几种注塑成型技术要点.docx
《几种注塑成型技术要点.docx》由会员分享,可在线阅读,更多相关《几种注塑成型技术要点.docx(9页珍藏版)》请在冰豆网上搜索。
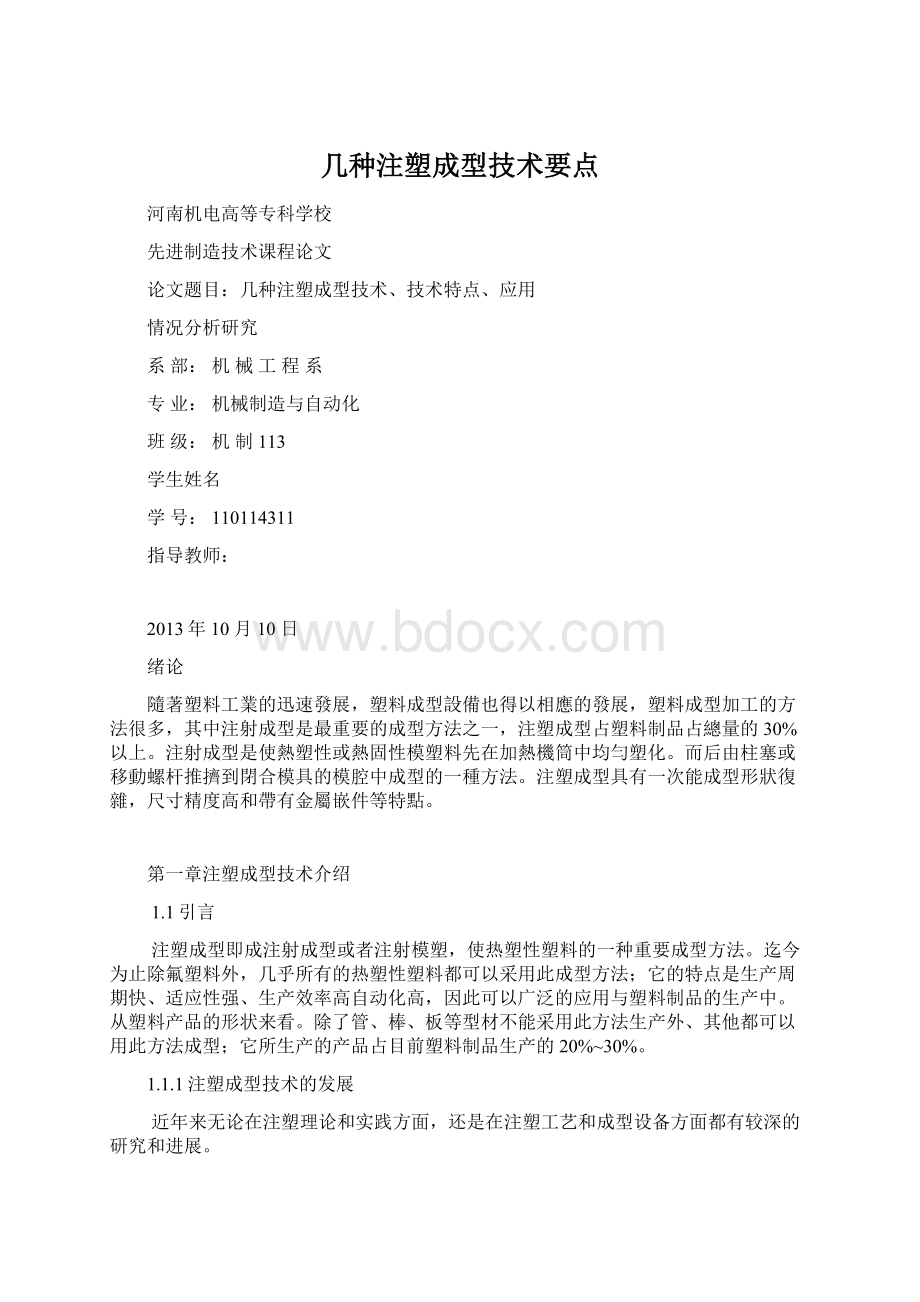
几种注塑成型技术要点
河南机电高等专科学校
先进制造技术课程论文
论文题目:
几种注塑成型技术、技术特点、应用
情况分析研究
系部:
机械工程系
专业:
机械制造与自动化
班级:
机制113
学生姓名
学号:
110114311
指导教师:
2013年10月10日
绪论
隨著塑料工業的迅速發展,塑料成型設備也得以相應的發展,塑料成型加工的方法很多,其中注射成型是最重要的成型方法之一,注塑成型占塑料制品占總量的30%以上。
注射成型是使熱塑性或熱固性模塑料先在加熱機筒中均勻塑化。
而后由柱塞或移動螺杆推擠到閉合模具的模腔中成型的一種方法。
注塑成型具有一次能成型形狀復雜,尺寸精度高和帶有金屬嵌件等特點。
第一章注塑成型技术介绍
1.1引言
注塑成型即成注射成型或者注射模塑,使热塑性塑料的一种重要成型方法。
迄今为止除氟塑料外,几乎所有的热塑性塑料都可以采用此成型方法;它的特点是生产周期快、适应性强、生产效率高自动化高,因此可以广泛的应用与塑料制品的生产中。
从塑料产品的形状来看。
除了管、棒、板等型材不能采用此方法生产外、其他都可以用此方法成型;它所生产的产品占目前塑料制品生产的20%~30%。
1.1.1注塑成型技术的发展
近年来无论在注塑理论和实践方面,还是在注塑工艺和成型设备方面都有较深的研究和进展。
注塑时,首先遇到的是注塑的可成型性,这是衡量塑料能否快速和容易地成型出合乎质量要求的品。
并希望能在满足质量要求的前提下,以最短注塑周期进行高效率生产。
不同的高分子材料对其加工的工艺条件及设备的感性别很大,材料性和工艺条件将最终影响塑料制品的理机械性能,因此全面了解注塑周期内的工作程序,搞清可成型性和成型工艺条件及各种因素的相互作用和影响,对注塑加工有重要意义。
在对充模压力的影响实验表明:
高聚物的非牛顿特性越强,则需要的压越低;结晶型比非结晶型高聚物制品有更大的收收缩,在相变中比容变化较大。
在对注塑过程中大分子取向的机理研究证明聚合物熔体受剪切变形时,大分子由无规卷曲状态解开,并向流动方向延伸和有规则的排列,如果熔体很快冷却到相变温度以下,则大分子没有足够的时间松和恢复到它原来的无规则卷曲的构象程度,这时的聚合物就要处于冻结取向状态,这种冻结取向使注塑制品在双折射热传导以及力学性质方面显示出各向导性。
由于流变学和聚合物凝固过程的形变原因,制品取向可能在一个方向占优势形成单轴取向,也可能在两个方向上占优势,形成双轴取向。
双轴取向会使制品得到综合的机械特性,所以在注塑制品中总希望得到双轴取向制品。
而在纡维抽丝过程中却希望得到单轴取向。
对于取向分布的试验表明:
取向最大是发生在距离制件表面20%的厚度处,发现取向程度随熔体温度与模温减小而增加,而提高注射压力或延长注射时间会增加制品的取向程度。
对聚苯乙烯试样表明:
拉伸强度在平行取向方向上随取向度增加而提高,在垂直方向上则下降。
对聚甲醛的观察表明:
注射时间的加长会使过渡晶区的厚度增加,注射压力的提高会使制品断裂伸长加大。
测试表明:
注塑的残余应力与应变对制品质量有着重要影响,一般注塑制品有三种残余应变形式;A伴随热应力而产生的应变,B与分子冻结取向相关的残余应变,C形体应变,对一般塑料而言注射压力的增加会增加制品中的残余应力,而对ABS不十分明显。
对于制件拉伸特点的分布研究表明:
一般聚合物的密度增加会提高拉伸强度,断裂伸长率和硬度,使冲击强度降低。
综上所述,如何能把这些理论应用到生产实践中去,改善工艺过程中的控制以减少材料,劳动量,达到缩短周期和减少废品的目的。
1.2注塑成型工艺流程
注塑成型过程一般包括加料、塑化、注射、冷却和脱模几个步骤。
由于注射成型是一种间歇过程,因此保持定量加料,以保证操作稳定、塑料均匀最终获得良好制品。
加料过多、受热时间过长等容易引起物料的热降解,同时注塑机的功率损耗增加;加料过少时,料桶内缺少传递介质,模腔内塑料熔体压力降低,难于补塑,容易引起制品出现收缩、凹陷、空洞等缺陷。
加入的塑料在料筒中加热,由固体粒子转变为熔体,经过混合和塑化后,塑化好的熔体被柱塞或螺杆推到塑料桶前端;经过喷嘴、模具浇注系统进入并填满型腔,这一阶段称为“充模”。
在模具中熔体冷却收缩时,继续保持施压状态的柱塞或螺杆,迫使浇口和喷嘴附近的熔体不断补充入模中。
使模腔中的塑料能形成完整而致密的的制品,这一阶段称为“保压”。
当浇注系统中的塑料硬化后,继续保压以不再需要,因此可退回柱塞和螺杆,并加入新料;卸除料桶内塑料中的压力,同时并通入冷水、油或空气等冷却介质,对模具进行进一步冷却;这一阶段称为“冷却”。
实际上冷却过程从塑料从注射入模腔就开始了,它包括从充模完成,保压到脱模前这一段时间。
制品冷却到所需的温度后,就可以人工或机械方式脱模。
所以注塑过程通常由塑化、冲模、保压、冷却和脱模等五个工序组成
。
1.3注塑成型设备
注塑成型机是注塑成型的主要设备;注塑机的类型和规格很多,目前其规格已经统一,以用注塑机‘一次所能注射的聚苯乙烯。
克’为标准。
但对于其分类还没有统一的意见。
有按外形特征分类的,分为立式、卧式、旋转式;也有按塑料在料筒中的塑化方式分类的;也有按结构分类的,分为主赛事和螺杆式。
目前多采用按结构特征来区分,并适当考虑外形。
所以可分为柱塞式和螺杆式两类。
最大注射量在60克以下的注塑机通常为柱塞式,60可以上的多数为移动螺杆式。
注塑机主要有注射系统、锁模系统、模具三部分组成。
1.4注塑成型工艺的主要影响因素
1.4.1料温
塑料的温度是由料筒控制的,多以料筒温度关系到塑料的塑化质量。
选定料筒的温度是,主要着眼于保证塑料塑化良好,能顺利实现注射而又不一起塑料局部降解等。
1.4.2模具温度
塑料充模后在模腔中冷却僵化而得到所需的形状。
模具的温度影响物料熔体充满时的流动行为,并影响塑料制品的性能。
模具的温度实际上决定了塑料熔体体的冷却速度,模具温度是有冷却介质控制的!
1.4.3注射压力
注射压力推动塑料熔体向料筒前端流动,塑料充满模腔而成形,所以它是塑料充满和成型的重要因素。
它主要有三个方面的作用:
(1)推动料筒中塑料箱前端移动,同时使塑料混合和塑化,柱塞必须提供克服固体塑料粒子和熔体在料筒和喷嘴中流动是所引起的阻力;
(2)充模阶段注射压力应克服浇注系统和型腔对塑料的流动阻力,并使塑料获得足够的充模速度及流动长度,使塑料在冷却前能充满型腔;(3)保压阶段注射压力能压实模腔中的塑料,并对塑料因冷却而产生的收缩进行补料,时从不同方向先后进入模腔中的塑料融为一体,从而使制品保持形状精确,获得所需要的性能。
1.4.4注射周期和注射速度
完成一次注射成型所需的时间称注射周期。
它由注射、保压时间、冷却和加料时间以及开模、辅助作业和闭模时间组成。
注射速度常用单位时间内柱塞移动的距离表示,有时也用重量或容积流率表示;注射速度主要影响塑料熔体在模腔内流动的行为,并影响模腔内压力、温度以及制品的性能。
第二章注塑成形的特点与研究概况
2.1气体辅助注射
气体辅助注射成型是从注射成型发展而来的。
这一工艺克服了注射成
型的一个重要的缺限:
缩痕。
由于塑料固有的绝缘性,部件腔壁的冷却速度不均匀,导致了缩痕的产生。
气体辅助射出成型的工作原理是通过“欠料注射法”将树脂注入模腔中,接着将气体注入熔化的树脂。
由于低压高温度,气体能够沿阻力最小的路径进入铸件的各个部分。
当气体穿过成型件时,它会将壁厚部分的树脂熔液均匀地推向铸件的其他部分。
气辅设备包括气辅控制单元和氮气发生装置。
它是独立于注塑机外的另一套系统,其与注塑机的
唯一接口是注射信号连接线。
注塑机将一个注射信号注射开始或螺杆位置传递给气辅控制单元之后,便开始一个注气过程,等下一个注射过程开始时给出另一个注射信号,开始另一个循环,如此反复进行。
气辅注塑所使用的气体必须是隋性气体(通常为氮气),气体最高压力为35MPa,特殊者可达70MPa,氮气纯度≥98%。
气辅控制单元是控制注气时间和注气压力的装置,它具有多组气路设计,可同时控制多台注塑机的气辅生产,气辅控制单元设有气体回收功能,尽可能降低气体耗用量。
今后气辅设备的发展趋势是将气辅控制单元内置于注塑机内,作为注塑机的一项新功能。
气辅注塑是采用所谓的“短射”方法,即先在模腔内注入一定量的料(通常为满射时的70-95%),然后再注入气体,实现全充满过程。
熔胶注射量与模具气道大小及模腔结构关系最大。
气道截面越大,气体越易穿透,掏空率越高,适宜于采用较大的“短射率”。
这时如果使用过多料量,则很容易发生熔料堆积,料多的地方会出现缩痕。
如果料太少,则会导致吹穿
如果气道与流料方向完全一致,那么最有利于气体的穿透,气道的掏空率最大。
因此在模具设计时尽可能将气道与流料方向保持一致
2.2粉末冶金
粉末冶金是最早用来制造金属基复合材料的方法,早在1961年Kopenaal等人就利用粉末冶金制造纤维体积含量为20%到40%的碳铝复合材料,但由于性能很低,也无有效措施加以提高,这种反方法已不再用来制造长纤维增强复合财力,而主要用来制造颗粒或晶须增强金属基复合材料。
2.2.1金属粉末工艺流程图
混合
烧结
冷压
成品
成品
热压
→→
颗粒(晶须)
→
→→→
合金粉末
→
封装除氧
成品
挤压
→→→
粉末冶金法制造金属基复合材料的工艺流程图
常规的粉末冶金的工艺流程事先将混合粉末冷压成型,在经过烧结完成复合,其特点是设备要求相对较低,便于大批生产,制品的致密程度较低、空隙率较高,性能较低,对于力学性能要求较高的零件,通常采用挤压、轧制、锻压等二次成型手段进行致密处理。
但对于有润滑的耐磨零件,适当的空隙存在对连续油膜的形成、减少摩擦系数有利,则无需进行致密处理。
常用机械粉碎、雾化、物理化学法制取粉末。
制取的粉末经过筛分与混合,混料均匀并加入适当的增塑剂,再进行压制成型,粉粒间的原子通过固相扩散和机械咬合作用,使制件结合为具有一定强度的整体。
压力越大则制件密度越大,强度相应增加。
有时为减小压力合增加制件密度,也可采用热等静压成型的方法
将压制成型的制件放置在采用还原性气氛的闭式炉中进行烧结,烧结温度约为基体金属熔点的2/3~3/4倍。
由于高温下不同种类原子的扩散,粉末表面氧化物的被还原以及变形粉末的再结晶,使粉末颗粒相互结合,提高了粉末冶金制品的强度,并获得与一般合金相似的组织。
经烧结后的制件中,仍然存在一些微小的孔隙,属于多孔性材料。
一般情况下,烧结好的制件能够达到所需性能,可直接使用。
但有时还需进行必要的后处理。
如精压处理,可提高制件的密度和尺寸形状精度;对铁基粉末冶金制件进行淬火、表面淬火等处理可改善其机械性能;为达到润滑或耐蚀目的而进行浸油或浸渍其它液态润滑剂;将低熔点金属渗入制件孔隙中去的熔渗处理,可提高制件的强度、硬度、可塑性或冲击韧性等。
2.2.2粉末冶金的应用
1、在汽车行业的应用。
据文献报道,2003年,北美粉末冶金机械零件在轿车中的使用为12.3kg;日本轿车平均每辆为6.5kg;欧洲平均每辆车为7kg;国内上海普通桑塔纳轿车每辆为6kg;上海通用别克轿车为12kg左右。
2、在家电行业。
随着国内空调机、冰箱等家电迅速发展,粉末冶金在该领域得到了发展,其中压缩机中活塞、连杆、缸体、缸盖等重要部件都采用粉末冶金。
3、在电动工具行业。
由于电动工具中存在大量齿轮,而粉末冶金齿轮的制造成本低、噪声低、自润滑性能好等优点,不少电动具制造厂家使用粉末冶金替代机加工齿轮,扩大粉末冶金产品的应用范围。
2.3低压结构发泡注塑成型技术
随着高分子成型工艺技术的发展,结构发泡注塑与气体辅助注塑两项成型工艺越加完善,应用领域不断扩大。
但是,随着人们生活水平的日渐提高,对很多产品提出了更高的要求,比如在音响号筒领域大家越来越关注音质效果以及产品的耐用性、外观效果等等。
传统的注塑已经很难满足这些塑件的需求,低压结构发泡注塑的诞生填补了传统注塑技术的空白。
最早是20世纪20年代初期的泡沫胶木,用类似制造泡沫橡胶的方法制取;30年代出现硬质聚氨酯泡沫和聚苯乙烯泡沫;40年代有聚乙烯、聚氯乙烯、环氧树脂、酚醛泡沫;50年代则有可发性聚苯乙烯泡沫和软质聚氨酯泡沫。
现在,基本上所有的塑料,包括热塑性和热固性的都可以发泡。
工业上的制备方法有:
挤出发泡、注塑发泡、模塑发泡、压延发泡、粉末发泡和喷涂发泡等等。
其中,注塑发泡是最重要的成型方法之一,也是低压结构发泡注塑的前身。
2.3.1发泡工艺流程
1、将我们通常用的材料如:
ABS、HIPS、PP等(注意必须是成型温度与AC发泡剂发泡温度接近的塑料),与AC进行一定比例的混合,通常比例为0.5%-5%。
2、混合均匀的材料通过注塑机螺杆共混,此时喷嘴的阀门关闭。
3、气体辅助设备运转向密封模具内打入低压氮气,抑制发泡剂在瞬间发泡。
4、当模腔压力达到0.8-2.0MPA时,自锁式喷嘴阀门打开开始注射,熔融塑料通过模具内的热流道的加热,让发泡剂达到发泡温度。
5、塑料即将填满模腔时(通常在90%-95%左右),气体辅助设备开始排气,与此同时塑料件内部也充分进行发泡,最后添满整个模腔。
2.3.2常见的缺陷及解决
1、注塑件缩水:
由于填充过于饱和经常会造成发泡不充分,因而造成筋位和柱位的缩水。
解决方法:
减少注射量、降低注气时间、降低注气压力、提高喷嘴温度。
2、注塑件欠注:
由于注塑量不足经常会有欠注现象。
解决方法:
适当增加注塑量。
3、 熔体破裂、气痕:
由于充填不均匀或者发泡的时机不对,在注塑件表面会有橘皮状缺陷或者有类似于熔接痕的缺陷。
解决方法:
调整注塑件充填平衡,适当降低浇口位置填充速度、降低气体压力,适当提高气体排放的斜率、降低料管温度,避免材料在料管中提前发泡。
其他的缺陷处理办法与传统注塑比较接近,在此不再重复说明。
主要是通过气体辅助设备调整模具内部的压力,进而控制发泡剂发泡的时机
2.4热固塑料注射成型
2.4.1热固塑性成型发展
热固性树脂在受热或在固化剂的作用下,能发生交联而变成不熔不溶状态的树脂。
热固性塑料在热固性树脂中加入增强材料、填料及各种助剂所制得的制品称为热固性塑料热固性塑料具有耐热好、刚性大、价格低等优点,随着塑料工业的发展,热固性塑料制品的应用也越来越广泛。
20世纪60年代前,→压制和挤出工艺加工20世纪60年代后,→注射成型工艺。
其中日本已有85%的热固性塑料制品是用注射成型方法获得的,我国70年代开始推广应用热固性塑料注射成型工艺,目前只占所有热固性塑料制品的3%~4%,可见热固性塑料注射成型工艺技术在我国是大有发展空间。
2.4.2成型原理及工艺过程
排气
注射成型料筒
热固性塑料
低粘度塑性体
加热
→
固体
模腔
注射反应冷却
→→→
热固性塑料受热成型过程中不仅发生物理状态的变化,而且还发生不可逆的化学变化。
这种历程的快慢取决于温度和经历的时间。
为使注射过程顺利进行,应控制使物料通过喷嘴时必须达到最好的流动性,物料进入模腔后,反应基团与加入的固化剂发生交联反应,使线性树脂逐渐变成体型结构。
反应过程中,会逐渐释放出低分子物(如氨、水等),必须及时排出,才能保证反应顺利进行。
当交联反应进行到使模内物料的物理—力学性能达到最佳值时,即可以从模内脱出,成为制品。
2.4.3热固性材料加工的要求
1、在工艺条件方面,对于温度、压力与时间的控制均要因料筒、模具内物料的运动与反应阶段而进行选择。
2、在原料方面,不同塑料顺利变成注射制品的难易程度是不同的。
例如,酚醛塑料具有较好的成型工艺性。
3、在设备方面,要求设备有精确的加热控温精度,较高的注射压力和较高的锁模力吨位。
注射成型机的锁模系统还应伴随有排气动作等。
2.5电磁动态塑化注射成型
2.5.1电磁动态塑化注射成型简介
聚合物动态注射成型技术以及实现该技术的塑化注射装置。
注射成型加工过程中使注射螺杆产生轴向脉动的激振力,可以利用电磁、机械、液压等方式来产生。
电磁式振动塑化注射装置结构紧凑、振动频率高;模块化设计的液压激振装置结构简单,输出功率高,方便对传统塑料注射机进行改造。
新技术具有加工能耗低制品质量高等特点,通过控制振动频率与振幅可以对制品的质量进行调控。
2.5.2电磁动态塑化注射成型技术
注射成型过程中引入振动,使注射螺杆在振动力的作用下产生轴向脉动,则成型过程料筒及模腔中熔体的压力将发生脉动式的变化,改变外加振动力的振动频率与振幅,熔体压力的脉动频率与振幅也会发生相应的变化,熔体进入模腔进行填充压实的效果也必然会发生相应的变化。
通过调控外加振动力的振动频率与振幅,可以使注射成型在比较低的加工温度下进行,或者是可以降低注射压力和锁模力,从而减小成型过程所需的能耗,减小制品中的残余应力,提高制品质量。
在动态注射成型过程中,塑化计量、注射、保压阶段螺杆均处于周期性脉动状态。
在不同外加振动频率与振幅下,动态注射充模过程的模腔压力变化的。
外加振动频率或振幅为零的情况相当于传统的注射成型充模。
动态注射充模过程的模腔压力上升比较快,而且可以达到比较高的峰值,表明该过程的压力损耗要小,这主要是熔体表观粘度下降的结果。
相应地,熔体的充模能力也将有所提高。
参考文献
【1】夏巨谌塑形成型工艺及设备北京:
机械工业出版社2011,7
【2】黄家康复合材料成型技术及应用北京:
化学工业出版社2011,2
【3】王贵恒,成都科技大学高分子材料成型加工原理北京:
化学工业出版社2012,7
【4】于化顺金属基复合材料及其制备技术北京:
化学工业出版社2006,10
【5】孙燕华先进制造技术北京:
电子工业出版社2007,6