单斗反铲挖掘机动臂设计计算说明书.docx
《单斗反铲挖掘机动臂设计计算说明书.docx》由会员分享,可在线阅读,更多相关《单斗反铲挖掘机动臂设计计算说明书.docx(21页珍藏版)》请在冰豆网上搜索。
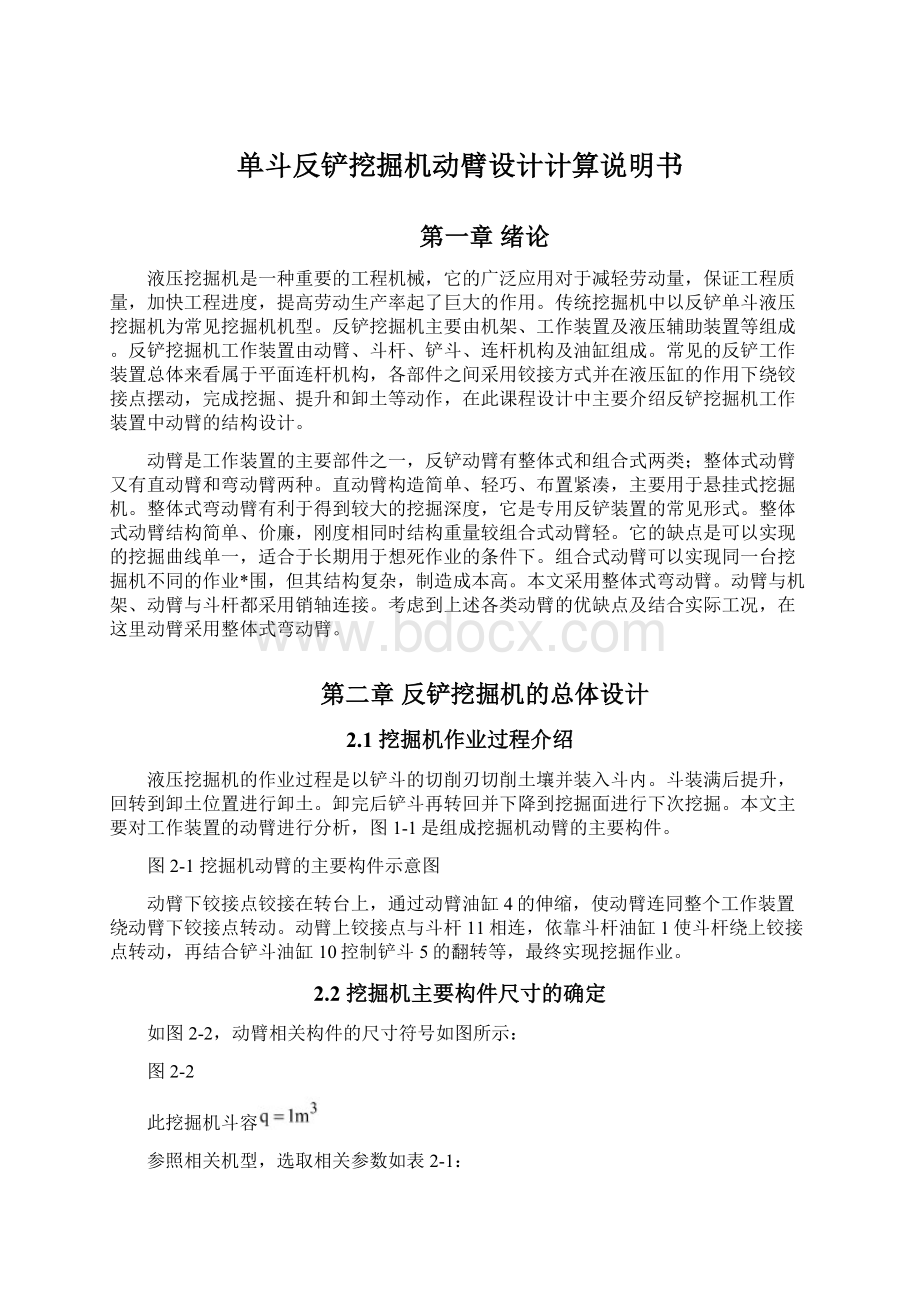
单斗反铲挖掘机动臂设计计算说明书
第一章绪论
液压挖掘机是一种重要的工程机械,它的广泛应用对于减轻劳动量,保证工程质量,加快工程进度,提高劳动生产率起了巨大的作用。
传统挖掘机中以反铲单斗液压挖掘机为常见挖掘机机型。
反铲挖掘机主要由机架、工作装置及液压辅助装置等组成。
反铲挖掘机工作装置由动臂、斗杆、铲斗、连杆机构及油缸组成。
常见的反铲工作装置总体来看属于平面连杆机构,各部件之间采用铰接方式并在液压缸的作用下绕铰接点摆动,完成挖掘、提升和卸土等动作,在此课程设计中主要介绍反铲挖掘机工作装置中动臂的结构设计。
动臂是工作装置的主要部件之一,反铲动臂有整体式和组合式两类;整体式动臂又有直动臂和弯动臂两种。
直动臂构造简单、轻巧、布置紧凑,主要用于悬挂式挖掘机。
整体式弯动臂有利于得到较大的挖掘深度,它是专用反铲装置的常见形式。
整体式动臂结构简单、价廉,刚度相同时结构重量较组合式动臂轻。
它的缺点是可以实现的挖掘曲线单一,适合于长期用于想死作业的条件下。
组合式动臂可以实现同一台挖掘机不同的作业*围,但其结构复杂,制造成本高。
本文采用整体式弯动臂。
动臂与机架、动臂与斗杆都采用销轴连接。
考虑到上述各类动臂的优缺点及结合实际工况,在这里动臂采用整体式弯动臂。
第二章反铲挖掘机的总体设计
2.1挖掘机作业过程介绍
液压挖掘机的作业过程是以铲斗的切削刃切削土壤并装入斗内。
斗装满后提升,回转到卸土位置进行卸土。
卸完后铲斗再转回并下降到挖掘面进行下次挖掘。
本文主要对工作装置的动臂进行分析,图1-1是组成挖掘机动臂的主要构件。
图2-1挖掘机动臂的主要构件示意图
动臂下铰接点铰接在转台上,通过动臂油缸4的伸缩,使动臂连同整个工作装置绕动臂下铰接点转动。
动臂上铰接点与斗杆11相连,依靠斗杆油缸1使斗杆绕上铰接点转动,再结合铲斗油缸10控制铲斗5的翻转等,最终实现挖掘作业。
2.2挖掘机主要构件尺寸的确定
如图2-2,动臂相关构件的尺寸符号如图所示:
图2-2
此挖掘机斗容
参照相关机型,选取相关参数如表2-1:
表2-1
挖掘机最大挖掘半径r
10030mm
斗宽b
1232mm
动臂油缸行程
1305mm
斗杆油缸行程
1400mm
铲斗最大挖掘力
149KN
转台回转制动力矩
150KNm
最大工作压力
35MPa
闭锁压力
40MPa
本装置动臂油缸采取两个对称布置形式,并且油缸与动臂铰接点与动臂弯点重合。
下面开始计算动臂的相关尺寸
(1)计算动臂长度
及斗杆长度
取
,
为动臂长度与斗杆长度的比值,其参考*围为1.5~2,
又
,
其中:
为铲斗回转半径;
为铲斗从开始接触土壤到挖掘过程结束并脱离土壤的转角
,初选
;
为松散系数,
,初选
。
从而得
=1300mm。
近似取
由于
,从而解得
。
(2)计算上动臂长度
及下动臂长度
初选动臂弯角
,其中
的参考*围为
,
的参考*围为1.1~1.3。
在动臂组成的三角形CBF中,根据
,
得:
。
(3)动臂油缸最长尺寸
,最短尺寸
及动臂油缸缸径
及活塞杆直径
的确定
,取
,其中
的参考*围为1.6~1.8,依据上述两式得
。
初选
=135mm
=90mm。
(4)铰点A与C之间的距离
及AC与水平面间倾角的确定
由
取
,由于此挖掘机为反铲装置,
取
。
(5)斗杆油缸最长尺寸
和最短尺寸
的确定,初选斗杆油缸缸径
及活塞杆直径
由
,
取
=1.65,得
,初选
=140mm
=100mm。
(6)确定斗杆油缸的最大力臂
,如图2-3
图2-3
由
,
,
又
为背压,
得
。
(7)确定斗杆油缸在动臂上铰接点D的位置
由于D点位置只是安装斗杆油缸,故只需满足有足够安装空间即可,取DF与CF的夹角为
.
取
,得
(8)初选斗杆前厚段的夹角
(9)初步确定铰点G的位置
。
(10)初选铲斗油缸缸径
=120mm及活塞杆直径
=80mm
(11)初选各连杆长度
2.3动臂干涉及合理性检查
(1)校核动臂三角形ABC是否存在干涉
因为
所以动臂三角形ABC不存在干涉。
(2)动臂机构设计的合理性
将公式中的前述各值代入得
,所以动臂机构设计合理。
第三章典型工况下的受力分析
对动臂的强度分析应以动臂可能承受的最大载荷的工况作为计算工况,根据经验初步可以选定如下2个:
工况1:
如图所示,该工况动臂油缸全缩、动臂处于最低位置,动臂与斗杆铰接点、斗杆与铲斗铰接点、斗齿尖三点一线且垂直于停机面,即斗齿尖处于最大挖掘深度位置。
工况2:
动臂油缸和斗杆油缸的作用力臂最大、铲斗油缸工作、工作装置处于发挥最大挖掘力姿态。
3.1工况1下各铰接点的受力分析
此姿态的示意图如图3-1所示:
图3-1
3.1.1YZ平面上的受力分析
取铲斗和斗杆为研究对象,受力如图3-2所示:
图3-2
连杆传动比为
其中:
为铲斗液压缸对N点的作用力臂;
为连杆HK对N点的作用力臂;
为连杆HK对Q点作用力臂,此三个力臂都可由示意图3-1测出;
为铲斗的回转半径,已由前面求出。
故可得i=0.14。
挖掘机的理论挖掘力
,
为铲斗油缸提供的力;根据
得
=389.4KN,进而得
=54.5KN
(1)隔离出铲斗对Q点取矩
其中:
为铲斗绕Q点转动的重力力臂;
为铲斗及土壤重量,取26KN;得
=61.7KN。
(2)求E点受力
根据图3-2,对F点取矩,有
其中:
为铲斗和斗杆重力
对F点的力臂,可由示意图3-1得出;
为斗杆油缸作用力对F点的力臂,可由示意图3-1得出;
为铲斗及斗杆的总重量,
=38KN。
解得:
=523KN
(3)求F点受力
,
得
。
(4)求B点受力
对动臂受力分析,如图3-3:
对C点取矩有
图3-3
其中:
为力
对Q点的作用力臂,可由示意图3-1得出;
为力
对Q点的作用力臂,
为动臂重力对Q点的作用力臂,可由示意图3-1得出;
为铲斗油缸作用力
对Q点的作用力臂,可由示意图3-1得出;
为动臂油缸作用力
对Q点的作用力臂,可由示意图3-1得出。
根据作用力与反作用力的关系有:
=125.4KN,
=557.1KN,
=523KN,各力的方向如图3-3所示:
得
=1107KN,单个油缸所承受的压力
=
/2=553.5KN
动臂油缸闭锁力
=572.3KN,故
<
,动臂油缸能够承受。
对动臂依据:
得:
=866.7KN,
=-544.6KN。
3.1.2*Y平面内受力分析
横向力作用方向如图3-4所示:
为横向力。
图3-4
横向力作用下对C点和F点产生的横向作用力为:
其中:
为转台制动力矩(已知),
为斗齿尖至回转中心的垂直距离(由图3-1可以得出)。
得:
=57.9KN
=-57.9KN
横向力作用下在C处和F处产生的横向附加弯矩及附加扭矩为:
471.9KNM
偏载在*Y平面内产生的弯矩为:
3.2工况2下动臂的受力分析
此工况为动臂油缸作用力臂最大,铲斗油缸作用力臂最大,铲斗处于最大挖掘力姿态。
此姿态下挖掘机的示意图如图3-5所示:
图3-5
3.2.1YZ平面的受力分析
以铲斗和动臂为研究对象,受力图如图3-6:
图3-6
(1)求E点的受力
对F点取矩有:
其中:
为力
对F点的作用力臂;
由图3-5得出;
为
对F点的作用力臂;
由图3-5得出;
为铲斗油缸发挥最大的挖掘力,为149KN;
为铲斗和斗杆的总重量,为38KN;
为斗杆油缸作用的最大力臂。
得:
=605.4KN。
斗杆油缸的闭锁力
KN>
,所以铲斗油缸能承受此力。
(2)求F点的受力
依据
得
=-666.1KN,
=385.6KN
(3)求B点的受力
对动臂进行受力分析,受力图如图3-7:
图3-7
对C点取矩,有
其中:
为力
对C点的作用力臂;
为
对C点的作用力臂;
为力
对C点的作用力臂;
为
对C点的作用力臂;这些值可以从图3-5上得出;
为动臂的重力,取
=20.33KN。
又
,
得
。
(4)求C点的受力
根据
得
=23.2KN,
=231.2KN。
3.2.2*Y平面内受力分析
*Y平面内的受横向力
作用如图3-7所示:
图3-7
求横向力作用下在F和C处产生的横向力
和
=
=
其中
为斗齿尖至回转中心的垂直距离,可以图纸中测出;从而求得
=29.8KN,
=-29.8KN
横向力作用下在F处和C处产生的附加弯矩和附加扭矩为:
=118.8KNM
=180.9KNM
=47.6KNM
=114.5KNM
偏载在横向平面内产生的弯矩为:
=91.8KNM
第四章动臂的内力图
4.1工况1下的内力图
根据第三章的受力分析,可得该工况下的YZ平面内的轴力图、YZ平面内的剪力图、YZ平面内的弯矩图、*Y平面的剪力图、*Y平面内的弯矩图及扭矩图如图4-1的(a)、(b)、(c)、(d)、(e)、(f)所示:
(a)(b)(c)
(d)(e)(f)
图4-1
4.2工况2下的内力图
根据第三章的受力分析,可得该工况下的YZ平面内的轴力图、YZ平面内的剪力图、YZ平面内的弯矩图、*Y平面的剪力图、*Y平面内的弯矩图及扭矩图如图4-2的(a)、(b)、(c)、(d)、(e)、(f)所示:
(a)(b)
(c)(d)
(e)(f)
图4-2
根据上两个工况的内力图可以得出,工况1姿态下,动臂受力更大,且受力最大的位置为动臂弯折处(B点),故可按工况1动臂的受力状况对动臂进行结构设计。
第五章动臂的结构设计及校核
根据上一章的分析可知,动臂的受力为弯扭组合状态,在这拟用第三强度理论对其进行设计及校核。
根据经验初选动臂钢板的材料为低合金钢16Mn,其屈服极限
=350MPa,初选安全系数S=1.5;初步选择动臂底板的宽度
=420mm,底板的厚度
=18mm。
由于上动臂所受的载荷较大,取上下动臂侧板的厚度
=18mm,参考有关机型,初选动臂拐弯处截面高度h=500mm。
动臂拐弯处截面如图5-1所示:
图5-1
5.1正应力计算与校核
(1)YZ平面内弯矩产生的正应力
计算
其中:
可由平面内弯矩图看出,其值为477KNm;
为*向抗弯截面系数,其值为
,
惯性矩;
又
把上述初选值带入即可得
,进而得出
=98.7MPa。
(2)*Y平面内弯矩产生的正应力
计算
其中:
可由工况1下*Y平面内弯矩图看出,其值为352.4KNm,
为Z向抗弯截面系数,其值为
;
又
,
把上述初选的值代入即可得
,进而得出
=80.4MPa
(3)轴力产生的正应力
其中:
N为轴力,其值为1008KN;
为危险截面面积
;
将
的值代入即可得
=
,从而得
=31.7MPa
综上可得此工况下,动臂危险截面所受的正应力
5.2切应力计算与校核
(1)YZ平面剪力产生的切应力
根据薄壁闭合截面的剪力切应力公式,确定
:
将初选值代入上式即可得
=
,又最大切应力为:
将上述值代入即得
=11.3MPa。