《药品生产和质量管理规范附录15》征求意见稿.docx
《《药品生产和质量管理规范附录15》征求意见稿.docx》由会员分享,可在线阅读,更多相关《《药品生产和质量管理规范附录15》征求意见稿.docx(38页珍藏版)》请在冰豆网上搜索。
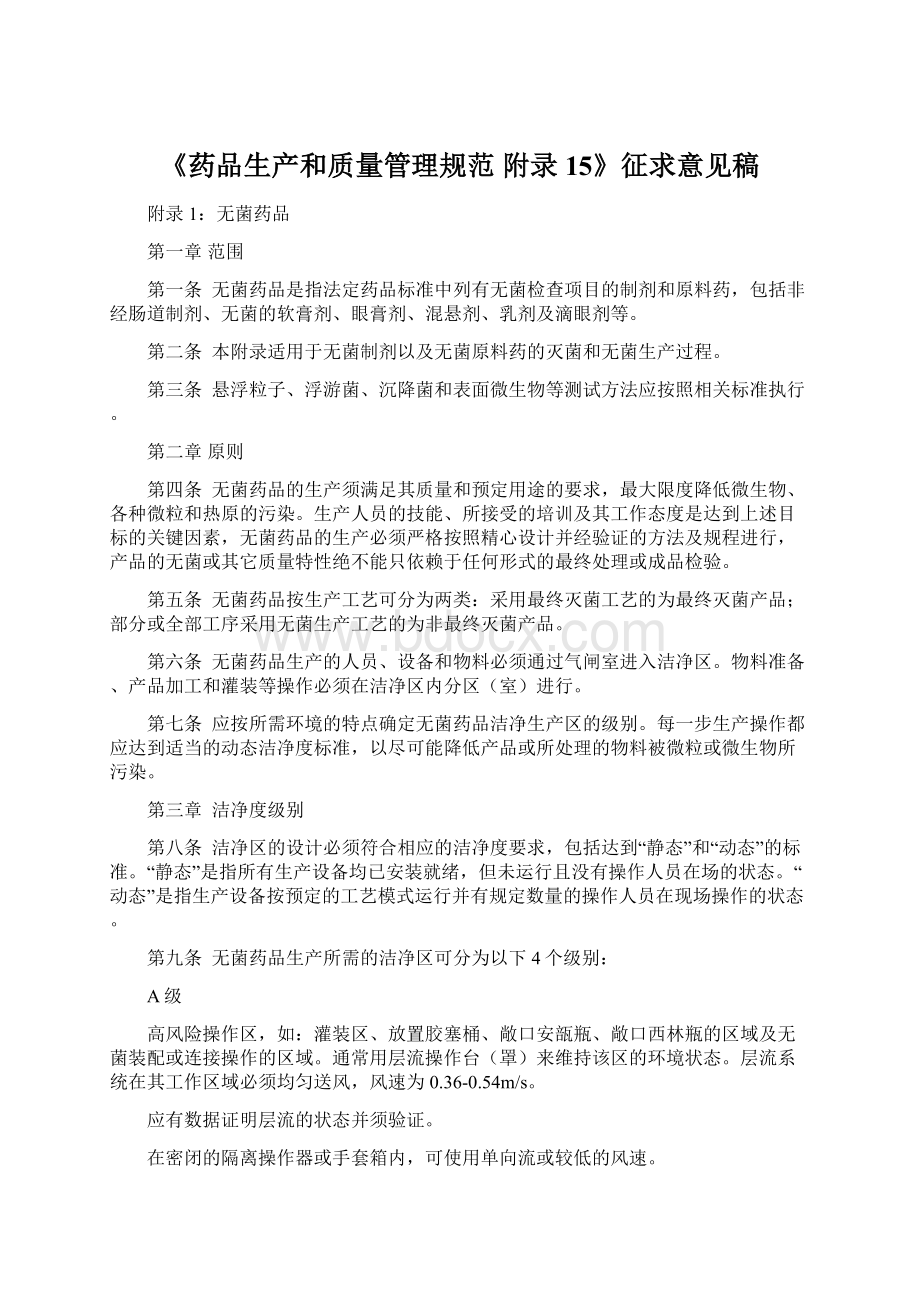
《药品生产和质量管理规范附录15》征求意见稿
附录1:
无菌药品
第一章范围
第一条无菌药品是指法定药品标准中列有无菌检查项目的制剂和原料药,包括非经肠道制剂、无菌的软膏剂、眼膏剂、混悬剂、乳剂及滴眼剂等。
第二条本附录适用于无菌制剂以及无菌原料药的灭菌和无菌生产过程。
第三条悬浮粒子、浮游菌、沉降菌和表面微生物等测试方法应按照相关标准执行。
第二章原则
第四条无菌药品的生产须满足其质量和预定用途的要求,最大限度降低微生物、各种微粒和热原的污染。
生产人员的技能、所接受的培训及其工作态度是达到上述目标的关键因素,无菌药品的生产必须严格按照精心设计并经验证的方法及规程进行,产品的无菌或其它质量特性绝不能只依赖于任何形式的最终处理或成品检验。
第五条无菌药品按生产工艺可分为两类:
采用最终灭菌工艺的为最终灭菌产品;部分或全部工序采用无菌生产工艺的为非最终灭菌产品。
第六条无菌药品生产的人员、设备和物料必须通过气闸室进入洁净区。
物料准备、产品加工和灌装等操作必须在洁净区内分区(室)进行。
第七条应按所需环境的特点确定无菌药品洁净生产区的级别。
每一步生产操作都应达到适当的动态洁净度标准,以尽可能降低产品或所处理的物料被微粒或微生物所污染。
第三章洁净度级别
第八条洁净区的设计必须符合相应的洁净度要求,包括达到“静态”和“动态”的标准。
“静态”是指所有生产设备均已安装就绪,但未运行且没有操作人员在场的状态。
“动态”是指生产设备按预定的工艺模式运行并有规定数量的操作人员在现场操作的状态。
第九条无菌药品生产所需的洁净区可分为以下4个级别:
A级
高风险操作区,如:
灌装区、放置胶塞桶、敞口安瓿瓶、敞口西林瓶的区域及无菌装配或连接操作的区域。
通常用层流操作台(罩)来维持该区的环境状态。
层流系统在其工作区域必须均匀送风,风速为0.36-0.54m/s。
应有数据证明层流的状态并须验证。
在密闭的隔离操作器或手套箱内,可使用单向流或较低的风速。
B级
指无菌配制和灌装等高风险操作A级区所处的背景区域。
C级和D级
指生产无菌药品过程中重要程度较次的洁净操作区。
以上各级别空气悬浮粒子的标准规定如下表:
洁净度级别
悬浮粒子最大允许数/立方米(a)
静态(b)
动态(b)
≥0.5μm(d)
≥5μm
≥0.5μm(d)
≥5μm
A级
3500
1(e)
3500
1(e)
B级(c)
3500
1(e)
350000
2000
C级(c)
350000
2000
3500000
20000
D级(c)
3500000
2,0000
不作规定(f)
不作规定(f)
注:
(a)指根据光散射悬浮粒子测试法,在指定点测得等于和/或大于粒径标准的空气悬浮粒子浓度。
应对A级区“动态”的悬浮粒子进行频繁测定,并建议对B级区“动态”也进行频繁测定。
A级区和B级区空气总的采样量不得少于1米3,C级区也宜达到此标准。
(b)生产操作全部结束,操作人员撤离生产现场并经15~20分钟自净后,洁净区的悬浮粒子应达到表中的“静态”标准。
药品或敞口容器直接暴露环境的悬浮粒子动态测试结果应达到表中A级的标准。
灌装时,产品的粒子或微小液珠会干扰灌装点的测试结果,可允许这种情况下的测试结果并不始终符合标准。
(c)为了达到B、C、D级区的要求,空气换气次数应根据房间的功能、室内的设备和操作人员数决定。
空调净化系统应当配有适当的终端过滤器,如:
A、B和C级区应采用不同过滤效率的高效过滤器(HEPA)。
(d)本附录中“静态”及“动态”条件下悬浮粒子最大允许数基本上对应于ISO14644-10.5μm悬浮粒子的洁净度级别。
(e)这些区域应完全没有大于或等于5μm的悬浮粒子,由于无法从统计意义上证明不存在任何悬浮粒子,因此将标准设成1个/米3,但考虑到电子噪声、光散射及二者并发所致的误报因素,可采用20个/米3的限度标准。
在进行洁净区确认时,应达到规定的标准。
(f)须根据生产操作的性质来决定洁净区的要求和限度。
温度、相对湿度等其它指标取决于产品及生产操作的性质,这些参数不应对规定的洁净度造成不良影响。
第一十条应对A、B、C级洁净区的悬浮粒子进行动态监测。
第一十一条为评估无菌操作区的微生物状况,应对微生物进行动态监测,监测方法有沉降碟法、定量空气采样法和表面取样法(如:
棉签擦拭法和接触碟法)等。
动态取样应避免对洁净区造成不良影响。
成品批记录的审核应同时考虑环境监测的结果,决定是否放行。
对表面和操作人员的监测,应在关键操作完成后进行。
除在生产过程中需进行微生物监控外,系统验证、清洁和消毒等操作完成后,也应进行微生物监控。
洁净区微生物监控的动态标准(a)如下:
级别
浮游菌
cfu/m3
沉降菌(90mm)
cfu/4小时(b)
表面微生物
接触碟(55mm)
cfu/碟
5指手套
cfu/手套
A级
1
1
1
1
B级
10
5
5
5
C级
100
50
25
-
D级
200
100
50
-
注:
(a)表中各数值均为平均值。
(b)可使用多个沉降碟连续进行监控,但单个沉降碟的暴露时间可以少于4小时。
第一十二条应制定适当的悬浮粒子和微生物监控警戒和纠偏限度。
操作规程中应详细说明结果超标时需采取的纠偏措施。
第一十三条无菌药品的生产操作应在符合下表中规定的相应级别的洁净区内进行,未列出的操作可参照下表在适当级别的洁净区内进行:
洁净度级别
最终灭菌产品生产操作示例
C级背景下的局部A级
高污染风险(a)的产品灌装(或灌封)
C级
产品灌装(或灌封)
高污染风险(b)产品的配制和过滤
滴眼剂、眼膏剂、软膏剂、乳剂和混悬剂的配制、灌装(或灌封)
直接接触药品的包装材料和器具最终清洗后的处理
D级
轧盖
灌装前物料的准备
产品配制和过滤(指浓配或采用密闭系统的稀配)
直接接触药品的包装材料和器具的最终清洗
注:
(a)此处的高污染风险是指产品容易长菌、灌装速度很慢、灌装用容器为广口瓶、容器须暴露数秒后方可密闭等状况;
(b)此处的高污染风险是指产品容易长菌、配制后需等待较长时间方可灭菌或不在密闭容器中配制等状况。
洁净度级别
非最终灭菌产品的无菌操作示例
B级背景下的A级
产品灌装(或灌封)、分装、压塞、轧盖
灌装前无法除菌过滤的药液或产品的配制
冻干过程中产品处于未完全密封状态下的转运
直接接触药品的包装材料、器具灭菌后的装配、存放以及处于未完全密封状态下的转运
无菌原料药的粉碎、过筛、混合、分装
B级
冻干过程中产品处于完全密封容器内的转运
直接接触药品的包装材料、器具灭菌后处于完全密封容器内的转运
C级
灌装前可除菌过滤的药液或产品的配制
产品的过滤
D级
直接接触药品的包装材料、器具的最终清洗、装配或包装、灭菌
第四章隔离操作技术
第一十四条采用隔离操作技术能最大限度降低操作人员的影响,并大大降低无菌生产中环境对产品微生物污染的风险。
高污染风险的操作宜在隔离器中完成。
隔离操作器及其所处环境的设计,应能保证相应区域空气的质量达到设定标准。
传输装置可设计成单门或双门、甚至可以是同灭菌设备相连的全密封系统。
物品进出隔离操作器应特别注意防止污染。
隔离操作器所处环境的级别取决于其设计及应用。
无菌操作的隔离操作器所处环境的级别至少应为D级。
第一十五条隔离操作器只有经过适当的验证后方可投入使用。
验证时应当考虑隔离技术的所有关键性因素,如隔离系统内部和外部所处环境的空气质量、隔离操作器的消毒、传递操作以及隔离系统的完整性。
第一十六条隔离操作器和隔离用袖管或手套系统应进行常规监测,包括经常进行必要的检漏试验。
第五章吹灌封技术
第一十七条吹气、灌装、密封(简称吹灌封)系统是一套专用机械设备,可连续操作,从将热塑性材料吹制成容器至灌装和密封,整个过程由一台全自动机器完成。
第一十八条用于生产非最终灭菌产品的吹灌封设备本身应装有A级空气风淋装置,在操作人员按A/B级区要求着装的条件下,该设备可安装在洁净度至少为C级的环境中。
在静态条件下,此环境的悬浮粒子和微生物均应达到标准,在动态条件下,此环境的微生物应达到标准。
用于生产最终灭菌产品的吹灌封设备至少应安装在D级环境中。
第一十九条因吹灌封技术的特殊性,应特别注意设备的设计和验证、在线清洗和在线灭菌的验证及结果的重现性、设备所处的洁净区环境、操作人员的培训和着装,以及设备关键区域内的操作,包括灌装开始前设备的无菌装配。
第六章人员
第二十条无菌操作洁净区内的人数应严加控制,检查和监督应尽可能在无菌操作的洁净区外进行。
第二十一条凡在洁净区工作的人员(包括清洁工和设备维修工)都必须定期培训,以使无菌药品的操作符合要求,培训的内容应包括卫生和微生物方面的基础知识。
未受培训的外部人员(如外部施工人员或维修人员)在生产期间需进入洁净区时,应对他们进行特别详细的指导和监督。
第二十二条从事动物组织加工处理的人员或者从事与当前生产无关的微生物培养的工作人员通常不应进入无菌药品生产区,不可避免时,应严格遵循相关的人员净化规程。
第二十三条高标准的个人卫生要求及清洁极为重要。
应指导从事无菌药品生产的员工随时报告任何可能导致污染的异常情况,包括污染的种类和数量;应定期进行健康检查,对有可能导致微生物污染风险增大的员工,应由指定的称职人员采取适当的措施。
第二十四条更衣和洗手必须遵循相应的书面规程,以尽可能减少对洁净区的污染或将污染物带入洁净区。
第二十五条洁净区内不得佩戴手表和首饰,不得涂抹化妆品。
第二十六条工作服及其质量应与生产操作的要求及操作区的洁净度级别相适应,其穿着方式应能保护产品免遭污染。
各洁净区的着装要求规定如下:
D级区:
应将头发、胡须等相关部位遮盖。
应穿普通的工作服和合适的鞋子或鞋套。
应采取适当措施,以避免带入洁净区外的污染物。
C级区:
应将头发、胡须等相关部位遮盖,应戴口罩。
应穿手腕处可收紧的连体服或衣裤分开的工作服,并穿适当的鞋子或鞋套。
工作服应不脱落纤维或微粒。
A/B级区:
应用头罩将所有头发以及胡须等相关部位全部遮盖,头罩应塞进衣领内,并戴防护目镜,应戴口罩以防散发唾液液滴。
应戴经灭菌且无颗粒物(如滑石粉)散发的橡胶或塑料手套,穿经灭菌或消毒的脚套,裤腿应塞进脚套内,袖口应塞进手套内。
工作服应为灭菌的连体工作服,不脱落纤维或微粒,并能滞留身体散发的微粒。
第二十七条人员的便服不得带入通向B、C级区的更衣室。
每位员工每次进入A、B级区操作,都应更换无菌工作服;或至少一天更换一次,但须用监测结果证明这种方法的可行性。
操作期间应经常消毒手套,并在必要时更换口罩和手套。
第二十八条洁净区所用工作服的清洗和处理方式应确保其不携带有污染物,不会污染洁净区。
工作服的清洗、灭菌应遵循书面规程,并最好在单独设置的洗衣间内进行操作,工作服处理不当会损坏纤维并增加散发微粒的风险。
第七章厂房
第二十九条为了尽可能减少微粒或微生物的散发或积聚、便于反复清洁和消毒,洁净区内所有暴露的内表面应平整光滑、密封、无裂缝。
第三十条为了减少尘埃积聚并便于清洁,洁净区内不应有难清洁的部位,货架、柜子、设备及门应尽可能便于清洁,不得使用移动门。
第三十一条天棚应作密封处理,防止来自上方的污染。
第三十二条管道、风管以及其它设施的安装应便于清洁,应避免不能密封的敞口和难以清洁的表面。
第三十三条无菌生产的A/B级区内禁止设置水池和地漏。
在其它洁净区内,机器设备或水池与地漏不应直接相连。
洁净区内的地漏应设水封,防止倒流。
第三十四条更衣室应设计成气闸室并使更衣的不同阶段分开,以尽可能避免工作服被微生物和微粒污染。
更衣室应有足够的换气次数。
更衣室后段的静态级别应与其相应洁净区的级别相同。
必要时,最好将进入和离开洁净区的更衣间分开设置。
一般情况下,洗手设施只能安装在更衣室前段。
第三十五条气锁室两侧的门不应同时打开。
应采用连锁系统或光学或(和)声学的报警系统防止两侧的门同时打开。
第三十六条洁净区过滤空气的送风应能确保在任何运行状态下对周围低级别区保持正压及气流方向,并有足够的自净能力。
应特别注意对高风险操作区的保护,即重点保护产品以及与产品相接触的物料清洁后直接暴露的工艺环境。
当涉及某些致病性、剧毒、放射性或者活性病毒或细菌物料或产品时,空调净化系统的送风和压差可作适当调整,必要时,有些生产操作的设备及该区域的排风应作去污染处理(如排风口安装过滤器)。
第三十七条应证明各种气流方式无导致污染的风险并记录(如烟雾试验的录像),应采取适当的措施确保气流不会将操作或设备以及操作人员散发的微粒吹向洁净度要求高的区域。
第三十八条应设送风故障的报警系统。
应在压差十分重要的相邻级别区之间安装压差表。
压差数据应定期记录或者归入有关文挡中。
第三十九条由于轧盖会产生大量的微粒,应设置单独的轧盖间,并有措施防止所产生的微粒对其它区域的污染。
第八章设备
第四十条除传送带本身能连续灭菌(如隧道式灭菌器)以外,传送带不得穿越A、B或C级区与更低级别洁净区的隔离墙。
第四十一条在现实和可能条件下,生产设备及辅助装置的设计和安装方式,应便于在洁净区外操作、保养和维修。
需灭菌的设备应尽可能在完全装配后进行灭菌。
第四十二条无菌药品生产的洁净区空调净化系统应保持连续运行,不得经常关闭,以始终维持相应的洁净度级别或无菌状态。
因故关闭后再次开启空调净化系统,应重新进行洁净区的验证,验证合格后方可用于无菌药品的生产。
第四十三条在洁净区内进行设备维修时,如所规定的洁净度或无菌状态遭到破坏,应对该区域进行必要的清洁、消毒或灭菌(可能时)后,方可重新开始生产操作。
第四十四条所有设备如灭菌柜、空气处理及过滤系统、呼吸过滤器和气体过滤器、工艺用水的处理、生产、贮存和分配系统等,都必须验证并定期维修保养;维修保养后,经批准方可投入使用。
第四十五条关键公用介质(如压缩空气、氮气)的过滤器和呼吸过滤器的完整性应定期检查。
第九章卫生
第四十六条应按照书面规程对洁净区进行必要的清洁和消毒。
所采用消毒剂的种类应多于一种并定期轮换。
为及时发现是否出现耐受菌株及其蔓延情况,应定期进行环境监测。
紫外线杀菌效力有限,不能用以替代化学消毒剂。
第四十七条宜监测消毒剂和清洁剂的微生物污染状况,稀释液应存放在事先清洁过的容器内,存放期不得超过规定时限(密封且经灭菌的除外)。
A、B级区应使用无菌的消毒剂和清洁剂。
第四十八条可采用熏蒸以降低洁净区内卫生死角的微生物污染。
第十章生产管理
第四十九条生产加工的每个阶段(包括灭菌前的各阶段)都必须采取预防措施,以尽可能降低污染。
第五十条无菌生产工艺的验证应当包括培养基的模拟试验。
应根据产品的剂型、培养基的选择性、澄清度、浓度和灭菌的适用性来选择培养基。
应尽可能模拟常规的无菌生产工艺,并包括所有对结果有影响的关键生产工序。
此外,还应考虑正常生产中已出现过的各种偏差及最差情况。
培养基模拟试验的初始验证需要连续进行3次试验。
此模拟试验应在规定的时间间隔以及空调净化系统系统、设备、生产工艺及班次数有重要的变更后重复进行。
培养基模拟试验通常每一生产工艺每年进行2次。
培养基灌装容器的数量应足以保证评价的有效性。
对批次量比较小的产品而言,培养基灌装的数量应至少等于产品的批次量。
培养基模拟试验的目标是不出现长菌,但置信度为95%时,污染率应小于0.1%。
企业应建立警戒及纠偏限度标准。
发生任何微生物污染时,均应进行调查。
第五十一条应采取措施确保任何验证试验不危及生产的安全性。
第五十二条无菌原料药的精制、无菌药品的配制、直接接触药品的包装材料和器具等最终清洗、A/B级区内消毒剂和清洁剂的配制用水应符合注射用水的质量标准。
第五十三条水源、水处理设施及水的化学和微生物污染状况应定期监测,必要时还应监测细菌内毒素。
应保存监测结果及所采取纠偏措施的相关记录。
第五十四条当无菌操作正在进行时,应特别注意减少洁净区内的各种活动。
人员走动应有控制并应十分小心,以避免剧烈活动散发过多的微粒和微生物。
由于所穿工作服不透气,环境的温湿度不宜过高。
第五十五条应尽可能减少物料的微生物污染程度。
如检测结果表明有必要时,物料的质量标准中应当包括微生物限度标准。
第五十六条洁净区内不得存放易脱落纤维的容器和物料;在无菌操作的过程中,应完全避免使用此类容器和物料。
第五十七条应采取各种措施减少最终产品的微粒污染。
第五十八条最终清洗后物料、容器和设备的处理应避免再次污染。
第五十九条应尽可能缩短物料、容器和设备的清洗、干燥和灭菌的间隔时间以及灭菌至使用的间隔时间。
应建立规定贮存条件下的时限控制标准。
第六十条应尽可能缩短药液从开始配制到灭菌(或除菌过滤)的间隔时间。
应根据每一产品组份及规定的贮存方法来确定各自的时限控制标准。
第六十一条应根据所用灭菌方法的效果确定灭菌前产品微生物污染水平的监控标准,并定期监控。
必要时,还应监控热原或细菌内毒素。
应尽可能在接近灌装点的位置处安装除菌过滤器,并对灭菌前的药液进行过滤。
第六十二条无菌操作所需的物料、容器、设备和任何其它物品都应灭菌,并通过与墙密封的双扉灭菌柜进入无菌操作区,或以其它方式进入无菌操作区,但不得引入污染。
用于保护产品或药液的气体应通过除菌过滤器进入洁净区。
第六十三条无菌药品批次划分的原则:
1)大、小容量注射剂以同一配液罐最终一次配制的药液所生产的均质产品为一批;同一批产品如用不同的灭菌设备或同一灭菌设备分次灭菌的,应可追溯。
2)粉针剂以同一批无菌原料药在同一连续生产周期内生产的均质产品为一批;
3)冻干粉针剂以同一批配制的药液使用同一台冻干设备在同一生产周期内生产的均质产品为一批;
4)滴眼剂、眼膏剂、软膏剂、乳剂和混悬剂以同一配制罐最终一次配制所生产的均质产品为一批。
第六十四条粉针剂的有效期不得超过生产所用无菌原料药的有效期。
第十一章灭菌
第六十五条所有的灭菌方法都应经过验证。
应特别注意现行《中华人民共和国国药典》未收载的灭菌方法或被灭菌产品不是一种简单的水溶液或油溶液时所采用的灭菌方法。
应尽可能采用热力灭菌法。
第六十六条任何灭菌方法在投入使用前,都必须通过物理检测手段验证其对产品的适用性及灭菌效果,即每种被灭菌产品的所有部位都达到了设定的灭菌要求,必要时还应进行生物指示剂试验,作为灭菌监控的补充手段。
第六十七条应对灭菌方法的有效性定期进行再验证(每年至少一次)。
设备有重大变更后,应进行再验证。
应保存再验证的结果和记录。
第六十八条所有的待灭菌物品均须按规定的要求处理,以获得良好的灭菌效果,灭菌工艺的设计应确保灭菌完全。
第六十九条灭菌设备腔室内待灭菌物品的装载方式应通过验证确立。
第七十条应按供应商的要求保存和使用生物指示剂,并通过阳性对照和D值测试来确认其质量。
使用生物指示剂时,应采取严格措施,防止由其所致的微生物污染。
第七十一条应有明确区分已灭菌产品和待灭菌产品的方法。
每一车(盘或其它装载设备)产品或物料均应贴签,清晰地注明品名、批号并标明是否已经灭菌。
必要时,可用湿热灭菌指示带来指示一批(或一个亚批)产品是否已灭过菌,但灭菌指示带并不能确保该批的无菌特性。
第七十二条每一个灭菌批次都应有灭菌记录。
应把灭菌记录作为该批产品放行与否的依据之一。
第十二章最终灭菌
热力灭菌
热力灭菌通常有湿热灭菌和干热灭菌。
第七十三条在验证和生产过程中,用于监测或记录的温度探头与用于控制的温度探头应分别设置,设置的位置应通过验证确定。
每次灭菌均应记录灭菌过程的时间/温度曲线。
如采用自控和监测系统,该系统应经过验证,以确保符合关键工艺的要求。
该系统应能记录系统本身以及工艺运行过程中出现的故障,操作人员应监控这类故障的发生。
应定期将独立的温度显示器的读数与灭菌过程中记录获得的图谱对照。
第七十四条可使用化学或生物指示剂监控灭菌工艺,但它们不得替代物理测试。
第七十五条灭菌时间应从能保证所有被灭菌品都达到设定的灭菌温度后才开始计算。
每种装载方式所需升温时间均须测定并记录。
第七十六条应有措施防止灭菌冷却过程中已灭菌物品遭受污染,任何与产品相接触的冷却用介质(液体或气体)应经过灭菌或除菌处理,除非能证明生产过程中可剔除任何渗漏的产品。
湿热灭菌
第七十七条湿热灭菌工艺监控的参数应包括灭菌温度、时间和压力。
对腔室底部装有排水口的灭菌柜而言,可能需要测定并记录该点在灭菌全过程中的温度数据。
如灭菌工艺中包括抽真空操作,则应经常对腔室作检漏测试。
第七十八条被灭菌物品如不密封容器中的产品,则应用合适的材料将其适当包扎,所用材料及包扎方式应有利于空气排放、蒸汽穿透并在灭菌后能防止污染。
在规定的温度和时间内,被灭菌物品所有部位均应与灭菌介质充分接触。
第七十九条直接接触产品的包装容器、灌装设备、胶塞及可能与产品接触的工器具等的灭菌应采用纯蒸汽灭菌。
干热灭菌
第八十条干热灭菌时灭菌柜腔室内的空气应循环并保持正压,以阻止非无菌空气进入。
进入腔室的空气应经过高效过滤器过滤,高效过滤器应经过完整性测试。
当干热灭菌用于去除热原时,验证应包括细菌内毒素挑战试验。
干热灭菌过程中的温度、时间和压差应有记录。
辐射灭菌
第八十一条只有经试验证明本法对产品质量没有不良影响时方可采用辐射灭菌。
第八十二条辐射灭菌过程中,应采用剂量指示剂测定辐射剂量。
剂量指示剂能指示产品本身所吸收的剂量,不受辐射源辐射速率的影响。
为确保辐射灭菌器中始终有剂量指示剂,被灭菌物品中应安放足够数量的剂量指示剂,其安放间隔不宜过大。
塑料剂量指示剂应在其校正的有效期内使用。
辐射灭菌后,应尽快从剂量指示剂读取数据。
第八十三条生物指示剂可作为一种附加的监控手段。
第八十四条验证方案应包括考察包装密度变化对灭菌效果的影响的考察。
第八十五条物料处理规程应能防止已辐射物品与未辐射物品的混淆。
为区分已辐射物品和未辐射物品,在每个包装上均应有辐射后能产生颜色变化的辐射指示片。
第八十六条应在规定的时间内达到总辐射剂量标准。
环氧乙烷灭菌
第八十七条只有在其它灭菌方法不能采用时方可采用本法。
灭菌工艺验证应能证明环氧乙烷对产品不会造成破坏性影响,并能证明针对不同产品或物料所设定的排气条件和时间能够确保所有残留气体及反应产物降至设定的合格限度。
第八十八条气体与微生物直接接触极为重要,应采取预防措施,以避免微生物被包藏在晶体或干燥的蛋白质内。
包装材料的性质和数量对灭菌效果有明显的影响。
第八十九条被灭菌物品达到灭菌工艺所规定的温、湿度条件后开始通气灭菌,应尽可能缩短灭菌的等待时间。
第九十条每次灭菌时,应将适当的、一定数量的生物指示剂安放在被灭菌物品的不同部位,用以监控灭菌工艺,所获得的监控结果应归入相应的批记录。
第九十一条每次灭菌记录的内容应包括:
完成整个灭菌过程的时间、灭菌过程中腔室的压力、温度和湿度、环氧乙烷的浓度及总消耗量。
应用仪表记录整个灭菌过程的压力和温度,灭菌曲线应归入相应的批记录。
第九十二条灭菌后的物品应存放在受控的通风环境中,以便将残留的气体及反应产物降至规定的限度内。
该工艺过程应经过验证。
第十三章非最终灭菌产品的过滤
第九十三条对可最终灭菌的产品而言,不得以除菌过滤工艺替代最终灭菌工艺。
如果药品不能在其最终包装容器中灭菌,可用孔径为0.22μm(或更小)的除菌过滤器(或除菌效