管壳式换热器教案.docx
《管壳式换热器教案.docx》由会员分享,可在线阅读,更多相关《管壳式换热器教案.docx(28页珍藏版)》请在冰豆网上搜索。
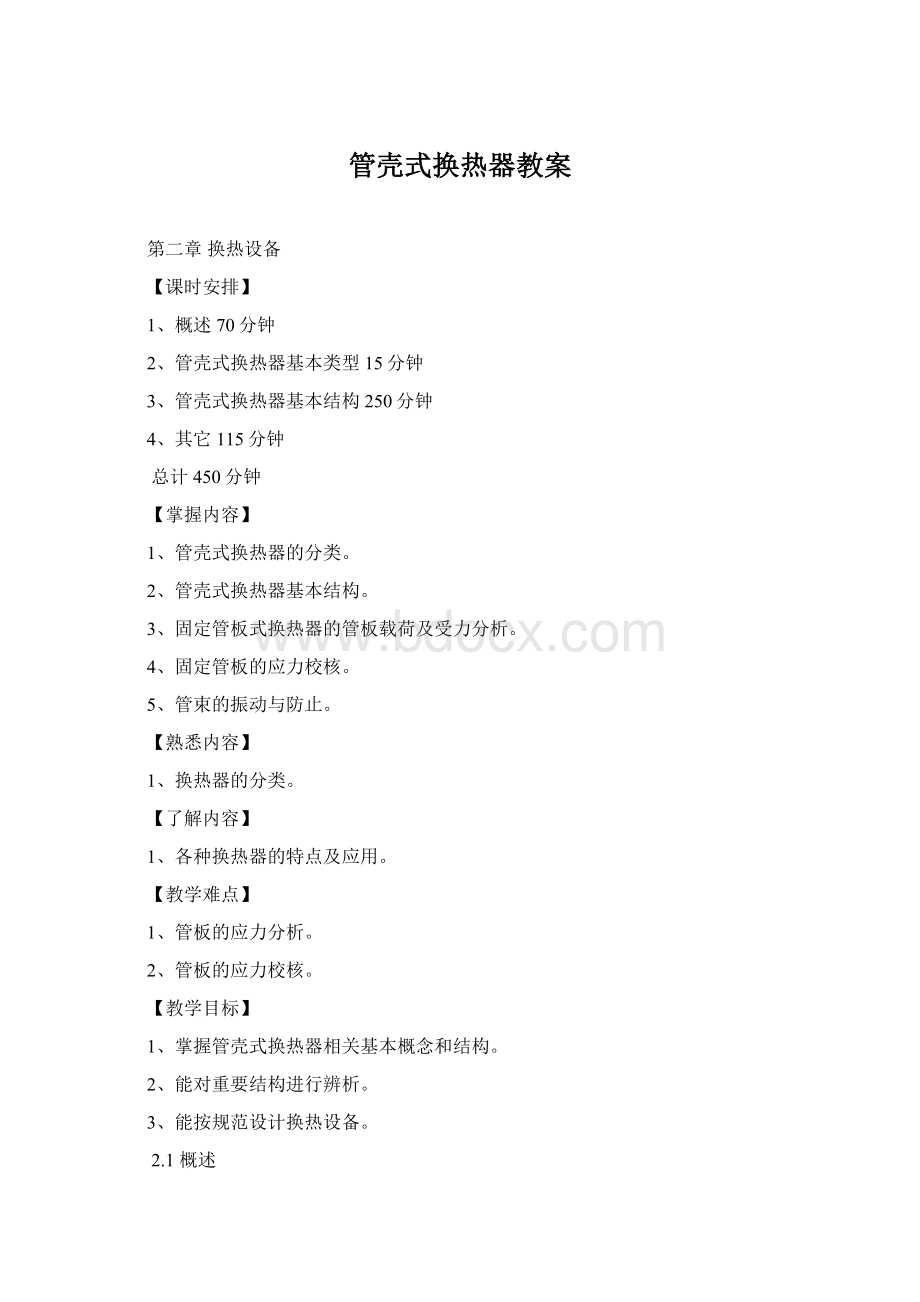
管壳式换热器教案
第二章换热设备
【课时安排】
1、概述70分钟
2、管壳式换热器基本类型15分钟
3、管壳式换热器基本结构250分钟
4、其它115分钟
总计450分钟
【掌握内容】
1、管壳式换热器的分类。
2、管壳式换热器基本结构。
3、固定管板式换热器的管板载荷及受力分析。
4、固定管板的应力校核。
5、管束的振动与防止。
【熟悉内容】
1、换热器的分类。
【了解内容】
1、各种换热器的特点及应用。
【教学难点】
1、管板的应力分析。
2、管板的应力校核。
【教学目标】
1、掌握管壳式换热器相关基本概念和结构。
2、能对重要结构进行辨析。
3、能按规范设计换热设备。
2.1概述
【教学内容】
一.换热器的应用
二.换热器的分类及特点
三.换热器的选型
【授课时间】70分钟
【教学重点】基本概念的建立
【教学难点】各种换热器的区别
【教学目标】了解换热器的特点及应用
【教学手段】课堂讲授,辅以设备挂图。
25
【教学过程】
2.1.1换热设备的应用
换热设备:
使热量从热流体传递到冷流体的设备。
化工厂:
换热设备的投资约占总投资的10%~20%;
炼油厂:
换热设备的投资约占总投资的35%~40%。
2.1.2换热器的分类及特点
2.1.2.1按作用原理或传热方式分类
一.直接接触式换热器(混合式换热器)
利用冷、热流体直接接触与混合的作用进行热量的交换。
如:
冷却塔等。
二.蓄热式换热器(回热式换热器)
借助于固体构成的蓄热体与热流体和冷流体交替接触,把热量从热流体传递给冷流体的换热器。
两种流体有少量混合。
如:
回转式空气预热器等。
三.间壁式换热器(表面式换热器)
利用间壁(固体表面)将进行热交换的冷、热两种流体隔开互不接触。
热量由热流体通过间壁传递给冷流体的换热器。
如:
管壳式换热器等。
四.中间载热体式换热器
把两个间壁式换热器由在其中循环的载热体连接起来的换热器。
载热体在高温流体和低温流体之间循环。
如:
热管式换热器等。
2.1.2.2间壁式换热器分类
一.分类
二.特点
1.管式换热器
通过管子壁面进行传热的换热器。
优点:
结构坚固、可靠性高、适应性广、易于制造,能承受较高的温度和压力。
缺点:
传热效率、结构紧凑性及金属的消耗量等均不如高效紧凑式换热器。
2.板面式换热器
通过板面进行传热的换热器。
优点:
传热性比管式换热器优越,流体在较低流速下即可达到湍流,强化了传热。
制造成本低,结构紧凑、使用灵活、清洗和维修方便、能精确控制换热温度等。
缺点:
a.密封周边太长,不易密封,渗漏的可能性大;
26
b.承压能力低,耐压性差;
c.使用温度受密封垫片材料耐温性能的限制不宜过高;
沉浸式蛇管
蛇管式换热器
喷淋式蛇管
套管式换热器
管式换热器
管壳式换热器
缠绕管式换热器
螺旋板式换热器
板式换热器
间壁式换热器
板面式换热器板翅式换热器
板壳式换热器
伞板式换热器
石墨换热器
其它型式换热器聚四氟乙烯换热器
热管换热器
3.其它型式换热器
为满足工艺特殊要求,具有特殊结构的换热器。
2.1.3换热器选型
需要考虑的因素:
1.流体的性质;
27
2.压力、温度、允许的压力降;
3.清洗、维修的要求;
4.材料、价格;
5.使用寿命等。
2.2管壳式换热器
【教学内容】
一.管壳式换热器的基本类型
二.管壳式换热器结构
三.管板设计
四.膨胀节设计
五.管束振动和防止
【授课时间】330分钟
【教学重点】管壳式换热器结构的建立
【教学难点】管板的应力分析
【教学目标】熟悉管壳式换热器的结构及应用
【教学手段】课堂讲授,辅以设备挂图。
【教学过程】
2.2.1基本类型
可分为固定管板式、浮头式、U形管式、填料函式和釜式重沸器五类,如图2.1所示。
一.固定管板式
固定管板式换热器的典型结构如图2.1(a)所示。
结构特点:
管束连接在管板上,管板与壳体焊接。
优点:
结构简单、紧凑、能承受较高的压力,造价低,管程清洗方便,管子损坏时易于堵管或更换;
缺点:
是当管束与壳体的壁温或材料的线膨胀系数相差较大时,壳体和管束中将产生较大的热应力。
适用范围:
1.适用于壳侧介质清洁且不易结垢并能进行清洗;
2.管、壳程两侧温差不大或温差较大但壳侧压力不高的场合。
二.浮头式换热器
浮头式换热器的典型结构见图2.1(b)。
结构特点:
两端管板中只有一端与壳体固定,另一端可相对壳体自由移动,称为浮头。
28
浮头的组成:
浮头由浮头管板、钩圈和浮头端盖组成。
优点:
管间和管内清洗方便,不会产生热应力。
缺点:
结构复杂,造价比固定管板式换热器高,设备笨重,材料消耗量大,且浮头端盖在操作中无法检查,制造时对密封要求较高。
适用范围:
适用于壳体和管束之间壁温差较大或壳程介质易结垢的场合。
三.U形管式换热器
U形管式换热器的典型结构如图2.1(c)所示。
结构特点:
只有一块管板,管束由多根U形管组成,管的两端固定在同一块管板上,管子可自由伸缩。
优点:
结构比较简单、价格便宜,承压能力强,不会产生热应力。
缺点:
由于受弯管曲率半径的限制,其换热管排布较少,管束最内层管间距较大,管板的利用率较低,壳程流体易形成短路,对传热不利。
当管子泄漏损坏时,内层换热管坏了不能更换,只能堵死。
适用范围:
适用于管、壳壁温差较大或壳程介质易结垢需要清洗,又不适宜采用浮头式和固定管板式的场合。
特别适用于管内走清洁而不易结垢的高温、高压、腐蚀性大的物料。
四.填料函式换热器
填料函式换热器结构如图2.1(d)、(e)所示。
结构特点:
与浮头式换热器相类似,浮头部分露在壳体以外,在浮头与壳体的滑动接触面处采用填料函式密封结构。
优点:
比浮头式换热器简单,加工制造方便,节省材料,造价较低廉,管束可抽出,清洗,维修方便。
缺点:
填料处易产生泄漏,不适用于易挥发、易燃、易爆、有毒及贵重介质,使用温度也受填料的限制。
适用范围:
适用于4MPa以下的工作条件。
五.釜式重沸器
釜式重沸器的结构如图2.1(f)所示。
结构特点:
其管束可以为浮头式、U形管式和固定管板式结构,它具有浮头式、U形管式换热器的特性。
在结构上与其他换热器不同之处在于壳体上部设置一个蒸发空间,蒸发空间的大小由产气量和所要求的蒸气品质所决定。
此种换热器和浮头式、U形管式换热器一样,清洗维修方便,可处理不清洁、易结垢的介质,并能承受高温、高压。
2.2.2、管壳式换热器的结构
管程:
流体流经换热管内的通道及与其相贯通部分。
壳程:
流体流经换热管外的通道及与其相贯通部分。
29
(a)固定管板式换热器;(b)浮头式换热器;(c)U形管式换热器;
(d)填料函双壳层换热器;(e)填料函分流式换热器;(f)釜式重沸器
图2.1管壳式换热器的主要型式
30
2.2.2.1管程结构
一.换热管
1.换热管型式
光管、翅片管、螺旋槽管、螺纹管等。
当管内外两侧给热系数相差较大时,翅片管的翅片应布置在给热系数低的一侧。
2.换热管尺寸(常用)
无缝钢管:
φ19×2φ25×2.5φ38×2.5
不锈钢管:
φ25×2φ38×2.5
标准管长为:
10、1.5、2.0、2.5、3.0、4.5、6.0、7.5、9.0、12.0m等。
外径范围:
φ10~φ57
3.换热管材料
黑金属:
碳素钢、低合金钢、不锈钢等。
有色金属:
铜、铜镍合金、铝合金、钛合金等。
非金属:
石墨、陶瓷、聚四氟乙烯等。
4.换热管排列形式及中心距
换热管在管板上的排列形式:
正三角形、正方形、转角正三角形、转角正方形。
如图2.2所示,
在同样的管板面积上正三角形排列的管数最多,故用得最为普遍,但管外不易清洗。
为便于管外清洗,可以采用正方形或转角正方形排列的管束。
图2.2换热管排列型式
换热管中心距一般不小于1.25倍的换热管外径。
常用的换热管中心距见表2-1。
表2-1常用换热管中心距mm
换热管外径do
12
14
19
25
32
38
45
57
换热管中心距
16
19
25
32
40
48
57
72
31
二.管板
作用:
a.用来排布换热管
b.分隔管程和壳程的流体,避免冷、热流体混合。
c.同时受管程、壳程压力和温度的作用。
1.管板材料
选择管板材料,除力学性能外,还应考虑管程和壳程流体的腐蚀性,以及管板和换热管之间的电位差对腐蚀的影响。
工程上常用材料:
a.碳素钢
b.低合金钢钢板、锻件
c.不锈钢
d.不锈钢+钢
e.钛+钢复合板
f.铜+钢
g.堆焊衬里。
2.管板结构
在满足强度的前提下,应尽量减少管板厚度。
薄管板一般为:
8~20mm。
形状主要有:
平面形、椭圆形、碟形、球形、挠性薄管板等。
最为常用的是平面形薄管板。
图2.3薄管板结构形式
图2.4椭圆形管板图2.5双管板结构
32
图2.3所示为用于固定管板式换热器中的薄管板四种结构形式。
图2.4所示为椭圆形管板。
图2.5所示为双管板结构
三.管箱
管箱位于管壳式换热器的两端。
作用:
把从管道输送来的流体均匀地分布到各换热管和把管内流体汇集在一起送出换热器。
在多管程换热器中,管箱还起改变流体流向的作用。
图2.6管箱结构形式
管箱的结构形式主要以换热器是否需要清洗或管束是否需要分程等因素来决定。
图2.6为管箱的几种结构形式。
图2.6(a)的管箱结构适用于较清洁的介质情况。
因为在检查及清洗管子时,必须将连接管道一起拆下,很不方便。
图2.6(b)为在管箱上装箱盖,将盖拆除后(不需拆除连接管),就可检查及清洗管子,但其缺点是用材较多。
图2.6(c)形式是将管箱与管板焊成一体,从结构上看,可以完全避免在管板密封处的泄漏,但管箱不能单独拆下,检修、清理不方便,所以在实际使用中很少采用。
图2.6(d)为一种多程隔板的安置形式。
四.管束分程
管程:
管内流动的流体从管子的一端流到另一端为一个管程。
在管壳式换热器中,最简单常用的是单管程的换热器。
也可采用多管程结构。
从制造、安装、操作等角度考虑,偶数管程有更多的方便之处,最常用的程数为2、4、6。
★注意:
管束分程可采用多种不同的组合方式,对于每一程中的管数应大致相等,且程与程之间温度相差不宜过大,温差以不超过20℃左右为宜,最大不超过28℃。
否则在管束与管板中将产生很大的热应力
表2-2列出了1~6程的几种管束分程布置形式。
33
表2-2管束分程布置图
对于4程的分法,有平行和工字形两种,一般为了接管方便,选用平行分法较合适,同时平行分法亦可使管箱内残液放尽。
工字形排列法的优点是比平行法密封线短,且可排列更多的管子。
五.换热管与管板的连接
换热管与管板的连接是管壳式换热器的关键部位,是换热器事故率最多的部位。
管子与管板的连接方法:
胀接、焊接、胀焊并用。
①胀接
保证换热管与管板连接的密封性能及抗拉脱强度的胀接。
管孔结构示于图2.7。
一般采用光孔,管端伸出2~3mm。
胀接时,管端翻边成圆锥形,能提高管子的抗拉脱能力。
当管子承受压应力时,翻边可取消。
图2.7胀接的型式
带槽孔的结构用于抗拉脱能力与密封性要求高的场合。
管孔中开的环形小槽深为0.4~0.5mm,管子材料被胀挤进槽内,可防止介质外泄。
管板厚度小于30mm时,槽数为1,厚度大于30mm时,槽数为2。
方法:
机械滚胀法是应用最早的胀接方法。
它靠电动或风动等动力使胀管器的锥形心轴旋转并挤入管内,迫使管子扩张并产生塑性变形,而管板只产生弹性变形。
取出胀管器的心轴后,管板弹性恢复,使管板与管子间产生一定的挤压力而贴合在一起。
除机械滚
34
胀法外,近年来出现了液压胀接、橡胶胀接和爆炸胀接法。
液压胀接法是利用液体压力使换热管产生塑性变形。
橡胶胀接是利用机械压力使特种橡胶长度缩短,直径增大,从而带动换热管扩张达到胀接的目的。
爆炸胀接是利用炸药在换热管内有效长度内爆炸,使换热管贴紧管板孔而达到胀接目的。
这些胀接方法具有生产率高,劳动强度低,密封性能好等特点。
适用范围:
胀接主要适用于设计压力小于等于4.0MPa;设计温度小于等于300℃;操作中无剧烈振动、无过大温度波动及无明显应力腐蚀等场合。
②焊接
保证换热管与管板连接的密封性能及抗拉脱强度的焊接。
结构形式见图2.8。
由于管孔不需要开槽,且对管孔的粗糙度要求不高,管子端部不需要退火和磨光,因此制造加工简单。
焊接结构强度高,抗拉脱力强。
在高温高压下也能保证连接处的密封性能和抗拉脱能力。
管子焊接处如有渗漏可以补焊或利用专用工具拆卸后予以更换。
图2.8焊接管孔结构
当换热管与管板连接处焊接之后,管板与管子中存在的残余热应力与应力集中,在运行时可能引起应力腐蚀与疲劳。
此外,管子与管板孔之间的间隙中存在的不流动的液体与间隙外的液体有着浓度上的差别,还容易产生缝隙腐蚀。
适用范围:
除有较大振动及有缝隙腐蚀的场合,只要材料可焊性好,焊接可用于其他任何场合。
管子与薄管板的连接应采用焊接方法。
③胀焊并用
胀接与焊接方法都有各自的优点与缺点,在有些情况下,例如高温、高压换热器管子与管板的连接处,在操作中受到反复热变形、热冲击、
35
腐蚀及介质压力的作用,工作环境极其苛刻,很容易发生破坏。
无论单独采用焊接或是胀接都难以解决问题。
要是采用胀焊并用的方法,不仅能改善连接处的抗疲劳性能,而且还可消除应力腐蚀和缝隙腐蚀,提高使用寿命。
因此目前胀焊并用方法已得到比较广泛的应用。
胀焊并用的方法:
从加工工艺过程来看,主要有强度胀+密封焊、强度焊+贴胀、强度焊+强度胀等几种形式。
“密封焊”:
是指保证换热管与管板连接密封性能的焊接,不保证强度;
“贴胀”:
是指为消除换热管与管孔之间缝隙并不承担拉脱力的轻度胀接。
★如强度胀与密封焊相结合,则胀接承受拉脱力,焊接保证紧密性。
如强度焊与贴胀相结合,则焊接承受拉脱力,胀接消除管子与管板间的间隙。
至于胀、焊的先后顺序,虽无统一规定,但一般认为以先焊后胀为宜。
因为当采用胀管器胀管时需用润滑油,胀后难以洗净,在焊接时存在于缝隙中的油污在高温下生成气体从焊面逸出,导致焊缝产生气孔,严重影响焊缝的质量。
适用范围:
胀焊并用主要用于密封性能要求较高;承受振动和疲劳载荷;有缝隙腐蚀;需采用复合管板等的场合。
2.2.2.2、壳程结构
壳程主要由壳体、折流板或折流杆、支承板、纵向隔板、拉杆、防冲挡板、防短路结构等元件组成。
一、壳体
壳体一般是一个圆筒,在壳壁上焊有接管,供壳程流体进入和排出之用。
为防止进口流体直接冲击管束而造成管子的侵蚀和振动,在壳程进口接管处常装有防冲挡板,见图2.9。
当壳体法兰采用高颈法兰或壳程进出口接管直径较大或采用活动管板时,壳程进出口接管距管板较远,流体停滞区过大;靠近两端管板的传热面积利用率很低。
为克服这一缺点,可采用导流筒结构,见图2.10。
导流筒除可减小流体停滞区,改善两端流体的分布,增加换热管的有效换热长度,提高传热效率外,还起防冲挡板的作用,保护管束免受冲击。
防冲挡板或导流筒的设置条件:
1.若进口管流体ρυ2值为下列值时设防冲挡板或导流筒
①非腐蚀、非磨蚀的单相流体ρυ2>2230kg/ms2;
②其他液体、包括沸点下的液体ρυ2>740kg/ms2;
2.有腐蚀、磨蚀的介质设防冲挡板;
3.接管距管板较远设导流筒,减小流体停滞区,增加换热管的有效
36
换热长度。
ρ—密度
υ—流速
导流筒:
减小流体停滞区,改善两端流体的分布,增加换热管的有效换热长度,提高换热率,并起防冲挡板的作用。
图2.9防冲挡板
图2.10导流筒结构
二、折流板
设置折流板的目的:
是为了提高壳程流体的流速,增加湍动程度,并使壳程流体垂直冲刷管束,以改善传热,增大壳程流体的传热系数,同时减少结垢。
在卧式换热器中,折流板还起支撑管束的作用。
常用的折流板形式有弓形和圆盘-圆环形两种。
其中弓形折流板有单弓形、双弓形和三弓形三种。
各种形式的折流板见图2.11所示。
根据需要也可采用其他形式的折流板。
★弓形折流板缺口高度应使流体通过缺口时与横向流过管束时的流速相近。
缺口大小用切去的弓形弦高占壳体内直径的百分比来表示。
如单弓形折流板,缺口弦高一般取O.20~0.45倍的壳体内直径,最常用的是0.25倍壳体内直径。
对于卧式换热器,壳程为单相清洁液体时,折流板缺口应水平上下
37
布置。
若气体中含有少量液体时,则在缺口朝上的折流板最低处开设通液口,见图2.12(a);若液体中含有少量气体,则应在缺口朝下的折流
图2.11折流板形式
图2.12折流板缺口布置
板最高处开通气口,如图2.12(b)。
卧式换热器的壳程介质为气液相共存或液体中含有固体颗粒时,折流板缺口应垂直左右布置,并在折流板最低处开通液口,如图2.12(c)。
★折流板一般应按等间距布置,管束两端的折流板应尽量靠近壳程进、出口接管。
折流板的最小间距应不小于壳体内直径的1/5,且不小于50mm;最大间距应不大于壳体内直径。
折流板上管孔与换热管之间的间隙以及折流板与壳体内壁之间的间隙应合乎要求,间隙过大,泄漏严重,对传热不利,还易引起振动;间隙过小,安装困难。
从传热角度考虑,有些换热器(如冷凝器)是不需要设置折流板的。
但是为了增加换热管的刚度,防止产生过大的挠度或引起管子振动,当
38
换热器无支撑跨距超过了标准中的规定值时,必须设置一定数量的支持板,其形状与尺寸均按折流板规定来处理。
图2.13拉杆结构
折流板与支持板一般用拉杆和定距管连接在一起,如图2.13(a)所示。
拉杆数不少于4根,每个折流板不少于3个支点。
当换热管外径小于或等于14mm时,采用折流板与拉杆点焊在一起而不用定距管,如图2.13(b)所示。
在大直径的换热器中,如折流板的间距较大,流体绕到折流板背后接近壳体处,会有一部分流体停滞起来,形成了对传热不利的“死区”。
为了消除这个弊病,宜采用多弓形折流板。
如双弓形折流板,因流体分为两股流动,在折流板之间的流速相同时,其间距只有单弓形的一半。
不仅减少了传热死区,而且提高了传热效率。
三、折流杆
图2.14折流杆结构
39
目的:
装有折流板的管壳式换热器存在着影响传热的死区,流体阻力大,且易发生换热管振动与破坏。
为了解决传统折流板换热器中换热管与折流板的切割破坏和流体诱导振动,并且强化传热提高传热效率,近年来开发了一种新型的管束支撑结构——折流杆支撑结构。
结构:
由折流圈和焊在折流圈上的支撑杆(杆可以水平、垂直或其他角度)所组成。
折流圈可由棒材或板材加工而成,支撑杆可由圆钢或扁钢制成。
一般4块折流圈为一组,如图2.14所示,也可采用2块折流圈为一组。
支撑杆的直径等于或小于管子之间的间隙。
因而能牢固地将换热管支撑住,提高管束的刚性。
四、防短路结构
为了防止壳程流体在某些区域发生短路,降低传热效率,需要采用防短路结构。
常用的防短路结构主要有旁路挡板、挡管(或称假管)和中间挡板。
①旁路挡板
为了防止壳程边缘介质短路而降低传热效率,需增设旁路挡板,以迫使壳程流体通过管束与管程流体进行换热。
旁路挡板可用钢板或扁钢制成,其厚度一般与折流板相同。
旁路挡板嵌入折流板槽内,并与折流
板焊接,如图2.15所示。
图2.15旁路挡板结构
通常当壳体公称直径DN≤500mm时,增设一对旁路挡板;DN=500mm时,增设二对旁路挡板;DN≥1000mm时,增设三对旁路挡板。
②挡管
当换热器采用多管程时,为了安排管箱分程隔板,在管中心(或在每程隔板中心的管间)不排列换热管,导致管间短路,影响传热效率。
为此,在换热器分程隔板槽背面两管板之间设置两端堵死的管子,即挡管,如图2.16所示。
挡管一般与换热管的规格相同,可与折流板点焊固定,也可用拉杆
40
(带定距管或不带定距管)代替。
挡管应每隔3~4排换热管设置一根,但不应设置在折流板缺口处。
图2.16挡管结构
③中间挡板
在U形管式换热器中,U形管束中心部分存在较大间隙,流体易走短路而影响传热效率。
为此在U形管束的中间通道处设置中间挡板。
中间挡板一般与折流板点焊固定,如图2.17所示。
图2.17中间挡板
通常当壳体公称直径DN≤500mm时,增设一块挡板;DN=500mm时,增设二块挡板;DN≥1000mm时,增设三块挡板。
中间挡板的数量不宜多于4块。
五、壳程分程
根据工艺设计要求,或为增大壳程流体传热系数,可将壳程分程。
在图2.18中列出了几种代号的壳程型式。
图2.18(a)为E型,是最普通的一种,壳程是单程的,管程可为单程,也可为多程。
为了增大平均温度差提高传热效率,对于二管程的换热器,可采用图2.18(b)所示的F型,在壳体中装入了一块平行于管子轴线方向的纵向隔板,成为二壳程的换热器,流体按逆流方式进行热交换。
图2.18(c)为G型,也属二壳程的换热器,纵向隔板从管板的一端移开使壳程流体得以分流。
壳体上的进、出口接管对称地分置于壳体的两侧且放在中央部位。
壳程中流体的压力降与E型的相同,但在传热
41
面积与流量相同的情况下,具有更高的热效率。
G型壳体也称为分流壳体。
壳程中可通入单相流体,也可通入有相变的流体。
如用作水平的热虹吸式再沸器,壳程中的纵向隔板起着防止轻组分的闪蒸与增强混合的作用。
图2.18(d)为H型。
与G型相似,同属二壳程的换热器,但进口接管、出口接管与纵向隔板均多一倍,故又称双分流壳体。
G型与H型两种壳体都可用于以压力降作为控制因素的换热器中,且有利于降低壳程流体的压力降。
尽管在工业中已成功地制造出六壳程的管壳式换热器,但考虑到制造方面的困难,一般的设计,壳程数很少超过2。
如有必要,可通过增加串联台数的办法来解决。
★应该指出,在管外空间设置了垂直于管子轴线的折流板后,不能把换热器看成是多壳程的,实际上它仍属单壳程的范围。
图2.18换热器的壳程型式
2.2.3管板设计
管板是管壳式换热器的主要部件之一,往往成为整台设备生产的决定性因素。
它和换热管、壳体、管箱、法兰等连接构成一个复杂的弹性体系,故设计时进行了各种假设:
★1.将管板看成周边支承条件下承受均布载荷的圆平板,应用平板理论得出计算公式,考虑管孔的削弱,再引入经验性的修正系数。
2.将管子当作管板的固定支撑,而管板是受管子支撑的平板。
管板的厚度取决于管板上不布管区的范围。
3.将管板视为在广义弹性基础上承受均布载荷的多孔圆平板,既把实际的管板简化为受到规则排列的管孔削弱,同时又被管子加强的等效弹性基础上的均质等效圆平板。
一、管板设计的基本考虑
把实际的管板简化为承受均布载荷,放置在弹性基础上且受管孔均匀削弱的当量圆平板,在此基础上还考虑了以下几方面因素。
★1.管束对管板挠度的约束作用,但忽略管束对管板转角的约束作用。
2.管板周边不布管区对管板应力的影响。
将管板划分为两区,即靠近
42
中央部分的布管区和靠近周边处较窄的不布管区。
不布管区可简化为一个圆环形实心板,由于它