净化车间动态环境挑战验证方案4教材.docx
《净化车间动态环境挑战验证方案4教材.docx》由会员分享,可在线阅读,更多相关《净化车间动态环境挑战验证方案4教材.docx(11页珍藏版)》请在冰豆网上搜索。
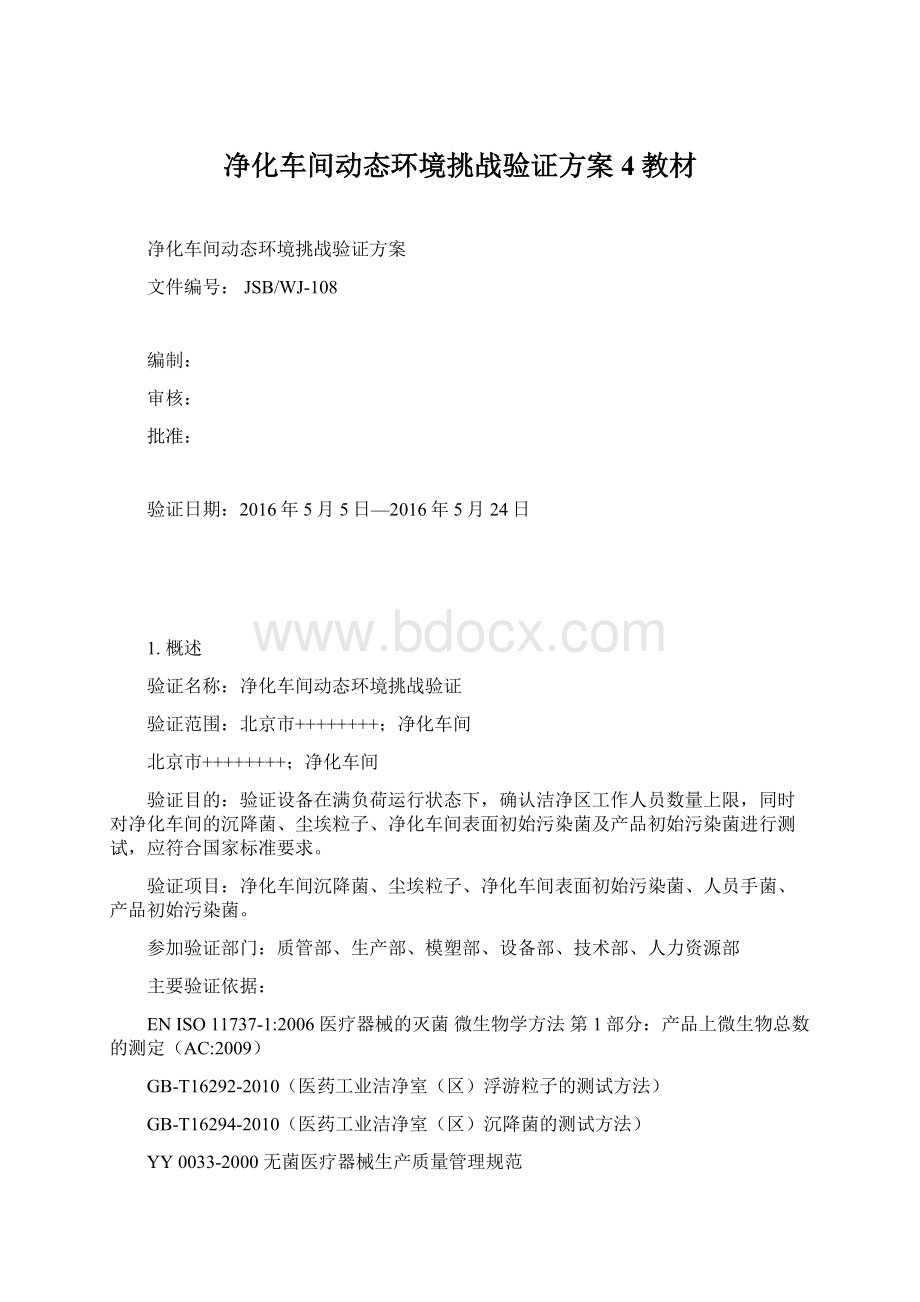
净化车间动态环境挑战验证方案4教材
净化车间动态环境挑战验证方案
文件编号:
JSB/WJ-108
编制:
审核:
批准:
验证日期:
2016年5月5日—2016年5月24日
1.概述
验证名称:
净化车间动态环境挑战验证
验证范围:
北京市++++++++;净化车间
北京市++++++++;净化车间
验证目的:
验证设备在满负荷运行状态下,确认洁净区工作人员数量上限,同时对净化车间的沉降菌、尘埃粒子、净化车间表面初始污染菌及产品初始污染菌进行测试,应符合国家标准要求。
验证项目:
净化车间沉降菌、尘埃粒子、净化车间表面初始污染菌、人员手菌、产品初始污染菌。
参加验证部门:
质管部、生产部、模塑部、设备部、技术部、人力资源部
主要验证依据:
ENISO11737-1:
2006医疗器械的灭菌微生物学方法第1部分:
产品上微生物总数的测定(AC:
2009)
GB-T16292-2010(医药工业洁净室(区)浮游粒子的测试方法)
GB-T16294-2010(医药工业洁净室(区)沉降菌的测试方法)
YY0033-2000无菌医疗器械生产质量管理规范
GB50073-2013洁净厂房设计规范
2015版《中国药典》
2.验证小组的构成及人员职责
2.1验证小组职责
负责制定验证方案,并进行审核
负责验证的实施、协调,保证本验证方案按规定项目顺利实施
负责收集各项验证、试验记录,对验证、试验记录的审核
2.2设备部
负责管理净化车间换风等日常操作
负责仪器、仪表的校正
负责配合完成验证工作
2.3技术部
负责验证方案的起草,负责验证数据收集和整理报告
2.4质管部
负责净化车间沉降菌、尘埃粒子、净化车间表面初始污染菌、人员手菌、产品初始污染菌的检测。
2.5生产部
负责配合验证及人员控制
2.6人力资源部
负责验证人员培训及相关人员培训档案归档
验证人员应经过该方案的培训,培训合格后方可进行相应的确认工作,具体验证培训见记录附表3。
3.验证实施
3.1验证用仪器设备
验证中所需要用到的仪器设备。
3.2净化车间确认
现净化车间面积及人员情况统计见下表
生产地址
净化车间名称
总面积(㎡)
设备及产品占用面积(㎡)
标准规定人数上限
生产工艺操作的最多人数
++++++++
生产车间1(十万级)
55
9
12
2
生产车间3(十万级)
135
45
25
30
生产车间4(十万级)
210
15
55
40
生产车间2(十万级)
130
15
32
20
中间库1(十万级)
45
20
7
4
中间库2(十万级)
175
120
15
12
精洗间(十万级)
20
0
5
3
裁切间(十万级)
45
3
12
4
男二更
8
0
2
4
女二更
27
0
6
15
走廊、缓冲走廊
35
0
8
8
++++++++
注塑车间(十万级)
1039
260
228
30
生产车间(十万级)
1087
260
258
100
中间库(十万级)
528
400
40
10
精洗间(十万级)
22.5
4
8
2
男二更(十万级)
34.2
9
9
9
女二更(十万级)
47.9
12
12
30
缓冲走廊(十万级)
32
21
21
21
3.3净化车间动态挑战性验证方法
3.3.1根据国家标准GB50073-2013《洁净厂房设计规范》的规定:
第4.2.5条根据不同的空气洁净度等级和工作人员数量,洁净厂房内人员净化用室和生活用室的建筑面积应合理确定。
第5.1.4条洁净室内应保证一定的新鲜空气量,其数值频取下列风量中的最大值;
一、乱流洁净室总送风量的10%~30%,层流洁净室总送风量的2~4%。
二、补偿室内排风和保持室内正压值所需的新鲜空气量。
三、保证室内每人每小时的新鲜空气量不小于40立方米。
注意:
第4.2.5条是指人员净化用室(如更衣室)和生活用室的面积参考值,而非指操作间。
另外第5.1.4条每人每小时送风量要求是用来根据人员数量计算送风量的,而不能反过来计算。
3.3.2《洁净厂房设计规范》GB50073-2013
计算公式
C级,房间高度按3米计算,换气次数取15次/小时,新风量取20%。
每人最低需要面积=40立方米÷20%÷15÷3米=4.44平方米,约为4.5㎡/人。
C级,房间高度按4米计算,换气次数取15次/小时,新风量取20%。
每人最低需要面积=40立方米÷20%÷15÷4米=3.33平方米,约为3.5㎡/人。
可以看出人均需要面积与于新风量、换气次数、房间高度均是反比关系,应根据净化车间具体的参数来确定各个房间的人数限制,在图纸设计时是根据工艺要求设计的各房间新风量、换气次数、房间高度、面积等参数。
上面计算出的人数是第一优先满足的(生产需要),然后确认完成工艺操作最少的人员,根据以上两点,且设备在全运行状态,来进行挑战试验。
是否应增加各车间人员的数量(查各个车间高度)
3.3.3实施方法
根据各净化车间现有人员密度可以看出净化车间人员聚集区通常为生产车间的组装区域,此区域为产品的工艺聚集区,因此所需人员较多,根据现有各车间密度,可以看出明显人员密度差异,由于每个厂区各车间所用空调换风系统为同一系统同时供应,不再将空调换风系统换风能力等进行挑战,对净化车间的最大人员密度进行挑战即可对各个净化车间人员数量上限进行有效确认。
根据现有车间各分车间面积及人员情况统计表,可以看出实际车间人数远小于国家规定的理论允许人数,根据我公司人员实际情况,为了使验证的合理性,做出以下设计。
3.3.3.1验证设计:
待洁净车间空调系统稳定运行1小时后,在各个车间依次进行所有试验项目,采样点按照均匀布点图进行。
首次测试以确认各个布点的风险区域,不做人员上限要求,均为日常人流、物流设计。
沉降菌检测时间设置为4小时。
3.3.3.2待第一次检测结果出来后,按照检测结果作为风险区域参考,在定义的风险区域内进行一次重复性实验,采样点按照风险区域布置图执行,重复性实验做挑战设计,环境以最大人流、物流进行,所有验证区域设备处于全开状态,最终确认各个风险区域布点位置的环境状态是否满足要求。
3.3.4人员在洁净区操作间生产操作时,按照《医药工业洁净室(区)尘埃粒子的测试方法》对尘埃粒子进行动态监测。
3.3.5按照《医药工业洁净室(区)沉降菌的测试方法》对沉降菌进行动态监测。
3.3.6关键操作完成后,按照棉签擦拭法或接触碟法对台面进行微生物监测。
3.3.7挑战环境:
1、++++++++厂区;以第一次测试结果,选择采样点菌落较多的点进行,以第一次结果做出危险区域布局图,新的布局图增加检测密度。
实验设计:
设备全运行状态(即所有工艺步骤同时生产)。
2、++++++++厂区;以第一次测试结果,选择采样点菌落较多的点进行,以第一次结果做出危险区域布局图,新的布局图增加检测密度。
对两个车间分别进行环境检测以验证其最高人员密度和最高设备密度的条件下,车间环境仍然符合要求,其它车间环境即可进行理论性对照。
3.3.8人数上限实验方法:
在全工艺生产情况下,按车间实际最大值增加5人进行最大人数值验证,当天对车间环境进行监测;如果出现不合格项,则每次单区域内减少5人作为人数上限值间隔(小于10人的净化车间每次减少2人),如果全部项目合格则确认车间实际最大值为人数上限。
4.微生物试验
4.1培养基及其制备方法
(1)大豆酪蛋白琼脂培养基(TSA)
大豆酪蛋白琼脂培养基,微热溶解,调节PH值使灭菌后为7.3±0.2,分装于三角瓶中,于压力蒸汽灭菌器内121℃灭菌30min。
冷却至约60℃,在无菌操作要求下倾注约20ml至无菌平皿(φ90mm)中,加盖后在室温放至凝固。
4.2可接受标准
4.2.1洁净区尘埃粒子限度(GB/T16292-2010)
洁净度级别
尘埃粒子最大允许数/立方米
≥0.5μm
≥5μm
10万级
3500000
20000
4.2.2洁净区空气微生物检测限度(GB/T16294-2010)
洁净度级别
沉降菌(φ90mm)静态30min
沉降菌(φ90mm)动态小于4h
10万级
≤10个/皿
≤100个/皿
4.2.3洁净区初始污染菌限度和人员手菌限度(GB15980)
洁净度级别
物体表面细菌总数
手菌
10万级
≤100cfu/100cm²
≤300cfu/每只手
4.2.4洁净区产品初始污染菌限度(产品技术要求)
洁净度级别
产品表面初始污染菌落总数
10万级
≤100cfu/件次
5.洁净室(区)采样点数目及位置图
5.1法规规定的采样点数目(GB/T16292-2010)
10万级洁净车间:
5.2洁净室采样点布置图(GB/T-16294-2010)
图1:
++++++++
图2:
++++++++
生产地址
净化车间名称
总面积(㎡)
设备及产品占用面积(㎡)
人员空间
采用点数量
++++++++
生产车间1(十万级)
55
9
46
2
生产车间3(十万级)
135
45
90
3
生产车间4(十万级)
210
15
195
6
生产车间2(十万级)
130
15
115
3
中间库(十万级)
45
20
25
2
中间库(十万级)
175
120
55
6
精洗间(十万级)
20
0
20
2
裁切间(十万级)
45
3
42
2
男二更(十万级)
8
0
8
2
女二更(十万级)
27
0
27
2
走廊、缓冲走廊(十万级)
35
0
35
2
++++++++
注塑车间(十万级)
1060
260
800
32
生产车间(十万级)
1165
260
905
32
中间库(十万级)
540
400
140
13
精洗间(十万级)
35
4
31
2
男二更(十万级)
36
9
27
2
女二更(十万级)
48
12
36
2
缓冲走廊(十万级)
85
21
64
2
6.验证结果确认
根据各检验项目验证的情况,对净化车间最大人员数量提供明确结论,详见净化车间动态环境挑战验证报告。
7.重新确认
设备、产品、车间环境发生改变会影响到生产环境,则应进行再确认。
其余每年进行一次再确认。