塑料模具课程设计说明书赖东双.docx
《塑料模具课程设计说明书赖东双.docx》由会员分享,可在线阅读,更多相关《塑料模具课程设计说明书赖东双.docx(28页珍藏版)》请在冰豆网上搜索。
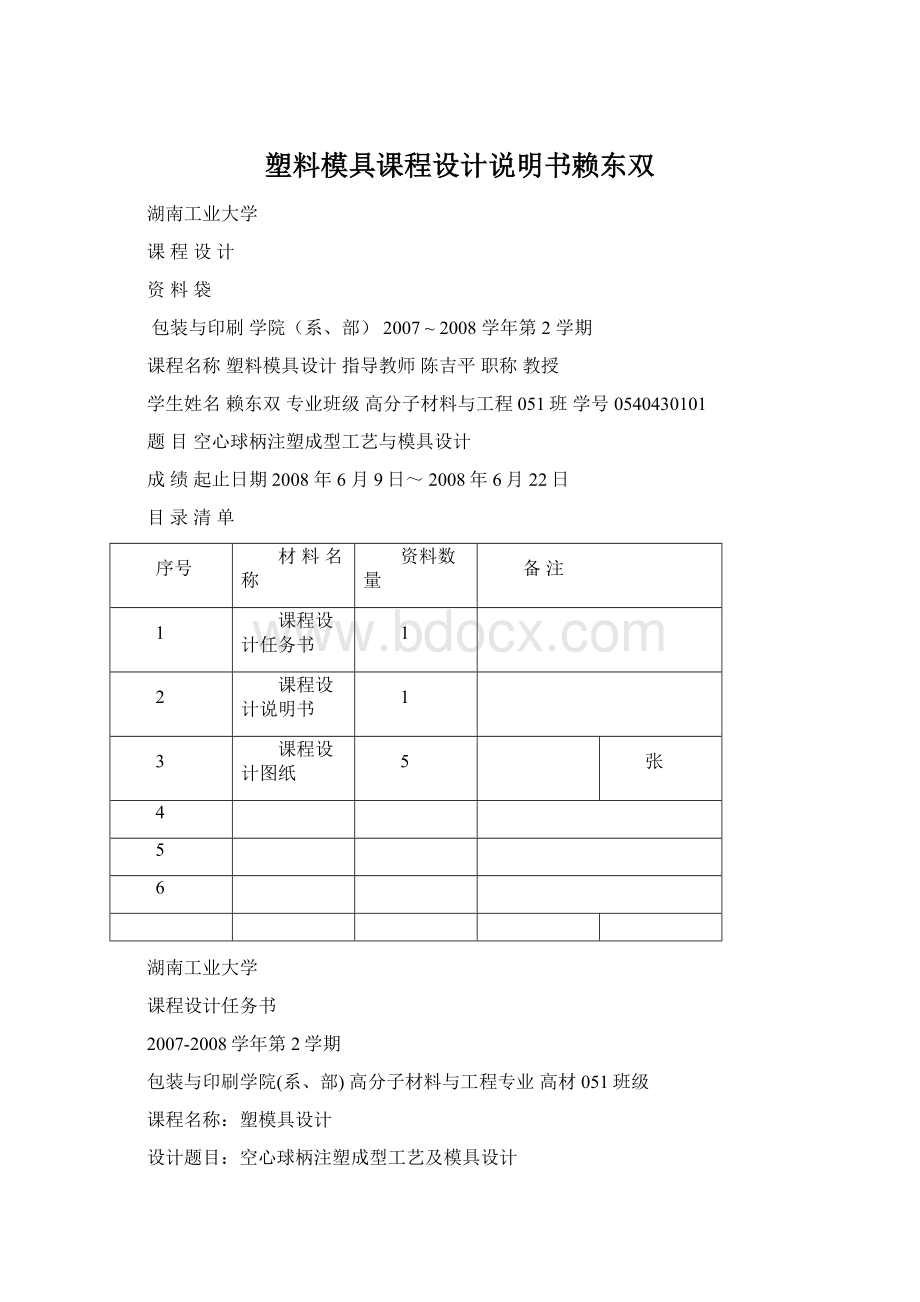
塑料模具课程设计说明书赖东双
湖南工业大学
课程设计
资料袋
包装与印刷学院(系、部)2007~2008学年第2学期
课程名称塑料模具设计指导教师陈吉平职称教授
学生姓名赖东双专业班级高分子材料与工程051班学号0540430101
题目空心球柄注塑成型工艺与模具设计
成绩起止日期2008年6月9日~2008年6月22日
目录清单
序号
材料名称
资料数量
备注
1
课程设计任务书
1
2
课程设计说明书
1
3
课程设计图纸
5
张
4
5
6
湖南工业大学
课程设计任务书
2007-2008学年第2学期
包装与印刷学院(系、部)高分子材料与工程专业高材051班级
课程名称:
塑模具设计
设计题目:
空心球柄注塑成型工艺及模具设计
完成期限:
自2008年6月9日2008年6月22日共2周
内容及任务
1、独立拟订塑件(见产品附图)的注塑成型工艺,正确选用成型设备;
2、合理设计模具结构,绘制注射模具总装图一张(CAD绘制成A1图幅);
3、合理设计模具零件图结构,绘制注射模具零件图纸4张(CAD绘制成A3或A4图幅);
4、编写设计计算说明书一份(A4幅面,20页左右)
进度安排
起止日期
工作内容
6.9
设计准备工作
6.10
拟订设计方案
6.11至6.13
装配草图的绘制
6.14至6.15
装配图的绘制
6.16至6.18
零件工作图的绘制
6.19至6.21
编写设计说明书
6.22
答辩
主要参考资料
[1]黄虹主编.塑料成型加工与模具.北京:
化学工业出版社.,2003年8月
[2]申开智主编.塑料成型模具.北京:
中国轻工业出版社,2002.
[3]李德群主编.塑料成型工艺及模具设计.北京:
机械工业出版社,1994.
[4]黄锐主编.塑料成型工艺学.北京:
中国轻工业出版社,1997.5
[5]徐佩弦.高聚物流变学及其应用.北京:
化学工业出版社,2003.
[6]塑料模具编写组.塑料模具设计手册.北京:
机械工业出版社,1985.
[7]黄锐主编.塑料工程手册.北京:
机械工业出版社,2000.
[8]徐佩弦.塑料制品与模具设计.北京:
中国轻工业出版社,2001.
指导教师(签字):
________________年月日
系(教研室)主任(签字):
_________________年月日
空心球柄产品图
材料HDPE
二维图
三维图
技术要求:
1.塑件外表光滑,无注塑缺陷;
2.脱模斜度30’—1°
3.中批量生产
4未注圆角R1—R2
《塑料成型模具设计》课程设计
设计说明书
空心球柄注塑成型工艺及模具设计
起止日期:
2008年6月9日至2008年6月22日
学生姓名
赖东双
班级
高材051班
学号
0540430101
成绩
指导教师(签字)
包装与印刷学院
08年6月22日
目录
第1章塑料成型工艺性分析·····································································7
1.1塑件分析··································································································7
1.2性能分析··································································································7
1.3注射工艺参数··························································································8
第2章分型面位置的分析和确定···························································8
2.1分型面的选择原则····················································································8
2.2分型面选择方案························································································9
第3章塑件型腔数量及排列方式的确定··············································9
3.1数量·······································································································9
3.2排列方式································································································9
第4章注射机的选择和有关工艺参数的校核···································10
4.1所需注射量的计算················································································10
4.2塑件和流道凝料在分型面上的投影面积及所需锁模力的计算·············10
4.3注射机型号的选定················································································11
4.4有关工艺参数的校核·············································································11
第5章浇注系统的形式选择和截面尺寸的计算·······························13
5.1主流道的设计···························································································13
5.2冷料穴的设计···························································································14
5.3分流道的设计···························································································14
5.4浇口设计··································································································16
5.5浇注系统的平衡·······················································································17
第6章成型零件的设计及力学计算························································17
6.1成型零件的结构设计············································································17
6.2成型零件工作尺寸计算········································································17
6.3成型零件的强度及支撑板厚度计算······················································19
第7章模架的确定和标准件的选用······················································20
第8章导向机构的设计············································································20
第9章脱模机构的设计·············································································21
第10章温度调节系统的设计···································································22
第11章模具总体结构·············································································24
第12章设计总结························································································25
参考文献··········································································································26
第1章塑料成型工艺性分析
1.1塑件分析
(1)结构分析
该塑件为HEPE空心球柄,外形为光滑的球面,外表光滑,无注射缺陷,无翘曲变形,外观质量要求较高,尺寸精度要求相对较低。
因此,在模具设计和制造时要有精密的定位措施和良好的加工工艺,以保证空心球各尺寸的吻合、和形状的逼真。
无侧凹侧孔侧槽,结构简单,易于用模具成型。
由于中间管较长,故设计脱模机构时需采用特殊脱模机构。
(2)成型工艺性分析
生产纲领:
中批量生产。
精度等级:
由表3—3[1]查得,采用一般精度6级。
(3)脱模斜度:
该塑件厚度约为2mm,由于该塑料的收缩率较小,形状比较简单,高度较大,孔隙较深,又由表3—4[1]查得其型腔脱模斜度20'—45',型芯脱模斜度为25'—45'。
1.2性能分析
(1)使用性能
高密度聚乙烯的产生:
聚乙烯按聚合时采用的压力不同分为高压,中压,低压。
低压聚乙烯的分子链上支链较少,相对分子质量大,结晶度和密度较高,因此称为高密度聚乙烯。
广泛应用于制造塑料管、塑料板、塑料绳,以及承载不高的零件,如齿轮轴、手柄等。
(2)主要性能指标
表1-1[4]
密度(g/cm3)
0.94~0.96
比体积(cm3/g)
1.03~1.06
吸水率(%)
≤.01
玻璃化温度(oc)
-120~-125
熔点(oc)
105~137
成型收缩率(%)
1.5~3.0
比热容(J/(kg.k))
2310
屈服强度(MPa)
22~30
抗拉强度(MPa)
27
拉伸弹性模量(GPa)
0.84~0.95
抗弯强度(MPa)
27~40
弯曲弹性模量(MPa)
1.1~1.4
抗压强度(MPa)
22
泊松比
0.38
(3)成型性能
结晶料吸湿性小;
流动性极好,溢边值0.02mm左右,流动性对压力敏感;
可能发生熔融破裂,与有机溶剂接触可能发生开裂;
加热时间过长则发生分解烧焦;
冷却速度慢,因此必须充分冷却,宜设冷料穴,模具应有冷却系统;
收缩率范围大,应控制模温,保持冷却,均匀稳定;
⑦高压低温注射,料温均匀,填充速度快,保压充分;
⑧宜用直接进料口,可能产生收缩不均匀,应选择进料的位置与数量,防止产生缩孔和缩松;
⑨质软易脱模。
1.3注射工艺参数
表1-2[1]
注射成型机类型
螺杆式
转速(r/min)
30~60
料筒温度(℃)
中段180~200
喷嘴温度(℃)
150~180
模具温度(℃)
30~60
喷嘴形式
直通式
注射压力(MPa)
70~100
保压力(MPa)
40~50
注射时间(s)
0~5
保压时间(s)
15~60
成型周期(s)
40~140
冷却时间(s)
15~60
第2章分型面位置的分析和确定
2.1分型面的选择原则
在塑件设计阶段,就应该考虑成型时分型面的形状数量,否则就无法用模具成型。
在模具设计阶段,应首先确定分型面的位置,然后才选择模具的结构。
分型面选择是否合理,对塑件质量工艺,操作难易程度和模具设计制造有很大影响。
因此分型面的选择是注射模设计中的一个关键因素。
选择分型面总的原则是保证塑件质量,且便于制品脱模和简化模具结构:
由参考书[1]可知
分型面的选择应便于塑件脱模和简化模具结构,选择分型面应尽量使塑件开模时留在动模;
分型面应尽可能选择在不影响外观的部位,并使其产生的溢料边易于消除和修整;
分型面的选择应保证塑件尺寸精度;
分型面选择应有利于排气;
分型面选择应便于模具零件的加工;
分型面选择应考虑注射机的规格。
2.2分型面选择方案
根据上述选择原则和该塑件的形状,选择分型面方案如下,如图1-1所示:
图2-1
分型面与开模方向平行,置于最大截面处,塑件包紧在动模型芯上。
利用推出机构易于推出,开模行程合理,模具结构简单,制造方便,塑件成型精度高,能够满足要求。
经分析可知,该模具结构简单,塑件成型精度可靠。
第3章塑件型腔数量及排列方式的确定
3.1数量
分型面确定以后,就需要考虑是采用单型腔模还是多型腔模。
一般来说,大中型塑件和塑件精度要求较高的小型塑件优先采用一模一腔的结构。
但对于精度要求不高的小型塑件(没有配合精度要求),形状简单,又是大批量生产时,若采用多型腔模可使生产率大为提高且降低成本。
结合塑件的批量、质量要求、塑料的品种形状尺寸、塑件的生产成本及所选用的技术要求和规范,本套模具选择一模四腔。
3.2排列方式
多型腔模具设计的重要问题之一就是浇注系统的布置方式。
由于型腔布置方式与浇注系统布置密切相关,因而型腔的排布在多型腔模具设计中应加以考虑:
(1)型腔的布置应使每个型腔都通过浇注系统从总压力中均等的分得所需要的足够的压力;
(2)型腔与主流道之间的距离应尽可能的短,同时采用平衡的流道和合理的尺寸以及均匀分布的冷却系统等。
综上所述,采用的布置如图3-1所示:
图3-1
第4章注射机的选择和有关工艺参数的校核
注射模是安装在注射机上使用的工艺装备,因此设计注射模时应该详细了解现有注射机的技术规格才能设计出符合要求的模具。
注射机规格的确定主要是依据塑件的大小及型腔的数目和排列方式。
在确定模具结构形式及初步估算外形尺寸的前提下,设计人员应对模具所需的注射量、锁模力、注射压力、拉杆间距、最大和最小模具厚度、推出形式、推出位置和开模距离等进行计算。
4.1所需注射量的计算
(1)塑件质量和体积的计算
对于该设计,用户提供了塑件样图,据此进行三维建模,对其分析得:
塑件体积V1≈17.55cm3
塑件质量m1=ρV1≈0.95×17.55=16.67g
(2)浇注系统凝料体积的估算
可按塑件体积的0.6倍计算,由于该模具采用一模四腔,所以浇注系统凝料体积为V2=4V1×0.6=4×17.55×0.6=42.12cm3
(3)该模具一次注射所需塑料
体积V0=4V1+V2≈4×17.55+42.12=112.32cm3
质量m0=ρV0≈0.95×112.32=106.70g
4.2塑件和流道凝料在分型面上的投影面积及所需锁模力的计算
流道凝料(包括浇口)在分型面上的投影面积为A2,在模具设计前是个未知数,根据多型腔模的设计分析,A2是每个塑件在分型面上的投影面积A1的0.2~0.5倍。
因此可用0.35A1来进行计算,所以:
A=nA1+A2=nA1+0.35nA2=1.35nA1
A1=πR2/4=3.14×20×20/4=314mm2
A=1.35×4×314=1695.6mm2
则Fm=A×P型=1695.6×25=42390N=42.39KN
4.3注射机型号的选定
由上述数据查阅参考文献[1]附录6及参考文献[3]选注射机型号为XS-ZY-250,基本参数如表4-1所示:
表4-1
螺杆直径
50mm
额定注射量
250mm3
额定注射压力
130MPa
锁模力
1800KN
最大成型面积
550cm2
最大开模行程
500mm
顶出行程
100mm
最大模具厚度
350mm
最小模具厚度
200mm
螺杆转速
25-89r/min
定位孔直径
Ø125+0.006
推出孔径
Ø40
两侧孔距
280mm
喷嘴球半径
SR18mm
孔直径
Ø4
4.4有关工艺参数的校核
(1)按注射机的最大注射量校核型腔数量
公式4-2[3]
式中K—注射机最大注射量的利用系数,一般取0.8;
Vn—注射机允许的最大注射量cm3;
V2—浇注系统所需塑件的体积cm3;
V1—单个塑件的体积cm3。
左边=4,右边=
,满足要求。
(2)注射量的校核
根据生产经验,注射机的最大注射量是其允许最大注射量的80%,由参考文献[3]式4-4有:
nV1+V2≤80%Vn
式中Vn—注射机允许的最大注射量cm3;
V2—浇注系统所需塑件的体积cm3;
V1—单个塑件的体积cm3。
左边=112.32cm3,右边=80%×250=200cm3,满足要求。
(3)塑件在分型面上的投影面积与锁模力的校核
计算投影面积与锁模力远小于所选注射机的投影面积和锁模力,满足要求。
(4)注射压力的校核
所选注射机额定注射压力为130MPa,该塑件的注射压力为70-100MPa,由于选用的是螺杆式注射机,其注射压力的传递比柱塞式要好,同时HDPE流动性好,因此注射压力选用80MPa,注射应满足:
Pmax≥k’P0
式中max—注射机额定注射压力;
P0—注射成型时所用的注射压力;
k’—安全系数,常取k’=1.25~1.4。
左边=130MPa,右边=1.25×80~1.4×80=100~112MPa,满足要求。
(5)模具厚度的校核
模具厚度指模板闭合后达到规定锁模力时,动模板与定模板之间的距离。
厚度H应满足:
Hmin≤H≤Hmax
对于所选注射机,式中Hmin=200mm,Hmax=350mm,
厚度为H=40+20+25+25+114+20mm=243mm,满足要求。
(6)开模行程的校核
XS-ZY-250式注射机为全液压式注射机,注射机最大开模行程与模具厚度有关,必须满足:
Sk-Hm≥S
式中Sk—注射机的最大开模行程;
Hm—模具闭合高度;
S—开模距离。
对于单分型面,S=H1+H2+(5~10)=64+62+8mm=134mm,
即Sk≥Hm+S=243+134=377,满足要求。
综上所述,注射机选择合理,能够满足使用要求。
第5章浇注系统的形式选择和截面尺寸的计算
所谓浇注系统是指注射模中从主流道的始端到型腔之间的熔体进料通道。
浇注系统可分为普通流道浇注系统和无流道浇注系统两类。
普通浇注系统由主流道、分流道、浇口、冷料穴四部分组成。
浇注系统的作用是使来自注射模喷嘴的塑料熔体平稳而顺利的充模、压实、保压。
5.1主流道的设计
主流道是浇注系统中从喷嘴与模具相接触部位开始,到分流道为止的塑料熔体的流动通道,属于从热的塑料熔体到相对较冷的模具中的过渡阶段,因此它的形状和尺寸非常重要。
主流道部分在成型过程中,其小端入口处与注射机喷嘴及一定温度和压力的塑料熔体冷热交换的反复接触,属于易损件,对材料的要求高,因而模具的主流道部分常设计成可拆卸更换的主流道衬套式—浇口套。
主流道部分尺寸如下:
(1)主流道小端直径d=注射机喷嘴直径+(0.5~1)
=4+0.5mm=4.5mm;
(2)主流道球面半径SR=注射机喷嘴球面半径+(1~2)
=18+1mm=19mm;
(3)球面配合高度h=3~5,取h=3mm;
(4)主流道锥角α=2°~6°,取α=4°;
(5)主流道长度L尽量≤60mm,取L=40-3mm=37mm;
(6)主流道大端直径D=d+2Ltg
=7.15mm,取D=7.2mm。
主流道衬套及定位圈的固定形式如图5-1所示:
图5-1
5.2冷料穴的设计
冷料穴的作用是贮存两次注射间隔而产生的冷料及熔体流动前锋冷料,以防止熔体冷料进入型腔。
冷料穴一般设置在主流道的末端,当分流道较长时,在分流道的末端有时也设冷料穴。
同时冷料穴兼有分模时将主流道凝料从主流道衬套中拉出并滞留在动模一侧。
本设计采用推板脱模机构,采用代球形头的冷料穴,适用于弹性较好的HDPE,结构如图5-2所示:
图5-2
5.3分流道的设计
(1)分流道的布置形式
分流道在分型面上的布置与前面所述型腔排列密切相关,有多种不同的形式,但应遵循两个方面的原则:
一是排列紧凑,缩小模板尺寸,二是流程尽量短,锁模力均匀。
该流道布置采用平衡式,其布置形式如图5-3所示即为最佳:
图5-3
(2)分流道的长度
长度应尽可能短,结合模具尺寸结构,取分流道长度L=20mm。
(3)分流道形状及尺寸
圆形分流道截面积虽然效率高,但其是以分型面为界分成两半进行加工才利于凝料脱出,因而其加工工艺性不佳,不予采用。
许多模具设计采用梯形截面,加工工艺性好,且塑料熔体的热量散失,流动阻力均不大,一般采用如下公式5-5,5-6[3]确定截面尺寸的大小,即:
式中B—梯形大底面的宽度,mm;
m—塑件质量,g;
L—分流道的长度,mm;
H—梯形高度,mm。
注:
上述公式的适用范围,塑件厚度在3mm以下,质量小于200g且B的计算结果在3.2~9.5mm才合理。
符合公式的应用范围,可以采用。
其截面形状尺寸如图5-4所示:
图5-4