加工中心主轴准停操纵原理及常见故障分析出自网络.docx
《加工中心主轴准停操纵原理及常见故障分析出自网络.docx》由会员分享,可在线阅读,更多相关《加工中心主轴准停操纵原理及常见故障分析出自网络.docx(14页珍藏版)》请在冰豆网上搜索。
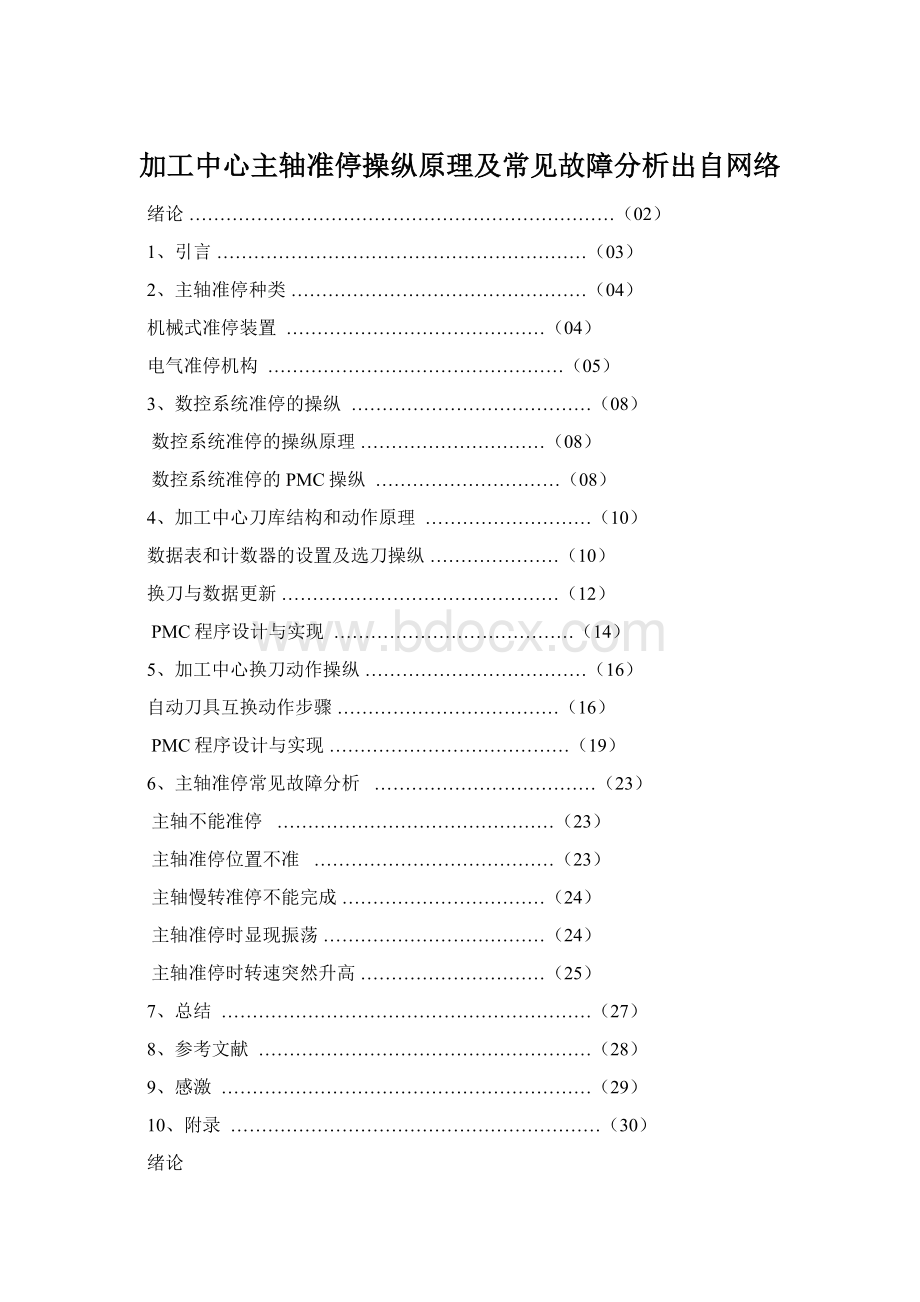
加工中心主轴准停操纵原理及常见故障分析出自网络
绪论……………………………………………………………(02)
1、引言……………………………………………………(03)
2、主轴准停种类…………………………………………(04)
机械式准停装置……………………………………(04)
电气准停机构…………………………………………(05)
3、数控系统准停的操纵…………………………………(08)
数控系统准停的操纵原理…………………………(08)
数控系统准停的PMC操纵…………………………(08)
4、加工中心刀库结构和动作原理………………………(10)
数据表和计数器的设置及选刀操纵…………………(10)
换刀与数据更新………………………………………(12)
PMC程序设计与实现…………………………………(14)
5、加工中心换刀动作操纵………………………………(16)
自动刀具互换动作步骤………………………………(16)
PMC程序设计与实现…………………………………(19)
6、主轴准停常见故障分析………………………………(23)
主轴不能准停………………………………………(23)
主轴准停位置不准…………………………………(23)
主轴慢转准停不能完成……………………………(24)
主轴准停时显现振荡………………………………(24)
主轴准停时转速突然升高…………………………(25)
7、总结……………………………………………………(27)
8、参考文献………………………………………………(28)
9、感激……………………………………………………(29)
10、附录……………………………………………………(30)
绪论
主轴停转时要求停在一个固定位置的功能称为准停功能。
自动换刀的数控镗床或铣床,切削转矩一般是通过主轴上的端面键和到柄上的键槽来传递的,因此每一次自动换刀时,都必需使刀柄上的键槽对准主轴的端面键,因此要求有准停功能。
在加工周密孔系时,假设每次都能在主轴固定的圆周位置上换刀,就能够保证刀尖与主轴相对位置的一致性,从而减少被加工孔的尺寸的分散度。
本文结合加工中心明白换刀系统,详细的讲述主轴准停的分类,原理和故障分析。
关键字:
主轴准停,加工中心,数控机床,自动换刀
1、引言
加工中心数控机床的重要功能之一确实是主轴的定向准停,以实现自动换刀或周密加工的对刀、让刀。
据统计,有关主轴自动换刀装置(ATC)这一部份的故障,在加工中心的实际应用中显现最为频繁。
而且很多加工中心保护者对加工中心主轴准停的结构、原理及其维修不清楚,为此,本文对目前几种常见的加工中心主轴准停装置进行总结分类,别离介绍其结构、工作原理,并给出几种常见的故障实例和维修方式。
二、主轴准停装置的种类
通常主轴准停机构有两种,即机械式与电气式。
机械式准停装置
图2-1为典型的机械式准停装置,要紧由带有V形槽的粗、精定位盘、定位油缸、定向活塞、无触点接近开关等组成,装在主轴的尾部。
其中,粗定位盘用螺钉紧固在精定位盘上,带有V形槽的精定位盘与主轴维持必然关系,以实现主轴圆周位置的准停。
准停前,假设主轴处于运行状态,当CNC发出准停指令后,主轴迅速降速至该机床设定的定向准停的低速度nort(一样设定在60~300r/min)旋转;假设主轴静止时,当CNC发出准停指令后,主轴那么迅速升速到设定的定向准停的最低速度旋转,当检测到无触点开关的有效信号后,主轴电动机当即停止并断开主传动链(现在主轴由于惯性会继续运转),同时准停油缸右腔进油,定向活塞带动定位销伸出并压向接触精定位盘面,定位销端部滚子在精定位盘面上转动,当其正对定位盘V形槽时,定位销在油缸的压力下插入V形槽,卡住槽轮,完成准停精定位。
最终,准停到位信号LS2有效,准停动作
图2-1机械式准停装置原理图
完成。
机械准停装置只能进行单角度准停。
采纳这种传统方式定位,结构复杂,在初期数控机床上利用较多。
电气准停机构
现代数控机床采纳电气方式定位较多。
电气方式定位一样有以下三种实现方式。
2.2.1 磁传感器型主轴准停装置
如图2-2所示,磁传感器主轴准停装置是利用磁性传感器检测定位。
在主轴上安装个发磁体,在距离发磁体旋转外轨迹1~2mm处固定一个磁传感器,它通过放大器并与主轴操纵单元相连接,当主轴操纵单元接收到数控系统发来的准停信号ORT时,主轴当即变速至主轴准停时的设定速度,当主轴操纵单元接收到磁传感器信号后,主轴驱动立
图2-2磁传感器主轴准停装置原理图
即进入磁传感器作为反馈元件的位置闭环操纵,目标位置即为准停位置。
准停完成后,主轴驱动装置向数控系统发出准停完成信号ORE。
磁传感器主轴准停装置也是单角度准停。
2.2.2 编码器型主轴准停装置
如图2-3所示,这种方式是通过主轴电动机内置安装的位置编码器或在机床主轴箱上安装一个与主轴1∶1同步旋转的位置编码器来实现准停操纵,准停角度可任意设定。
主轴驱动装置内部可自动转换,使主轴驱动处于速度操纵或位置操纵状态。
图2-3编码器型主轴准停装置原理图
2.2.3 数控系统操纵主轴准停装置
数控系统操纵主轴准停原理如图2-4所示,准停的角度可由数控系统内部设定成任意值,准停由数控代码M19执行。
当执行M19或M19S××时,数控系统先将M19送至可编程操纵器(PLC),经PLC处置后送出操纵信号,操纵主轴电动机由静止迅速升速或在原先运行的较高速度下迅速降速到定向准停设定的速度nort运行,来寻觅主轴编码器零位脉冲C,然后进入位置闭环操纵状态,并按系统参数设定定向准停。
假设执行M19,无S指令,那么主轴(定位)准停于相对C脉冲的某一缺省位置;假设执行M19S××,那么主轴(定位)准停于指令位置,即相对零位脉冲××度处。
需要说明的是,关于加工中心主轴定向准停的具体操纵进程,不同的系统,其具体操纵执行进程可能略有区别,但大同小异。
图2-4数控系统操纵主轴准停原理图
3、数控系统准停的操纵
本文以FANUC数控系统专用PMC系统为例,偏重讲述数控系统准停,在加工中心的操纵原理和操纵方式。
数控系统准停的操纵原理
数控系统操纵主轴准停原理如图2-4所示,准停的角度可由数控系统内部设定成任意值,准停由数控代码M19执行。
当执行M19或M19S××时,数控系统先将M19送至可编程操纵器(PLC),经PLC处置后送出操纵信号,操纵主轴电动机由静止迅速升速或在原先运行的较高速度下迅速降速到定向准停设定的速度nort运行,来寻觅主轴编码器零位脉冲C,然后进入位置闭环操纵状态,并按系统参数设定定向准停。
假设执行M19,无S指令,那么主轴(定位)准停于相对C脉冲的某一缺省位置;假设执行M19S××,那么主轴(定位)准停于指令位置,即相对零位脉冲××度处。
需要说明的是,关于加工中心主轴定向准停的具体操纵进程,不同的系统,其具体操纵执行进程可能略有区别,但大同小异。
数控系统准停的PMC操纵
当执行M06时,M06的宏程序中M19开始执行,系统M码选通信号为1,系统读出M指令后使得F10中的数据改变,译码指令DECB执行后,对应的继电器导通。
主轴主向继电器为1,其中,别离为主轴正转和反转的操纵信号,在此起互锁作用,CNC读取信号为1时,主轴开始寻觅主轴编码器零位脉冲。
然后进入位置闭环操纵状态,并按系统参数设定方向准停。
使主轴准停到位信号灯亮,至此M代码完成。
如梯形图2-5所示。
图2-5数控系统准停PMC操纵程序
4、加工中心刀库结构和动作原理
本文以BT50-24TOOL圆盘式刀库自动换刀为例,讨论运算机经历随机换刀方式的PMC的操纵。
数据表和计数器的设置及选刀操纵
在随机自动换刀方式中,刀库上的刀具能与主轴的刀具任意的
直接互换。
随机换刀操纵方式需要在PMC内部设置一个模拟刀库的数据表,其长度为刀库容量+1,数据表的表序号与刀套编号相对应,主轴的刀套编号为0,数据表内容对应刀套中所存刀具号。
以图4-1十工位鼓盘式刀库为例,以地址D420~D430成立数据表#其数据表序号和对应刀具号如表4-1。
表4-1刀号数据表图4-1刀库示用意
其中0~10为刀套号,也是数据表序号,且0是将主轴作为刀库中的一个刀套,11~21为刀库中相应刀套号中的刀具号,由于刀具数据表事实上是刀库中寄存刀具的一种映象,因此数据表与刀库中刀具的位置应始终维持一致,对刀具的识别实质上转变成对刀库位置的识别。
当PMC接到寻觅新刀具的指令(Txx)后,在模拟刀库的刀号数据表中进行数据检索,检索到T代码给定的刀具号在数据表中的表序号也确实是刀套号,存入目标刀套号存储器中,设目标刀套号的存储地址为D431。
假设在刀号数据表中没有检索刀指令刀具号,那么机床显现报警,终止换刀指令处置。
将目标刀套号与当前换刀位置的刀套号(称为当前刀套号)相较较来决定是不是转动刀库,因此需要成立一个环形计数器来记录当前刀套号。
见图4-2。
据FANUC数控系统专用PMC指令中计数器操纵数据的格式:
D350~D351:
计数器的预置值,那个地址为刀库中的刀套数。
D352~D353:
计数值,那个地址为当前图4-2环形计数器设定刀套号。
D354:
为PMC系统利用。
当刀库旋转时,每一个刀套通过换刀位置时,由外部检测装置产生一个脉冲信号送到计数器。
当刀库正转1个工位时,当前刀套号增1;当刀库反转1个工位时,当前刀套号减1;因此D352~D353中的值老是指示刀库的此刻位置。
当目标刀套号为0,即目标刀号已经在主轴上,那么不用换刀;当检索刀套号与当前刀套号一致时,就不用旋转刀库,直接换刀;不一致时,那么可利用ROT功能指令计算刀库旋转方向和旋转步数。
刀库旋转方向输出给W1,旋转步数计算结果存储到D355中。
用W1信号驱动刀库转动,刀库转动后,检测装置发出脉冲给PMC,更新D352当前刀套号的内容,再循环执行ROT指令,直到D355中的结果为0。
换刀与数据更新
铛铛前刀套号旋转到与目标刀套号一致后,就可执行M06指令,即实现刀库与机床主轴之间的刀具互换动作。
刀具互换装置不同,其换刀动作就不同,以立式加工中心鼓盘式刀库双臂回转机械手换刀方式为例,其换刀动作有:
(1)抓刀:
手臂转到主轴和当前刀座所在位置,同时抓住刀库和主轴上的刀具。
(2)拔刀→换刀→插刀:
主轴夹头松开刀具,机械手同时将刀库和主轴上的刀具拔出。
手臂旋转,新旧刀具互换。
机械手同时将新旧刀具别离插入主轴和刀库,然后主轴夹头加紧刀具。
(3)复位:
转动手臂,回到原始位置。
换刀后,刀号数据表中的数据发生转变,需要更新,将数据表中当前刀套号对应的刀具号与主轴上的刀具号相对调,如此就保证了数据表与刀库中刀具的位置始终维持一致。
换刀完成后,数据表中的数据必需更新,以知足随机换刀后,下次的再次利用。
刀库中寄放器的数据更新及将刀套0(主轴)中刀号和所换刀套中的刀号调换,以此保证寄放器中刀号相匹配。
在此,咱们通过XMOVE指令,先将D431中的数据移动到D432中,然后将D420中的数据移动到D431中,最后将D432中的数据移动至D420中。
因为D431中存
储的是换刀进程中被换的刀具号,通过以上的几个XMOVE指令,即便得D431和D420对调,完成数据的更新。
PMC操纵加工中心随机自动换刀程序流程图如图4-3。
图4-4随机自动换刀I/O地址分派图
图3-3刀库动作流程图
3.3PMC程序设计与实现
3.3.1系统PMC输入/输出地址分派
如图4-4为随机制动换刀I/O地址分派图,其中SQ3()为刀库刀位计数信号,FR1为刀库电机过载信号。
为刀库电机正转操纵信号,为刀库电机反转操纵信号。
3.3.2随机制动换刀的PMC操纵
以FANUC数控系统专用PMC系统为例,其关键指令如图4-4。
图4-4加工中心随机自动换刀PMC程序
5、加工中心换刀动作操纵
自动刀具互换动作步骤
本文以BT50-24TOOL圆盘式刀库绝个为例说明,如图5-1。
1.程序执行到选刀指T令码时,系统通过方向判别后操纵刀库电动机1正转或反转,刀库中刀位计数开关2开始计时(计算出抵达换刀点的位置),当刀库上所选的刀具转到换刀位置时,旋转刀库电动机当即停止,完成选刀定位操纵。
2.今世码执行后,倒刀电磁阀线圈获电,气缸推动选刀的刀杯向下翻转90度,倒刀到位检测信号开关8发出信号,完成倒刀操纵,同时那个信号仍是互换刀具的开始信号,如图5-2b所示。
3执行到互换刀具指令,互换刀具指令一样为M06,第一主轴自动返回换刀点(一样是机床的第二参考点),且实现主轴准停,然后换刀电动机10启动运行,通过锥齿轮14、凸轮滚子1五、十字轴17带动机械手从原位逆时针旋转60度,进行机械手抓刀操纵,当机械手扣刀定位开关6发出到位信号后,换刀电动机10当即停止,主轴刀具加紧装置自动松开,如图5-2c所示。
4.主轴刀具松开后,换刀电动机10起动运行,通过圆柱凸轮1二、杠杆13是机械手下降,进行拔刀操纵,机械手完成拔刀后,换刀电动机10继续运转,持续完成下一个换刀动作,如图5-2d所示。
5.当机械手完成拔刀操纵后,通过锥齿轮14、凸轮滚子1五、十字轴17带动机械手逆时针旋转180度,使主轴刀具与刀库刀具互换位置。
然后通过圆柱凸轮1二、杠杆13使机械手上升,把互换后的刀具插入主轴锥孔和刀库的刀套中。
机械手完成插刀后,换刀电动机停止开关5发出信号使电动机当即停止。
刀具插入主轴锥孔后,刀具的自动加紧机构加紧刀具,如5-2e所示。
6.当机械手扣刀到位检测信号开关6再次接通后,换刀电动机10启动运行,通过锥齿轮14、凸轮滚子1五、十字轴17带动机械手顺时针转动60度,回到机械手的原点位置。
机械手原位到位开关7接通后,换刀电动机10当即停止,如图5-2f所示。
7.当机械手回到原位后,机械手原位到位后,机械手原位到位开关7接通回刀电磁阀线圈获电,气缸推动刀杯向上翻转90度,为下次选刀做预备。
回刀气缸伸出定位开关9接通,完成整个换刀进程。
其PMC操纵加工中心随机自动换刀程序流程图如图5-3。
图5-3机械手动作流程图
5.2PMC程序设计与实现
5.2.1系统PMC输入/输出地址分派
图5-4,为主轴准停PMC输入/输出信号地址分派图,为机械手换刀电动机停信号,为机械手扣刀定位信号,为机械手原点确认信号,为倒气缸缩回定位信号,为回刀气缸伸出定位信号,为主轴汽缸操纵信号,为汽缸复位到位信号,为机械手电机过载信号,为刀杯液压泵过载信号;为机械手电机操纵信号,为刀杯液压驱动信号,为刀杯液压复位操纵信号,刀杯复位操纵信号,为主轴汽缸动作操纵信号。
图5-4机械手动作I/O地址分派图
5.2.2PMC程序设计与实现
以FANUC数控系统专用PMC系统为例,当执行M06时,M06的宏程序中M80,M81,M90,M82,M91,M83,M84依次执行,系统M码选通信号为1,系统读出M指令后使得F10中的数据改变,译码指令DECB执行后,对应的R继电器导通。
执行M80时,为1,使得刀杯动作中间继电器为1,使得刀杯复位液压泵停止工作(),刀杯动作液压泵工作(),直至换换刀动作完全完成(,都为1),当刀杯液压泵过载()时那么显现过载报警。
当执行M81,M82,M83时,机械手动作中间继电器,接踵为1,使得机械手操纵信号为1,机械手开始动作,由连续贯的机械传动,完成机械手动作,,,为机械手动作中的行程到位检测信号,为机械手电机过载爱惜信号。
当刀杯复位信号为1时,机械手动作完成。
M90为主轴汽缸操纵,当系统读到M90时,使得为1,接通,通过操纵主轴汽缸电磁阀,使得汽缸下移,现在即可开始换刀动作,M91为汽缸复位操纵,当执行M91时,中间继电器为1,使汽缸操纵信号失电,使得汽缸复位。
M85为显现故障机会械手无条件复位信号,它使机械手操纵电机一直带电,直到机械手复位信号为1。
具体操纵梯形图如图5-5。
图5-5机械手动作PMC操纵
6、主轴准停常见故障分析
主轴不能准停
故障现象:
某SIEMENS810M的立式加工中心,配套6SC6502主轴驱动器,调试时,当主轴转速大于200r/min时,主轴不能准停。
分析与维修进程:
为了分析故障缘故,维修时进行了如下实验。
1)输入并依次执行“S100 M03;M19”指令,机床准停正常。
2)输入并依次执行“S100 M04;M19”指令,机床准停正常。
3)输入并依次执行“S200 M03;M05;M19”指令,机床准停正常。
4)直接输入并依次执行依照以上实验,可确认数控系统和驱动器工作正常,引发故障的缘故可能是编码器高速特性不良或主轴实际准停速度太高。
检查主轴电动机的实际转速,发觉该机床的主轴实际转速与指令值相差专门大,当执行指令M03 S200时,实际机床主轴转速为300r/min,调整主轴驱动器参数,使主轴实际转速与指令值相符后,故障排除,机床恢复正常。
主轴准停位置不准
故障现象:
某配套YASKAWAJ50M的加工中心,在机床换刀时,主轴准停不准。
分析与维修进程:
认真检查机床的准停动作,发觉机床在主轴转速小于10r/min时,主轴准停位置正确,但在主轴转速大于10r/min时,准停点在不同的速度下均不一致。
通过系统的号诊断参数#1287bit0~bit2,检查主轴编码器信号输入,发觉该机床的主轴零位脉冲输入信号在一转内有多个,引发了准停点的混乱。
检查CNC与主轴编码器的连接,发觉机床出厂时,主轴编码器的连接电缆线未依照规定的要求利用双绞屏蔽线,当机床环境发生转变后,由于线路干扰,引发主轴零位脉冲的混乱。
从头利用双绞屏蔽线连接后,故障排除,机床恢复正常工作。
主轴慢转准停不能完成
此类故障通常与主轴准停的磁性传感器、主轴位置编码器等部件有关,或是由机械传动系统的安装联接等因素引发的。
故障现象:
一台采纳FANUC10T系统的数控车床,在加工进程中,主轴不能按指令要求进行正常准停,主轴驱动器准停操纵板上的ERROR指示灯亮,主轴一直维持慢速转动,准停不能完成。
分析与维修进程:
由于主轴在正常旋转时动作正常,故障只是在进行主轴准停时发生,由此能够初步判定主轴驱动器工作正常。
依照机床与系统的维修说明书,对照故障的诊断流程,检查了PLC梯形图中各信号的状态,发此刻主轴360°范围旋转时,主轴准停的磁性传感器信号始终为“0”正常。
主轴准停时显现振荡
故障现象:
某SIEMENS810M的立式加工中心,在改换主轴编码器后,主轴准停时不断振荡,无法完成准停。
分析故障:
由于该机床改换了主轴位置编码器,机床在执行主轴准停时减速动作正确,分析故障缘故应与主轴位置反馈极性有关,当位置反馈极性设定错误时,必然会引发以上现象。
改换主轴编码器极性,能够通过互换编码器的输出信号以Ua1/Ua2,3Ua1/3Ua2进行。
当编码器准停由CNC操纵时,也能够修改CNC机床参数,在本机床上通过修改810M的主轴位置反馈极性参数(MD5200bit1),主轴准停恢复正常。
主轴准停时转速突然升高
故障现象:
某配套YASKAWAJ50M的加工中心在机床改换主轴编码器后,发觉主轴能够正常旋转,但在执行主轴准停指令M19时,主轴先减速,随后转速突然升高,且系统进行报警。
分析与维修进程:
分析该机床的主轴准停动作,该机床采纳编码器准停方式。
按准停原理,其准停进程如下:
1)执行M19指令,主轴第一减速到参数#6462所设定的速度慢速旋转;
2)在主轴按参数#6462所设定的速度值转动稳固后,检测编码器零位脉冲;
3)系统检测到零位脉冲后,进入位置闭环调剂,并以参数#6463所设定的速度寻觅准停点;
4)主轴抵达指定的准停点后,维持位置闭环,使主轴停止在准停点。
依照以上的动作进程,检查机床的实际动作,发觉机床主轴是在执行到进程3)动作开始时,显现转速突然升高现象的。
因此,故障的缘故应该是主轴的位置反馈极性错误,致使了位置环的正反馈,引发了主轴转速的突然上升。
在以上分析的基础上,通过对调主轴编码器的反馈脉冲A与B、3A与3B,再次进行实验,故障消失,机床恢复正常。
7、总结
本文从主轴准停、刀库随机自动选刀、机械手动作等方面,分析了数控加工中心的换刀进程及其原理,本文应用FANUC专用PMC功能指令给出了部份操纵程序。
本次毕业设计,进一步巩固了以前所学的一些知识并将他们灵活应用,也学到了一些书本上学不到的东西,培育了自己的自学能力;同时也深深感受到了自己在知识方面的欠缺,为下一步的学习找到了方向。
8、参考文献:
【1】王润孝.机床数控原理与系统[M].西北工业大学,2000
【2】李佳.数控机床及应用[M].清华大学出版社,2002
【3】王侃夫.机床数控技术基础[M].机械工业出版社,2001
【4】廖成效.朱启逑.数字操纵机床[M].武汉:
华中理工大学出版社,1996
【5】刘永久.数控机床故障诊断与维修技术[M].机械工业出版社,2006
9、致谢
由于本次毕业设计采纳小组一起完成的方式,在小组成员的一起尽力下圆满完成了本次设计,切身感受了小组成员合作的优势和重要性,在此对本次毕业设计小组成员表示感激。
在整个毕业设计的进程中,也取得了王进平等教师和其他同窗的大力支持和帮忙,在此一并表示忠心的感激,同时在学校几年的学习里,对列位教师对我的栽培和教育表示感激!
10、附录
空军航空维修技术学院
毕业设计(论文)任务书
数控设备应用与保护专业数设0601班姓名XXXXX学号31
指导教师:
XXXXX
设计题目:
加工中心主轴准停操纵及常见故障分析
设计题号:
wxw02
设计内容及要求:
1.绘制并打印所在单位数控加工中心换刀动作流程图一张(2号图纸);
2.绘制并打印PLC自动换刀相关输入输出信号地址分派图一张(2号图纸);
3.绘制并打印PLC操纵梯形图(主轴准停)一张(2号图纸);
4.完成设计说明书编制(很多于8000字);
设计说明书内容应包括:
结合所在单位具体加工中心,分析刀库结构和动作原理;主轴准停操纵及其工作原理,完成PLC操纵程序编写(利用梯形图)和说明;主轴准停进程中常见故障分析及解决方法。
联系方式:
:
邮箱:
JPWLX
数控教研室
二00八年十一月