基本方程为:
式中:
K——换热器的平均传热系数,w/
;
——换热器的间壁两侧流体的平均温差,℃;
S——换热器的传热面积,
。
、
——管外的对流传热系数,反映了对流传热的快慢,对流传热系数大,表示传热快。
流体在管内的流速越快,对流传热系数越大。
、
——管内外的污垢热阻
——壁面的导热系数
为此,要提高换热器的传热速率,应提高换热器的传热系数,单位体积的传热面积,为此,换热器使用一段时间后,要进行清洗,清除污垢。
6.间壁式换热器的类型
间壁式换热器主要有管式、板式和翅片式三种类型
1)沉浸式换热器
这种换热器是将金属管弯绕成各种与容器想适应的形状(多盘成蛇形,常称蛇管),并沉浸在容器内的液体中。
蛇管内、外的两种流体进行热量交换。
沉浸式换热器的优点是结构简单、价格低廉,能承受高压,可用耐腐蚀材料制造;缺点是容器内液体湍动程度低,管外对流传热系数小。
为提高传热系数,可在容器内安装搅拌器。
2)喷淋式换热器
喷淋式换热器也为蛇管式换热器,如图所示,多用作冷却器。
这种换热器是将蛇管成行地固定在钢架上,热流体在管内流动,自最下管进入,由最上管流出。
冷水由最上面的淋水管流下,均匀地分布在蛇管上,并沿其两侧逐排流经下面的管子表面,最后流入水槽而排出,冷水在各排管表面上流过时,与管内流体进行热交换。
这种换热器的管外形成一层湍动程度较高的液膜,因而管外对流传热系数较大。
另外,喷淋式换热器常放置在室外空气流通处,冷却水在空气中汽化时也带走一部分热量,提高了冷却效果。
因此,和沉浸式相比,喷淋式换热器的传热效果要好得多。
同时它还便于检修和清洗等优点。
其缺点是喷淋不易均匀。
3)列管式换热器
列管式(又称管式)换热器的应用有着悠久的历史,而且至今仍是工业上应用最为广泛的一种换热设备。
它主要的优点是单位体积所具有的传热面积大,结构紧凑、紧固,传热效果好。
而且能用多种材料制造,故适用性较强,操作弹性较大,尤其在高温、高压和大型装置中多采用列管式换热器。
在列管式换热器中,由于管内外流体温度不同,管束和壳体的温度也不同,因此它们的热膨胀程度也有差别。
若两流体的温差较大,就可能由于热应力而引起设备变形,管子弯曲,甚至破裂或从管板上松脱。
因此,当两流体的温差超过50℃时,就应采用热补偿的措施。
根据热补偿方法的不同,列管式换热器分为以下几种主要形式:
(1)固定管板式
固定管板式的两端管板和壳体制成一体。
因此它具有结构简单和成本低的优点。
但是壳程清洗和检修困难,要求壳程流体必须是洁净而不易结垢的物料。
当两流体的温差较大时,应考虑热补偿。
图为具有补偿圈(或称膨胀节)的固定管板式换热器,即在外壳的适当部位焊上一个补偿圈,当外壳和管束热膨胀不同时,补偿圈发生弹性变形(拉伸或压缩),以适应外壳和管束不同的热膨胀程度。
这种补偿方法简单,但不宜应用两流体温差过大(应不大于70℃)和壳程流体压强过高的场合。
(2)浮头式换热器
浮头式换热器的结构原理如图所示,其特点是有一端管板不与外壳连为一体,可以沿轴向自由浮动。
这种结构不但完全消除了热应力的影响,且由于固定端的管板以法兰与壳体连接,整个管束可以从壳体中抽出,因此便于清洗和检修。
故浮头式换热器应用较为普遍,但它的结构比较复杂,造价较高。
(3)U型管式换热器
U型管式换热器每根管子都弯成U型,如图。
进出口分别安装在同一管板的两侧,封头用隔板分成两室。
这样,每根管子可以自由伸缩。
而与其他管子和壳体均无关。
这种换热器结构比浮头式简单,重量轻,但管程不易清洗,只适用于洁净而不易结垢的流体,如高压气体的换热。
以上几种列管式换热器,都有系列标准,可供选用。
规格型号中通常标明型式、壳体直径、传热面积、能承受的压强和管程数等,例如FB500-65-25-2换热器,FB表示浮头式B型,换热管为φ25×2.5(mm),正方形排列,壳体公称直径500mm,公称传热面积65m2,公称压强为2.5Mpa。
管程数为2。
4.板式换热器
1)螺旋板式换热器
如图所示,螺旋板式换热器是由两张间隔一定的平行薄金属板卷制而成,在其内部形成两个同心的螺旋形通道。
换热器中央设有隔板,将螺旋形通道隔开,两板之间焊有定距柱以维持通道间距。
在螺旋板两侧焊有盖板。
冷热流体分别通过两条通道,在器内逆流流动,通过薄板进行换热。
螺旋板式换热器的优点:
(1)传热系数高:
螺旋流道中的流体由于惯性离心力的作用和定距柱的干扰,在较低