机械加工工艺内容.docx
《机械加工工艺内容.docx》由会员分享,可在线阅读,更多相关《机械加工工艺内容.docx(19页珍藏版)》请在冰豆网上搜索。
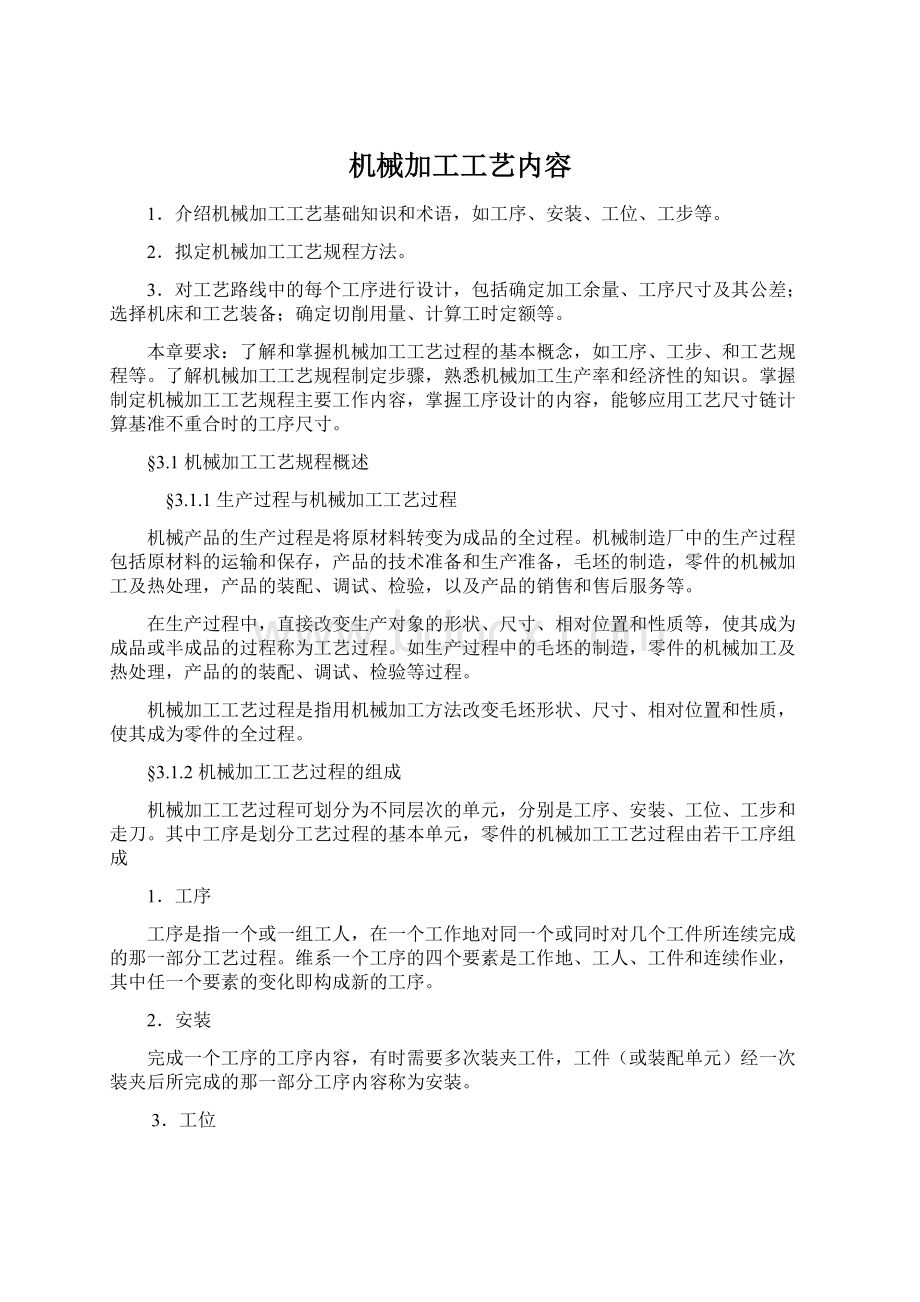
机械加工工艺内容
1.介绍机械加工工艺基础知识和术语,如工序、安装、工位、工步等。
2.拟定机械加工工艺规程方法。
3.对工艺路线中的每个工序进行设计,包括确定加工余量、工序尺寸及其公差;选择机床和工艺装备;确定切削用量、计算工时定额等。
本章要求:
了解和掌握机械加工工艺过程的基本概念,如工序、工步、和工艺规程等。
了解机械加工工艺规程制定步骤,熟悉机械加工生产率和经济性的知识。
掌握制定机械加工工艺规程主要工作内容,掌握工序设计的内容,能够应用工艺尺寸链计算基准不重合时的工序尺寸。
§3.1机械加工工艺规程概述
§3.1.1生产过程与机械加工工艺过程
机械产品的生产过程是将原材料转变为成品的全过程。
机械制造厂中的生产过程包括原材料的运输和保存,产品的技术准备和生产准备,毛坯的制造,零件的机械加工及热处理,产品的装配、调试、检验,以及产品的销售和售后服务等。
在生产过程中,直接改变生产对象的形状、尺寸、相对位置和性质等,使其成为成品或半成品的过程称为工艺过程。
如生产过程中的毛坯的制造,零件的机械加工及热处理,产品的的装配、调试、检验等过程。
机械加工工艺过程是指用机械加工方法改变毛坯形状、尺寸、相对位置和性质,使其成为零件的全过程。
§3.1.2机械加工工艺过程的组成
机械加工工艺过程可划分为不同层次的单元,分别是工序、安装、工位、工步和走刀。
其中工序是划分工艺过程的基本单元,零件的机械加工工艺过程由若干工序组成
1.工序
工序是指一个或一组工人,在一个工作地对同一个或同时对几个工件所连续完成的那一部分工艺过程。
维系一个工序的四个要素是工作地、工人、工件和连续作业,其中任一个要素的变化即构成新的工序。
2.安装
完成一个工序的工序内容,有时需要多次装夹工件,工件(或装配单元)经一次装夹后所完成的那一部分工序内容称为安装。
3.工位
在带有转位(或移位)夹具(或工作台)的机床上进行加工时,在一次装夹中,工件(或刀具)相对机床要经过几个位置依次进行加工,此时,为完成一定的工序部分,一次装夹工件后,工件(或装配单元)与夹具或设备的可动部分一起相对刀具或设备的固定部分所占据的每一个位置,称为工位。
4.工步
工步是划分工序的单元,在一个工序中,工步是在加工表面(或装配时的连接表面)和加工(或装配)工具不变的情况下,所连续完成的那一部分工序。
加工表面和加工工具两个要素中有一个发生变化就是另一个工步。
对于在一次安装中连续加工的若干相同工步,可写成一个工步。
5.走刀
在一个工步内,如果要切除的金属层很厚,需要对同一表面进行几次切削,这时刀具以加工时的进给速度相对工件所完成的一次进给运动的工步部分,称作走刀。
§3.1.3机械加工工艺规程
1.机械加工工艺规程
机械产品的生产中,用来规定产品或零件制造工艺过程和操作方法等的工艺文件称为机械加工工艺规程。
有多种工艺规程文件在生产过程中使用,下面介绍常用的两种工艺规程文件:
机械加工工艺过程卡片和机械加工工序卡片。
(1)机械加工工艺过程卡片这种卡片是以工序为单位说明零件机械加工过程的一种工艺文件。
机械加工工艺过程卡概述了加工过程的全貌,是制订其它工艺文件的基础。
但是在单件小批生产中,通常不再编制更详细的工艺文件,而以这种卡片直接指导生产。
(2)机械加工工序卡片这种卡片是在机械加工工艺过程卡的基础上,按每道工序的工序内容所编制的一种工艺文件。
该卡片中一般附有工序简图,并详细说明该工序中每个工步的加工内容、工艺参数、操作要求以及所用的设备和工艺装备等。
它是用于具体指导工人操作的技术文件。
2.工序简图
在机械加工工序卡片中附有工序简图,工序简图可以清楚直观地表达出一道工序的工序内容,其绘制要求有以下几点:
(1)工序简图可按比例缩小,并尽量用较少的投影绘出,可以略去视图中的次要结构和线条。
(2)工序简图主视图应是本工序工件在机床上装夹的位置。
例如,在卧式车床上加工的轴类零件的工序简图,其中心线要水平,加工端在右,卡盘夹紧端在左。
(3)工序简图中工件上本工序加工表面用粗实线表示,本工序不加工表面用细实线表示。
(4)工序简图中用规定的符号表示出工件的定位、夹紧情况。
(5)工序简图中标注本工序的工序尺寸及其公差,加工表面的表面粗糙度,以及其它本工序加工中应该达到的技术要求。
3.机械加工工艺规程作用
(1)工艺规程是组织生产的指导性文件生产的计划和调度、工人的操作、产品质量的检查都是以工艺规程为依据,生产人员不得违反工艺规程,以确保生产的产品质量。
(2)工艺规程是生产准备工作的依据
(3)工艺规程是新建工厂(车间)的技术文件
§3.1.4制定机械加工工艺规程的原则和步骤
在一定的生产条件下,确保加工质量和最少的生产成本是制定工艺规程的基本原则。
制订零件机械加工工艺规程的工作大致可分为下述四个阶段进行:
1.准备性工作阶段 在拟定零件机械加工工艺路线之前,需要做必要的准备性工作,包括计算生产纲领,确定生产类型;对零件进行工艺分析;确定毛坯种类。
2.工艺路线拟定阶段 这是制定工艺规程的核心,其主要内容是:
选择定位基准;选择零件表面加工方法;划分加工阶段;安排加工顺序和工序整合等。
3.工序设计阶段 在拟定了的工艺路线后,该阶段用于确定工艺路线中每一道工序的工序内容,包括确定加工余量、工序尺寸及其公差;选择机床和工艺装备;确定切削用量、计算工时定额等。
4.填写工艺文件 零件机械加工工艺规程经上述步骤确定后,应将有关内容填入各种不同的卡片,以便贯彻执行.这些卡片总称为工艺文件。
填写工艺文件是零件工艺规程编制的最后一项工作。
工艺文件的种类很多,可以根据生产实际的需要,选择相应的工艺文件作为生产中使用的工艺规程。
§3.2制订机械加工工艺规程的准备性工作
制定零件机械加工工艺规程的准备性工作,包括计算生产纲领,确定生产类型;对零件进行工艺分析;确定毛坯种类等。
§3.2.1生产纲领和生产类型
1.生产纲领
生产纲领是指在计划期内企业应当生产的产品产量和进度计划。
在计划期为一年的零件年生产纲领N可按下式计算:
N=Qn(1+a%)(1+b%)(件/年)(3-1)
式中Q—产品的年产量(台/年);
n—每台产品中该零件的数量;
a%—备品的百分率;
b%—废品的百分率。
2.生产类型
生产类型可以反映出企业生产专业化程度。
根据企业生产的产品特征(即产品属于重型、中型或轻型零件)、年生产纲领、批量以及投入生产的连续性,一般分为三种生产类型,即单件生产、成批生产和大量生产。
单件生产指企业生产的同一种零件的数量很少,企业产品品种多而且很少重复,企业中各工作地点的加工对象经常改变。
例如重型机器制造、专用设备制造和新产品试制都属于单件生产。
大量生产指企业生产的同一种产品的数量很大,连续的大量制造同一种产品。
企业中大多数工作地点固定地加工某种零件的某一道工序。
例如汽车、轴承、摩托车等产品的制造。
成批生产指企业按年度分批生产相同的产品,生产呈周期性重复。
例如普通机床制造、纺织机械的制造等。
通常企业并不是把全年产量一次投入车间生产,而是根据产品的生产周期、销售以及车间生产的均衡情况,按一定期限分次、分批投产。
一次投入或产出的同一产品或零件数量称为生产批量,简称批量。
成批生产中,按照批量不同,分为小批生产、中批生产和大批生产三种。
为取得好的经济效益,不同生产类型的工艺特点是不一样的,小批生产的工艺特点与单件生产相似,大批生产的工艺特点与大量生产相似。
表3-1列出了各种生产类型的工艺特点。
表3-1各种生产类型的工艺特点
工艺特点
生产类型
单件小批生产
中批生产
大批大量生产
零件的互换性
用修配法,缺乏互换性
多数互换,部分修配
全部互换,高精度偶件采用分组装配
毛坯情况
锻件自由锻造,铸件木工手工造型,毛坯精度低
锻件部分采用模锻,铸件部分用金属模,毛坯精度中等
广泛采用锻模,机器造型等高效方法生产毛坯,毛坯精度高
机床设备及其布置形式
通用机床,机群式布置,也可用数控机床
部分通用机床,部分专用机床,机床按零件类别分工段布置
广泛采用自动机床,专用机床,按流水线、自动线排列设备
工艺装置
通用刀具、量具和夹具,或组合夹具,找正法装夹工件
广泛采用夹具,部分靠找正装夹工件,较多采用专用量具和刀具
高效专用夹具,多用专用刀具,专用量具及自动检测装置
对工人的技术要求
高
中等
对调整工人的技术水平要求高,对操作工人技术水平要求低
工艺文件
仅要工艺过程卡
工艺过程卡,关键零件的工序卡
详细的工艺文件,工艺过程卡、工序卡、调整卡等
加工成本
较高
中等
低
§3.2.2零件的工艺分析
在制订零件的机械加工工艺规程之前,应对零件的工艺性进行分析,主要有以下两方面内容。
1.分析、审查零件图样和产品的装配图
制订工艺规程时,通过分析零件图样和部件的装配图,主要是明确被加工零件在产品中的位置与作用,找出该零件上有多少主要加工表面,找出该零件主要的技术要求和加工中的关键的技术问题,了解各项公差与技术要求制定的依据,在编制工艺过程中,有针对性的解决这些问题。
具体内容包括:
(1)审查零件图的视图、尺寸、公差和技术条件等是否完整。
(2)审查各项技术要求是否合理。
(3)审查零件材料及热处理选用是否合适。
2.零件的结构工艺性分析
零件的结构工艺性是指所设计的零件在满足使用要求的前提下,制造的方便性、可行性和经济性。
即零件的结构应方便于加工时工件的装夹、对刀、测量,可以提高切削效率等。
结构工艺性不好会使加工困难,浪费材料和工时,有时甚至无法加工。
所以应该对零件的结构进行工艺性审查,如发现零件结构不合理之处.应与有关设计人员一起分析,按规定手续对图样进行必要的修改及补充。
3.数控加工对零件结构工艺性的影响
数控加工的特点是自动化程度高,加工精度高,对加工对象的适应性强,可以与计算机通讯(DNC),实现计算机辅助设计与制造一体化。
因此数控加工对传统的零件结构工艺性衡量标准产生了很大影响,在下列情况下采用数控加工,其工艺性是好的:
⑴单件小批生产的零件的加工,成批生产中的关键工序的加工。
⑵加工精度高,具有形状复杂的曲线或曲面的零件加工。
⑶需要多次改型设计的零件的加工。
⑷需要钻、镗、铰、攻丝及铣削多个工步加工的工件,如箱体零件的加工。
⑸价值高的零件。
⑹进行精密复制的零件的加工。
⑺用通用机床加工时,需要复杂的专用夹具或需要很长的调整时间的零件的加工。
§3.2.3毛坯的选择
毛坯是根据零件所要求的形状、工艺尺寸等而制成的供进一步加工用的生产对象。
机械加工中常用的毛坯类型有下述几种:
1.常用的毛坯类型
(1)铸件 将熔融金属浇入铸型,凝固后所得到的金属毛坯。
适用于形状比较复杂,所用材料又具备可铸性的零件。
铸件的材料可以是铸铁、铸钢或有色金属。
(2)锻件 金属材料经过锻造变形而得到的毛坯。
适用于力学性能要求高,材料(钢材)又具有可锻性,形状比较简单的零件。
生产批量大时,可用模锻代替自由锻。
(3)型材 各种热轧和冷拉的圆钢、板材、异型材等,适用于形状简单的、尺寸较小的零件。
(4)焊接件 是将各种金属零件用焊接的方法,而得到的结合件。
在单件小批生产中,用焊接件制作大件毛坯,可以缩短生产周期。
2.毛坯的形状与尺寸
现代机械制造发展的趋势之一是精化毛坯,使毛坯形状和尺寸尽量接近零件,从而实现少屑甚至无屑加工。
确定毛坯的形状与尺寸的步骤如下:
首先选取毛坯加工余量和毛坯公差,其次将毛坯加工余量迭加在零件的相应加工表面上,从而计算出毛坯尺寸,最后标注毛坯的尺寸与公差。
在决定毛坯形状时,还需要考虑加工工艺对毛坯形状的影响。
例如有时为使零件在加工中装夹方便,在其毛坯上做出工艺凸台,所谓工艺凸台是为了满足工艺的需要而在工件上增设的凸台,如图3-1a所示。
零件加工后一般应将其切除;有时将分离的零件做成一个毛坯,使其易于加工,并确保加工质量,如图3-1b所示,机床丝杠的开合螺母,将其毛坯做成整体,待加工到一定阶段后才切割分离开。
a)工艺凸台 b)丝杠的开合螺母
图3-1毛坯形状
§3.3定位基准的选择
§3.3.1定位基准种类
定位基准是加工中用来使工件在机床或夹具上定位的所依据的工件上的点、线、面。
按工件上用作定位的表面状况把定位基准分为粗基准、精基准,以及辅助基准。
(1)粗基准和精基准在零件加工的第一道工序,只能用毛坯上未经加工的表面作为定位基准,这种定位基准称为粗基准。
粗基准是用工件上未经加工的表面定位。
而利用工件上已加工过的表面作为定位基准面,称为精基准。
(2)辅助基准零件设计图中某不要求加工的表面,有时为了工件装夹的需要,而专门将其加工作为定位用;或者为了定位需要,加工时有意提高了零件设计精度的表面,这种表面不是零件上的工作表面,只是由于工艺需要而加工的基准面,称为辅助基准或工艺基准。
例如加工过程中使用的中心孔定位;图3-1a所示零件的工艺凸台。
零件的加工过程是首先用粗基准定位,加工出精基准表面;然后采用精基准定位,加工零件的其它表面。
在选择定位基准时,首先考虑用那一组精基准定位加工出工件的主要表面,然后确定用怎样的粗基准定位加工出精基准的表面。
§3.3.2粗基准的选择
粗基准的选择对工件主要有两个方面的影响,一是影响工件上加工表面与不加工表面的相互位置,二是影响加工余量的分配。
粗基准的选择原则是:
(1)对于同时具有加工表面和不加工表面的零件,当必须保证其不加工表面与加工表面的相互位置时,应选择不加工表面为粗基准。
如果零件上有多个不加工表面,应选择其中与加工表面相互位置要求高的表面为粗基准。
(2)对于有较多加工表面的工件,粗基准的选择应能合理分配加工余量。
合理分配加工余量指:
1)若工件必须首先保证某重要表面的余量均匀,应选择该表面为粗基准。
2)应选择毛坯上余量最小的表面为粗基准,以保证各加工表面都有足够加工余量。
(3)作为粗基准的表面应尽量平整,不应有飞边、浇口、冒口及其它缺陷,这样可减少定位误差,并使工件夹紧可靠。
(4)为保证重要加工面的余量均匀,应选择重要加工面为粗基准。
(5)应避免重复使用粗基准,在同一尺寸方向上粗基准只准使用一次。
因为粗基准是毛坯表面,定位误差大,两次以同一粗基准装夹下加工出的各表面之间会有较大的位置误差。
§3.3.3精基准的选择
选择精基准主要应从保证工件的位置精度和装夹方便这两方面来考虑。
精基准的选择原则是:
(1)基准重合原则 应尽量选择加工表面的设计基准作为定位基准,这一原则称为基准重合原则。
(2)基准统一原则 当零件需要多道工序加工时,应尽可能在多数工序中选择同一组精基准定位,称为基准统一原则。
(3)自为基准原则 有时精加工或光整加工工序要求余量小而均匀,则应以加工表面本身作为定位基准,称为自为基准原则。
如拉孔、铰孔、研磨、无心磨等。
(4)互为基准原则 某个工件上有两个相互位置精度要求很高表面,采用工件上的这两个表面互相作为定位基准,反复加工另一表面,称为互为基准。
(5)所选精基准应能保证工件定位准确,装夹方便,夹具结构简单适用。
§3.3.4定位基准选择实例
表3-2为图3-2轴座加工工艺过程,表中列出各工序的定位基准以及选择定位基准的依据。
表3-2轴座机械加工工艺过程
工序号
工序内容
设备
定位基准(括弧内数字为限制自由度数)
简述原因
10
铣底面
铣床
粗基准为φ40外圆及底面侧面
保证不加工面φ40外圆与加工面(底面)的位置精度
20
车端面,钻、车φ25H7孔
车床
精基准为底面、φ40外圆侧面
基准重合,即定位基准与设计基准重合
30
车另一端面
车床
φ25H7孔
基准重合
40
钻3-φ9、锪φ14孔
钻床
底面及底面边侧
基准重合
注:
粗基准可以用划线基准体现。
例如表中在10工序前安排划线工序,以φ40轴线为基准,划出底面加工线,在10工序中按线加工底面,则可以认为划线基准(φ40外圆的轴线)是粗基准
3-2轴座零件
§3.4机械加工工艺路线的拟定
机械加工工艺路线是指零件在生产过程即仅用工序顺序简单地表明零件的工艺过程。
拟定机械加工工艺路线是制定机械加工工艺过程中的关键环节。
在拟定工艺路线时,除应合理选择定位基准外,还需要解决下列问题:
§3.4.1零件表面加工方法的选择
1.加工经济精度和加工经济表面粗糙度
一种加工方法能够保证的加工精度有一个相当大的范围,但如果要求它保证的加工精度过高,需要采取的一些特殊的工艺措施,加工成本随之加大。
一种加工方法的加工经济精度是指在正常加工条件下(采用符合质量标准的设备、工艺装备和标准技术等级的工人,不延长加工时间)所能保证的加工精度。
各种加工方法达到的加工经济精度和加工经济表面粗糙度可查阅各种金属切削加工工艺手册。
2.典型表面的加工路线
机械零件是由一些简单的几何表面如外圆柱、孔、平面等组合而成的,因此零件的工艺路线就是这些表面加工路线的恰当组合,表3-3、表3-4和表3-5分别是外圆柱、孔、平面的典型加工路线,供选用时参考。
表3-3 外圆柱面的加工路线
序号
加工方法
公差等级
粗糙度Ra值/μm
适用范围
1
粗车
IT11~13
12.5~50
适用于淬火钢以外的各种金属
2
粗车-半精车
IT8~10
3.2~6.5
3
粗车-半精车-精车
IT7~8
0.8~1.6
4
粗车-半精车-精车-滚压(或抛光)
IT7~8
0.025~0.2
5
粗车-半精车-磨削
IT7~8
0.4~0.8
主要用于淬火钢,也可以用于未淬火钢,不宜加工有色金属
6
粗车-半精车-粗磨-精磨
IT6~7
0.1~0.4
7
粗车-半精车粗磨-精磨-超精加工
IT5
0.012~0.1
8
粗车-半精车-精车-精细车
IT6~7
0.025~0.4
主要用于精度高的有色金属加工
9
粗车-半精车-粗磨-精磨-超精磨
IT5
0.006~0.025
极高精度的外圆加工
10
粗车-半精车粗磨-精磨-研磨
IT5
0.006~0.1
表3-4 孔的加工路线
序号
加工方法
公差等级
粗糙度Ra值/μm
适用范围
1
钻
IT11~13
12.5
加工未淬火钢及铸铁。
也可用于加工有色金属。
孔径小于φ15~φ20
2
钻-铰
IT8~10
1.6~6.3
3
钻-粗铰-精铰
IT7~8
0.8~1.6
4
钻-扩
IT10~11
6.3~12.5
加工未淬火钢及铸铁。
也可用于加工有色金属。
孔径大于φ15~φ20
5
钻-扩-铰
IT8~9
1.6~3.2
6
钻-扩-粗铰-精铰
IT7
0.8~1.6
7
钻-扩-机铰-手铰
IT6~7
0.2~0.4
8
钻-扩-拉
IT7~9
0.1~1.6
大批大量生产
9
粗镗(或扩)
IT11~13
6.3~12.5
除淬火钢外的各种材料
10
粗镗(粗扩)-半精镗(精扩)-
IT9~10
1.6~3.2
11
粗镗(粗扩)-半精镗(精扩)-精镗(铰)
IT7~8
0.8~1.6
12
粗镗(粗扩)-半精镗(精扩)-精镗-浮动镗刀镗孔
IT6~7
0.4~0.8
13
粗镗(扩)-半精镗-磨
IT7~8
0.2~0.8
主要用于淬火钢,也可用于未淬火钢,不宜用于有色金属
14
粗镗(扩)-半精镗-粗磨-精磨
IT6~7
0.1~0.2
15
粗镗-半精镗-精镗-精细镗
IT6~7
0.05~0.4
主要用于高精度有色金属加工
16
粗镗-半精镗-精镗-珩磨
IT6~7
0.025~0.2
用于加工精度很高的孔
17
以研磨代替上述方法的珩磨
IT5~6
0.006~0.1
表3-5 平面的加工路线
序号
加工方法
公差等级
粗糙度Ra值/μm
适用范围
1
粗车
IT11~13
12.5~5.0
端面
2
粗车-半精车
IT8~10
3.2~6.3
3
粗车-半精车-精车
IT7~8
0.8~1.6
4
粗车-半精车-磨削
IT6~8
0.2~0.8
5
粗刨(或粗铣)
IT11~13
6.3~25
一般不淬硬平面(端铣表面粗糙度Ra值较小)
6
粗刨(或粗铣)-精刨(或精铣)
IT8~10
1.6~6.3
7
粗刨(或粗铣)-精刨(或精铣)-刮研
IT6~7
0.1~0.8
精度高的不淬硬平面
8
以宽刃刨刀精刨代替上述刮研
IT7
0.2~0.8
9
粗刨(或粗铣)-精刨(或精铣)-磨削
IT7
0.2~0.8
精度高的淬硬平面或不淬硬平面
10
粗刨(或粗铣)-精刨(或精铣)-粗磨-精磨
IT6~7
0.025~0.4
11
粗铣-拉
IT7~9
0.2~0.8
大量生产,较小平面
12
粗铣-精铣-磨削-研磨
IT5以上
0.006~0.1
高精度平面
§3.4.2工序顺序的确定
在选定零件各表面加工方法和加工时的定位基准之后,要把对零件的加工分散到各工序中去完成,确定工艺路线中各工序的内容和工序的顺序,这时须考虑下述两个问题:
1.加工阶段的划分
在加工较高精度的工件时,如工序数较多,可把工件各表面的粗加工工序集中起来,安排工序顺序时,首先加工,称为粗加工阶段;然后集中进行各表面的半精加工工序,称为半精加工阶段;最后集中完成各表面的精加工工序,称为精加工阶段。
即把工艺路线分成几个加工阶段,各加工阶段的作用是:
(1)粗加工阶段 高效率地去除各加工表面上的大部分余量,并为半精加工提供精度准备和表面粗糙度的准备。
粗加工阶段所能达到的精度较低,表面粗糙度大,要求粗加工中能够有高的生产率。
(2)半精加工阶段 目的是消除主要表面上经粗加工后留下的加工误差,使其达到一定的精度,为进一步精加工做准备,同时完成一些次要表面的加工。
(3)精加工阶段 该阶段中的加工余量和切削用量都很小,其主要任务是保证工件的主要表面的尺寸、形状、位置精度和表面粗糙度。
(4)光整加工阶段 包括珩磨、超精加工、镜面磨削等光整加工方法,其加工余量极小,主要目的是进一步提高尺寸精度和减小表面粗糙度,一般不能用于纠正位置误差。
划分加工阶段的原因是:
(1)保证加工质量
(2)合理使用机床设备
(3)粗加工阶段可及时发现毛坯缺陷
(4)便于安排热处理工序
将工艺路线划分为几个加工阶段,会增加工序数目,从而增加加工成本。
因此在工件刚度高,工艺路线不划分阶段也能够保证加工精度的情况下,就不应该划分加工阶段,即在一个工序内连续完成某一表面的粗、半精和精加工工步。
例如重型零件的加工中,为减少工件的运输和装夹,常在一次装夹中完成某些表面的加工。
数控加工中因其设备的刚度高、功率大、精度高,常不划分加工阶段,通常加工中心就是在一次装夹下完成工件多个表面的粗加工、半精加工和精加工工步,达到零件的设计尺寸要求。
2.机械加工顺序的安排
机械加工顺序应该遵循下述原则:
(1)先加工基准面,后加工其他面 即先用粗基准定位加工精基准表面,为其他表面的加工提供可靠的定位基准