学士学位论文20万吨合成氨转变工序.docx
《学士学位论文20万吨合成氨转变工序.docx》由会员分享,可在线阅读,更多相关《学士学位论文20万吨合成氨转变工序.docx(48页珍藏版)》请在冰豆网上搜索。
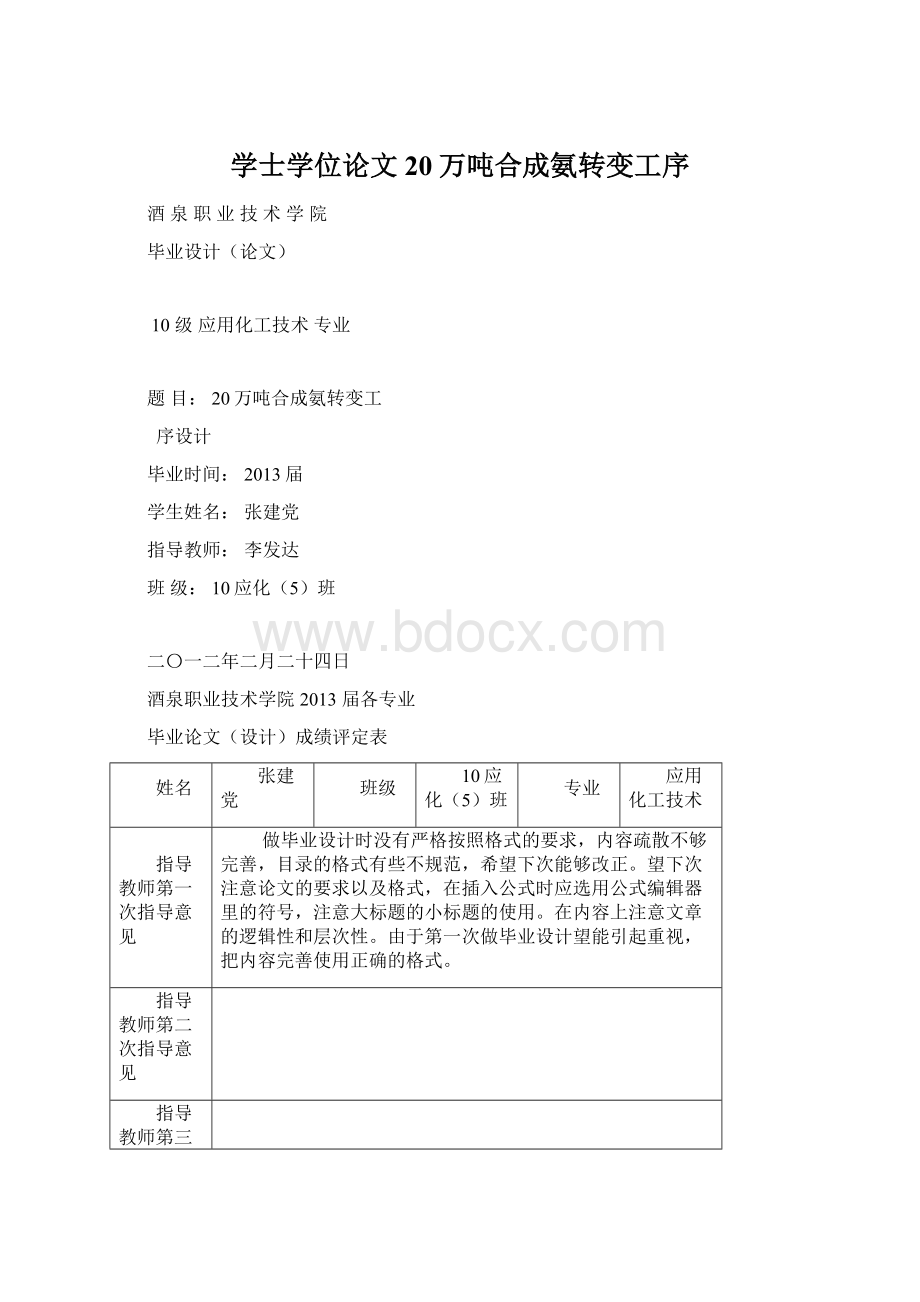
学士学位论文20万吨合成氨转变工序
酒泉职业技术学院
毕业设计(论文)
10级应用化工技术专业
题目:
20万吨合成氨转变工
序设计
毕业时间:
2013届
学生姓名:
张建党
指导教师:
李发达
班级:
10应化(5)班
二〇一二年二月二十四日
酒泉职业技术学院2013届各专业
毕业论文(设计)成绩评定表
姓名
张建党
班级
10应化(5)班
专业
应用化工技术
指导教师第一次指导意见
做毕业设计时没有严格按照格式的要求,内容疏散不够完善,目录的格式有些不规范,希望下次能够改正。
望下次注意论文的要求以及格式,在插入公式时应选用公式编辑器里的符号,注意大标题的小标题的使用。
在内容上注意文章的逻辑性和层次性。
由于第一次做毕业设计望能引起重视,把内容完善使用正确的格式。
指导教师第二次指导意见
指导教师第三次指导意见
指导教师评语及评分
成绩:
签字(盖章)年月日
答辩小组评价意见及评分
成绩:
签字(盖章)年月日
教学系毕业实践环节指导小组意见
签字(盖章)年月日
学院毕业实践环节指导委员会审核意见
签字(盖章)年月日
20万吨合成氨转变工序工艺设计
摘要:
氨是一种重要的化工原料,特别是生产化肥的原料,它是由氢和氮合成。
合成氨工业是氮肥工业的基础。
为了生产氨,一般均以各种燃料为原料。
首先,制成含H2和CO等组分的煤气,然后,采用各种净化方法,除去气体中的灰尘、H2S、有机硫化物、CO、CO2等有害杂质,以获得符合氨合成要求的洁净的1:
3的氮氢混合气,最后,氮氢混合气经过压缩至15Mpa以上,借助催化剂合成氨。
氨是重要的基础化工产品之一,在国民经济中占有重要地位。
合成氨生产经过多年的发展,现已发展成为一种成熟的化工生产工艺。
本设计是以天然气为原料年产二十万吨合成氨转变工序的设计。
近年来合成氨工业发展很快,大型化、低能耗、清洁生产均是合成氨设备发展的主流,技术改进主要方向是开发性能更好的催化剂、降低氨合成压力、开发新的原料气净化方法、降低燃料消耗、回收和合理利用低位热能等方面上。
设计采用的工艺流程简介:
天然气经过脱硫压缩进入一段转化炉,把CH4和烃类转化成H2,再经过二段炉进一步转化后换热进入高变炉,在催化剂作用下大部分CO和水蒸气反应获H2和CO2,再经过低变炉使CO降到合格水平,去甲烷化工序。
本设计综述部分主要阐述了国内外合成氨工业的现状及发展趋势以及工艺流程、参数的确定和选择,论述了建厂的选址;介绍了氨变换工序的各种流程并确定本设计高-低变串联的流程。
工艺计算部分主要包括转化段和变换段的物料衡算、热量衡算、平衡温距及空速计算。
设备计算部分主要是高变炉催化剂用量的具体计算,并根据设计任务做了转化和变换工序带控制点的工艺流程图。
本设计的优点在于选择较为良好的厂址和原料路线,确定良好的工艺条件、合理的催化剂和能源综合利用。
另外,就是尽量减少设备投资费用。
关键字:
合成氨,天然气,转化,变换
一、综述
(一)氨的性质、用途及重要性
1.氨的性质
氨分子式为NH3,在标准状态下是无色气体,比空气轻,具有特殊的刺激性臭味。
人们在大于100cm3/m3氨的环境中,每天接触8小时会引起慢性中毒。
氨的主要物理性质有:
极易溶于水,溶解时放出大量的热。
氨水溶液呈碱性,易挥发。
液氨和干燥的氨气对大部分物质没有腐蚀性,但在有水的条件下,对铜、银、锌等金属有腐蚀作用。
氨的化学性质有:
在常温下相当稳定,在高温、电火花或紫外光的作用下可分解为氮和氢。
具有可燃性,自然点为630℃,一般较难点燃。
氨与空气或氧的混合物在一定范围内能够发生爆炸。
氨的性质比较活泼,能与各种无机酸反应生成盐。
2.氨的用途及在国民生产中的作用
氨是重要的无机化工产品之一,在国民经济中占有重要地位。
合成氨指由氮和氢在高温高压和催化剂存在下直接合成的氨。
世界上的氨除少量从焦炉气中回收外,绝大部分是合成的氨。
氨主要用于农业,合成氨是我化肥工业的基础,氨本身是最重要的氮素肥料,其他氮素肥料也大都是先合成氨,再加工成尿素或各种铵盐肥料,这部分均占70%的比例,称之为“化肥氨”;同时氨也是重要的无机化学和有机化学工业基础原料,用于生产铵、胺、染料、炸药、合成纤维、合成树脂的原料,这部分约占30%的比例,称之为“工业氨”。
氨作为工业原料和氨化饲料,用量约占世界产量的12%。
硝酸、各种含氮的无机盐及有机中间体、磺胺药、聚氨酯、聚酰胺纤维和丁腈橡胶等都需直接以氨为原料生产。
液氨常用作制冷剂。
合成氨是大宗化工产品之一,世界每年合成氨产量已达到1亿吨以上,其中约有80%的氨用来生产化学肥料,20%作为其它化工产品的原料。
氨作为最为重要的基础化工产品之一,同时也是能源消耗的大户,世界上大约有10%的能源用于合成氨。
随着世界人口的不断增加,用于制造尿素、硝酸铵、磷酸铵、硫酸铵以及其它化工产品的氨用量也在增长。
据统计1994年世界氨产量为113.46Mt,其中中国、美国、印度、俄罗斯三个主要产氨国占了一半以上。
在化学工业中合成氨工业已经成为重要的支柱产业[1]。
(二)合成氨生产技术的发展
1.世界合成氨技术的发展
(1)原料构成的变化
为了合成氨,首先必须提供氮和氢。
氮来自空气,氢来自水。
气和水到处都有,而且取之不尽。
传统的制氮方法是在低温下将空气液化、分离,以及水电解制氢。
由于电解制氢法,电能消耗大,成本高。
传统方法还是采用高温下将各种燃料和水蒸气反应制造氢。
因此合成氨生产的初始原料是焦炭、煤、焦炉气、天然气、石脑油、重油等,60多年来世界合成氨原料的构成变化见下表1-1。
表1.1世界合成氨原料构成(%)
原料
1929
1939
1953
1965
1971
1975
1980
1985
1990
焦炭、煤
65.2
53.6
37
5.8
9.0
9.0
5.5
6.5
13.5
焦炉气
15.8
27.1
22
20
天然气
-
1.3
26
44.2
60
62.0
71.5
71.0
77
石脑油
-
-
-
4.8
20
19.0
15.0
13.0
6
重油
-
-
-
9.2
4.5
5.0
7.5
8.5
3
其它
19
18
15
16
6.5
5.0
0.5
1.0
0.5
合计
100
100
100
100
100
100
100
100
100
由表1-1可知,合成氨的原料构成是从以固体燃料为主转移到以气体燃料和液体原料为主。
自从北美大量开发天然气资源成功之后,20世纪50年代开始采用天然气制氨。
因为天然气便于管道运输,用作合成氨的原料具有投资省、能耗低等明显优点。
到20世纪60年代末,国外主要产氨国都已先后停止用焦炭、煤为原料,而以天然气、重油等为原料,天然气所占比重不断上升。
一些没有天然气资源的国家,如日本、英国在解决了石脑油蒸汽转化过程的析碳问题后,1962年开发成功石脑油为原料生产合成氨的方法。
石脑油经脱碳、气化后,可采用和天然气为原料的相同生产装置制氨。
但石脑油价格比天然气高,而且又是石油化工的重要原料,用于制氨受到一定限制。
为了扩大原料范围,又开发了用重油部分氧化法制氢。
从此比石脑油价廉、来源广泛的重油和减压渣油开始作为合成氨的另一种原料。
表1-2为各种原料的日产1043.3t合成氨厂,相对投资和能量消耗比较。
由表可见,虽然各国资源不同,但选用原料的基本方向相同。
只要资源条件具备作为合成氨的原料。
首先应考虑天然气和油田气,其次采用石脑油。
表1.2氨厂采用的各种原料的相对投资和能量消耗
原料
天然气
重油
煤
相对投资费用
1.0
1.5
2.0
能量消耗/(GJ/t)
28
38
48
特别是以天然气为原料的合成氨工业占了很大的比重,本设计就是以天然气为原料合成氨,主要是转化工段的设计。
(2)生产规模大型化
20世纪50年代以前,氨合成塔的最大能力为日产200t氨,到60年代初期为400t。
随着蒸汽透平驱动的高压离心式压缩机研制成功,美国凯洛格公司运用建设单系列大型炼油厂的经验,首先运用工艺过程的余热副产高压蒸汽作为动力,于1963年和1966年相继建成日产544.31t和907.19t的氨厂,实现了单系列合成氨装置的大型化,这是合成氨工业发展史上第一次突破。
大型化的优点是投资费用低,能量利用率高,占地少,劳动生产率高。
从20世纪60年代中期开始,新建氨厂大都采用单系列的大型装置。
但是,大型的单系列合成氨装置要求能够长周期运行,对机器和设备质量要求很高,而且在超过一定规模以后,优越性并不十分明显了。
因此大型氨厂通常是指日产600t级,日产1000t级和日产1500t级的三种。
现在世界上规模最大的合成氨装置为日产1800t氨,1991年在比利时的安特卫普建成投产。
(3)低能耗新工艺
合成氨,除原料为天然气、石油、煤炭等一次能源外。
整个生产过程还需消耗较多的电力、蒸汽等二次能源,而用量又很大。
现在合成氨能耗占世界能源消费总量的3%,中国合成氨生产能耗约占全国能耗的4%。
由于吨氨生产成本中能源费用占70%以上,因此能耗是衡量合成氨技术和经济效益的重要标志。
以天然气为原料的日产1000t合成氨装置吨氨能耗目前已从20世纪70年代的40.19GJ下降到39.31GJ左右,而且以天然气为原料的大型氨厂的所需动力约有85%可由余热供给[3]。
(4)生产自动化
合成氨生产特点之一是工序多、连续性强。
20世纪60年代以前的过程控制多采取分散方式,在独立的几个车间控制室中进行。
自从出现单系列装置的大型氨厂,除泵类有备用外,其它设备和机器都是一台。
因此,某一环节的失调就会影响生产,为了保证长周期的安全生产,对过程控制提出更高的要求,从而发展到把全流程的温度、压力、流量、物位和成分五大参数的模拟仪表、报警、连锁系统全部集中在中央控制室显示和监视控制。
自从20世纪70年代计算机技术应用到合成氨生产以后,操作控制上产生了飞跃。
1975年美国霍尼威尔公司开发成功TCP-2000总体分散控制系统(TotolDistributedControlSystem),简称集散控制系统(DCS)。
DCS是现代计算机技术、控制技术、数据通讯技术和荧光显示技术(CRT)相结合的产物。
在CRT操作平台上可以存取、显示多种数据和画面,包括带控制点的流程,全部过程变量、控制过程变量,以及其参数的动态数值和趋势图,从而实现集中监视和集中操作。
操作人员对于人一控制点、控制单元、生产设备、车间以及全厂的运作情况进行随机或定势的观察,只要通过键操作调出相应的画面,即可把所需内容显示在CRT上,以便监视、控制和修改某些参数。
需要的数据、流程都可随机或定时在打印机上打印和彩色硬拷贝机上拷贝。
与此同时,报警、连锁系统,程序控制系统,采用了微机技术的可编程序逻辑控制器(PLC)代替过去的继电器,采用由用户编写的程序,实现自动或手动的“开”或“停”和复杂程序不同的各种逻辑控制,计时、计数、模拟控制等。
近年由于机电一体化需要逻辑控制和模拟控制计时、计数、运算等功能相结合,各仪表厂家的产品已从单一的逻辑控制,趋向多种控制功能结合为一体。
因此,用“可编程序控制器”(PC)这一名称较为确切。
制和管理,这种新颖的过程控制系统不仅可以取代常规模拟仪表,而且还可以完成局部优化控制以及模拟仪表难以实现的复杂自控系统。
若能用仿真技术进行操作人员的模拟培训只需在一此外,若配置有高一级管理、控制功能的上位机系统,还能进行全厂综合优化控台高性能的计算机上配合相应的软件以代替实际生产装置的控制、运作设备,这样就可以在较短的时间内学习开停车、正常操作和事故状态操作。
这些都表示氨生产技术自动化进入新的阶段,改变了几十年合成氨生产控制的面貌。
(5)合成氨工业在国民经济中的重要地位
合成氨是化工的重要组成部分,在国民经济中有相当重要的位置。
氨是化学工业的重要原料之一,用途十分广泛。
以氮和氢为原料合成氨,是目前世界上采用最广泛,也是最经济的一种方法。
氨的用途很广。
以氨为主要原料可以制造各种氮素肥料和复合肥料。
氨本身就是一种高效肥料,液氨含氮82.3%,一些国家已大规模直接施用液氨。
可见,合成氨工业是氮肥工业的基础,对农业增产起着十分重要的作用。
氨是氮肥的主要原料,可生产尿素、硫酸铵、硝酸铵、碳酸氢铵等;氨还可用来生产多种复合化肥,如磷酸氢铵等。
对农业生产有重大意义。
氨也是一些工业部门的重要原料。
工业用氨量已占合成氨产量的百分之十以上。
基本化学工业中的硝酸、纯碱、各种含氮无机盐,有机化学中的各种含氮中间体。
制药工业中的磺胺类药物和高分子化学工业中的氨基塑料、聚酰胺纤维、丁腈橡胶等,都需直接或间接以氨为原料。
食品工业中,氨广泛用作冷冻剂,冶金工业、石油加工工业、机械工业亦需使用氨或其加工产品。
氨还应用于国防和尖端科学技术部门。
制造三硝基甲苯、三硝基苯酚、硝化甘油、硝化纤维等多种炸药都要消耗大量的氨。
生产导弹、火箭的推进剂和氧化剂,同样也离不开氨。
不仅如此,合成氨工业的迅速发展,又促进了一系列科学技术和化学合成工业的发展。
如高压低温技术、催化和特殊金属材料的应用、固体燃料气化、液体和气体燃料的合理使用,以及尿素、甲醇、高级醇的合成,石油加氢,高压聚合物(如高压聚乙烯)的生产等,都是在合成氨工业的基础上发展起来或应用其生产技术成就而获得成功的。
随着科学和生产技术的发展,合成氨工业在国民经济各部门中的作用必将日益显著。
2.中国合成氨工业的发展概况
1784年,有学者证明氨是由氮和氢组成的。
19世纪,人们试图利用高温、高压、电弧、催化剂等手段试验直接合成氨,均未成功。
19世纪末,在化学热力学、动力学和催化剂等领域取得一定进展后,对合成氨反应的研究有了新的进展。
1901年法国物理化学家吕·查得利开创性地提出氨合成的条件是高温、高压,催化剂存在。
1912年在德国建立了世界上第一个日产30吨的合成氨厂。
在以后的生产过程中,人们对合成氨的生产工艺进行了不断改进和完善,如变换工艺的改进。
原料气净化方法的革新及合成塔的改造等,但工艺路线没有大的变化。
改革开放以来,我国合成氨工业发展很快,产量不断增加,在原料气制造方面,基本掌握了煤、油、气不同原料的气化技术。
为了满足我国社会主义建设发展的需要,在发展煤炭加工业的同时,还积极开发石油和天然气资源,开展综合利用,逐步扩大了合成氨工业的原料来源。
近年来,由于透平式离心压缩机和电子计算机自动控制等新技术的应用,使我国合成氨工业朝现代化方向迈进了一步。
但是,单位氨产量的能量消耗、劳动生产率等方面和工业发达国家相比仍有较大差距。
按人口平均的化肥产量(吨/人·年)和单位种植面积施肥量仍然较低。
所以高速发展合成氨工业仍是一项紧迫的任务。
中国合成氨生产是从20世纪30年代开始的,但当时仅在南京、大连两地建有氨厂,一个是由著名爱国实业家范旭东先生创办的南京永利化学工业公司铔厂——永利宁厂,现南京化学工业公司的前身;另一个是日本占领东北后在大连开办的满洲化学工业株式会社,最高年产量不超过50Kt(1941年)。
此外在上海还有一个电解水制氢生产合成氨、硝酸的小型车间。
中华人民共和国成立以来,化工部门贯彻为农业服务的方针,把发展化肥生产放在首位。
经过50多年的努力,中国已拥有多种原料、不同流程的大、中、小型合成氨厂1000多个,1999年总产量为34.52Mt氨,已跃居世界第1位,已掌握了以焦炭、无烟煤、褐煤、焦炉气、天然气及油田气和液态烃等气固液多种原料生产合成氨的技术,形成中国大陆特有的煤、石油、天然气原料并存和大、中、小生产规模并存的合成氨生产格局。
中国合成氨工业的发展经历了以下几个阶段。
第一、恢复老厂和新建中型氨厂
20世纪50年代初,在恢复和扩建老厂的同时,从原苏联引进以煤为原料、年产50kt的三套合成氨装置,并创建了吉化、兰州、太原三大化工基地,后又自行设计、制造了7.5万吨合成氨系统,以川化的创建为标志。
到60年代中期中氮已投产了15家。
20世纪60年代随着石油、天然气资源的开采,又从英国引进一套以天然气为原料的加压蒸汽转化法年产100kt合成氨装置(即泸天化);从意大利引进一套以重油为原料的部分氧化法年产50kt合成氨装置,从而形成了煤油气原料并举的中型氨厂生产系统,迄今为止,已建成50多座中型氨厂。
第二、小型氨厂的发展
从20世纪60年代开始在全国各地建设了一大批小型氨厂,1979年最多时曾发展到1539座氨厂。
第三、大型氨厂的崛起
20世纪70年代是世界合成氨工业大发展时期。
由于大型合成氨装置的优越性,1972年2月中国作出了成套引进化学肥料技术和设备的决定。
1973年开始,首批引进13套年产300kt合成氨的成套装置(其中10套为天然气为原料,建在川化、泸天化、云南、贵州等地),为了扩大原料范围,1978年又开始第二批引进4套年产300kt合成氨装置。
中国是世界上人口最多的农业大国,为了在2000年氮肥产量达到基本自给自足,最近十年先后陆续引进14套具有20世纪90年代先进水平的年产300kt合成氨成套设备,同时从20世纪70年代起,我国开始了大型合成氨成套装置的自行设计、自行制造工作,第一套年产30万吨的合成氨装置于80年在上海建成投产。
特别是于90年代初在川化建成投产的年产20万吨合成氨装置达到了当时的国际先进水平。
从而掌握了世界上几乎所有先进的工艺和先进技术如低能耗的凯洛格工艺、布朗工艺等,通过对引进技术的消化吸收和改造创新,不但使合成氨的技术水平跟上了世界前进的步伐,而且促进了国内中小型氨厂的技术发展。
至今,在32套引进装置中,原料为天然气、油田气的17套,渣油7套,石脑油5套,煤2套和尤里卡沥青1套,加上上海吴泾,成都的两套国产化装置,合成氨总能力为10.22Mt。
中国潜在的天然气资源十分丰富,除新勘探的新疆塔里木盆地有大量的天然气可以通过长距离的管线东输外,对海南莺歌海域蕴藏的天然气已决定在新世纪初新建一套引进的年产450kt合成氨装置,这将是中国规模最大的一套合成氨装置[1]。
(三)合成氨转变工序的工艺原理
1.合成氨的典型工艺流程介绍
合成氨的生产过程包括三个主要步骤:
原料气的制备、净化和压缩和合成。
(1)原料气制备
将煤和天然气等原料制成含氢和氮的粗原料气。
对于固体原料煤和焦炭,通常采用气化的方法制取合成气;渣油可采用非催化部分氧化的方法获得合成气;对气态烃类和石脑油,工业中利用二段蒸汽转化法制取合成气。
(2)净化
对粗原料气进行净化处理,除去氢气和氮气以外的杂质,主要包括变换过程、脱硫脱碳过程以及气体精制过程。
①一氧化碳变换过程
在合成氨生产中,各种方法制取的原料气都含有CO,其体积分数一般为12%~40%。
合成氨需要的两种组分是H2和N2,因此需要除去合成气中的CO。
变换反应如下:
CO+H2O→H2+CO2ΔH=-41.2kJ/mol;
由于CO变换过程是强放热过程,必须分段进行以利于回收反应热,并控制变换段出口残余CO含量。
第一步是高温变换,使大部分CO转变为CO2和H2;第二步是低温变换,将CO含量降至0.3%左右。
因此,CO变换反应既是原料气制造的继续,又是净化的过程,为后续脱碳过程创造条件。
②脱硫脱碳过程
各种原料制取的粗原料气,都含有一些硫和碳的氧化物,为了防止合成氨生产过程催化剂的中毒,必须在氨合成工序前加以脱除,以天然气为原料的蒸汽转化法,第一道工序是脱硫,用以保护转化催化剂,以重油和煤为原料的部分氧化法,根据一氧化碳变换是否采用耐硫的催化剂而确定脱硫的位置。
工业脱硫方法种类很多,通常是采用物理或化学吸收的方法,常用的有低温甲醇洗法(Rectisol)、聚乙二醇二甲醚法(Selexol)等。
粗原料气经CO变换以后,变换气中除H2外,还有CO2、CO和CH4等组分,其中以CO2含量最多。
CO2既是氨合成催化剂的毒物,又是制造尿素、碳酸氢铵等氮肥的重要原料。
因此变换气中CO2的脱除必须兼顾这两方面的要求。
一般采用溶液吸收法脱除CO2。
根据吸收剂性能的不同,可分为两大类。
一类是物理吸收法,如低温甲醇洗法(Rectisol),聚乙二醇二甲醚法(Selexol),碳酸丙烯酯法。
一类是化学吸收法,如热钾碱法,低热耗本菲尔法,活化MDEA法,MEA法等。
③气体精制过程
经CO变换和CO2脱除后的原料气中尚含有少量残余的CO和CO2。
为了防止对氨合成催化剂的毒害,规定CO和CO2总含量不得大于10cm3/m3(体积分数)。
因此,原料气在进入合成工序前,必须进行原料气的最终净化,即精制过程。
目前在工业生产中,最终净化方法分为深冷分离法和甲烷化法。
深冷分离法主要是液氮洗法,是在深度冷冻(<-100℃)条件下用液氮吸收分离少量CO,而且也能脱除甲烷和大部分氩,这样可以获得只含有惰性气体100cm3/m3以下的氢氮混合气,深冷净化法通常与空分以及低温甲醇洗结合。
甲烷化法是在催化剂存在下使少量CO、CO2与H2反应生成CH4和H2O的一种净化工艺,要求入口原料气中碳的氧化物含量(体积分数)一般应小于0.7%。
甲烷化法可以将气体中碳的氧化物(CO+CO2)含量脱除到10cm3/m3以下,但是需要消耗有效成分H2,并且增加了惰性气体CH4的含量。
甲烷化反应如下:
CO+3H2
CH4+H2OΔH=-206.2kJ/mol;
CO2+4H2
CH4+2H2OΔH=-165.1kJ/mol;
(3)氨合成
将纯净的氢、氮混合气压缩到高压,在催化剂的作用下合成氨。
氨的合成是提供液氨产品的工序,是整个合成氨生产过程的核心部分。
氨合成反应在较高压力和催化剂存在的条件下进行,由于反应后气体中氨含量不高,一般只有10%~20%,故采用未反应氢氮气循环的流程。
氨合成反应式如下:
N2+3H2
2NH3(g)ΔH=-92.4kJ/mol;
2.合成氨转化工序的工艺原理
本设计中的合成氨转变工序是指转化工序和变换工序的合称。
转换工序是指天燃气中的气态烃类转换成H2、CO和CO2,并达到要求,合成氨厂的转化工序分为两段进行。
在一段转化炉里,大部分烃类与蒸汽于催化剂作用下转化成H2、CO和CO2。
烷烃:
CnH2n+n+nH2O→nCO+(2n+1)H2
或
C0nH2n+n+2nH2O→nCO2+(3n+1)H2
烯烃:
CnH2n+nH2O→nCO+2nH2
CnH2n+2nH2O→nCO2+3nH2
接着一段转化气进入二段转化炉,在此加入空气,由一部分H2燃烧放出热量,催化剂床层温度上升到1200~1250℃,并继续进行甲烷的转化反应。
CH4+H2O→CO+3H2
CH4+2H2O→CO+4H2
二段转化炉出口气体温度约950~1000℃,残余甲烷含量和(H2+CO)/N2比均可达到指标。
3.合成氨变换工序的工艺原理
变换工序是指CO与水蒸气反应生成二氧化碳和氢气的过程。
在合成氨工艺流程中起着非常重要的作用。
目前,各种方法制取的原料气都含有CO,其体积分数一般为12%~40%,合成氨需要的两种组分是H2和N2,因此需要除去合成气中的CO。
变换工段主要利用CO变换反应式:
CO+H2O→CO2+H2ΔH298=-41.20kJ/mol
在不同温度下分两步进行,第一步是高温变换(简称高变)使大部分CO转化为CO2和H2,第二步是低温变换简称低变,将CO含量降到0.3%左右。
因此,CO变换既是原料气制造的继续,又是净化的过程。
(四)设计方案的确定
1.原料的选择
合成氨生产的原料