炼钢一厂转炉工艺技术操作规程解析.docx
《炼钢一厂转炉工艺技术操作规程解析.docx》由会员分享,可在线阅读,更多相关《炼钢一厂转炉工艺技术操作规程解析.docx(14页珍藏版)》请在冰豆网上搜索。
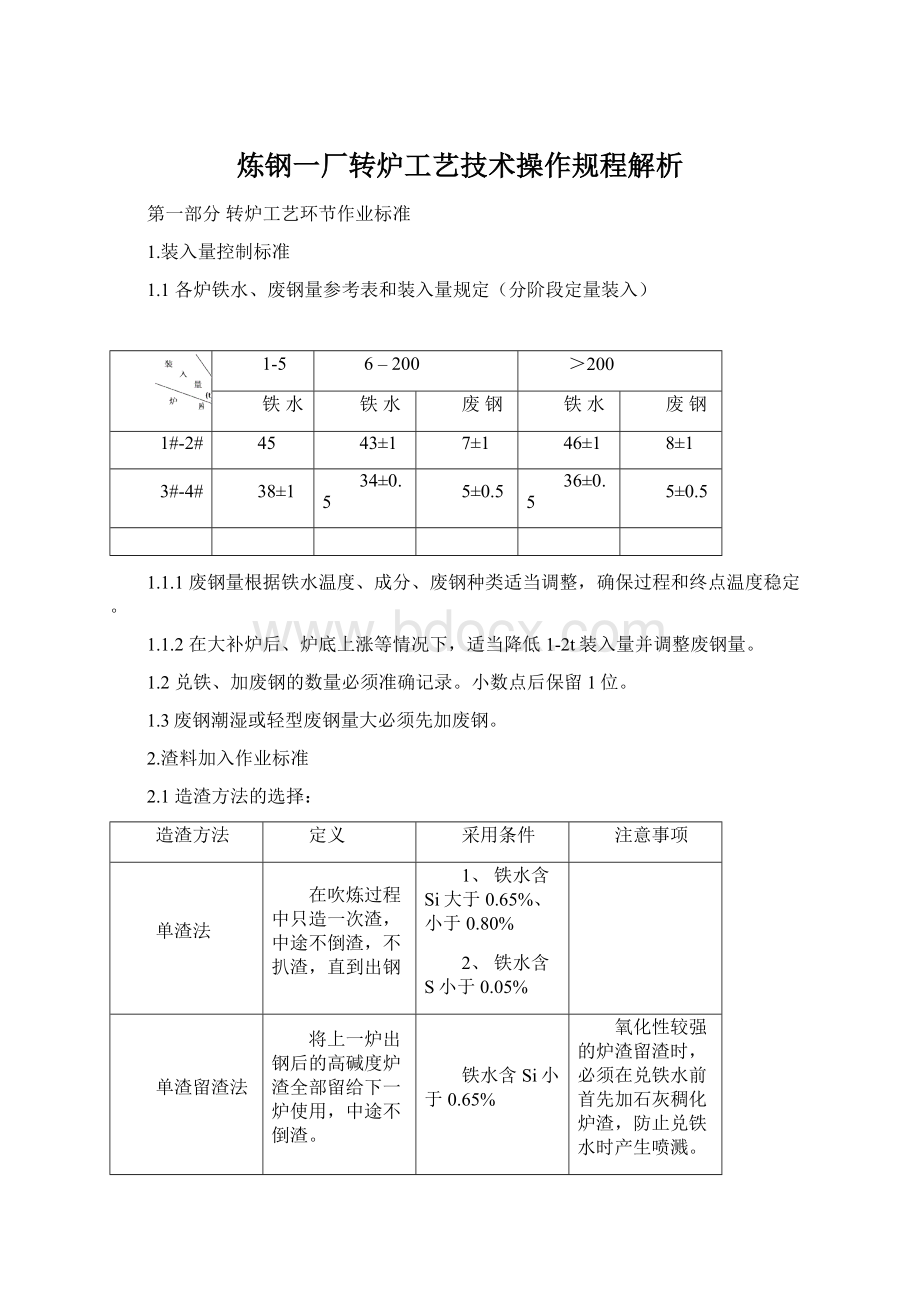
炼钢一厂转炉工艺技术操作规程解析
第一部分转炉工艺环节作业标准
1.装入量控制标准
1.1各炉铁水、废钢量参考表和装入量规定(分阶段定量装入)
1-5
6–200
>200
铁水
铁水
废钢
铁水
废钢
1#-2#
45
43±1
7±1
46±1
8±1
3#-4#
38±1
34±0.5
5±0.5
36±0.5
5±0.5
1.1.1废钢量根据铁水温度、成分、废钢种类适当调整,确保过程和终点温度稳定。
1.1.2在大补炉后、炉底上涨等情况下,适当降低1-2t装入量并调整废钢量。
1.2兑铁、加废钢的数量必须准确记录。
小数点后保留1位。
1.3废钢潮湿或轻型废钢量大必须先加废钢。
2.渣料加入作业标准
2.1造渣方法的选择:
造渣方法
定义
采用条件
注意事项
单渣法
在吹炼过程中只造一次渣,中途不倒渣,不扒渣,直到出钢
1、铁水含Si大于0.65%、小于0.80%
2、铁水含S小于0.05%
单渣留渣法
将上一炉出钢后的高碱度炉渣全部留给下一炉使用,中途不倒渣。
铁水含Si小于0.65%
氧化性较强的炉渣留渣时,必须在兑铁水前首先加石灰稠化炉渣,防止兑铁水时产生喷溅。
双渣留渣法
将上一炉出钢后炉内的高碱度、高温度并含有一定数量Σ(FeO)终渣留下一部分或全部给下一炉使用,吹炼中途倒渣后造新渣
铁水含Si大于0.80%
双渣法操作的关键是倒渣时间,应选择在渣中含磷量最高,含铁量最低的时刻,能达到脱磷效率最高,铁的损失最小的效果;
2.2渣料量以及加入方式和加入时间的确定:
2.2.1渣料量的确定:
在保证终渣R2.6-2.8的基础上,根椐铁水和生铁含Si、P、S及其装入数量、冶炼钢种以及上炉温度、终点渣情况、物料质量等条件确定渣料加入种类和数量。
铁水成分%
白灰Kg
白云石Kg
镁球Kg
0.60
45
20
5
0.70
60
20
5
0.80
65
20
5
2.2.2渣料加入方式:
所有物料基本上可分2-3批加入。
特别是冷却剂、化渣剂在冶炼中期加入时,更要采取小批量多批次的方法。
2.2.3每批渣料加入时间以及加入数量:
2.2.3.1正常情况下,第一批料在降枪开吹的同时,加入白灰总量的1/2-2/3(双渣时加入总量的1/3);镁球、白云石的全部或1/2(双渣时在二批料加入);冷却剂量大时加入总量的1/2,冷却剂量小时在二批料分批加入。
第二批料在Si、Mn反应基本完成,C火焰初起,头批料基本化透时加入剩余的各种物料。
剩余白云石、镁球一次加入;冷却剂、化渣剂、根据化渣和温度情况分批加入,以小批量、多批次为原则,并要求所有物料在终点前3分钟加完。
2.2.3.2当铁水温度特别低(小于1150℃)时,要在降枪开吹30-60秒后再开始加料。
加入方式同正常情况。
3.氧枪操作作业标准
3.1接班后仔细观察相关仪表、确认各种联锁是否正常。
前三炉内必须组织测有效高度和量液面,并记录。
3.2使用氧压和氧气流量的控制要求:
3.2.1总管氧压应在1.0-1.2Mp,使用氧压应控制在0.8-0.9Mp,以确保充分发挥氧枪的设计能力。
3.2.2氧气流量1-2#炉按10000-12000m3/h;3#炉按8500-9500m3/h;4#炉按9500-11000m3/h。
3.3枪位控制:
3.3.1正常枪位的控制基准
炉座枪位
开吹枪位
最高枪位
拉碳枪位
1#-2#
1000mm
1500mm
900mm
3#-4#
800mm
1300mm
600mm
过程枪位控制原则
吹炼时期
原则
特点
要求
操作
前期
早化渣、化好渣、以利于最大限度的脱除S、P。
Si、Mn迅速氧化、渣中SiO2的浓度大,熔池温度不高
石灰尽快地化好
适当加入氧化铁皮球,采用较高枪位
中期
继续化好渣、化透渣、快速脱C、不喷溅、熔池均
强烈脱C
避免“返干
适当提枪,使渣中Σ(FeO)在10%-15%,均匀升温
后期
进一步调整好炉渣的氧化性和流动性,继续脱除S、P,均匀熔池的温度和成分,降低终渣的Σ(FeO)含量。
保证温度和成分均匀
化渣不良时应先适当提枪化渣,在接近终点时,再适当降枪,加强搅拌,降低Σ(FeO
3.3.2开新炉时的开吹枪位应比基准枪位提高100mm,以便加强化渣和对炉衬的烧结。
3.3.3冶炼回炉钢时开吹枪位和过程枪位要比正常基准枪位降低50-100mm。
3.3.4冶炼中碳和高碳钢、复吹工艺正常使用时,拉碳枪位应提高50-100mm。
3.3.5冶炼低碳时拉碳枪位应降低50-100mm。
3.3.6当氧气使用压力低于设计氧压10%-15%时,各期操作枪位必须降低50-100mm。
当氧气使用压力低于设计氧压15%以上时,停止冶炼。
3.3.7拉碳降枪时间必须大于30s,最好大于1min。
低氧压拉碳时,降枪时间必须大于1min,最好大于1.5min。
3.4氧枪操作严禁吊吹,降枪时要缓慢,幅度应控制在100-200mm。
特别是拉碳降枪时,每次动作应控制在50-100mm。
3.5氧枪粘钢时严禁撸枪。
当氧枪粘钢不能涮掉且粘枪位置接近炉口时要及时更换。
3.6吹炼过程中发现氧枪大量漏水,要及时关闭氧气和氧枪水提起氧枪,严禁摇炉。
4.温度控制作业标准
4.1温度控制的基本原则:
前期升温迅速,中期升温平稳,后期按钢种要求温度调整。
4.2过程温度的判断和调整
4.2.1吹炼前期:
主要根据碳火焰上来的早晚判断温度的高低,在2.5-3min碳火焰上来温度属于正常。
前期温度低,可适当降低枪位50-100mm吹炼提温;反之,温度高,可提前加入二批料加以控制。
此期温度易偏低。
4.2.2吹炼中期:
主要根据炉口火焰特征、氧枪进出水温差(与氧枪设计有关,一般应保持在8-10℃)、返干情况判断温度。
此期温度易偏高。
温度高,向炉内追加冷却剂进行调整,但每次加入量应控制在50-100kg。
温度低时,可适当降枪100-200mm提温。
4.2.3吹炼末期(重点):
主要依据炉口火焰、取勺样、看炉膛情况和测温枪测温进行综合判断。
4.2.3.1当终点温度低于要求20℃以内,碳高于钢种要求上限时,可直接补吹提温出钢;温度低超出20℃以上,且碳低于钢种要求中下限时,应加硅铁提温。
硅铁升温0.14℃∕kg吨钢。
但要注意回磷情况和降碳的升温。
一般含C0.20%左右时,每降0.01%的C出钢温度可升高1.5-2℃
4.2.3.2当终点温度高于钢种要求10℃以内,碳符合钢种要求的中下限时,可直接出钢,到吹氩站用干净冷钢调温或延长吹氩时间和镇静时间进行调整;当温度高于要求10℃以上,且C在钢种要求上限时,要适当加入生白云石及白云石后(此时加入的物料必须干燥)降枪点吹降温,并测温取样合适后出钢,严禁使用铁皮球及矿石降温。
4.3各种冷却剂的冷却效应换算值(以废钢冷却效应为1)
废钢
矿石
铁皮
白灰
白云石
生铁
生白云石
1.0
3.0
3.35
1.0
1.05
0.6-0.7
3.0
4.4钢种终点炉内、氩前、氩后温度控制标准
按工艺卡要求执行
4.4.1采用凉包或有包底、包壁结冷钢,可比要求温度适当提高10-20℃。
有包底的包或非复产时的凉包禁止开新机使用。
4.4.2开新炉前10炉以内的温度,要比正常炉炉内温度控制提高10-20℃。
4.5温度控制参考值
4.5.1钢水在炉内镇静温降为2-3℃∕min。
4.5.2吹氩过程温降为20℃左右。
4.5.3正常情况下,出钢温度损失为30-50℃
4.5.4钢水在钢包内镇静温降为0.8-1.5℃∕min,小钢包取上限。
4.5.5各种不同因素的变化对终点温度的影响:
项目
铁水Si
T℃
废钢
铁水量
Fe-Si
包内合金化
变化量
±0.01%
±10℃
±6kg
±1t
1kg∕t
±7kg∕t
影响温度
±1.8℃
±8℃
10℃
±13℃
6℃
10℃
5.测温作业标准
5.1检查测温系统,线无破损、枪头紧固、仪表显示环境温度。
5.2偶头头部无凹陷、纸管完好。
按到枪上与枪头紧密结合,仪表回零,指示灯显示绿色。
5.3不能用枪头顶硬物。
测温时身体不能正对炉口。
5.4测温时枪与钢液面呈30度角,保证插入钢水30cm以上。
5.5钢包测温时,测温枪与水平夹角呈45°-60°插入,插入深度在20-40cm之间。
枪头与包壁和翻腾钢液处距离大于20cm以上。
5.6枪插入钢水测温时间不能超过15秒。
温度显示后快速把枪拔出。
5.7测温完毕,立即换好偶头,准备下次测温。
6.取样作业标准
6.1取样前检查样勺应干燥洁净。
取样时身体不能正对炉口,并且应先将样勺在炉渣中翻转两次均匀挂渣,然后将样勺倒扣与钢液面呈30°角插入钢液约30cm后翻正,再平稳的端出样勺。
6.2取出的样应达到:
样勺满而不裸露钢水,表面有渣层均匀覆盖,勺中钢水应不少容积的2∕3。
6.3样子取出后,选择干燥地面平稳放好。
待炼钢工快速拨去渣子看完钢样后,迅速端起样勺40-50cm高,把钢水均匀细流倒入样模或另一人用洁净铁锨与地面约呈45°角快速配合片取氧化样。
6.4待钢液凝固后,把样勺残钢磕出备用。
7.出钢作业标准
7.1实行前后挡渣出钢。
出钢前加挡渣塞挡前期渣,出钢末期加挡渣球防止下渣。
7.2出钢前要确认合金加料管通畅、旋转灵活。
加合金时,合金加料管要对准钢流。
7.3出钢时,一人摇炉操作一人指挥。
见出钢口圆流出钢时再停止摇炉或缓慢摇炉,避免从出钢口大量下渣和从炉口下渣。
7.4合金加入时间控制:
出钢到1∕3时开始加入合金至出钢到3∕4时加完。
7.5挡渣球加入时间:
根据出钢口的大小决定。
较大时,出钢到1∕2加入。
较小时,出钢到3∕5加入。
挡渣球应加到出钢口上方。
7.6出钢后期,要认真观察钢流情况,既要保证钢水出净,又要避免后期大量下渣。
钢包内渣层厚度应控制在50-80mm以内。
7.7出钢不能过满,钢包液面与包沿距离不小于300mm。
7.8出钢时间控制:
50t转炉不得小于2.5min;40t转炉不得小于2min;
7.9出钢口维护以钢水圆流为标准,否则进行维护或更换。
8.脱氧合金化作业标准
8.1脱氧方法采取钢包沉淀脱氧,炉后喂线微调。
8.2脱氧后钢水氧活度应控制在40-60ppm范围之内。
(特殊钢种按工艺卡执行)
8.3脱氧剂加入原则:
脱氧用的先加,合金化用的后加;不易氧化的早加,易氧化的贵重合金后加。
8.3.1对于普通建筑用钢,可按先强后弱或强-弱-强的顺序加入,但必须充分吹氩。
能保证合金吸收率的稳定。
8.3.2钢种纯净度要求较高或冷轧用料,应按先弱后强的顺序加入。
确保夹杂物的上浮。
8.3.3合金化应本着“死配活加”的原则。
根据装入量准确计量合金数量,但必须根据出钢量和终点C、温度、出钢口、脱氧情况等因素进行调整。
合金加入量计算公式:
合金加入量=钢种规格中限%-终点残余成分%/铁合金中合金元素含量%×合金元素吸收率%×1000
8.4合金化要求:
钢种成分按照工艺卡要求执行
8.5加入时间:
对准钢流出钢1∕3时开始加入到3∕4时加完。
8.6各种合金的吸收率
Si
Mn
Ti
V
Cr
P
Nb
≤0.08
65-75
70-80
45-60
80-90
90-95
与Si的
80-90
0.08-0.15
70-80
75-85
55-70
85-95
90-95
吸收率
-
≥0.16
75-85
80-90
-
90-95
90-95
相同
-
9.吹氩作业标准
9.1吹氩必须采用底吹方式,当底吹不透时,可采用氩棒顶吹,但氩棒必须干燥。
9.2吹氩开气时,要缓慢开启阀门,调整吹氩强度。
用氩棒时必须先开气再降棒。
9.3吹氩强度控制:
吹氩前期1分钟采用大氩气量,之后采用软吹,钢面微微波动即可。
9.4吹氩时间控制:
50t包必须大于8min
40t包必须大于6min
品种钢按工艺卡要求执行。
9.5后吹20s以上或后吹二次以上的钢水,吹氩时间延长2min。
9.5采用顶吹方式时,如氩棒中部漏气或直径小于新棒1/2或长度不足棒长3/5时,必须更换。
9.6采用顶吹方式时,氩棒必须降至最低点或距离包底300-400mm处调整吹氩强度至要求控制范围。
10.冶炼回炉钢作业标准
10.1发生回炉钢必须清楚回炉原因、钢种、数量,禁止折包或隐瞒不报。
10.2处理回炉钢时,装入量必须准确,严禁超装。
10.3满包钢需要回炉处理时,必须分二次回炉,每次回炉钢量不能超过装入量的一半。
10.4处理低温回炉钢必须在20min以内完成,以防温度损失严重造成钢包不能使用。
10.5大约3t回炉钢相当于1t废钢的冷却效应。
10.6当回炉钢量大,温度不足时,可采用加入Fe-Si提温。
禁止干吹。
10.7回炉钢的冶炼:
10.7.1按补充的铁水的成分和数量配加渣料。
回炉钢量大时,渣料可一次加入。
终渣R按2.8-3.0控制。
10.7.2枪位控制要比正常冶炼时降低50-100mm,保证熔池搅拌均匀,但要防止烧枪和金属喷溅。
10.8冶炼回炉钢注意终点脱氧和合金化。
钢水氧化性比较强,不能造成翻包。
合金吸收率比正常时偏低5%左右。
同时注意考虑钢中余Mn。
余Mn可按30-40%考虑。
10.9冶炼的回炉钢水禁止开新机使用。
11.冶炼高S铁水的作业标准
11.1高S(≥0.050%)铁水不能冶炼品种钢。
同时,加强生产组织协调,保证炉机匹配。
11.2当在冶炼终点发现S高时,必须及时采取措施处理,倒掉一部分终渣,从造新渣。
当氧化样低于工艺卡内控要求时,方可出钢。
11.3当铁水S高,按正常冶炼不能满足钢种需要时,必须采用双渣操作。
渣料白灰最多可加入120㎏/t。
同时,可加入Mn-Si帮助去S。
11.3.1装入量按正常装入量的95%装入,降低废钢比到10%。
废钢采用优质废钢。
当铁水S≥0.070%时,采用全铁水炼钢。
11.3.2冶炼过程要全程化渣,可按3-4kg/t钢加入萤石,保证渣子良好的流动性,创造脱S的条件。
11.3.3过程温度控制要高些。
终点温度按钢种上限控制出钢。
11.3.4终渣R按3.5-4.0左右控制。
合金化时,Mn按中上限配加。
11.4高S铁水冶炼的钢水必保吹氩时间≥5min,喂Ca-Si线1m/t,并在吹氩站调整好温度。
11.5在吹氩站用定氧枪定氧,控制钢水的氧活度在40-60ppm范围以内。
12.氧枪漏水更换及倒氧枪作业标准
12.1氧枪漏水成线时,必须及时倒枪更换。
12.2倒氧枪时,电钳工到现场监护操作工操作。
并确认每步操作正确。
12.3首先确保氧枪能提出氮封口,并提到最高点。
同时,把高压水、氧气、氮气转换到备用氧枪。
12.4提到最高点后,拔横移小车出固定销,开动横移小车,把备用氧枪与滑道对正,插好横移小车的固定销,降枪。
12.5降枪时,氮封口处有专人扶枪并指挥。
氧枪降到氮封口以内后,确认烟道内无粘钢顶卡,氧枪钢丝绳卷曲规范、无压绳、乱绳,高压水、氧气、氮气正常后转入正常操作。
13.转炉维护标准
13.11、主任要每天观察炉况,及时调整操作。
炼钢工、渣料工、一助手要炉炉观察炉况及终渣情况,做到看好渣、调好渣、溅好渣。
13.2溅渣终渣成份:
碱度控制在2.6-2.8,若炉况不佳可适当提高。
渣中氧化镁含量为8—12%,氧化铁含量控制在FeO<15%,后吹钢水的炉渣FeO偏高可提高MgO到11%-13%,以提高炉渣耐火度。
13.3溅渣渣量:
根据铁水Si及加入的渣料多少,控制留渣量,加入的渣料不多时,在倒炉测温取样时,尽量少倒渣;加入的渣料较多时,在倒炉测温取样时可多倒些渣,以利于溅渣。
13.4溅渣时间:
一般控制在2-3分钟左右,一次倒炉的炉渣粘度合适,留渣量合适,一般在2分钟即可溅好,后吹的炉渣,氧化性强,在溅渣时需加100-200公斤镁球先调渣,待加入的镁球熔化后,渣子变粘,再进行正常溅渣,时间控制在3分钟左右。
条件允许可适当延长。
13.5溅渣枪位:
出完钢,摇正炉体,先高枪位放氮气10-20秒,初步将渣子及炉膛打凉(适宜溅渣)。
根据炉衬的侵蚀情况,有针对性的溅渣。
溅熔池、耳轴,则枪位按上限控制;溅炉帽,则枪位按下限控制;正常情况下,则上下匀速动枪,以期做到炉衬溅渣层厚度均匀。
13.6大小面根据实际情况可进行挂渣操作,挂渣无效时及时安排垫料,避免小面出钢不净影响溅渣效果。
13.7加强操作,杜绝高低温钢,减少高氧化渣对炉衬的化学侵蚀。
13.8铁水铁块S高时,调整渣料和R或调锰铁提高脱硫率,避免严重后吹侵蚀炉衬。
13.9生产组织保证氮气压力在10Mpa以上,溅渣使用充足。
杜绝因生产事故造成的泡炉发生,泡炉时间不得超过20分钟。
14.喷溅的预防与控制
14.1预防喷溅的原则:
(1)控制好熔池温度,保证前期温度不过低,中、后期温度不过高
严格避免熔池温度突然降低
(2)保证脱碳反应均衡地进行,消除爆发性的脱碳反应。
(3)控制好渣中(FeO)含量,保证渣中(FeO)不出现积聚现象,以避免炉渣泡沫化程度严重,或引起爆发性的碳氧反应。
14.2前期喷溅及控制
(1)泡沫渣形成过多溢出炉口时形成喷溅,泡沫渣形成的条件有:
①表面张力。
刚开吹炉渣粘度大,温度低,表面张力大,减小表面张力利于炉渣泡沫化。
②粘度。
合适的粘度使CO气泡稳定,促进泡沫渣形成,粘度的大小取决于炉渣碱度和熔池温度。
③脱碳反应速度快时有利于泡沫渣的形成。
(2)影响炉渣泡沫化程度的因素有(FeO)、碱度、脱碳速度及渣量四方面:
①(FeO)的影响。
降低前期(FeO)的生成量,使熔池温度尽快升温。
②碱度的影响。
碱度在1.5-1.7时炉渣泡沫化程度最大,尽量避开这一碱度范围。
③脱碳速度。
使脱碳速度保持平稳,避免爆发性碳氧反应。
④前期渣量。
渣量大时必然导致泡沫渣总量增加。
(3)在实际生产中,炉前操作者通过控制氧压、枪位、造渣材料加入方法来控制(FeO)、脱碳速度及炉渣碱度。
①开吹氧压应偏高,枪位应尽可能低,增加直接传氧,加快碳氧反应速度,减少渣中(FeO)的富集。
②随着冶炼进行,碳氧反应激烈可观察到炉口有渣片溅出,这时应根据火焰变化及炉口甩渣情况逐步提枪并减小氧气压力。
硬吹→软吹
③随着脱碳进行,渣中(FeO)以间接传氧的方式被消耗掉一部分,炉渣泡沫化程度逐渐降低,此时应逐渐低枪位,保持合理的(FeO)含量。
④石灰加入应使熔池碱度满足吹炼要求,开吹的同时加入一定数量的造渣材料,尽量提高熔池前期碱度,超过最有利于炉渣泡沫化的碱度范围。
⑤减少前期渣量,将上炉钢富含S、P的炉渣倒入渣罐。
2、中、后期喷溅及其控制
(1)后期喷溅的分类
爆发性喷溅:
指由于操作上的原因抑制了碳氧反应,(FeO)大量聚积,当渣(FeO)超过20%时,由于中、后期温度较高,碳的氧化反应重新以更猛烈的速度进行,瞬间排出大量CO气体,巨大的搅拌能量夹带着金属液和炉渣瞬时从熔池排出。
(多发生在处理返干和氧枪熄火时)
泡沫渣喷溅:
指由于枪位长时间偏高,使(FeO)的生成速度大于(FeO)的消耗速度,造成(FeO)聚积,此时炉渣中大量的CO气泡不能自由移动和聚合长大,不能顺利从炉渣中排出,导致液态渣体积持续增加而从炉口溢出。
(2)后期喷溅的主要原因:
渣中的(FeO)和熔池温度控制不当,而枪位和氧压是影响渣中(FeO)含量的主要因素。
(3)调整枪位和氧压来处理返干
枪位合适时,渣中(FeO)的消耗与生成保持平衡,炉渣既不返干,也不喷溅。
炉渣返干时,首先提高枪位,视返干程度降低氧压。
火焰变软后,首先降低枪位,待火焰稳定后,再提高氧压。
总之,处理返干的全过程都应使熔池保持较低的脱碳速度。
(4)冷却剂使用过程要注意喷溅的发生
冷却剂的作用:
一是降低熔池温度;二是增加渣中(FeO)。
处理方法:
①熔池温度偏高时,向熔池中加入冷却剂,补充渣中(FeO),并适当降低熔池温度,避免因熔池温度剧烈上长使炉渣返干。
②熔池温度偏低时,采用调整枪位和氧压的方法使渣中(FeO)的生成和消耗保持平衡,使吹炼操作平稳运行。
第二部分铁水预处理操作标准
1.操作前的准备
1.1打开脱硫站供电总电源,给相关系统供电。
1.2检查其它各种能源介质的供给情况,如氮气等,是否符合需要的参数。
1.3检查喷吹罐和储镁仓中存料情况,如果料量偏少,应当及时补充加料。
1.4检查所有机、电、液设备的状况,是否处于可使用的完好状况。
1.5按照润滑和维护的要求进行工作前的必要的润滑和维护工作。
1.6联系铁水罐,了解铁水情况、重量反馈至主控室。
1.7联系吊车,吊车应当将铁水情况。
1.8检查渣罐车及渣罐是否到位。
2.操作工艺:
2.1将铁水罐倾翻车开到处理工位。
2.2进行测温取样操作。
铁样必须无夹渣、无气孔。
2.3将铁水罐号、初始硫值、铁水重量、目标硫值、预定的喷吹速度都输入专家系统,然后即可启动喷吹按钮进行自动喷吹。
2.4喷吹完成后再次操作测温取样。
2.5然后操作扒渣机和倾翻铁水罐进行扒渣作业。
2.6完成扒渣后扒渣杆收回、铁水罐回复直立,开动铁水罐车至待罐位,等待吊车吊运铁水罐至转炉。
3.发生报警时应采取的措施
3.1喷吹罐中料量少于设定值(50kg)时:
在操作室有声光报警,应当采取的措施:
立即按动自动上料按钮,即可按照程序从储镁仓向喷吹罐供料。
3.2储镁仓中料量少于设定值(500kg)时:
在操作室有声光报警,应当采取的措施:
立即调度汽车载颗粒镁料袋至现场,操作悬臂吊,吊料袋到高位料仓,打开蝶阀,向储镁仓加料。
3.3喷吹罐前氮气压力低于设定下限值(0.5MPa)时:
在操作室有声光报警,应当采取的措施:
立即与供气部门联系,要求增加氮气压力。
同时应当检查脱硫站氮气管路或阀门有无泄露等情况。
4.脱硫处理中应当注意的事项及发生故障时应采取的消除故障的方法
4.1密切观察喷吹中铁水翻腾的情况,如果过于激烈,有较多的铁水喷溅,应当分次、微小地调小氮气压力,调一次后观察情况再决定是否第二次调整。
切勿连续或大幅调整,以免由于压力低造成堵枪。
如果铁水翻腾趋于平静,说明有堵枪的趋势或者已经堵枪。
4.2密切观察喷吹罐电子秤残料量的变化和喷吹量流量表,如果发现变化缓慢甚至停止,说明有堵枪的趋势或者已经堵枪;
4.3堵枪的原因主要有:
4.3.1给料速度过大;
4.3.2氮气压力波动过大或氮气压力下降;
4.3.3颗粒镁料中有大的异物;
4.3.4输镁管路中有异物,包括法兰中密封垫位置偏移,造成通道减小;
4.3.5输镁管路曲率半径过小,造成输送镁粒困难;
4.3.6喷镁操作程序发生错误;
预防堵枪就必须对上述各点密切注意,妥善掌握和排除造成堵枪的问题。
4.4发生堵枪的处理方法
4.4.1立即提升喷枪到上极限,同时打开助吹阀门,停止给料电机工作,关闭主吹阀门;