质量管理与可靠性课程设计.docx
《质量管理与可靠性课程设计.docx》由会员分享,可在线阅读,更多相关《质量管理与可靠性课程设计.docx(13页珍藏版)》请在冰豆网上搜索。
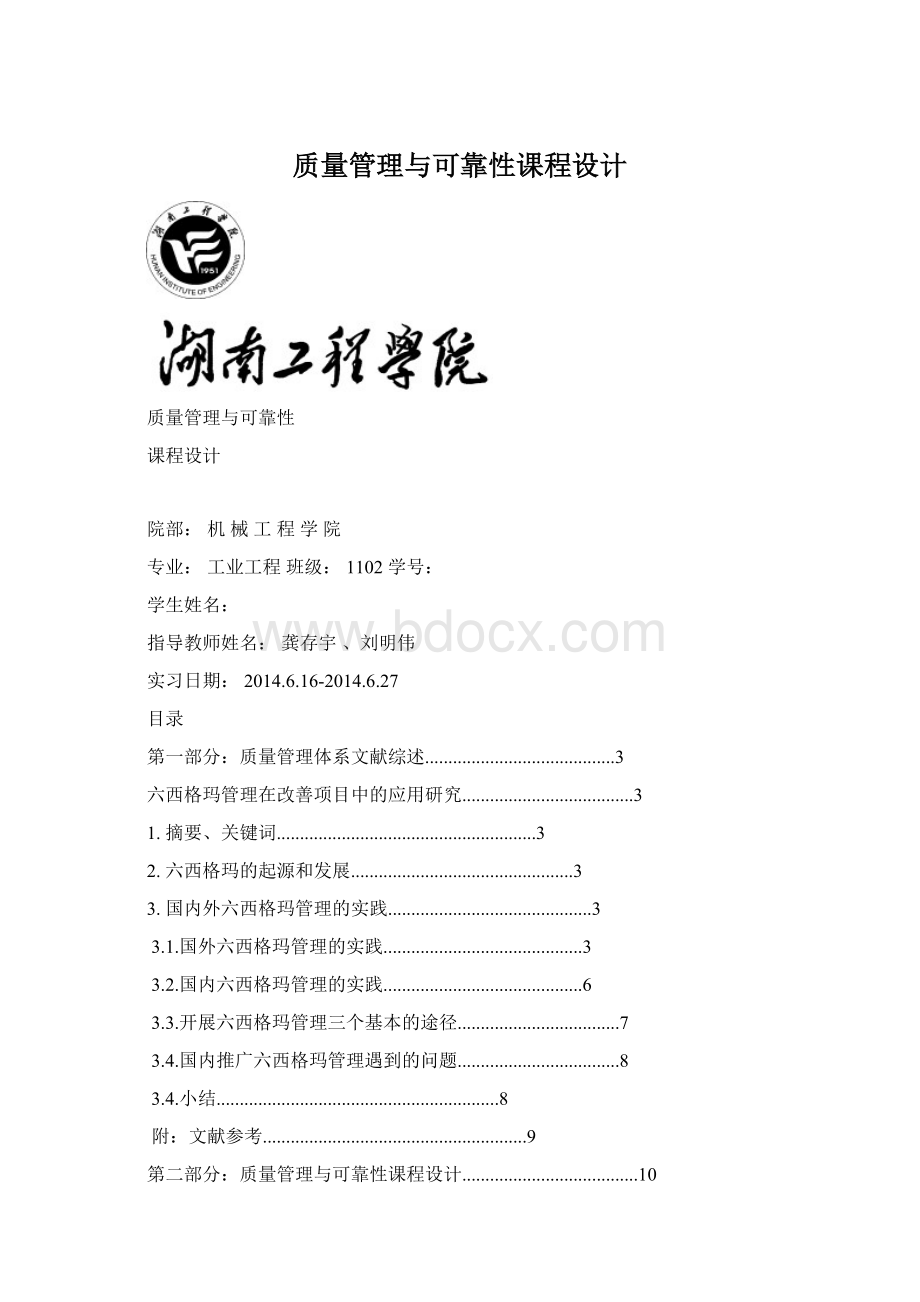
质量管理与可靠性课程设计
质量管理与可靠性
课程设计
院部:
机械工程学院
专业:
工业工程班级:
1102学号:
学生姓名:
指导教师姓名:
龚存宇、刘明伟
实习日期:
2014.6.16-2014.6.27
目录
第一部分:
质量管理体系文献综述.........................................3
六西格玛管理在改善项目中的应用研究.....................................3
1.摘要、关键词........................................................3
2.六西格玛的起源和发展................................................3
3.国内外六西格玛管理的实践............................................3
3.1.国外六西格玛管理的实践...........................................3
3.2.国内六西格玛管理的实践...........................................6
3.3.开展六西格玛管理三个基本的途径...................................7
3.4.国内推广六西格玛管理遇到的问题...................................8
3.4.小结.............................................................8
附:
文献参考.........................................................9
第二部分:
质量管理与可靠性课程设计......................................10
1.课程设计的性质、目的和任务............................................10
2.课程设计的内容和要求..................................................10
3.设计题目..............................................................10
4.设计结果..............................................................11
5.课程设计小结..........................................................15
附:
文献参考............................................................16
第一部分:
质量管理体系文献综述
六西格玛管理在改善项目中的应用研究
摘要:
六西格玛是一种改善企业流程管理质量的技术,以”零缺陷”的完美商业追求,带动质量成本的大幅度降低,最终实现财务成效的提升与企业竞争力的突破。
关键词:
六西格玛、零缺陷,差异化战略优势
六西格玛的起源和发展
六西格玛思想起源于本世纪80年代末期,美国摩托罗拉公司。
六西格玛建立在许多其他以往先进的管理理念和实践的基础之上,其特点是从顾客的要求出发,以流程为导向。
其追求的六西格玛目标是每百万机会3.4个缺陷的产品或服务质量。
不仅在生产制造中起着重大作用,对市场营销、服务、人力资源、财务、销售等流程也同样适用。
六西格玛改善方法论的典型步骤是D(定义)、M(测量)、A(分析)、I(改善)、C(控制),而用于研发设计的典型步骤是D(定义)、M(测量)、A(分析)、D(设计)、V(验证)或I(识别)、D(设计)、O(优化)、V(验证)。
六西格玛侧重以数据说话的观点,在实践中结合了许多传统的统计方法和工具如QFD(质量功能展开)、FMEA(失效模式及后果分析),SPC(统计过程控制),MSA(测量系统分析),ANOVE(方差分析),DOE(实验设计)等,通过相关软件如MINITAB的使用,大大简化了统计的运算过程,使六西格玛得以广泛地推行。
在企业高层领导的强力支持和推动下,借助外部力量培养黑带和绿带人员,以黑带和绿带作为火种,领导完成改善项目,达到降低流程的变差和COPQ、优化流程、降低成本提高经济效益的目标。
同时,通过提高顾客满意度,使企业的整体竞争力得到提高。
也就是说,六西格玛所关注的不仅是节流,更强调开源。
六西格玛方法在美国通用电气公司得到广泛运用和发扬,作为公司的四大战略之一,GE前总裁杰克.韦尔奇将六西格玛方法演变成一种无边界的企业文化,和员工处理日常工作的行为方式或行为习惯。
几年来为企业赢得了近百亿的经济效益。
六西格玛正在被世界上越来越多的企业所接受和认同。
1、国内外六西格玛管理的实践
(1)国外六西格玛管理的实践
在20世纪80年代和90年代早期,摩托罗拉公司与许多美国和欧洲企业一样,其“午餐及其他膳食和点心”都在遭受日本竞争对手的蚕食。
当时,摩托罗拉的高层领导承认其产品质量低劣。
借用摩托罗拉一位资深专家的话来说,他们正“置身于一个充满痛苦的世界”。
摩托罗拉的工程师迈克尔·哈默(MikelHarry)开始说服他的组织把研究变异作为改进绩效的一种途径。
在1987年,一个新的尝试出现在摩托罗拉的通讯部门,这个创新性的改善概念被称为“六西格玛”,通讯工程部的工程师比尔·史密斯(BillSmith)第一次提出了这一术语。
该部门当时的领导者是乔治·费希尔(GeorgeFisher),后来成了柯达的高层管理者。
比尔·史密斯和乔治·费希尔因此被认为是六西格玛的创始人。
在时任摩托罗拉首席执行官(CEO)的鲍勃·高尔文(BobGalvin)的大力支持下,六西格玛在全公司进行了推广,取得了巨大成功,在发起六西格玛活动仅仅两年后(即1988年)就获得了首届美国国家质量奖——马尔科姆·鲍德里奇国家质量奖(MalcolmBaldrigeNationalQalityAward)。
六西格玛使摩托罗拉有力地推动了在当时看来几乎是不可能的改进目标:
初始目标是在20世纪90年代的初期同五年时间实现10倍的改进,而后每两年实现10倍改进,即在四年里改进100倍。
从六西格玛开始的1987—1997年的10年时间里,销售额增长了5倍,利润每年攀升将近20%,有六西格玛努力产生的累计节约额达140亿美元,其股价平均每年上涨21.3%。
摩托罗拉应用六西格玛远远超出了一套工具范畴,而是把它当成了变革企业的方法,一种由沟通、培训、领导、团队、测量和关注客户所驱动的方法。
正如阿兰·拉森(AlanLarson)——一位摩托罗拉六西格玛项目的早期内部顾问(后来又在GE和联合信号(AlliedSignal)帮助推行六西格玛)所言:
“六西格玛确实是一种有关文化的事物——一种行为方式。
”
正是由于六西格玛管理方面创造性的先驱工作,使得摩托罗拉的名字永远与六西格玛联系在了一起。
1987年以来,在使顾客完全满意的目标之下,摩托罗拉就一直推动着六西格玛管理不断前行,而且追随者越来越多,极大地影响着全世界质量管理的发展进程。
继摩托罗拉之后,在1991年成为联合信号(AlliedSignal,1999年与霍尼韦尔(Honeywell)合并后改名为霍尼韦尔)CEO的拉里·博西迪(LarryBossidy),曾在GE任职多年,将六西格玛引入了联合信号,并取得了辉煌的业绩。
正是博西迪和联合信号公司,华尔街第一次听说了六西格玛管理,最终促使杰克·韦尔奇(JackF.Welch)将六西格玛引入了通用电气公司(GeneralElectric,GE),从而真正地把六西格玛管理这一有效的质量管理战略变成管理哲学和实践方法,形成一种企业文化,创造了更大的奇迹。
联合信号在20世纪90年代就开始六西格玛,到1999年,年节约金额超过了6亿美金,公司的市值(到1998年财政年度为止)综合起来以每年27%的速度攀升。
联合信号在六西格玛方面的领导能力使它赢得了世界上最具多样化和最受尊敬的全球航空公司的盛誉(见《福布斯》全球版和《财富》)。
真正使六西格玛发扬光大的是杰克·韦尔奇(JackF.Welch)领导下的GE(通用电气)。
拉里·博西迪把六西格玛管理的理念介绍给了通用电气前任CEO杰克·韦尔奇(JackF.Welch)。
1995年,韦尔奇开始十分坚定的在整个组织中推行六西格玛。
他描述GE致力于六西格玛如同“发了狂”,GE也在其最“狂热”的CEO的推动下成为最成功实施六西格玛管理的企业。
通用电气自1995年引入六西格玛管理以来,六西格玛项目从1996年的3000个上升到1997年的6000个,并且实现了3.2亿美元的收益,比韦尔奇原先设定的1.5亿美元的目标翻了一倍多。
到了1998年,由于六西格玛质量改进项目而产生的直接收益,超过7.5亿美元,远远高于通用电气在六西格玛质量行动上的投入。
由于六西格玛的作用,通用电气营销利润率从1996年的14.8%上升到2000年的18.9%。
六西格玛管理方法的成功还体现于效益增长速度的不断加快。
通用电气在实施六西格玛管理后,1998年年底的获得的收益是7.5亿美元,1999年是15亿美元左右,分析家认为到2010年前公司的收益将会达到50亿美元。
通用电气的管理层认为,企业效益的扩张就是六西格玛管理对公司财务贡献的证明:
1996年,支出是2亿美元,回报为1.7亿美元;1997年,支出是3亿美元,回报是6亿美元;1998年,支出是4亿美元,回报却高达10亿美元。
在通用电气应用六西格玛取得了巨大成功之后,六西格玛为全世界认识并接受,很多企业开始推行六西格玛管理。
从此,六西格玛的理念和方法犹如旋风般迅速传遍全球。
财富500强企业都纷纷开始实施六西格玛管理战略。
从制造业到非制造业,掀起了一场开展六西格玛质量管理运动的热潮。
可以说六西格玛己经使GE有了质的改变,它已经融入在每个GE员工的血液里,使得每做一件事情、每设计一件产品等等所有方面,都会使用六西格玛。
杰克·韦尔奇说:
“六西格玛永远地改变了GE。
每一个人——从黑带之旅涌现出来的六西格玛狂热者到工程师、审计员和科学家,以及把公司领向新环境的高层领导者——都是六西格玛的忠实信徒。
六西格玛是公司的工作方式。
”
除了这些特别醒目的公司在推行六西格玛并将六西格玛融入到他们的战略中去,现在加入六西格玛阵营的除了制造型企业以外,还有其他服务性组织,甚至可以说是几乎所有行业都适用六西格玛。
几乎所有的财富500强的企业以及其他服务性组织都陆续开始实施六西格玛管理战略。
这些企业包括ABB(AseaBrownBoveri)、白得(Black﹠Decker)、庞巴迪(Bombardier)、杜邦(Dupont)、陶氏化学公司(DowChemical)、联邦速递(FederalExpress)、强生(Johnson﹠Johnson)、柯达(在21世纪早期实现了8500万美元的节约)、鑫星(Navistar)、宝丽来(Polaroid)、希捷科技(SeagateTechnologies)、希比(SiebeApplianceControls)、索尼(Sony)、东芝(Toshiba)、飞利浦(Philips)、诺基亚(Nokia)、三星(SamsungElectronics)、艾博特实验室(AbbottLabs)、好事达保险(Allstate)、唐纳利物流(DonnelleyLogistics)、花期银行(Citicorp)、美国宇航局(NASA)、园景医院(ParkviewHospital)、美国陆军(UnitedStatesArmy)、五角大楼(Pentagon)等组织纷纷加入六西格玛阵营。
在这些组织的推进下,也显现出了很好的效果。
美国ASO、韩国KSA等组织也在推行六西格玛的过程中,起了巨大的推动作用。
很多咨询公司也开始跨国界的交流,六西格玛文化正在逐渐的铺展开来。
虽然成功实施六西格玛的企业很多,但品尝到失败苦果的企业也不在少数,有部分企业未达到预期的愿景:
流程没得到改善,质量没得到提高,成本没得到有效控制,更恐怖的是财务数据更糟糕了。
(2)国内六西格玛管理的实践
中国企业实施六西格玛主要还是由于受GE公司的巨大成功的吸引。
最近几年,由于一些相关书籍(其中由潘迪(Pande,P.S.)、纽曼(NeumanR.P.)、卡瓦纳(Cavanagh,R.R.)著,马钦海,陈桂云译的《六西格玛管理法:
世界顶级企业追求卓越之道》是我国引进的第一本六西格玛管理法经典图书),尤其是《杰克·韦尔奇自传》的出版,使众多读者得知,韦尔奇是如何看重六西格玛管理,六西格玛管理的威力又是如何神奇,一时间,不少中国企业的管理者如获至宝。
从2000年开始,中国的一些大型企业先后尝试了这个先进的管理方法,如:
宝钢、中兴通讯、哈飞、中远、TCL、美的、中航一集团、太钢等。
据不完全统计,国内目前推进六西格玛管理的企业已经超过500家(包括在华独资及合资企业)。
上海质量管理科学研究院所属上海朱兰质量研究院是美国朱兰研究院(JuranInstitute)在中国设立的合作机构,该院从1998年开始跟踪和研究六西格玛理论与应用,并已对几十个企业进行咨询指导。
2001年,美国六西格玛培训和咨询公司(SBTI)与中青创新企业管理研究院合作,在北京正式推出六西格玛“黑带”的认证培训,把六西格玛的整套咨询和培训计划引进到中国和亚洲地区。
中国企业实施六西格玛管理也得到了政府的大力支持。
2001年8月24日,在国家经贸委、中国质量管理协会支持下,三家在中国从事六西格玛管理教育、咨询和实施的机构(中青创新企业管理研究院、北京普罗维智资讯有限公司、中航科技质量技术中心)在北京举办了第一届高层研讨会,主题是:
六西格玛管理与中国企业的国际竞争力。
引入先进的六西格玛管理正式被提上议事日程,促使国内企业积极引入六西格玛管理提升自身竞争力。
2002年9月在北京召开的“第八届亚太质量组织论坛”,六西格玛管理成为中外质量管理专家讨论的热点话题。
会议期间(2002年9月16日),发起成立了中国质协“全国六西格玛管理推进委员会”,这标志着中国质协六西格玛推进工作正式启动,今后将致力于研究六西格玛理论,指导企业实践,以提高企业的竞争力。
这预示着六西格玛将植根于中国的企业,六西格玛将为中国企业带来巨大的冲击和发展动力。
2003年7月,中国质量协会向所属会员企业发出通知,中国质量协会将全面推进六西格玛管理工作,引导和帮助企业开展六西格玛管理。
在大型企业中实施六西格玛管理、具有多年实践经验的六西格玛国际学院(SII,sixsigmaInternationalInstitute)致力于在全球推广六西格玛管理方法与战略实践,旨在通过提供专业的六西格玛咨询服务和卓越的管理培训,帮助企业学员掌握六西格玛精髓,为企业培养一流的高级管理人员,提升国际竞争力,由该院主持的六西格玛培训工作也相继在我国陆续展开。
从目前我国企业推行六西格玛的情况来看,绝大部分实施六西格玛的企业是有外资背景的外企或其供应商、客户企业。
大体上有这样几种类型:
一是通用电气(GE)、摩托罗拉(Motorola)等跨国公司的中国公司,直接从总部移植过来开展六西格玛活动:
二是国内合资、独资的公司,在顾问公司的指导下开展六西格玛管理;三是公司招聘或培训六西格玛管理专业人员,自行组织六西格玛管理活动;四是虽然没有明确开展六西格玛管理,但是在经营管理中根据六西格玛管理的理念、方法开展质量经济性管理活动。
(3)开展六西格玛管理三个基本的途径
由于我国开展六西格玛管理的企业一般都有一定的管理基础,如已经取得IS09000质量管理体系认证,或者有着国外的合作背景等等。
伴随着我国加入WTO和经济全球化的发展,六西格玛管理会进一步受到广大企业的关注。
如何确保六西格玛管理的有效进行,结合我国的实践,我们认为把六西格玛管理看成是帮助企业走向一个新的更美好的未来之路,这条道路有三个“途径”。
开展六西格玛管理三个基本的途径:
途径一:
业务变革
途径二:
战略改进
途径三:
解决问题
每个途径都会有不同的方法或路线,可能会带到不同的目的地。
组织所选的路线会决定六西格玛管理对组织和员工带来影响的广度和深度。
企业所要选择的方法或者是六西格玛管理开展的深度,取决于哪种方法最适合企业。
每种途径和方法都有它的好处和风险。
如果企业采取的是“业务变革”方法,那么有望在儿个月之内看到迅速的变化和一些重大改进。
另一方面,可能会出现很明显混乱的场面,对控制时间和人员都是个很大的挑战。
“战略改进”可以帮助企业把重点放在高度优先的问题上,并且限制了管理变革和使整个企业接受变革所带来的挑战。
然而,这种方法可能会让一些人觉得被冷落在改进过程之外,管理人员也很难把企业中正在做六西格玛管理的部门与不做六西格玛管理的部门统一起来。
“解决问题”相对力度最小,能使企业对六西格玛管理如何起作用有个感性认识。
但是,这种方法也是有不小风险的,不能解决企业的潜在问题,不能对如何获得成功有个全局性的认识。
最重要的是,不管企业采取哪种途径和方法,都要把它做好。
(4)国内推广六西格玛管理遇到的问题
中国已经具备了一个很好的推广六西格玛管理的氛围,但至今还未出现象通用电气、韩国三星这样的实施六西格玛的标志性企业。
国内推行六西格玛与国外一些情况类似,也是存在一些共性的问题。
比如:
中国企业总体管理水平不高;数据信息管理、过程管理等基础管理薄弱;对六西格玛管理法的认识程度不够;先期培训不充分,对六西格玛管理技术方法掌握不佳;中国传统文化与六西格玛管理文化存在冲突;财力有限等。
小结
六西格玛的产生与发展已经极大地推动了质量经济的发展,六西格玛逐渐从一种质量统计方法变成了一个高度有效的企业流程设计、改造和优化技术,继而成为世界上追求管理卓越的企业最为重要的战略举措。
其思想是对顾客真正的关注;由数据和事实驱动:
对流程的关注,管理和提高;系统的观点和无边界的合作;对完美的渴求和对失败的容忍。
六西格玛有两种方法:
改进类DMAIC和设计类DMADV。
六西格玛DMAIC法五个步骤:
定义阶段,确定问题,建立函数关系式;测量阶段,收集收据,找出变动源;分析阶段,选择合适的工具,确定关键问题源X;改进阶段,确定并实施项目改善方案:
控制阶段,通过控制图检测改善后过程,使问题不重复发生。
在实施六西格玛过程中需要使用相关工具,如过程流程图,因果(鱼骨)图,头脑风暴法等。
同时还可结合使用DOE(实验设计),MSA(测量系统分析),TRIZ理论等。
参考文献
[1]G.J.Hahn,N.Doganaksoy,andR.Hoed.TheEvolutionofSixSigma.QualityEngineering.2000,12(3):
317-326.
[2]G.H.Watson.SixSigma:
AnEvolvingStageintheMaturityofQuality,(T.Conti,Y.Kondo,G.H.Watson,Editors)Qualityintothe21thCentury.ASQQualityPress.MilwaukeeWisconsin,2003.
[3]何桢.六西格玛项目综合评价方法研究[J].生产力研究,2007,12:
115-116.
[4]刘毅.企业推行六西格玛活动的自我评鉴[J].市场周刊·理论研究,2007,4.
[5]陈永清.六西格玛实施关键成功因素及其评价分析[J].企业天地,2007,
(1):
154-155.
[6]赵骁耘、莳苹.推进六西格玛的成功经验[J].上海质量,2004,
(1).
[7]胡桂林.实施六西格玛管理的必备要素[J].企业改革与管理,2005,(9):
18-19.
[8]刘欢.制造型企业实施六西格玛关键成功因素与实证分析[D].南京:
南京理工大学,2007.
[9]何晓群.六西格玛及其导入指南[M].北京:
中国人民大学出版社,2003.
[10]唐晓芬.质量竞争力[M].北京:
中国标准出版社,2006.128-134.
[11]朱兰·朱兰质量手册[M].焦叔斌译.北京:
中国人民大学出版社,2003
[12]周延虎,何桢,高雪峰.精益生产与六西格玛管理的对比与整合[J].工业工程,2006(6):
1-4
第二部分:
质量管理与可靠性课程设计
1、课程设计的性质、目的和任务
《质量管理》课程是工业工程专业的主干课程之一,通过本课程的学习,学生不仅要求掌握基本的质量理论、质量管理的基本内容和基本方法,还必须具有较强的质量管理理论水平和较高的质量意识,能够参与企业开展质量宣传、贯彻GB/T9000-ISO9000:
2000标准以及参与企业质量认证的工作能力。
因此,《质量管理》课设的目的就在于使学生在学习了《质量管理与可靠性》课程的基础理论之后,能把该课程的一些基本知识应用到实践中去,使理论和实践紧密的结合起来,培养和锻炼学生深入企业调查研究的实际工作能力、分析问题的能力、解决问题的能力,为培养应用性人才作出努力。
2、课程设计的内容和要求
(一)内容
课程设计开始后,同学们可针对下列课题进行课程设计:
1、做一篇质量管理课题相关的专题性文献综述:
查阅质量管理方面的各个研究方向的专题学术论文。
对该方向的研究方法,发展趋势综合性的论述
2、进行质量控制方面的课程设计:
重点联系排列图、因果图、对策表、直方图、控制图、工序能力分析等在质量控制中的应用方法,培养学生能够合理运用质量控制方法解决设计工程问题的能力。
(二)要求
1.查阅10篇以上文献资料,认真阅读文献资料;
2.撰写质量管理专题文献综述,并提出自己的观点;
3.在文献综述中要说明生产实际中这些质量管理方法的运用场合;
4.认真阅读《工业工程专业课程设计指导书》按照指导书上的例题,根据给定的课题做好相应的图表,并仔细分析产生质量问题的原因找出改进的措施。
3、设计题目
罗茨鼓风机机壳的加工质量一直困扰着产品装配精度的提高。
质量控制小组对整个机壳加工工艺流程进行了分析,该零件的加工工艺流程:
铸造——清砂——退火消除内应力——划线——机壳上半部/下半部粗铣结合面——钻绞结合面螺纹孔——组合装配——划线——铣削机壳底部(定位面)——粗铣、精铣两侧面——粗镗内孔——精镗内孔——钻孔、扩孔——去毛刺——检验。
为了寻找出现废品的原因,对3500件零件各加工工序的一次合格率进行测试,一分析那些工序是影响质量的主要因素;哪些是次要因素,这样对有利于找出问题的主要环节。
对机壳加工工序的一次合格率测试数据见下表。
表5罗茨鼓风机机壳质量缺陷表
序号
工序名称
测试数/件
合格数/件
合格率(%)
不合格品数/件
1
铸造
3500
3245
92.71%
255
2
清砂
1200
1115
92.92%
85
3
退火消除内应力
3500
2795
79.86%
705
4
划线
2600
2236
86.00%
364
5
机壳上半部/下半部粗铣结合面
1600
1460
91.25%
140
6
钻绞结合面螺纹孔
650
640
98.46%
10
7
组合装配
50
49
98.00%
1
8
划线
750
740
98.67%
10
9
铣削机壳底部(定位面)
650
645
99.23%
5
10
粗铣、精铣两侧面