镀铬辊制造焊接规范.docx
《镀铬辊制造焊接规范.docx》由会员分享,可在线阅读,更多相关《镀铬辊制造焊接规范.docx(10页珍藏版)》请在冰豆网上搜索。
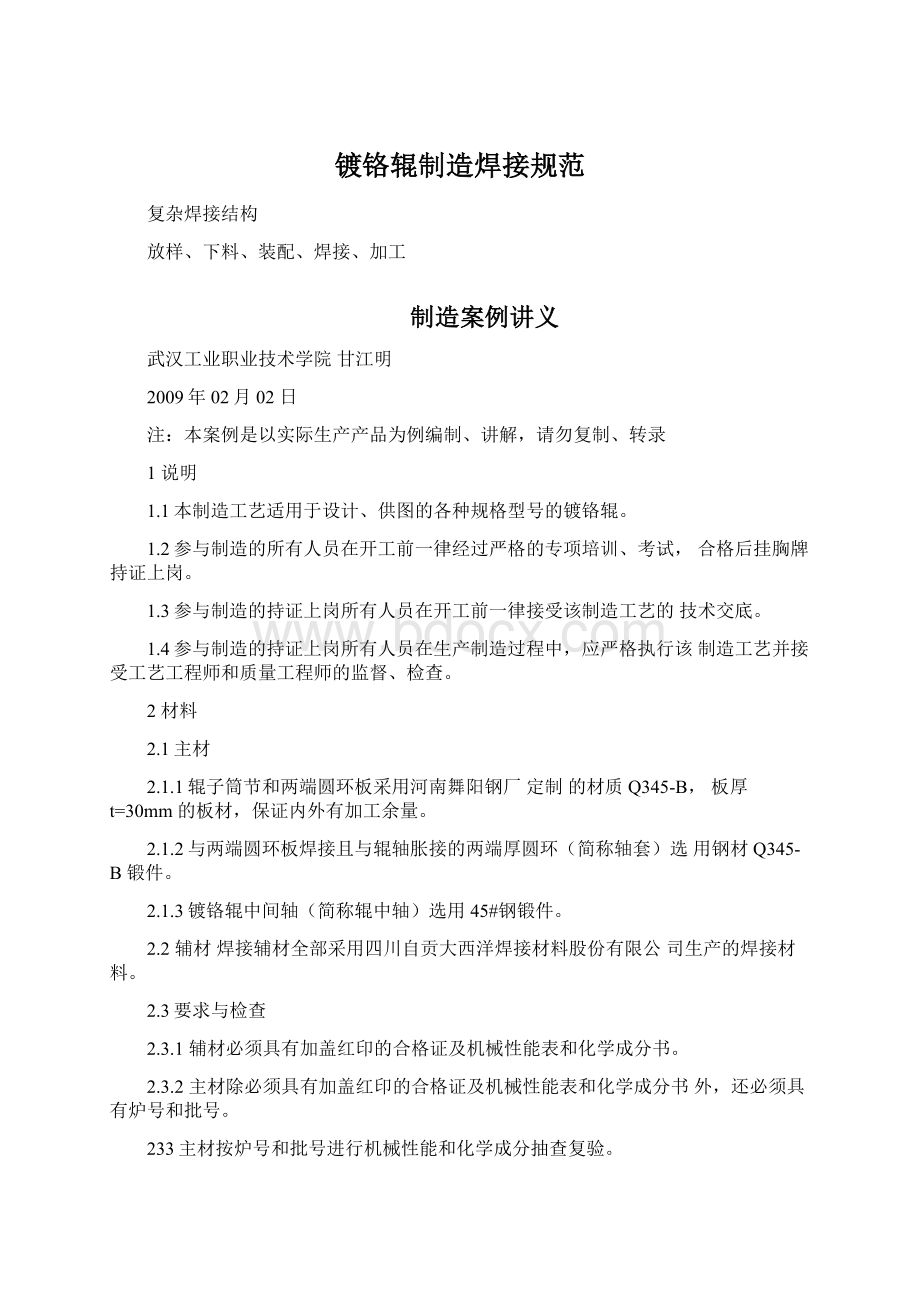
镀铬辊制造焊接规范
复杂焊接结构
放样、下料、装配、焊接、加工
制造案例讲义
武汉工业职业技术学院甘江明
2009年02月02日
注:
本案例是以实际生产产品为例编制、讲解,请勿复制、转录
1说明
1.1本制造工艺适用于设计、供图的各种规格型号的镀铬辊。
1.2参与制造的所有人员在开工前一律经过严格的专项培训、考试,合格后挂胸牌持证上岗。
1.3参与制造的持证上岗所有人员在开工前一律接受该制造工艺的技术交底。
1.4参与制造的持证上岗所有人员在生产制造过程中,应严格执行该制造工艺并接受工艺工程师和质量工程师的监督、检查。
2材料
2.1主材
2.1.1辊子筒节和两端圆环板采用河南舞阳钢厂定制的材质Q345-B,板厚t=30mm的板材,保证内外有加工余量。
2.1.2与两端圆环板焊接且与辊轴胀接的两端厚圆环(简称轴套)选用钢材Q345-B锻件。
2.1.3镀铬辊中间轴(简称辊中轴)选用45#钢锻件。
2.2辅材焊接辅材全部采用四川自贡大西洋焊接材料股份有限公司生产的焊接材料。
2.3要求与检查
2.3.1辅材必须具有加盖红印的合格证及机械性能表和化学成分书。
2.3.2主材除必须具有加盖红印的合格证及机械性能表和化学成分书外,还必须具有炉号和批号。
233主材按炉号和批号进行机械性能和化学成分抽查复验。
234板材和锻件进行100%的UT检测,达到相应原材料超声波探伤检测国家标准H级合格。
3放样、下料、坡口加工
3.1辊子筒节以板厚中径计算展开(筒节长度方向放加工余量
+25x2=50mm)放样、号线下料。
尺寸精度要求如下表1,严格执行
三检制度,确认无误后才能流入下道工序。
放样、下料、坡口加工尺寸精度表表1
测定位置
标准尺寸
M样
切箭
-
A
1
IC-Czl
i1.5
*放欝精慶要检查皐体
尺寸
+滴精度由峨查鯉切穌端进行检査
口3
切割
e
i
iZo'
4
3.2两端圆环板外径留+8mm,内径留一6mm的加工余量数控编程。
3.3锻件尺寸必须留有足够的加工余量,锻件加工前应进行严格的几何尺寸检查和化学成分、机械性能复验。
3.4采用事先编程,检查,然后全自动数控切割下料和机械加工坡口
3.5下料切割和坡口加工完成后严格执行三检制,尺寸公差必须达到上表1的精度要求。
4辊子筒节的制造加工
4.1辊子筒节采用液压四辊成形,由于是四辊成形可以避免形成“桃子口”。
4.2辊子筒节在滚圆成形过程中,不间断采用超过内径2/3的样板对
弧度进行检查。
4.3采用门形卡对辊子筒节纵缝进行装配,严格控制装配间隙和错边
量,装配间隙精度达到3±1mm;错边量精度达到w1mm。
4.4辊子筒节纵缝焊接
4.4.1焊接方法采用碳弧气刨清根,双面埋弧自动焊(SMAW)打底、填充、盖面。
4.4.2焊前将坡口及其两侧30〜50mm范围内彻底打磨干净,直至露出金属光泽。
4.4.3焊接材料及焊接工艺参数见下表2
埋弧自动焊焊接材料及焊接工艺参数表表2
层
次
焊接材料
焊接电源
电弧电
压(V)
焊接速度
(cm/min)
牌号
直径
极性
电流(A)
打底层
H10Mn2
直流
480-500
34-36
48-50
填充层
+
©4.0
500-550
35-37
48-50
盖面层
HJ431
反接
550-620
35-37
48-50
4.4.4辊子筒节纵缝焊接完毕后敲净熔渣,内外焊缝打磨至与母材表
面平齐,然后采用液压四辊对成形和焊接变形进行校正。
校形后辊子
筒节形位公差应达到如下表3的精度要求。
辊子筒节校形后形位公差精度要求表表3
形位公差类别
圆度
直线度
同心度
精度要求(mm)
w2
w1.5
w2
4.5辊子筒节转入镗床,按图纸尺寸和公差对内圆进行机械加工,加
工后应保证直线度w0.05mm/m,同心度w0.05mm/m,粗糙度w125
4.6辊子筒节内圆经镗床加工后,对纵缝进行100%的UT检测,达到
JB4730-2005标准中的H要求。
4.7辊子筒节两端长度方向暂不进行加工,留待最后整体加工。
5两端圆环板的制造加工
5.1将全自动数控切割下料好的,内、外圆留有加工余量的两端圆板
转入车工班。
5.2按图纸尺寸和精度要求进行内、外圆直径和坡口的机械加工。
7
L
3
2
5.3按下表4的尺寸公差要求对两端圆环板进行检查和工序验收。
两端圆环板加工后尺寸公差要求表表4
尺寸类别
外圆直径
内圆直径
坡口钝边
坡口角度
公差要求
w0.50mm
0~+0.50mm
士1mm
士2.5°
6轴套的制造加工
6.1按图纸尺寸和公差要求对轴套外圆和两端面进行精确机械加工。
6.2按图纸尺寸对轴套内圆直径留-6mm进行初次机械加工(待将轴
套与端部圆环板焊接成部件后,对轴套内圆直径和端部圆环板内外表
面进行精加工)。
「卞--
6.3按下表5的尺寸公差要求对轴套进行检查和工序验收。
轴套机加工后尺寸公差要求表表5
尺寸类别
外圆直径
内圆直径
端面与外圆垂直度
粗糙度
公差要求
w0.50mm
—6mm
w0.10mm
w12.5
7轴套与端部圆环板的装配、焊接、机加工
7.1轴套与端部圆环板的装配
7.1.1铺设平台,用水准仪测平,保证平台平面度w1mm。
平台铺设
合格后经专检员复验。
7.1.2在经专检员复验平度合格的平台上放样装配轴套与端部圆环板,大样放好经专检员复验合格后,在内外圆装配基准线上打上样冲,才能进行正式装配。
7.2轴套与端部圆环板的焊接
721焊前应用砂轮认真清理焊缝区域,使其两侧30-50mm范围内不
得有水、氧化皮、油污、油漆或其它杂物,并露出金属光泽。
7.2.2焊前采用远红外线加热片或中性火焰对焊缝区域进行预热,预热温度》200C,预热尺寸范围不小于3倍的轴套壁厚,且》100mm。
7.2.3采用碳弧气刨清根,双面半自动CO2气体保护焊打底、填充、盖面。
7.2.4采用焊接材料及焊接工艺参数见下表6。
半自动CO2气体保护焊焊接材料及焊接工艺参数表表6
层数
焊接材料
工艺参数
型号
规格
(mm)
电源
极性
焊接电流
(A)
电弧电压
(V)
打底层
直流
反接
80-100
21-23
填充层
CHW-50C6
©1.2
150-170
23-25
盖面层
90-110
22-24
7.2.5焊接后立即采用矿棉对焊缝区域进行包裹保温,使其缓慢冷却
7.3轴套与端部圆环板的机加工
7.3.1将焊接后经专检员检验合格的轴套与端部圆环板转入机加车间7.3.2以轴套端面为基准对轴套与端部圆环板(组件)上的端部圆环板内外表面进行机加工
7.3.3以轴套与端部圆环板(组件)上的端部圆环板外圆为基准对轴套内圆进行精确的机械加工,使其尺寸和公差符合图纸设计要求(注意:
这是最重要的尺寸公差之一)。
8镀铬辊中间轴的加工
8.1对辊中轴外圆和两端头留余量进行粗加工(粗加工后轴的长度
+6mm,外圆半径+3mm)。
8.2对辊中轴进行调质热处理,使其表面硬度达到HB225〜255。
8.3对辊中轴外圆和两端头进行精加工,使其达到图纸设计尺寸和公差的要求,特别重视两头与轴套胀接部分的尺寸与公差(注意:
这也是最重要的尺寸公差之一)。
说明:
辊中轴两端露出轴套部分的各轴颈、轴阶暂不加工,留待最后整体加工。
8.4检查员对辊中轴已精加工的尺寸和公差进行严格的检查,合格后转入压力容器车间与辊子筒节进行装配、焊接。
9辊中轴与两端轴套(组件)的胀接
9.1将两端轴套(组件)放入圆形油槽中进行加热,加热速度W125C
/h,加热温度》350C。
9.2自制热胀四爪夹钳,通过两端圆环板四孔进行热胀工作。
9.3将达到加热温度的两端轴套(组件)从圆形油槽中吊出,迅速与未加热的“冷”辊中轴进行热胀。
9.4边热胀边检查定位尺寸,严格控制两端轴套(组件)之间的距离
和方向,使其符合图纸的设计要求。
10辊子筒节与胀接后的组件(整体)装配、焊接
10.1辊子筒节与胀接后的组件间的装配
10.1.1将胀接冷却检查合格的组件吊上测平的平台(要求平台平面度<1mm)。
10.1.2将内圆加工检查合格的辊子筒节吊上测平的平台。
10.1.3将两者在平台上按图纸尺寸和要求进行装配、点固。
10.2辊子筒节与账接后的组件间的焊接
10.2.1焊前应用砂轮认真清理焊缝区域,使其两侧30-50mm范围内不得有水、氧化皮、油污、油漆或其它杂物,并露出金属光泽。
10.2.2焊前采用远红外线加热片或中性火焰对焊缝区域进行预热,预
热温度》200C,预热尺寸范围不小于3倍的两板间较厚板材的壁厚,且》100mm。
10.2.3采用单面半自动CO2气体保护焊打底、填充、盖面。
10.2.4采用焊接材料及焊接工艺参数见上表6。
I0.2.5焊接后立即采用矿棉对焊缝区域进行包裹保温,使其缓慢冷却。
10.2.6待焊缝冷却后对其进行外观处理和焊脚尺寸的检查。
10.2.7焊缝外观质量检查合格后,对其进行100%的PT检测,达到JB4730-2005标准中的H要求。
II镀铬辊整体热处理
11.1为了消除焊接残余应力,稳定机械加工后的尺寸,镀铬辊需进行整体炉内退火热处理。
11.2退火热处理加热速度W125士15C/h,加热温度》550士25C,炉内保温2h,然后随炉冷却,冷却速度W115±15C/h。
11.3提供带退火曲线的热处理纸质报告。
12镀铬辊整体机加工
12.1以辊中轴中心为基准,根据图纸尺寸和公差要求,从辊子筒节中间向两端加工棍子筒节抛物线外圆。
12.2按图纸尺寸和公差要求加工辊中轴两端露出轴套部分的各轴颈、轴阶等。
12.3检查员按图纸尺寸和公差要求对加工部位进行专检。
13镀铬辊整体平衡试验
13.1按图纸尺寸设计要求先做静平衡,出具带具体数据的静平衡试验报告。
13.2为了更好地满足使用性能,静平衡试验合格后再做动平衡试验,出具带具体数据的动平衡试验报告。
14镀铬辊整体加工完成后的表面处理
14.1按图纸设计精度要求对整体加工完后的辊身表面嗬毛,或上磨床加工。
专检员检查合格后转入下道工序镀铬。
14.2按图纸设计要求的厚度、粗糙度、硬度对辊身进行镀铬。
专检员检查合格后转入下道工序包装。
15镀铬辊镀铬完成后包装15.1使用时装配用的机加工表面涂防绣脂。
15.2镀铬表面先用泡膜纸包裹,然后外层用防水彩条布包扎。
15.3每个镀铬辊用两个U型木质支架支撑固定后,放入内钉防水彩条布的木箱中。
15.4木箱外四侧面和上表面贴有发货口麦头。