熔喷布生产中的制备工艺参数与问题和解决办法.docx
《熔喷布生产中的制备工艺参数与问题和解决办法.docx》由会员分享,可在线阅读,更多相关《熔喷布生产中的制备工艺参数与问题和解决办法.docx(9页珍藏版)》请在冰豆网上搜索。
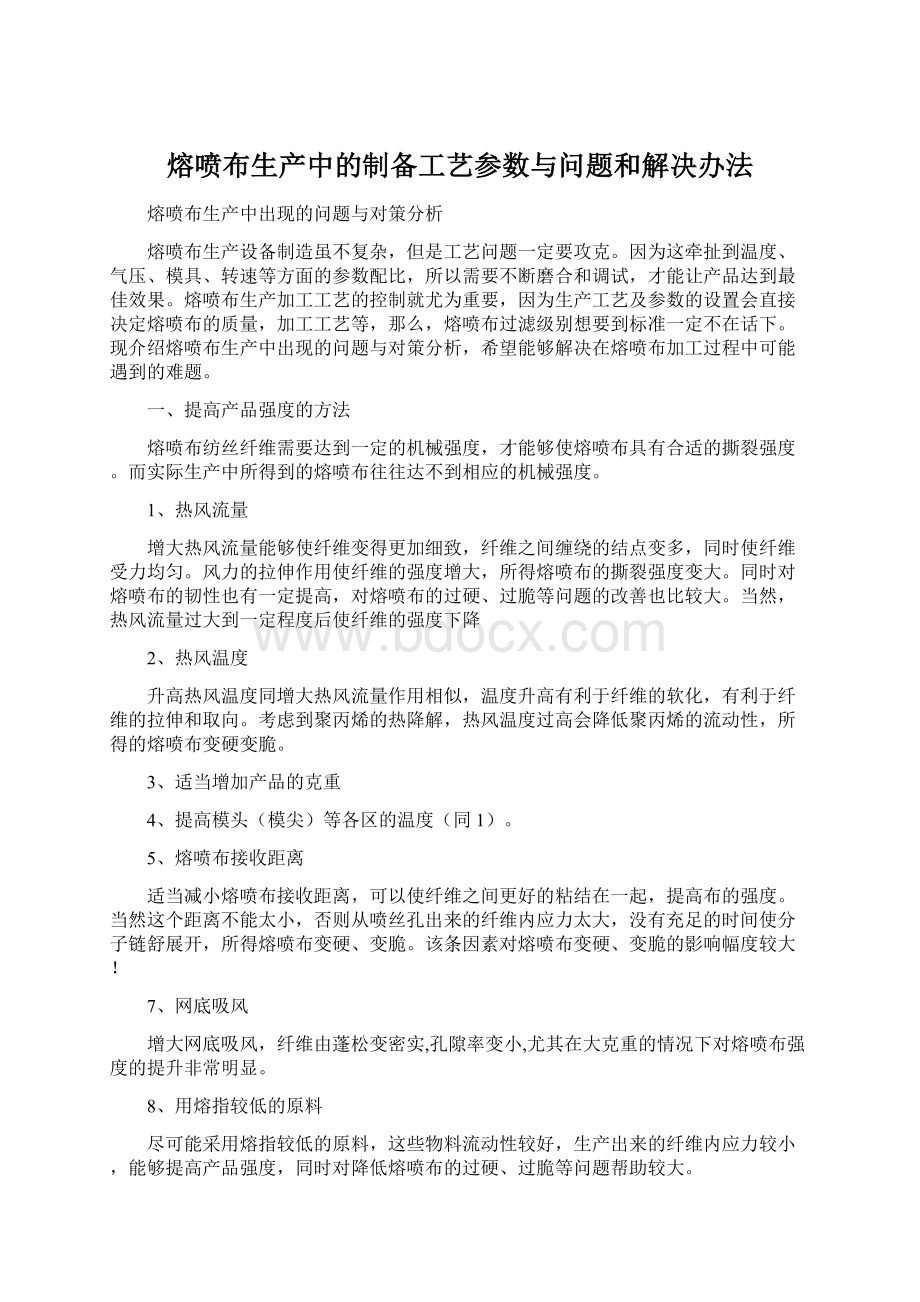
熔喷布生产中的制备工艺参数与问题和解决办法
熔喷布生产中出现的问题与对策分析
熔喷布生产设备制造虽不复杂,但是工艺问题一定要攻克。
因为这牵扯到温度、气压、模具、转速等方面的参数配比,所以需要不断磨合和调试,才能让产品达到最佳效果。
熔喷布生产加工工艺的控制就尤为重要,因为生产工艺及参数的设置会直接决定熔喷布的质量,加工工艺等,那么,熔喷布过滤级别想要到标准一定不在话下。
现介绍熔喷布生产中出现的问题与对策分析,希望能够解决在熔喷布加工过程中可能遇到的难题。
一、提高产品强度的方法
熔喷布纺丝纤维需要达到一定的机械强度,才能够使熔喷布具有合适的撕裂强度。
而实际生产中所得到的熔喷布往往达不到相应的机械强度。
1、热风流量
增大热风流量能够使纤维变得更加细致,纤维之间缠绕的结点变多,同时使纤维受力均匀。
风力的拉伸作用使纤维的强度增大,所得熔喷布的撕裂强度变大。
同时对熔喷布的韧性也有一定提高,对熔喷布的过硬、过脆等问题的改善也比较大。
当然,热风流量过大到一定程度后使纤维的强度下降
2、热风温度
升高热风温度同增大热风流量作用相似,温度升高有利于纤维的软化,有利于纤维的拉伸和取向。
考虑到聚丙烯的热降解,热风温度过高会降低聚丙烯的流动性,所得的熔喷布变硬变脆。
3、适当增加产品的克重
4、提高模头(模尖)等各区的温度(同1)。
5、熔喷布接收距离
适当减小熔喷布接收距离,可以使纤维之间更好的粘结在一起,提高布的强度。
当然这个距离不能太小,否则从喷丝孔出来的纤维内应力太大,没有充足的时间使分子链舒展开,所得熔喷布变硬、变脆。
该条因素对熔喷布变硬、变脆的影响幅度较大!
7、网底吸风
增大网底吸风,纤维由蓬松变密实,孔隙率变小,尤其在大克重的情况下对熔喷布强度的提升非常明显。
8、用熔指较低的原料
尽可能采用熔指较低的原料,这些物料流动性较好,生产出来的纤维内应力较小,能够提高产品强度,同时对降低熔喷布的过硬、过脆等问题帮助较大。
二、提高产品伸长率的方法
1、适当降低热风流量或温度,使纤维的取向度降低,从而使熔喷布中纤维之间形成的结点在拉伸过程中的滑移路径变大。
但是降低幅度过大反而使熔喷布的手感变硬。
2、降低模头(模尖)的工作温度(同上)。
3、适当减小产量,使熔喷布的厚度降低,提高布的伸长率。
4、增大熔喷布接收距离,降低熔喷布的脆性,提高伸长率。
5、降低环境温度(纺丝环境温度)。
6、增大网底吸风(效果不太明显,大克重较好)。
7、改变纤维角度(改变纤维铺网的结构,不常用)
8、适当提高产量(此方法会造成其它物理指标的降低,不常用)。
三、喷丝堵模口的原因
喷丝堵模口是熔喷产线最常见的问题之一,喷丝堵模口的原因有如下几点:
1、材料灰分大,有杂质
2、喷丝孔不够光滑
3、材料不稳定
4、没有加过滤器
5、料桶没有清理干净
评测熔喷料不能光看熔融指数(只代表一个点的数据)和灰分,其实很重要的是看压力升(流变),这个进口熔喷线都有机头压力在线实时显示,需要观测压力波动曲线,判断原料熔融指数稳定性和杂质控制水平。
熔压的在线检测和实时显示很重要。
波动控制在允许范围内才会有均匀而柔软的优质布料。
四、熔喷PP无纺布拆模头后出风不均匀,产品变硬的原因
出风不均匀原因:
左边和右边分刀口,一边宽一边窄,模头不标准,模头质量差,需要校正。
布硬没有强度原因:
风力不够,风道要调好。
喷丝板第一次喷丝基本都不全正,观察哪不正后,调整喷丝板旁边的螺栓再试,开机调不好的话,就要关机把喷丝板拆下来,重新调校后,再安装喷丝。
现在模头为了赶进度,都不热处理,烧了会变形。
让师傅或者找喷丝板厂家或者熔喷线厂家,请教一下重新调校喷丝板。
尽量让厂家出机之前安装过滤器,最好是做双过滤是最保险的。
五、熔喷布当天质感很好,放一两天流到客手里变脆的原因
可能由于喷丝不匀均、冷风机风量不足导致散热不匀均,产生内应力而造成易脆现象。
可以通过调整挤出机挤出熔体量,调整热风机的温度,增大冷风机风量进行改善。
也可以换原材料试试,PP熔喷料现在品质参差不齐。
物料分子量分布不均匀,恢复常温以后,应力导致产品发硬发脆。
同样也不排除自身设备问题,毕竟一个生产过程牵扯“人料物法环”等诸多因素。
选择分子量分布集中的聚丙烯熔喷料,可以降低喷出的熔喷布发脆的风险。
赛诺新材出品熔喷料熔指1500±100,出丝均匀,提高加工稳定性。
低灰分,降低清理模口的频次,减少停开机带来的损耗。
气味低。
六、实际上熔喷布的生产并不复杂,产生的问题无非是温度、气压、模具、材料、转速等因素引起,所以需要不断磨合和调试设备与工艺,才能使产品达到最佳效果。
下面针对熔喷布的七个常见缺陷展开来谈:
1、晶点
产生机理:
a、空气速度太小或熔体粘度太高,部分熔体细丝未完全牵伸。
b、熔体粘度太小,空气速度高时,喷丝孔对熔体的握持作用减弱,熔体还没有被牵伸成纤维便脱离喷丝孔。
解决对策:
a、根据材料的熔指进行升温或降温。
b、调整螺杆转速。
c、选用合适的模头和喷丝孔熔指的材料。
2、飞絮
产生机理:
原料与相应的纺丝温度没有很好地匹配,温度较高所致。
解决对策:
a、若是全宽幅飞絮,可以调整螺杆纺丝温度和热风温度。
b、若是区域性飞絮,可以调整相应区位的模头温度。
3、布脆、硬
产生机理:
熔体未被喷成纤维状或者多个纤维粘成团导致熔喷布脆、硬。
解决对策:
a、调整热气流气压。
b、调整模头温度。
c、减少喂料量。
d、调整滚筒或帘子与喷丝孔的距离。
4、堵孔
产生机理:
一般堵孔主要是因为驻极母粒添加过多、无机组分多、熔喷料有杂质以及未加过滤网造成。
解决对策:
a、减少驻极母粒的添加量。
b、增加过滤网。
c、选用干净的原料。
d、及时更换过滤网。
5、喷丝不均
产生机理:
各喷丝孔的阻力或气流大小不一导致各孔的喷丝量不一样。
解决对策:
a、选用各喷丝孔压力一致的精密模头和喷丝板。
b、及时更换过滤网。
c、定期清洗喷丝板。
d、减少驻极母粒的添加量。
6、气孔
产生机理:
材料水分含量过高,导致在喷丝过程中水气喷溅而产生气孔。
解决对策:
对材料进行烘干处理。
7、过滤效率低
产生机理:
a、喷出的纤维较粗且间隙大。
b、未加驻极母粒或添加不够。
c、未进行电晕处理或处理不够。
解决对策:
a、升高温度。
b、调整布的接收距离。
c、减少喂料量。
d、加大气压。
f、加大驻极母粒含量。
e、电晕处理。
如果大家通过正规渠道买到严格符合标准的熔喷布原料,那么,熔喷布生产加工工艺的控制就尤为重要,因为生产工艺及参数的设置会直接决定熔喷布的质量,加工工艺不出问题,那么,熔喷布过滤级别想要到标准一定不在话下。
一、提高产品强力的方法
1、增大热风流量(纤维细,缠绕的结点多,纤维受力均匀,强力增大,但是增大到一定程度后反而会下降)。
2、升高热风温度(同上)。
3、适当增加产品的克重(在内控范围内)。
4、提高模头(模尖)等各区的温度(同a)。
5、适当降低产量。
6、适当减小熔喷布接收距离(不能太小,反而布脆强力会下降,结合其它参数共同运用)。
7、增大网底吸风(大克重较明显)。
8、用熔指较低的原料。
二、提高产品伸长率的方法
1、适当降低热风流量或温度(结点滑移路径变大,手感变硬)。
2、降低模头(模尖)的工作温度(同上)。
3、适当减小产量。
4、增大熔喷布接收距离(和a或b配合使用效果更明显)。
5、降低环境温度(纺丝环境温度)。
6、增大网底吸风(效果不太明显,大克重较好)。
7、改变纤维角6度(改变纤维铺网的结构,不常用)
8、适当提高产量(此方法会造成其它物理指标的降低,不常用)。
三、减小阻力的方法
1、降低热风流量或温度(纤维变粗,孔隙率大,阻力小,效率变差)。
2、增大熔喷布接收距离(增加纤维的蓬松性,孔隙率大,效率变差)。
3、降低纺丝环境温度(纤维冷却充分,结构蓬松,孔隙率增大,配合热空气可以达到降低阻力,提高效率的目的)。
4、减小网底吸风(纤维由密变蓬松,孔隙率变大,大克重较明显)。
5、降低模头(模尖)等加热区的工作温度(纤维变粗,孔隙率变大)。
6、增大计量泵(挤出量变大纤维变粗,孔隙率增大,一般在快速转单时使用)。
7、适当减小克重(在内控范围内)。
四、提高过滤效率的方法
1、增大热风流量或温度(增加纤维的细度,减小孔隙率,提高扑捉能力,但阻力增加)。
2、增大静电电压(电流)(极化纤维,增大纤维的静电场能,提高其吸附能力)。
3、在原料中加入粉料或其它驻极体(提高纤维的受电能力和储电时间,让纤维携带更多的电荷和带电荷时间)。
4、加大网底吸风(增大纤维的密实程度,提高纤维的扑捉能力。
大克重明显,不常用)。
5、适当降低产量(同工艺下,挤出量变小,纤维变细,阻力增大)。
6、提高模头(模尖)等区的工作温度(熔体流动性变好,纤维变细)。
7、提高纺丝环境温度(纤维变细,一般是在室温升高的情况下,阻力增加较明显,其它物理指标下降)。
8、适当增大粉料的添加量。
五、既能减小阻力,又能提高效率的方法
1、增大熔喷布接收距离的同时,适当增加热风流量或温度,减小网底吸风(增加纤维的细度和蓬松度)。
2、提高纤维细度同时降低纺丝环境温度(比如加冷风装置)。
3、提高纤维的蓬松度同时,加大静电电压(电流),适当增大粉末的添加量。
4、提高纤维的细度,适当减小克重(不常用)。
六、既能提高强力,又能提高伸长率的方法
1、适当降低热风流量或温度,减小熔喷布接收距离,适当增大网底吸风(用于环境温度过高、原料熔指过高造成的物理指标不合格)。
2、适当增大热风流量或温度,增大熔喷布接收距离,适当减小网底吸风(用于环境温度过低、原料熔指过低造成的物理指标不合格)。
3、减小产量。
4、增加纤维细度同时降低纺丝环境温度。
七、减小产品CV值的方法
1、对应改变模头各区的工作温度(克重小升温,反之降温)。
2、当局部效率、阻力与CV值矛盾时可以采用在其位置加上挡板(提高局部纺丝环境温度)。
3、纵向克重的CV值主要与成网系统速度的稳定性有关。
八、出现“Shot”团块状聚合物原因
1、工作温度设定不当(过高或过低,一般过高容易出现)。
2、原料或母粒太脏(一般布面整体,或大面积出现)。
3、模头使用后期,模尖脏(有时是局部出丝不良或大面积出现,可以采用刮刀刮模尖解决)。
4、模尖周围有碳化物质或脏堵造成出丝不良(通常是异常停机造成的。
一般是局部少量出现,可以采用刮刀刮模尖解决)。
5、风刀局部脏或风刀有物理损伤(影响正常纺丝气流的均匀性,局部出现并伴有纵向的薄沟出现)。
6、产量过高或过低(一般为大面积出现,降低或提高产量解决)。
7、原料熔指过高或过低(通常过高易出现)。
8、原料中有水。
九、出现“飞花”的原因
1、热风流量过大或温度过高(断纤维太多)。
2、各区工作温度过高(断纤维太多)。
3、熔喷布接收距离太小(布太密实,影响吸风效率)。
4、纺丝环境温度太高(同a)。
5、在加回收料时,回收量过大,回收料熔指不定。
6、产量太低。
7、网底吸风参数设定不当或网帘太脏(吸风小,纤维不能被充分吸附在网帘上,脱离网帘)。
8、原料熔指太高。
十、30g熔喷制备工艺参数表
综上所述的各种方法,在实际应用过程中需根据生产实际情况,本着工艺优化的原则进行筛选使用。
在工艺调节过程中的每一个工艺参数和每一种方法都不是孤立的,它们是相辅相成,相互制约的。
若想实现一个物理指标的提高而不影响其它指标,需要多种方法共同作用才能达到目的。
至于产品的指标提高的幅度,主要根据自己平时的工作经验选择最优的方法和参数组合来实现。
虽然有多种组合方式都可以完成一种产品,但是一个优秀的工艺参数组合可以实现产品各个物理指标的同时提升。
只有达到这个目的的工艺,才是一个完美的工艺!
同时也是衡量一名工艺合格与否的标准。
所以,我们在今后的工作中,应本着提高产品质量,降低能耗,降低成本的目的去调整。