污泥干化概况.docx
《污泥干化概况.docx》由会员分享,可在线阅读,更多相关《污泥干化概况.docx(16页珍藏版)》请在冰豆网上搜索。
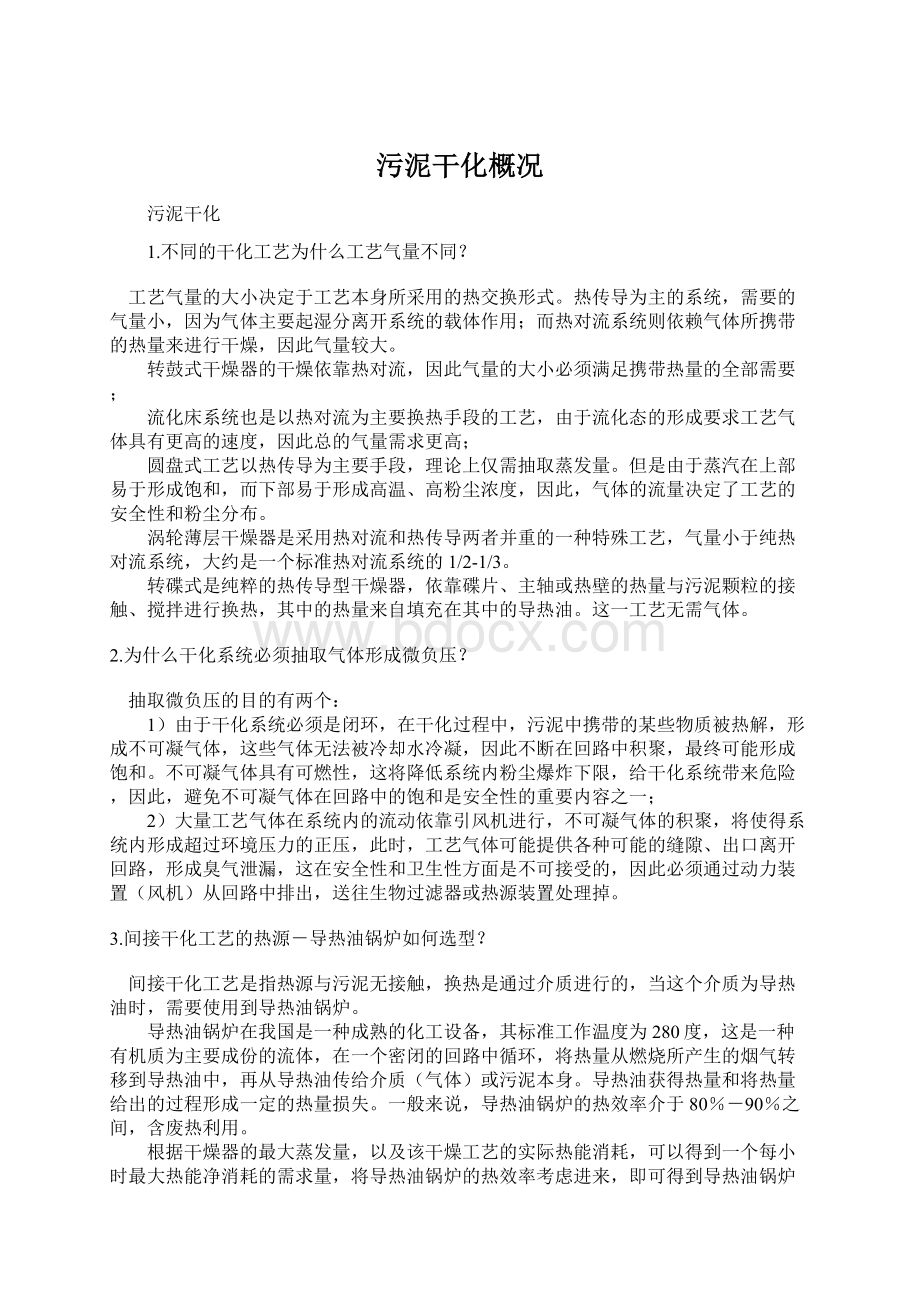
污泥干化概况
污泥干化
1.不同的干化工艺为什么工艺气量不同?
工艺气量的大小决定于工艺本身所采用的热交换形式。
热传导为主的系统,需要的气量小,因为气体主要起湿分离开系统的载体作用;而热对流系统则依赖气体所携带的热量来进行干燥,因此气量较大。
转鼓式干燥器的干燥依靠热对流,因此气量的大小必须满足携带热量的全部需要;
流化床系统也是以热对流为主要换热手段的工艺,由于流化态的形成要求工艺气体具有更高的速度,因此总的气量需求更高;
圆盘式工艺以热传导为主要手段,理论上仅需抽取蒸发量。
但是由于蒸汽在上部易于形成饱和,而下部易于形成高温、高粉尘浓度,因此,气体的流量决定了工艺的安全性和粉尘分布。
涡轮薄层干燥器是采用热对流和热传导两者并重的一种特殊工艺,气量小于纯热对流系统,大约是一个标准热对流系统的1/2-1/3。
转碟式是纯粹的热传导型干燥器,依靠碟片、主轴或热壁的热量与污泥颗粒的接触、搅拌进行换热,其中的热量来自填充在其中的导热油。
这一工艺无需气体。
2.为什么干化系统必须抽取气体形成微负压?
抽取微负压的目的有两个:
1)由于干化系统必须是闭环,在干化过程中,污泥中携带的某些物质被热解,形成不可凝气体,这些气体无法被冷却水冷凝,因此不断在回路中积聚,最终可能形成饱和。
不可凝气体具有可燃性,这将降低系统内粉尘爆炸下限,给干化系统带来危险,因此,避免不可凝气体在回路中的饱和是安全性的重要内容之一;
2)大量工艺气体在系统内的流动依靠引风机进行,不可凝气体的积聚,将使得系统内形成超过环境压力的正压,此时,工艺气体可能提供各种可能的缝隙、出口离开回路,形成臭气泄漏,这在安全性和卫生性方面是不可接受的,因此必须通过动力装置(风机)从回路中排出,送往生物过滤器或热源装置处理掉。
3.间接干化工艺的热源-导热油锅炉如何选型?
间接干化工艺是指热源与污泥无接触,换热是通过介质进行的,当这个介质为导热油时,需要使用到导热油锅炉。
导热油锅炉在我国是一种成熟的化工设备,其标准工作温度为280度,这是一种有机质为主要成份的流体,在一个密闭的回路中循环,将热量从燃烧所产生的烟气转移到导热油中,再从导热油传给介质(气体)或污泥本身。
导热油获得热量和将热量给出的过程形成一定的热量损失。
一般来说,导热油锅炉的热效率介于80%-90%之间,含废热利用。
根据干燥器的最大蒸发量,以及该干燥工艺的实际热能消耗,可以得到一个每小时最大热能净消耗的需求量,将导热油锅炉的热效率考虑进来,即可得到导热油锅炉的选型参照标准。
举例来说,一个2000升/小时蒸发量的干燥器,采用闭环空气作为介质,其净热能消耗约820大卡/升水蒸发量,导热油锅炉的热效率为88%,则:
2000升/小时x820大卡/升/88%=1,860,000大卡/小时
需要配备大约200万大卡的导热油锅炉。
导热油锅炉应提供以下配套参数:
-油泵,装机容量;
-燃烧器,装机容量;
-流量;
-导热油进出口温度,最大温差,平均温差;
-导热油一次填充量;
4.干燥器的处理能力是固定的吗?
干燥器的处理能力具有一定的变化区间。
其区别来自两个方面:
物料本身性质使得干燥时间延长或缩短;因最终含固率的变化而提高或降低产能。
对于污泥干化来说,由于污泥的性质决定了大多数干燥工艺必须采用干泥返混,因此,其由于物料本身性质原因而导致的干燥时间变化不大,而凡是采用干泥返混的工艺在最终含固率方面不具有伸缩性,因此,可以说其干燥器的处理能力是“固定”的。
这一点对于无干泥返混的工艺来说就不一样了,最终含固率的改变会导致处理量方面较大的变化。
5.全干化和半干化是怎么划分的?
所谓干化和半干化的区别在于干燥产品最终的含水率不同,这一提法是相对的,并没有科学的定义。
“全干化”指较高含固率的类型,如含固率85%以上;而半干化则主要指含固率在50-65%之间的类型。
如果说干化的目的是卫生化,则必须将污泥干燥到较高的含固率,最高可能要求达到90%以上,此时,污泥所含的水分大大低于环境温度下的平均空气湿度,回到环境中时会逐渐吸湿。
如果说干化的目的仅仅是减量,则会产生不同的含固率要求。
将含固率20%的湿泥干化到90%或干化到60%,其减量比例分别为78%和67%,相差仅11个百分点。
根据最终处置目的的不同,事实上要求不同的含固率。
比如填埋,填埋场的垃圾含固率平均低于60%,要求污泥达到90%意义不大。
将污泥干燥到该处置环境下的平衡稳定湿度,即周围空气中的水蒸气分压与物料表面上的水蒸气压达到平衡,应该是最经济合理的要求。
6.半干化时的产能为什么高于全干化?
有些污泥干化工艺可以将湿泥处理至含固率50-65%,而这时的处理量明显高于全干化时的处理量。
其原因有两个:
首先,对于干燥系统来说,干燥时间决定了干燥器的处理量。
当物料的最终含水率较高(所谓半干化)时,蒸发相同水量的时间要少于最终含水率高的情况(所谓全干化),单位处理时间内可以有更高的处理量。
其次,污泥在不同的干燥条件下失去水分的速率是不一样的,当含湿量高时失水速率高,相反则降低。
7.污泥干燥的机理是怎样的?
干燥是为了去除水分,水分的去除要经历两个主要过程:
1)蒸发过程:
物料表面的水分汽化,由于物料表面的水蒸气压低于介质(气体)中的水蒸气分压,水分从物料表面移入介质。
2)扩散过程:
是与汽化密切相关的传质过程。
当物料表面水分被蒸发掉,形成物料表面的湿度低于物料内部湿度,此时,需要热量的推动力将水分从内部转移到表面。
上述两个过程的持续、交替进行,基本上反映了干燥的机理。
8.干化为什么要讨论换热形式?
干化所应用的换热形式是分析干化系统效能的重要理论基础。
所有的换热均需通过一定的介质或界面来进行,这些介质或界面要么是气体,如空气、蒸汽、氮气、烟气等;要么是金属,这时其热量是通过烟气、导热油、蒸汽等介质来输送的。
介质蓄积和携带热量。
含湿物料接触金属热壁时,水分子与金属分子的接触,形成了热传导;气态介质分子与含湿物料中水分子的包裹、混合和接触,形成了热对流。
热传导和热对流是干化过程中应用最多的两种换热形式。
绝大部分干化工艺均采用其中的一种作为主要换热形式,少数则两种兼备。
除去烟气可以用于直接加热方式外,其余介质的应用均属于间接加热方式的热利用。
换热形式决定了干化系统热量损耗的基本特点。
9.为什么污泥干化的时间长?
大多数干化工艺需要20-30分钟才能将污泥从含固率20%干化至90%。
干燥是由表面水汽化和内部水扩散这两个相辅相成、并行不悖的过程来完成的,一般来说,水分的扩散速度随着污泥颗粒的干燥度增加而不断降低,而表面水分的汽化速度则随着干燥度增加而增加。
由于扩散速度主要是热能推动的,对于热对流系统来说,干燥器一般均采用并流工艺,多数工艺的热能供给是逐步下降的,这样就造成在后半段高干度产品干燥时速度的减低。
对热传导系统来说,当污泥的表面含湿量降低后,其换热效率急遽下降,因此必须有更大的换热表面积才能完成最后一段水分的蒸发。
10.缩短干燥时间的可能性?
对所有干燥器来说,缩短干燥时间意味着生产效率的提高。
能够用5分钟干燥的物料,谁也不会用10分钟。
能否缩短干燥时间,不是主观意愿决定的,而是干燥条件决定的。
影响干燥过程的因素很多,比如介质环绕物料的状况,介质运动的速度、方向,物料的性质、大小、堆置情况、湿度、温度等。
这些因素的总和,决定了干燥时间。
以上状况的改善和优化事实上是工艺决定的,其中一个普遍采用的方法是干泥返混,除避免污泥在干燥器内的粘结外,在很大程度上可以改善物料在干燥器内的受热条件,从而有效地缩短时间。
11.关于污泥处理量的计算?
根据蒸发量、入口和出口的含固率,可以推导出干燥器的理论产能。
污泥理论处理量=蒸发量+(蒸发量X湿泥含固率)/(干泥含固率-湿泥含固率)
例如,一个蒸发量为每小时2500公斤水的干燥器,如果将20%的湿泥干化到90%,则:
2500+(2500x20%)/(90%-20%)x24/1000=77吨/日
做适合于焚烧的半干化产品时:
2500+(2500x20%)/(60%-20%)x24/1000=90吨/日
12.污泥干化厂的公用配套设施有哪些?
一般来说,干化工艺需要配备以下基础配套设施,但根据工艺可能有较大变化:
-冷却水循环系统:
用于干泥产品的冷却等
-冷凝水处理系统:
工艺气体及其所含杂质的洗涤等;
-工艺水系统:
用于安全系统的自来水
-电力系统:
整个系统的供电
-压缩空气系统:
气动阀门的控制
-氮气储备系统:
干泥料仓以及工艺回路的惰性化;
-除臭系统:
湿泥料斗、储仓、工艺回路的不可凝气体的处理
-制冷系统:
导热油热量撤除
-消防系统:
为整厂配置的灭火系统和安全区
13.干化工艺如何利用废热烟气?
所有的干化系统都可以利用废热烟气来进行。
其中,间接干化系统通过导热油进行换热,对烟气无限制性要求;而直接干化系统由于烟气与污泥直接接触,虽然换热效率高,但对烟气的质量具有一定要求,这些要求包括:
含硫量、含尘量、流速和气量等。
焚烧炉的烟气与间接干化系统的导热油换热时,尚需注意烟尘具有一定的磨蚀性,烟气中可能含有一定的腐蚀性气体成份,以及换热器的高温腐蚀问题。
导热油系统的温度调整可以通过气动阀门调节烟气流量的办法来进行,但是当这种调节可能影响敏感的焚烧效果时,则有必要设立独立的燃气或燃油锅炉,通过对热值不足部分进行调温来实现。
14.干化系统如何利用蒸汽进行干化?
只有间接加热工艺才能利用蒸汽进行干化,但并非所有的间接工艺都能获得较好的干化效率。
一般来说,蒸汽由于温度相对较低,必然在一定程度上影响干燥器的处理能力。
蒸汽的利用一般是首先对过热蒸汽进行饱和,只有饱和蒸汽才能有效地加以利用。
饱和蒸汽通过换热表面加热工艺气体(空气、氮气)或物料时,蒸汽冷凝为水,释放出全部汽化热,这部分能量就是蒸汽利用的主要能量。
15.干化工艺中产品温度意味着什么?
污泥是一种高有机质含量的超细粉末,污泥干燥的目的首先在于减量、卫生化。
无论对于何种最终处置方法,污泥干化本身并不会改变污泥的性质,即温度并不会导致污泥产品的降解或质量问题。
有鉴于此,无论从污泥产品的质量角度,还是干燥器的效率角度看,应该是温度越高越好。
但是,由于安全性问题的存在,绝大部分干化工艺倾向于尽可能降低产品的温度,即降低所谓粉尘爆炸的点燃能量。
然而,根据研究,污泥粉尘的点燃能量很低,当氧气、粉尘浓度达到一定量时,100度左右的温度下,其点燃能量低至几个到十几个毫焦。
当点燃能量达到1焦耳时,70-80度也足以形成燃烧。
当粉尘浓度更高时,即使20-30度的环境都可能存在风险。
许多料仓的自燃和爆炸均属于这种情况。
干化工艺为了保证一定的处理效率,温度是必然存在的,而且不可能很低,典型值在105-125度之间。
工艺的安全性只能从降低粉尘浓度和抑制燃烧气氛入手。
单纯依靠降低产品温度来保证安全性是不正确的想法。
16.干化为什么要进行污泥成份分析?
根据经验,对污泥成份做一定的分析,对于确定干化工艺、获得最佳设计参数、确认工作条件是必要的。
与干化工艺相关的湿泥检测内容包括:
含水率、粘度、含油脂比例、酸碱腐蚀性、含沙率等。
与污泥最终处置相关的干泥检测内容包括:
重金属含量、有机质含量、热值、细菌含量等。
17.为什么说污泥干化是资源化利用的第一步?
污泥无论来自工业还是市政,其处理的一个可行目标就是使所有来自工业中的污染物作为原料返回到工艺中去。
所有的污染物事实上都是中间过程流失的原料,造成流失的媒介大多数情况下是水,去除水,将使得大量的潜在污染物可以重新得到利用。
污泥所含的污染物一般均有很高的热值,但是由于大量水分的存在,使得这部分热值无法得到利用。
如果焚烧高含水率的污泥,不但得不到热值,还需要大量补充燃料才能完成燃烧。
如果将污泥的含水率降到一定程度,燃烧就是可能的,而且,燃烧所得到的热量可以满足部分甚至全部进行干化的需要。
同样的道理,无论制造建材还是图例利用,减少含水率是关键。
因此,可以说污泥干化或半干化事实上是污泥资源化利用的第一步。
18.旋风分离器的固体回收率是多少?
在许多热对流系统中,污泥干化必须将全部或部分产品通过旋风分离的方式收集起来,由于各个工艺的风量和风压不同,通过此方法进行回收的颗粒粒径和比例不同,造成其设计的千差万别。
一般来说,旋风分离器的固体回收率在95-98%之间。
含固率越高,产品的粒度越小,捕集的难度也就会提高。
19.干化包括哪些必要的工艺步骤?
污泥干化的目的在于去掉湿泥中的部分水分,以适应不同的处置要求。
干化意味着在单位时间里将一定数量的热能传给物料所含的湿分,这些湿分受热后汽化,与物料分离,失去湿分的物料与汽化的湿分被分别收集起来,这就是干化的工艺过程。
从设备角度来描述这一过程,包括上料、干化、气固分离、粉尘捕集、湿分冷凝、固体输送和储存等。
如果因物料的性质(粘度、含水率等)可能造成干化工艺的不稳定性的(如黏着、结块等),则有必要采用部分干化后产品与湿物料混合的工艺(返料、干泥返混)。
此时,在上料之前和固体输送之后应相应增加输送、储存、分离、粉碎、筛分、提升、混合、上料等设备。
20.干化为什么要区分间接或直接加热方式?
直接和间接加热方式的划分在于热源利用的形式区别,具体来说就是直接作为介质还是间接对换热的介质进行加热。
干化是依靠热量来完成的,热量一般都是能源燃烧产生的。
燃烧产生的热量存在于烟道气中,这部分热量的利用形式有两类:
(1)直接利用:
将高温烟道气直接引入干燥器,通过气体与湿物料的接触、对流进行换热。
这种做法的特点是热量利用的效率高,但是如果被干化的物料具有污染物性质,也将带来排放问题,因高温烟道气的进入是持续的,因此也造成同等流量的、与物料有过直接接触的废气必须经特殊处理后排放。
(2)间接利用:
将高温烟道气的热量通过热交换器,传给某种介质,这些介质可能是导热油、蒸汽或者空气。
介质在一个封闭的回路中循环,与被干化的物料没有接触。
热量被部分利用后的烟道气正常排放。
间接利用存在一定的热损失。
对干化工艺来说,直接或间接加热具有不同的热效率损失,也具有不同的环境影响,是进行项目环评和经济性考察的重要内容。
21.干化工艺都有哪些工艺气体体系?
工艺气体对于采用热对流换热形式的工艺来说是必要的。
工艺气体的作用有三个:
1)它是热量的携带者,从外部将热量带入干燥器,在干燥的过程中将热量传递给湿物料;
2)它是湿分的携带者,通过工艺气体本身的水蒸气压和物料表面的水蒸汽压差,将后者的湿分分散、转移到工艺气体中来,并通过循环和冷凝(部分或全部),达到带走湿分的目的。
3)工艺气体在某些工艺中还具有一定的搅拌、混合作用。
干化工艺可以使用的工艺气体包括空气、氮气、烟气、二氧化碳气、蒸汽等。
最常见的是空气体系,无论使用烟气还是添加氮气,均是有一定惰性化特征的空气体系。
仅有极少数工艺能够采用蒸汽体系。
值得注意的是,界定其是否属于工艺气体的蒸汽体系应判断其是否满足以下两点特征:
携入热量和带走湿分。
显然,某些工艺中基本不存在大量工艺气体的循环,系统仅抽取相当于蒸发量的部分进行冷凝,此时仍属于典型的热传导系统。
22.蒸汽体系的优缺点有哪些?
蒸汽体系与空气体系的区别在于,在热干化的工艺回路中以蒸汽彻底取代了空气(烟气、氮气、二氧化碳),并由此获得以下两个重要优点:
(1)节能:
取消了对全部工艺气体的洗涤,仅对相当于蒸发量的部分进行冷凝,其余的蒸汽在系统内循环。
作为热对流系统,取消了工艺气体洗涤,意味着能耗的极大节约。
(2)绝对安全性:
全蒸汽的回路内含氧量极低,并由于蒸汽的有效保护,使得粉尘爆炸的下限上升至绝对安全条件下。
蒸汽体系当然也存在一些缺点,其中:
(1)管线的保温、耐压要求高于空气体系,因此这部分投资较高;
(2)取消湿法除尘,而采用干法除尘,增加了除尘装置的维护量。
(3)工艺气体的温度降低,可能导致相同质量的工艺气体所携带的热量有所降低,即处理效率的降低。
这一体系对于某些特殊条件或特殊物料的干化,不失为一种极端的安全措施。
如来自不同脱水装置的污泥,含水率波动极大,这种波动对于即使采用干泥返混措施的工艺来说都可能是非常危险的;另如某些物料中混合有易燃成份等。
23.湿泥含水率的变化是否重要?
进料含水率的变化对于干化系统来说是非常重要的经济参数。
这个数值越低,意味着投资更大。
此外,它还是一个有关安全性的重要参数。
含水率因不同来源的湿泥(可能来自几个不同的污水处理厂)、脱水机的运行不正常(机械故障、机械效率降低、更换蓄凝剂或改变添加量)等原因,可能出现波动。
当波动幅度超过一定范围时,就可能对干化的安全性形成威胁。
产生危险的原因在于干燥系统本身的特点。
一般干燥系统在调试的过程中,给热量及其相关的工艺气体量已经确定,仅通过监测干燥器出口的气体温度和湿度来控制进料装置的给料量。
给热量的确定,意味着单位时间里蒸发量的确定。
当进料含水率变化,而进料量不变时,系统内部的湿度平衡将被打破,如果湿度增加,可能导致干化不均;如果湿度减少,则意味着粉尘量的增加和颗粒温度的上升。
全干化系统的含水率变化较为敏感,在直接进料时,理论上最多只允许2个百分点的波动(如设定20%,而实际22%),此时由于污泥水分的急遽减少,干燥器内产品的温度会飞升,形成危险环境。
由于这一区间非常狭小,对调整湿泥进料量的监测反馈系统要求较高。
24.如何解决湿泥含水率变化的敏感性?
解决湿泥含水率变化敏感性的最好方法是在可能的范围内降低最终产品的含固率。
当最终含固率从90%降为80%时,理论上可允许5个百分点的波动(如设定20%,而实际25%)。
大多数全干化工艺都采用了干泥返混。
这样做的目的一般都是为了避免污泥的胶粘相特性使之在干燥器内易于黏着、板结,另外一个好处正是由此扩大了可允许的湿泥波动范围。
干泥返混一般要求将原含固率20-25%的湿泥,经过添加相当于湿泥重量1-2倍的已经干化到90%以上的干泥细粉,将其混合到平均含固率60-70%。
从绝干物质量上增加了7-10倍以上。
如果将干燥器的湿泥进料含固率设定为60%,其最高理论波动范围可以达到66%,这对返混工艺来说应该是可以轻松实现的了。
干泥返混在解决干燥器湿度敏感方面是有效的,但它同时还带来了其它一些安全性问题。
25.污泥干化技术的前景如何?
纵观40年来污泥干化技术的发展历程,可以看出,污泥干化采用的仍是几十年前的传统干燥技术,只不过经过一定的改造,以使之更适应污泥这种物料而已。
在污泥干化领域,至今仍不断有新的技术出现,但是在近期内发现一种更好的、革命性的技术来代替一切,其可能性很小。
绝大多数干化设备是已经存在几十年甚至上百年的“古老”技术,这方面的技术壁垒并不高。
干化工艺是一种综合性、实验性和经验性很强的生产技术,它并不特别复杂和神秘。
其核心在于干燥器本身。
并非所有的干燥器都易于仿制,特别是当制造精度、变形量、材料的变化成为诀窍的时候。
对干化技术进行不断的优化努力,一直是以安全性为目标的,而解决安全性的出路极为有限,它仍然是以干燥器结构为中心、综合一系列边缘技术的持续不断的改进过程。
考虑到污泥干化完全是污水处理的延伸,全球水环境的治理仍处于刚刚起步阶段,因此其前景非常广阔,所有的新技术、新工艺都将有一个广阔的发展空间。
26.影响干化工艺安全性的要素有哪些?
对工艺安全性具有重要影响的要素包括:
-粉尘浓度
-工艺允许的最高含氧量(燃烧气氛的惰性化)
-温度(点燃能量)
-湿度(气体的湿度和物料的湿度对提高或降低粉尘爆炸下限具有重要影响)
以上几个参数中,对于大多数系统来说,事实上只有从降低含氧量、进行燃烧气氛的惰性化入手。
27.干化时产品温度低就更安全吗?
众所周知,环境压力下的水汽化温度是100度,以这个温度作为分界线,将干燥工艺按照产品的温度来划分,可以形成所谓的“高温工艺”和“低温工艺”两种类型。
这种区分的直接目的与干化的安全性相关,它容易使人产生“低温就安全”的误解。
蒸发的产生并非一定要到100度这个标准的汽化温度。
环境温度下清风徐徐,人的皮肤仍然会感到仍然清凉干爽。
当空气中的湿度较高时,即使温度不超过30度,也仍然会感到闷热难当。
其原因首先是气体的含湿量应低于湿表面,其次是气量本身,依靠大量气体和微弱的蒸汽压差,仍然可以进行蒸发,但是其能耗在干化工艺中处于上限。
温度是影响所谓粉尘爆炸条件的因素之一。
但是鉴于污泥的粉尘浓度下限较低,如果含氧量条件具备,所需的点燃能力非常小。
即使30度的温度下,污泥粉尘爆炸也都是可能的。
因此,干燥器内的产品温度低并不是一个能够排除粉尘爆炸的根本性条件。
28.污泥混入沙石是否对干化设备产生影响?
沙石混入对设备的安全性存在着负面影响。
首先,沙石在高粉尘、低湿环境中的运动可能导致火花的产生。
其次,沙石具有磨蚀性。
很多污泥干化系统对沙石是敏感的,特别是当其含量较大时,可能对设备产生严重的磨蚀。
其中,有着强烈搅拌的工艺,特别是靠金属表面剪切力来推动物料向前运动的设备,可能产生的磨蚀会较为严重。
多数干化工艺是间接加热的,当这种磨蚀威胁到承载高温介质——导热油时,则是十分危险的。
鉴于市政污泥的性质及其产生工艺,混入沙石的可能性较小。
对大多数设备来说是可以接受的。
而来自管网淘挖、江河清淤的污泥则可能有较多杂质,应优化前端沉沙工艺,避免不必要的设备损耗。
29.为什么干化工厂不宜频繁开停机或单班生产?
干燥设备因为是利用热能进行的,加温和降温过程耗时耗能,属于非产出过程;同时由于污泥是高有机质超细粉末,为了安全原因,频繁的清空过程,徒然增加系统在安全方面的能耗支出;再者,鉴于污泥是低附加值的产品,应尽可能提高设备利用效率,以降低其折旧费用,因此干化系统不建议做非全日制生产的设计,事实上也是不存在经济可行性的。
一般来说,一个干化系统的加温过程需时30-40分钟,降温过程需要20-30分钟,如果是冷机,所需时间可能更长。
频繁清空,其加温和降温过程均需惰性化,如果采用氮气则成本颇高,采用蒸汽(水)则少,但设备终归是非生产状态。
如果因此而降低设备开机利用率(从每年340x24=8200小时变成360x8=3000小时),其设备折旧和大修提存将成倍增加。
30.污泥干化能耗的构成有哪些?
能耗包括了干化工艺本身的热能、电能消耗,同时也必须包括与该工艺安全运行密切相关的其它辅助性工艺设施的开支,其中包括:
氮气系统、制冷系统、干泥返混系统。
氮气系统:
由于干化系统必须抽取蒸发量、不可凝气体进行冷凝,由此所形成的微负压状态,可能导致空气中的氧气进入系统。
当工艺中的氧气达到一定浓度,而此时的粉尘浓度超过爆炸下限,在极小的点燃能量下可能产生粉尘爆炸。
因此,降低系统内