电镀故障.docx
《电镀故障.docx》由会员分享,可在线阅读,更多相关《电镀故障.docx(21页珍藏版)》请在冰豆网上搜索。
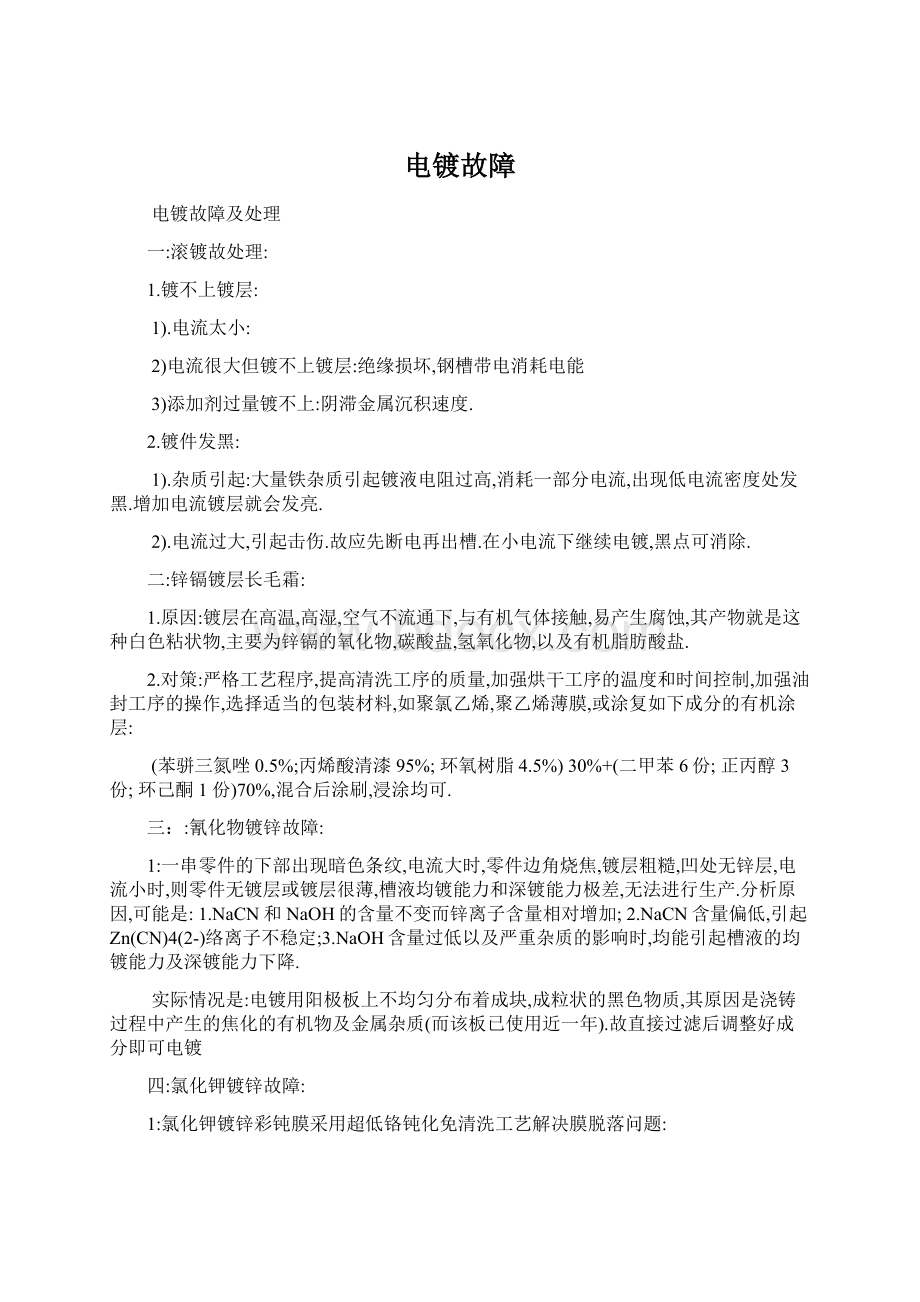
电镀故障
电镀故障及处理
一:
滚镀故处理:
1.镀不上镀层:
1).电流太小:
2)电流很大但镀不上镀层:
绝缘损坏,钢槽带电消耗电能
3)添加剂过量镀不上:
阴滞金属沉积速度.
2.镀件发黑:
1).杂质引起:
大量铁杂质引起镀液电阻过高,消耗一部分电流,出现低电流密度处发黑.增加电流镀层就会发亮.
2).电流过大,引起击伤.故应先断电再出槽.在小电流下继续电镀,黑点可消除.
二:
锌镉镀层长毛霜:
1.原因:
镀层在高温,高湿,空气不流通下,与有机气体接触,易产生腐蚀,其产物就是这种白色粘状物,主要为锌镉的氧化物,碳酸盐,氢氧化物,以及有机脂肪酸盐.
2.对策:
严格工艺程序,提高清洗工序的质量,加强烘干工序的温度和时间控制,加强油封工序的操作,选择适当的包装材料,如聚氯乙烯,聚乙烯薄膜,或涂复如下成分的有机涂层:
(苯骈三氮唑0.5%;丙烯酸清漆95%;环氧树脂4.5%)30%+(二甲苯6份;正丙醇3份;环己酮1份)70%,混合后涂刷,浸涂均可.
三:
:
氰化物镀锌故障:
1:
一串零件的下部出现暗色条纹,电流大时,零件边角烧焦,镀层粗糙,凹处无锌层,电流小时,则零件无镀层或镀层很薄,槽液均镀能力和深镀能力极差,无法进行生产.分析原因,可能是:
1.NaCN和NaOH的含量不变而锌离子含量相对增加;2.NaCN含量偏低,引起Zn(CN)4(2-)络离子不稳定;3.NaOH含量过低以及严重杂质的影响时,均能引起槽液的均镀能力及深镀能力下降.
实际情况是:
电镀用阳极板上不均匀分布着成块,成粒状的黑色物质,其原因是浇铸过程中产生的焦化的有机物及金属杂质(而该板已使用近一年).故直接过滤后调整好成分即可电镀
四:
氯化钾镀锌故障:
1:
氯化钾镀锌彩钝膜采用超低铬钝化免清洗工艺解决膜脱落问题:
氯化钾镀锌属单盐体系,镀液中无铬合物存在,靠添加多种有机物的组合添加剂来增加阴极极化,镀层中有不同程度的有机物夹杂.镀液的整平性能远远优于锌酸盐或铵盐镀锌,镀层表面很光滑整,故钝化膜的附着力较差.一般脱膜处的膜层较其余部分厚,膜层疏松结合力差.因此,减慢成膜速度,让膜层厚度适中且均匀是关键.工件上残留的钝化液在干燥过程中继续慢慢钝化,可使工件在钝化液中停留时间缩短,且膜层厚度均匀,结合力增加.
配方:
CrO31-2g/L;HNO32-3ml/L;H2SO40.3-0.4ml/L;CH3COOH3-5ml/L;KMnO40.1-0.5g/L;PH=1-1.5;15-25s
注意:
钝化时一出现金黄色即可,在十燥过程中逐渐出现彩虹色.不可将色泽钝得过深,否则膜厚面无光也易脱落.钝化出槽后最好进行甩干再烘烤,尽量减少残留钝化液痕迹.使用一段时间后钝化时间延长可补充铬酐0.5-1g/L,光泽度差时可适量补充硝酸.仍差时可另配新液.
2镀液中铁离子的去除(电镀与环保92.1):
少量铁离子在镀液中影响不大,但积累到1g/L以上时,会恶化镀层质量。
镀液中多量的铁离子杂质会使镀液浑浊变黄,甚至泛红,降低均镀能力和深镀能力,使镀层明显变暗.使用锌粉置换法效果不大.可用化学法处理:
加双氧水将二价铁氧化成三价铁,再加烧碱调PH6.2(有条件加热到60℃可防止提高PH值时生成氢氧化铁沉淀),过滤.如只有铁杂质,也可用柠檬酸掩蔽.柠檬酸和镀液中的铁离子能形成一种可溶性的络合物,即生成淡绿色的,透明清澈的柠檬酸铁络合物.它会使镀液中三价铁离子还原为二价铁离子,通过电镀沉积到镀层中,可防氢氧化铁析出,防镀液浑浊.有些配方中已加入50g/L柠檬酸钾以改善分散能力和深镀能力.
3:
镀锌钝化不合格返修:
可示重新电镀,而经过下述工序:
退膜(10%NaOH)----水洗----出光----钝化
对低铬钝化:
退膜(10%硫酸)---水洗---出光---钝化.(退膜时间不可过长:
表面发黑即可)
4:
铸铁镀锌:
高温除碳----喷砂----酸洗----混合酸洗-------
五:
锌酸盐镀锌
1.镀锌后放置一夜(或更长)后会出现雨点状白点,大小不一,时间越长越明显.产品表面钝化膜变暗变淡,失去原有光洁度.分析原因,可能是:
1).镀液问题(加锌粉,硫化钠处理杂质,再电解处理数小时,按正常添加光亮剂).2)前处理不良.3)原材料有麻点,导致镀后清洗不良(变一次清洗为两次清洗);4).钝化液问题;5).生产环境差,有污染;6)老化不够.对此一一改进,仍未能解决问题.实际原因为钝化后热水洗时水温达到75℃.水温超过60度时,膜中的六价铬溶解,造成抗蚀性很差的多孔性钝化膜.水温较高,六价铬的溶解范围扩大,就会出现雨点白点.若水温再高,钝化膜将会脱落.故热水槽温度不能超过65℃.
2.30CrMnSi基材镀锌(防止镀层起泡):
汽油洗--阳极电解去油--热水洗--冷水洗--强腐蚀(盐酸100-200g/L;乌洛托品1-3g/L)--冷水洗--阳极电解去残渣(1-3分钟)--热水洗--冷水洗--弱腐蚀(盐酸(工业级)50-100g/L;氢氟酸(工业级)50-80ml/L)--冷水洗--中和(NaOH20-30g/L)--镀锌--冷水洗--热水洗--吹干--去氢(195℃/4h)--硝酸出光(1-3%)--冷水洗--钝化--回收--二级逆流漂洗--热水洗(60-80℃).
弱腐蚀为关键工序.因基材中有Si,Mn,Cr等较易氧化的元素,如不在氢氟酸中弱腐蚀,活化,则锌层结合力受到影响.结合力不良的镀层因受光亮剂的内应力和零件析氢的作用,未去氢的零件在存放中起小泡,或去氢过程中起小泡.
3.DE型碱性锌酸盐镀锌,发现钝化膜发花,表面有许多大块不规则的灰黑色斑块(滴稀盐酸在该处产生大量气体说明已镀上锌).观察发现镀锌后的清洗槽中白色絮状物较多,出光槽液呈红棕色,测出光液的PH近4.其产生原因是镀后没仔细清洗,镀锌零件受到碱液的腐蚀而变黑.而出光液的PH太高,中和作用和出光作用弱,不能有效的去除锌层表面的腐蚀产物,在被腐蚀折锌层表面上不能生成良好的钝化膜.
4.盲孔内螺纹镀锌:
试图用提高氢氧化钠含量,降低锌离子含量,提高电流密度来提高分散能力和深镀能力,效果不明显.最后采用提高镀液浓度的办法来提高阴极电流密度范围,解决了问题:
氢氧化钠220g/L;氧化锌30g/L;DE添加剂5ml/L;香草醛0.15g/L;电流增大了50%.
5.弹性零件镀锌(电镀与环保92.2)机械除油---绕制---化学除油(电解除油采用阳极除油)--镀前第2次回火处理(320-370℃)---酸洗(一般盐酸酸洗2分钟)---电镀.
电镀时应注意:
漂洗时不能在水中停留过久,防止脆性增加.电镀开始时采用比正常值大2-3倍的电流冲击0.5-1分钟后再降到允许Dk的下限进行电镀,减少过大Dk引起的渗氢量.采用阴极移动,在工艺范围内适当提高槽温,降低浓差极化和电化学极化,提高电流效率,减少渗氢量.严格控制DE添加剂及光亮剂的添加量:
DE比常规少1/3左右,香草醛少1/4.
6.酒石酸处理镀锌层发花(钝化膜表面有分散性的片状兰膜)(电镀与环保91.2):
酒石酸实际上是多种金属的络合剂,能络合镀锌液中的多种金属杂质,同时对锌离子也起络合作用,加入镀锌液中并无害处.加入后可立即解决题.如用硫化钠处理需配合较长时间的电解,再经较长时间生产后发花兰膜才逐渐减少.
7.(电95.5)门窗插销两端底部镀不上.以前是铜,铅杂质过多,而两端底部表面粗糙较难沉积锌,故前处理滚光也无法解决,用锌粉处理后解决.本次是因镀液中含锌量低(一般资料要求阳极:
阴极为2-3:
1,而滚镀显然无法达到.当阳极钝化后,势必消耗镀液中锌离子),锌含量低会引起两端更难沉积锌.但经过一昼夜的自然溶液,矛盾可缓解.本次处理为加氧化锌2克/升.
六:
电镀镍液中金属杂质影响及去除:
1.铜杂质:
1.1.影响:
当镀镍液中铜离子含量达5mg/L以上,钢铁及锌压铸件电镀时就会产生置换铜,造成结合力不良,特别在电流中断及低电流密度区最易发生.铜杂质往往使低电流密度区镀层外观呈灰色,甚至黑色.常常出现粗糙,疏松,呈海绵状等不良镀层.
1.2.鉴别:
取镀液2ml,加2mol/LH2SO4使溶液呈酸性,再加1mol/LK4[Fe(CN)6]2ml;如产生沉淀[Cu2[Fe(CN)6],此沉淀溶于氨水呈现兰色,示有Cu2+存在.生产中简单方法是用稀硫酸调PH2-3;浸入用HCl活化处理过的钢丝,约3-5分钟取出,观察有否红色置换铜.
1.3.去除:
A.电解法:
0.2-0.4A/dm2,如激烈搅拌可用稍大电流密度.阴极有瓦楞形铁板.
B.化学药剂法:
用仅对铜离子有选择性沉淀的药剂去除,如加入铜含量(摩尔)2倍左右喹啉酸,可使铜含量下降到1mg/L以下.也可加入亚铁氰化钾,2-巯基苯并噻唑生成沉淀后过滤.如要生成氢氧化铜沉淀不合理,因需要调PH=6.3,会有相当多的氢氧镍沉淀生成.
2.锌杂质:
2.1:
影响:
光亮镀镍溶液中如如含微量锌所得镀层呈白色,如含量再提高,低电流密度处呈灰黑色,镀层呈现条纹状.在PH较高镀液中,由于锌的存在还会使镀层出现针孔.锌允许极限因光亮剂不同而异,一般在20-100mg/L范围内.
2.2:
鉴别:
取2ml镀液加于试管中,加蒸馏水30ml;1%甲基紫1滴,1:
1HCl2滴.15%KCNS1滴,若镀液变紫,示有锌.或取2ml镀液加于试管中,调PH至石蕊试纸呈中性,再加CH3COOH1-2滴及0.5mol/LK3[Fe(CN)6]1ml.此时如有黄棕色沉淀,且该沉淀溶于HCl及氨水中,示有Zn2+存在.
2.3:
去除:
A:
电解法:
当Zn2+较低时用瓦楞形铁板作阴极,搅拌下:
0.2--0.4A/dm2
B.当Zn2+较高时用化学沉淀法.用稀NaOH或CaCO3(优于烧碱)将电镀液调PH6.2;加热至於5-70℃,搅拌1-2h,再调PH稳定在6.2;静置4h以上,过滤,除Zn(OH)2及CaCO3沉淀(本法镍盐损失较大)
3.铅杂质:
3.1:
影响:
类似于铬杂质对镀层质量影响.当镀液中达5mg/L以上时,得到灰色甚至黑色镀层,镀层粗糙,甚至无镀层.
3.2鉴别:
取2ml镀液加于试管中,调PH至石蕊试纸呈中性,加1mol/LK2CrO41-2滴.如有黄色沉淀,将此沉淀溶于NaOH中,通入H2S或加入(NH4)2S.如试液中有Pb2+,可出现黑色PbS沉淀.
3.3去除:
低电流密度电解除去.
4.铁杂质:
4.1:
影响:
铁是镀镍液中最主要的杂质,主要是零件未及时捞出或未镀上锌的部位溶解而成.二价铁可以和镍共沉积.当镀液中PH在3.5以上时,此时阴极区PH更高,三价铁可形成Fe(OH)3,并夹杂于镀层中,使镀层发脆,粗糙,是形成斑点及针孔主要原因.一般铁杂质在较高PH溶液中,应在0.03g/L以下,PH较低时不超过0.05g/L.
4.2鉴别:
取2ml镀液加于试管中,加2mol/L硫酸使之呈明显酸性,然后再多加2-3滴,加入亚铁氰化钾K4[Fe(CN)6].3H2O2-3滴,如有Fe2+则生成亚铁氰化钾兰色沉淀.或取2ml镀液加于250ml烧杯中,加蒸馏水20ml,加1:
1HNO3,煮沸,冷却后加KCNS或NH4CNS(约15%)数滴,摇匀静置,此时出现红色溶液,示有Fe3+.如在此溶液中和加NH4F或KF后,颜色消失.
Fe3++3CNS-=Fe(CNS)3;Fe(CNS)3+F-=[FeF6]3-6+3CNS-
4.3去除:
A.电解法:
0.4A/dm2
B.化学法:
:
稀硫酸调PH3左右,加30%H2O20.5-1mol/L,加热65-70℃,使Fe2+转化为Fe3+并除去多余的H2O2,用BaCO3或NiCO3,Ba(OH)2调PH至6,搅拌2h,重复调PH,使之稳定在6,静置过滤.当处理铁杂质同时,还要除去有机物杂质,可在加入H2O2及升温后,加入活性炭2-4g/L.
5.铬杂质:
5.1影响:
铬是镀镍液中最敏感的金属元素之一,主要来自镀铬件清洗及镀铬时铬雾扩散.微量铬的存在,使镀液分散能力,电流效率降低,镀层发灰,结合力下降.当六价铬含量达到3-5ml/L时,在低电流密度区镍层难以沉积,如含量达到5ml/L以上时,就会使镀层产生条纹,引起镀层剥落.在低电流密度处无镀层.三价铬在PH3.5以上就会产生沉淀,使镀镍层粗糙.
5.2鉴别:
取2ml镀液加于试管中,加3mol/LNaOH至偏碱性,加H2O2(30%)2-3滴,加热至沸,有铬存在则变成黄色溶液,冷至室温,用1mol/L硫酸酸化至酸性,加乙醚3-5滴,再慢慢滴加H2O2,同时摇动试管,乙醚层有兰色出现,则有Cr6+存在.
酸性溶液中Cr2O72-占优势,在碱性溶液中CrO42-占优势,通过调PH使之相互转化.在酸性溶液中Cr2O72-是强氧化剂,此时加H2O2则Cr6+被还原成Cr3+而出现兰色.
5.3去除:
将六价铬还原成三价铬,然后用化学沉淀法去除
A.连二亚硫酸钠(保险粉)法:
2H2CrO4+Na2S2O4+H2SO4=Na2SO4+Cr2(SO4)3+4H2O
Cr2(SO4)3+6NaOH=Cr(OH)3↓+3Na2SO4
稀硫酸调PH至3,再按0.2-0.4g/L量加入保险粉,加热60-70℃,搅拌1h;用稀NaOH或Ba(OH)2,也可用NiCO3或BaCO3调PH,使其稳定在6.2;静置2-3h,过滤.最后按0.2-0.4mol/L量加入H2O2(30%)以除去过量保险粉,调PH至工艺规范,试镀.
B.硫酸亚铁法:
六价铬被还原成三价铬,二价铬被氧化成三价铬,提高PH值,分别生成Fe(OH)3或Cr(OH)3沉淀,加入H2O2,使多余二价铁氧化成三价铁
H2Cr2O7+6FeSO4+6H2SO4=Cr(SO4)3+3Fe(SO4)3+7H2O
稀硫酸调PH3,按1g/L加入FeSO4,搅拌1h;加入H2O2(30%)1mol/L,调PH值至6.2,加热60-70℃,并保温4h(目的是便于沉淀,凝聚),搅拌,重复调PH使之稳定在6.2,静置2-3h,过滤,最后用硫酸调PH至正常.
C.高锰酸钾法:
调PH=3,加热至60℃,加高锰酸钾(10%)至呈紫色,加2-6g/L碳酸铅(醋酸铅),搅拌,用NaOH调PH=5-5.5,静置2h,过滤.
6.硝酸根:
因硫酸镍不纯而带入,对镀镍极有害.微量的硝酸根可使镀层三灰色,脆性增大.当含量达0.2g/L以上,镀层呈黑色,阴极电流效率显著下降.去除原理:
高电流密度时,硝酸根在阴极还原为铵(为避免镍的沉积可调PH=3).
7.(电镀与环保96.4)用碳酸钡调节PH,可不浪费镍盐.且过量也无妨,并能得到一个合适的PH值上限(PH5.5),在此条件下铁铝等杂质可完全除去.而Ni2+尚未达到沉淀的PH值范围.溶液的PH值勤升高至5.5,碳酸钡过量也不再升高.碳酸钡进入镀镍液后生成白色BaSO4沉淀(溶解度极低,且易过滤)和逸出CO2气体.但用碳酸钡净化液体不易除去铜,锌等杂质.加为铜锌沉淀PH范围在6.3左右.故推荐净化工艺如下:
用稀硫酸调PH3左右.搅拌下加3ml/L30%H2O2,加热65-70℃,使Fe2+转化为Fe3+并除去多余的H2O2.将6-8g/L粉未状BaCO3分3次加入,搅拌1h,待PH升至5.5时,铁铝杂质除去.再加入SQT去铜剂3g/L,搅拌1h,使铜锌杂质除去.将3g/L活性炭用水调成糊状后加入,搅拌1h,静置4h,过滤.调pH至正常,加工艺下限十二烷基硫酸钠和次级光亮剂以及1/2工艺量的糖精,试镀
8.(电92.4)当锌离子较多时采用NaOH和BaCO3提高PH,不能使锌离子彻底沉淀(试验表明在低Dk区仍有黑条,示用锌离子存在).采用NiCO3提高PH=6.2,效果较理想,镍盐损失较小.
9.(电91.6)亮镍镀液中误加乙二胺的处理:
采用电解法,过氧化氢氧化法,过氧化氢氧化-电解法,高锰酸钾氧化法,高锰酸钾氧化-电解法,过硫酸铵氧化-电解法,均不能解决.因胺类物质是一种较稳定的化合物,用一般氧化剂很难在低浓度下氧化掉.但它和亚硝酸盐有一个特殊反应:
在酸性介质中能被亚硝酸盐氧化为醇;同时亚硝酸盐在酸性介质中发生歧化反应生成亚硝酸根和一氧化氮(转化为红棕色的二氧化氮),并伴有PH值升高.生产中用硫酸调PH0.5,搅拌下加亚硝酸钠7克/升,瓦楞铁板作阴极,镍板作阳极,1.5-2A/dm2电解,达15小时安培电量后镀注液恢复正常,PH也由0.5升高到4.2左右.
七:
镀镍
1.镀镍光亮剂失调:
采用预镍,亮镍,镀铬工艺,配方为:
NiSO4250-300g/L;H3BO330-40g/L;NaCl15-20g/L;1,4丁炔二醇0.6-0.8g/L;糖精1.2-1.6g/L;十二烷基硫酸钠0.05-0.1g/L;PH4.2-4.8;50-60℃;8-10min;Dk2-4A/dm2.其故障为:
(1).1,4丁炔二醇失调:
亮镍层镀好后,尖端的高电流区黑亮,并带有蓝色,说明其失调.如按正常工艺套铬,则高电流区尖端烧焦,低电流区露黄.对这种现象,可调亮镍液的PH值.如PH值在4.8左右时,用试剂硫酸调至4.2以下,使1,4丁炔二醇失效,分解成其它的有机杂质.光亮剂失调镀出的件,在1:
1盐酸中浸蚀0.5h,然后清洗,活化套铬.
(2)糖精失调:
件从亮镍槽中取出时,平面上似呈灰白色,手感不滑,严重的有一簇一簇的蘑菇团,呈钝化状态.套铬时边缘高电流区发灰,低电流区彩虹,无铬层沉积.对此首先用回收液适当稀释镀液,再升温到70度左右,再加润湿剂0.02g/L,搅拌,然后用瓦楞铁板低电流电解2h,再冷却至正常温度,试镀.
(3).二种光亮剂同时失调:
一般亮镍层发蓝是由镀液温度太高而引起的.但二种光亮剂失调,亮镍层也是发蓝的.故判断时首先要测量温度,受镀时间等.发蓝的镀层不符质量要求,只好返工.对失调的亮镍镀液,先抽掉1/3,重新配制.抽出的亮镍液可作回收液添加.
2.光亮镍槽出现毛刺:
(电镀与环保92.5)其原因一般有如下几点:
1)前处理不净;2)电镀过程中电流密度过大,3)过滤系统出现故障,双氧水-活性炭处理后,槽液中残留粉未状活性炭;4)电解液PH值过高:
(A):
PH>4时易生成Fe(OH)3和Cr(OH)3沉淀;(B):
当PH>4.2时,十二烷基硫酸钠能与镍离子生成不溶性化合物而沉淀,它也能附在零件表面形成毛刺;(C)如PH>4,阴极附近还会出现碱式镍盐沉淀在阴极零件镀层中.
实际按以上处理镀液,并除去铁,铬等杂质而仍未解决问题.故考虑阴极扩散层中的PH值往往比主体镀液高出一个单位,且高出数值大小与Dk有关,Dk愈大,高出的数值愈大,故将Dk与PH值一起考虑,将PH控制在3-3.5,Dk在2-3A/dm2间,当Dk取上限时,PH取下限,毛刺消失
3.(电镀与环保95.4)镀亮镍时亮镍层灰暗不亮,分散能力差.调PH,适当提高Dk,不但镍层亮度未提高,分散能力也未能好转,同时发现析氢相当严重,试镀30分后工件内孔或低Dk区无镀层或镀层仍为灰暗色.分析认为可能是混入六价铬.故将工件放入盛有清水的槽内,蒸汽煮沸30分后发现己变黄色,证实是由六价铬引起的.调PH3;加NaHSO31g/L处理.
4.亮镍溶液中误加乙二胺后的处理:
在PH0.5时加NaNO27g/L,瓦楞铁板作阴极,镍板作阳极,1.5-2A/dm2电解,每升镀液中通过15A.h后镀液恢复正常,且PH由0.5上升到4.2左右.
5.铜基上镀镍层的退除:
硝酸8-10mol/L;唑类缓蚀剂20-30g/L.铜应用的缓蚀剂有:
疏基苯并噻唑,苯并三氮唑,苯并咪唑,乙基硫醇氨基苯并咪唑,疏基丙酸二烷基咪唑.
八:
酸性光亮镀铜阳极钝化的原因:
1.硫酸含量过高或过低:
低于50g/L时分散能力和镀层光亮度明显下降阳极易钝化,铜粉易产生,镀层粗糙,此时电压升高,电流反而开不大.当高于120g/L以上时,硫酸铜结晶析出,同时镀层脆性增大,光亮度下降,阳极黑膜脱落,难再形成,此时可观察到阳极周围有氧气产生,电流明显下跌,到此阳极明显钝化,阳极溶解后呈上小下大形状.
2.硫酸铜含量过高:
超过220g/L时,分散能力下降,气温低时硫酸铜结晶析出,而有些覆盖在阳极表面,使阳极不能正常溶解.同时,冬季温低,槽液粘度大,铜阳极反应产物铜离子扩散速度大大降低,在槽液浓度近饱和的情况下,铜盐于极板溶液界面高浓度区形成过饱和而结晶.温度越低,电流越高,结晶越快,越多.
3.氯离子过量:
含量低于10mg/L时,镀层亮度低,微粗糙,有条纹.当超过150mg/L时,镀层光亮范围变窄,零件凹处镀层不亮,发暗,边缘粗糙发白.此时阳极表面覆盖着白膜,系氯离子与铜的化合物,严重影响阳极正常溶解.(可用锌粉或除氯剂除去多余的氯,而由于阳极上氧化不完全,会生成Cu+,并行于Cu2+析出,造成粗糙,毛刺,低电流区不亮等,当用较多氯根存在时,生成CuCl沉淀,使镀液浑浊,故可采用循环过滤法去除CuCl并除去过量的氯根)
4.铁离子过多:
<10g/L时,影响不大,达15g/L时,镀层将有针孔,并对光亮度有一定影响.如到18g/L,若此时温度较低(如加热到20℃以上可用于临时生产),则开槽时电流表指针很快下降,阳极表面覆盖着一层棕绿色结晶,造成阳极钝化.
5.阳极面积过小:
阳极:
阴极=1:
3-4,阳极电流密度1.5-3A/dm2.如磷铜短缺,阳极电流>3A/dm2,将引起阳极脱膜,呈暗红色,造成钝化,并有一价铜和铜粉产生.
6.导电棒勾接触不良
7.未能及时清洗阳极与阳极袋:
正常电解过程,磷铜阳极不断溶解,黑膜不断生长,覆盖,并有部分污泥与黑膜脱落.如不及时清洗,阳极袋将被堵塞,阳极过厚,难以正常溶解.防止方法:
清洗阳极袋,洗刷阳极,除去黑膜.加(30%)H2O20.03-0.05ml/L,同时低电流电解半小时以上,以除去一价铜和铜粉,也使黑膜重新生成.
九:
氰化镀铜故障:
1.(电镀与环保96.6):
镀前分析:
CuCN(通过测铜的含量按分子式计算出)52.8克/升,游离氰化钠(没有测总氰化物含量)8.5克/升.镀6小时后再分析则分别为52.9g/L,3.9g/L,导致镀层粗糙,分散能力差.分析氰化钠的损耗有:
电解过程中分解,与大气接触挥发分解,零件带出等,但均为缓慢消耗.现场发现:
槽液呈暗红色,槽壁有大面积铜层,阳极不正常溶解.故确定游离氰化钠迅速降低的原因是槽液有过量的铜离子,在槽液中发生如下反应:
[Cu(CN)3]2-=Cu++3CN-.实际上因[Cu(CN)3]2-离解常数很小,反应向右进行.当添加游离氰化钠后,大量铜离子与氰根结合成络合离子,导致游离氰化钠减少.
原因:
过量挂放施镀零件,造成阴,阳极失调,阳极钝化,产生氧化铜.同时电极位置不当,零件挂具与柄体不正常接触,在槽壁上形成大面积铜层.
处理:
过滤杂质和铜粉.清理阳极,槽体.用波纹钢作阴极,槽体作阳极小电流电解,直至铜层退尽,槽液清亮.柄壁与槽液用塑胶皮隔开,分析调整槽液,严格控制阴,阳极面积.
十:
镀铜层:
1:
(电镀与环保90.6)锌粉除去酸性光亮镀铜液中过量的氯离子:
电解法去除氯离子,必须在高温(>65℃)下搅拌并经长时间电解处理.且效果较差.在酸性镀铜溶液中加入锌粉时,发生如下反应:
Zn+2H+=Zn2++H2
(1)Zn+Cu2+=Zn2++Cu
(2)
Zn+2Cu2+=Zn2++2Cu+(3)Cu2++Cu=2Cu+(4)
Cu++Cl-=CuCl(5)
当锌粉以干粉状态加入到镀液中时,以反应
(1)为主,以浆糊状态加