GC型水冷板甲醇合成反应.docx
《GC型水冷板甲醇合成反应.docx》由会员分享,可在线阅读,更多相关《GC型水冷板甲醇合成反应.docx(10页珍藏版)》请在冰豆网上搜索。
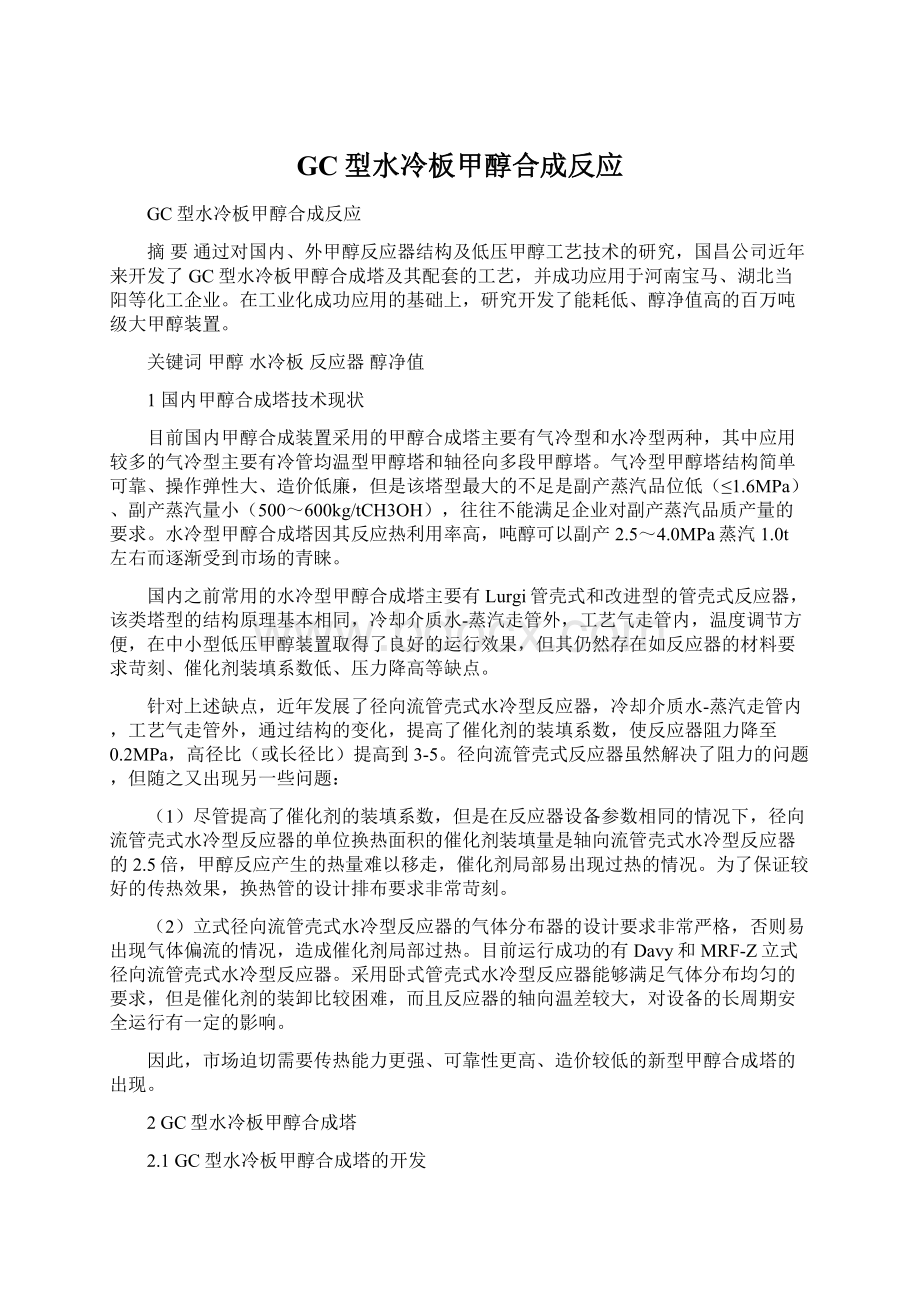
GC型水冷板甲醇合成反应
GC型水冷板甲醇合成反应
摘要通过对国内、外甲醇反应器结构及低压甲醇工艺技术的研究,国昌公司近年来开发了GC型水冷板甲醇合成塔及其配套的工艺,并成功应用于河南宝马、湖北当阳等化工企业。
在工业化成功应用的基础上,研究开发了能耗低、醇净值高的百万吨级大甲醇装置。
关键词甲醇水冷板反应器醇净值
1国内甲醇合成塔技术现状
目前国内甲醇合成装置采用的甲醇合成塔主要有气冷型和水冷型两种,其中应用较多的气冷型主要有冷管均温型甲醇塔和轴径向多段甲醇塔。
气冷型甲醇塔结构简单可靠、操作弹性大、造价低廉,但是该塔型最大的不足是副产蒸汽品位低(≤1.6MPa)、副产蒸汽量小(500~600kg/tCH3OH),往往不能满足企业对副产蒸汽品质产量的要求。
水冷型甲醇合成塔因其反应热利用率高,吨醇可以副产2.5~4.0MPa蒸汽1.0t左右而逐渐受到市场的青睐。
国内之前常用的水冷型甲醇合成塔主要有Lurgi管壳式和改进型的管壳式反应器,该类塔型的结构原理基本相同,冷却介质水-蒸汽走管外,工艺气走管内,温度调节方便,在中小型低压甲醇装置取得了良好的运行效果,但其仍然存在如反应器的材料要求苛刻、催化剂装填系数低、压力降高等缺点。
针对上述缺点,近年发展了径向流管壳式水冷型反应器,冷却介质水-蒸汽走管内,工艺气走管外,通过结构的变化,提高了催化剂的装填系数,使反应器阻力降至0.2MPa,高径比(或长径比)提高到3-5。
径向流管壳式反应器虽然解决了阻力的问题,但随之又出现另一些问题:
(1)尽管提高了催化剂的装填系数,但是在反应器设备参数相同的情况下,径向流管壳式水冷型反应器的单位换热面积的催化剂装填量是轴向流管壳式水冷型反应器的2.5倍,甲醇反应产生的热量难以移走,催化剂局部易出现过热的情况。
为了保证较好的传热效果,换热管的设计排布要求非常苛刻。
(2)立式径向流管壳式水冷型反应器的气体分布器的设计要求非常严格,否则易出现气体偏流的情况,造成催化剂局部过热。
目前运行成功的有Davy和MRF-Z立式径向流管壳式水冷型反应器。
采用卧式管壳式水冷型反应器能够满足气体分布均匀的要求,但是催化剂的装卸比较困难,而且反应器的轴向温差较大,对设备的长周期安全运行有一定的影响。
因此,市场迫切需要传热能力更强、可靠性更高、造价较低的新型甲醇合成塔的出现。
2GC型水冷板甲醇合成塔
2.1GC型水冷板甲醇合成塔的开发
国昌公司在发展轴径向多段塔技术的同时,密切关注国内外水冷型甲醇合成塔技术的发展,并结合自身的技术优势,对现有的技术在应用中所暴露出的一些弱点进行改进,在新塔型的开发中,力求在强化传热、结构安全可靠、降低造价和易于大型化方面取得新的突破。
第一台φ2800GC型水冷板甲醇合成塔于2007年2月在河南宝马化肥厂投运成功,设计压力5.5MPa,年生产能力达到15万吨。
GC型水冷板甲醇合成塔由外壳和内件两部分组成,外壳和内件分别独立制造和运输,现场组装。
内件由径向分布器1、径向集气筒2、分水联箱3、集水联箱4、换热板5等主要元件组成(见图1)。
GC型水冷板甲醇合成塔流程:
气体由上部进入,沿外壳与内件间的环隙经径向分布器进入催化剂床层,在催化剂床层内气体不断改变
气流方向,来自第一层两换热板之间的气体分 图1GC型水冷板反应器
别沿顺时针及逆时针两个切线方向流经第一层换热板与第二层换热板之间催化剂床层(第2层催化剂床层),然后气体由经过第二层换热板与左右两块换热板之间形成的气流通道进入第二层换热板与第三层换热板之间的催化剂床层(第3层催化剂床层),气体重复上述流动方向及路径,不断改变流动方向和另一方向过来的图2气体流向示意图
气体混合,一直到达第n层换热板,由第n层换热板之间缝隙进入第n+1催化剂床层,气体分别沿顺时针及逆时针两个切线方向流经第n+1催化剂床层后进入径向集体筒,由径向集体筒内部中心管流出反应器(见图2)。
锅炉水通过下降管进入分水联箱,自下而上经过每一块换热板吸收催化剂床层反应放出的热量,经换热板内部到达上部集水联箱,经上升管到达汽包进行汽水分离,产生的饱和蒸汽送入蒸汽管网,过饱和水蒸发出蒸汽。
2.2GC型水冷板甲醇合成塔的技术特点
GC型水冷板甲醇合成塔具备一般水冷型塔的副产蒸汽品位高、产量大,操作简单等优点,还具有独特的优点,归结起来主要有以下几点:
(1)气体径向、折流分布技术
GC型水冷板甲醇合成塔气体径向分布技术采用径向层分气流侧和集气流侧两向小孔同时补偿的专利技术ZL200620077859.3和鱼鳞筒二次分布器专利技术ZL200520077058.2,使气体分布均匀。
工艺气从塔顶进入到壳体与内件间的环隙,经不等径小孔一次分布后再经鱼鳞筒进行二次分布,然后切向进入催化剂床层,提高了催化剂床层气体分布的均匀度及催化剂的利用率。
催化剂床层设置板式水冷换热结构,换热板采用独特的同心圆环成组错行排列,使气流沿径向在每组换热板之间反复折流绕行,有效避免了纯径向流气体流程短,分布不易均匀的缺陷。
GC型水冷板甲醇合成塔采用了径向流分布和折流水冷板相结合的新颖结构,径向流分布器具有流体阻力低的最大优点,催化剂床层内采用折流,因此流体阻力介于纯径向流阻力(0.05~0.1MPa)和轴向流阻力(0.3~0.5MPa)之间,一般位于0.1~0.2MPa。
(2)改善催化剂床层的传热特性,传热系数大,移热能力强
GC型水冷板甲醇合成塔采用特殊工艺加工的水冷板作为换热元件,锅炉水在水冷板内腔狭小不规则的通道内扰动上升形成湍流,同时工艺气在催化剂床层内折向流动,并与冷却介质锅炉水错流,从而显著提高了水冷板的换热效率,气侧、水侧的传热膜系数分别达到1200W/m2·℃、5000W/m2·℃以上。
工艺气沿径向在每组水冷板之间反复折流绕行,采取气体折流设计,使通道内的流速基本相等,有效克服了以往径向催化床的缺点;另外,水冷板可以设计成非等间距结构,使单位催化剂的水冷板换热面积随着甲醇反应进度的变化而变化,从而实现了甲醇反应与传热完全同步,优化催化剂床层的温度分布,有效降低了局部催化剂过热现象的发生。
GC型水冷板甲醇合成塔采用板式换热元件后,比表面比圆管型水冷结构大幅提高,因此在催化剂装填量相同的情况下,GC型水冷板反应器的换热面积比水冷型管壳式反应器高,有效提高了设备的换热能力。
生产运行过程中,GC型水冷板甲醇合成塔产生的反应热由水冷板内的循环沸水移出,气水两侧的温差通常在10℃以下,催化剂床层温差小,使甲醇合成反应几乎达到等温反应(见图3)。
图3催化剂床层温度分布示意图
(3)催化剂装填系数高,生产能力强
GC型水冷板甲醇合成塔将管式水冷却单元改变为板式冷却单元,在相同换热面积条件下,板式冷却单元所占空间比管式冷却单元小,因此板壳式反应器的空间利用率比管壳式的利用率高,通常可增大10~20%,GC型水冷板甲醇合成塔催化剂装填系数可达到70%左右;同时GC型水冷板甲醇合成塔移热能力强,可以及时移走甲醇的反应热,因此醇净值比较高,5.5MPa可以达到6~8%,8.0MPa可以达到10~12%。
2.3GC型水冷板甲醇合成塔的质量保证
2.3.1水冷板换热元件的质量
GC型水冷板甲醇合成塔品质的关键在于水冷板元件的制造质量,其中最关键的是水冷板元件的焊缝质量和强度。
(1)水冷板焊缝的质量
目前,国昌公司水冷板的制造采用技术非常成熟的自动化生产线,通过自动焊接生产线完成水冷板的密封焊焊缝,焊缝均匀稳定,并经过严格的焊接质量检验,保证水冷板密封焊焊缝的质量合格率达到100%。
水冷板两板之间的凹形接触面全部为点式电阻焊,电阻焊为不填丝的等强度金属焊接,母材与母材之间瞬间高温熔合,如同不锈钢冶炼加固熔热处理的过程,不仅焊接牢固,而且焊接过程中晶格及材料成分没有变化。
通过电阻焊焊接好的整块水冷板相当于不锈钢冷做成形并经固熔处理后的型材,牢固、耐腐蚀。
水冷板在制造、组装过程中根据不同节点的要求分别进行5次水压试验和氨渗透试验,更好的确保了水冷板及附件的可靠性。
(2)水冷板强度的保证
水冷板在制造过程中采用的点式电阻焊,使每块水冷板被电阻焊点分成若干个区域,从而水冷板的受压面积缩小使其有足够的强度,然后在限位模具中以16.0MPa的水压充压成型。
水冷板充压成型过程中,水冷板的焊点在压力16.0MPa的情况下得到了检验。
充压成型后的水冷板,采取随机抽样并在无限位模具条件下进行水压试验,保证水冷板在8.0MPa的内压下不发生可见的变形,且在外压试压舱对样品进行外压试验,保证水冷板在10.0MPa的外压下不发生可见的变形。
水冷板在装配过程中,采用《压力容器安全技术监察规程》中的耐压试验标准对水冷板组及内件整体进行试压、检验。
2.3.2水冷板的安全稳定性
GC型水冷板甲醇合成塔在生产运行过程中内件与壳体以及内件各部件间存在温差,尽管温差不大,但为了保证该设备的安全运行,对每个可能产生热应力的部件都采取了热应力补偿措施,如每块水冷板上下设置尾巴管,保证水冷板自由膨胀;反应器顶部上升管设置膨胀节,保证内件受热自由伸缩,消除了热应力隐患,提高了设备的安全性。
因此,通过优化结构设计,强化设备的材料控制、加工制造、焊接、检验以及总体组装等环节的要求,确保了GC型水冷板反应器加工制造的工艺性和质量的可靠性。
3GC水冷板甲醇合成塔与管壳式甲醇反应器的比较
GC水冷板甲醇合成塔(GCSRC)采取板式水冷的换热方式,比管壳式甲醇反应器如气冷型反应器(TCC)、鲁奇型轴向反应器(LurgiSRC)、戴维径向反应器(DPTSRC)具有如下优势(见表1):
(1)LurgiSRC、GCSRC反应器单位催化剂装填量的换热面积较高,表明催化剂装填量相同的情况下,LurgiSRC、GCSRC反应器的换热面积大,甲醇反应热不易积聚;
(2)TCC、DPTSRC、GCSRC反应器催化剂装填系数较高,表明设备的空间利用率高;
(3)GCSRC反应器采用独特的板式结构设计,综合传热系数高。
表1GC型水冷板甲醇合成塔与管壳式甲醇反应器的比较
甲醇反应器类型
TCC
LurgiSRC
DPTSRC
GCSRC
换热管直径(或板腔高度)
mm
38
44
38
15
管(或板)间距
mm
68
51
68
40
单位催化剂的换热面积
m2/m3
45
100
45
80
催化剂装填系数
(理论值/实际值)
%
71/65
56/48
71/65
75/70
总传热系数
W/m2.K
350~450
450~550
450~650
650~750
注:
催化剂与换热单元的最大间距为20mm。
综上所述,GC型水冷板甲醇合成塔单位体积的催化剂传热能力达到60000W/m3catK,而Lurgi管壳式或相似结构形式的甲醇反应器一般低于50000W/m3catK,因此在相同条件下,GC型水冷板生产能力大,换热能力强,催化剂层温度平稳均匀,同平面温差小。
4GC型水冷板甲醇合成塔的应用及大型化前景
4.1GC型水冷板甲醇合成塔的应用
GC型水冷板甲醇合成塔是国昌公司开发的新型反应器,可应用于大甲醇装置上,单塔能力达到10~100万吨/年,目前已被河南鹤壁宝马化工有限公司与湖北当阳华强化工有限公司的15万吨/年甲醇装置采用,运行达到了设计的标准。
35万吨/年甲醇工艺包及关键设备GC型水冷板反应器于2008年通过内蒙古金诚泰化工有限公司及上海惠生设计院的审核,该装置的工艺流程(见图4):
合格的新鲜气(35℃、5.2MPa)与循环气汇合进入塔前换热器预热至210~220℃,然后进入甲醇合成塔催化剂床层进行反应,反应热由塔内的水冷板中的锅炉水移去,副产中压饱和蒸汽。
出塔工艺气(240~250℃)经回收热量、冷却后进入甲醇分离图4工艺流程示意图
器进行气液分离、洗涤,分离后的粗甲醇经闪蒸槽后进入精馏单元,分离下来的气体大部分经循环机提压后与补充气汇合进入系统,少部分去氢回收系统。
金诚泰35万吨/年甲醇装置GC型水冷板甲醇合成塔的技术参数见表2。
通过表2可知,在反应压力为5.2MPa的条件下,甲醇合成塔的醇净值可达到6~7%,比传统的管壳式反应器提高大约1%。
表235万吨/年甲醇装置GC型水冷板甲醇合成塔技术参数
公称直径mm
φ3500
正常运行压力MPa
5.2
运行阻力MPa
~0.2
醇净值%
6~7
副产蒸汽(2.5~4.0MPa)t/tCH3OH
1.1~1.3
合成反应器操作弹性%
50~110
4.2GC型水冷板甲醇合成塔的大型化前景
在世界基础有机化工原料中,甲醇消费量仅次于乙烯、丙烯和苯,是一种很重要的大宗化工产品。
虽然目前世界甲醇市场已供大于求,而且新建装置还将继续建成投产,但是根据专家对汽车代用能源的预测,甲醇是必不可少的替代品之一;另外,甲醇下游产品的开发也会进一步促进甲醇工业的发展,因此,甲醇工业的发展前景还是比较乐观。
国内甲醇工业目前面临着进口产品的冲击,原因是国内大部分装置规模小、技术落后、能耗高,造成生产成本高,无法与国外大型或超大型甲醇装置抗衡;另一方面,通过多年来技术引进及国内科研设计院所、高校的研究开发,目前我国甲醇工业已基本使用了国外各种类型的传统低压气相法反应装置,催化剂研制也达到国际水平,新工艺的研究也有较大的进展,主要问题在于装置的大型化,尤其是大型甲醇反应器的研究开发。
研究表明,甲醇装置的大型化将大大降低单位产能的投资及运行费用,详见表3。
表3煤制甲醇装置的投资与产品成本的关系
装置规模/(万t·a-1)
相对吨产品投资/%
相对产品成本/%
30
100
100
60
87
89
120
76
79
150
72
76
240
69
74
300
68
73
由表3可知,甲醇装置规模由30万t/a提高到150万t/a后,单位产品的投资可降低28%,产品成本可降低24%。
装置规模增大后,可带来明显的效益,因此,国内外新建甲醇装置均向大型化发展。
我国目前的产业政策也明确规定,新建甲醇装置规模需在100万t/a以上。
甲醇反应器是大型甲醇技术的核心,为实现甲醇装置的大型化,各甲醇技术供应商竞相开发新型甲醇反应器,各种新型甲醇反应器的开发主要从以下几个方面进行考虑:
(1)甲醇合成反应是强放热反应,甲醇反应器的结构应能满足快速移除反应热的要求,尽可能实现温度在整个催化剂床层内的均匀分布。
(2)甲醇合成反应是可逆反应,受反应热力学和动力学控制,反应的单程转化率达不到100%。
反应器出口气体中未反应的CO、H2和CO2需与甲醇产品分离,然后进一步压缩循环到反应器进行反应。
因此,甲醇反应器的床层压降应尽可能小,以减少循环气压缩的能耗。
(3)单台甲醇反应器的产量与其装填的催化剂量密切相关,甲醇装置大型化带来的是反应器体积的增加。
在装置规模一定的前提下,反应器催化剂的装填系数越大,所需的反应器体积越小,设备投资也越小。
(4)甲醇反应器需定期装卸催化剂并进行检修维护。
因此,甲醇反应器的结构设计应便于催化剂的装卸和检修维护。
(5)甲醇反应器是甲醇装置的关键核心设备,其投资占整个甲醇界区(包括合成圈及精馏装置)总投资的20%以上,因此降低甲醇反应器的造价可大大节省甲醇装置的投资。
目前已实现工业化或具备工业化条件的大型甲醇反应器有Lurgi、Topsoe、Davy、Casale、MGC等甲醇反应器,国昌公司在此基础上进行深入研究,成功开发了移热能力强、催化剂装填系数高、价格相对低廉的GC型水冷板甲醇合成塔,并在低压甲醇合成串联、串并联等相关工艺技术的基础上研究开发百万吨甲醇工艺流程及甲醇反应器设备,其工艺工艺流程及技术参数见见图5、图6、表4、表5。
通过表4、表5可知:
(1)甲醇反应器的内径Φ3800,完全能够满足国内现有的正常运输条件,方便反应器的制造及运输。
(2)国昌公司开发的百万吨级甲醇系统在压力8.5MPa的情况下,循环比为2.0~3.0,醇净值可达到12.5%以上。
(3)GC水冷板径向甲醇反应器在正常操作情况下的压力降低于0.2MPa,系统总阻力约为0.6MPa,因此循环机压缩功相对较低,为14.4kWh/tCH3OH。
图5120万吨/年GC型水冷板甲醇反应器串联工艺流程示意图
图6180万吨/年GC水冷型/气冷型串并联甲醇反应器工艺流程示意图
表4180万吨/年甲醇反应器主要技术参数
甲醇合成塔
第一、二反应器
第三反应器
直径:
mm
φ3800
φ3800
生产能力:
kt/a
600
600
反应器操作压力:
MPa
8.5
8.5
反应器阻力:
MPa
≤0.2
≤0.2
蒸汽产量(2.5~4.0MPa):
t/tCH3OH
1.1~1.3
合成反应器操作弹性:
%
50~110
表5180万吨/年甲醇系统主要工艺参数
序号
名称
单位
参数
备注
1
醇净值
%
12.5
2
新鲜气单耗
Nm3/tCH3OH
2240
3
系统阻力
MPa
0.6
4
锅炉水循环泵功耗
kWh/tCH3OH
0
正常自然对流
5
循环机功耗
kWh/tCH3OH
14.4
6
循环比
2.0~3.0
设备制造技术的进步,计算技术的发展,为新型甲醇反应器及工艺流程的开发以及甲醇合成催化剂性能的提高,奠定了甲醇装置大型化的技术基础。
当前国内年产百万吨级的大型甲醇技术已经发展成熟。
对于新建甲醇项目,应根据自身特点,综合考虑工程业绩、投资费用、运行成本、设备维护的难易程度等多方面因素,择优选择适宜的甲醇技术,建设大规模装置,以降低单位产能的投资及运行费用