片剂岗位SOP培训资料.docx
《片剂岗位SOP培训资料.docx》由会员分享,可在线阅读,更多相关《片剂岗位SOP培训资料.docx(10页珍藏版)》请在冰豆网上搜索。
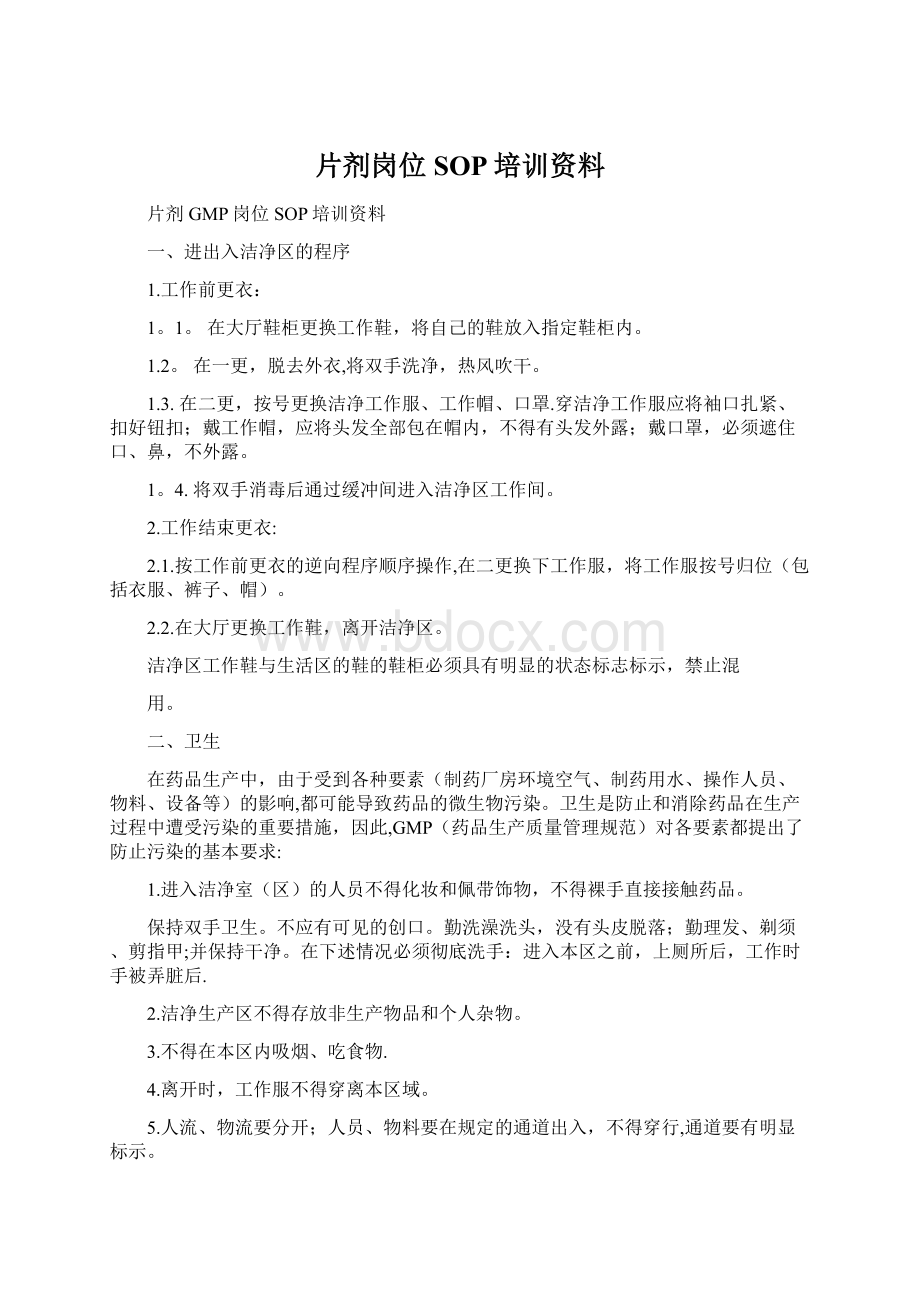
片剂岗位SOP培训资料
片剂GMP岗位SOP培训资料
一、进出入洁净区的程序
1.工作前更衣:
1。
1。
在大厅鞋柜更换工作鞋,将自己的鞋放入指定鞋柜内。
1.2。
在一更,脱去外衣,将双手洗净,热风吹干。
1.3.在二更,按号更换洁净工作服、工作帽、口罩.穿洁净工作服应将袖口扎紧、扣好钮扣;戴工作帽,应将头发全部包在帽内,不得有头发外露;戴口罩,必须遮住口、鼻,不外露。
1。
4.将双手消毒后通过缓冲间进入洁净区工作间。
2.工作结束更衣:
2.1.按工作前更衣的逆向程序顺序操作,在二更换下工作服,将工作服按号归位(包括衣服、裤子、帽)。
2.2.在大厅更换工作鞋,离开洁净区。
洁净区工作鞋与生活区的鞋的鞋柜必须具有明显的状态标志标示,禁止混
用。
二、卫生
在药品生产中,由于受到各种要素(制药厂房环境空气、制药用水、操作人员、物料、设备等)的影响,都可能导致药品的微生物污染。
卫生是防止和消除药品在生产过程中遭受污染的重要措施,因此,GMP(药品生产质量管理规范)对各要素都提出了防止污染的基本要求:
1.进入洁净室(区)的人员不得化妆和佩带饰物,不得裸手直接接触药品。
保持双手卫生。
不应有可见的创口。
勤洗澡洗头,没有头皮脱落;勤理发、剃须、剪指甲;并保持干净。
在下述情况必须彻底洗手:
进入本区之前,上厕所后,工作时手被弄脏后.
2.洁净生产区不得存放非生产物品和个人杂物。
3.不得在本区内吸烟、吃食物.
4.离开时,工作服不得穿离本区域。
5.人流、物流要分开;人员、物料要在规定的通道出入,不得穿行,通道要有明显标示。
6.楼道、走廊、电梯间不得放置任何生产用具或其它物品,不得堆放成品及半成品,保持运输通道的清洁、畅通。
7.药品生产人员应有健康档案,直接接触药品的生产人员应每年至少体检一次.传染病、皮肤病患者和体表有伤口者不得从事直接接触药品的生产.
三、岗位注意事项
1.各操作人员要严格执行批生产指令及其所规定的标准操作规程,不得随意变更。
2。
操作间状态标志,应标明生产产品的名称、规格、批号、日期、批量.
2.设备生产状态标志,标明生产产品名称、规格、批号、日期、批量。
3.物料使用前需核对品名、规格、批号、数量。
4.工场剩余的物料、中间产品均应撤离现场。
5.待验、合格、不合格物料要严格管理,不合格的物料要专区存放,有易于识别的明显标志,物料质量状态标志有3种:
待验—黄色标志,标识处于搁置等待状态.
合格—绿色标志,标识允许使用或被批准放行。
不合格—红色标志,标识不能被使用或不准放行.
6.地面必须无积水,无灰尘、无结垢;门窗、室内照明灯、管道、墙面、开关箱外壳等无积尘。
7.室内不得存放与生产无关的物品.
8.使用工具、容器应清洁无异物,无前次产品遗留物。
9.设备内外应无前次生产遗留的药品,无油垢。
凡直接接触药品的机器、设备及管道、工具、容器及辅助用具应在生产结束后及时清洗或消毒。
10.清场范围应包括生产操作的整个区域、空间,包括生产线上、地面、辅助用房等。
11.对整装物料启封后,剩余的散装物料应及时密封,对连续生产的品种,剩余物料放在中间站储存。
12.车间每个工艺用水使用点,长时间不用时,在使用之前需放掉部分水后再行使用。
13.中间站随时保持清洁,不得有散落的物料,进了中间站的物料外包装必须清洁,无浮尘。
14.中间产品在中间站必须按品种、批号码放整齐,不同品种批号之间要有一定距离。
15.外形色泽相近的中间产品的存放,要采取有效的隔离措施,杜绝混药。
16.使用中应随时检查容器的完好情况,如发现裂隙、破口等应及时更换。
17.每班生产完毕做好清洁卫生工作,应将适量消毒液灌注于地漏中,避免对药品生产造成污染。
生产现场必须保持清洁、整齐、安静。
18.生产区内各操作间应设置相应的清洁间或清洁设施,卫生工具齐全,消毒措施完备,通风良好,工作间清洁.用具使用后及时放入清洁间处理干净,工作间内不得存放清洁工具。
清洁工具有清洁剂(消毒剂)要分别存放,不能造成对药品生产环境的污染。
领料岗位:
1.车间领料人负责车间各班组领料与退料方面的工作.
2.领料员凭批生产指令或批包装指令领料领料时,须对所领用物料一一核对,并作好相应记录.
3.核对验收内容
3.1.核对所有物料名称是否相符。
3.2。
原辅料是否有检验报告单,批号、规格、数量是否准确。
4.核对验收准确无误后,即可发送各班组,并记录。
5.进入洁净区的物料必须在外消间清洁,使其符合洁净要求后方可经缓冲区进入洁净区。
6。
每批产品生产结束后,各班组将清场剩余的物料清理后交付领料人员.
7.领料人员将物料一一清点登记后,打包后退库。
8。
退库时,须同仓库接料人员办理好交接.
9.退库物料要求准确、标志明确、包装整齐。
中间站管理:
1.生产前须检查中间站的温、湿度是否符合要求,工作环境是否清洁。
2.进站
2.1.物料进出站时,容器均应密封,外壁清洁。
2。
2.物料进出站时,须认真填写好中间站物料交接记录,收发双方均须在记录上签字。
2。
3。
对进站物料应核对品名、规格、批号、数量、生产日期。
2.4.核对无误后挂好待检牌,围上黄色围栏,填写半成品(中间体)请验单,交质量管理部质监员取样检验.
2。
5。
对进站的中间体或半成品按批号、品名、规格分别摆放整齐,并在容器盖上挂好状态牌,防止混淆。
2。
6。
经检验合格的中间体或半成品,取下“待验”标示牌和黄色围栏,换上“合格”标示牌,围上绿色围栏。
3.出站:
检验合格的半成品、成品才能发放到下工序,发料时核对批号、品名、规格、桶数、重量,填写中间站物料交接记录,双方签字。
4。
经检验不合格的半成品要立即转移到不合格品存放间,并报告生产和质量管理部门.
5.做好物料台帐,做到帐、物、卡相符。
6.对各班组交来的尾料称重后根据不同品种分别存放。
7.下班时搞好本岗位清洁卫生工作。
脱外包装操作:
1。
有数种原、辅材料要拆除外包装时,应先按品名、规格、批号分别堆码整齐,同一品名、规格、批号的物料拆完后再拆另一品名、规格、批号的物品,不允许同时或交叉进行。
2.如是桶装或木箱装,拆下的钉子、封口铅要集中放在一固定容器内。
轻轻除去外包装,将内容物连同内包装一起取出放在干净的容器内,填写包装单,放在该容器内(可扎在袋口上)。
3.复核合格证(包装单)上所填写内容与外包标签内容是否一致。
4。
将去外包装的物料置传递柜或缓冲间中,开启紫外灯并记录时间.
5。
通知车间领料员接料。
6。
搞好本岗位清场工作。
紫外灯操作:
1.每天工作前及下班后开紫外灯照射30分钟。
2.使用紫外灯时,注意观察紫外灯是否正常,有异常情况应及时向负责人反映,必要时进行更换.
3.每天在开启与关闭紫外灯时须认真填写紫外灯使用记录,记录中必须明确紫外灯的开启时间、关闭时间、使用时间和累计使用时间,累计使用时间超过2000小时必须对紫外灯进行更换。
生产过程偏差处理的工作标准
偏差范围
1.1物料平衡超出规定范围
1.2生产过程工艺条件发生偏移、变化。
1.3生产过程中设备突发异常,可能影响产品质量。
1.4产品质量发生偏移。
1.5跑料.
1.6生产中其他异常。
2偏差处理原则:
确认不能影响最终产品的质量,符合质量标准,安全、有效。
3偏差处理程序
3.1凡发生偏差时,发现人必须及时向部门主管报告,并填写偏差报告,内容包括:
品名、规格、批号、数量、工序偏差的内容,发生的过程及可能原因、地点、填表人签字、日期。
将偏差报告单交给车间管理人员,并通知车间主任及质量管理部门。
3.2车间主任及车间管理人员会同有关人员进行调查,根据调查结果提出处理措施.
3.2.1确认不影响产品最终质量的情况下继续加工。
3.2.2确认不影响产品质量的情况下进行反工,或采取补救措施。
3.2.3确认不影响产品质量的情况下采取再回收、再利用措施。
3.2.4确认影响产品质量,应报废或销毁。
3.3车间管理人员将上述调查结果及需采取的措施,写出书面报告,一式两份,经车间主任签字后附于偏差处理单之后,上报质量管理部,经部门负责人审核、批准、签字,一份留质量管理部门,一份送回车间。
4车间按批准的措施组织实施,并详细记入批记录,同时将偏差处理情况附于批记录之后。
5相关事宜:
若调查发现有可能与本批次前后生产批次的产品有关联,则必须立即通知质量管理部负责人,采取措施停止相关批次的放行.直至调查确认与之无关方可放行.
生产车间各种状态标志的管理
1.每一生产操作间或生产用设备、容器应标明所生产的产品或物料的名称、批号、数量等。
2.操作间状态标志,应标明生产产品的名称、规格、批号、日期;
3.设备生产状态标志,标明生产产品名称、规格、批号、日期;
4.容器状态标志,标明容器盛装物料的名称、批号、数量等。
5.生产场所状态标志发放、使用.
5.1状态标志由车间管理人员负责填写发放.
5.2状态标志均由工序负责人负责回收更换.
5.3每批生产结束后,均需对生产场所各种状态标志进行收回和更换。
6.状态标志检查
6.1车间管理人员、QA人员日常巡查各生产区域是否有状态标志、是否在指定位置、状态标志是否准确,与生产是否相符.
6。
2对在检查中发现的问题应及时纠正、更改。
物料使用规范化管理
生产车间根据生产管理部下达的批生产指令填写领料单,向仓库领取.
1.车间领料人员应根据领料单,核对物料品名、规格、批号、数量.
2.领料员领回物料时,车间接收人应检查物料包装严密、完好,标志明显,予以收货.
3.车间领用的物料按物料进入车间一般区域及洁净区域规程操作进入。
4.物料使用前需核对品名、规格、批号、数量、填写记录。
5.对整装物料启封后,剩余的散装物料应及时密封,对连续生产的品种,剩余物料放在中间站储存.
6.生产过程如发现物料存在异常或可疑情况,应暂停使用,并立即向车间管理人员汇报,经确认无误后方可使用。
7.更换品种时,由车间领料员负责将剩余物料退回仓库,仓库保管员负责核对确认后予以接收,并做好记录.
生产车间中间站管理
1中间站、暂存间存放的范围:
1.1中间产品
1.2待包装品
1.3各种可以再利用的物料
1.4待处理的物料
1.5待验的物料
1.6上述范围以外的物料暂存按中间站管理。
2中间站随时保持清洁,不得有散落的物料,进了中间站的物料外包装必须清洁,无浮尘。
3进入中间站的物料容器外必须有状态标志,内容有:
品名、批号、规格、数量、操作日期等.
4中间产品在中间站必须按品种、批号码放整齐,不同品种批号之间要有一定距离。
5状态标记表示:
“红色牌”表示不合格,“绿色牌"表示合格,“黄色牌"表示待验、待查、待返工、待利用、待确认.
6外形色泽相近的中间产品的存放,要采取有效的隔离措施,杜绝混药。
7出入中间站必须有交接单,并且填写中间产品进出站记录.程序为:
7.1进站
7.1.1操作工将要进站的物料填写中间产品交接单(一式二份).写明:
品名、批号、规格、数量、容器数、加工状态、递交人、接交人日期,随同物料递交中间站。
7.1.2中间站管理员按交接单逐项核对无误,检查外包清洁后,在交接单上签字,并填写进出站台帐.双方签字后,由中间站管理员接货,将物料码放到规定位置.由车间及时填请验单.
7.1.3交接单由操作工留一份附于批生产记录中,中间站管理员留一份,贴于台帐背面备查。
7.2出站
7.2.1中间站的物料必须有检验合格的报告单方可发出中间站。
以批生产指令及批生产记录规定的规格标准作为验收依据。
7。
2。
2发出中间站的物料,需由中间站管理员做好记录。
不合格中间产品的管理
1.“中间产品”指制剂生产中各工序所配制或加工的、在成为成品之前必须经过进一步加工处理的产物。
2.不合格中间产品的确认:
中间产品经化验室检验复核后,确定为不符合质量标准要求的中间产品。
3.经质量管理部确认的不合格中间产品由质量管理部下发检验报告书。
4.车间立即将该不合格中间产品移至指定区域,挂上醒目状态标志.
5.生产车间根据不合格项目情况,查明不合格原因,填写不合格中间产品处理报告单,提出意见及措施,报质量管理部审核批准。
不合格中间产品处理报告单内容包括:
品名、批号、生产数量、判定不合格依据、检验单号、处理意见、填报日期等。
6.生产车间按照批准的措施进行处理,并做好详细记录。
7.经过处理后能达到合格要求的,报质量管理部检验,检验合格后作为正常合格品使用。
8.不能处理或处理后仍不合格的按不合格物料管理规程的程序执行。
9.涉及到质量事故的按质量事故管理规程执行.
10。
不合格中间产品在任何情况下都不得进入下道工序继续加工。
紫外灯使用的标准管理
1紫外灯使用范围
1.1紫外灯使用的范围主要是洁净生产区的房间.
1.2具体包括各操作间、中间站、容器存放间、车间内走廊等.
2紫外灯的使用时间
2.1每次生产前20分钟为紫外灯照射时间,生产结束后也应开启紫外灯30分钟.
2.2如遇特殊情况紫外灯照射时间可适当延长30分种.
3注意事项
3.1使用紫外灯时,注意观察紫外灯是否正常,有异常情况应及时反映给车间,必要时进行更换。
紫外灯使用时间超过2000小时,及时更换新的灯管。
3。
2及时填写紫外灯使用记录,并由使用者签名。
生产事故管理规程
1生产事故的范围
凡生产操作中,因违反工艺规程、标准操作规程、错误操作或安排不当造成原辅料、半成品、包装材料和成品损失的,均属生产事故。
2生产事故的等级划分。
2.1造成原辅料、包装材料,半成品和成品报废、返工或停产,直接经济损失按成本价计在20000元以上的为重大生产事故.
2.2造成原辅料、包装材料,半成品和成品报废、返工或停产,直接经济损失在20000元以下2000元以上的为一般生产事故.
2.3造成原辅料、包装材料、半成品和成品报废、返工或停产,直接经济损失在2000元以下的为微小生产事故。
3生产事故的调查处理。
3.1重大生产事故由生产副总经理组织生产部、设备工程部、质量管理部等有关部门进行调查和处理。
3.2一般生产事故由生产管理部会同质量管理部、物料管理部和生产车间等有关部门进行调查处理。
3.3微小生产事故由所在车间主任会同质量管理部、设备工程部、仓库等有关部门和班组长进行调查和处理.
3.4生产事故发生后,应由负责单位组织召开事故分析会,按事故“三不放过”(即事故原因分析不清不放过,事故责任者和群众没有受到教育不放过;没有防范措施不放过)的原则,找出事故原因,明确事故责任者,提出防范措施.
3.5根据生产事故的情节和性质,可分别给予责任者批评教育、经济处罚。
3.6对重大的生产事故和隐瞒事故的有关责任单位和人员,经查实后,应从重从严处罚,对制止生产事故的发生和扩大的有关人员,应予以表扬和奖励。
4生产事故的报告
4.1生产事故调查处理完毕,应由负责单位将书面调查处理意见上报主管领导。
报告时间:
微小事故和一般事故不超过三天,重大事故不超过七天。
经领导批准后予以通报。
重大生产事故在公司范围内通报,一般生产事故和微小质量事故在车间范围内通报。
4.2生产事故处理完毕,应由负责单位填写生产事故处理记录,并存档。
安全生产管理规程
1基本原则
1.1要坚决贯彻“隐患险于明火,防范胜于救灾,责任重于泰山"的观点和“安全第一,预防为主”的生产方针,严格执行国家劳动安全法规。
1.2实行企业法人是企业安全生产第一责任人和“管生产必须同时管安全"的原则.
1.3各部门负责人为本部门安全生产第一责任人,带头严格执行安全生产法和各项安全管理制度。
2安全教育
2.1操作工必须经过安全生产教育和培训,具备必要的安全生产知识,熟悉有关的安全生产规章制度和安全操作规程,掌握本岗位的安全操作技能。
2.2未经安全生产教育的人员,不得上岗作业。
2.3每年安全教育(集中培训)不少于二次,每次不少于2小时;
2.4车间负责人要对新招员工、临时工、变换工种的工人进行上岗前的安全、消防知识教育。
2.5新职工所在班组的班组长要对其进行安全教育,在日常工作安排中,注意以老带新,使之共同促进、共同提高。
3生产操作安全要求
3.1各部门布置生产工作任务时要强调安全工作;
3.2生产操作人员认真执行各项规章制度,在操作中要思想集中、严格按岗位操作规程操作,不得违章操作,对违章指挥有权拒绝。
3.3机器运行过程中,操作人员不得离开;
3.4机器上的安全防护设备必须按要求安装,否则不得开机;
3.5发现异常现象应停机检查;
3.6在运行中的设备万一发生故障,必须关掉总电闸,防止故障蔓延;
3.7电器出现问题时必须找电工来检查维修.
4消防安全要求
4.1生产区严禁明火,各部门如必须用火,需经批准;
4.2生产区内严禁吸烟;
4.3生产用电炉要专人看管,严禁用电炉烤火;
4.4中途停产,或法定休息日,各部门均要关闭总电闸;
4.5消防器材不得挪作他用,并定期检查,及时更换,保证其有效性;
4.6万一发现火警要立即关闭电闸,拨打119报火警,采取灭火措施。
5安全员职责
5.1公司设安全员一人,负责公司安全生产工作。
5.2车间由车间工艺员或设备员兼任安全工作。
5.3安全员应经常检查车间使用的设备、设施及安全防护装置,保证正常运行,安全可靠。
5.4若发现隐患,应及时报告、及时处理。
6安全检查
6.1车间组织安全员、班组长不定期对车间进行安全检查,对安全隐患制定整改措施。
6.2生产操作人员应认真学习所操作的机器设备的有关知识,按规定做好维护保养工作,发现异常情况正确分析、判断、及时处理。
7安全生产事故处理
7.1安全生产事故的划分、调查处理、报告参照《生产事故处理管理规程》处理.
7.2若造成人员伤亡的安全事故,必须报上级有关部门。