生产线平衡分析与改善.docx
《生产线平衡分析与改善.docx》由会员分享,可在线阅读,更多相关《生产线平衡分析与改善.docx(12页珍藏版)》请在冰豆网上搜索。
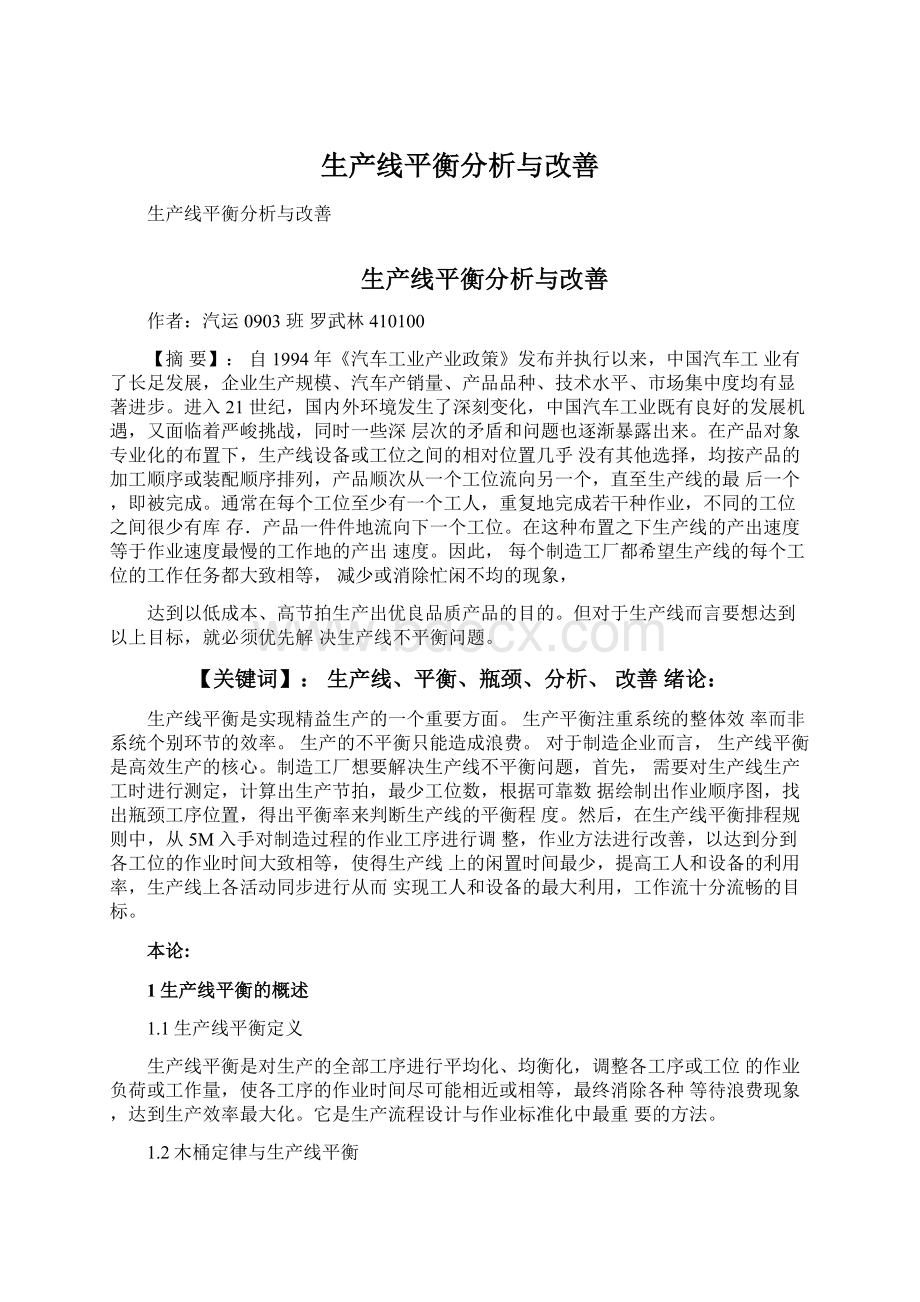
生产线平衡分析与改善
生产线平衡分析与改善
生产线平衡分析与改善
作者:
汽运0903班罗武林410100
【摘要】:
自1994年《汽车工业产业政策》发布并执行以来,中国汽车工业有了长足发展,企业生产规模、汽车产销量、产品品种、技术水平、市场集中度均有显著进步。
进入21世纪,国内外环境发生了深刻变化,中国汽车工业既有良好的发展机遇,又面临着严峻挑战,同时一些深层次的矛盾和问题也逐渐暴露出来。
在产品对象专业化的布置下,生产线设备或工位之间的相对位置几乎没有其他选择,均按产品的加工顺序或装配顺序排列,产品顺次从一个工位流向另一个,直至生产线的最后一个,即被完成。
通常在每个工位至少有一个工人,重复地完成若干种作业,不同的工位之间很少有库存.产品一件件地流向下一个工位。
在这种布置之下生产线的产出速度等于作业速度最慢的工作地的产出速度。
因此,每个制造工厂都希望生产线的每个工位的工作任务都大致相等,减少或消除忙闲不均的现象,
达到以低成本、高节拍生产出优良品质产品的目的。
但对于生产线而言要想达到以上目标,就必须优先解决生产线不平衡问题。
【关键词】:
生产线、平衡、瓶颈、分析、改善绪论:
生产线平衡是实现精益生产的一个重要方面。
生产平衡注重系统的整体效率而非系统个别环节的效率。
生产的不平衡只能造成浪费。
对于制造企业而言,生产线平衡是高效生产的核心。
制造工厂想要解决生产线不平衡问题,首先,需要对生产线生产工时进行测定,计算出生产节拍,最少工位数,根据可靠数据绘制出作业顺序图,找出瓶颈工序位置,得出平衡率来判断生产线的平衡程度。
然后,在生产线平衡排程规则中,从5M入手对制造过程的作业工序进行调整,作业方法进行改善,以达到分到各工位的作业时间大致相等,使得生产线上的闲置时间最少,提高工人和设备的利用率,生产线上各活动同步进行从而实现工人和设备的最大利用,工作流十分流畅的目标。
本论:
1生产线平衡的概述
1.1生产线平衡定义
生产线平衡是对生产的全部工序进行平均化、均衡化,调整各工序或工位的作业负荷或工作量,使各工序的作业时间尽可能相近或相等,最终消除各种等待浪费现象,达到生产效率最大化。
它是生产流程设计与作业标准化中最重要的方法。
1.2木桶定律与生产线平衡
1.2.1木桶定律
一个木桶盛水多少,并不取决于桶壁上最高的那块木板,而恰恰取决于桶壁上最短的那块木板,这一规律我们称之为“木桶定律”。
1.2.2木桶定律的三个推论
A.只有桶壁上所有木板都足够高,木桶才能盛满水
B.所有木板高出最低木板的部分是没有意义的,而且高出越多,浪费就越大
C.提高木桶容量最有效的办法就是设法加高最低木板的高度
1.2.3生产线平衡与木桶定律的关系
“生产线平衡”与“木桶定律”非常相似:
生产线的最大产能不是取决于作业速度最快的工位,而恰恰取决于作业速度最慢的工位,最快与最慢的差距越大,产能损失就越大。
制造现场,各个车间或小组之间,彼此的管理水平、产能等往往是不等的,企业现场管理的整体水平并不取决于最优秀的车间单位
而是取决于最差的车间单位,同理,对一条生产线来言,其产量、效率高低也是如此。
1.3生产线不平衡的影响与瓶颈工序
图1.1
项目
工位1
工位2
工位3
工位4
能力
100件/H
125件/H
80件/H
100件/H
达成率
100%
125%
80%
80%
效率
个别效率合格
个别效率
高
个别效率
低
个别效率
低
表1
1.3.2瓶颈工序
1.321瓶颈的定义:
阻碍企业流程更大程度增加有效产出或减少库存和费用的环节谓之瓶颈,瓶颈可能是有形的,也可能是无形的。
1.3.2.2瓶颈效应:
是指瓶子颈部流量的大小限制了倒水时的水流
工序辿度r恆坝"示庖国
A_Lrr日工序c_crru丄rru工咛■
图1.2
生产系统的目标是平衡生产能力同时平衡物流,非瓶颈”资源的充分利用
不仅不能提高有效产出,而且还会使库存和搬运增加;瓶颈环节损失1小时,相
当于整个系统损失1小时,而且是无法补救的;非瓶颈环节上节约1小时,毫无实际意义;瓶颈制约了生产系统的有效产出和库存。
图1.3
1.3瓶颈的不良影响
工序的先后关系,会影响后续工序进度:
一些工序的半成品堆积过多(如B),而另一些则很少(如DE);整体进度缓慢,生产效率下降(瓶颈工序C未完成作业影响DE的进度)
先后关系;影响后续进度
工序间的平行关系,贝U会影响产品配套:
出现产品零部件不能配套的现象;
一些工序加班赶货,而另一些则很轻松;个别工序在等材料、设备,其他工序进
展正常;个别生产线流动停止,出现在制品滞留时间过长情况。
1.4提高生产线平衡效率的意义
提高生产线平衡效率的意义在于缩短每一制品装配时间,增加单位时间的
生产量;降低生产成本减少工序间的在制品;减少现场场地的占用减少工程之
间的预备时间,缩短生产周期;消除人员等待现象,提升员工士气;改变传统小批量作业模式,使其达到一个流生产;可以稳定和提升产品品质;提升整体生产线效率和降低生产现场的各种浪费。
2生产线平衡的分析
2.1平衡分析用语
节拍:
节拍是指在规定时间内完成预定产量,各工序完成单位成品所需的作业时间。
其计算公式:
节拍二有效出勤时间/[生产计划量X(1+不良率)](式1)
例:
每月的工作天数为20天,正常工作时间每班次为480分钟,该企业实行每天2班制,如果该企业的月生产计划量为19200个,不良率为0%请问该企业的生产节拍是多少?
答:
节拍时间=有效出勤时间/[生产计划量X(1+不良率)]=480X2X20/[19200X(1+0%]=60秒/个
2.瓶颈工时:
指生产线所有工序中所用人均工时最长的工序,通常指一道工序,有时也指几道工序。
3.平衡率:
计算公式=生产线各工序时间总和/(瓶颈工时*人员数),一般制造生产线的效率不应低于0.75,以手工为主装配线应在0.85~0.9以上
2.2生产线平衡分析原则与步骤
2.2.1分析原则
(1)――5W1HI则
项目
问题
为什么?
改善方向
Why
目的是什么?
为什么?
去除不必要及目的不明确的工作。
Where
在什么地方?
为什么?
有无其他更合适的位置和布局?
When
什么时候做此事?
为什么?
有无其他更合适的的时间与顺序?
Who
有谁来做?
为什么?
有无其他更合适的人?
What
做什么?
为什么?
可否简化作业内容?
How
如何做?
为什么?
有无其他更好的方法?
表2.1
2.3分析的步骤
2.3.1秒表法工时分析步骤:
1明确分析目的,确定观测工序;
2选定合适的操作者(被观测者);
3观测准备(秒表、板、表格、用具等);
4记录必要事项;
5把作业分解成单元作业并记录在表格上;
6确定观测次数;
循环周期
<0.10
<0.10
<0.5
<0.7
<1.0
<2.0
(分)
(6S)
(6s)
(30s)
(45s)
(60s)
(120s)
观察次(次)
100
60
40
20
20
10
表2.2
7实施观测;
站在易观察作业内容的位置上不打扰作业者;合适的观察方向和距离;一般在作业者斜后方或前方2m左右最适宜眼、秒表和作业位置在一条直线上交替观察秒表和操作
8观测完毕即时整理观测结果
算出每次测量的单元作业的纯工时(纯作业时间);算出单元作业纯工时的平均值;算出每次测量的一个循环需要的时间
异常值判断基准:
一般把偏离相邻值、小于25%或大于30鸠上的纯工时值
判定为异常值(红色字体为异常值)。
589991011
121219
9研究观测结果,制定改进方案。
2.3.2计算装配线上需要的理论上的最小工序数
最小工序数ti/CT(刀ti=各作业时间之和)
假设节拍是1.0分钟,各作业时间之和是2.5分钟,那么为最少所需要的
工序数为:
NU=[2.5/1.0]=3(个)
2.3.3结合工时测定表绘制作业顺序图找出瓶颈
作业工序
作业时间(分)
前项作业工序
A
10
一
B
11
A
C
5
B
D
4
B
E
12
A
F
3
C,D
G
7
F
H
11
E
I
3
G,H
总时间
66
瓶颈图2.1
表2.3
234通过平衡率判断生产线平衡情况
结合表2.3和图2.1计算出该生产线平衡率=生产线各工序时间总和/(瓶颈工时*人员数)=66/[(11+12)*9]=0.32;根据平衡法则:
一般制造生产线的效率
不应低于0.75,以手工为主装配线应在0.85〜0.9以上,可得出该生产线不
平衡。
3生产线平衡改善的方法与原则
3.1平衡改善的排程规则
主规则:
以其后跟随任务数目最多的秩序安排工位。
附加规则:
最长作业
时间的任务先排
3.2作业工位内容分配条件
作业工位内容分配条件:
保证各工序之间的先后顺序;每个工作地分配到的基本作业时间之和,不能大于节拍;各工位的作业时间之和应尽量相等或接近节拍;应使工位数目尽量少。
3.3启发式分配作业的排程规则排程规则:
作业分配按作业先后顺序图由左到右进行
1确定当前有资格被分配的作业(约束)
(a)该作业的所有先行作业都已被分配
(b)该作业时间不超过该工位的剩余时间(剩余时间:
等于节拍减去工位上总的作业时间)
2如果没有有资格被分配的作业,转向下个工作地的分配
3如果出现两个或两个以上有资格被分配的作业,可采用不同的规则加以选择,如:
(a)先分配后续作业最多的作业
(b)先分配加工时间最长的作业
(c)先分配位置权数最大的作业
(d)任意选择其中的一个作业先分配
3.4消除瓶颈
1)作业分割——将此作业的一部分分割出来移至工时较短的作业工序。
2)利用或改良工具、机器一一将手工改为工具;或半自动或全自动机器;或在原有工具;夹具做改善;自可提升产量,缩短作业工时。
3)提高作业者的技能——运用工作教导,提升作业者的技能
4)调换作业者——调换效率较高或熟练作业人
5)增加作业者——上面几项都做了,还未达到理想,可能就得考虑增加工序人手了。
3.55M方法减少耗时最长工序作业时间
5M人员,机器设备,物料,作业方法,环境
人员(Man):
调换作业者;增加作业者;多能工训练;新手避免工作负荷过重,利用作业员熟练程度的差异性,平衡作业流程.
机器设备(Machine):
利用或改良工具、机器;人机比合理配置;人机同步作业;提高自动半自动化水平;人机工程分析,提高机械效率.
物料(Material):
确保物料供应及时准确;物料摆放合理取用;物料包装合理减少拆卸作业.
作业方法(Method):
避免在同一工站使用太多工具;动作要合理化,尽量减
少辅助动作:
寻找.发现.选择.思考.预定位,取消无效动作:
保持.延迟.放置.休息;遵循动作经济四原则:
减少动作数量.双手同时作业.缩短动作的距离.轻松作业.
作业环境(MotherNature):
保持整洁、清洁的作业环境;有适当的操作安全措施;适当的照明、空调和通风设备;桌椅和静电设备有适当的规格
3.6作业方法的改善
ECRS原则:
取消不必要的动作;合并微小的动作;重排作业工序或动作简化复杂的动作
3.7平衡改善方法图解
图3.3作业分割转移
图3.5拆解去除
业时间
[人作业
I
工序
1
2
3
4
5
作业Ihr同
□
亡
ut
1
3
4
图3.6作业改善后合并图3.7重排
结论:
生产线平衡的核心就是----克服瓶颈!
解除瓶颈生产工序:
这是生产线平衡改善最简单的一招,但也是最厉害的一招,在汽车制造行业有句“名言”是“把简单的招式练到极至就是绝招”。
有一句格言:
“瓶颈工序决定最大产能”。
众所周知,均衡是生产进度的重要保证,在100个环节中,只要存在一个环节
效率低下,那么99个环节的努力都可能解决不了进度落后的问题。
因此,抓住瓶颈工序的生产节拍,不断予以改善,是提升效率最重要的法宝。
生产线平衡改善是多方面的,但在生产线平衡过程中应注意:
A.需要同样工具和机器的作业要素可分配在同一专用设备工序内
B.作业要素相同或前后相近的应尽量分配在同一工序
C.不相容的作业尽量不分在同一工序
D.必要时可对关键作业,增加操作人数或改用更有效的工具/设备以缩短其作业时间,提高平衡率
E.生产线补进新手时,因新手对工作不熟悉,在配置上需特别注意,否则会造成
F.采用ECRSt则进行改善时的优先顺序为:
“取消”不必要的动作或工序(第一选择);“合并”微小动作(次选);“重排”作业工序或动作(第三选择);
“简化”复杂动作或工序(最后选择)
参考文献
[1]徐学军:
现代工业工程,广州:
华南理工大
学出版社,2000
[2]无:
精益生产之线平衡模式,XX文库
[3]无:
IE管理之作业测定与效率管理,XX文库
[4]无:
班组长管理技能提升教程,广汽菲亚特班组长培训资料
致谢
感谢我的导师刘智婷老师,在我的论文撰写过程对我孜孜不倦的指导,她细致、一丝不苟的作风一直是我工作、学习中的榜样;老师循循善诱的教导和不拘一格的思路给予我无尽的启迪;感谢我的室友们,从遥远的家来到这个陌生的城市里,是你们和我共同维系着彼此之间兄弟般的情谊,维系着寝室那份家的融洽。
三年了,仿佛就在昨天。
我们在一起的日子,我会铭记一生。
在论文即将完成之际,我的心情无法平静,从开始进入课题到论文的顺利完成,有多少可敬的师长、同事、同学、朋友给了我无言的帮助,在这里请接受我诚挚的谢意!