基于PLC的自动轧钢机控制.docx
《基于PLC的自动轧钢机控制.docx》由会员分享,可在线阅读,更多相关《基于PLC的自动轧钢机控制.docx(46页珍藏版)》请在冰豆网上搜索。
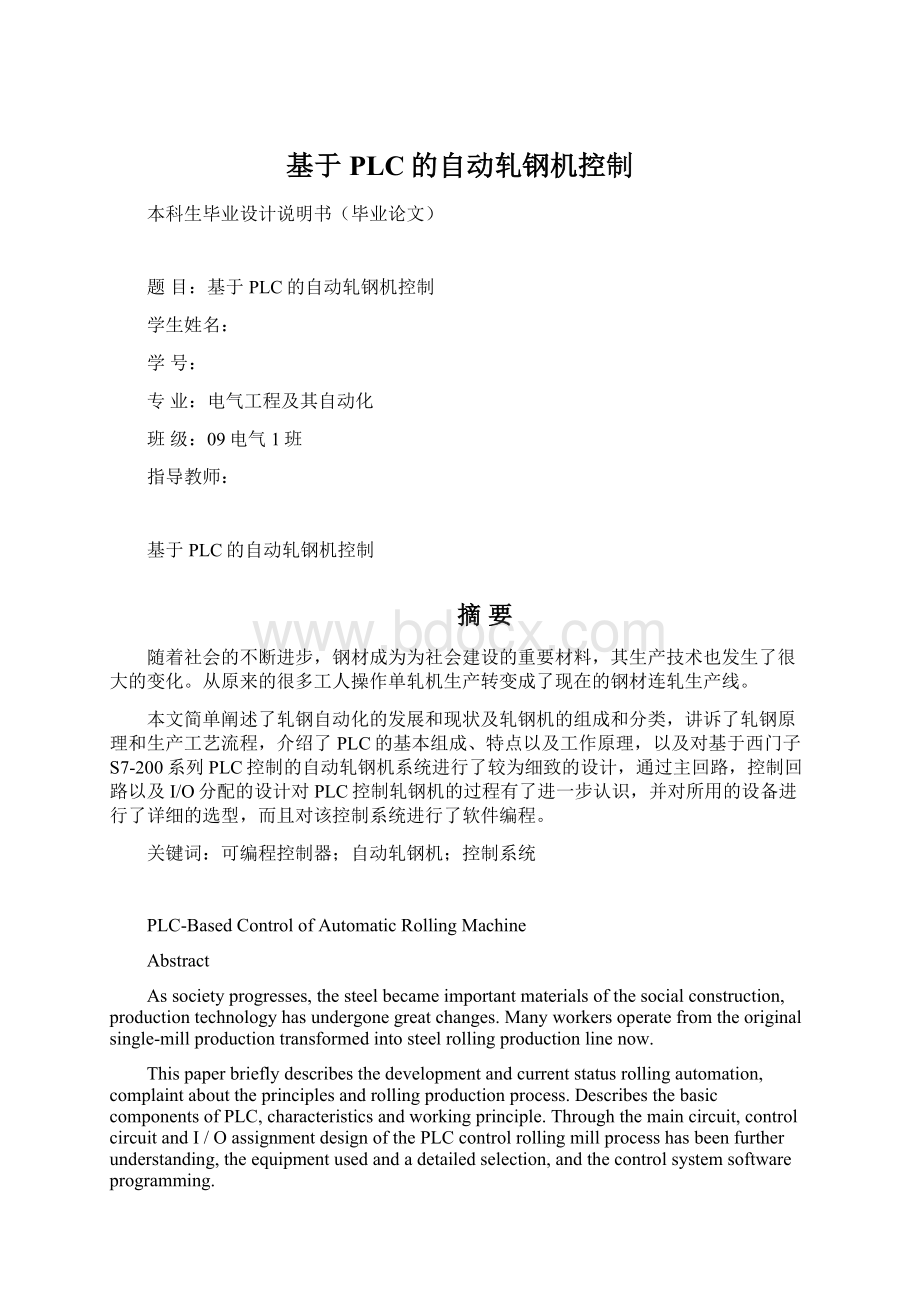
基于PLC的自动轧钢机控制
本科生毕业设计说明书(毕业论文)
题目:
基于PLC的自动轧钢机控制
学生姓名:
学号:
专业:
电气工程及其自动化
班级:
09电气1班
指导教师:
基于PLC的自动轧钢机控制
摘要
随着社会的不断进步,钢材成为为社会建设的重要材料,其生产技术也发生了很大的变化。
从原来的很多工人操作单轧机生产转变成了现在的钢材连轧生产线。
本文简单阐述了轧钢自动化的发展和现状及轧钢机的组成和分类,讲诉了轧钢原理和生产工艺流程,介绍了PLC的基本组成、特点以及工作原理,以及对基于西门子S7-200系列PLC控制的自动轧钢机系统进行了较为细致的设计,通过主回路,控制回路以及I/O分配的设计对PLC控制轧钢机的过程有了进一步认识,并对所用的设备进行了详细的选型,而且对该控制系统进行了软件编程。
关键词:
可编程控制器;自动轧钢机;控制系统
PLC-BasedControlofAutomaticRollingMachine
Abstract
Associetyprogresses,thesteelbecameimportantmaterialsofthesocialconstruction,productiontechnologyhasundergonegreatchanges.Manyworkersoperatefromtheoriginalsingle-millproductiontransformedintosteelrollingproductionlinenow.
Thispaperbrieflydescribesthedevelopmentandcurrentstatusrollingautomation,complaintabouttheprinciplesandrollingproductionprocess.DescribesthebasiccomponentsofPLC,characteristicsandworkingprinciple.Throughthemaincircuit,controlcircuitandI/OassignmentdesignofthePLCcontrolrollingmillprocesshasbeenfurtherunderstanding,theequipmentusedandadetailedselection,andthecontrolsystemsoftwareprogramming.
Keywords:
PLC;automaticrollingmill;controlsystem
第一章轧钢机
1.1自动轧钢机的目的及实际意义
随着生产技术的不断发展,钢铁产品的应用也日益扩大,世界钢材料消耗量约占全部金属的95%以上,钢铁作为一种结构—功能材料具有不可替代的主导作用。
轧钢机是实现钢铁轧制的设备。
现代钢铁联合企业由炼铁、炼钢和轧钢三个主要生产系统所组成。
轧钢生产属于技术含量最高的工序,用轧制方法生产钢材,具有生产率高,品种多,生产过程连续性强,易于实现高速化、大型化、连续化和自动化等优点,其中约90%的钢材都是通过轧制方法所生产的。
自动轧钢机具有一机多能的特点,可在开坯的同时轧制小型的线材;减少了工人的劳动强度和力度,从而提高工作效率。
1.2轧钢自动化发展的历史和现状
据说14世纪欧洲就有轧机,但也有记载称在1480年,意大利人达·芬奇设计出了轧机的草图。
在1553年法国人布律列尔轧制出了金和银板材,用以制造钱币。
接着,英国于1766年设计出了串行式小型轧机,到了19世纪中叶,第一台可逆式板材轧机在英国投产。
1848年德国发明了万能式轧机,1853年美国也开始使用三辊式轧机,并采用蒸汽机传动的升降台实现了机械化生产。
紧接着美国出现了劳特式轧机并于1859年制造了第一台连轧机
。
近十年来国内轧钢企业的规模和技术水平提升的很快,对于轧钢设备和生产过程自动化的控制也成为轧钢生产的主流。
以前,整个轧钢电气控制系统是以传动控制为核心,用大量的继电器及逻辑组合来实现轧钢过程。
到了20世纪60年代,计算机开始用于冷轧自动厚度控制,采用计算机的直接数字控制的模型优化控制也得到广泛应用。
从此,计算机便成为了整个轧钢控制系统的核心,传动控制器作为其输出装置,检测仪表作为其输入装置,这就标志着现代轧钢自动化系统的开始。
随着生产技术的发展,钢铁产品的应用也日益扩大,据统计,世界钢材料消耗量占全部金属的95%以上,因为钢铁作为结构—功能材料具有不可替代的主导作用。
钢铁行业自动化技术经过多年的探索和发展,水平显著提高,有的技术已经领先国外,有的也已达到了国际先进水平,特别是有的已经具有了自主知识产权,并形成了产品在行业内也已经进行推广应用。
早期的自动控制系统是依靠简单的继电-接触器来实现的,其优点是:
结构简单、价格低廉、抗干扰能力强,可以实现集中控制和远距离控制,但也有缺点;因为采用固定接线,所有通用性和灵活性差;又采用了触点的开关动作,工作频率较低,触点容易损坏,可靠性也差。
随着自动轧钢机的出现,继电接触器控制逐渐被取代,自动轧钢机生产也已经向大型化、高速化、精密化、连续化方向发展。
轧钢生产对自动化装备的要求要比其他生产工序高,自动化系统装备的水平对产品的质量影响也很大。
因此,轧钢系统中所采用的自动化设备和系统比较多,各级自动化控制程度也比较高,是现代钢铁产业自动化技术应用最多的地方。
轧钢生产属于技术含量特别高的工序,用轧制方法来生产钢材,具有生产效率高,产品种类多,生产过程连续性强,易于实现高速化、连续化和自动化,大约90%的钢材都是用轧制方法生产的
。
随着低价微型计算机的诞生,轧钢自动化开始快速的发展,特别是PLC和DCS的出现,使轧钢自动化系统得到迅速的发展和普及。
我国大钢厂从70年代已经选用先进的连轧机,连轧机采用了一整套先进的自动化控制系统,全线生产过程和操作监控均有计算机来控制实施,轧件在连轧机上可以同时轧制,这大大提高了生产效率和生产质量。
随着我国轧制加工业的发展,我国轧制设备也经历了一个自主开发—引进—学习借鉴—国产化的一个往复循环过程。
经过20多年的探索和创新,在90年代,轧钢自动化系统的开发主要是控制轧件的开发,硬件和系统是以进口的PLC为主。
全国各钢铁公司大量引进现代化轧钢生产线、冷轧机、热轧机、棒材连轧、高速线材、型钢和钢管轧机等等。
到了21世纪,我国轧钢自动化系统和技术开始高速发展和大规模推广应用。
近年来,我国轧制加工设备市场出现了多样化的要求,正在逐步向高精化、宽幅化、高速化以及高技术和连续轧制的方向发展。
目前,我国轧钢自动化系统和技术也已得到了广泛应用,据统计,重点钢铁企业轧钢自动化系统中基础自动化系统普及率约为99.67%,过程控制级普及率为68.76%。
在轧钢自动化工程技术方面,我们已全面接近和大部分已达到国际先进水平,正在走向世界市场
。
1.3轧钢机的定义及组成
1.3.1定义
狭义定义:
轧制钢材的机械设备。
它使轧件在旋转的轧辊间产生塑性变形,轧出所需的断面形状和尺寸的钢材。
即主要设备—主机列。
广义定义:
用于轧制钢材生产工艺全部所需的主要设备和辅助设备的成套机组。
包括轧制、翻钢、运输、冷却、剪切等设备。
1.3.2轧机的组成
轧钢机主要包括工作机座及其传动装置和主电动机等。
直接使轧件产生塑性变形的设备称为主要设备。
它包括由轧辊、轴承、轧辊调整装置、导卫装置及机架等组成的工作机座;主联轴器、减速器、齿轮机座、万向或梅花接轴等组成的传动装置。
辅助设备是指主机列以外的各种设备,它用于完成一系列辅助工序。
辅助设备种类很多,机械化程度越高,它占的比重越大。
1.4轧钢机的分类
按结构分类:
根据轧辊在机座中的布置方式分
1二辊式轧机该种轧机结构比较简单,工作可靠,由直流电动机来驱动,用于二辊可逆式初轧机,可将钢锭往复轧制成各种矩形坯。
二辊可逆式轧机也可以用于轧制轨梁和中厚板。
2复二辊式轧机此轧机作用与三辊式基本相似,轧辊调整、孔型配置较方便,用于横列式中小型轧机。
3三辊式轧机其在同一机座上轧件可以两向轧制,轧机无需反转,由一台交流电动机经过减速器和齿轮座来驱动数台三辊式轧机,可实现轧件往复多道次轧制。
它用于开坯和型钢的生产,具有设备简单、投资少的特点。
轨梁轧机及大型轧机可以用直流电动机驱动,在生产中必要时可调速,来改善轧制条件。
4特殊轧机它是根据不同产品设计的专用轧机,例如:
钢球轧机、周断面三辊斜轧机、轮箍轧机、车轮轧机等。
此外还有很多种轧机,在此就不一一列举。
1.5轧钢原理及工艺流程
1.5.1轧钢原理
轧钢就是用轧机对钢坯进行压力加工,把炼钢厂送过来的铸坯,先进入加热炉,达到一定的温度后出来经过初轧钢设备反复轧制后进入精轧钢机。
轧钢属于金属压力加工,在热轧生产线上,轧坯加热变软,被辊道送人轧钢设备,最后轧成用户所要求的尺寸。
轧机主要由几组轧辊构成,轧辊是一对转动方向相反的辊子,两个辊子之间形成一定形状的缝或孔,钢坯通过轧辊就能成为一定形状的钢材。
1.5.2轧钢系统工艺流程
图1.1模拟示意图
圆钢的轧制工艺流程:
原料(方坯有280mm*380mm、280mm*325mm、319*410;圆坯有φ350mm、φ300mm、φ270mm、φ210mm,φ110mm)——加热(加热炉)——开坯机轧制(得到进入连轧机需要的尺寸)——横移(通过拉钢机实现)——连轧(有3架轧机成一字排列,出来后就是需要得到的成品尺寸)——成品——横移——锯切——冷床——描号——搜集——打捆——过磅——入库(打标牌、贴标签)——码垛——发车.
1.6轧钢工艺的发展前景
目前,我国轧钢生产的钢材品种有很多,主要有薄钢板、钢带、无缝钢管、焊接钢管、铁道用钢、普通大中小型材、优质型材、冷弯型钢、线材、特厚钢板、中厚钢板等。
轧钢生产的产品如果按钢材断面形状分,可分为:
钢管、钢板和型钢。
其中型钢是一种应用范围比较广泛的钢材,我国型钢产量约占钢材总产量的25%~30%。
型钢按用途又可分为:
普通型钢和专用型钢;若从断面形状分为异型断面型钢和简单断面型钢;从生产方式的角度来分,有焊接型钢、弯曲型钢和轧制型钢。
板材和带材也是广泛应用的钢材,我国的板带材产量占钢材总产量的45%~55%。
板带钢按应用领域分,有建筑板、船板、桥板、汽车板、电工钢板、机械用板等;按照轧制温度的不同分为热轧板带和冷轧板带;按钢板按厚度分为:
中厚板、薄板和箔材。
钢管的主要用途有建筑用管和石油管道等,我国钢管产量占钢材总产量的10%~15%,钢管的规格由外形尺寸及壁厚标称来决定。
钢管从制造角度分为无缝钢管、螺旋钢管与直缝钢管、冷轧钢管等;若按断面形状又分为圆形管、异型钢管和变断面钢管。
随着轧钢工艺技术的不断发展,钢材的生产范围将不断扩大,产品品种也会不断增多。
近年来我国有许多有价值的钢板产量大幅度增长,其中冷轧硅钢片2003年已达89.6万吨,镀锡板在2002年也已经达到110万吨,管线钢、石油管、耐火钢板、冷轧不锈钢板产量也达到55万吨
。
随着我国钢铁工业结构调整步伐的加快,国际钢铁市场也竞争激烈,加上对世界环境要求,轧钢技术装备及技术轧制趋向高质量、高精度、短流程以及智能环保的方向发展。
这些进步主要体现在生产工艺流程上,由于钢铁工业的高速发展也日益受到资源短缺和环境保护要求逐渐严格等多方面的制约,发展循环经济也就成为钢铁企业走可持续发展的必由之路。
同时随着工业用户自身的自动化水平的提高,它们对钢材生产工艺流程优化和钢材质量要求越来越高。
展望未来,轧钢工艺和技术的发展主要体现在以下几方面:
1.轧制过程柔性化
板带热连轧生产中的压力调宽技术和板形控制技术的应用,实现了板宽的自由规程轧制。
棒、线材生产的粗、中轧平辊轧辊技术的应用,也实现了部分规格产品的自由轧制。
冷弯和焊管机也可实现自由规格生产。
这些新技术使轧制过程变的柔性化。
2.铸轧一体化
利用轧辊来进行钢材生产因为其过程连续、高效、可控而且便于计算机控制等,在今后相当长一段时间内,以辊轧为特点的连续轧钢技术仍将是钢铁工业钢材成型的主流技术但轧钢前后工序的衔接技术必将有长足的进步。
在20世纪,由于连铸的应用和发展,已经逐步淘汰了初轧工序。
而用连铸技术所生产的薄带钢直接进行冷轧,又使连铸与热轧工序合二为一。
铸轧的一体化,将使轧制工艺流程更加紧凑。
同时,低能耗、低成本的铸轧一体化,也是棒、线、型材生产发展的方向。
3.轧制过程清洁化
在热轧的过程中,钢的氧化不仅要消耗钢材与能源,同时也会带来环境的污染,并给深加工带来困难。
因此,低氧化燃烧技术和低成本氢的应用都成为无氧化加热钢坯的基本技术。
其中酸洗除鳞是冷轧在生产中的最大污染源,新开发的无酸清洁型(AFC)除鳞技术,可以使带钢表面全无氧化物,光滑并具有金属光泽。
无氧化(或低氧化)和无酸除鳞(氧化铁皮)这两项被称为绿色工艺的新技术,将使轧制过程清洁化。
4.高新技术的应用
20世纪轧钢技术取得了重大进步的主要原因是信息技术的应用。
其中板形自动控制,自由规程轧制,高精度、多参数在线综合测试等高新技术的应用使轧钢生产达到了全新水平。
轧机的控制已开始由计算机模型控制转向了人工智能控制,并且随着信息技术的发展,将实现生产过程的最优化,降低成本。
5.钢材的延伸加工
在轧钢的生产过程中,除应不断挖掘钢材的性能外,还要不断的扩大对多种钢材的延伸加工,。
如开发自润滑钢板来用于各种冲压件的生产;减少冲压厂润滑油的污染;开发建筑带肋钢筋焊网等,把钢材材料的生产和服务延伸到各个钢材使用部门。
随着工业的发展和轧钢技术的进步,轧钢工艺的装备水平和自动控制水平不断提高,老式轧机也不断被各种新型轧机所取代。
按照我国走新型工业化道路的要求,轧钢技术发展的重点也转移到可持续发展上,在保证满足环保要求的条件下,达到钢材生产的高质量和低成本。
6实现无头轧制
在棒线材生产上也应该广泛推广高技术集成的半无头、无头轧制工艺技术,从而缩短工艺流程,实现真正意义上的轧钢一火成材,或零火成材,最大限度地节约能源和降低生产成本。
无头轧制技术是轧钢技术最为理想的工艺形式,代表着当今轧钢的最高技术水平。
无头轧制技术与传统轧制方法相比具有以下几个优点:
(1)轧材全长以恒定速度轧制,减少甩尾和迭轧,降低了事故率,提高了轧制过程的稳定性,大大提高了轧机产能和设备利用率;
(2)轧制过程中张力恒定,使轧材断面波动减少;轧材质量均匀一致,具有优良的工艺性能、表面质量和外形尺寸公差;(3)成品长度不受限制,可根据交货要求任意剪切长度,轧材成材率显著提高;(4)轧件咬人次数减少,对轧辊的冲击降低,有利于轧辊以及易损件寿命的提高,总体降低生产成本
。
第二章可编程控制器
2.1PLC的由来和定义
2.1.1PLC的由来
在PLC问世之前,工业控制领域中是继电器控制占主导地位。
因为继电器控制系统有着十分明显的缺点:
体积大、耗电多、可靠性差、运行速度慢、适应性差,尤其当生产工艺发生变化时,就必须重新设计,重新安装,造成时间和资金的严重浪费。
为了改变这一现状,1968年美国最大的汽车制造商通用汽车公司(GM),为了适应汽车型号不断更新的需求,以在竞争激烈的汽车制造商中占优势,提出要研制一种新型的工业控制装置来取代继电器控制装置。
1969年美国数字设备公司(DEC)研制出了世界上第一台PLC,并再生产中得到应用。
从此,可编程序控制器这一新的控制技术迅速发展起来,而且,在工业发达国家发展很快。
2.1.2PLC的定义
在PLC的发展过程中,美国电气制造商协会(NEMA)经过四年的调查工作,于1980年首先将其正式命名为PC(ProgrammableController)作了如下定义:
“可编程序控制器是一种数字式的电子装置,它使用可编程序的储存器来存储指令。
并实现逻辑运算、顺序控制、计数、计时和算术运算等功能,用来对各种机械或生产过程进行控制。
定义强调了可编程序控制器应直接应用于工业环境,它必须具有很强的抗干扰能力、广泛的适应能力和应用范围,这是区别于一般微机控制系统的一个重要特征。
2.2可编程序控制器的发展历程及问题和解决对策
2.2.1可编程序控制器的发展历程
可编程序控制器在20世纪60年代出现,当时的可编程序控制器功能很简单,只有简单的逻辑、定时、计数等功能;用于可编程序控制器的集成电路的硬件还没有投入大规模工业化生产,CPU只以分立元件组成;存储器的存储容量也有限;用户指令只有二三十条,而且还没有成型的编程语言,机型单一。
所以一台可编程序控制器也最多能替代200~300个继电器组成的控制系统,但在体积方面,与现在的可编程序控制器相比却很大。
进入到70年代,随着中小规模集成电路的生产,可编程序控制器技术得到了很大的发展。
这时的可编程序控制器除了逻辑运算外,还增加了数值运算、计算机接口和模拟量控制等;软件开发也有了自诊断程序,程序存储开始使用EPROM;可靠性进一步提高,结构上开始有了模块式和整体式的区分,整机功能已经从专用向通用过渡。
70年代后期到80年代初期,微处理器技术日益成熟,单片微处理器、半导体存储器开始进入工业化生产,大规模集成电路开始大量应用。
可编程序控制器开始向多处理器方向发展,这样使得可编程序控制器的功能和处理速度大大增强,并具有了通信和远程I/O的能力,增加了多种特殊功能,比如浮点运算、查表、列表等,自诊断和容错技术也迅速发展起来。
80年代后期到90年代中期,随着计算机和网络技术的普及,以及超大规模集成电路、门阵列和专用集成电路的迅速发展,可编程序控制器的CPU已经发展成为由16位或32位微处理器构成,处理速度变得更快,而且引入了高速计数、中断、PID、运动控制等功能。
使得可编程序控制器几乎能够满足工业生产的各个领域,此时的可编程序控制器已完全取代了传统的逻辑控制装置,以小型机为核心的DDC(直接数字控制)控制装置和模拟量仪表控制装置。
由于联网能力的增强,既可与上位计算机联网,也可下挂FLEXI/O或远程I/O,从而可以组成分布式的控制系统(DCS)。
此时的梯型图语言和语句表语言也完全成熟,基本上标准化,SFC(顺序功能图)语言开始普及,专用的编程器也被个人计算机和相应编程软件替代,人机界面装置渐渐完善,已能进行对整个工厂的监控和管理,并发展了冗余技术,大大增强了可靠性。
进入到21世纪,可编程序控制器仍保持着旺盛的发展势头,并不断扩大其应用领域。
目前的可编程序控制器主要优两个发展方向:
一是综合化控制系统方向,它已经突破了原有的可编程序控制器的概念,并将工厂生产过程控制与信息管理系统密切结合起来,可向上为MES和ERP系统准备技术基础,这种趋势会使得举步维艰的ERP系统拥有坚实的技术基础,从而带来工业控制的一场变革,实现真正意义上的电子信息化工厂;二是微型可编程序控制器异军突起,体积就如手掌大小,但功能可覆盖单体设备以及整个车间的控制功能,并且具备联网功能,这种微型化的可编程序控制器使得控制系统可将触角延伸到工厂的各个角落。
随着世界经济一体化进程的加快,在技术发展的同时,发达国家更加注重了对可编程序控制器的知识产权的保护,国际大型可编程序控制器制造商纷纷加入了可编程序控制器的国际标准化组织,他们利用许多技术标准建立了符合他们经济利益的技术保护壁垒
。
2.2.2我国可编程序控制器发展中的问题及对策
目前我国的可编程序控制器发展主要面临三大问题。
一是技术层面上的,在国际可编程序控制器迅速发展的形势下,我国还没有具有自主的知识产权,也没有能够参与国际竞争的可编程序控制器产品,原因主要在于我国的整个基础工业都还有一定的差距,如芯片制造、模具加工等方面限制了我们的发展。
二是竞争层面上的,实际上也是一个经济竞争的问题。
现在95%的国内市场是由外国的可编程序控制器产品所占领,大、中型可编程序控制器中,几乎全部是由国外几大公司所垄断,随着我国使用可编程序控制器领域的扩大,市场也越来越大,然而国外几家大公司几乎每年都会推出新的产品针对市场,一旦使用了新的产品后,他们就会逐渐的提高产品的市场价格。
如果没有我国自己的自主知识产权的产品,我们在经济竞争中就只能处于被动。
三是市场秩序层面上的,随着改革开放的不断深入,特别是在加入WTO后,我国巨大的市场份额极大的吸引了国外的大公司,他们开拓市场的方法大多都是采用大范围建立代理销售渠道,这样每个公司的分销商和系统集成商都会有数十家,甚至上百家,这就造成了我国的分销商、系统集成商之间的激烈竞争,而这些无序的竞争便为国际大公司分而治之、获取稳定的高额利润创造了条件。
那么面对这些问题,我国的可编程序控制器的发展应该采取什么措施呢?
(1)面对如此大的市场,我国应该集中资金和技术力量,尽快研制出具有属于我国自己的自主知识产权的可编程序控制器的系列产品,就像以前的家电行业一样。
(2)发挥我国科学技术人员在可编程序控制器应用技术的优势,从而扩大可编程序控制器的应用领域。
特别是在我国加入WTO后,中国成为了“世界制造工厂”的过程正在加速,我国在努力将可编程序控制器应用在国民经济中的同时,还要凭借技术和劳动力优势,将可编程序控制器投资到外商企业中进行应用,并逐步进入国际可编程序控制器的应用市场,让我国的应用技术形成真正的增值服务,从而带动我国相关成套设备和软件产业的发展。
(3)在扩大可编程序控制器应用的同时,要在软件集成化上下功夫。
针对不同的工业生产过程,形成具有我国特点的系统集成软件、人机界面软件和系统应用软件,在一些我国领先的工业行业中制造出具有核心技术的系统应用软件。
真正形成具有国际标准的、可进行复制的模块化软件。
采取上述策略后,我国就能在可编程序控制器的应用上率先实现突破,融入全球一体化经济之中,形成具有自主知识产权的软件产业,进而研制、开发、生产出具有自主知识产权,能够参与国际竞争的可编程序控制器产品
。
2.3可编程控制器的基本构成
2.3.1可编程控制器的硬件组成
PLC种类繁多,但从广义上讲,PLC也属于一种计算机系统,只不过它比计算机具有更强的与工业相连接的I/O接口,更适应于工业环境,但它的实际组成和一般的计算机系统基本相同,由硬件和软件两部分。
PLC的硬件结构框图如图2-1所示。
输入
设备
PLC
打印机
编程器
图2.1PLC的硬件结构框图
(1)中央处理器(CPU)
与一般计算机一样,CPU是PLC的核心,它包括微处理器和控制接口电路,起着总指挥的作用。
微处理器用来实现逻辑运算、数字运算,协调控制系统内部各部分的工作。
控制接口电路是微处理器与主机内部其他单元进行联系的部件,它主要有数据缓冲、单元选择、信号匹配、中断管理等功能。
微处理器通过控制接口电路来实现与各个内部单元之间的可靠的信息交换和最佳的时序配合。
CPU主要的任务有:
控制从编程器键入的用户程序和数据的连接与储存;用扫描的方式通过I/O部件接受现场的状态和数据,并存入输入映像存储器或数据存储器中;诊断PLC内部电气的工作故障和编程中的语法错误等;PLC进入运行状态后,从存储器逐条读取用户指令,经过命令解释后按指令规定的任务进行数据传送,逻辑或算术运算等。
(2)存储器
PLC内部存储器包括有两类;一类是系统程序存储器,另一类是用户程序存储器。
系统存储器主要用来存放系统管理程序、用户指令和标准