铝合金工艺.docx
《铝合金工艺.docx》由会员分享,可在线阅读,更多相关《铝合金工艺.docx(9页珍藏版)》请在冰豆网上搜索。
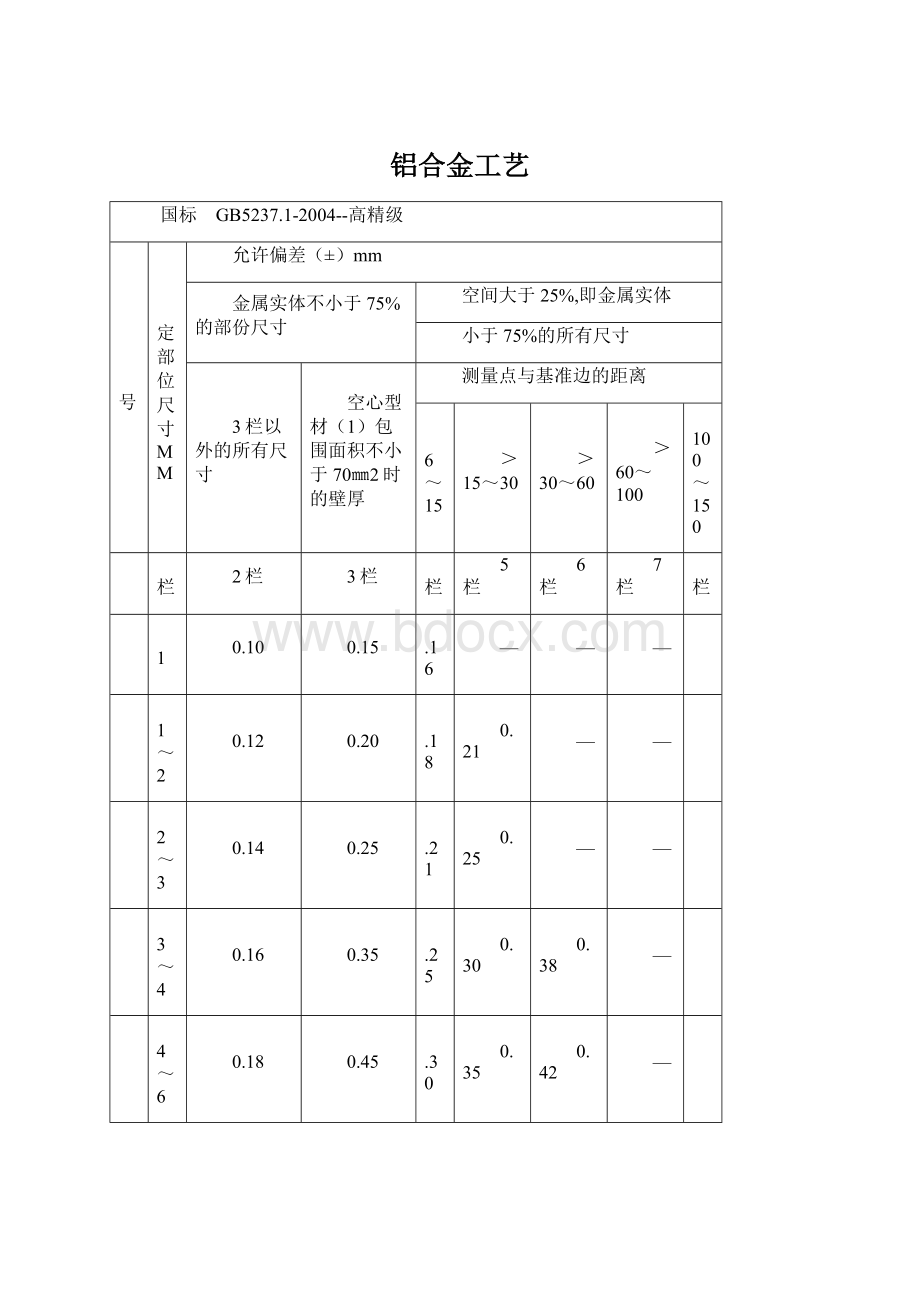
铝合金工艺
国标 GB5237.1-2004--高精级
序号
指定部位尺寸MM
允许偏差(±)mm
金属实体不小于75%的部份尺寸
空间大于25%,即金属实体
小于75%的所有尺寸
3栏以外的所有尺寸
空心型材
(1)包围面积不小于70㎜2时的壁厚
测量点与基准边的距离
>6~15
>15~30
>30~60
>60~100
>100~150
1栏
2栏
3栏
4栏
5栏
6栏
7栏
8栏
1
≤1
0.10
0.15
0.16
—
—
—
—
2
>1~2
0.12
0.20
0.18
0.21
—
—
—
3
>2~3
0.14
0.25
0.21
0.25
—
—
—
4
>3~4
0.16
0.35
0.25
0.30
0.38
—
—
5
>4~6
0.18
0.45
0.30
0.35
0.42
—
—
6
>6~12
0.20
0.60
0.35
0.40
0.46
0.50
—
7
>12~19
0.23
—
0.41
0.45
0.51
0.56
—
8
>19~25
0.25
—
0.46
0.51
0.56
0.64
0.76
9
>25~38
0.30
—
0.53
0.58
0.66
0.75
0.89
10
>38~50
0.36
—
0.61
0.66
0.79
0.91
1.07
11
>50~100
0.61
—
0.86
0.97
1.22
1.45
1.73
12
>100~150
0.86
—
1.12
1.27
1.63
1.98
2.39
13
>150~200
1.12
—
1.37
1.57
2.08
2.51
3.05
14
>200~250
1.37
—
1.63
1.88
2.54
3.05
3.68
最小壁厚
弯曲度,不大于
外接圆
普精级
高精级
超高精级
直径
任意300mm
全长L米
任意300mm
全长L米
任意300mm
全长L米
长度上h
长度上h
长度上h
≤38
≤2.4
1.5
4×L
1.3
3×L
1.O
2×L
>2.4
0.5
2×L
0.3
1×L
0.3
0.7×L
>38
_
0.5
1.5×L
0.3
0.8×L
0.3
0.5×L
外接圆
扭拧度/(mm/毫米宽).不大于
直径mm
普精级
高精级
超高精级
每米长度
总长度上
每米长度
总长度上
每米长度
总长度上
>12.5-40
0.052
0.156
0.035
0.105
0.026
0.078
>40-80
0.035
0.105
0.026
0.078
0.017
0.052
>80-250
0.026
0.026
0.026
0.052
0.026
0.026
型材宽度B
平面间隙
普精级
高精级
超高精级
≤25
≤0.20
≤0.15
≤0.10
>25
≤0.8%×B
≤0.6%×B
≤0.4%×B
任意25mm宽
≤0.20
≤0.15
≤0.10
一.铝合金型材相关工艺(基材)
1.熔炼温度:
720-760度,铸造温度:
710-730度
2.均匀化处理工艺参数:
560±10度,时间:
4-6小时,出炉后强制冷却,冷却速度控制在100-200度/min,
3.挤压及淬火
1.挤压温度:
450-480度,用分流模组合时采用上限温度,用平模时采用下限温度;挤压速度:
实心型材为20-60m/min,空心型材9-20m/min;挤压系数:
30-150为宜,30-70最佳,淬火:
为了使模子出口处的型材快速冷却到室温,将在淬火温度下固溶于基体金属中的强化相硅化镁保留在基体内。
(6063合金采用风冷淬火,6061合金采用水冷淬火)
2.6063合金型材拉伸量为0.5%-1.5%
4.造成铝合金型材典型缺陷及产生原因:
1.弯曲.扭拧.波浪:
由于模孔的设计不合理,挤压速度过快,模孔润滑不适当,导路不合适和未安装导路;挤压在拉直过程中型材拉伸量过大。
2.汽泡及起皮:
由于挤压筒内径磨损超差,挤压垫与筒间隙过大,挤压筒和挤压垫粘有油污.水分等;锭坯表面有气孔.砂眼.油污且锭坯表面过于粗糙;挤压筒温度和锭坯温度过高,填充过快;挤压时模具抹油等原因。
3.挤压裂纹:
由于挤压锭坯温度过高,挤压速度太快,锭坯均匀化处理不好;模具设计不合理,以致中心与边缘流速度差过大等原因。
4.成层:
由于锭坯表面有油污.灰尘.锭坯,表面质量不好,有较大的偏析瘤;在模子表面上留有残料;锭坯本身有分层.气泡等原因。
5.缩尾:
由于挤压残料留得太短,挤压垫片涂油或不干净,锭坯表面不清洁,制品切尾长度太短;挤压终了时突然提高挤压速度等原因。
6.挤压横纹:
由于模具设计不合理,相同部位的工作带不等长;挤压速度控制不当,挤压机运行不平衡等原因。
二:
坯料壁厚控制
1:
光身料按图纸公差控制
2:
喷涂料:
涂层膜厚壁厚控制
一涂+20UM一0.02MM
二涂+30UM一0.03MM
三涂+40UM一0.04MM
四涂+65UM一0.07MM
3:
喷粉料:
+40/120UM-0.07MM
4:
氧化料:
碱蚀银白+0.05MM4.5#古铜+0.05MM
3.0#古铜+0.03MM5.0#古铜+0.03MM
机抛银白+0.02M电解抛光+0.00MM
光面银白+0.02MM注:
(一)表示在坯料基础减去涂层厚度.(十)表示在坯料基础加上碱蚀厚度.
三:
表面质量控制及要求
1:
光身料:
装饰面无手感.
2:
氧化银白:
装饰面无手感,无明显线纹.
3:
光面料:
装饰面线纹均匀,表面光滑.
4:
氧化古铜:
装饰面线纹均匀,表面光滑.
5:
机抛料:
装饰面线纹均匀,表面光滑.,必须试机抛有无起骨/起坑现象.
6:
电解抛光:
装饰面线纹均匀,表面光滑.
7:
喷涂一涂:
装饰面无手感,注意试喷有无起骨/起坑.
8:
氟碳喷涂:
装饰面无手感,表面平直.
9:
喷粉一涂:
装饰面无手感,表面平直.
10:
一至九点非装饰面无严重拉伤为合格.如客户有特殊要求按客户要求执行.喷涂/喷粉/机抛料特别注意起骨/起坑.喷涂喷粉料特别注意挤压毛刺!
四:
配套控制及要求
1:
光身料:
能压入但不能脱落.
2:
氧化料:
能压如但不能自由滑动.
3:
喷涂/喷粉/木纹料:
能压入不脱落,保整能自由滑动.
4:
如客户有特殊要求按客户要求生产.
五:
各国角度公差:
1:
GB5237.1-2004:
普精±2度高精±1度超高±0.5度
2:
美国(AA):
S≥5MM±2度5/20MM±1.5度≥20MM±1度
3:
BS1474-1987(英国)S≥1.6MM±2度1.6/5.0MM±1.5度≥5.0MM±1度
4:
AS/NZS1866.1997(澳洲)±2度
5:
JIS4100(日本):
普精±2度特殊±1度
六.表面处理型材的相关标准和表面要求:
1.一涂分为丙稀酸和聚脂漆:
丙稀酸:
平均膜厚≥20um,局部膜厚≥17um
聚脂漆:
平均膜厚≥25um,局部膜厚≥20um
2.平均膜厚:
喷漆型材装饰面上测量的若干个(不少于5个)局部膜厚的平均值。
3.局部膜厚:
喷漆型材装饰面上某个面积不大于1平方厘米考察内做若干次(不少于3次)的膜厚测量所得的测量值的平均值
4.最小局部膜厚:
喷漆型材装饰面上测量的若干个局部膜厚中最小的一个。
5.前处理(铬化)作用:
以提高基材与涂层的附着力,铬化膜烘烤温度不应过高,温度高会导致铬化膜结晶(烘干水分子)会对铬化膜影响,导致附着力不合格一般铬化膜厚度在200-1300每平方米毫克
6.涂层平均膜厚局部膜厚
二涂料≥30≥25
三涂料≥40≥34
四涂料≥65≥55
7.铅笔硬度≥H附着力干式≥O级水煮:
一涂料15分钟二/三/四涂20分钟。
划格刀为1mm
8.表面质量:
涂层应平滑.均匀,不应有流痕,皱纹,气泡,脱落。
七.喷涂工艺:
1.爆基材原因分析:
由于操作工在穿胶滚压时,穿胶滚压机压力过大,造成穿胶型材牙位爆裂与胶条分离所引起的爆基材。
2.由于型材硬度偏高,超出型材所能承受的最大压力;本厂内控标准穿胶料控制在10-13HW,如硬度偏高型材延伸率也会随之变化.
纠正措施:
1.对现场操作员工和质检进行相关培训,让他们对穿胶料有所了解并熟知穿胶料标准及相关检验;2.在生产产品时,先试压一支最大压力的料(一般以500帕斯卡为基准,在没有爆基材为最适宜)做检测并从中摸索经验做好相关记录,总结经验.3.质检在生产前先抽查来料的硬度,如硬度偏高及早通知车间并试压得出型材的最大承受压力,做到生产时得先应手。
4.对于硬度偏高的型材,分两次压紧,一定要保证不压爆,强度达到260每平方毫米牛顿以上。
2.露底原因分析:
1.流量过小,涂层偏薄,2.挂料太密3.工件与挂具接触不良或挂具因多次喷涂,涂层太厚.绝缘4.粉末本身原因(上粉率太差.)
纠正措施:
1.控制好流量,生产时多观察粉末在型材上的流平效果.2.上架挂料时注意控制挂料的密度,注意型材与型材间的间距一致性.3.经常清理挂具,对涂层太厚的挂具及时清出并安排人清理干净.
3.碰伤原因分析:
1.本身来料在喷粉前已存在.2.挤压装框不当或中转运输中型材被碰撞.3.下料时未保护好型材造成型材与型材磨擦.碰撞
纠正措施:
1.各工序加强型材的保护,并落实一款条例.2.生产前加强自检.特别是有尖角的料做到重点保护.
4.针孔原因分析:
1.受不相溶粉末污染2.使用受污染的回收粉3.空气或粉末中有水或挥发物.油物4.型材表面上有挥发物。
5。
涂膜太厚或太薄。
纠正措施:
1.生产前检查粉末的原材料质量和成品含水量。
2。
控制好喷涂时间
5.色差原因分析:
1.油漆未调好,搅拌不充分2.烘烤时间不恰当或多次停机.过度烘烤3.膜厚不符合标准要求偏薄或偏厚4.金属油漆对应粘度未控制好。
纠正措施:
1.检查容器底部是否有沉淀物?
充分让油漆搅拌均匀2.减少停机时间及检查炉温曲线波段3.调整油漆粘度控制好膜厚
6.针孔原因分析:
1.涂膜太薄。
2.流平时间太短,挥发性过快,3.油漆粘度过高,表面粘性过强4.油漆本身存在一种张力
纠正措施:
1.控制好流量,调整膜厚达到规范要求2.加入慢干剂并调整油漆粘度3.加入添加剂
7.油污原因分析:
因坯料为冲孔料之前硬度不合格退回重时效;冲孔料之前表面粘有许多油,重时效后油污沾死在坯料表面,喷涂前处理水洗不净,喷油漆后粘在型材表面的油与油漆在固化这个工序发生化合反应;冷却后明显。
纠正措施:
控制好型材硬度,冲孔料硬度不合格需先水洗后在送挤压重时效。
8.杂色原因分析:
1.粉房清理不干净,不彻底。
2.粉末飞扬与残留在喷房的其它粉混合.
纠正措施:
1.安排粉房人员彻底清理粉房,不盲目生产.2.检查喷房的回收系统
9.起粉原因分析:
1.粉末配方2.输送空气中有水3.表面有挥发物
纠正措施:
1.与粉商联系2.检查空压机的排气量及排出压缩空气中的水3.清除型材表面的污物
10.碰伤原因分析:
1.本身来料在喷粉前已存在.2.挤压装框不当或中转运输中型材被碰撞.3.下料时未保护好型材造成型材与型材磨擦.碰撞
纠正措施:
1.各工序加强型材的保护,并落实一款条例.2.生产前加强自检.特别是有尖角的料做到重点保护.
11.云状原因分析:
1原料分散不匀2.油漆未调好,搅拌不充分3.油漆成分密度不一致4.漆膜过薄或过厚5.雾化不充分。
6.清漆喷薄,面漆喷厚.....................纠正措施:
1.加助剂2.粘度适当调高3.控制清漆与面漆的膜厚,调整至符合要求4.控制链速与枪速同步运行。
5。
增加雾化压力。
12.色差原因分析:
1.油漆未调好,搅拌不充分2.烘烤时间不恰当或多次停机.过度烘烤3.膜厚不符合标准要求偏薄或偏厚4.金属油漆对应粘度未控制好。
纠正措施:
1.检查容器底部是否有沉淀物?
充分让油漆搅拌均匀2.减少停机时间及检查炉温曲线波段3.调整油漆粘度控制好膜厚
13.颗粒原因分析:
1。
粘附在基材上的毛刺,喷涂后在漆膜上形成颗粒2。
外来灰尘及空气中的尘埃3。
固化炉内的灰尘.链条上的漆垢4.油漆过滤不干净。
纠正措施:
1.基材上的毛刺可以用手感触,挤压锯切下框时可用细砂纸打磨,时效后可作喷砂处理.2.不定期清理设备和勤刷链条
14.桔皮原因分析:
1膜厚过薄2.流平性差,溶剂挥发过快3.型材温度过高/环境温度过高/烤炉温差过大4.涂料粘度太高
纠正措施:
1.检查膜厚并调整至规范要求2.增加慢干剂3.降低烘干炉温度或闪干时间,增设通风设备3.调整粘度。
八.氧化料碱冼余量及碱洗时间:
A:
各种表面处理的表面质量和壁厚的控制参考:
光面料→表面要有光泽、光滑、线纹均匀,加0.02MM碱冼余量。
古铜料→表面光滑、线纹均匀,加0.02MM碱冼余量。
银白料→表面无严重线纹、纹粗、无手感,加0.05MM碱冼余量。
喷沙料→表面无手感、特别注意起坑起骨,喷沙面要均匀,加0.02MM碱冼余量。
(中山顶固要求非常严,不能有任何线纹)
抛光料→扫纹料不能有伤到基材的刮伤、拉伤,表面不能有严重的起坑、起骨,扫纹表面要均匀,加0.03MM碱冼余量。
机抛料→表面光滑、线纹均匀,不能有任何手感的缺陷,加0.03MM碱冼余量,但机抛后不允许有任何线纹。
电解抛光料→表面光滑、线纹均匀,无手感,无需加碱洗余量。
B:
碱洗时间:
a银白料:
10-12分钟
b古铜料:
6-8分钟
c喷砂料:
6分钟
dGBC光面料:
2分30秒
e抛光料及其它有色光面料一般不作试碱洗。
*★** *
╱-◥██◣^.^HappyEveryDay!
^.^
︱田︱田田| ---------------------
╬╬╬╬╬╬╬╬╬╬╬
谢雄
06.09.10