机械设计制造编程数控和PLC.docx
《机械设计制造编程数控和PLC.docx》由会员分享,可在线阅读,更多相关《机械设计制造编程数控和PLC.docx(32页珍藏版)》请在冰豆网上搜索。
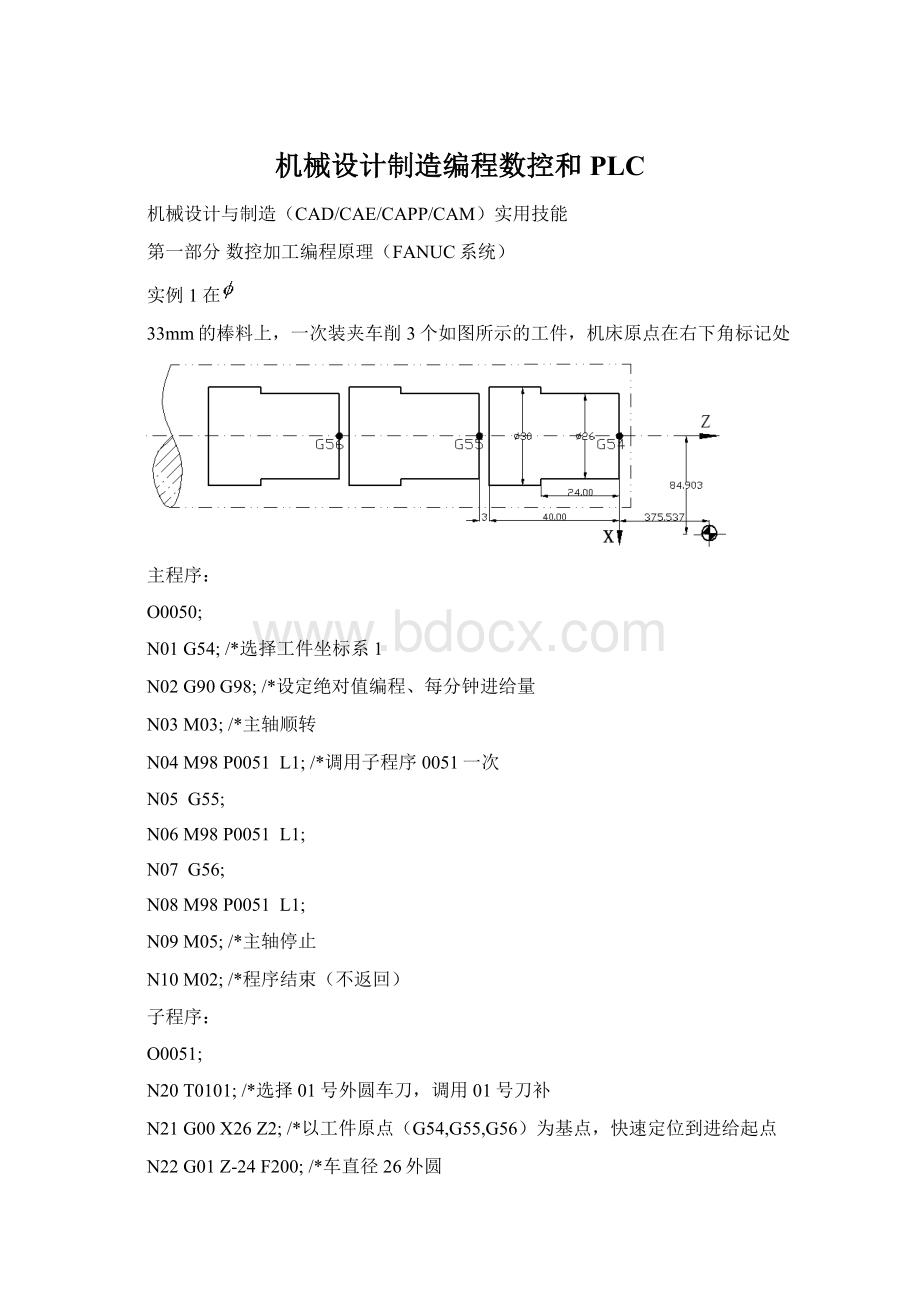
机械设计制造编程数控和PLC
机械设计与制造(CAD/CAE/CAPP/CAM)实用技能
第一部分数控加工编程原理(FANUC系统)
实例1在
33mm的棒料上,一次装夹车削3个如图所示的工件,机床原点在右下角标记处
主程序:
O0050;
N01G54;/*选择工件坐标系1
N02G90G98;/*设定绝对值编程、每分钟进给量
N03M03;/*主轴顺转
N04M98P0051L1;/*调用子程序0051一次
N05G55;
N06M98P0051L1;
N07G56;
N08M98P0051L1;
N09M05;/*主轴停止
N10M02;/*程序结束(不返回)
子程序:
O0051;
N20T0101;/*选择01号外圆车刀,调用01号刀补
N21G00X26Z2;/*以工件原点(G54,G55,G56)为基点,快速定位到进给起点
N22G01Z-24F200;/*车直径26外圆
N23X30;/*车台阶面
N24Z-43;/*车直径30外圆
N25G00X50Z20;/*快速退刀至换刀点
N26T0100;/*取消01号刀刀补
N27T0202;/*选择切断刀
N28G00X34Z-40;/*定位到切断进给起点(进给起点不接触坯料)
N29G01X-1F200;(G01程序中必须含有F指令)
N30G00X34;/*退刀
N31X50Z20;/*快速退刀至换刀点
N32T0200;
N33M99;/*子程序结束,返回主程序
运行程序前,设置零点偏置值(工件原点相对于机床原点的偏置)并输入数控系统:
坐标轴
G54
G55
G56
X(两倍)
-169.806
-169.806
-169.806
Z(实际值)
-375.537
-418.537
-461.537
实例2复合固定循环应用
如图,进行成型粗车短轴,X方向退刀量为14mm,Z方向退刀量14mm,精车削预留量X方向预留量0.5mm,Z方向为0.25mm,分割次数为3,粗车进给率0.3mm/r,主轴转速180r/min。
程序:
O0600;
N10G50X260Z220;/*G50对刀
N11G30U0W0T0100M03M08;
/*G30第二参考点返回(第二参考点也是机床上的固定点,它和机床参考点之间的距离由参数给定,第二参考点指令一般在机床中主要用于刀具交换);粗车不用刀具补偿
N12G00X220Z160;/*快速定位到车削起始点C
N14G73U14W14R3;/*退刀量分别为14mm(到B点)
N16G73P18Q28U0.5W0.25F0.3S180;
N18G00X80W-40;/*Z轴以C为基点,进给到精车起点
N20G01W-20F0.15S600;
N22X120W-10;
N24W-20S400;
N26G02X160W-20R20;
N28G01X180W-10S280;
N30G30U0W0T0202;/*G30第二参考点返回,换刀
N32G70P18Q28;
N34G30U0W0M09;
N36M30;/*程序结束并返回
/*精、粗车共用程序段N18~N28,粗车中的F、S、T按G73中指定的为准,精车中的F、S、T按程序段N18~N28中指定的为准;粗车中的刀尖补偿功能无效,精车中的刀尖补偿功能有效。
实例3螺纹车削复合循环(除第一次车削深度外,其余深度自动计算)
如图所示零件轴上的一段直螺纹,螺纹高度3.68,导程为6,螺纹尾端倒角为1.1L,刀尖角为60°,第一次车削深度为1.8,最小车削深度为0.1,精车余量为0.2,精车削次数为1,螺纹车削前先精车外圆柱面。
程序:
O0022;
N01G50X80Z130;/*对刀
N02G30U0W0;/*返回第二参考点,选刀
N03G96S200T0101M08M03;/*G96设定主轴线速度
N04G00X68Z132;
N05G42G01Z130F0.2;/*G42刀尖半径右补偿
N06X68Z9F0.2;
N07G40G00U10;/*G40刀尖半径补偿取消
N08G30U0W0;/*换刀
N09G97S800T0202M08M03;/*G97设定主轴转速
N10G00X80Z130;/*定位到对刀点
N11G76P01(精车次数)11(螺纹尾端倒角)60(刀具角度)Q100(最小车削深度)R200(精车余量);
N12G76X60.64Z25P3680(螺纹深度)Q1800(第一次车削深度)F6;
/*在上述两个程序段中,P,Q,R地址后的数值应以无小数点的形式表示!
N13G30U0W0M09;
N14M30;
实例4轴类零件车削综合
由毛坯尺寸为
72mm×120mm的铝棒料车削如图所示的工件
步骤:
1确定装夹方式:
由于轴的长度不是很长,采用工件的左端面和
72的外圆面作为定位基准,使用普通三爪卡盘夹紧。
取工件的右端面中心为工件坐标原点,对刀点选在(150,60)处。
2确定数控加工刀具
3确定加工工序
4合理选择切削用量
5编写加工程序:
O0026;
N01G50X150Z60;/*对刀
N02S450M03T0101;
N03G00X74Z0M08;
N04G01X-1F0.25;/*车端面
N05G00X80Z5;/*退刀(与X74Z0比较…)
N06X150Z60;
N07T0100M01;/*程序选择停止
N08T0202M03;
N09S650;
N10G00X74Z5;
N11G71P13Q27U0.5W0.1(精车预留量)D2F0.3S650;/*调用粗车循环
N12G42G00X15Z0.5;
N13G01X20Z-2F0.15;/*车第一个倒角
N14Z-15.2;/*车螺纹外径
N15X18Z-20;/*车退刀槽斜面
N16Z-25;/*车退刀槽
N17X29;/*车台阶面
N18X35Z-28;/*车第二个倒角
N19Z-42;
N20G02X50Z-50R8;
N21G01Z-60;
N22X60.7Z-80;
N23X66;
N24X70Z-82;
N25Z-94;
N26X74;/*退刀
N27G40;/*取消刀补
N28G00X150Z60;
N29M01;/*主轴停
N30T0303M03;(T02为粗车刀,T03为精车刀)
N31S650;
N32G70P13Q27;
N33G00X150Z60;
N34T0300M01;
N35T0404M03S600;
N36G00X20Z5;
N37G92X19Z-22.5F1.5;/*车削螺纹循环
N38X18.6;
N39X18.2;
N40X18.052;
N41G00X150Z60;
N42T0400M01;
N43T0505M03S600;
N44G00X74Z-94M08;
N45G01X-1F0.1;/*切断
N46G00X150Z60M09T0500;
N47M30;
(%%C——
;%%d——°;%%%——%;%%p——±;%%O——给文字添加上划线;“%%u——给文字添加下划线;输入不对称公差:
如上差+0.1,下差-0.2,输"+0.1^-0.2",选中它们,点工具栏里的"b/a"堆叠按钮即可;斜杠(/)用于定义分数形式)
实例5盘类零件数控车削
步骤:
1确定装夹方式:
由于零件壁厚较大,采用工件左端面和外圆作定位基准,使用普通三爪卡盘夹紧,并且一次装夹完成全部加工。
取工件的右端面中心为工件坐标系原点,对刀点选在(200,200)处。
2确定加工刀具
3确定加工工序
4合理选择切削用量
5编写加工程序:
方法1:
粗车外轮廓→精车外轮廓→粗镗内孔→精镗内孔
O0001;
N01G50X200Z200;
N02S400M03T0101;
N03G00X62Z0M08;
N04G01X0F0.15;
N05G00Z1;
N06X200Z200T0100;
N07T0202;
N08G00X64Z2;
N09G71P10Q16U0.4W0.1D1.5F0.3S400;/*粗车外轮廓循环,刀T02
N10G42G00X46.8Z0;
N11G01X50Z-6;
N12X54;
N13X56W-1;
N14Z-20;
N15X62Z-23;/*令刀具完全切出工件
N16G40G00X65;
N17X200Z200T0200;
N18T0404;
N19G00X64Z2;
N20G70P10Q16;/*精车外轮廓,刀T04
N21G00X200Z200T0400;
N22T0303;
N23G71P21Q30U-0.4W0.1D1.5F0.2S400;/*粗镗内孔循环,刀T03
N24G42G00X32;
N25G01Z0F0.08;
N26G02X24Z-4R4;
N27G01Z-15;
N28X14;(直径为15mm孔,由于左端有夹具不能车削)
N29Z17;/*退刀
N30G40G00X64Z2;
N31G00X200Z200T0300;
N32T0505;
N33G00X12Z2;
N34G70P21Q30;/*精镗内孔,刀T05
N35G00X200Z200T0500;
N36M09;
N37M05;
N38M30;
方法2:
粗车外轮廓→粗镗内孔→精车外轮廓→精镗内孔
O0002;
N01G50X200Z200;
N02S400M03T0101;
N03G00X62Z0M08;
N04G01X0F0.15;
N05G00Z1;
N06X200Z200T0100;
N07T0202;
N08G00X64Z2;
N09G71P10Q16U0.4W0.1D1.5F0.3S400;/*粗车外轮廓循环,刀T02
N10G42G00X46.8Z0;
N11G01X50Z-6;
N12X54;
N13X56W-1;
N14Z-20;
N15X62Z-23;
N16G40G00X65;
N17X200Z200T0200;
N18T0303;
N19G00X12Z2;
N20G71P21Q26U-0.4W0.1D1.5F0.2S400;/*粗镗内孔循环,刀T03
N21G42G00X32;
N22G01Z0F0.08;
N23G02X24Z-4R4;
N24G01Z-15;
N25X14;
N26Z17;
N27G40G00X200Z200T0300;
N28T0404
N29G00X64Z2;
N30G70P10Q16;/*精镗内孔,刀T04
N31G00X200Z200T0400;
N32T0505;
N33X12Z2;
N34G70P21Q26;/*精镗内孔,刀T05
N35G00X200Z200T0500;
N36M09;
N37M05;
N38M30;
实例6孔加工固定循环
如图,工件要加工3种类型的孔:
6个直径为10mm的通孔、4个直径为20mm的沉孔、3个直径为50的通孔。
使用刀具分别为T01、T02、T03,Z轴主轴端面作为编程起始点,使用刀具长度正补偿G43,3把刀的长度补偿值存入H01、H02、H03中。
工件坐标系原点:
X、Y轴在机床参考点,Z轴在初始平面,用G92设置工件坐标系。
程序:
O3530;
N01G92X0Y0Z0;
/*设置工件坐标系原点,X、Y轴在机床参考点,Z轴在距工件顶面40mm处
N02G90G00Z200;
N03T01M06;
N04G43Z0H01;
N05S600M03;
N06G99(返回R点平面)G81(定点钻)X100Y-150(钻孔位置)Z-123R-77(孔数据)F120;/*钻小孔
N07Y-210;
N08G98Y-270;/*返回初始面
N09G99X560;
N10Y-210;
N11G98Y-150;
N12G00X0Y0M05;
N13G49Z200;/*刀具长度补偿取消
N14T02M06;
N15G43Z0H02;
N16S300M03;
N17G99G82X180Y-180Z-110R-77P300F70;
/*钻7号沉孔,孔底停300ms,返R面
N18G98Y-240;
N19G99X480;
N20G98Y-180;
N21G00X0Y0M05;
N22G49Z200;
N23T03M06;
N24G43Z0H03;
N25S200M03;
N26G99G85X330Y-150Z-123R-37F50;/*镗孔
N27Y-210;
N28G98Y-270;
N29G00X0Y0M05;
N30G49Z0;
N31M30;
实例7编制如图心形凸轮零件的加工程序,毛坯加工余量上下底面为5mm,其余2mm。
步骤:
1工艺分析,确定定位基准:
首先以顶面为基准加工底面、安装孔、定位孔;然后以两孔和底面定位,一次装夹将所有表面和轮廓全部加工完成。
2工件装夹方案确定
3确定工件坐标系、对刀位置和对刀方法:
根据工艺分析,工件坐标原点设在安装孔的轴线上,且在工件安装后(两次安装)的上表面处;对刀位置与工件坐标原点重合,采用手工对刀。
4数值计算:
根据已确定的加工路线和允许的编程误差,计算出构成凸轮轮廓几何元素的交点坐标(0,31.633)(-13.019,-26.820)(-33.825,-4.072)(-17.275,43.715)(-9.966,42.66)(9.966,42.66)(17.275,43.715)(33.825,-4.072)(13.019,-26.820)
5编制程序
O8798;
N01G90G17G40G49G80G54;
/*绝对坐标编程、XY平面选择、刀具半径和长度补偿取消、钻孔固定循环取消、第一坐标系设置
N02T01M06;
N03S220M03;
N04G00X-50Y-40Z20;
/*第一次装夹后,Z轴原点位于剖视图的左端面和安装孔轴线交点,X正向为左,Y正向向上
N05G43G01Z5(Z为补偿轴的终点坐标)F44H01;
/*G43Z5H1;(如H1中的补偿值为3,则实际刀具的位置为5+3=8)
N06M08;
N07G01Z-2F44;/*粗加工底面,以下为走刀路线
N08X50Y-40;
N09X50Y-10;
N10X-50Y-10;
N11X-50Y20;
N12X50Y20;
N13X50Y50;
N14X-50Y50;
N15X-50Y80;
N16X50Y80;
N17G00Z20;
N18G01Z-4.5F44;
N19X50Y-40;
N20X50Y-10;
N21X-50Y-10;
N22X-50Y20;
N23X50Y20;
N24X50Y50;
N25X-50Y50;
N26X-50Y80;
N27X50Y80;
N28G00Z20;
N29S500M03;
N30G43G01Z5F44H02;/*精加工底面
N31X-50Y-40;
N32G01Z-5;
N33X50Y-40;
N34X50Y-10;
N35X-50Y-10;
N36X-50Y20;
N37X50Y20;
N38X50Y50;
N39X-50Y50;
N40X-50Y80;
N41X50Y80;
N42M05;
N43M09;
N44G49G00Z20;
N45T02M06;
N46S900M03;
N47G43G00Z5H03;
N48M08;
N49G98(返回起始平面)G81X0Y0Z-2R3F80;/*定点钻循环
N50X0Y30;
N51G80;
N52G49G00Z20;
N53M05;
N54M09;
N55T03M06;
N56S450M03;
N57G43G00Z30H04;
N58M08;
N59G98G83X0Y0Z-42R2Q5(指定每次的切削量)F45;
/*深孔钻循环(排屑)
N60G80;
N61G49G00Z20;
N62M05;
N63M09;
N64T04M06;
N65S450M03;
N66G43G00Z30H05;
N67M08;
N68G98G83X0Y30Z-23R2QF45;
N69G80;
N70G49G00Z20;
N71M05;
N72M09;
N73T05M06;/*铰孔循环
N74S30M03;
N75G43G00Z30H06;
N76M08;
N77G98G81(也作铰孔)X0Y0Z-42R2QF10;
N78G80;
N79G49G00Z20;
N80M05;
N81M09;
N82T06M06;
N83S30M03;
N84G43G00Z30H07;
N85M08;
N86G98G81X0Y30Z-23R2QF10;
N87G80;
N88G49G00Z20;
N89M05;
N90M09;
N91M30;
装夹变换...
N101G54G49G90G80G40G17;
N102T07M06;
N103S290M03;
N104G00X60Y-50;
/*第二次装夹后,Z轴原点位于剖视图的右端面和安装孔轴线交点,X正向为右,Y正向向上
N105G43G00Z20H08;
N106M08;
N107G01Z-45F44;
N108G41G01X60Y-31.633F44D08;/*半径补偿
N109G01X0Y-31.633;
N110G02X-13.019Y-26.820R20;/*粗铣外轮廓
N111G02X-33.825Y-4.072R127.5;
N112G02X-17.275Y43.715R30;
N113G02X-9.9660Y42.660R10;
N114G03X9.9660Y42.660R20;
N115G02X17.275Y43.715R10;
N116G02X33.825Y-4.072R30;
N117G02X13.019Y-26.820R127.5;
N118G02X0Y-31.633R20;
N119G01X-40Y-31.633;
N120G49G00Z50;
N121G00X60Y-50;
N122G43G00Z20H08;
……
N221G40G01X-60Y-50;/*精铣外轮廓
N222G49G00Z50;
N223S500M03;
N224G00X60Y-50;
N225G43G00Z20H08;
N226G01Z-45F60;
N227G41G01X60Y-31.633F44D09;
N228G01X0Y-31.633;
N229G02X-13.019Y-26.820R20;
N230G02X-33.825Y-4.072R127.5;
N231G02X-17.275Y43.715R30;
N232G02X-9.9660Y42.660R10;
N233G03X9.9660Y42.660R20;
N234G02X17.275Y43.715R10;
N235G02X33.825Y-4.072R30;
N236G02X13.019Y-26.820R127.5;
N237G02X0Y-31.633R20;
N238G01X-40Y-31.633;
N239G40G01X-60Y-50;
N240G49G00Z50;
N241M05;
N242M09;
……
N300T08M06;/*铣上面
N301S220M03;
N302G43G00Z30H09;
N303M08;
N304G01X-20Y0F44;
N305G01Z-2;
N306G01X20Y0;
N307G01Z-4.5;
N308G01X-20Y0;
N309S500M03;
N310G01Z-5;
N311G01X20Y0;
N312G49G00Z50;
N313G00X0Y0;
N314T09M06;
N315S220M03;
N316G43G00Z30H10;
N317M08;
N318G01Z-2;/*倒角(图中未显示)
N319G49G00Z50;
N320M05;
N321M09;
N322M30;
实例8壳类零件加工
如图所示,在数控加工之前已完成底面和直径为80的孔,要求在加工中心上铣上表面、槽和4个螺纹孔。
步骤:
1工艺分析
a.确定定位基准,选择夹紧方案,采用螺钉和压板,压板压在直径为80的孔上,旋紧螺母将工件夹紧;
b.工艺顺序安排