九仟案例手册.docx
《九仟案例手册.docx》由会员分享,可在线阅读,更多相关《九仟案例手册.docx(33页珍藏版)》请在冰豆网上搜索。
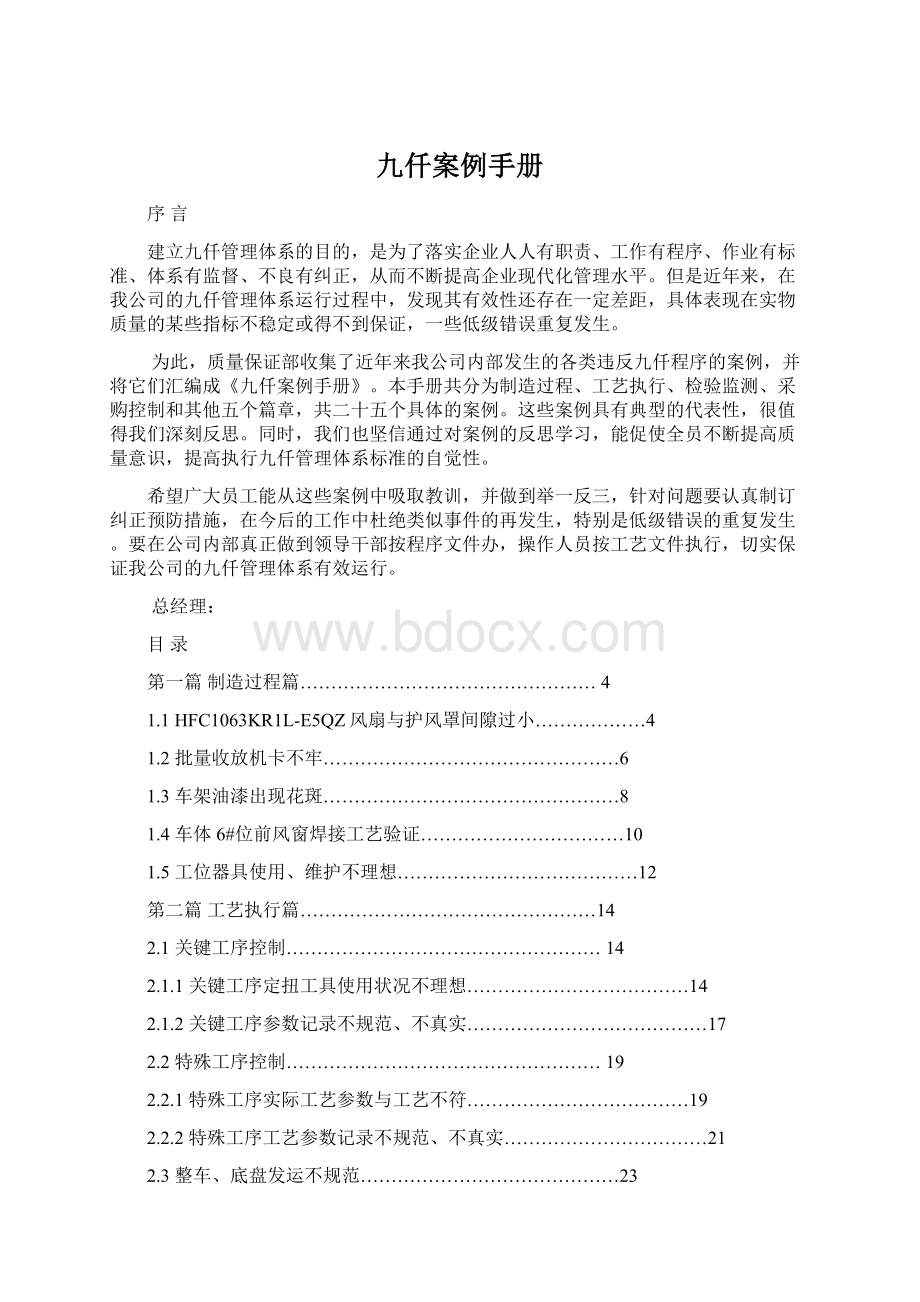
九仟案例手册
序言
建立九仟管理体系的目的,是为了落实企业人人有职责、工作有程序、作业有标准、体系有监督、不良有纠正,从而不断提高企业现代化管理水平。
但是近年来,在我公司的九仟管理体系运行过程中,发现其有效性还存在一定差距,具体表现在实物质量的某些指标不稳定或得不到保证,一些低级错误重复发生。
为此,质量保证部收集了近年来我公司内部发生的各类违反九仟程序的案例,并将它们汇编成《九仟案例手册》。
本手册共分为制造过程、工艺执行、检验监测、采购控制和其他五个篇章,共二十五个具体的案例。
这些案例具有典型的代表性,很值得我们深刻反思。
同时,我们也坚信通过对案例的反思学习,能促使全员不断提高质量意识,提高执行九仟管理体系标准的自觉性。
希望广大员工能从这些案例中吸取教训,并做到举一反三,针对问题要认真制订纠正预防措施,在今后的工作中杜绝类似事件的再发生,特别是低级错误的重复发生。
要在公司内部真正做到领导干部按程序文件办,操作人员按工艺文件执行,切实保证我公司的九仟管理体系有效运行。
总经理:
目录
第一篇制造过程篇…………………………………………4
1.1HFC1063KR1L-E5QZ风扇与护风罩间隙过小………………4
1.2批量收放机卡不牢…………………………………………6
1.3车架油漆出现花斑…………………………………………8
1.4车体6#位前风窗焊接工艺验证……………………………10
1.5工位器具使用、维护不理想…………………………………12
第二篇工艺执行篇…………………………………………14
2.1关键工序控制……………………………………………14
2.1.1关键工序定扭工具使用状况不理想………………………………14
2.1.2关键工序参数记录不规范、不真实…………………………………17
2.2特殊工序控制……………………………………………19
2.2.1特殊工序实际工艺参数与工艺不符………………………………19
2.2.2特殊工序工艺参数记录不规范、不真实……………………………21
2.3整车、底盘发运不规范……………………………………23
第三篇检验监测篇………………………………………25
3.1关于两台D4XZ前轴总成制动鼓错装…………………25
3.2前轮毂轮毂盖螺纹孔牙距与螺栓不符…………………26
3.3重卡纵梁成形压反……………………………………28
3.4关于6832转向器未加油………………………………30
3.5HFC1048KL因双码而退车…………………………………31
3.6合格品与不合格品标识不清,不合格品随处放置,无标识·33
第四篇采购控制篇………………………………………35
4.1前大灯灯眉与前小灯间隙大…………………………35
4.2HFC1045驾驶室歪斜……………………………………37
4.3帅铃倒车雷达无法装配…………………………………38
4.4M7方向机支架孔位不对无法装配…………………………39
4.5B10JC-nfD变速器侧支架的质量问题………………………40
第五篇其他篇…………………………………………41
5.1车架清洗线设备控制…………………………………41
5.2关于HFC1083直拉杆与制动气室干涉……………………43
5.3关于HFC1063K2R1可口可乐红面漆喷错…………………44
5.4出口车驾驶室质量问题………………………………47
第一篇制造过程篇
1.1HFC1063KR1L-E5QZ风扇与护风罩间隙过小
1.案例回放
3月12日,质监部发现总装厂下线的20台HFC1063KR1L卡车护风罩与风扇叶间隙过小(大都在10mm),其中最小间隙仅为6mm,检测标准为20-30mm。
2.案例分析
Ø2002年5月,汽研所下发“2002Y-163”技术文件修改通知单至生产部,有生产部领用人签字。
通知单要求冷却系中匹配应为:
水箱E4QZ-YCO,护风罩E4QZ。
查生产部受控文件管理,未见2002Y-163号文。
违反CX423B3.3.2受控技术文件均应建档,各部门都应填写“受控技术文件一览表”(JL423B-01表),文件应妥善保管。
Ø生产部在安排计划时,未根据技术文件调整BOM清单,也未下发相关生产工艺。
总装厂无相关技术文件,依据BOM清单生成物料清单BOP。
物管部按BOP清单送料到工位。
导致实际生产状态为:
水箱E0-h0,护风罩E0-h0,与技术要求水箱E4QZ-YCO,护风罩E4QZ不一致。
违反CX423B2.2生产部负责组织生产过程工艺文件的编制、发放、更改和管理。
3.改进建议
Ø生产部在接到相关技术文件后,应及时根据技术文件下切换通知并调整BOM。
Ø质监部在技术文件下发后应立即对检验文件进行修改,未能及时转化的要依据技术文件实施相关检验。
Ø技术部门下发文件时要考虑所有使用场所,达到多层把关控制目的。
1.2批量收放机卡不牢
1.案例回放
2004年3月10日,在小卡厂总装车间发现48台1020装江苏天宝收放机出现批量收放机卡不牢,在送检测线途中被弹出来的质量问题。
收放机前挂角与图不符,造成收放机卡不住
2.案例分析
Ø江苏天宝首次供货是2003年10月15日,采购依据是:
汽研所确认的样件。
违反CX740B3.1.1采购产品的技术文件是产品采购的重要依据,其具体内容包括:
产品图样、技术标准、技术协议和品种、规格、型号、验收标准等,由技术中心提供给采购部。
Ø江苏天宝首次向我公司供收放机时未见采购部选点报告。
违反CX740A3.2.1对于新选定的供方或新增非同类产品品种的合格供方,采购部必须履行选点审批手续。
Ø首批到货20只,送检,均合格,有外购配件检查报告单;后又到货200只,查收放机总成每周抽检记录中没有对收放机总成的检查记录。
违反CX7432.1质监部归口管理采购产品验证工作,负责对采购产品的检验、试验及相应的理化分析。
Ø操作工、检验人员未进行有效自检、巡检,导致48台车下线。
违反CX751A3.2.8生产过程中,生产人员应进行自检,检验人员按CX824进行测量与监控。
3.改进建议
Ø试制阶段设计人员应明确试制技术要求并以书面形式提供给厂家、采购部,样件的确认应有记录且传递给采购部。
Ø采购部对候选供方严格执行样品、小批、成批的顺序供货。
Ø质监部应严格按规定实施产品检验,确保过程和产品符合要求。
Ø对操作工、检验员进行培训,按文件要求进行自检、巡检。
1.3车架油漆出现花斑
1.案例回放
04年2月1日,总装厂发现上线车架总成表面油漆不均匀,呈现花斑状。
车架表面油漆质量差
2.案例分析
Ø春节期间涂装线停线,电泳漆未实行连续搅拌,导致漆液沉淀。
节后上班车架厂电泳搅拌不均就开始生产。
违反CX7523.4.1特殊工序使用的各种介质,由使用单位按规定定期分析、调整和更换,保证其成分在规定的范围内。
Ø车架总成油漆首件未经严格首检,检验员未认真检验,导致不合格品流入下道工序。
违反CX751A3.2.8生产过程中,生产人员应进行自检。
违反CX751A3.4.1生产过程工序结束后,应由检验人员进行全数或抽样检验,检验合格应出具合格证,产品才能转序或入库。
3.改进建议
Ø强化车架厂技术、管理人员九仟意识,完善工艺标准,做到管理人员按程序办,工人按工艺干。
Ø严格专业厂内部二级工艺纪律检查,加强过程控制。
Ø加强涂装操作工工作责任心,杜绝批量问题再次出现。
1.4车体6#位前风窗焊接工艺验证
1.案例回放
车体6#位前风窗焊接改关键工序为质控点,批量生产前需小批试制进行工艺验证。
验证前,车身厂通知生产部、质监部、质保部等部门参与。
实际验证时,生产部、质监部都未派人参与。
验证时只对焊接电流、气压、电极压力等进行验证。
2.案例分析
Ø生产制造部作为工艺验证管理的归口部门,没有做好验证前的准备工作。
违反WJ751A—027.1验证程序的有关规定。
Ø质监部没有起到检验和数据记录的作用。
违反WJ751A—027.1.4质监部负责检验和数据记录工作。
Ø验证结束后,参加验证人员未在《工艺验证单》上签字。
违反WJ751A—027.2.1验证结束应由专人编写《工艺验证单》,按要求逐项填写并经参加验证人员签字后报生产部。
Ø验证时只对焊接电流、气压、电极压力等工艺参数进行验证,设备、工装等未验证。
违反CX751A3.1.6工艺文件必须经工艺验证,包括对材料、设备、工装和方法的验证,方可正式实施。
Ø工序验证是否合格,没有进行判定,只是对工艺参数进行验证。
违反WJ751A—027.3工序验证合格的判定,按工艺规程规定的工序内容进行操作,连续生产出一批产品,质量符合工艺要求且稳定,工序所需工艺装备齐全,检验方法、器具合理适用。
3.改进建议
Ø专业厂需要进行工艺验证时,应先报生产部,并由专业厂(技术科或车间)做好相关工艺文件以及试生产的准备工作。
Ø生产部应起到工艺验证管理归口部门的作用,做好事先的验证准备工作。
Ø实施验证时,应按照主要验证内容进行逐项验证,按程序编写“工艺验证单”(JL751A--01)和“工艺参数记录表”,并经参加验证人员签字后报生产制造部。
1.5工位器具使用、维护不理想
1.案例回放
工位器具无标识或标识不清,导致零部件混用或误用;工位器具因长时间使用损坏,未及时维护;工位器具码放混乱,有的器具中放有垃圾杂物。
前桥制动本体标识不清
2.案例分析
Ø工位器具无标识或标识不清,导致零部件混用或误用。
违反CX7533.2.2生产单位的产品作内、外部转移时,在工位器具或料箱上应挂有标明产品名称、型号(或图号)的产品标识。
Ø工位器具因长时间使用损坏,未及时维护,影响产品质量。
违反JAC-GL-108-20005.1.2各单位应教育操作人员和流转人员正确使用和精心爱护工位器具,装载不得超过规定数量或限额重量,流转要轻置轻放,摆放整齐,不得乱堆乱放无故损坏。
Ø工位器具码放混乱,有时放有垃圾。
违反JAC-GL-108-20005.4严禁用工位器具装载垃圾。
工位器具挡条变形车门流转工位器具损坏
3.改进建议
Ø对操作人员进行培训,提高操作人员现场物料定置的意识。
Ø各专业厂定期或不定期对工位器具及标识情况进行调查,修复损坏的工位器具,标识磨损严重的制作新的产品标识卡。
Ø各相关单位应教育操作人员和流转人员正确使用和精心爱护工位器具。
第二篇工艺执行篇
2.1关键工序控制
2.1.1关键工序定扭工具使用状况不理想
1.案例回放
公司为涉及螺栓拧紧力矩的关键工序配置了定扭工具(如:
气动/电动/油压脉冲式扳手、单轴/多轴拧紧机、定值喀哒扳手等),但存在较多问题。
有些定扭工具带伤作业,有些定扭工具损坏后不能及时被修复,从而导致部分关键工序拧紧力矩不能有效控制在工艺要求范围内。
(见下图)
定扭工具能力状况(2004年4月统计)
使用
单位
应使用总数
正常
使用
带伤
作业
损坏
使用
不便
应用
未用、未配
备用
正常
使用率%
小卡厂
19
11
—
5
3
2
2
57.89
总装厂
33
15
5
8
7
2
—
45.45
前桥厂
19
16
—
1
2
—
—
84.21
商务车
54
50
—
2
2
—
12
92.59
车厢厂
0
0
—
—
—
1
—
0
合计
125
92
5
16
14
5
14
73.6
2.案例分析
Ø定扭工具选型不当,致使配备的工具不适用或使用不便。
违反JAC-GL-211-20042.2工程院负责确定定扭工具的工艺
维修跟不上,损坏后不能使用定扭风枪使用不方便
参数及选型工作,在定扭工具采购之前应组织使用单位、采购单位、质监部进行工艺评审工作。
违反JAC-GL-213-20044.1新购定值扭力工具使用前须进行校验,验证主参数是否符合工艺要求,符合工艺要求的准予使用,并统一编号、标识,建立校验、维修档案,不符合的交机动部,机动部牵头查明原因并处理。
Ø定扭工具带伤作业。
违反JAC-GL-211-20043.6.5定扭工具绝对不能“带伤作业”。
Ø定扭工具维修跟不上,损坏后不能用。
违反JAC-GL-211-20043.6.10出现异常情况,由专管员及时通知机动部,由机动部确定解决方案,并牵头解决。
Ø没按规定的要求进行定扭工具运行过程中的定期校准,不能保证其精度的准确性。
违反JAC-GL-213-20043.1采取周期校验和日常校验相结合的方式,周期校验为气动定扭工具每周校验一次,电动定扭工具每月校验一次,日常校验则根据需要由专业厂安排校验。
违反JAC-GL-213-20043.2不同批的坚固件和工件由于物理性能上的差异,为防止非工具因素引起扭矩飘移,在使用前使用单位应该对工具进行校准。
3、改进建议
Ø定扭工具选型时除进行工艺评审外,必要时可请厂家技术人员参与指导。
Ø专业厂应对关键工序操作工和检验员进行技艺培训,提高对设备和检验工具的操作技能以及对工序的自控能力。
Ø质监部按要求对定扭工具进行校验,加强在用定扭工具的控制,使之保持良好状态。
Ø对于损坏的定扭工具,机动部应及时联系厂家进行维修。
2.1.2关键工序参数记录不规范、不真实
1.案例回放
方向盘紧固:
尚未检测,已填好检测记录
2.案例分析
Ø未对关键工序操作人员进行有效培训,造成许多在关键工序岗位的操作工意识和操作技能不能满足关键工序控制的要求。
违反CX751A3.3.3专业厂对关键工序操作人员进行培训,经考核合格并征得质保部、人力资源部同意后,由专业厂发放上岗证。
Ø操作人员未按工艺要求记录扭矩数值,且存在作假现象。
违反CX751A3.3.4关键工序操作人员应进行自检,按要求填写“自检记录表”(JL751A-05表)。
Ø检验人员未按规定对工序进行监督检查。
违反CX751A3.3.7检验人员按检验指导书的规定,对工序进行监督检查。
3.改进建议
Ø加强对关键工序操作人员的培训,考核合格后才能上岗,提高关键工序操作工的质量意识和操作技能。
Ø加强工艺纪律检查及专业厂二级工艺管理,突出对关键工序记录真实性的检查,一经发现严格考核,杜绝作假现象。
2.2特殊工序控制
2.2.1特殊工序实际工艺参数与工艺不符
1.案例回放
前处理烘干温度工艺要求85-95℃,面漆烘干温度工艺要求85-95℃。
而实际生产中前处理烘干温度和面漆烘干温度都达不到工艺要求,就开始生产。
前处理烘干:
工艺要求85-95℃
面漆烘干:
工艺要求85-95℃
2.案例分析
Ø前处理温度、面漆烘干温度升至工艺要求85-95℃,需要1小时以上。
而车间每天一上班就开动流水线,故实际作业温度达不到工艺要求。
违反CX7523.4.5严格按工艺规程操作,控制影响参数波动的各种因素。
操作人员对工艺参数进行连续监控,填写“特殊工序工艺参数记录表”(JL752-02表),将工艺参数如实记录在表上。
检验人员应在记录上签字,以表明实施了监督。
记录应予保持。
Ø作业人员未培训,缺乏工艺意识与质量意识。
违反CX7523.3.4操作人员应经培训,考核合格后持资格证上岗。
3.改进建议
Ø严格按工艺参数要求进行作业,需要升温的可提前开动设备,待达到要求后才能工作。
Ø设备有问题的及时报修。
Ø加强特殊工序操作工的培训,提高其按工艺操作的意识。
2.2.2特殊工序工艺参数记录不规范、不真实
1.案例回放
车厢面漆施工粘度测量需用秒表,生产现场秒表损坏,但检测记录填写完整。
车厢围板焊接电极压力需用压力计测量,生产现场压力计损坏,但检测记录填写完整。
2.案例分析
Ø测量器具计时秒表与压力计应定期检定,发现损坏应及时送修。
违反CX760A3.3测量器具的周期检定。
违反CX760A3.5.1在对测量器具的周检或抽查中发现量查具偏离校准状态,示值发生误差时,应立即停止使用,并对以往测量结果的有效性进行评价和记录。
Ø操作工在对特殊工序工艺参数检查并记录时,没有真实反映实际情况。
违反CX7523.4.5严格按工艺规程操作,控制影响参数波动的各种因素。
操作人员对工艺参数进行连续监控,填写“特殊工序工艺参数记录表”(JL752-02表),将工艺参数如实记录在表上。
检验人员应在记录上签字,以表明实施了监督。
记录应予保持。
3.改进建议
Ø操作工应按工艺要求做好特殊工序工艺参数记录。
Ø质监部应对测量器具进行周期检定,确保测量器具处于正常使用状态。
Ø专业厂车间、技术科发现测量器具故障,应及时报质监部、机动部进行维修。
2.3整车、底盘发运不规范
1.案例回放
在发运整车、底盘过程中,操作不规范。
底盘件随意拆放,捆绑时无防护或防护不到位,造成车架及车厢底板、边板变形或油漆磕碰划伤。
底盘件随意拆放
整车底盘发运时捆绑无防护
2.案例分析
Ø整车、底盘在发运时捆绑无防护。
违反CX7553.2.1为防止产品在搬运过程中发生撞击、磨损、变质、丢失等情况,对不同产品应采用合适的工位器具和搬运方法。
违反JAC-GL-509-20002.1公司生产的各类底盘,严格按工艺研究所下发的底盘运输、装载及紧固的技术文件规定执行。
Ø整车、底盘发运人员缺乏培训,质量意识不够。
违反CX751A3.2.1操作者初次上岗前,必须经过岗前培训。
3.改进建议
Ø完善运输、装载及紧固的技术文件,使整车、底盘发运有法可依。
Ø对操作人员进行培训,提高操作工质量意识。
第三篇检验监测篇
3.1关于两台D4XZ前轴总成制动鼓错装
1.案例回放
2004年2月,小卡厂现场装配轮胎时发现两台D4XZ前轴总成制动鼓合件错装。
经查,此两台前桥为前期试制返工桥。
2.案例分析
Ø返工时,装配工未认真履行自检程序,导致制动鼓合件错装。
违反CX8243.1.2操作工应对加工产品展开自检和自控活动。
Ø检验员完工检验把关不严,导致不合格品流入下道工序。
违反CX751A3.4.1生产过程工序结束后,应由检验人员进行全数或抽样检验,检验合格应出具合格证,产品才能转序或入库。
3.改进建议
Ø此案例纯属员工责任心不强而导致的低级错误。
专业厂全体员工应从中吸取教训,杜绝低级错误的重复发生。
Ø操作工认真履行自检程序,坚决杜绝错、漏装现象发生。
Ø检验员严格执行“三检制”,坚决杜绝不合格品流入下道工序。
3.2前轮毂轮毂盖螺纹孔牙距与螺栓不符
1.案例回放
2004年8月,外协件前轮毂轮毂盖螺纹孔螺纹加工错误,牙距应为1.25mm,实际加工成1mm。
在前桥厂装配38台后才发现螺栓与孔牙距不符(螺栓M10×1.25孔M10×1.0),导致部分螺纹被损坏。
螺栓与孔牙距不符(螺栓M10×1.25孔M10×1.0)
2.案例分析
Ø生产过程中,操作工未认真履行自检程序,导致在螺栓与孔牙距不符的状态下装配了38台。
违反CX8243.1.2操作工应对加工的产品展开自检和自控活动。
Ø检验员未认真检验,导致在螺栓与孔牙距不符的状态下装配了38台才发现。
违反CX8243.1.1检验员在每班开始生产时,应进行首件检验,作首检标识;在加工期间,按“检验指导书”规定的检验频次进行巡检。
3.改进建议
Ø操作工认真履行自检程序,坚决杜绝错、漏装现象发生。
Ø检验员严格执行“三检制”,首检、巡检、完工检情况均应记录在“检验台账”相应栏目内,坚决杜绝不合格品流入下道工序。
3.3重卡纵梁成形压反
1.案例回放
公司重卡纵梁在车架厂下料、冲孔后,委托江苏丹阳宏运农用车厂进行冲压成形。
2004年2月18日,生产部组织工程院、质监部、采购部的员工一行四人去丹阳对本批60台套的重卡纵梁的冲压成形进行现场确认、协调、检查。
2月20日检完模具(对方告知是右纵梁成形模)。
在进行首检时,没有对成形正反进行检查。
22日上午压制左右副梁时,工程院派出人员发现主梁左右件方向成形反了,并擅自决定采取将副梁也跟着压反,造成本次质量事故,直接经济损失达18万元。
左梁前段,孔位却为右梁孔位一堆压反的纵梁
2.案例分析
Ø生产部是本次生产的组织部门,在组织委托加工中,生产部没有生产图纸(此次用图是从车架厂技术科借的),工艺文件状态不清。
违反CX751A生产过程控制程序的要求。
Ø收到新产品图纸后,质监部未编制相应的检验指导书,造成现场检查缺乏依据,检查项目不清,导致首检时只发现导正销孔偏差等问题,并没有对成形正反进行检查。
违反CX8242.2质量监查部负责产品最终检验和试验、质量监督考核及组织编制检验指导书。
Ø工程院签定技术协议时没有对质量责任提出要求且没发放工艺文件给对方。
生产部在签定试验费用协议时也未对质量责任提出要求。
采购部在签定费用协议时未体现质量要求和验收标准。
最终致使被委托方无质量责任,造成质量损失无法索赔。
3.改进建议
Ø建立规范的委托加工(包括临时采购)。
各类协议要有规范的样表,且注明对方的质量责任要求。
Ø工艺文件、检验文件要明确检验项目。
Ø对于不易区分的件(如左、右纵梁)在模具上要有防错措施,同时件的正反面要有标识。
3.4关于6832转向器未加油
1.案例回放
2003年7月17日,技术服务部转来江西赣州利丰服务站传真,反映该市公交公司6月24日购买的上海产6832型10辆公交客车行驶时发现方向沉重。
后经利丰服务站检查
,该批10辆车转向器全部未加油。
2.案例分析
Ø该批方向机系2003年4月2日到货,质监部未按检验文件规定打开螺塞检查是否加油,仅验证其有加油标识,当日即上线装车10台。
违反CX7433.2外购配件的验证检验人员根据相关标准、验收规范或检验指导书的要求进行检验。
3.改进建议
Ø加强对配套厂家管理,确保其按公司技术要求生产产品。
Ø质监部检验人员应按检验指导书逐项认真检验。
3.5HFC1048KL因双码而退车
1.案例回放
2003年4月10日,接销售公司报告称一辆底盘号为2012791的黄色1048KL高栏卡车因四川成都用户在上牌时被当地车管部门发现该车在右纵梁相邻位置出现两组不同的VIN码而不准入户,最终造成顾客退车,直接经济损失4500元,并给公司形象造成一定的损害。
后经查因该车是黄色,总装厂员工误以为是杭州爱知所订车辆,按惯例根据生产入库单打了一组1048KL的VIN码,并粘贴了车辆铭牌(此类普通卡车总装厂无需打码,应由质监部打码)。
车辆