SMT培训元器件基础知识.docx
《SMT培训元器件基础知识.docx》由会员分享,可在线阅读,更多相关《SMT培训元器件基础知识.docx(26页珍藏版)》请在冰豆网上搜索。
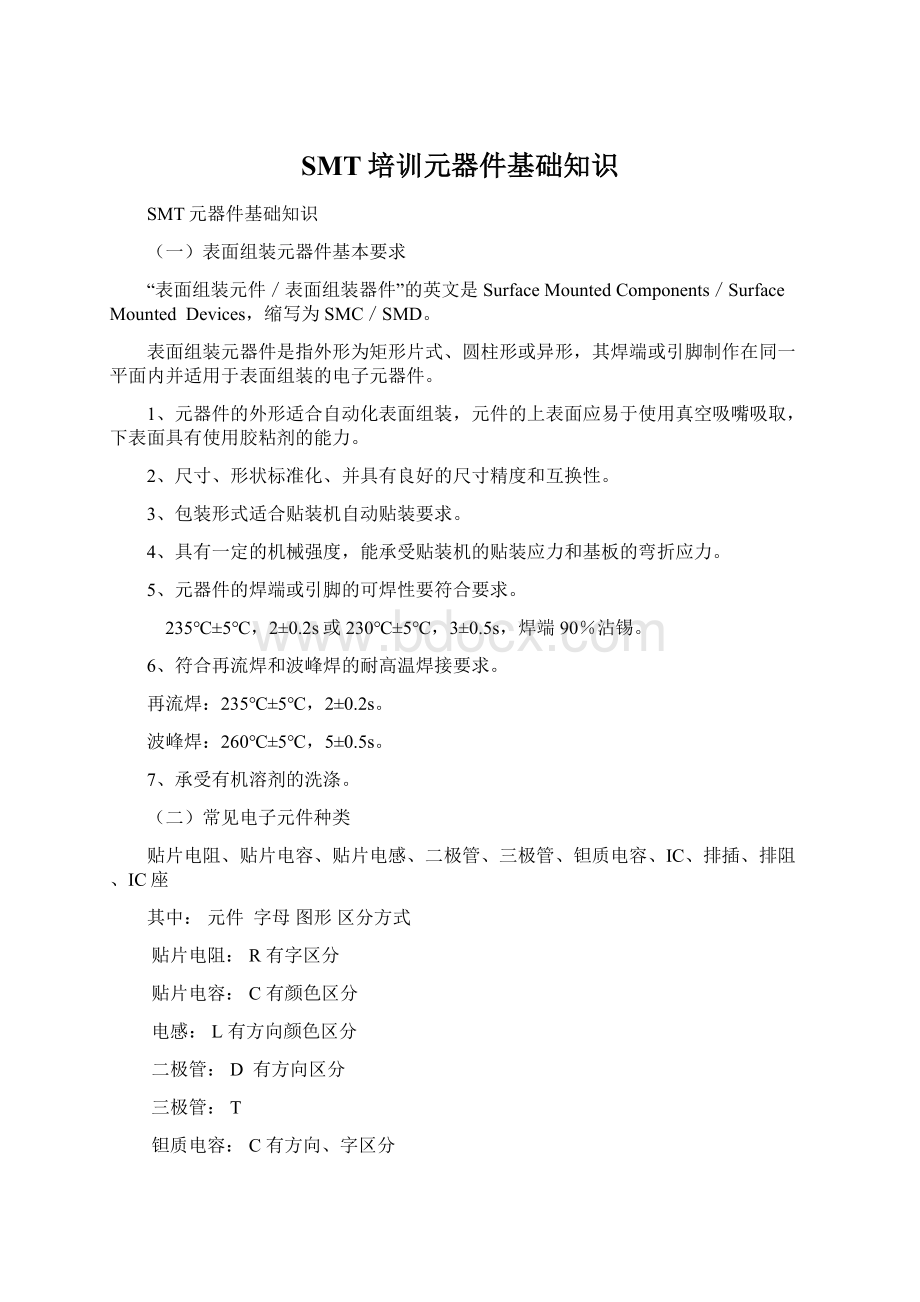
SMT培训元器件基础知识
SMT元器件基础知识
(一)表面组装元器件基本要求
“表面组装元件/表面组装器件”的英文是SurfaceMountedComponents/SurfaceMounted Devices,缩写为SMC/SMD。
表面组装元器件是指外形为矩形片式、圆柱形或异形,其焊端或引脚制作在同一平面内并适用于表面组装的电子元器件。
1、元器件的外形适合自动化表面组装,元件的上表面应易于使用真空吸嘴吸取,下表面具有使用胶粘剂的能力。
2、尺寸、形状标准化、并具有良好的尺寸精度和互换性。
3、包装形式适合贴装机自动贴装要求。
4、具有一定的机械强度,能承受贴装机的贴装应力和基板的弯折应力。
5、元器件的焊端或引脚的可焊性要符合要求。
235℃±5℃,2±0.2s或230℃±5℃,3±0.5s,焊端90%沾锡。
6、符合再流焊和波峰焊的耐高温焊接要求。
再流焊:
235℃±5℃,2±0.2s。
波峰焊:
260℃±5℃,5±0.5s。
7、承受有机溶剂的洗涤。
(二)常见电子元件种类
贴片电阻、贴片电容、贴片电感、二极管、三极管、钽质电容、IC、排插、排阻、IC座
其中:
元件字母图形区分方式
贴片电阻:
R有字区分
贴片电容:
C有颜色区分
电感:
L有方向颜色区分
二极管:
D有方向区分
三极管:
T
钽质电容:
C有方向、字区分
IC:
U
IC分为:
SOJ两边脚朝内
SOP两边脚朝外
QFP四方有脚
(三)电子元件的基本常识:
1、电阻
电阻按功率分可分为1/4W、1/6W、1/8W等;
按材料分:
碳膜电阻、金属膜电阻、陶瓷电阻等;
按阻值分:
色环电阻、数字电阻等;
电阻在电路中的主要作用为分流、限流、分压、偏置、滤波(与电容器组合使用)和阻抗匹配等。
矩形片式电阻器主要由基板.电阻膜.保护膜.电极四大部分组成.
1)基板 基板材料一般采用96%的三氧化二铝陶瓷.基板除了应具有良好的电绝缘性外,还应在高温下具有优良的导热性.电性能和机械强度等特征.此外还要求基板平整,划线准确.标准,以充分保证电阻.电极浆料印刷到位.
2)电阻膜 用具有一定电阻率的电阻浆料印刷到陶瓷基板上,再经烧结而成.电阻浆料一般用二氧化钌.
3)保护膜 将保护膜覆盖在电阻膜上,主要是为了保护电阻体.它一方面起机械保护作用,另一方面使电阻体表面具有绝缘性,避免电阻与邻近导体接触而产生故障.在电渡中间电极的过程中,还可以防止电渡液对电阻膜的侵蚀而导致电阻性能下降.保护膜一般是低熔点的玻璃浆料,经印刷烧结而成.
4)电极 是为了保证电阻器具有良好的可焊性和可靠性,一般采用三层电极结构:
内.中.外层电极.
内层电极是连接电阻体的内部电极,其电极材料应选择与电阻膜接触电阻小,与陶瓷基板结合力强以及耐化学性好,易于施行电镀作业.一般用银钯合金印刷烧结而成.
中间层电极是镀镍层,又称阻挡层.其作用是提高电阻器在焊接时的耐热性,缓冲焊接时的热冲击.它还可以防止银离子向电阻膜层的迁移,避免造成内部电极被蚀现象(内部电极被焊料所熔蚀)
外层电极锡铅层,又称可焊层.其作用是使电极有良好的可焊性,延长电极的保存期.一般用锡铅系合金电镀而成.
矩形片式电阻按电阻材料分成薄膜型电阻和厚膜电阻.其中薄膜型电阻的精度高电阻温度系数小.稳定性好,但阻值范围较窄,适用于精密和高频领域.厚膜电阻则是电路中应用最广泛的.
2、电容
电容按极性分:
无极性电容、有极性电容;
按材料分:
陶瓷电容、电解电容、绦纶电容、钽质电容等;
电容主要电路所起的作用:
滤波、移植、通交隔直藕合;
表面组装用电容器简称片式电容器.目前使用较多的主要有两种:
陶瓷系列电容器和钽电容器.其中瓷介电容器约占80%,其次是钽和铝电解电容器.
结构
片式电容器主要有:
内电极.陶瓷基材.和外电极三个部分组成.内电极主要是材料白金.钯或银的浆料印刷在生坯陶瓷膜上,经过叠层烧结而成.
外电极的结构与片式电阻器一样,采用三层结构:
内层为Ag或Ag-Pb中间镀Ni主要作用是阻止Ag离子迁移,外层镀Sn或镀Sn-Pb,主作用是易于焊接.
电容的误差值:
误差值:
在误差范围内可以接受的数值;
分为:
A.B.C.D、、、、、、Z;
每个电容后的字母都代表一个误差值;
字母的偏差范围:
104K:
±10%
104M:
±20%
104Z:
+80%-20%
104J:
±5%
精度高的物料可代替精度低的物料,反之,则不可;
3、二极管:
按材料分:
硅二极管、锗二极管;
按PN结的接触形状分:
点接触、面接触;
在电路中所起的作用:
检波、整流、限幅;
4、三极管:
按材料分:
硅三极管、锗三极管;
按频率分:
大功率、小功率;
主电路中所起的作用:
放大、限流、调整、检波;
三极管有三个脚分别为:
基极(B)、集电极(C)、发射极(E)
在电路中的表示符号:
(集电极)C(集电极)C
BB
(基极)(基极)
E(发射极)E(发射极)
NPN型PNP型
5、集成电路(IC):
IC由英文INTERGRATEDCIRCUIT的缩写;
IC按封装形式可分为双列式和单列式
双列式的IC脚数一定是双数,单列式可双数或单数;
IC是按下列方法规定那一个脚为第一个脚及各脚的顺序
①IC有缺口标志②以圆点作标识
1以横杠作标识
③以横杠作标识④以文字作标识(正看IC下排引脚的左边第一个脚为“1”)
(四)CHIP元件的規格﹕
名稱(英制)名稱(公制)LW
040210051.0mm×0.5mm
060316081.6mm×0.8mm
080521252.0mm×1.25mm
120632163.2mm×1.6mm
121032253.2mm×2.5mm
(五)阻容标称值的换算
1.电阻R(举例说明)
标称值
换算方法(基本换算单位:
欧姆—Ω)
实际电阻阻值值
2R2
R代表小数点:
2.2Ω
2.2Ω
5R6
R代表小数点:
5.6Ω
5.6Ω
R102
“2”代表“10”后面“0”的个数:
1000Ω
1KΩ
R682
“2”代表“68”后面“0”的个数:
6800Ω
6.8KΩ
R333
“3”代表“33”后面“0”的个数:
33000Ω
33KΩ
R104
“4”代表“10”后面“0”的个数:
100000Ω
100KΩ
R564
“4”代表“56”后面“0”的个数:
560000Ω
560KΩ
2.电容C
A.单位:
法拉,简称法,用“F”表示,微法(uF)、微微法(nF)、皮法(pF)。
B.换算法则:
1F=106uF=1012pF1uF=103nF1uF=106pF
C.举例:
标称值
换算方法(基本换算单位:
皮法—pF)
实际电容容值
C104
10×104pF=100000pF=0.1uF
(1uF=106pF)
0.1uF
C103
10×103pF=10000pF=0.01uF
(1uF=106pF)
0.01uF
C102
10×102pF=1000pF=1nF
(1nF=103pF)
1nF
C101
10×101pF=100pF
100pF
C470
47×100pF=47pF
47pF
C222
22×102pF=2200pF=2.2nF
(1nF=103pF)
2.2nF
3焊接缺陷:
常见焊接缺陷及其对策。
现将SMT生产过程中常见的焊接缺陷、产生原因及对策
缺陷种类
现象
引起原因
对策
印刷性差
(塌落)
1.印刷图形不挺刮,图形四周浸流\互连
2.焊膏量不够
3.粘接力不够
1.焊锡膏品质下降,如粘度太低
2.环境温度太高
3.钢板质量差
1.换锡膏
2.改变环境温度
3.换钢板,或清洗
桥连
两个或多个引线互连
模板窗口大或焊膏过干
换模板或焊膏
虚焊
元件端头未爬上锡
1.元件可焊性不好
2.再流炉温度未调好
3.焊膏的活性低
1.检测元件可焊性
2.调整炉温曲线
3.检测焊的活性
位移
元件偏移,严重时部分元件发生”冲浪”现象,片式R\C冲击到一处
1.PCB可焊性不好
2.元件可焊不好
3.焊膏活性差
1.解决PCB可焊性
2.解决元件可焊性
3.换焊膏
飞珠
元件四周出现小锡球
1.焊膏质量差
2.焊膏保管不当,混入水汽
3.焊接时升温过快
4.元件放置不准
1.换焊膏
2.正确使用焊膏
3.改善工艺方法
4.将元器件放正确
焊点
不光亮
焊点灰暗
1.焊膏质量差
2.焊接温度不正确
1.换锡膏
2.正确设置温度
残留物多
焊点出现黄色残留物
焊膏配比不正确
换焊膏
清洗后PCB发白
清洗后元件四周存在白色残留物
1.焊膏清洗性能差
2.清洗剂不好
1.换焊膏
2.换清洗剂
碑立
元件一端翘起
1.PCB及元件的可焊性
2.焊膏的选用
3.加热速度过快
4.焊盘设计不合理,以及受其它组件影响
1.解决可焊性
2.换焊膏
3.适当减低加热速度
4.改善PCB及焊盘设计
(Δ宽<10mil,Δ长<50m)
焊料的疲劳损坏
焊后测试良好,但经高低温循环后出现虚焊,是一种常见的隐性毛病.此时焊点内有气孔,锡层薄
1.焊膏中残留的有害杂质过多如Al、Zn、Ca
2.焊接温度不正确
3.元件可焊性差,引脚的共面性差
4.焊盘太小,以致锡缘太薄
1.最好采用耐疲劳性焊锡膏
2.重新设定工艺参数
3.使用好的元器件
4.改善焊盘设计
7.2.7贴片机常见故障
7.2.7.1当出现故障时,建议按如下思路来解决问题:
A:
详细分析设备的工作顺序及它们之间的逻辑关系。
B:
了解故障发生的部位、环节及其程度,以及有无异常声音。
C:
了解故障发生前的操作过程。
E:
是否发生在特定的器件上。
F;是否发生在特定的批量上。
G:
是否发生在特定的时刻。
7.2.7.2常见故障的分析。
A:
元器件贴装偏移
主要指元器件贴装在PCB上之后,在X-Y方向出现位置偏移,如图七所示,其产生的原因如下:
⑴:
PCB板的原因
a:
PCB板曲翘度超出设备允许范围,一般要求如图八所示:
上翘最大1.2mm,下曲最大0.5mm。
b:
支撑销高度不一致,致使印制支撑不平整。
C:
工件台支撑平台平面度不主良(倾斜)
d:
电路板布线精度低、一致性差,特别是批量与批量之间差异大。
⑵:
贴装吸嘴着气压过低,在取件(A位)及贴装(E位)应在400mHG以上。
⑶:
贴装时(E位)吹气压力异常,(一般为0.1kgf/cm)
⑷:
胶粘剂、焊锡膏涂布量异常或偏离。
(过多导致元件贴装时或焊接时位置发生漂移,过少导致元件贴装后在工作台高速运动时出现偏离原位,涂敷位置不准确,因其张力作用而出现相应偏移。
)
⑸:
程序数据设置不正确(X-Y坐标、取件、旋转、贴装速度、补偿值等,元器件数据设置错误、部品不规则或引脚共面度差)。
⑹:
基板定位不良(定位销损坏或严重磨损,导致PCB定位不准而出现元件贴装位置偏移)。
⑺:
贴装吸嘴上升时运动不平滑,较为迟缓。
⑻:
X-Y工作台动力件与传动件间连轴器松动。
⑼:
贴装头吸嘴安装不良(松动、弯曲、磨损)。
⑽:
吹气时序与贴装头下降时序不匹配(不同步,一般当吸嘴下降至PCB表面0.2-0.3mm高度时吸嘴应吸气转换为吹气)。
⑾:
吸嘴中心数据、光学识别系统的摄像机的初始数据设值不良。
B:
器件贴装角度偏移
主要是指器件贴装时,出现角度方向(θ方向)旋转偏移,如图九所示,其产生的主要原因有以下几方面:
⑴:
PCB板的原因
a:
PCB板曲翘度超出设备允许范围:
上翘最大1.2MM,下曲最大0.5MM。
b:
支撑销高度不一致,使印制板支撑不平整。
C:
工作台支撑平台平面度不良(倾斜)
d:
电路板布线精度低、一致性差,特别是批量与批量之间的差异大。
⑵:
贴装吸嘴吸着气压过低,在取件(A位)及贴装(E位)应在400mmHG以上。
⑶:
贴装时(E位)吹气压力异常,(一般为0.1kgf/cm)
⑷:
胶粘剂、焊锡膏涂布量异常或偏离。
(过多导致元件贴装时或焊接时位置发生
漂移,过少导致元件贴装后在工作台高速运动时出现偏离原位,涂敷位置不准
确,因其张力作用而出现相应偏移。
)
⑸:
程序数据设置不正确(X-Y坐标、取件、旋转、贴装速度、补偿值等,元器件
数据设置错误、部品不规则或引脚共面度差)。
⑹:
吸嘴端部磨损、堵塞或粘有异物。
⑺:
贴装吸嘴上升或旋转运动不平滑,较为迟缓。
⑻:
吸嘴单元与X-Y工作台之间的平行度不良或吸嘴原点检测不良。
⑼:
光学摄像机安装松动或数据库设置不当。
⑽:
吹气时序与贴装头下降时序不匹配(不同步,一般当吸嘴下降至距PCB表面
0.2-0.3mm高度时吸嘴应吸气转换为吹气)。
C:
元件丢失:
主要是指元件在吸片位置(A位)与贴片位置(B位)间丢失.其产生的主要原因
有以下几方面:
⑴:
程序数据设置错误(速度、吸嘴选择、器件厚度)。
⑵:
贴装吸嘴吸着气压过低,在取下(A位)及贴装(E位)应在400MMHG以上。
⑶:
吹气时序与贴装头下降时序不匹配(不同步,一般当吸嘴下降至距PCB表面
0.2-0.3mm高度时吸嘴应吸气转换为吹气,吹气时间太早,导致吸嘴未下降到
位就已由吸件转换为吹气)。
⑷:
姿态检测供感器不良(脏),基准设置错误。
⑸:
反光板、光学识别摄像机的清洁与维护。
D:
取件不正常:
主要指从元件供料器上不能正常取走元器件,吸着率低下。
其产生的主要原因有以下几方面。
⑴:
编带规格与供料器规格不匹配(元件的外形尺寸与编带不匹配)。
⑵:
真空泵没工作和或吸嘴吸着气压过低太低(CHIP最低400mmHg、IC最低700mmHg)
⑶:
在取件位置编带的塑料热压带没剥离,塑料热压带未正常拉起。
⑷:
吸嘴竖直运动系统运行迟缓。
⑸:
贴装头的贴装速度选择错误。
⑹:
供料器安装不牢固,供料器顶针运动不畅、快速开闭器及压带不良。
⑺:
切纸刀不能正常切断编带。
⑻:
编带不能随齿轮正常转动或供料器运转不连续(驱动不顺畅)。
⑼:
吸片位置时吸嘴不在低点,下降高度不到位或无动作(止动气缸磨损或缸体内
太脏,其动作是否良好)。
⑽:
在取件位吸嘴中心轴丝与供料器中心轴线不重合,出现偏离。
⑾:
吸嘴下降时间与吸片时间不同步(电磁闸未动作)。
⑿:
供料部有振动。
⒀:
元件厚度数据设置不正确(规格尺寸、大小、高度)。
⒁:
吸片高度的初始值设置有误。
E:
随机性不贴片(漏贴):
主要是指吸嘴在贴片位置低点时不贴装元件(出现漏贴)。
其产生的主要原因
有以几方面。
⑴:
PCB板翘曲度超出设备允许范围攻,上翘最大1.2mm,下曲最大0.5mm。
⑵:
支撑销高度不致或工作台支撑平台平面度不良(倾斜)。
⑶:
吸嘴端部粘有胶液或吸嘴被严重磁化。
⑷:
吸嘴竖直运动系统运行迟缓。
⑸:
吹气时序与贴装头下降时序不匹配(一般当吸嘴下降至距PCB表面0.2-0.3mm
高度时吸嘴应吸气转换为吹气)。
⑹:
印制板上的胶量不足、漏点或机插引脚太长。
⑺:
吸嘴贴装高度设置不良。
⑻:
电磁阀切换不良,吹气压力太小。
⑼:
某吸嘴NG而被子屏蔽后,其余吸嘴在器件贴装时STOPPER气缸动作不畅,未
及时复位。
F:
取件姿态不良:
主要指出现立片,斜片等情况。
其产生的订原因有以下几方面:
⑴:
真空吸着气压调节不良(标准400mmHg)。
⑵:
吸嘴竖直运动系统运行迟缓。
⑶:
吸嘴下降时间与吸片时间不同步。
⑷:
吸片高度或元件厚度的初始值设置有误,吸嘴在低点时与供料部平台的距离不
正确。
⑸:
编带包装规格不良,元件在安装带内晃动。
⑹:
供料器顶针动作不畅、快速开闭器及压带不良。
⑺:
供料器中心轴线与吸嘴垂直中心轴线不重合,偏移太大。
7.10“竖碑”现象的成因与对策
在表面贴装工艺的回流焊接工序中,贴片元件会产生因翘立顼脱焊的缺陷,如图1,人们形象地称之为“竖碑”现象(也有人称之为“曼哈顿”现象)。
它和浮起、移位一起被认为是回流焊接工艺中最常见的缺陷。
“竖碑”现象常发生在Chip元件(如贴片电容和贴片电阻)的回流焊接过程中,元件体积越小越容易发生。
特别是在1005(1mm×0.5mm)或更小的0603(0.6mm×0.3mm)贴片元件的生产中,很难消除“竖碑”现象。
“竖碑”现象的产生原因是,元件两端焊盘上的锡膏在回流溶化时,对元件两个焊接端的表面张力不平衡。
典型的情况如图2,元件两端焊盘上的锡膏不同时溶化,先溶化的一端会产生一个表面张力r,相对于A点,有一个拉动力矩M,M=h×r=hrSina,同时,元件本身的重力相对于A点也有一个重力矩MC,Mc=f×LGA=mg×0.51mgl.当M>Mc时,元件会被拉起,产生“竖碑”现象。
根据以上对“竖碑”现象的成因分析,我们可以找出以下6种主要原因:
7.10.1加热不均匀
回流焊内温度分布不均匀。
板面温度分布不均匀。
7.10.2元件的问题
焊接端的外形和尺寸差异大。
焊接端的可焊性差异大。
元件的重量太轻。
7.10.3基板的材料和厚度
基板材料的导热性差。
基板的厚度均匀性差状和可焊性
7.10.4焊盘的形状和可焊性
焊盘的热容量差异较大。
焊盘的可焊性差异较大。
7.10.5锡膏
锡膏中助焊剂的均匀性差或活性差。
两个焊盘上的锡膏厚度差异较大。
锡膏太厚。
印刷精度差,错位严重。
7.10.6预热温度
预热温度太低。
7.10.7贴装精度
贴装精度差,元件偏移严重。
焊接方法
发生率
GRM39(1.6×0.8×0.8mm)
GRM40(2.0×1.25×0.7mm)
IR
0.1%
0
VPS
6.6%
2.0%
试验条件:
玻璃环氧基板,Stencil厚度200mm,锡膏为Sn63/Pb37.
“竖碑”现象是以上各种因素混合作用的结果,下面对以上这些主要因素做简单分析。
预热期表1是IR(红外线加热)和VPS(气相加热)回流焊中“竖碑”现象的试验统计结果。
在试验中采用了1608(1.6mm×0.8mm)和2125(2.0mm×1.25mm)贴片电容,试验设备是IR热风回流焊炉和无预热的VPS回流炉.从表1中可以明显看出,“竖碑”现象的发生率,后者远大于前者。
这是因为VPS炉没有预热区,使升温速度很快,结果,元件两端锡膏不同时溶化的概率大大增加。
所以预热温度和时间相当重要,我们分别对预热时间1-3分钟、预热温度130-160ºC条件下的回流焊接作了试验统计,结果如图3。
可以很明显地看出,预热温度越高、预热时间越长,“竖碑”现象的发生率就越低。
焊盘尺寸图4显示了焊盘尺寸与“竖碑”现象发生率关系的试验结果。
很明显,当b和c减小时,“竖碑”现象的发生率降低。
但是当C〈0.7mm时,随着c的减少,“元件移位”缺陷的发生率明显上升。
锡膏厚度表2显示了Strncial(印刷钢模)厚度为200mm和100mm时,“竖碑”现象的发生率。
可从表2中看出,Stencial的厚度为200mm时,“竖碑”现象的发生率远远大于Stencial的厚度为100mm时情况。
这是因为
(1)、减小钢模厚度,就是减小了锡膏的涂布量,锡膏熔化时的表面张力随之减小。
(2)、减小钢模厚度,使锡膏较薄,整个焊盘的热容量减小,两个焊盘上锡膏同时溶化的概率大大增加。
贴装精度一般情况下,贴装时产生的元件偏移,在回流过程中,由于锡膏熔化时的表面张力,拉动元件而自动纠正,我们称之为“自适应”,但偏移严重时,拉动反而会使元件立起,产生“竖碑”现象。
这是因为:
(1)从元件焊接端向锡膏传递的热量不平均,如图5,元件右端的锡膏从元件得到的热量会更多,从而先溶化。
(2)元件两端与锡膏的粘力不平
预热期我们进行试验的预热最高温度是170,比正常生产时的预热温度要稍高一点,发现预热温度从140上升到170时,“竖碑”现象的发生率大大降低。
这是因为,预热温度越高,进回流炉后,元件两端的温差越小,两端焊锡膏溶化时间越接近。
但是,锡膏在较高的预热温度下越久,其助焊剂的劣化就越严重,助焊性越差,越容易产生焊接缺陷。
焊盘尺寸试验中发现焊盘间距b从2.8mm减小到2.0mm,“竖碑”现象的发生率降低了9成,仅为原来的十分之一。
这是因为焊盘尺寸减小后,锡膏的涂布量相应减少,锡膏溶化时的表面张力也跟着减小。
所以,设计中,在保证焊接点强度的前提下,焊盘尺寸应尽可能小。
基板材料试验采用了3种不同材料的基板,发生率最高,其次是玻璃环氧板,矾士陶瓷板最低。
这是因为,不同材料的导热系数和热容量不同。
在实际生产中,不可能采用单一品种材料的基板,所以应找出每一种材料基板的最佳预热温度和时间,保证焊接缺陷最低。
锡膏试验采用了3种不同厂家生产的锡膏,由于锡膏中助焊剂成分、活性和金属含量不同,“竖碑”现象的发生率出不尽相同。
元件重量试验采用了两种不同重量的元件,结果显示,“竖碑”现象的发生率有微小的差异,重量较小的元件,缺陷发生率较高。
当然,还有其它很多影响因素,如贴装严重偏移、锡膏涂布量明显不对称等,但占整个发生率的比重较小。
我们对试验结果作了统计分析,画出了如图7的分布图。
可以看出,在总共5个影响因素中,预热期和焊盘尺寸两项占了总缺陷发生率的72%,是两个最关键因素。
随着贴装密度的不断提高,体积更小的1005和0603元件越来越多地被使用。
经过大量试验证明,以上这些分析结论,在1005和0603元件的生产中,是同样适用的。
只不过,由于贴装偏移造成“竖碑”现象占整个缺陷发生率的比例大大提高,变成关键因素。
3.6焊膏漏印生产过程控制
焊膏漏印是一项十分复杂的工艺,既受材料的影响,同时又跟设备和参数有直接关系,通过对漏印中各个细小环节的控制,可以防止在漏印中经常出现的缺陷。
下面将简要介绍漏印时产生的几种最常见的缺陷及相应的防止或解决办法。
8.3.6.1印刷不完全
印刷不完全是指焊盘上部分地方没印上焊膏。
产生的原因可能是:
A.窗孔阻塞或部分焊膏粘在模板底部。
B.焊膏粘度太小。
C.焊膏中有较大尺寸的金属粉末颗粒。
D.刮刀磨损。
防止或解决办法:
清洗窗孔和模板底部,选择粘度全适的焊膏,并使焊膏印刷能有效地覆盖整个印刷区域,选择金属粉末颗粒尺寸与窗孔尺寸相对应的焊膏,检查或更换刮刀。
8.3.6.2拉尖
拉尖是指漏印后焊盘上的焊膏呈小山峰状,产生的原因可能是刮动间障或焊膏粘度太适当调小刮动间障或选择合适粘度的焊膏。
8.3.6.3坍塌
印刷后,焊膏往焊盘两边塌陷。
产生的原因可能是:
A.刮刀压力太大。
B.印制板定位不牢。
C.焊膏粘度或金属百分含量太低。
防止或解决办法。
调整压力,重新固定印制板,选择合适粘度的焊膏。
8.3.6.4焊膏太薄
产生的原因可能是:
(1)模板厚度不符合要求(太薄)。
(2)刮刀压力太小。
(3)焊膏流动性差
防止或解决方法:
选择厚度合适的模板,选择颗粒度和粘度合适的焊膏。
提高刮刀压力。
8.3.6.5厚度不一致
印刷后,焊盘上焊膏厚度不一